材料异常工时评估规范(含表格)
生产线_异常工时明细纪录表_柏拉图分析
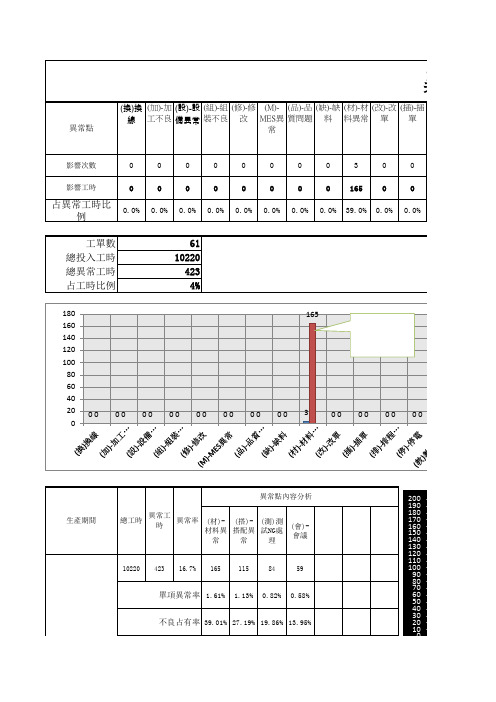
200 190 180 170 160 150 140 130 120 110 100 90 80 70 60 50 40 30 20 10 0
0 累計不良占有率
39.0% 66.2% 86.1% 100.0%
(材)-材料異常
異常時間
日期
上線機種
問題
異常工時明細
(排)-排 (停)-停 (教)教 (掃)-掃 (新)-新 (搭)-搭 (E)- (試)-試 (測)測 (N (準)-上 (會)-會 (作)-作 (出)-人 程異動 電 育訓練 除 人作業 配異常 ECN/R 產 試NG )NOT 線準備 議 業落後 力調出 D 處理 ES
0 0 0.0%
0 0 0.0%
0 0 0.0%
0 0 0.0%
0 0 0.0%
2 115 27.2%
0 0 0.0%
0 0 0.0%
1 84 19.9%
0 0 0.0%
0 0 0.0%
3 59 13.9%
0 0 0.0%
0 0 0.0%
115
84 59
0
00
00
00
2
00
00
1
00
00
3
00
00
00
3
00
பைடு நூலகம்
00
00
00
異常點內容分析 生產期間 總工時 異常工 異常率 (材)- (搭)- (測)測 時 (會)材料異 搭配異 試NG處 會議 常 常 理
10220
423
16.7%
165
115
84
59
單項異常率 1.61%
1.13%
0.82%
0.58%
异常工时管理规范(含表格)
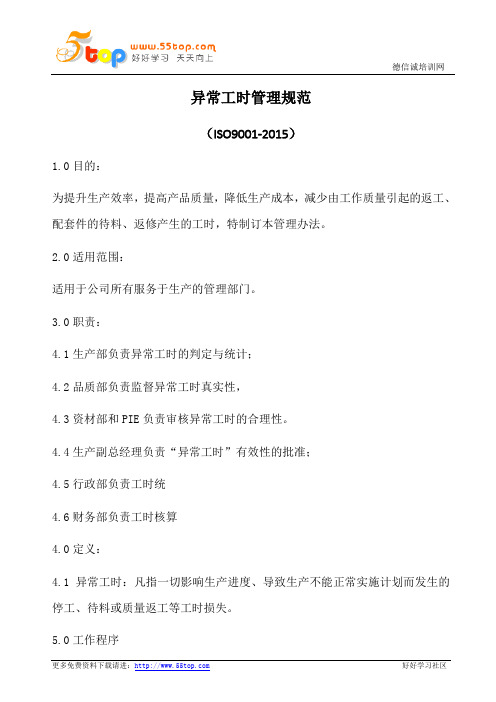
异常工时管理规范(ISO9001-2015)1.0目的:为提升生产效率,提高产品质量,降低生产成本,减少由工作质量引起的返工、配套件的待料、返修产生的工时,特制订本管理办法。
2.0适用范围:适用于公司所有服务于生产的管理部门。
3.0职责:4.1生产部负责异常工时的判定与统计;4.2品质部负责监督异常工时真实性,4.3资材部和PIE负责审核异常工时的合理性。
4.4生产副总经理负责“异常工时”有效性的批准;4.5行政部负责工时统4.6财务部负责工时核算4.0定义:4.1异常工时:凡指一切影响生产进度、导致生产不能正常实施计划而发生的停工、待料或质量返工等工时损失。
5.0工作程序5.1异常的处理5.1.1生产部按生产计划排期提前到仓库领料并安排做首件并量产。
5.1.2生产部在生产过程中发现产品、物料与要求不符,生产的成品达不到标准要求或来料无法使用等现象,5分钟内上报部门负责人、工程、资材部、品质部等相关人员确认。
5.1.3工程部、品质部确认异常可接受,通知生产继续生产,如确认异常不能接收,则由生产部或品质IPQC在接到需特别加工或退货信息10分钟内开出《品质异常处理单》进行跟踪处理。
5.1.4经品质分析,给出初步分析结果,结果为工艺问题,设计问题,来料问题。
5.1.5由品质分析,如果需要返工或改变工艺则由工程部更改样品给品质部确认,品质判定方案可行后,工程必须在现场跟进指导产线员工作业方法。
品质判定是否符合要求,工程等员工生产出2件合格品后方可离开现场,品质部跟踪监控过程确认。
5.1.6如果确认是来料问题,按照解决方案的意见,找供应商沟通协助处理或由我司加工挑选扣除供应商相应费用并要求在一个工作日内对来料问题给予回复处理意见(临时解决办法),生产部要给予相应的配合,和支持。
同时品质应协助。
5.1.7如果由于制程异常原因造成的,则由相关责任部门协助处理。
5.1.8待工,返工工时,由生产线记录,并填定在《车间导常工时申报表》,并在当天的《生产日报表》上备注。
异常工时评估规范
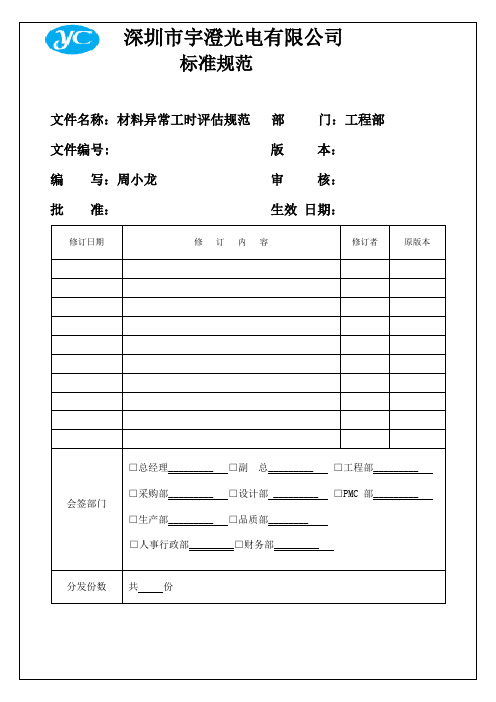
标准规范
文件名称:材料异常工时评估规范部 门:工程部
文件编号:版本:
编 写:周小龙审 核:
批 准:生效日期:
修订日期
修 订 内 容
修订者
原版本
会签部门
□总经理_________□副 总_________□工程部_________
□采购部_________□设计部_________□PMC部_________
5.3、需全检后上线的材料异常工时损耗计算方法:全检每pcs材料耗费时间*来料总数
5.4、全检后需返工的材料异常工时损耗计算方法:全检每pcs材料耗费时间*来料总数+不良率*来料总数*返修工站标准工时总和*5
举例:因40F18的导光板来料1000pcs,来料不良10%,导致半成品需全检后上线,则工时损耗为:全检每pcs半成品的时间*1000pcs+#43;贴组件标准工时)*5
6、相关表单:
《材料异常追踪表》
《异常工时确认表》
《效率工时表》
□生产部_________□品质部________
□人事行政部_________□财务部_________
分发份数
共份
1、
目的:规范来料异常的处理,使来料异常工时评估有据可依,提升来料异常处理效率,降低因来料异常导致的工时损耗对我司各部门的影响。
2、范围:我司所有来料异常导致我司工时损耗后的工时损耗评估。
3、权责:生产部:按产线实际工时损耗填写《异常工时确认表》,或按本规范计算异常工时损耗并填写相关表格。
工程部:制作出标准的异常工时评估规范,并按此规范复核生产部计算出的工时损耗。
品质部:按《材料异常追踪表》上工程复核的工时损耗项。
采购部:根据品质开出的《扣款单》向供应商执行对账扣款。
标准工时测定制定规范(含表格)
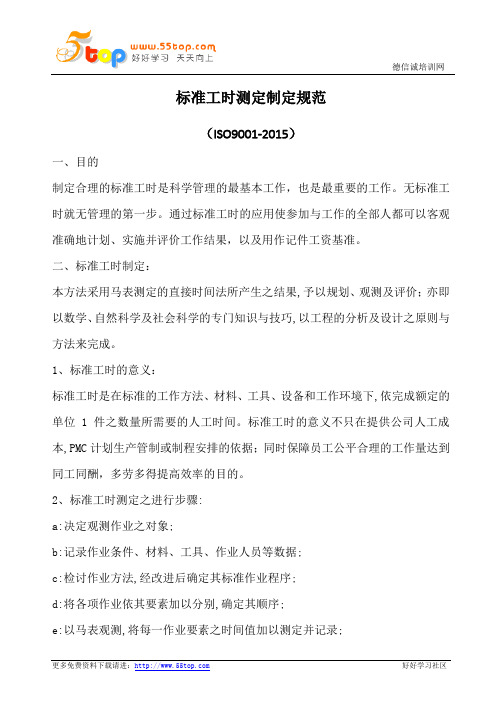
标准工时测定制定规范(ISO9001-2015)一、目的制定合理的标准工时是科学管理的最基本工作,也是最重要的工作。
无标准工时就无管理的第一步。
通过标准工时的应用使参加与工作的全部人都可以客观准确地计划、实施并评价工作结果,以及用作记件工资基准。
二、标准工时制定:本方法采用马表测定的直接时间法所产生之结果,予以规划、观测及评价;亦即以数学、自然科学及社会科学的专门知识与技巧,以工程的分析及设计之原则与方法来完成。
1、标准工时的意义:标准工时是在标准的工作方法、材料、工具、设备和工作环境下,依完成额定的单位1件之数量所需要的人工时间。
标准工时的意义不只在提供公司人工成本,PMC计划生产管制或制程安排的依据;同时保障员工公平合理的工作量达到同工同酬,多劳多得提高效率的目的。
2、标准工时测定之进行步骤:a:决定观测作业之对象;b:记录作业条件、材料、工具、作业人员等数据;c:检讨作业方法,经改进后确定其标准作业程序;d:将各项作业依其要素加以分别,确定其顺序;e:以马表观测,将每一作业要素之时间值加以测定并记录;f:迭计要素作业时间并求其循环时间;g:评定被观测者之作业速度,技术,努力度修正观测值,以求基本时间;h:决定计算放宽率,并最后决定标准工时。
3、实际工作时间说明a、工作时间:上班时间:08:00~20:30总时间:750min用餐/中休:150min实际工作时间:600min=10Hrb、宽放时间:因各工作岗位性质、环境、作业条件和作业范围、作业姿势、作业的精细不同,为了公平合理的测评标准工时,需根据不同评价补偿宽放时间如;(1)补偿根据作业人员的去卫生间,喝水,擦汗等个人的需要中断作业的时间,个人的因素认定为是属于标准的是处理生理需求的行为;(2)补偿根据作业环境,作业条件的情况,因体力精神上有些吃力发生的中断、犹豫,降低速度的时间;(3)使人疲劳的作业环境有热、冷、照明、气体、灰尘、噪音、振动等等,作业条件有作业范围、作业姿势、作业的精细等等。
标准工时制定规范(含表格)
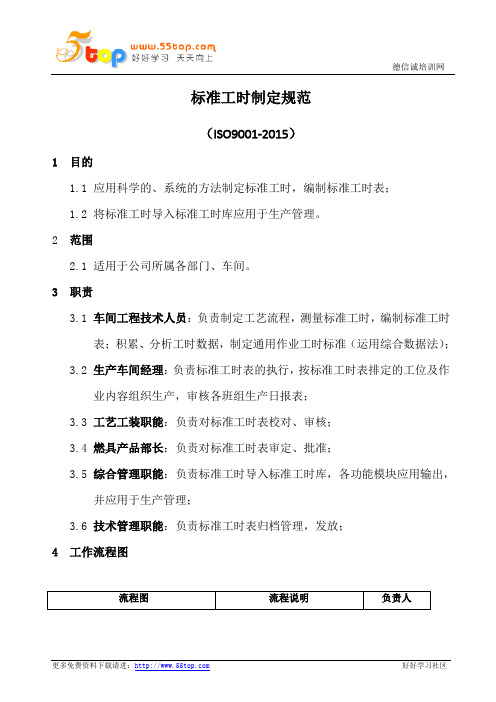
标准工时制定规范(ISO9001-2015)1目的1.1应用科学的、系统的方法制定标准工时,编制标准工时表;1.2将标准工时导入标准工时库应用于生产管理。
2范围2.1适用于公司所属各部门、车间。
3职责3.1车间工程技术人员:负责制定工艺流程,测量标准工时,编制标准工时表;积累、分析工时数据,制定通用作业工时标准(运用综合数据法);3.2生产车间经理:负责标准工时表的执行,按标准工时表排定的工位及作业内容组织生产,审核各班组生产日报表;3.3工艺工装职能:负责对标准工时表校对、审核;3.4燃具产品部长:负责对标准工时表审定、批准;3.5综合管理职能:负责标准工时导入标准工时库,各功能模块应用输出,并应用于生产管理;3.6技术管理职能:负责标准工时表归档管理,发放;4工作流程图5工作程序5.1标准工时制定原则5.1.1在产产品:所有在一年内生产的产品必须制定相应品名的标准工时,超过3年未生产产品的标准工时表可以不维护更新,但保留旧版电子档,以备查看;5.1.2新增产品:新产品试产时需制定一个临时工艺流程图,在批量生产后5个工作日须发行新版正式标准工时表;新版标准工时表版本号统一定为“00”版;5.1.3工艺变更:当生产工艺发生变更时,须调整相应变更工位的工时数据,并升级发行新的标准工时表,版本号为原版本号加“1”,并在表上相应位置注明升级原因。
例:原版为“00”版,升级后发行版本为“01”版,以此类推。
5.1.4制程改善:当对生产制程进行改善时,改善成果将通过“标准工时”的降低,“线平衡率”的提高来体现;改善完成后须升级标准工时表,以进行相应措施的固化;5.1.5与实际差异过大:当正式版标准工时表投入使用后,若发现与生产实际存在较大差异时,需要就部分或全部工位进行重新观测分析,再升级发行新版标准工时表;差异过大的标准为:在去除外部影响与内部问题后的产出工时与投入工时的差异超过10%;5.2数据测量标准工时制定初期阶段以秒表法为主,待积累了大量的作业单元数据进行分析后,再运用综合数据法制定常用作业的工时标准参数表,以在后期制定标准工时时直接取用,提高制作效率。
异常工时冾取管理规范

异常工时冾取管理规范1.目的通过量化标准产能配置,摒弃一切造成产能低下的外在因素,从而达到提高效率、降低成本的目的。
2.使用范围本规范适用于制造事业部。
3.定义3.1.1标准产能:将线平衡损失降至最低的状况下,按照标准人力制程配置资源,单小时所能达到的最佳产能3.1.2标准工时:在适宜的操作条件下用最合适的操作方法以普通熟练工人的正常速度完成标准动作所需要的时间,一般包含生理宽放、疲劳宽放、管理宽放,本标准动作时间必须通过PTS法获得,若用秒表粗略计时估算,必须扣除故延同时将浪费动作时间扣除,同时物资、工装需提前配置至要求区标准工时=标准动作时间*(1+生理宽放+疲劳宽放+管理宽放);3.1.3标配人力:在特定工艺流程下,通过执行标准动作及手法,按照标准产能生产所需配备的人力,包含直接人力及间接人力;3.1.4直接人力:在特定流程下,直接作用于标准动作的人力之和;3.1.5间接人力:在特定流程下,直接服务于直接人力的人力之和,包含但不限于服务类人力;3.1.6直接作业时间:在特定流程下,有直接人力标准动作所产能的时间之和;3.1.7间接作业时间:在特定流程下,有间接人力服务于直接人力所产生的时间之和;3.1.8生产节拍:在特定工艺流程下,完成单个工序的最长耗时;3.1.9WIP: work in process (在制品),自投入加工开始至OQC验收合格入库之前的所有产品均属于在制品即WIP产品;3.1.10Rework:(重工)首先逆向特定工艺流程,通过排除非需求条件,然后在正常工艺流程下重新复原的过程;任何状况下的Rework都必须有相关人员提供Rework流程图及Rework工时;3.1.11瓶颈时间:作业动作所需消耗最长的动作,生产线作业时最长的工站的节拍称之为瓶颈,所需的时间成为瓶颈时间。
流水线产出的速度取决于瓶颈工时;单小时产能粗略算法=3600/瓶颈节拍时间;3.1.12线平衡损失:作业动作之间由于作业量的不均衡造成的损失,(正常工序因瓶颈工序所造成的损失时间的百分比);3.1.13宽放:基于对人因工程,环境工程以及人文关怀考量,将标准作业动作在原基础之上放大一定倍数,宽放分为三类:生理宽放(5%),作业宽放(10%),管理宽放(15%)。
异常工时责任划分与责任判定标准参照表

产品研发中心开发的产品在分公司试产产生的异常工时(记录异常工时需要注明)
正常费用补偿、 只做统计不考核
产品结构不良
产品工程部 因产品结构改良设计、产品结构不良等造成的异常;
工程问题
开发遗留问题点-开发部
开发部
研发部负责开发的产品,其产品未释放,在产品开发过程中遗留未能解决的问题造成的 异常(《新产品试(生)产问题改善一览表》中记录的且未改善完成问题点)
异常工时责任划分与责任判定标准参照表
异常大类 异常小类
具体细项
责任部门
异常产生原因概述
备注
换产品工时
换产品工时
生产部
生产线切换产品生产造成多能工岗位训练
人力闲置-总装部
生产部
产品切换,导致多余人力无法外借
人力闲置-综合部(取消)
生产部
综合部招人多出公司配置人员
人员不足-总装部
生产部
人员离职、请假、旷工、自离导致生产时人力不足
人
人员状态
人员内部借调-产品工程部 人员内部借调-开发部 人员内部借调-PMC部
产品工程部 开发部 PMC部
产品工程部从总装部借调直接人员 开发部从总装部借调直接人员 PMC部从总装部借调直接人员
人员内部借调-IE部
IE部
IE部从总装部借调直接人员
塑胶件缺料(发外)
PMC部
塑胶件供应不及时,供应商为PMC部发外厂家
排程提前-主计划员
主计划员 突然的大单/急货而总装提前生产造成的缺料
排程提前-PMC
PMC部
大单/急货而总装提前生产,主计划已提前通知,造成的缺料
物料结构缺陷或规格变更-产品 工程部
产品工程部
物料规格临时变更等造成的异常(如﹕来料需做加工才能上线等)
车间异常工时方案
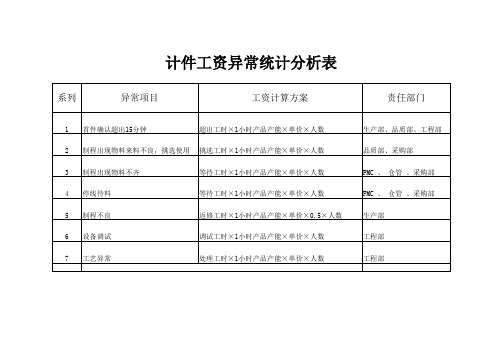
异常项目
首件确认超出15分钟 制程出现物料来料不良,挑选使用 制程出现物料不齐 停线待料 制程不良 设备调试 工艺异常
工资计算方案
超出工时×1小时产品产能×单价×人数 挑选工时×1小时产品产能×单价×人数 等待工时×1小时产品产能×单价×人数 等待工时×1小时产品产能×单价×人数 返修工时×1小时产品产能×单价×0.5×人数 调试工时×1小时产品产能×单价×人数 处理工时×1小时产品产能×单价×人数
责任部门
生产部、品质部、工程部 品质部、采购部 PMC 、 仓管 、采购部 PMC 、 仓管 、采购部 生产部 工程部 工程部
- 1、下载文档前请自行甄别文档内容的完整性,平台不提供额外的编辑、内容补充、找答案等附加服务。
- 2、"仅部分预览"的文档,不可在线预览部分如存在完整性等问题,可反馈申请退款(可完整预览的文档不适用该条件!)。
- 3、如文档侵犯您的权益,请联系客服反馈,我们会尽快为您处理(人工客服工作时间:9:00-18:30)。
材料异常工时评估规范
(ISO9001-2015)
1、目的:
规范来料异常的处理,使来料异常工时评估有据可依,提升来料异常处理效率,降低因来料异常导致的工时损耗对我司各部门的影响。
2、范围:
公司所有来料异常导致我司工时损耗后的工时损耗评估。
3、权责:
生产部:按产线实际工时损耗填写《异常工时确认表》,或按本规范计算异常工时损耗并填写相关表格。
工程部:制作出标准的异常工时评估规范,并按此规范复核生产部计算出的工时损耗。
品质部:按《材料异常追踪表》上工程复核的工时损耗项。
采购部:根据品质开出的《扣款单》向供应商执行对账扣款。
财务部:执行对供应商的扣款。
人事部:根据《异常工时确认表》上工程复核的个人工时损耗计算员工计时工资。
4、定义:
4.1、异常工时:一切影响生产进度,导致生产不能正常实施计划而发生的停工、待料或质量返工等工时损失,在生产绩效考核范畴内,都被定义为生产异常工时。
4.2、材料异常工时:因材料导致的异常工时。
4.3、返修工时损耗:用于返修因材料不良造成成品不良的产品所耗费的工时,返修时使用的时间是做正常品的2.5倍时间,由于此时的2.5倍做正常品的时间并没有用来做正常品,而是被用来返修了,所以没有产能,因此返修工时其实是使用了5倍正常品的时间。
算法为:标准工时*
5.
4.4、返修时的检测工时损耗:如4.3中所述,由于返修并没有给我司带来收益,所以返修的检测工时损耗实际为检测标准工时*2.
5、材料异常工时计算方法:
5.1、造成返修的材料异常工时损耗计算方法:损耗工时=返修工站标准工时总和*5+检测的标准工时*2+其他损耗时间
举例:若38F06因扩散按压白点导致成品返修,那么损耗工时为:3.8寸产品贴膜标准工时*5+3.8寸产品检测标准工时*2
若38F06因扩散按压白点导致可退返修,那么损耗工时为:3.8寸产品贴膜标准工时*5+3.8寸产品检测标准工时*2+打包时间+装箱时间.
5.2、未造成返修的材料异常工时损耗计算方法:每pcs材料耗费的工时*材料不良总数
举例:若任意一型号扩散来料保护膜不易离型50%,每pcs比正常扩散撕离保
护膜多耗时5s,则此时损耗工时为扩散来料总数*50%*5s
5.3、需全检后上线的材料异常工时损耗计算方法:全检每pcs材料耗费时间*来料总数
5.4、全检后需返工的材料异常工时损耗计算方法:全检每pcs材料耗费时间*来料总数+不良率*来料总数*返修工站标准工时总和*5
举例:因40F18的导光板来料1000pcs,来料不良10%,导致半成品需全检后上线,则工时损耗为:全检每pcs半成品的时间*1000pcs+10%*1000pcs*(组装导光板标准工时+贴FPC胶标准工时+贴组件标准工时)*5
6、相关表单:
《材料异常追踪表》
《异常工时确认表》
《效率工时表》
效率工时表.xls
异常工时记录表.xl
s
月异常工时统计表.
xl s。