产品质量检验方法培训
规范产品检验会议培训计划

规范产品检验会议培训计划一、培训目标1. 提高产品检验员的专业技能,使其能够熟练掌握各类产品检验技术和方法。
2. 规范操作流程,确保产品检验过程的准确性和科学性。
3. 增强产品检验员的安全意识和责任意识,确保产品质量和安全。
二、培训内容1. 产品检验基础知识(1)产品检验的意义和目的(2)产品检验的分类和流程(3)产品检验的标准和要求2. 产品检验技术和方法(1)外观检验技术和方法(2)尺寸检验技术和方法(3)功能检验技术和方法3. 产品检验仪器的使用和维护(1)常用产品检验仪器的使用方法(2)产品检验仪器的日常维护和保养4. 产品检验操作规范(1)检验前的准备工作(2)检验过程的注意事项(3)检验结果的记录和报告5. 产品质量和安全意识培训(1)产品质量和安全意识的重要性(2)产品质量和安全意识培训的方法和途径三、培训方式1. 理论培训通过讲座、研讨等形式进行产品检验基础知识、技术和方法的理论培训。
2. 实践演练组织产品检验员进行实际操作,熟练掌握产品检验技术和方法,提高实际操作能力。
3. 现场考察安排产品检验员到相关企业、机构进行现场考察和学习,了解行业最新发展和技术应用。
四、培训计划1. 第一阶段:理论培训(2天)第一天:产品检验基础知识培训第二天:产品检验技术和方法培训2. 第二阶段:实践演练(3天)第一天:外观检验技术和方法演练第二天:尺寸检验技术和方法演练第三天:功能检验技术和方法演练3. 第三阶段:现场考察(1天)到相关企业、机构进行现场考察和学习,了解行业最新发展和技术应用。
五、培训评估1. 理论考核对产品检验基础知识、技术和方法进行理论考核,合格方可进入下一阶段培训。
2. 实际操作考核对产品检验技术和方法进行实际操作考核,合格方可获得培训结业证书。
六、培训措施1. 培训材料准备准备培训手册、PPT等相关培训资料,方便产品检验员学习。
2. 培训师资力量邀请具有丰富产品检验经验的专家担任培训讲师,确保培训质量。
检验人员培训学习资料

检验人员培训学习资料一、培训目标检验人员培训的主要目标是确保所有检验人员能够全面理解其职责,掌握必要的检验技能,以及熟悉相关的法规和标准。
通过培训,检验人员应能够独立完成产品质量的检测工作,保证检测结果的准确性和可靠性。
二、培训内容1. 基础知识- 产品质量检验的基本概念- 产品质量法规和标准概述2. 检验技能- 产品抽样方法- 检测仪器的使用与维护- 数据记录与分析3. 专业技能- 特定产品检验流程- 缺陷识别与分类- 检验报告的编写4. 法规与标准- 国家及行业标准解读- 产品质量法规的遵守要点5. 安全与伦理- 实验室安全规程- 职业道德与责任三、培训方法1. 理论学习- 通过讲座、研讨会等形式,传授理论知识。
2. 实践操作- 在实验室进行实际操作练习,加深对检验流程的理解。
3. 案例分析- 分析历史案例,学习处理复杂问题的方法。
4. 模拟考试- 通过模拟考试检验学习成果,确保培训效果。
四、培训效果评估1. 知识测试- 定期进行书面测试,评估理论知识掌握程度。
2. 技能考核- 通过实际操作考核检验技能的熟练度。
3. 综合评价- 结合知识测试和技能考核,对检验人员进行全面评价。
五、持续教育1. 行业动态更新- 定期获取行业最新动态,更新培训内容。
2. 技术交流- 鼓励检验人员参与技术交流,分享经验。
3. 进阶培训- 为检验人员提供进阶培训机会,提升专业水平。
六、结语检验人员是产品质量保证体系中的关键一环。
通过系统的培训,不仅可以提升检验人员的专业技能,还能增强其对产品质量重要性的认识,从而为社会提供更加可靠的产品和服务。
以上内容为检验人员培训学习资料的概述,旨在提供一个全面、系统的培训框架,以确保检验人员能够胜任其职责,为产品质量保驾护航。
OQC成品检验培训
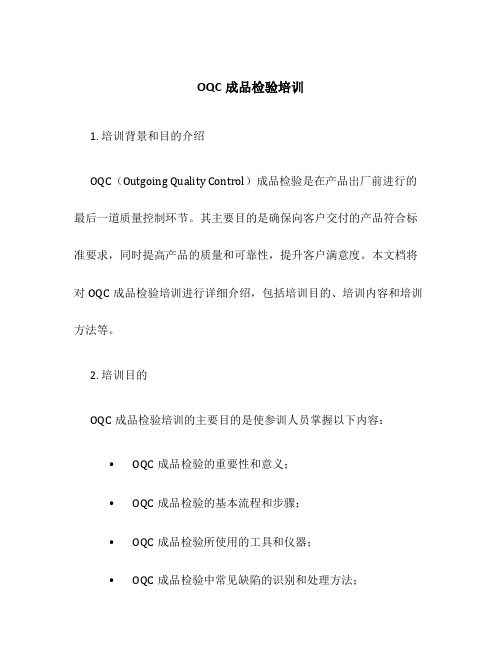
OQC成品检验培训1. 培训背景和目的介绍OQC(Outgoing Quality Control)成品检验是在产品出厂前进行的最后一道质量控制环节。
其主要目的是确保向客户交付的产品符合标准要求,同时提高产品的质量和可靠性,提升客户满意度。
本文档将对OQC成品检验培训进行详细介绍,包括培训目的、培训内容和培训方法等。
2. 培训目的OQC成品检验培训的主要目的是使参训人员掌握以下内容:•OQC成品检验的重要性和意义;•OQC成品检验的基本流程和步骤;•OQC成品检验所使用的工具和仪器;•OQC成品检验中常见缺陷的识别和处理方法;•OQC成品检验结果的记录和报告。
通过培训,参训人员将能够熟练进行OQC成品检验,并能准确地判断产品的质量状况,及时发现和解决问题,确保产品的质量符合要求。
3. 培训内容OQC成品检验培训主要包括以下内容:3.1 OQC成品检验基本概念•OQC成品检验的定义和作用;•OQC成品检验与其他质量控制环节的关系。
3.2 OQC成品检验的流程和步骤•OQC成品检验的主要流程和步骤介绍;•每个步骤的具体操作和注意事项。
3.3 OQC成品检验所使用的工具和仪器•不同产品种类所使用的常见工具和仪器;•工具和仪器的正确使用方法和维护保养。
3.4 OQC成品检验中常见缺陷的识别和处理方法•常见缺陷的分类和特征介绍;•缺陷的识别和判断方法;•缺陷的处理和修复方法。
3.5 OQC成品检验结果的记录和报告•检验结果的记录方式和要求;•如何编写OQC成品检验报告;•检验结果的数据分析和应用。
4. 培训方法OQC成品检验培训可以采用以下多种培训方法:•理论讲解:通过PPT、教材等形式对相关知识进行详细讲解,使参训人员了解OQC成品检验的理论基础;•实际操作:提供实际产品样品,让参训人员亲自进行OQC 成品检验,熟悉操作流程和步骤;•案例分析:通过实际案例的分析,让参训人员学会识别和处理不同缺陷;•讨论交流:组织参训人员进行小组讨论和交流,分享经验和策略;•考核评估:通过闭卷考试或实际操作评估的方式,检验参训人员的培训效果。
产品质量检验人员通用基础知识培训教材
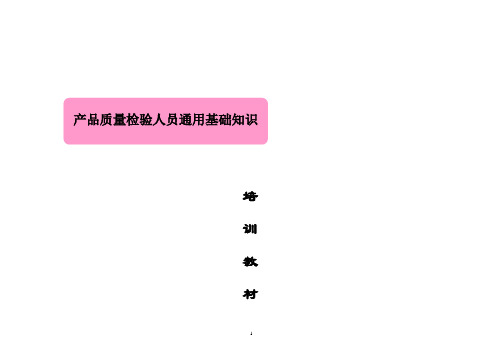
产品质量检验人员通用基础知识培训教材编制日期:2007年1月23日产品质量检验人员通用基础知识培训教材质量是构成社会财富的物质内容。
优良的产品质量和服务质量能给人们带来便利和愉快,给企带业来效益和发展。
而劣质的产品和服务会给人们带来烦恼甚至灾难。
一、质量定义质量概念的发展:二十世纪中,具有代表性的质量概念主要有——符合性质量、适用性质量、广义质量。
1、狭义的符合性质量概念:符合标准就是产品质量,符合的程度就是质量水平。
2、狭义的适用性质量概念:以适合顾客需要的程度作为衡量依据。
即产品在在使用时能成功满足用户需要的程度。
3、广义的质量概念:一组固有的特性满足要求的程度。
即要反映符合标准的要求,也反映了要满足顾客的需要,综合了符合性和适用性的含义。
1)“特性”——“固有的特性”:就是指某事物或某物中本来就有的,特别是永久的特性。
如彩色电视机,其固有的特性有:电性能、环境适应性能、安全性能、音色和彩色特性等。
——“赋于的特性”:不是某事物或某物中本来就有的,而是完成产品后因不同的要求而对产品所增加的特性。
如产品的价格,产品的交货时间等。
——关键质量特性:是指若超过规定的特性要求,会直接颢响产品安全性或产品整机功能丧失的质量特性。
——重要质量特性:是指若超过规定的特性要求,将造成产品部分功能丧失的质量特性。
——次要质量特性:是指若超过规定的特性要求,暂不影响产品功能,但可能会引起产品的功能逐渐丧失。
2)要求:明示的,通常陷含的或必需履行的需求。
——明示的:可以理解为规定的要求。
如在文件阐明的要求或顾客明确提出的要求。
——通常隐含的:可以理解在组织、顾客或相关方的例或一般的做法,如银行顾客的保密性。
——必须有履行的:是指法律法规的要求及强制性标准要求。
如在我国对人身、财产的安全和健康有关的产品,发布了相应的强制性的行政文件或制定了代号为GB的强制性标准。
3)质量程度:差、好或优秀级等表示。
二、质量管理1、质量管理概念:在质量方面指挥和控制组织的协调的活动。
产品质量检测所培训计划

产品质量检测所培训计划一、培训背景在当今社会,产品质量越来越受到消费者的关注,产品质量的稳定和可靠性不仅直接影响着企业的声誉和市场地位,也直接关系到产品的销售和企业的长期发展。
良好的产品质量控制体系对企业产品的研发、生产和销售过程,以及在市场上的产品服务起了至关重要的作用。
产品质量检测所作为企业产品质量管理的重要部分,对产品的质量进行检测和验证,进一步保障了产品的品质和性能。
因此,加强产品质量检测人员的培训和提高其专业技能水平,对于企业提高产品质量和降低产品质量风险具有重要意义。
二、培训目标1、了解产品质量检测的基本概念和方法;2、掌握产品质量检测的基本技能和操作流程;3、培养严谨的工作态度和严格的操作标准;4、提高产品质量检测人员的专业水平和责任意识。
三、培训内容1. 产品质量检测的基本概念和方法(1)产品质量的概念和意义(2)产品质量控制的原则和方法(3)产品质量检测的基本流程和方法2. 产品质量检测的基本技能和操作流程(1)产品检测仪器设备的基本原理和使用方法(2)产品质量检测的基本技能和操作流程(3)产品质量检测的标准和要求3. 严谨的工作态度和严格的操作标准(1)工作态度和职业道德(2)检测操作的严格标准和要求(3)工作中的注意事项和安全保障4. 产品质量检测人员的专业水平和责任意识(1)专业知识和技能的提升(2)责任意识和团队合作精神(3)职业发展和规划四、培训方法1. 理论教学:通过课堂讲授、讨论和案例分析等方式,使学员对产品质量检测的基本概念和方法有所了解;2. 实操训练:在实验室环境中模拟产品质量检测操作流程,让学员掌握产品检测仪器设备的使用方法和产品质量检测操作流程;3. 专家讲座:邀请产品质量检测领域的专家,就相关理论和实践经验进行深入讲解和交流;4. 实地考察:安排学员到相关企业或实验室进行实地考察和学习,深入了解和学习先进的产品质量检测技术和管理经验。
五、培训评估1. 培训前评估:通过调查问卷,了解学员的基本情况和学习需求,为培训内容的设计和实施提供参考;2. 培训中评估:通过随堂测试、作业等方式进行中期评估,了解学员的学习情况和水平;3. 培训后评估:通过考试、综合能力测试等方式进行培训后评估,评价培训效果和学员掌握的知识和技能。
产品质量培训内容
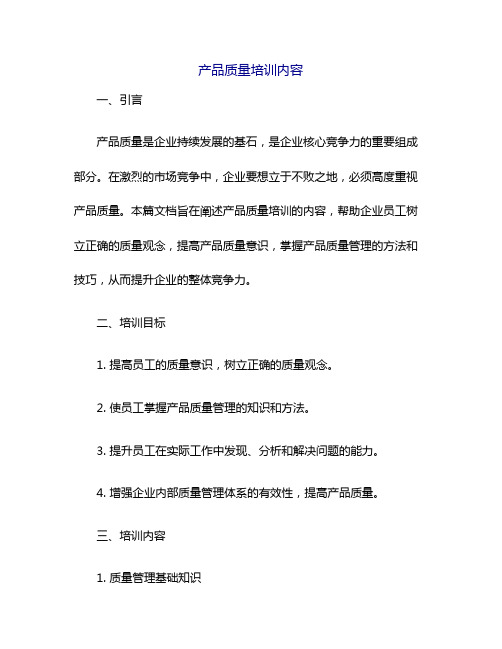
产品质量培训内容一、引言产品质量是企业持续发展的基石,是企业核心竞争力的重要组成部分。
在激烈的市场竞争中,企业要想立于不败之地,必须高度重视产品质量。
本篇文档旨在阐述产品质量培训的内容,帮助企业员工树立正确的质量观念,提高产品质量意识,掌握产品质量管理的方法和技巧,从而提升企业的整体竞争力。
二、培训目标1. 提高员工的质量意识,树立正确的质量观念。
2. 使员工掌握产品质量管理的知识和方法。
3. 提升员工在实际工作中发现、分析和解决问题的能力。
4. 增强企业内部质量管理体系的有效性,提高产品质量。
三、培训内容1. 质量管理基础知识(1)质量的概念:产品质量、过程质量、服务质量等。
(2)质量管理的发展历程:质量检验、统计质量控制、全面质量管理等。
(3)质量管理的基本原则:以顾客为关注焦点、领导作用、全员参与、过程方法、持续改进、事实决策、供应商关系管理等。
2. 质量管理体系(1)ISO 9001质量管理体系:标准内容、实施步骤、审核与认证等。
(2)质量管理体系文件:质量手册、程序文件、作业指导书、记录等。
(3)质量管理体系的运行:内部审核、管理评审、纠正措施、预防措施等。
3. 质量管理方法与工具(1)质量控制:直方图、因果图、流程图、散点图、排列图等。
(2)质量改进:PDCA循环、六西格玛管理、精益生产等。
(3)质量管理工具: affinity diagram(亲和图)、 tree diagram(树状图)、 matrix diagram(矩阵图)、 prioritization matrix(优先级矩阵)等。
4. 产品检验与试验(1)检验流程:进货检验、过程检验、成品检验、出货检验等。
(2)检验方法:视觉检验、尺寸检验、性能检验、寿命检验等。
(3)检验工具:通用量具、专用量具、试验设备等。
5. 质量成本与可靠性(1)质量成本:预防成本、鉴定成本、内部损失成本、外部损失成本等。
(2)可靠性基本概念:可靠性、维修性、保障性等。
质量检验技巧培训
品管七大手法七大手法:检查表、层别法、柏拉图、因果图、扩散图、直方图、控制图一、检查表检查表就是将需要检查的内容或者项目一一列出,然后定期或者不定期的逐项检查,并将问题点记录下来的方法,有时叫做查检表或者点检表。
例如:点检表、诊断表、工作改善检查表、满意度调查表、考核表、审核表、5S 活动检查表、工程异常分析表等.1、组成要素①确定检查的项目;②确定检查的频度;③确定检查的人员。
2、实施步骤①确定检查对象;②制定检查表;③依检查表项目进行检查并记录;④对检查出的问题要求责任单位及时改善;⑤检查人员在规定的时间内对改善效果进行确认;⑥定期总结,持续改进。
二、层别法层别法就是将大量有关某一特定主题的观点、意见或者想法按组分类,将采集到的大量的数据或者资料按相互关系进行分组,加以层别。
层别法普通和柏拉图、直方图等其它七大手法结合使用,也可单独使用。
例如:抽样统计表、不良类别统计表、排行榜等.实施步骤:① 确定研究的主题;②制作表格并采集数据;③将采集的数据进行层别;④ 比较分析,对这些数据进行分析,找出其内在的原因,确定改善项目。
三、柏拉图柏拉图的使用要以层别法为前提,将层别法已确定的项目从大到小进行排列,再加之积累值的图形.它可以匡助我们找出关键的问题,抓住重要的少数及有用的多数,合用于记数值统计,有人称为ABC 图,又因为柏拉图的排序识从大到小,故又称为罗列图。
1、分类1 )分析现象用柏拉图:与不良结果有关,用来发现主要问题。
A 品质:不合格、故障、顾客抱怨、退货、维修等;B 成本:损失总数、费用等;C 交货期:存货短缺、付款违约、交货期迟延等;D 安全:发生事故、浮现差错等。
2)分析原因用柏拉图:与过程因素有关,用来发现主要问题.A 操作者:班次、组别、年龄、经验、熟练情况等;B 机器:设备、工具、模具、仪器等;C 原材料:创造商、工厂、批次、种类等;D 作业方法:作业环境、工序先后、作业安排等。
质量检验员基础培训内容
• 抽取样本旳时间,能够在批旳形成过程中,亦能够 在批构成之后。
⑩.检验样本
• 根据产品技术原则或订货协议中对单位产品要求旳 检验项目,逐一对样本单位进行检验并合计不合格 (品)总数;
• 当不合格分类时应分别合计
⑾.逐批检验(不)合格旳判断
根据AQL和检验水平所拟定旳抽样方案,由 样品检验旳成果:
• 按鉴别措施分:计数检验、计量检验;
• 按产品检验后产品是否可供使用来分:破坏性检验、非破
坏性检验。
三、抽样计划
1 、全数检验和抽样检验
全数检验合用于:
检验是非破坏性旳; 检验数量和项目较少; 检验费用少; 影响产品质量旳主要特征项目 生产中尚不够稳定旳比较主要旳特征项目; 单件、小批生产旳产品; 昂贵旳、高精度或重型旳产品;
二、检验旳定义和分类
检验旳定义: 检验(Inspection)---采用某种措施(技术、手段)
测量、检验、试验和计量产品旳一种或多种质量特
征并将测定成果与鉴定原则相比较,以鉴定每个产
品或每批产品是否合格旳过程。
常用旳鉴定原则如: 国家或行业原则 检验规范(质量计划、作业指导书等) 产品规格书(程度样本、图片等)
能够应用自动化检验措施旳产品。
2.抽样检验合用于:
检验是破坏性旳; 被检对象是连续批
(如钢卷、胶片、纸张等卷状物或流程性材料) 产品数量多; 检验项目多; 希望检验费用少。
3.怎样拟定抽样容量?
进货检验、最终检验及出货检验可选用 GB2828-2023或其他抽样原则.(MILSTD-105E )
对过程检验,由质量筹划人员根据产品旳稳 定情况及过程能力等原因拟定抽样容量及 频次.
注:有关GB2828-2023旳使用措施请详见 <附录1>.
质量检验培训
数据处理原则
有效数字
数字修约
有效数字的 运算
报告单编写
检验结果反馈
检验报告
E-mail发 送
纸质报告
相关部门
填写报告接受单
采购部/物流部
试剂等级分级
试剂等级 试剂规格 标签颜色 国际通用 等级符号 杂质含量
一级 优级纯 绿色
GR
很低
二级 分析纯 红色
AR
低
三级 化学纯 蓝色
CP
略高于分析纯
适用范围
精确的分析和科研 一级分级
试剂贮存
一般化学试剂:应贮存在通风良好、干净和干燥的房间,要远离火源,并注意防止水分、灰尘和其他物质污染。 生化试剂:酶类、试剂盒等有贮存要的的试剂,一般应保存在0-5℃冷藏保存(不可冷冻结冰),如有特殊 要求的,应按要求存储。 危险试剂:硫酸,盐酸,有毒等危险试剂,常温保存(0-30℃)保存在阴凉通风的试剂柜中,双人双锁. 所有试剂摆放应分类有序,方便取用。
检验知识
2、质量检验的目的 ① 判定产品质量合格与否; ② 确定产品缺陷(不合格情况)的严重程度; ③ 把控源头,杜绝不合格产品流入。 ④ 获取质量信息; ⑤监督工序质量;
检验知识景
3、质量检验的重要作用
①把关——通过对原材料、成品的检验,鉴别,确定每个产品或产品批 次是否接收。严格做到“不合格的原材料不进入,不合格的产品不流出”。 ②预防——通过汇总数据,检测数据变化,及时发现问题,采取措施, 加以调整,预防不合格品的流入,预防问题产品。应该看到,把关本身也 是一种积极的预防。 ③反馈——通过对检验资料的分析整理,掌握产品质量情况和变化规律, 为改进设计、提高质量、加强管理提供必要的信息和依据。
数据处理
质量检验培训资料
01
02
03
按检验阶段可分为
进货检验、过程检验、最终检 验。
按检验性质可分为
破坏性检验、非破坏性检验。
按检验方法可分为
感官检验、理化检验。
04
按检法
抽样方法
随机抽样
按照随机原则从一批产品中抽 取一定数量的样本,确保样本
的代表性。
分层抽样
将产品按不同层次或类别进行 划分,然后从各层中分别抽取 样本。
质量检验培训资料
汇报人: 2024-01-05
目录
• 质量检验的基本概念 • 质量检验的流程和方法 • 质量检验标准和依据 • 质量检验工具和技术 • 质量检验中的问题与对策 • 质量检验案例分析
01
质量检验的基本概念
质量检验的定义
质量检验是对产品的一个或多个特性 进行测量、检查、试验、度量,并将 结果与规定的要求进行比较,以确定 每项特性是否合格的活动。
系统抽样
将产品按固定间隔进行抽取, 确保每个间隔都有被抽取的机 会。
周期抽样
按照固定的时间间隔或生产周 期进行抽样,适用于连续生产
的产品。
质量检验的目的是为了确保产品符合 规定的要求,防止不合格产品流入市 场。
质量检验的目的和意义
01
确保产品质量符合标准 或客户要求,提高客户 满意度。
02
及时发现不合格产品, 避免造成生产浪费和损 失。
03
提高生产效率和产品质 量水平,增强企业竞争 力。
04
保障消费者权益,维护 市场秩序。
质量检验的分类
- 1、下载文档前请自行甄别文档内容的完整性,平台不提供额外的编辑、内容补充、找答案等附加服务。
- 2、"仅部分预览"的文档,不可在线预览部分如存在完整性等问题,可反馈申请退款(可完整预览的文档不适用该条件!)。
- 3、如文档侵犯您的权益,请联系客服反馈,我们会尽快为您处理(人工客服工作时间:9:00-18:30)。
第三章质量检验大法第一节基本名词1.1 检验(Inspection)是指用某种方法(技术、手段)测量、检查、试验和计量产品的一种或多种质量特性并测定结果与判别标准相比较,以判定每个产品或每批产品是否合格的过程。
1.2 单位产品(unit product)单位产品是为了实施检验的需要而划分的基本单元。
1.3 批指同样制品或半制品的集合,也指“制造批”。
1.4 检验批(lot)需要进行检验的批,送检批的大小称批量(lot size),N表示。
1.5 样本(sample)指从检验批中抽取一个以上的单位产品所组在的。
1.6 缺陷(defect)指产品质量特征不满足预定使用要求的情况。
产品不符质量标准的任何一项要求就构成了一个缺陷,缺陷是指产品质量特性不满足预定使用要求的情况。
缺陷分为致命缺陷、重缺陷和轻缺陷三种。
1.6.1 致命缺陷(critical defect)致命缺陷是根据判断和经验认为,对使用和维护产品或以与此有关的人员可能造成危害或不安全状况的缺陷。
1.6.2 严重缺陷(major defect)重缺陷不同于致命缺陷,但能引起失效或显著降低产品预期性能的缺陷。
defect)轻缺陷是不会显著降低产品预期性能的缺陷,或偏离标准但只轻微影响产品有效使用或操作的缺陷。
1.7 不合格品(defective)含有任何一种缺陷的产品。
1.8 抽样计划(sampling plan)指每一检验批中需检验的样本大小,以决定该批允收准则,即允收数及拒收数。
1.9 允收品质水准AQL (Aueptable Quality Level)是指认为可以接受的连续提交检查批的过程平均上限值。
按批抽样程序,大部分皆将被允收,允收的机率约为95%,生产者冒险率约为5%。
*过程平均(Process Average)指供应商送初次检验的产品平均不良率(或平均百件缺点数)1.10 美军标准105E表(MIC-STD-105E)是一种抽样检验计划,主要用于连续在交货单独批检验,适用于AQC为0.01%较交者。
第二节检验的分类1、根据检验数量分类a)全数检验(100%inspection)。
是对批中,每一产品逐一进行检验,以确定每件产品的质量是否符合标准和否接收的检验,也称全检或100%检验。
b)抽样检验(sampling inspection)。
是按照统计方法从每一批产品中,抽取适当数量的部分产品作为样本,对样本中的每一个样品进行检验,通过这样的检验来判别整个一批产品是否符合标准和能否接收的检验。
2、根据流程分类a)来料检验(IQC)b)过程检验(IPQC)c)成品终检(FQC)d)出货检验(OQC)e)其他:库存检验,监督检验3、根据检验判别方法分类a)计数检验b)计量检验4、根据验质产品是否可供使用分类a)破坏性检验b)非破坏性检验5、根据检验内容分类a)试别检验b)性能检验(外观、尺寸、电性等)c)可靠性d)苛刻性6、抽样检验影响全数检验错误的多寡与下列因素有关:a)产品批量的大小;b)不合格品率的高低;c)检验工作的性质;d)检验工具的使用方法;e)检验人员技术水平和责任心。
7、抽样检验产品按统计方法进行抽样检验常常用于下列情况:a)检验是破坏性的;b)检验时,被检对象是连续体(如钢带、胶片、纸张等卷状物);c)产品数量多d)检验项目多;e)希望检验费用小;f)作为生产过程工序控制的检验。
抽样检验是利用样本进行的检验,所抽取的样本只占批中的一小部分,样本的质量特性检验结果当然也只能相对地反映整批产品的质量,不能把样本的不合格品率与整批产品的不合格品率等同起来。
随机抽样方法有下列几种:1)简单随机抽样(simple random sampling)简单随机抽样是从包含N个产品的检验批中抽取n个产品,使包含有n个产品的所有可能的组合具有相等的被抽取的概率。
a)确定页码b)确定起始点c)确定号码2)周期系统抽样(periodic systematic sampling)3)分层抽样(stratified sampling)各层在整批中所占的比例分别确定在各层中抽取的产品数量,则称为分层按比例随机抽样。
8、抽样检验标准及体系1) 计数与计量抽样检验标准按衡量产品质量特性指标和判别方法,分为计数抽样检验标准和计量抽样检验标准两种。
计数抽样检验标准是以计数抽样检验的结果作为判别质量特性指标的。
计量抽样检验标准是以计数抽亲检验的结果作为判别质量特性指标的。
2) 调整型与非调整型抽样检验标准按连续各批产品质量的变化是否根据抽样检验标准中确定的转换规则进行调整来分,可分调整型抽样检验标准和非调整型抽样检验标准两种。
除此之外,还有单水平和多水平连续抽样、链式抽样和跳批抽样也都属于调整型抽样检验。
3) 一次抽样、二次抽样、多次抽样和序贯抽样检验标准序贯抽样是每次检验一个产品或一组产品经检验后按照某一确定规则,做出该批接收、拒收或检验另一产品或另一组产品的检验。
我国抽样检验体系表大致如下图:抽样标准体系表抽样标准体系表抽样检验标准体系第三节抽样检验的实施以计数调整抽样检验为例,一般抽样检验的流程为:1.规定单位产品的质量特性2.不合格的分类3.合格质量水平的规定4.检查水平的规定5.检查批的形成与提出6.检查严格度的规定7.抽样方案类型的选择(表一严格度转移规则表)8.检索抽样方案(表二样本大小字码)9.样本的抽取10.样本的检查11.逐批检查合格或不合格的判断12.逐批检查后的处置表二样本大小字码第四节MIC-STD-105E抽样计划MIL-STD-105D计数值抽样表抽验程序a)选定AQL值b)决定检查水准c)选定样本代字d)查求抽样计划:应用AQL值及样本代字,从MIC-STD-105D表Ⅱ、Ⅲ或Ⅳ中可查得一个抽样计划。
若已知AQL 值及样本代字组合而不能查得抽样计划时,则可用表上所指引的其他样本代字。
其所求出的样本大小是依据新的样本代字,而非原来的代字。
如果这种方法对于不同等级的缺点得到不同的样本大小,经负责当局指定或认可后,对于各种等级的缺点,可以用相当于最大样本的样子代字。
又当允收数为0的单次抽样计划,经微得负责当局之指定或同意后,可以对指定之AQL值采用允收数为1及其相当的较大样本的抽样计划。
e)抽样计划的形式:用选定之AQL值及样本代字,可以求得数种抽样型式时,可使用任何一种的形式,无论是单次,双次抽样,通常是根据管理难易及平均样本大小加以比较。
单次抽样与双次抽样A)单次抽样:根据一次样本检查结果,来决定合格可不合格之形式。
例如:单次抽样法的检验步骤如下:B)双次抽样:第一次抽验结果可能被判定为合格、不合格和保留三种情况。
若被判定为保留时,追加第二次样本再决定合格或不合格之形式。
例如:由批量10000个中抽取32个第一样本,发现之不良品为2个或2个以下时,判定该批为合格,如不良品有3或4个时再抽取第二样本32个,合计64个样本加以检查,结果不良品个数的累计数在6个或6个以下时,判定该批为合格;7个或7个以上时为不合格。
以表示之如下:二次抽验法之形成:二次抽验法之步骤实例1:加压于瓶内的5.5kg/cm2经1分钟,作通过试验,须通过批量99.85%方为合格。
根据此标准,依MIL-SED-105D抽样表,试拟定单次抽样计划。
批量N=22000(解)AQL=0.15%,N=22000查样本数代字(表Ⅰ)知批量22000在(10001-35000)中,与Ⅱ级检验水准相交之处,其样本代字为M。
根据样本代字查表Ⅱ—A,得样本n=315再查样本数和AQL=0.15%相交之处,即得A C=1,R2=2。
实例2洋茹用玻璃瓶之重量应为97.45g±5.31g但不合于规定者,不得超过批量之4%,依MIL-STD-105D抽样表,试拟定其抽样计划,批量N=2000(解)N=2000,AQL=4%查样本数代字知批量2000在(1201-3200)中与Ⅱ级检验水准相交之处,其样本代字为K。
根据样本数代字K ,查表Ⅱ-A ,得样本数N=125再查样本数n=125和AQL=4%相交之处,即得Ac=10, Re=11 实例3洋茹粒状大小规格如下:粒状 茹伞直径(公里) 中No (medium)22至29假定该批之批量N=40000,某厂欲维持其大小直径,其品质在一定之标准内,商定AQL=2.5%,依照MIL-ATD-105D 抽样表,试拟定单次和双次抽样计划。
实例4试依下列条件,根据MIL-STD-105D 抽样表,拟定单次抽样计划之正常检验,严格检验及减量检验,并加以相互比较,N=9800。
本题的减量检验中,允收数Ac=2,拒收数Re=5,这样的程序有三个可能结果。
1. 一到拒收数或超过拒收数,就拒收该批,同时恢复使用正常检验。
2. 未超过允收数时,就允收该批。
并继续使用减量检验。
3. 当缺点数或不良品数超过允收数,但未达到拒收数时,就允收该批,下一批抽验时,则恢复使用正常检验。
实例5已知某批的批量N=200,允收水准AQL=0.10百件缺点数,试用MIL-STD-105D 正常检验,单次抽样,查出其样本大小,允收数及拒收数。
(解)由MIL-STD-105D 表Ⅰ,一般检验水准Ⅱ,得样本数代字G 查MIL-STD-105D 表Ⅱ-A ,样本数代字G 与AQL=0.10,箭头向下所指的抽样计划,得样本大小N=125,允收数Ac=0,拒收数Re=5。
第五节 抽样检验理论1、衡量批质量a) 批中不合格的单位产品所占的比例。
即b) 批中每百个单位产品平均包含的缺陷个数。
即c) 批中所有单位产品的某种质量指标的平均值u 。
如电灯泡的平均使用寿命。
d) 批中所有单位产品的某种质量指标的标准差б。
e) 过程平均不合格品率P 。
2、样本中不合格产品数的抽取概率×100%。