滑动轴承的应力分析
挖掘机曲臂关节滑动轴承油膜压力及合金层应力分布
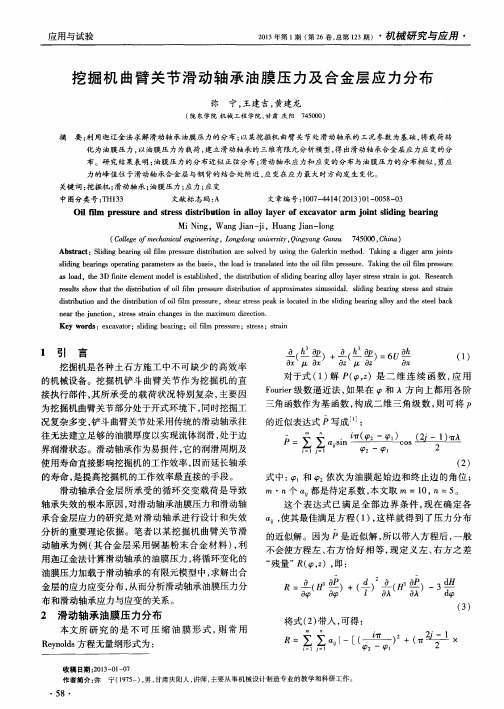
n e a r t h e j u n c t i o n , s t r e s s s t r a i n c h a n g e s i n t h e ma x i m u m d i r e c t i o n .
Ke y wo r d s:e x c a v a t o r ;s l i d i n g b e a in t g ;o i l i f l m p r e s s u r e;s t r e g , Wa n g J i a n - j i , H u a n g J i a n - l o n g
( C o l l e g e o fm e c h a n i c a l e n g i n e e r i n g, 几 g u n i v e r s i t y , Q i n g y a n g G a n s u 7 4 5 0 0 0 , C h i n a )
Oi l f i l m p r e s s u r e a n d s t r e s s d i s t r i b u t i o n i n a l l o y l a y e r o f e x c a v a t o r a m j o i n t s l i d i n g b e a r i n g
1 引 言
挖掘 机是 各种 土 石 方施 工 中不 可 缺少 的高 效 率
A ( h  ̄
应用与试验
2 0 1 3 年 第1 期( 第2 6 卷, 总 第1 2 3 期)・ 机械 研究与应用 ・
挖 掘机 曲臂 关 节 滑 动 轴 承 油 膜 压 力 及 合 金 层 应 力分 布
弥 宁, 王建吉, 黄建 龙
( 陇 东学院 机械 工程学院 , 甘肃 庆阳 7 4 5 0 0 0 )
滑动轴承的故障诊断分析 (DEMO)

滑动轴承的故障诊断分析一、滑动轴承的分类及其特点1、静压轴承静压轴承的间隙只影响润滑油的流量,对承载能力影响不大,因此、静压轴承可以不必调整间隙,静压轴承在任何转速下都能保证液体润滑,所以理论上对轴颈与轴瓦的材料无要求。
实际上为防止偶然事故造成供油中断,磨坏轴承轴承,轴颈仍用45#,轴瓦用青铜等。
2、动压轴承动压滑动轴承必须在一定的转速下才能产生压力油膜。
因此、不适用于低速或转速变化范围较大而下限转速过低的主轴。
轴承中只产生一个压力油膜的单油楔动压轴承,当载荷、转速等条件变化时,单油楔动压轴承的油膜厚度和位置也随着变化,使轴心线浮动,而降低了旋转精度和运动平稳性。
多油楔动压轴承一定的转速下,在轴颈周围能形成几个压力油楔,把轴颈推向中央,因而向心性好。
异常磨损:由于安装时轴线偏斜、负载偏载、轴承背钢与轴承座孔之间有硬质点和污物,轴或轴承座的刚性不良等原因,造成轴承表面严重损伤。
其特征为:轴承承载不均、局部磨损大,表面温度升高,影响了油膜的形成,从而使轴承过早失效。
二、常见的滑动轴承故障●轴承巴氏合金碎裂及其原因1.固体作用:油膜与轴颈碰摩引起的碰撞及摩擦,以及润滑油中所含杂质(磨粒)引起的磨损。
2.液体作用:油膜压力的交变引起的疲劳破坏。
3.气体作用:润滑膜中含有气泡所引起的汽蚀破坏。
●轴承巴氏合金烧蚀轴承巴氏合金烧蚀是指由于某种原因造成轴颈与轴瓦发生摩擦,使轴瓦局部温度偏高,巴氏合金氧化变质,发生严重的转子热弯曲、热变形,甚至抱轴。
当发生轴承与轴颈碰摩时,其油膜就会被破坏。
摩擦使轴瓦巴氏合金局部温度偏高,而导致巴氏合金烧蚀,由此引起的轴瓦和轴颈的热胀差,进一步加重轴瓦和轴颈的摩擦,形成恶性循环。
当轴瓦温度T大于等于230°C时,轴承巴氏合金就已烧蚀。
三、机理分析大多滑动轴承由于运行过程中处于边界润滑状态所以会产生滑动摩擦现象,同时又居有一定的冲击能量和势能,所以存在与产生滑动摩擦和碰摩相同的故障机理。
轴瓦合金层应力的有限元分析

第35卷第1期 2001年1月上海交通大学学报JOU RNAL O F SHAN GHA I J I AO TON G UN I V ER S IT YV o l .35N o.1 Jan .2001 收稿日期:1999209220 文章编号:100622467(2001)0120144205轴瓦合金层应力的有限元分析刘春慧, 王成焘, 程先华(上海交通大学机械工程学院,上海200030)摘 要:建立了合金层、钢背和轴承座的三层圆筒模型,利用AN SYS 软件对轴瓦应力,尤其是合金层应力进行了计算,计算过程中考虑应力沿合金层厚度方向的变化.结果显示,轴瓦周向应力分布取决于油膜压力的梯度,最大拉应力位于压力梯度最大处,而周向压应力的峰值则位于压力梯度方向改变处.径向应力的分布与油膜压力的分布相同,压应力存在于油膜压力区域.径向应力与周向应力的最大值位于轴瓦合金层内表面.剪应力存在于压力峰值周围,并有一个转向过程,且剪应力的峰值位于轴瓦中截面合金层与钢背的结合处.理论计算证实,轴瓦合金层愈薄,疲劳强度愈高.关键词:轴瓦合金层;应力;压力梯度;有限元分析中图分类号:TH 133.31 文献标识码:AF inite Elem e nt Ana lys is of S tre s s D is tribution on B e a ring A lloyL IU Chun 2hu i , W A N G Cheng 2tao , CH EN G X ian 2hua(Schoo l of M echan ical Eng .,Shanghai J iao tong U n iv .,Shanghai 200030,Ch ina )Abs tra c t :A th ree 2layer cylinder m odel con tain ing alloy ,steel lin ing and hou sing w as estab lished .W iththe help of fin ite elem en t m ethod (FE M )softw are p ackage AN SYS ,and con sidering the stress change along alloy th ickness ,the bearing stress esp ecially in alloy layer w as calcu lated .T he resu lts show that the tangen tial stress distribu ti on is decided by p ressu re gradien t ,that is ,the m ax i m um ten sile stress locates w here m ax i m um p ressu re gradien t is ,w h ile the com p ressive stress locates w here p ressu re gradien ts change their directi on .T he distribu ti on of radial stress is the sam e as that of o il fil m p ressu re ,w h ich m ean s com 2p ressive stress at the p ressu re regi on .T he radial and tangen tial stress m ax i m um s are bo th in the inner su r 2face of bearing alloy .T he shear stress is near the m ax i m um p ressu re ,and reaches m ax at the bonding su r 2face of m id 2secti on betw een back ing and alloy .It is p roved by theo retical calcu lati on that the th inner the alloy ,the h igher the bearing fatigue strength .Ke y w o rds :bearing alloy ;stress ;p ressu re gradien t ;fin ite elem en t analysis 动载滑动轴承在周期性循环变化的油膜压力作用下,将在合金层产生循环变化的径向应力Ρr 、周向应力Ρt 及剪切应力Σ.由于油膜压力形状的不规则性及实际轴承系统的复杂性,使得应力的求解有一定的难度,国内外学者曾提出了一种计算模型和计算方法[1~3],他们研究发现,轴瓦承载区合金层中的循环交变应力将导致轴瓦表面疲劳失效,合金层在周向拉应力作用下最易发生疲劳,疲劳裂纹常常出现在最大拉应力处.而拉应力的大小不仅和油膜压力的大小有关,更取决于压力梯度.压力梯度大时,合金层受到的拉应力较大.交变正应力使轴瓦合金层表面疲劳,而交变剪应力使钢背和合金层的结合面疲劳.轴瓦材料耐疲劳性随着合金层厚度和温度的升高而降低[4].本文利用有限元软件AN SYS 计算了轴瓦,尤其是合金层的应力分布,探讨了油膜压力分布、轴承座弹性模量、合金层厚度等对轴瓦应力的影响.1 轴瓦有限元模型实际轴瓦可以简化成三层圆筒模型:最里面是轴承合金层;中间是钢背;最外面是轴承座,与前两者相比,这部分通常较厚.假定这三层是紧密地结合在一起,合金层的径向尺寸只有0.2~0.6mm ,对于安装在整个机体中的主轴承来说,轴承座的厚度与之相比可以认为是无穷大的,但在有限元划分网格和计算时必须给轴承座厚度一个确定的值.由于油膜压力分布呈抛物线状,且轴瓦结构具有对称性,取轴瓦半宽作为分析求解区域.采用各向同性的线弹性材料,忽略轴瓦表面摩擦力.轴承系统共划分为3456个8节点六面体单元,其中合金层的划分较密,为1152个单元.中间剖面采用面对称约束,轴承座外部固定,负荷为作用在轴瓦内表面的油膜压力.在上述轴瓦模型中,涉及到截面、层等概念,现定义如下:轴瓦(合金层)内表面,即与轴颈产生相对运动的表面.截面,即与轴瓦中轴线垂直的平面.轴瓦宽度方向的中间剖面称为中截面(亦称截面5),轴瓦的端面称为边缘截面(亦称截面1),从边缘截面到中截面之间依次为截面1~5.层,即与轴瓦内表面平行的截面.根据有限元网格的划分,自轴瓦内表面至合金层与钢背的结合面依次为第1~5层.2 影响轴瓦合金层应力的因素影响轴瓦合金层应力的因素有很多,如:轴承座厚度、轴承座弹性模量、油膜压力梯度等.为分析上述各因素对轴瓦应力分布的影响,建立如下轴瓦模型:轴瓦宽度t k =27mm ,直径63.2mm .合金层材料A lSn 20Cu ,弹性模量E =63GPa ,泊松比Λ1=0.31,厚度t a =0.5mm ;钢背材料08A l ,E =210GPa ,泊松比Λ2=0.29,厚度为1.85mm .2.1 轴承座厚度对轴瓦应力的影响为确定轴承系统模型中轴承座的厚度,本文探讨了不同厚度轴承座t h 对合金层应力分布的影响.以轴瓦厚度t b 作为度量轴承座厚度的标准,选择了厚度分别为轴瓦厚度10、15、20、25、30、35、40、45、50、60、70和80倍的轴承座进行分析.利用图1所示的油膜压力p 分布作为轴瓦表面的压力负荷,对上述A lSn 20Cu 轴瓦(假定轴承座材料与钢背材料相同,即E =210GPa ,泊松比Λ=0.29)进行计算.图1 计算所用油膜压力瞬时分布图F ig .1 T ran sien t o il fil m p ressu re distribu ti on 图2(a )为轴瓦合金层中径向应力最大值Ρr,m ax 和最小值Ρr,m in 随轴承座厚度的变化,由图可见,径向应力对轴承座的厚度不敏感,只要轴承座厚度大于轴瓦厚度30倍即可满足精度要求.图2(b )为轴瓦合金层中周向应力的最大值Ρt,m ax 和最小值Ρt,m in 随轴承座厚度的变化,由图可见,Ρt,m ax 受轴承座厚度的影响较大,它开始时随轴承座厚度的增加而增大,直到轴承座厚度等于轴瓦厚度的50~60倍时达最大值,之后呈下降趋势,但从40倍后应力改变的幅值不大,故认为计算时取大于轴瓦厚度的40倍皆可.图2 应力随轴承座厚度的变化F ig .2 Stress variati on vs hou sing th ickness2.2 轴承座弹性模量对轴瓦应力的影响轴瓦的有限元模型中,轴承座内表面的变形可以直接传递到轴瓦.在弹性轴承座下允许轴瓦外层541 第1期刘春慧,等:轴瓦合金层应力的有限元分析径向位移,而刚性轴承座则限制轴瓦外表面的径向变形.为了观察轴承座弹性模量E 对轴瓦应力分布的影响,本文选择了刚性轴承座,E 分别为50、100、150、200和250GPa 的轴承座进行分析,钢、铸铁、铝合金等常用轴承座材料的E 在上述范围之内.以图1所示的瞬时油膜压力分布作为轴瓦负荷.由图3(a )可以看出,径向应力对轴承座的E 不敏感.由图3(b )可以看出,Ρt,m in 随轴承座E 的增加缓慢下降,而Ρt,m ax (即周向最大拉应力)在刚性轴承座下最小,在弹性轴承座支撑情况下,计算结果显示出了周向应力,特别是拉应力,随着轴承座E 的增加而显著降低.例如,在弹性轴承座情况下,当E =50GPa 时,Ρt,m ax =41.662M Pa ,当E =200GPa 时,Ρt,m ax =12.276GPa ,而在刚性轴承座情况下,Ρt,m ax ≈0.因此,E 低的轴承座将导致较高的轴瓦周向拉应力,从而加速轴瓦的疲劳失效.图3 应力随轴承座弹性模量的变化F ig .3 Stress variati on vs elastic modu les ofhou sing2.3 应力分布计算采用无摩擦的三层圆环系统模型,轴承座材料为钢背,厚度为轴瓦厚度的50倍,中截面用对称约束,轴承座外表面固定.径向应力的分布与油膜压力的分布相同,在油膜压力的峰值区域,径向压应力与径向拉应力均达到峰值,如图4(a )所示.所不同的是,径向压应力在轴瓦中截面附近,而径向拉应力在轴瓦边缘截面附近区域,应力值均在轴瓦表面最大,随轴瓦厚度增加逐渐降低,如图4(b )所示.图4 径向应力三维分布图F ig .4 3D radial stress distribu ti on 虽然假设合金层和钢背在结合面处有相同的应变,但由于弹性模量、泊松比等材料特性的不同,周向应力不等.从图5(a )中轴瓦周向应力Ρt 的分布可以得到,在油膜压力区域主要是周向压应力,应力值向压力区边缘逐渐减小.压应力的峰值与压力梯度的方向有关,最大压应力位于压力梯度改变符号的地方.合金层内表面各层周向应力具有相同的分布规律,即基本上呈双峰值分布,拉应力在115°和200°附近达到峰值,但各层的峰值大小不同,在中截面Α=200°处达到最大拉应力为31.37M Pa ,在中截面Α=115°处具有周向拉应力峰值为18.52M Pa .分析周向应力Ρt 与油膜压力p 的对应关系,可以发现最大拉应力的峰值与压力峰值有一个位置差,因此周向拉应力的峰值是由油膜压力梯度大小决定的,对该轴瓦在油膜压力的入口和出口处压力梯度达到峰值,周向拉应力的峰值产生在该位置处.另一方面中截面处的压力梯度峰值是各层中最大的,故合金层表面周向应力的最大值位于中截面处. 从图5(b )所示的中截面处合金层周向应力随合金层厚度的变化可知,合金层的周向应力分布基本上呈从合金层内表面向结合面逐渐减小的趋势,周向应力在合金层内表面具有最大值,中截面处最大周向压应力在175°为-189M Pa ,而在200°达到最大拉应力值31.37M Pa .边缘截面的周向应力值641 上 海 交 通 大 学 学 报第35卷 小于中截面,故中截面处周向应力对疲劳裂纹的萌生和扩展影响较大.且最大周向拉应力值位于轴瓦表面,疲劳裂纹应首先在轴瓦表面产生.图5 周向应力三维分布图F ig .5 3D tangen tial stress distribu ti on 由于这个模型忽略了轴瓦表面的摩擦力,故表面上的剪应力几乎为零,如图6(a )所示.从图6中可以得到:剪应力存在的区域为油膜压力峰值区域,其大小随合金层从表面至与钢背结合处呈递减趋势,在合金层与钢背结合处达到最大值,且最大值位于轴瓦中截面.另外在油膜压力的峰值区域,剪应力还存在一个转向过程.因此,由剪应力产生的裂纹通常在合金层与钢背结合处萌生,且扩展方向相反.2.4 合金层厚度对轴瓦应力的影响轴承合金层的疲劳裂纹,一般发生在应力集中点或合金层金相组织的薄弱处.轴承合金层的抗疲劳能力不仅取决于它的机械强度,还受其厚度的影响.轴承合金层愈薄,其疲劳强度愈高. 对合金层厚度分别为0.1~0.7mm 的A lSn 20Cu 轴瓦进行了应力计算,图7所示为合金层中截面处最大周向应力随合金层厚度的变化.周向应力值随合金层厚度的增加而增加,且周向应力是导致轴瓦疲劳失效的主要因素,轴瓦的疲劳抗力随合金层厚度增加逐渐降低,故从理论计算上证实了轴承合金层愈薄疲劳强度愈高这一结论.图6 剪切应力三维分布图F ig .6 3D shear stress distribu tion图7 最大周向拉应力随合金层厚度的变化F ig .7 M ax tangen tial stress changes vs.alloy th ickness 3 结 论(1)轴承座厚度大于轴瓦厚度的40倍对轴瓦应力的计算结果影响不大.(2)轴瓦径向应力和周向压应力对轴承座的弹性模量不敏感,而周向拉应力随轴承座弹性模量E 的增加而降低.(3)周向应力分布取决于油膜压力的梯度.周向拉应力随着压力梯度的增大而增大,最大拉应力产生在压力梯度最大处,而周向压应力的峰值则位于压力梯度方向改变处.(4)径向应力的分布与油膜压力的分布相同,741 第1期刘春慧,等:轴瓦合金层应力的有限元分析压应力存在与油膜压力区域,自内表面至结合处逐渐减小.(5)剪应力存在于压力峰值周围,并有一个转向过程,且剪应力的峰值位于轴瓦中截面合金层与钢背的结合处.(6)周向应力随合金层厚度的增加而增加,即轴瓦合金层愈薄疲劳强度愈高.参考文献:[1] Sinch S.Stress and defo rm ati on of a long hydrody2nam ic j ou rnal bearing[J].Compu ter&Structu res,1993,48(1):81~86.[2] 王成焘,倪学海.内燃机轴承疲劳损伤机理及理论计算[C].上海:上海市内燃机学会第三届学术会议论文集,1987.[3] H acifazli oglu S,Karaden iz S.A param etric study ofstress sou rces in j ou rnal bearings[J].In t J M ech Sci,1996,38(8):1001~1015.[4] T i m ohy L G,Hovard E B.M etals handbook[M].U SA:Am erican Society fo rM etals,M etals Park, O h i o,1985.作者简介: 刘春慧 1973年生,1999年毕业于交通大学机械工程学院,获博士学位.主要从事汽车发动机摩擦学设计的研究.现在上海日立电器有限公司技术中心任职,从事家用空调压缩机的开发和研制工作. 王成焘 男,1940年生,上海交通大学机械工程学院教授、博士生导师,先后主持了五项国家自然科学基金项目,三项国家教委基金项目;获得上海市科研成果二等奖,国家教委、上海市及机械部科技进步三等奖各一次.撰写《汽车摩擦学》、《现代机械设计》、《机械创新设计》、《假体工程学》等著作多部,发表学术论文50余篇. 程先华 1961年生,上海交通大学机械工程学院高级工程师,博士.目前主要从事材料表面磨损性能研究和新材料研制及其工艺性能研究.在国内外学术刊物上发表论文30多篇.获三项部级以上科研成果奖.下期发表论文摘要预报三个Buffers切换到达系统的混合系统建模和控制杨根科, 吴智铭(上海交通大学自动化系,上海200030)摘 要:采用被服务Buffer编号为离散标识,Buffer中待处理任务数为连续状态,建立了系统的代数微分方程模型.提出了3个Buffers切换到达系统不稳定周期轨道的一种基于混合状态的镇定控制方法.当Server服务于1个Buffer时,以此状态下在连续周期轨道上对应的2个顶点张成的一维线形子流型为滑动目标,仅通过系统许可的对极限连续处理时间的控制,使系统镇定于周期轨道.并从系统的混合模型角度,分析了镇定方法的鲁棒性.具有强鲁棒性的时滞滤波器设计梁春燕, 谢剑英, 钟庆昌(上海交通大学自动化系,上海200030)摘 要:采用了零极点配置方法来设计具有强鲁棒性的时滞滤波器,消除小阻尼不确定性系统的残留振动.通过在系统极点附近配置多个滤波器零点,建立离散传递函数得到时滞滤波器方程,设计简单.该方法在起重机载荷防摆控制中得到了很好的应用,能够有效地消除载荷的摆动,且对缆绳长度的变化具有很好的鲁棒性.841 上 海 交 通 大 学 学 报第35卷 。
AVL技术资料19_AVL_蓝军_径向滑动轴承载荷和磨损分析
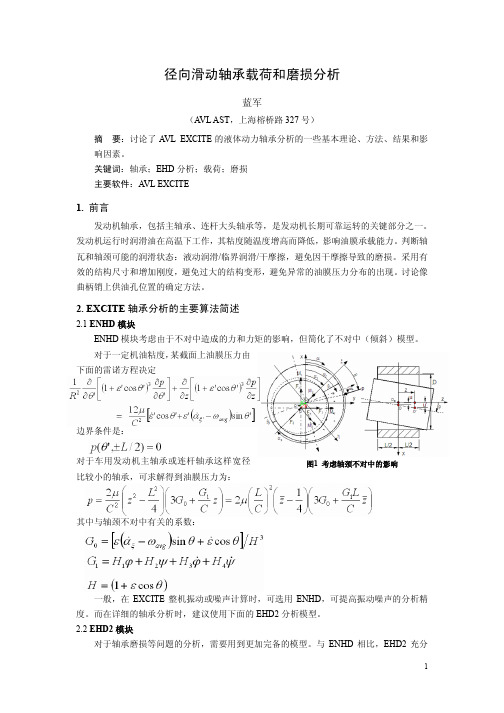
图1 考虑轴颈不对中的影响径向滑动轴承载荷和磨损分析蓝军(A VL AST ,上海榕桥路327号)摘 要:讨论了A VL EXCITE 的液体动力轴承分析的一些基本理论、方法、结果和影响因素。
关键词:轴承;EHD 分析;载荷;磨损 主要软件:A VL EXCITE1. 前言发动机轴承,包括主轴承、连杆大头轴承等,是发动机长期可靠运转的关键部分之一。
发动机运行时润滑油在高温下工作,其粘度随温度增高而降低,影响油膜承载能力。
判断轴瓦和轴颈可能的润滑状态:液动润滑/临界润滑/干摩擦,避免因干摩擦导致的磨损。
采用有效的结构尺寸和增加刚度,避免过大的结构变形,避免异常的油膜压力分布的出现。
讨论像曲柄销上供油孔位置的确定方法。
2. EXCITE 轴承分析的主要算法简述2.1 ENHD 模块ENHD 模块考虑由于不对中造成的力和力矩的影响,但简化了不对中(倾斜)模型。
对于一定机油粘度,某截面上油膜压力由下面的雷诺方程决定边界条件是:对于车用发动机主轴承或连杆轴承这样宽径比较小的轴承,可求解得到油膜压力为:其中与轴颈不对中有关的系数:一般,在EXCITE 整机振动或噪声计算时,可选用ENHD ,可提高振动噪声的分析精度。
而在详细的轴承分析时,建议使用下面的EHD2分析模型。
2.2 EHD2模块对于轴承磨损等问题的分析,需要用到更加完备的模型。
与ENHD 相比,EHD2充分)()(...)(...),(...cos ...,)2(1fixed shell direction axial ntial circumfere in coordinate z x time t shell journal of velocity ntial circumfere u ityvis height η雷诺方程中: h hp p含机油填充的扩展雷诺方程结果中,可详细了解油膜状态、弹性边界与油膜间的耦合作用、机油流入和流出状态等。
滑动轴承工作原理
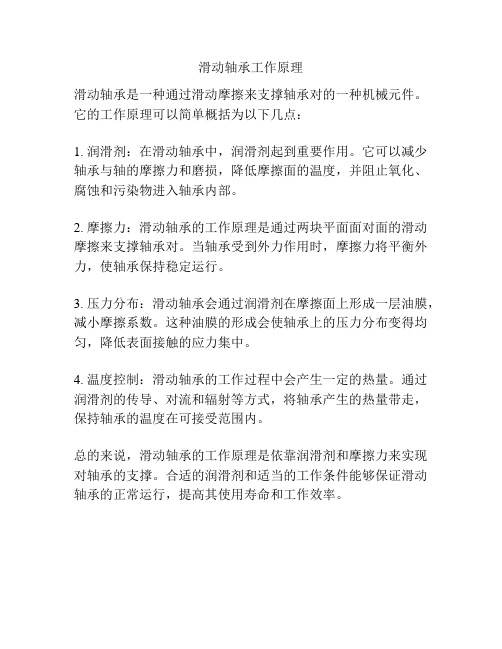
滑动轴承工作原理
滑动轴承是一种通过滑动摩擦来支撑轴承对的一种机械元件。
它的工作原理可以简单概括为以下几点:
1. 润滑剂:在滑动轴承中,润滑剂起到重要作用。
它可以减少轴承与轴的摩擦力和磨损,降低摩擦面的温度,并阻止氧化、腐蚀和污染物进入轴承内部。
2. 摩擦力:滑动轴承的工作原理是通过两块平面面对面的滑动摩擦来支撑轴承对。
当轴承受到外力作用时,摩擦力将平衡外力,使轴承保持稳定运行。
3. 压力分布:滑动轴承会通过润滑剂在摩擦面上形成一层油膜,减小摩擦系数。
这种油膜的形成会使轴承上的压力分布变得均匀,降低表面接触的应力集中。
4. 温度控制:滑动轴承的工作过程中会产生一定的热量。
通过润滑剂的传导、对流和辐射等方式,将轴承产生的热量带走,保持轴承的温度在可接受范围内。
总的来说,滑动轴承的工作原理是依靠润滑剂和摩擦力来实现对轴承的支撑。
合适的润滑剂和适当的工作条件能够保证滑动轴承的正常运行,提高其使用寿命和工作效率。
滑动轴承故障诊断
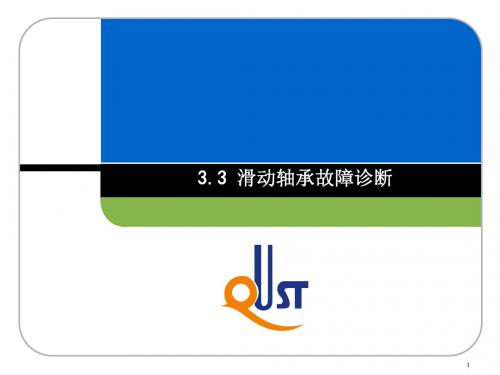
17
3.3 滑动轴承故障诊断
(6)轴承壳体配合松动 轴承壳体配合松动主要是轴承盖与轴承座之间压得不紧,轴承套和轴承 盖之间存在问隙,转子工作时轴瓦松动,影响轴承油膜的稳定性。
这种由于间隙作用引起的振动具有非线性特点,振动频率中既可能存在 倍转速频率的次谐波成分,又可能出现1/i倍转速频率的超谐波成分 (i为正整数)。为了消除轴承松动现象,轴承装配时应使轴承套和轴承 盖之间保持0~30um的过盈配合量。
3.3.3 高速滑动轴承不稳定故障的特征和防治措施
3. 3. 3. 1高速滑动轴承不稳定故障的原因 在化工、石化、电力、钢铁和航空工业部门中使用的许多高性能旋转机 器,多数转子轴承系统属于高速轻载,高速轻载滑动轴承由于设计不良 或使用中多种因素的影响,容易发生油膜不稳定。
不稳定油膜引起转子和轴承较大振动。在某种工作状态下,还会发生高 速滑动轴承的一种特有故障—油膜振荡,它是由油膜力引起的自激振动, 转子轴颈在油膜中的猛烈振动将会直接导致机器零部件的损坏。
b.轴承加工误差
圆柱轴承不圆,多油楔轴承油楔大小和形状不适当,轴承间隙太大或太小, 止推轴承推力盘端面偏摆量超过允许值,瓦块厚薄不匀使各个瓦块上的负 荷分配不均,这些因素可引起轴瓦表面巴氏合金磨损。 采用工艺轴检查,修理轴瓦不规则形状。
12
3.3 滑动轴承故障诊断
c.转子发生大振动
转子由于不平衡、不对中、油膜振荡、流体激振等故障产生的高振幅,将 使轴瓦摩擦、磨损的轴承。转子由于不平衡、不对中、油膜振荡、流体激 振等故障产生的高烧损、刮伤、拉毛。 首先要消除引起大振动的因素,更换已磨损的轴承 止推轴承设计的承载面积过小、压缩机超压、轮盖密封、段间密封或级间 密封损坏,产生过大轴向力,将使瓦块磨损或烧熔。 润滑油供量不足或中断,将引起轴颈与轴承摩擦、烧熔甚至抱轴等事故油 箱空气滤清器或供油系统滤网破损,轴承供油不清洁,造成油孔堵塞、轴 承磨损;油冷却器效果变坏、进油温度高、油的勃度下降、轴承变形、引起 转子振动、擦伤轴承;供油压力过低,不能建立正常油膜;润滑油带水,破 坏油膜,腐蚀轴颈和轴承。 修理或加大油冷却器,更换过滤器,更换润滑油。
测振仪三个参数

测振仪三个参数
位移、速度、加速度都是振动测量的测振仪度量参数,位移的测量能够直接反映轴承应力状况。
通过分析透平机上滑动轴承的位移,可以知道其轴承内轴杆的位置和摩擦情况。
速度反映轴承及其它相关结构所承受的疲劳应力,而这正是导致旋转设备故障的重要原因。
加速度测振仪反映设备内部各种力的综合作用,表达上三者均为正弦曲线,分别有90度,180度的相位差。
现场应用上,对于低速设备(转速小于1000RPM)来说,位移是最好的测量方法。
而那些加速度很小,其位移较大的设备,一般采用折衷的方法,即采用速度测量,对于高速度或高频设备,尽管位移很小,速度也适中,但测振仪加速度却可能很高的设备采用加速度测量是非常重要的手段。
安世亚太:基于ANSYS WB平台的滑动轴承分析工具(一)
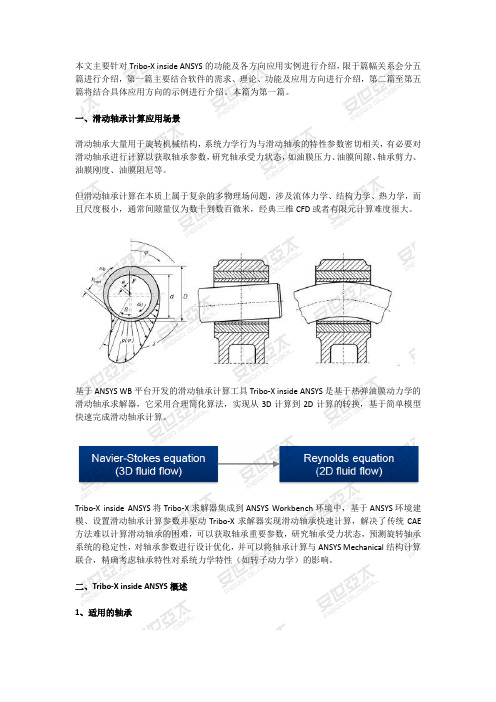
本文主要针对Tribo-X inside ANSYS的功能及各方向应用实例进行介绍,限于篇幅关系会分五篇进行介绍,第一篇主要结合软件的需求、理论、功能及应用方向进行介绍,第二篇至第五篇将结合具体应用方向的示例进行介绍。
本篇为第一篇。
一、滑动轴承计算应用场景滑动轴承大量用于旋转机械结构,系统力学行为与滑动轴承的特性参数密切相关,有必要对滑动轴承进行计算以获取轴承参数,研究轴承受力状态,如油膜压力、油膜间隙、轴承剪力、油膜刚度、油膜阻尼等。
但滑动轴承计算在本质上属于复杂的多物理场问题,涉及流体力学、结构力学、热力学,而且尺度极小,通常间隙量仅为数十到数百微米,经典三维CFD或者有限元计算难度很大。
基于ANSYS WB平台开发的滑动轴承计算工具Tribo-X inside ANSYS是基于热弹油膜动力学的滑动轴承求解器,它采用合理简化算法,实现从3D计算到2D计算的转换,基于简单模型快速完成滑动轴承计算。
Tribo-X inside ANSYS将Tribo-X求解器集成到ANSYS Workbench环境中,基于ANSYS环境建模、设置滑动轴承计算参数并驱动Tribo-X求解器实现滑动轴承快速计算,解决了传统CAE 方法难以计算滑动轴承的困难,可以获取轴承重要参数,研究轴承受力状态,预测旋转轴承系统的稳定性,对轴承参数进行设计优化,并可以将轴承计算与ANSYS Mechanical结构计算联合,精确考虑轴承特性对系统力学特性(如转子动力学)的影响。
二、Tribo-X inside ANSYS概述1、适用的轴承目前版本功能支持的滑动轴承类型如图所示:图-适用于TriboX-inside ANSYS进行分析的轴承(红线框内)2、合理假定油膜间隙远小于轴承尺寸厚度方向压力不变3、理论公式TriboX-inside ANSYS基于TEHD(热弹油膜动力学)的油膜轴承求解器,图-润滑方程图-三维NS方程(CFD)与二维雷诺方程(Tribo-X)计算结果对比●RDE与CFD计算结果存在微小偏差●RDE计算时间明显低于CFD的计算时间4、应用方向Tribo-X求解器集成在ANSYS Workbench环境中,二者优势互补。
- 1、下载文档前请自行甄别文档内容的完整性,平台不提供额外的编辑、内容补充、找答案等附加服务。
- 2、"仅部分预览"的文档,不可在线预览部分如存在完整性等问题,可反馈申请退款(可完整预览的文档不适用该条件!)。
- 3、如文档侵犯您的权益,请联系客服反馈,我们会尽快为您处理(人工客服工作时间:9:00-18:30)。
高很快。由此可知,速度足影响最小油膜厚度的重要 因素,而载荷是影响最大Mim*应力的重要冈素 3结论
通过在1;同转速和不『司载荷条件F分析滑动轴承 的压力分布及Ⅶses应力场,町得到以下结论:
(1)速度变化使油膜、压力昶I应力产生相应的变
化。当速度逐渐增大时,轴承形成油膜的能力逐渐变 强.Ⅻ㈣最大应力逐渐变小,而最大压力也逐渐减
多,求解难度哑人
另外,缸蛮同时具有滑着活塞往复运动方向的变
形及振动,这会影响润滑方程巾的}占鉴裙部与缸套I口J
的相对滑动速度,奉史中暂时忽略其影响
参考文献
:1]谢友柏,摩擦学的三个公』里.第届丧回]_毪受摩擦学学 术会议.西南交通大学,2000 8,
。2:刘琨,缸套活塞环系统摩擦、润滑持陀的研究厦磨损模 型的建立,西安交通大学博十学位论史,谢奠柚指导, 19%。
滑动轴承的应力分析
胡雄海汪久根蒋志浩 (浙江大学机械系杭州310027)
摘要:奉文埘发动机的滑动轴承进行r计算,求解r滑动轴承的雷诺方群、粘度方程、密度方程与载荷方程,得 到丁压力分布与油膜厚度分布.进而通过接触力学分析得到轴承讨内的应力分布。应力分布是影响利料的塑性变形, 并对分析滑动轴承的胶合失效有宴际意义,因此建议用最大Mt**应力来指导滑动轴承的设计。
I飘6砌N时的且主力丹布
圈7 12000N时的压 力分布
(3)二三维Mi”s应力分布 通过1二同转速和不同载倚情况下分析滑动轴承与
轴颈轰面之问的压力及切向力分布,利用弹性力学分
折方法得到接触表面应力分布场.联合切向应力r和
法向力口得到Mi解s应力分布;,轴承衬中的二维Mises
晦力分布,如图8,9.10所示,
魁10 5n—s时的三维血几分布
转速为15 r∥s, 载倚不同时的J直力分布如图ll
图4 5n∥t时的Jt力分布
目5=}(】n∥s时的压力分布
【二)转速为15n∥s.载荷不同叫的压力分布如图 6.7听示,随着载衙的增加,最大流体的压力盲规
律的增大,听最小油膜厚度的变化却无规律,在载荷 较小时.在轴承宽度方向上的压力分布较均匀,而载 荷较大时.油膜压力在轴承宽度方向上分布变化较 大,在中心宽度上,流体压山最大。
d删h即岫椰a甜load即p血册a陀“刊mt}l a fillite di丑em耐d Hmod Th hvdmdⅥl删。口嗍叫m dl蚰i}Ⅲi帅and fⅡm sh8pc are 0btaill。d,
Ⅲ“tIlP山r胛一dirr向orld Mis髓shcss 6eld is cd叫18侧ha刊(m L¨a}mve pf粥u忙d孟t—hudml T|m rTmxim呻Mis幅sⅡt鹦1s s1PF曲c蛐Ily陀laled
图3方程求解流程图
收敛条件的确定:求解此系统耦合方程的解可以 扶侄一曲柄转角位置开始计算(一般从曲柄转角0。开 始).设^(f)、%(f)、B。(F)、P^(£)为f时刻活塞顶端、 底端的偏移占乏速度,r(f)、r.(£)分别为缸套内肇面各 电的径向f矗移及速度。刘于四冲程内
燃叽.曲柄转角转4z为一个特王f、周期.崮此,其正 确的斛麻满足:
《润滑与密封》
万方数据
系起求南于以L每‘组方程都不可能求出其解析 解.凶此对整个系统我们也5{仃期望求出其数值解 对丁眦E每一个力程组.我们现在已有成熟的数值解 法卜8 当我们与虑它仃J间的相互影响而欲解其整个 系统的耦台方程时,便必须通过存解不同方程的程序 问通过变量的反复迭代来进行.直到计并结果满足收 敛条什,因此确定求解方程的合理流程及l恢敛条什便 关系到整个方程组是否可解
载荷为6000N,转速不同时应力的分布如图8,9
断示随着轴颈转速增大,出于流体雎力分布趋于均
4
佑
箭
总之,当戟茼恒定.转速不同,转速越高,最大 压力,乙,。变小,Mis融应力分布图彤中的最大应力也 逐渐变小;当转速不变,载荷变化时,载荷越大,最
大压力逐渐变大,压力分布在低载时沿着Байду номын сангаас嘘方向均
匀分布,重载时变化较大,同时最大Mises应力也升
式中,珊——大气压下室温条件时的润滑油粘 度;∞取0 6:
-浙江省自然科学基金(598039)与国家自然科学基金(59505006)资助项目。 2
《润滑与密封》
万方数据
(2)润滑剂的密度疗程
一P 2 孙mI 1(+-而+篇蕊畿J)
㈦L2)
式中,夫气压室温条件时,润滑油密度取895
(k∥nf)
(3)油膜厚度方程o
【31杨社通.弹性力学.高等教育出收社,1998 6
【4]frⅡh计州lN,ocfl山lerre】e gdlH眦nss,Im灿诅la砌vcllg蛩h¨,…Ⅱ“(p…an小iaJl衙}l(y1‘ellre【丌II【unbⅡ删Hc
luMcati咖.AsMF J¨¨1州1.1978.100(】):12~17。
(T0p卿h)方式作出,如图4~12所示。
2001年第5期
3
万方数据
表!不同载荷的计算结果《轴颈速度】sn∥-)
薮曲最赶『丘力 r f、1 P~l、玳I)
最小油嗅厚j譬
k。。…)
艟大M…应力 k.、(Mh)
s r贮!I壁::
‘6-型
8 19
二753×lu‘、I
40 42
J。。。。。。。。。’一
一
黑|l 茑如 强柏
半尤限体在受到分布压力p(s,£)作用下,女¨图3
所示,在(x,y,。)点产生的应力可由接触儿学计
算…。
/ P8” / :珂3于7“”
/}。l\… /
位置角≠,=”+口,在≠=≯,处压力p=0;
图3半无限体应力II算模掣
aP .
爵2 U'
)法向应力:
如Ⅱ制{蛐;喜:址边8+止掣 华)出出 “Ⅱ搿{Ⅱ芝』』导字L趔+‘丝警刨: 址产舻)出J以… 一 J…
(6)
2计算结果 利用数值计算方法计算滑动轴承的压力分布与油
膜厚度.联立以上各方程(1)一(4)..首先利用数 值计算网格离散化雷诺方程、膜厚方程与载荷方程, 可以得到压力分布与油膜厚度;用有限差分法求解以 上方程.轴承的应力分布在上述基础r由公式(5) 计算得出.求得滑动轴承的i维胁ses应力分布。其 中J.,为无量纲坐标,分别为4x/(耐)、w/口。 输人工况参数如表1所示,计算后得到计算结果,如 表2、3所示
;~n:o睁}'等r'尸哥鼍i,蠢管≯。 j§‰蜉谣鼍氅r鼍专。i擎害争宁
罔8 5m/s时M·啦s应,】场
罔9 30m,-HJ的M-瞄l直力场
s弘 e∞::j l
8;:l:嘲I 鬈:裟i-J■
(1)裁荷恒定为Hx砌N. 转速不同时压力分布如 罔4 5昕示速度增加后, 油膜中动压力分布变得 半缓 速度 人的
{083×10’ 4 q71 xlO 5
55 45 78 22
表3不同卷吸速度的计算结果{载荷6【)【】ON)
习,导致最人Mises应力卜降这刘轴承的抗胶合失
效是有利的 中心宽度处一维Mi州s廊J]分布ml图10 昕示.由罔a J知.愈靠近接触表而。M∽s血力愈大.
5厂——] 而最凡M批雌业力产生于最大流体动地力B域 o
少。 (2)载倚显著影响油膜、压力和Mi¥es监力分布。
载荷越大,形成油膜厚度逐渐变大,最大压力增加很
快,轴承衬中产隹的Mises血力迅速升高。 (3)在油膜的作用r,轴承与轴颈接触表层的最
大Ⅶ*s应力逐渐向内表层移动,低压接触区膻力值较
低,而轴承接触商外表屡Ⅶ*s直力分布密集,愈接近 接触表面.Mises应力值也逐渐提高。 (下转第8页)
方程求解流程:输入韧值(活塞副始位移、速 度,燃烧室气体压力分布;缸叁韧时位移及速度), 求解润滑方程得出油膜』t力分布及摩擦力,将油膜压 力J盘唪擦JJ代人jS塞动力学方程和缸套动力学方程求 解得活寒裙而各点及缸套内壁面各点处位移及速度, 将活塞裙面各点及缸套内壁面各点处位移及速度代人 油噗J7度及挤压膜项公式求得油膜厚度及挤压油膜 顾,^由修正后的油膜厚度及挤压油膜项进行缸食一 活塞动力润滑计算,如此反复迭代,直到收敛。流程 如图3所示
P,(f)=P,(f+塑).“(,)_n(,+塑)
P,(f)=e巾+堑).cf_㈩:P 6(,+塑)
“f)一吼t+警¨Ⅳ)一(f+警)
以上条件可作为计算的收敛条件,
如果考虑曲轴转r系统动力学的影响,需加人曲
轴转子动力学力程厦主轴承油膜润滑方程、其中卞轴
承油膜为曲轴运动与缸套运动问的耦合件,求解思路
同上述相近,但整个^程组的规模机欠,收敛条件增
maxlⅡu瑚str瞄s诂p叫删tn 诵山山e孵i珊“ng fduIe 0f beariIlg bush幅;tIlerdore t}le
k u9甜【o印1小tk捌印d JoLmlaIⅫ“茚-
K e11_or凼:J伽咖dⅨm自晖Pl髑蛐tⅨ曲曲Ilt;0n Sh璐neH sei迥l血罄
滑动轴承广泛应用在各种仪器设备,特别在高速、 重载、高精度和人转矩的场合。轴承的失效如磨损、 刮伤.牯着、胶合等失效形式经常发生,如图1常见 的粘着失效形式。尤其是发动机曲轴系中的滑动轴承 是存重载、润滑不良和高温条件下运行,轴瓦胶合失 效较为严重。近几年对滑动轴承应力分布的分析研究 比较少,众多学者主要集中在滑动轴承的粗糙度、变 形、非牛顿体等方面进行研究。,wmg和z}—#“针对 弹性支撑轴承的--二维热弹流体润滑研究,分析热弹变 形对轴承性能的影响,指出热弹变形对轴承性能的影 响比热变形大;Gn—Ilrai粕和PrakasH“学虑有限长含油 轴承的表面粗糙度的冈素,认为粗糙度的类型对含油 轴承的性能影响较大,横向粗糙度使轴承承载能力和 孽擦力增加,纵向粗糙度使摩擦力和摩擦系数有细微 的增加,偏位角随粗糙度的变化而不显著;Gecim”J在 多级通用的非牛顿体润滑油对轴承性能的影响文中阐 述了采用牛顿体和非牛顿模型计算功率损失、宽径比、 剪应率的稳定性等参数的差异,许多条件下不能简单 用牛顿体模型替代。本文分析·实际发动机应力场, 联立滑动轴承的雷诺方程、粘度和密度方程的求解, 并经迭代计算,得到滑动轴承的压力分布与油膜厚度 分布的三维曲线图,进而分析得到轴承衬内的应力分 布,材料塑性变形与应力分布有关。通过分析,寻找 滑动轴承的失效类型和主要原因,并比较在不同转速 和不同载荷情况下的Mises应力分布形式,从而得出轴