变频器多传控制方案
变频器多段速运行控制(可打印修改)
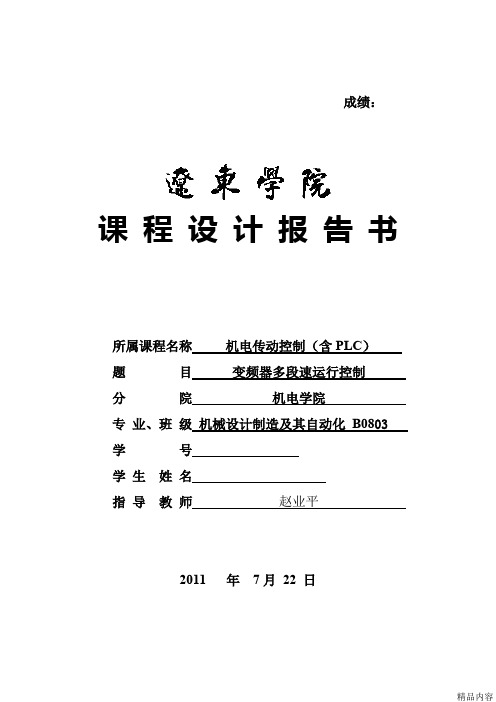
机电传动控制
MM440 变频器的六个数字输入端口(DIN1~ DIN6),通过 P0701~P0706 设 置实现多频段控制。每一频段的频率分别由 P1001~P1015 参数设置,最多可实 现 15 频段控制,各个固定频率的数值选择见表 2-1。在多频段控制中,电动机 的转速方向是由 P1001~P1015 参数所设置的频率正负决定的。六个数字输入端 口,哪一个作为电动机运行、停止控制,哪些作为多段频率控制,是可以由用 户任意确定的,一旦确定了某一数字输入端口的控制功能,其内部的参数设置 值必须与端口的控制功能相对应。
6 总结
通过这次课程设计让我学会了 plc 基本的编程方法,对 plc 的基本原理和 使用方法有了更深刻的理解。在对理论的运用当中,提高了我们的工程素质, 在没有做课程设计以前,我们对知道的掌握都是思想上的,对一些细节不加重 视,当我们自己想出来的程序应用到 plc 中的时候,,不是不能运行,就是运行 的结果和要求与结果不符合。能通过解决一个个在调试中出现的问题,我们对 plc 的理解得到了加强,看到了时间与理论的差距。
1 0 1 0 1 0 1 0
对应频率所 设置的参数
P1001 P1002 P1003 P1004 P1005 P1006 P1007
频率/Hz
10 20 50 30 -10 -20 -50 0
表 3-1
5
精品内容
辽东学院课程设计报告书
机电传动控制
参数号
P0003 P0004 P0700 P0003 P0004 P0701 P0702 P0703 P0704 P0003 P0004 P1000 P0003 P0004 P1001 P1002 P1003 P1004 P1005 P1006 P1007
多传变频器的工作原理
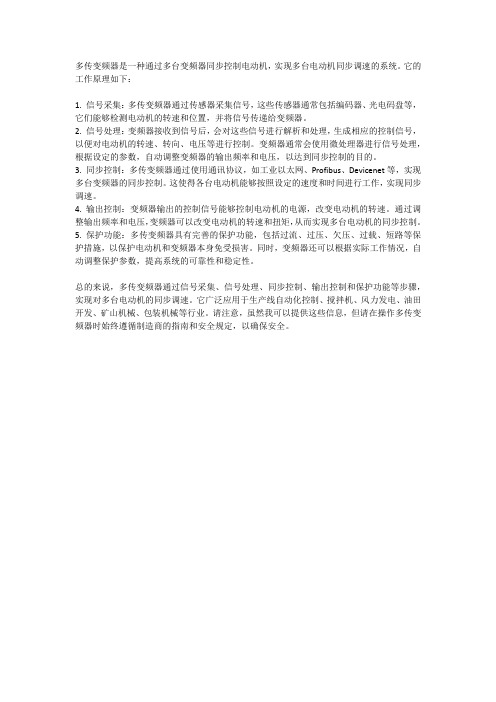
多传变频器是一种通过多台变频器同步控制电动机,实现多台电动机同步调速的系统。
它的工作原理如下:
1. 信号采集:多传变频器通过传感器采集信号,这些传感器通常包括编码器、光电码盘等,它们能够检测电动机的转速和位置,并将信号传递给变频器。
2. 信号处理:变频器接收到信号后,会对这些信号进行解析和处理,生成相应的控制信号,以便对电动机的转速、转向、电压等进行控制。
变频器通常会使用微处理器进行信号处理,根据设定的参数,自动调整变频器的输出频率和电压,以达到同步控制的目的。
3. 同步控制:多传变频器通过使用通讯协议,如工业以太网、Profibus、Devicenet等,实现多台变频器的同步控制。
这使得各台电动机能够按照设定的速度和时间进行工作,实现同步调速。
4. 输出控制:变频器输出的控制信号能够控制电动机的电源,改变电动机的转速。
通过调整输出频率和电压,变频器可以改变电动机的转速和扭矩,从而实现多台电动机的同步控制。
5. 保护功能:多传变频器具有完善的保护功能,包括过流、过压、欠压、过载、短路等保护措施,以保护电动机和变频器本身免受损害。
同时,变频器还可以根据实际工作情况,自动调整保护参数,提高系统的可靠性和稳定性。
总的来说,多传变频器通过信号采集、信号处理、同步控制、输出控制和保护功能等步骤,实现对多台电动机的同步调速。
它广泛应用于生产线自动化控制、搅拌机、风力发电、油田开发、矿山机械、包装机械等行业。
请注意,虽然我可以提供这些信息,但请在操作多传变频器时始终遵循制造商的指南和安全规定,以确保安全。
变频器多速控制研究
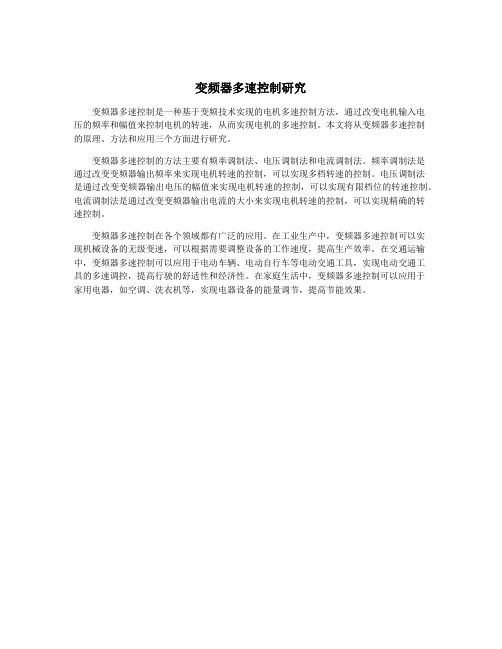
变频器多速控制研究
变频器多速控制是一种基于变频技术实现的电机多速控制方法,通过改变电机输入电
压的频率和幅值来控制电机的转速,从而实现电机的多速控制。
本文将从变频器多速控制
的原理、方法和应用三个方面进行研究。
变频器多速控制的方法主要有频率调制法、电压调制法和电流调制法。
频率调制法是
通过改变变频器输出频率来实现电机转速的控制,可以实现多档转速的控制。
电压调制法
是通过改变变频器输出电压的幅值来实现电机转速的控制,可以实现有限档位的转速控制。
电流调制法是通过改变变频器输出电流的大小来实现电机转速的控制,可以实现精确的转
速控制。
变频器多速控制在各个领域都有广泛的应用。
在工业生产中,变频器多速控制可以实
现机械设备的无级变速,可以根据需要调整设备的工作速度,提高生产效率。
在交通运输中,变频器多速控制可以应用于电动车辆、电动自行车等电动交通工具,实现电动交通工
具的多速调控,提高行驶的舒适性和经济性。
在家庭生活中,变频器多速控制可以应用于
家用电器,如空调、洗衣机等,实现电器设备的能量调节,提高节能效果。
如何通过RS-485控制多台变频器
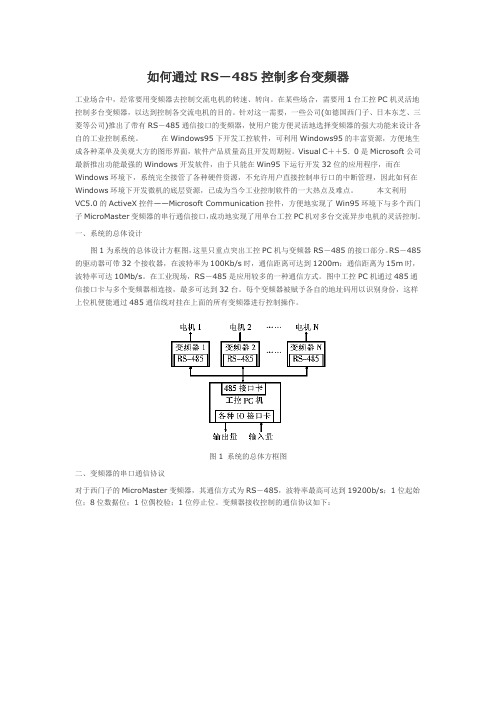
如何通过RS-485控制多台变频器工业场合中,经常要用变频器去控制交流电机的转速、转向。
在某些场合,需要用1台工控PC机灵活地控制多台变频器,以达到控制各交流电机的目的。
针对这一需要,一些公司(如德国西门子、日本东芝、三菱等公司)推出了带有RS-485通信接口的变频器,使用户能方便灵活地选择变频器的强大功能来设计各自的工业控制系统。
在Windows95下开发工控软件,可利用Windows95的丰富资源,方便地生成各种菜单及美观大方的图形界面,软件产品质量高且开发周期短。
Visual C++5.0是Microsoft公司最新推出功能最强的Windows开发软件,由于只能在Win95下运行开发32位的应用程序,而在Windows环境下,系统完全接管了各种硬件资源,不允许用户直接控制串行口的中断管理,因此如何在Windows环境下开发微机的底层资源,已成为当今工业控制软件的一大热点及难点。
本文利用VC5.0的ActiveX控件——Microsoft Communication控件,方便地实现了Win95环境下与多个西门子MicroMaster变频器的串行通信接口,成功地实现了用单台工控PC机对多台交流异步电机的灵活控制。
一、系统的总体设计图1为系统的总体设计方框图,这里只重点突出工控PC机与变频器RS-485的接口部分。
RS-485的驱动器可带32个接收器,在波特率为100Kb/s时,通信距离可达到1200m;通信距离为15m时,波特率可达10Mb/s。
在工业现场,RS-485是应用较多的一种通信方式。
图中工控PC机通过485通信接口卡与多个变频器相连接,最多可达到32台。
每个变频器被赋予各自的地址码用以识别身份,这样上位机便能通过485通信线对挂在上面的所有变频器进行控制操作。
图1 系统的总体方框图二、变频器的串口通信协议对于西门子的MicroMaster变频器,其通信方式为RS-485,波特率最高可达到19200b/s;1位起始位;8位数据位;1位偶校验;1位停止位。
变频器多段速控制设置及接线说明
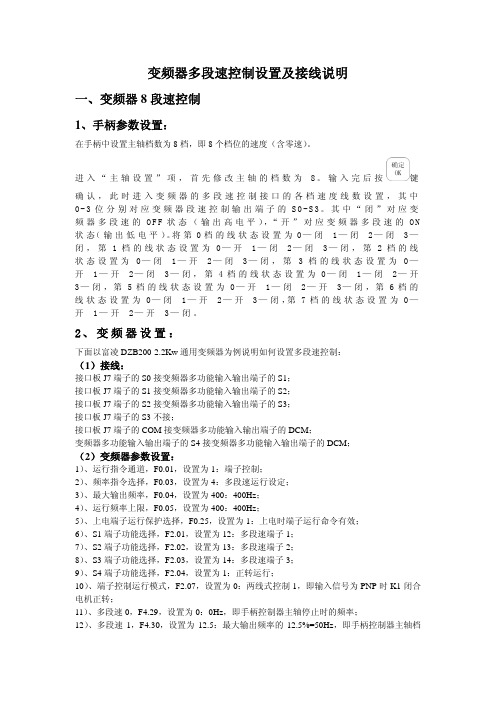
变频器多段速控制设置及接线说明一、变频器8段速控制1、手柄参数设置:在手柄中设置主轴档数为8档,即8个档位的速度(含零速)。
进入“主轴设置”项,首先修改主轴的档数为8。
输入完后按键确认,此时进入变频器的多段速控制接口的各档速度线数设置,其中0-3位分别对应变频器段速控制输出端子的S0-S3。
其中“闭”对应变频器多段速的O F F状态(输出高电平),“开”对应变频器多段速的O N 状态(输出低电平)。
将第0档的线状态设置为0—闭1—闭2—闭3—闭,第1档的线状态设置为0—开1—闭2—闭3—闭,第2档的线状态设置为0—闭1—开2—闭3—闭,第3档的线状态设置为0—开1—开2—闭3—闭,第4档的线状态设置为0—闭1—闭2—开3—闭,第5档的线状态设置为0—开1—闭2—开3—闭,第6档的线状态设置为0—闭1—开2—开3—闭,第7档的线状态设置为0—开1—开2—开3—闭。
2、变频器设置:下面以富凌DZB200-2.2Kw通用变频器为例说明如何设置多段速控制:(1)接线:接口板J7端子的S0接变频器多功能输入输出端子的S1;接口板J7端子的S1接变频器多功能输入输出端子的S2;接口板J7端子的S2接变频器多功能输入输出端子的S3;接口板J7端子的S3不接;接口板J7端子的COM接变频器多功能输入输出端子的DCM;变频器多功能输入输出端子的S4接变频器多功能输入输出端子的DCM;(2)变频器参数设置:1)、运行指令通道,F0.01,设置为1:端子控制;2)、频率指令选择,F0.03,设置为4:多段速运行设定;3)、最大输出频率,F0.04,设置为400:400Hz;4)、运行频率上限,F0.05,设置为400:400Hz;5)、上电端子运行保护选择,F0.25,设置为1:上电时端子运行命令有效;6)、S1端子功能选择,F2.01,设置为12:多段速端子1;7)、S2端子功能选择,F2.02,设置为13:多段速端子2;8)、S3端子功能选择,F2.03,设置为14:多段速端子3;9)、S4端子功能选择,F2.04,设置为1:正转运行;10)、端子控制运行模式,F2.07,设置为0:两线式控制1,即输入信号为PNP时K1闭合电机正转;11)、多段速0,F4.29,设置为0:0Hz,即手柄控制器主轴停止时的频率;12)、多段速1,F4.30,设置为12.5:最大输出频率的12.5%=50Hz,即手柄控制器主轴档位1对应的频率,可根据实际需要设置为不同的频率;13)、多段速2,F4.31,设置为25:最大输出频率的25%=100Hz,即手柄控制器主轴档位2对应的频率,可根据实际需要设置为不同的频率;14)、多段速3,F4.32,设置为37.5:最大输出频率的37.5%=150Hz,即手柄控制器主轴档位3对应的频率,可根据实际需要设置为不同的频率;15)、多段速4,F4.33,设置为50:最大输出频率的50%=200Hz,即手柄控制器主轴档位4对应的频率,可根据实际需要设置为不同的频率;16)、多段速5,F4.34,设置为62.5:最大输出频率的62.5%=250Hz,即手柄控制器主轴档位5对应的频率,可根据实际需要设置为不同的频率;17)、多段速6,F4.35,设置为75:最大输出频率的75%=300Hz,即手柄控制器主轴档位6对应的频率,可根据实际需要设置为不同的频率;18)、多段速7,F4.36,设置为100:最大输出频率的100%=400Hz,即手柄控制器主轴档位7对应的频率,可根据实际需要设置为不同的频率;二、变频器启/停(2段速)控制1、手柄参数设置:在手柄中设置主轴档数为2档,即2个档位的速度(启动和停止)。
多台变频器同步控制的接线和方法
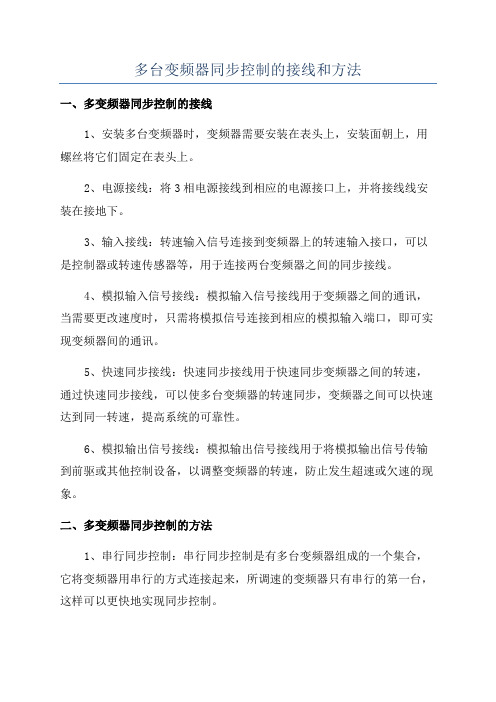
多台变频器同步控制的接线和方法
一、多变频器同步控制的接线
1、安装多台变频器时,变频器需要安装在表头上,安装面朝上,用螺丝将它们固定在表头上。
2、电源接线:将3相电源接线到相应的电源接口上,并将接线线安装在接地下。
3、输入接线:转速输入信号连接到变频器上的转速输入接口,可以是控制器或转速传感器等,用于连接两台变频器之间的同步接线。
4、模拟输入信号接线:模拟输入信号接线用于变频器之间的通讯,当需要更改速度时,只需将模拟信号连接到相应的模拟输入端口,即可实现变频器间的通讯。
5、快速同步接线:快速同步接线用于快速同步变频器之间的转速,通过快速同步接线,可以使多台变频器的转速同步,变频器之间可以快速达到同一转速,提高系统的可靠性。
6、模拟输出信号接线:模拟输出信号接线用于将模拟输出信号传输到前驱或其他控制设备,以调整变频器的转速,防止发生超速或欠速的现象。
二、多变频器同步控制的方法
1、串行同步控制:串行同步控制是有多台变频器组成的一个集合,它将变频器用串行的方式连接起来,所调速的变频器只有串行的第一台,这样可以更快地实现同步控制。
变频器单传or多传?多传动系统的控制分析
变频器单传or多传?多传动系统的控制分析在工业设备中多台电动机的交流调速系统应用日益广泛,例如冶金、机械制造、纺织、造纸、运输、起重等行业的许多生产设备要求多台电动机之间按照一定的规律协调地运行。
多电动机传动是相对于单电动机传动而言的,也就是说在一条生产线或者一套设备上有两个或两个以上的电动机同时运行,这些电动机大多要求精确速度控制、多电机同步运转或比例同步(牵伸)运转等,这种类型的多台电动机的变频控制系统就是多传动变频系统。
使用多传动变频系统不断可以满足现场工况多种控制要求,还可以提高生产工艺、提升产品质量、减轻人工劳动强度和提高生产效率等。
1多传动变频系统的基本组成多传动变频系统上的多台独立变频器来完成各自电动机的控制要求,这种方式最为简单,使用普通的变频器就能完成,多台变频器可以多路电源供电也可以在前级共用一路电源(如图1-a)。
将系统中的多台变频器的直流电源并联连接,这种方式为共直流母线,该方式中一种是将多台普通变频器的直流端并联(如图1-b),一种是由独立的整流装置提供直流电源,多台逆变装置共用此直流电源(如图1-c)。
2多传动变频系统的控制方式多传动变频系统的应用场合中一般要满足多台变频器之间的同步运行、协调运行和功率均衡等要求。
从而控制方式就有多样化,例如速度同步控制、主从控制和负荷分配等。
1. 速度同步控制速度同步控制方式是多台变频器同时按照一样的速度运行的一种控制方式。
速度同步控制方式一般有模拟量同步控制、脉冲信号同步控制和通讯总线控制等方法(如图2)。
1.1模拟量同步控制由同步控制器输出多路模拟量信号控制多台变频器的速度,这种以模拟量信号控制变频器输出速度的方式即为模拟量同步控制方式,该方式需要配备一台同步控制器。
1.2脉冲信号同步控制通过一台变频器脉冲信号来控制另一台变频器运行速度的一种方式为脉冲信号同步控制方式。
当第一台变频器接受到主令电位器的速度信号后进行运转并同时输出同步脉冲信号给下一台变频器,该台变频器接受到上一台变频器的同步脉冲信号后进行运转并同时输出脉冲信号给下一台变频器,以此类推一直到最后一台变频器。
ACS800多传动选型样本
ACS800多传动选型样本ACS800是ABB公司生产的一款全数字电机频率变速器,广泛应用于各种工业自动化领域。
ACS800多传动选型是指在一个变频器控制下,通过多个电机传动来实现特定的运动方式。
下面将为你介绍一个ACS800多传动选型的样本。
样本要求:1.使用ACS800系列变频器2.满足客户提供的三个电机传动需求3.选取符合客户需求的适当额定功率和额定电压的电机样本示例:客户需求:1.需要将一个工业搅拌机的搅拌杆与马达通过同步带传动连接在一起。
2.需要将一个工业输送带的马达与滚筒通过链条传动连接在一起。
3.需要将一个工业纺织机的两个马达通过齿轮传动连接在一起。
多传动选型方案:1.搅拌机传动方案根据搅拌机的功率需求和转速要求,选用ACS800变频器,额定功率为10KW,额定电压为380V。
选择适当的同步带和同步带轮,根据同步带的参数和传动比例选择合适的带轮直径和齿数,确保电机和搅拌杆之间的传动效果和转速匹配。
2.输送带传动方案根据输送带的功率需求和转速要求,选用ACS800变频器,额定功率为15KW,额定电压为415V。
选择适当的链条和链轮,根据链条的参数和传动比例选择合适的链轮齿数和齿轮直径,确保电机和滚筒之间的传动效果和转速匹配。
3.纺织机传动方案根据纺织机的功率需求和转速要求,选用ACS800变频器,额定功率为20KW,额定电压为480V。
选择适当的齿轮和齿轮轴,根据齿轮的参数和传动比例选择合适的齿轮齿数和齿轮轴直径,确保两个电机之间的传动效果和转速匹配。
总结:通过ACS800多传动选型,我们为客户提供了一个综合解决方案,满足了三个电机传动的需求,确保了传动效果和转速的匹配,实现了工业设备的高效运行。
以上是一个ACS800多传动选型样本,根据不同的实际需求和参数要求,可以灵活选择不同功率和额定电压的ACS800变频器和相应的传动方式,以满足客户的多传动需求。
变频器多段控制设置方法
变频器多段控制设置方法哇塞,今天咱们来聊聊变频器多段控制设置方法,这可真是个超实用的技能呢!首先呢,要进行变频器多段控制设置,步骤可不能马虎。
先进入变频器的参数设置界面,找到多段速相关的参数。
然后根据实际需求,设定不同的速度段和对应的频率值。
注意哦,一定要仔细核对参数,确保设置准确无误,不然可就麻烦啦!同时,还要注意不同品牌和型号的变频器设置方法可能会有所差异,得按照说明书来操作呀。
在这个过程中,就好像是在给机器打造一个专属的“速度套餐”,可得精心准备呢!接着说说安全性和稳定性。
这可是至关重要的呀!在进行多段控制设置时,要确保设备的电气连接牢固可靠,避免出现松动等情况。
就好比建房子,根基得打牢呀!这样才能保证在不同速度段切换时,机器能稳定运行,不会出现故障或意外。
要是不安全不稳定,那不就像走在钢丝上一样让人提心吊胆嘛!再讲讲应用场景和优势。
变频器多段控制简直太有用啦!它可以应用于各种需要不同速度运行的设备,比如风机、水泵等。
优势也是多多的呀!它能实现精确的速度控制,让设备运行更加高效节能。
就好像给设备装上了智能的“速度调节按钮”,想快就快,想慢就慢,多方便呀!而且还能延长设备的使用寿命呢,这可真是个宝贝呀!来看看实际案例吧。
比如说在一个工厂的生产线上,通过变频器多段控制,可以根据不同的生产环节,灵活调整设备的速度。
在加工阶段可以快速运行提高效率,在检测阶段可以慢速运行保证质量。
这样一来,生产效率大大提高,产品质量也有保障,那效果简直太棒啦!这不就像是给生产线注入了活力,让它活力满满地工作嘛!我觉得呀,变频器多段控制设置方法真的是非常实用且重要的技能,掌握了它,就能让各种设备变得更加智能、高效、稳定。
大家一定要好好去学习和应用哦!。
利用PLC和变频器实现多电机速度同步控制
利用PLC和变频器实现多电机速度同步控制在传统的传动系统中,要保证多个执行元件间速度的一定关系,其中包括保证其间的速度同步或具有一定的速比,常采用机械传动刚性联接装置来实现。
但有时若多个执行元件间的机械传动装置较大,执行元件间的距离较远时,就只得考虑采用独立控制的非刚性联接传动方法。
下面以两个例子分别介绍利用PLC和变频器实现两个电机间速度同步和保持速度间一定速比的控制方法。
1、利用PLC和变频器实现速度同步控制薄膜吹塑及印刷机组的主要功能是,利用挤出吹塑的方法进行塑料薄膜的加工,然后经过凹版印刷机实现对薄膜的印刷,印刷工艺根据要求不同可以采用单面单色、单面多色、双面单色或双面多色等方法。
在整个机组中,有多个电机的速度需要进行控制,如挤出主驱动电机、薄膜拉伸牵引电机、印刷电机以及成品卷绕电机等。
电机间的速度有一定的关系,如:挤出主电机的速度由生产量要求确定,但该速度确定之后,根据薄膜厚度,相应的牵引速度也就确定,因此挤出速度和牵引速度之间有一确定的关系;同时,多组印刷胶辘必须保证同步,印刷电机和牵引电机速度也必须保持同步,否则,将影响薄膜的质量、印刷效果以及生产的连续性;卷绕电机的速度受印刷速度的限制,作相应变化,以保证经过印刷的薄膜能以恒定的张力进行卷绕。
在上述机组的传动系统中,多组印刷胶辘的同步驱动可利用刚性的机械轴联接,整个印刷胶辘的驱动由一台电机驱动,这样就保证了它们之间的同步。
印刷电机的速度必须保证与牵引电机的速度同步,否则,在此两道工艺之间薄膜会出现过紧或过松的现象,影响印刷质量和生产的连续性。
但是印刷生置与牵引装置相距甚远,无法采用机械刚性联接的方法。
为实现牵引与印刷间的同步控制,牵引电机和印刷电机各采用变频器进行调速,再用PLC对两台变频器直接控制。
牵引电机和印刷电机采用变频调速,其控制框图如图1所示。
在这个闭环控制中,以牵引辘的速度为目标,由印刷电机变频器调节印刷辘速度来跟踪牵引辘的速度。
- 1、下载文档前请自行甄别文档内容的完整性,平台不提供额外的编辑、内容补充、找答案等附加服务。
- 2、"仅部分预览"的文档,不可在线预览部分如存在完整性等问题,可反馈申请退款(可完整预览的文档不适用该条件!)。
- 3、如文档侵犯您的权益,请联系客服反馈,我们会尽快为您处理(人工客服工作时间:9:00-18:30)。
附件1皮带机主从控制方案
头部4台变频器采取主从控制,主机为速度控制,从机为转矩控制,尾部2台变频器采用转矩控制,尾部2台变频器转矩由PLC给定。
头部变频器的转矩给PLC,由PLC对头部变频器的转矩调整,将调整后的转矩值给尾部的变频器做为转矩给定,以此来协调皮带输送机头部转动装置与尾部传动装置的转矩。
头部四台变频器通过光纤实现主从连接,通过光纤将主机的转矩发送给从机。
同时将头部主机的转矩通过现场总线发送给PLC。
再由PLC经过张力计算等环节将调整后的转矩通过现场总线发送给尾部变频器。
主/从功能是为多传动应用而设计的,其中系统由若干个ACS 800 变频器驱动,同时电机轴通过齿轮、链条或传送带等相互耦合在一起。
由于这种主/从功能,负载可以均匀地分配在传动单元之间。
外部控制信号只与主机连接。
主机通过一个光纤串行通讯链路来控制从机。
主机是典型的速度控制,其它传动单元跟随主机的转矩或速度给定。
环行结构连接可以用在大多数场合下。
如果使用一个光纤分配器,也可以采用并
行结构连接。
传输媒介: 光缆
• 结构:塑料芯、直径1 mm、外包塑料皮
• 衰减:0.23 dB/m
• 站间最大长度:10 m
• 其它:
参数设置–主机站
主机站如同一个独立的传动单元,对其设置和控制。
下表列出了一些需要调整的主/从机应用的参数。
参数设置–从机站
下表列出了在主/从机应用中需要调整的参数名。
现场总线连接
现场总线适配器可以用来监视从机,但是不能对从机进行控制。
从机由主机控制,可以用一种现场总线系统来控制主机。
操作:正常工作时,由于有视窗控制,从机的速度调节器输出(TORQ REF 2) 为零。
从机跟随主机的转矩给定(TORQ REF 1)。
当负载减小时,视窗控制功能激活速度调节器,从而防止从机速度上升到最大极限值:
–从机的实际转速开始迅速上升。
–转速偏差的绝对值(SPEED REF 3 - ACTUAL SPEED)超过参数60.05 WINDOW WIDTH NEG.的设定值。
这时,视窗控制将转速偏差输入速度调节器。
–速度调节器将一个负值加入到转矩给定(TORQ REF 1)。
电机的转矩受到限制,因此防止了电机转速的进一步升高。
主机的运行允许信号是通过从机的继电器输出RO3 接入的,在缺省情况下,只要从机出现故障或断电,RO3 将切断主机的运行允许信号。
附件2-主要电气元器件表。