试论铸造工艺参数的确定
低压铸造参数确定(精)

职业教育材料成型与控制技术专业教学资源库《铝合金铸件铸造技术》课程教案低压铸造参数确定制作人:张保林陕西工业职业技术学院低压铸造参数确定一、引言低压铸造的工艺规范包括升液、充型、增压、保压结晶、卸压、冷却、延时,以及铸型预热温度、浇注温度、铸型的涂料等。
二、升液压力和升液速率升液压力是指当金属液面上升到浇口,所需要的压力。
式中,p1——升液阶段所需压力(MPa ); h1——金属液面至浇道的高度(cm);ρ ——金属液密度(g/cm3 );10200——单位换算系数(g/N); K ——充型阻力因数,K=1~1.5(阻力小取下限,阻力大取上限)。
在升液过程中,升液高度将随着坩埚中金属液面下降而增加。
因此,所需的压力将相应增大。
金属液在升液管内的上升速度即为升液速度,升液应平稳,以有利于型腔内气体的排出,同时也可使金属液在进入浇口时不致产生喷溅。
随着压力增大,升液管中的液面升高。
因此,增压速度实际上反应了升液速度。
增压速度可用下式计算,即式中,v1——升液阶段的增压速度(MPa/s );p1——升液压力(MPa );t1——升液时间(s )。
1020011K h p ρ=111t p v =一般情况下,为了有利于型腔中气体的排出,升液速度缓慢些为好。
对于铝合金,升液速度控制在5~15cm/s ,加压速度为1.27~1.75KPa/s 。
三、充型压力和充型速度充型压力是指使金属液充型上升到铸型顶部所需的压力。
式中,p2——充型压力(MPa );h2——金属液上升至铸件顶面的高度(cm);同样,所需的充型压力随着坩埚中金属液面下降而增大。
充型速度取决于通入坩埚内气体压力增加的速度,可按下式计算:式中,v2——充型速度(MPa/s );p1、p2——分别为升液和充型压力(MPa );t2——充型时间(s ) 充型速度关系到金属液在型腔中的流动状态和温度分布,因而影响铸件的质量。
充型速度慢,金属液充填平稳,有利于型腔中气体的排除,铸件各种温差增大。
第二章-铸造工艺方案的确定
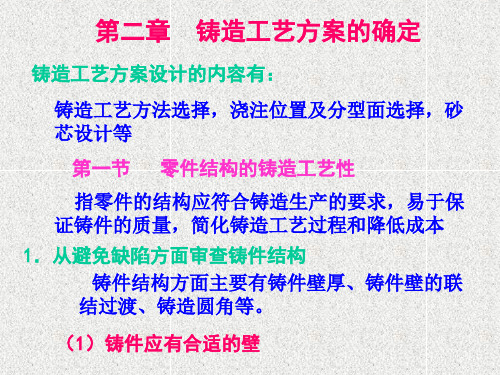
课堂讨论 图3-2-26
1.应使铸件全部或大部分置于同一半型内
图2-15 轮毂分型方案
2.应尽可能减少分型面数目 铸件的分型面少,铸件精度容易保ቤተ መጻሕፍቲ ባይዱ,且砂箱数目 少
图2-16 确定分型面数目的实例
3.平直分型面和曲折分型面的选择 尽可能选择平直分型面以简化工装结构及
其制造、加工工序和造型操作
图2-17 摇臂铸件的分型面
最小壁厚/㎜
高温合金
铝合金
0.6~1.0
1.5~2.0
0.8~1.5
2.0~2.5
1.0~2.0
2.5~3.0
—
3.0~3.5
—
3.5~4.0
铸件尺寸㎜
50×50 100×100 225×225
金属型铸造时铸件的最小壁厚
铝硅合 金
最小壁厚/㎜
铝镁合金、镁合 铜合金 金
灰铸铁
2.2
3
2.5
3
2.5
3
3
(1)改进妨碍起模的凸台、凸缘和肋板结构
改进妨碍起模的铸件结构 a)不合理 b)合理
教材220面,学生看,老师提问
(2)尽量取消铸件外表侧凹
图2-6 外壁内凹的框形件 a)不合理 b)合理
(3)有利于砂芯的固定和排气 (4) 减少或简化分型面(P221)
轴承架铸件
P222
(5)便于铸件的清理 (P222,图3-2-15) (6)简化模具制造 (P222,图3-2-16)
原则:
铸件精度和生产批量 吃砂量要求 吃砂量的确定
吃砂量: 铸件表面所需要的的最小型砂厚度。
根据铸件大小、重量、厚度、种类以 及型砂的特性和砂箱的结构确定。
吃砂量过小 砂型紧实困难,易引起胀砂、包砂、掉砂、
铸造成形技术铸造工艺设计

①选择铸件的浇注位置及分型面 ②型芯的数量、形状及其固定方法 ③确定工艺参数(加工余量、起模
斜度、圆角、 收缩率) ④浇冒口、冷铁形状、尺寸及其布
置
铸造工艺图——在零件图上用各种工艺 符号表示出铸造工艺方案的图形
它是制造模样和铸型,进行生产准备 和铸件检验的依据——基本工艺文件。
使型腔和主要芯位于下箱,便于下 芯、合型和检查型腔尺寸。
3.铸造工艺参数的确定
铸造工艺参数包括收缩余量、 加工余量、起模斜度、铸造圆角、 芯头、芯座等。
①收缩余量:
为了补偿收缩,模样比铸件图纸尺寸 增大的数值称收缩余量。收缩余量的大小 与铸件尺寸大小、结构的复杂程度和铸造 合金的线收缩率有关,常常以铸件线收缩 率表示:
工艺 打箱、清理等工艺操作 根据批量大小填写必要条
卡片 过程及要求
件
⑨ 综合整个设计内容
实例分析:
以C6140车 床进给箱体 为例分析毛 坯的铸造工 艺方案如下: 质量约35Kg。
车床进给箱体零件图
该零件没有特殊质量要求的表面, 仅要求尽量保证基准面D不得有明显 铸造缺陷,以便进行定位。
材料:灰铸铁HT150,勿需考虑补缩。
为了便于采用机器造型、尽量 避免活块,故凸台和凹槽均应 用型芯来形成。
为了克服基准面朝上的缺点, 必须加大D面的加工余量。
单件、小批量生产,采用手 工造型,使用活块造型较型芯 更为方便。同时,因铸件的尺 寸允许偏差较大,九个轴孔不 必铸出。
此外,应尽量降低上型高度, 以便利用现有砂箱。
显然,在单件生产条件下,宜 采用方案II或方案III。
在制订铸造工艺方案时,主要应着 眼于工艺上的简化。
1.分型面
三个方案供选择: 方案I:分型面在轴孔 的中心线上。 方案II:从基准面D分 型,铸件绝大部分位于 下型。 方案III:从B面分型, 铸件全部置于下型。
7.3铸造工艺设计解析
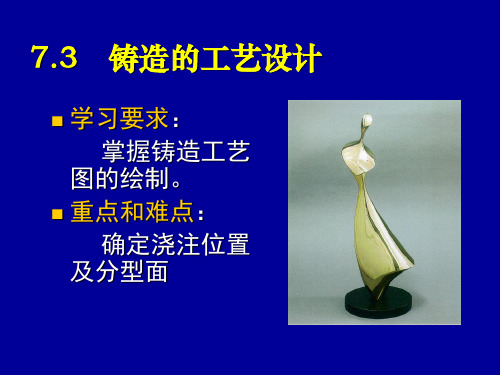
冒口
上
上
中
下
单件小批
中 下
放收缩率1% 余量:上面>侧面>下面
手工三箱造型 大批量
外 型 芯 块
两箱机器造型
7.3.5铸造工艺设计示例
例:支架零件如下图所示,材料为HT200, 单件、小批量生产工作时承受中等静载荷, 试进行铸造工艺设计。 1.零件结构分析:筒壁过厚,转角处未采用 圆角。修改后的结构如图b)所示。 2.选择铸造方法及造型方法 采用砂型铸造 (手工造型)中的两箱造型。 3.选择浇注位置和分型面
1.铸造工艺图: 利用各种的工艺符号,把制造模型和
铸型所需的资料直接绘在零件图上所得到 的图样。
即表示铸型浇注位置、分型面、浇冒口 系统、工艺参数、型芯结构尺寸、控制凝 固措施等的图样。
2. 铸件图:又称毛坯图,是反映铸件实际形 状、尺寸和技术要求的图样,也是铸造生产、 铸件检验与验收的主要依据。
(1)定义: 指铸件从线收缩开始温度冷却至室温时,
线尺寸的相对收缩量。 (2)选取: 大件、重要件不同部位可选取不同的收缩率; 一般件可选取同一收缩率。
4. 起模斜度
(1)定义:为了起模方便,在平行于起模方向的侧壁 加放的一定斜度。
(2)选取:对同一件,尽可能选用同一起模斜度; 立壁愈高,斜度应越小; 内壁的斜度值应大于外壁; 机器造型比手工造型斜度小; 金属模比木模斜度小。
3.铸型装配图:表示合型后铸型各组元之间
装配关系的工艺图。包括:浇注位置、型芯、 浇冒口系统和冷铁布置及砂箱结构和尺寸等。
7.3.2 铸造方法和造型方法选择
1.选择依据: 1)零件结构特点;2)合金种类; 3)生产批量等
2.选择原则: 单件、小批生产时一般采用砂型铸造
铸造生产工艺参数包括
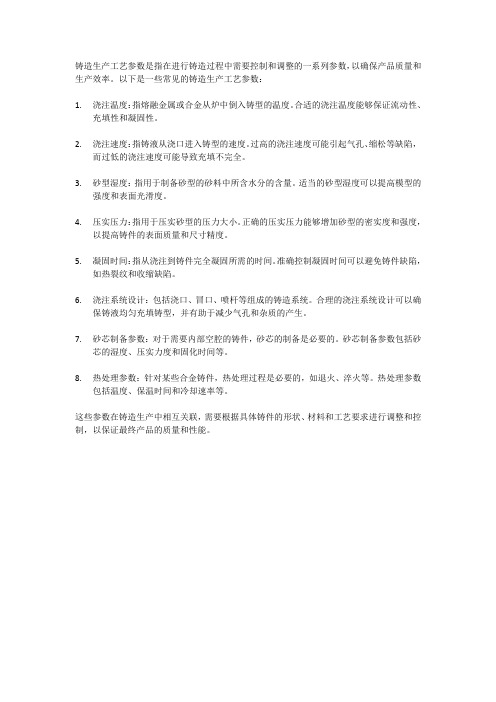
铸造生产工艺参数是指在进行铸造过程中需要控制和调整的一系列参数,以确保产品质量和生产效率。
以下是一些常见的铸造生产工艺参数:
1.浇注温度:指熔融金属或合金从炉中倒入铸型的温度。
合适的浇注温度能够保证流动性、
充填性和凝固性。
2.浇注速度:指铸液从浇口进入铸型的速度。
过高的浇注速度可能引起气孔、缩松等缺陷,
而过低的浇注速度可能导致充填不完全。
3.砂型湿度:指用于制备砂型的砂料中所含水分的含量。
适当的砂型湿度可以提高模型的
强度和表面光滑度。
4.压实压力:指用于压实砂型的压力大小。
正确的压实压力能够增加砂型的密实度和强度,
以提高铸件的表面质量和尺寸精度。
5.凝固时间:指从浇注到铸件完全凝固所需的时间。
准确控制凝固时间可以避免铸件缺陷,
如热裂纹和收缩缺陷。
6.浇注系统设计:包括浇口、冒口、喷杆等组成的铸造系统。
合理的浇注系统设计可以确
保铸液均匀充填铸型,并有助于减少气孔和杂质的产生。
7.砂芯制备参数:对于需要内部空腔的铸件,砂芯的制备是必要的。
砂芯制备参数包括砂
芯的湿度、压实力度和固化时间等。
8.热处理参数:针对某些合金铸件,热处理过程是必要的,如退火、淬火等。
热处理参数
包括温度、保温时间和冷却速率等。
这些参数在铸造生产中相互关联,需要根据具体铸件的形状、材料和工艺要求进行调整和控制,以保证最终产品的质量和性能。
铸造工艺参数及在工艺图中的表示方法
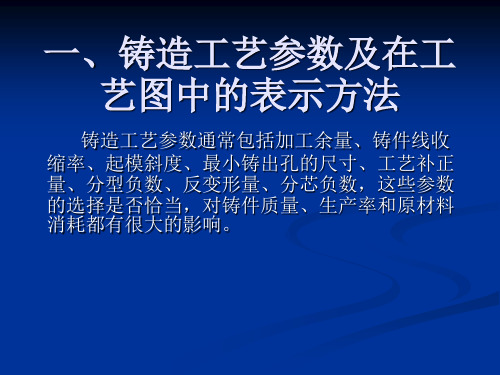
工艺补正量在工艺图中的表示方法:
6、分型负数
因起模后的修型和烘干引起砂型变形,致使分型 面凹凸不平,使合型不严密。为防止浇注时从分型 面跑火,合型时需在分型面上放耐火泥条或石棉绳, 这就增高了型腔的高度。为了保证铸件尺寸合图样 尺寸要求,模样上必须减去相应的高度,减去的数 值称为分型负数。
1)、若模样分为两半,且上、下两半是对称的, 则分型负数在上、下模样上各取一半,否则,分型 负数应在截面大的一侧模样上取。
起模斜度的设置方法:常采用增加壁厚法,对于加
工面一般采用增加壁厚的方法获得起模斜度,起模斜度 在加工余量后做出;加减厚度法,一般用各种铸筋,也 用于壁厚较小的模样侧面的起模斜度;减小壁厚法,一 般用于铸件壁厚较大的模样的起模斜度。
4、最小铸出孔
机械零件上往往有很多孔、槽和台阶,一般应尽 可能在铸造时铸出。这样既可以节约金属,减少机 械加工的工作量、降低成本,又可使铸件壁厚比较 均匀,减少形成缩孔、缩松等铸造缺陷的倾向。但 是,当铸件上的孔、槽尺寸太小,而铸件的壁厚又 较厚和金属压力较高时,反而会使铸件产生粘砂, 造成清理和机械加工困难。有的孔、槽必须采用复 杂而且难度较大的工艺措施才能铸出,而实现这些 措施还不如用机械加工方法制出更为方便和经济。 有时由于孔距要求很精确,铸出的孔如有偏心,就 很难保证加工精度。因此在确定零件上的孔和槽是 否铸出时,必须既考虑到铸出这些孔或槽的可能性, 又要考虑到铸出这些孔或槽的必要性和经济性。
一、铸造工艺参数及在工 艺图中பைடு நூலகம்表示方法
铸造工艺参数通常包括加工余量、铸件线收 缩率、起模斜度、最小铸出孔的尺寸、工艺补正 量、分型负数、反变形量、分芯负数,这些参数 的选择是否恰当,对铸件质量、生产率和原材料 消耗都有很大的影响。
材料成型第4章_铸造工艺设计1.答案

(2)尽量使铸件重要加工面或大部分加 工面、加工基准面放在一个砂型内,减少 错箱、披缝和毛刺,提高铸件精度。
床身铸件,其顶部平面为加工基准面。 图中方案a在妨碍起模的凸台处增加了外部型芯,因采用整模造型使加工 面和基准面在同一砂箱内,铸件精度高,是大批量生产时的合理方案。 若采用方案b,铸件若产生错型将影响铸件精度,但在单件、小批生产条 件下,铸件的尺寸偏差在一定范围内可用划线来矫正,故在相应条件下方 案b仍可采用。
25
方案1要考虑采用活块造型或加外型芯才能铸造; 方案2则省去了活块造型或加外型芯。
26
使铸件全部或大部分放在同一砂型
尽量使加工基准面与大部分 加工面在同一砂型内
不合理
合理
尽量使加工基准面与大部分 加工面在同一砂型内
27
(3)使型腔和主要型芯位于下箱,以便于造型、下 芯、合型和检查型腔尺寸。
于垂直或倾斜位置。图为油盘铸件的合理浇注位 置。
图4-2b 大面积薄壁铸件浇注位置
(4)对于容易产生缩孔的铸件,应使厚的 部分放在铸型的上部或侧面,以便在铸件 厚壁处直接安置冒口,使之实现自下而上 的定向凝固
铸钢卷扬筒,浇注时厚端放在上部是合理的; 反之,若厚端放在下部,则难以补缩。
23 图4-2-1 有热节的浇注位置
铸件的造型位置由分型面决定,而铸件的浇注位 置与造型位置通常是一致的。
浇注位置和分型面对铸件质量及铸造工艺都有很 大影响。
选择原则:着眼于控制铸件的凝固顺序
估计到铸件发生缺陷的可能
1.浇注位置的选择原则
(1) 铸件的重要加工面或主要工作面应朝下或位于 侧面,避免砂眼、气孔和夹渣
因为铸件的上表面容易产生砂眼、气孔、夹渣等缺陷,组 织也不如下表面致密。如果这些加工面难以朝下,则应尽 力使其位于侧面。当铸件的重要加工面有数个时,则应将 较大的平面朝下。
砂型铸造生产工艺参数选择.

加工基准
轮毂的分型面
分型面的选择原则
尽量选用平面,避免曲面分型,并应尽量选在最大截面上, 以简化模具制造和造型工艺。
分型面的选择原则
尽量选用平面。
分型面的选择原则
为便于造型、下芯、合箱、检验及检查,尽量将型腔置于 下箱
第三节 铸造工艺参数的选择
机械加工余量 最小铸出孔、槽 拔模斜度 铸造圆角 收缩率 型芯头 其它如分型负数、工艺补正量等
10
方案1
1. 选材: HT150 2. 铸型、造型方法:砂型,手工造型 3. 浇注位置/分型面:因支承台Φ50mm的内孔 及外壁均无需加工,只有两端面有机械加工 要求。为使支承台两端面组织致密、满足加 工要求,所以将铸件水平放置、使两加工面 在侧壁位置作为该件的浇注位置,这样还有 利于型芯的固定、排气和检验。为便于起模、 下芯和检验,选中间对称的最大截面为分型 面。此时分型面与分模面一致。
1机械加工余量铸件加工余量的大小取决于铸件的材料铸造方法铸件尺寸与复杂程度生产批量加工面与基准面的距离及加工面在铸型中的位置加工精度要求灰铸铁件较铸钢件线收缩率小熔点低铸件表面较光洁平整故其加工余量小铸钢件加工余量应比铸铁件大
铸件是怎样制造出来的?
第二节 浇注位置与分型面的选择
浇注位置的选择原则
分型面的选择原则
尽量将铸件全部或大部放在同一砂箱以防止错型、飞翅、 毛刺等缺陷,保证铸件尺寸的精确。
分型面的选择原则
应使铸件的加工面和加工基准面处于同一砂箱中。
方头
螺栓塞头
分型面的选择原则
铸件的加工面很 多,又不可能全部与 基准面放在分型面的 同一侧时,则应使加 工基准面与大部分加 工面处于分型面的同 一侧。
浇注位置的选择原则
- 1、下载文档前请自行甄别文档内容的完整性,平台不提供额外的编辑、内容补充、找答案等附加服务。
- 2、"仅部分预览"的文档,不可在线预览部分如存在完整性等问题,可反馈申请退款(可完整预览的文档不适用该条件!)。
- 3、如文档侵犯您的权益,请联系客服反馈,我们会尽快为您处理(人工客服工作时间:9:00-18:30)。
为了增加型 芯稳定性,常 采用两个或多 个铸件共一个 型芯的方法。
图4-8 悬臂式型芯及挑担式型芯
四件合铸
图4-9 联合式型芯
第二节 铸造工艺参数的确定
加工余量 拔模斜度 铸造圆角 收缩率
5/16/2009 4:29 PM
工艺参数
型芯头及型芯座
6
一、机械加工余量和铸孔
1. 加工余量
—指在铸件表面上留出的准备切削去的金属层厚度。
二、起模斜度
为了使模样(或型芯)便于从砂型(或芯盒)中取出,凡垂直 于分型面的立壁在制造模样时必须留出一定的倾斜度,此倾斜 度称为起模斜度。
➢ 起模斜度的大小取决于: 立壁的高度、造型方法、模样材料等 因素,通常为15’~3°。 立壁愈高,斜度愈小; 机器造型应比手工造型小, 木模应比金属模斜度大。 为使型砂便于从模样内腔中脱出、以形成自带型芯,内壁的起 模斜度应比外壁大,通常为3°~10°。
铸造收缩率主要取决于合金的种类,同时与铸件
的结构、大小、壁厚及收缩时受阻碍情况有关。
通常灰铸铁为0.7~1.0%, 铸造碳钢为0.3~2.0%, 铝硅合金为0.8~1.2%, 锡青铜为1.2~1.4%。
五、芯头及芯座
型芯的功用:是形成铸件的内腔、孔洞和形状复杂阻碍起模部 分的外形。 型芯头:是型芯的定位、支撑和排气的部分。
➢ 零件图上所有标注粗糙度符号的表面均需机械加工,均应 标注机械加工余量。
机械加工余量的具体数值取决于铸件的材料性质、造型方 法、加工要求、生产批量、铸件的结构的复杂程度和尺寸 及加工面在铸型中的位置等。
➢ 加工余量大浪费金属切去了晶粒细致性能较好的铸件 表层。
➢ 余量过小制品会因残留黑皮而报废,或者,因铸件表层
芯头的分类:
图4-12 垂直型芯及芯头
1)垂直型芯; 芯头必须留有一定的斜度α。
下芯头的斜度应小些(5°~10°), 上芯头的斜度为便于合箱应大些(6° ~15°)。h=15~150mm
型芯头与铸型型芯座之间应有 1~4 mm的间隙(S),以便于铸型的装配。
形式:上下都有芯头;只有下芯头,无上芯头; 上下都无芯头。
图4-11 自带型芯的起模斜度 宽度标注。
三、铸造圆角
铸造圆角 — 制造模样时,壁的连接和转角处要做成
圆弧过度。
目的: ① 可使转角处不产生脆弱面; ② 可减少应力集中; ③ 可避免产生冲砂、缩孔和裂纹。 圆角半径一般约为相交两壁平均厚度的1/3~1/2。 一般小型铸件: 外圆角半径取2~8mm,内圆角半径取4~16mm。
正方孔、矩形孔或气路孔深且直径小一般不铸出。 弯曲孔,当不能机械加工时原则上必须铸出。 正方孔、矩形孔的最短加工边必须大于30 mm才能铸出。
表4-4 铸件的最小铸出孔直径
生产批量
最小铸出孔直径
灰口铸铁件
铸钢件
大量生产 成批生产 单件、小批生产
12~15 15~30 30~50
-30~50
50
(1)若是加工孔,则孔的直径应为加上加工余量的数值; ห้องสมุดไป่ตู้2)有特殊要求的铸件例外。
再给出斜度数值。
➢垂直于分型面的孔,当其孔径大于高度时, 可在模样上挖孔,造型起模后,在砂型上形成 吊砂或自带型芯,并由此形成铸件孔。
起模时模样上的孔内壁与型砂的摩擦力较 其外壁大些,
即1、2、3 > 。 起模斜度在工艺图上用
或宽度a(mm)表示。 用机械加工方法加工模
具时,用角度标注;
用手工加工模具时,用
三、铸造圆角
凝固特 性
热节、 充型
不同转角 处的热节
30
四、铸造收缩率
铸件由于凝固、冷却后的体积收缩,其各部分尺寸均小于模样
尺寸。
为保证铸件尺寸要求,需在模样(芯盒)上加一个收缩的尺寸。
加大的这部分尺寸称为收缩量,一般根据铸造收缩率来定。
铸造收缩率K定义如下:
K L模-L件 100% L件
式中: L模──模样尺寸; L件──铸件尺寸。
垂直型芯一般都有上、下芯头; 短而粗的型芯也可省去上芯头。
2)水平型芯
图4-13 水平型芯及芯头
型芯头与铸型型芯座之间应有1~4 mm的间隙(S1), 以便于铸型的装配。 h=20~80mm。
芯头的形式
a) 一般式 b) 联合芯头 c) 加长加大芯头,d) 型芯撑。
•
1、有时候读书是一种巧妙地避开思考 的方法 。20.1 0.1020. 10.10Sa turday, October 10, 2020
误差也愈大,故余量也应随之加大。 – 浇注时朝上的表面因产生缺陷的机率较大.其加工余量应比
底面和侧面大。
2、铸出孔和槽的大小
铸件上的加工孔是否铸出,从可能性、必要性、经济性方面考虑: 较大的孔、槽应当铸出,以减少切削量和热节,提高铸件力学性能。 较小的孔和槽不必铸出,留待以后加工更为经济。
当孔深与孔径比L/D >4时,也为不铸孔。
二、型芯的形状、数量及分块
型芯是铸件的一个 重要的组成部分。
型芯的功用是形成 铸件的内腔,孔洞和 形状复杂阻碍起模部 分的外形。
图4-6 车轮铸件的型芯方案
对于内腔形状复杂的大铸件,常将形成内腔的型芯分割成数 块,使每块形状简单,尺寸较小,便于操作、搬运、烘干,简 化芯盒结构。
图4-7 复杂内腔的型芯分块
起模斜度形成方式: 增加厚度法、加减厚度法和减小厚度法。
增加铸件厚度
加减铸件厚度
图4-10 起模斜度的形式
减少铸件厚度
当侧面不加工时:
壁厚<8mm时,可采用增加壁厚法; 壁厚为8~16mm时,可采用加减壁厚法 壁厚>16mm时,可采用减小壁厚法
当铸件侧面需要加工时:
必须采用增加壁厚法; 加工表面上的起模斜度,应在加工余量的基础上
过硬而加速刀具磨损影响甚至达不到加工要求。
加工余量选择原则:
– 大量生产时,因采用机器造型,铸件精度高,故余量可减小 ;
– 手工造型误差大,余量应加大。 – 铸钢件表面粗糙、变形较大,其加工余量应比铸铁件大; – 有色合金铸件价格甚贵且表面较光洁、平整,其加工余量应
比铸铁小。 – 铸件的尺寸愈大或加工面与基准面的距离愈大,铸件的尺寸
设计时需考虑:保证定位准确、能承受砂芯自身重量和 液态合金的冲击、浮力等外力的作用,浇注时砂芯内部产生的 气体能顺畅引出铸型等。
制作时型芯及模样上须做出型芯头,对应造型时要在砂型中 做凹坑“座位”,使型芯定位。
1)定位作用; 主要确定: 型芯头的作用: 2)固定作用; 芯头长度、斜度和间隙。
3)排气作用。 长度取决于型芯的直径和长度