起亚数控车床对刀仪及双主轴功能使用方法
简述数控车床对刀操作步骤
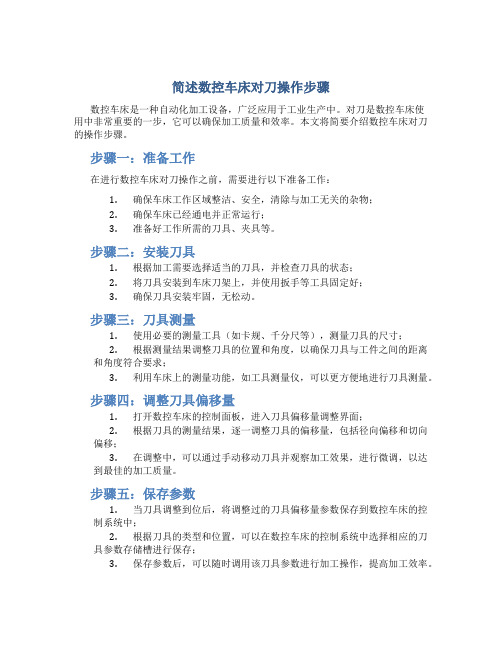
简述数控车床对刀操作步骤数控车床是一种自动化加工设备,广泛应用于工业生产中。
对刀是数控车床使用中非常重要的一步,它可以确保加工质量和效率。
本文将简要介绍数控车床对刀的操作步骤。
步骤一:准备工作在进行数控车床对刀操作之前,需要进行以下准备工作:1.确保车床工作区域整洁、安全,清除与加工无关的杂物;2.确保车床已经通电并正常运行;3.准备好工作所需的刀具、夹具等。
步骤二:安装刀具1.根据加工需要选择适当的刀具,并检查刀具的状态;2.将刀具安装到车床刀架上,并使用扳手等工具固定好;3.确保刀具安装牢固,无松动。
步骤三:刀具测量1.使用必要的测量工具(如卡规、千分尺等),测量刀具的尺寸;2.根据测量结果调整刀具的位置和角度,以确保刀具与工件之间的距离和角度符合要求;3.利用车床上的测量功能,如工具测量仪,可以更方便地进行刀具测量。
步骤四:调整刀具偏移量1.打开数控车床的控制面板,进入刀具偏移量调整界面;2.根据刀具的测量结果,逐一调整刀具的偏移量,包括径向偏移和切向偏移;3.在调整中,可以通过手动移动刀具并观察加工效果,进行微调,以达到最佳的加工质量。
步骤五:保存参数1.当刀具调整到位后,将调整过的刀具偏移量参数保存到数控车床的控制系统中;2.根据刀具的类型和位置,可以在数控车床的控制系统中选择相应的刀具参数存储槽进行保存;3.保存参数后,可以随时调用该刀具参数进行加工操作,提高加工效率。
步骤六:试切与调整1.在进行实际加工之前,进行试切操作,观察切削效果;2.根据试切结果,进行必要的调整,如调整切削速度、进给速度、切削深度等;3.不断试切与调整,直到达到满意的加工效果。
步骤七:加工生产1.在完成刀具调整和试切调整后,即可正式进行加工生产;2.根据加工要求,在数控车床上设置相应的加工参数,如切削速度、进给速度、切削深度等;3.监控加工过程,及时调整参数,保证加工质量和效率。
以上便是数控车床对刀操作的简要步骤。
数控车床对刀方法
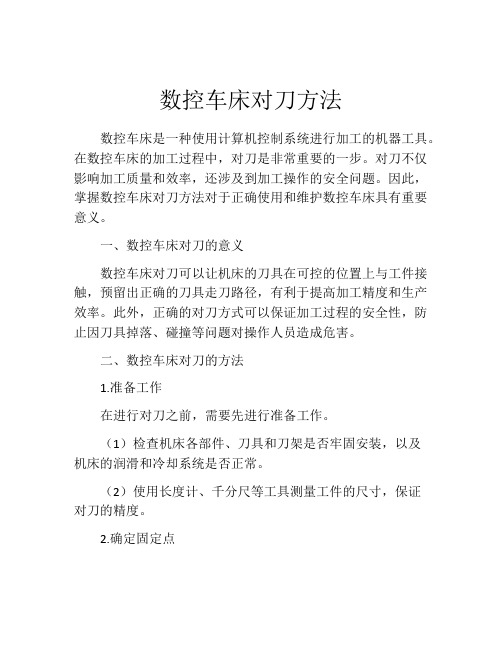
数控车床对刀方法数控车床是一种使用计算机控制系统进行加工的机器工具。
在数控车床的加工过程中,对刀是非常重要的一步。
对刀不仅影响加工质量和效率,还涉及到加工操作的安全问题。
因此,掌握数控车床对刀方法对于正确使用和维护数控车床具有重要意义。
一、数控车床对刀的意义数控车床对刀可以让机床的刀具在可控的位置上与工件接触,预留出正确的刀具走刀路径,有利于提高加工精度和生产效率。
此外,正确的对刀方式可以保证加工过程的安全性,防止因刀具掉落、碰撞等问题对操作人员造成危害。
二、数控车床对刀的方法1.准备工作在进行对刀之前,需要先进行准备工作。
(1)检查机床各部件、刀具和刀架是否牢固安装,以及机床的润滑和冷却系统是否正常。
(2)使用长度计、千分尺等工具测量工件的尺寸,保证对刀的精度。
2.确定固定点固定点是指在数控下处理的零点的位置,即要加工工件的原点。
通常,固定点需要根据手册或数控系统的参数手动输入。
在数控系统中,固定点可以利用修正处理实现校准。
3.选择刀具选择合适的刀具对于加工的质量和效率影响很大。
刀具的选择需要考虑加工件材质、表面形状、线速度、切削用量和切削液条件等。
在选择刀具的时候需要尽量避免出现中心偏差,以保证对刀的准确性。
4.调整刀具位置刀具需要在机床上调整到正确的位置,以保证加工质量和效率。
具体来说,以下两种对刀方式常见:(1)刮刀法:在使用前,需要将刀具调整到靠近工件的位置,打开机床手轮,然后用刀片轻轻的刮掉工件上的涂层。
当涂层刮净后,可以逐渐调整刀具的出刀量,将刀具调整到最佳位置。
(2)对刀仪法:在使用对刀仪的时候,需要在工件和刀具之间放置对刀仪,测量靠近工件的刀具尖端和对刀仪的距离,然后根据测量结果调整刀具的位置。
5.校正刃口补偿值在数控车床加工过程中,刃口补偿值是一个很重要的参数。
为了保证刃口补偿值的准确性,需要根据实际情况和手册要求进行校正。
通常在进行磨刀后需要重新校正刃口补偿值,以确保机床的加工精度。
简述数控车床对刀操作步骤
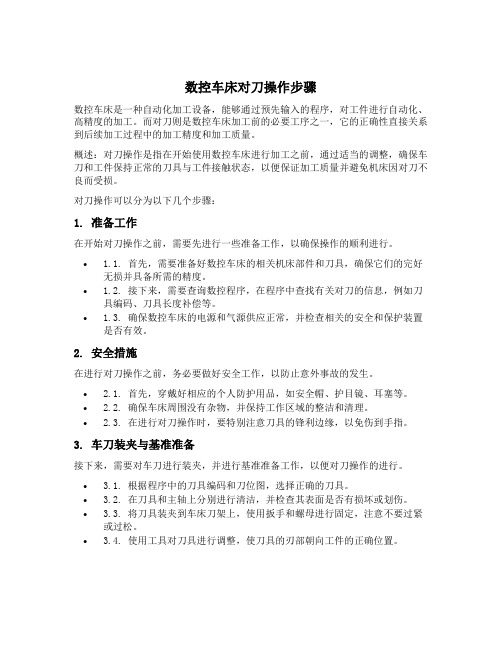
数控车床对刀操作步骤数控车床是一种自动化加工设备,能够通过预先输入的程序,对工件进行自动化、高精度的加工。
而对刀则是数控车床加工前的必要工序之一,它的正确性直接关系到后续加工过程中的加工精度和加工质量。
概述:对刀操作是指在开始使用数控车床进行加工之前,通过适当的调整,确保车刀和工件保持正常的刀具与工件接触状态,以便保证加工质量并避免机床因对刀不良而受损。
对刀操作可以分为以下几个步骤:1. 准备工作在开始对刀操作之前,需要先进行一些准备工作,以确保操作的顺利进行。
• 1.1. 首先,需要准备好数控车床的相关机床部件和刀具,确保它们的完好无损并具备所需的精度。
• 1.2. 接下来,需要查询数控程序,在程序中查找有关对刀的信息,例如刀具编码、刀具长度补偿等。
• 1.3. 确保数控车床的电源和气源供应正常,并检查相关的安全和保护装置是否有效。
2. 安全措施在进行对刀操作之前,务必要做好安全工作,以防止意外事故的发生。
• 2.1. 首先,穿戴好相应的个人防护用品,如安全帽、护目镜、耳塞等。
• 2.2. 确保车床周围没有杂物,并保持工作区域的整洁和清理。
• 2.3. 在进行对刀操作时,要特别注意刀具的锋利边缘,以免伤到手指。
3. 车刀装夹与基准准备接下来,需要对车刀进行装夹,并进行基准准备工作,以便对刀操作的进行。
• 3.1. 根据程序中的刀具编码和刀位图,选择正确的刀具。
• 3.2. 在刀具和主轴上分别进行清洁,并检查其表面是否有损坏或划伤。
• 3.3. 将刀具装夹到车床刀架上,使用扳手和螺母进行固定,注意不要过紧或过松。
• 3.4. 使用工具对刀具进行调整,使刀具的刃部朝向工件的正确位置。
4. 刀具长度补偿在进行对刀操作之前,需要对刀具的长度进行补偿,以确保刀具与工件的接触状态良好。
• 4.1. 通过数控程序中的对刀功能,找出刀具长度补偿的参数值,并输入到数控系统中。
• 4.2. 根据刀具的长度补偿参数,使用对刀仪或辅助工具,测量刀具的实际长度。
对刀仪的使用方法
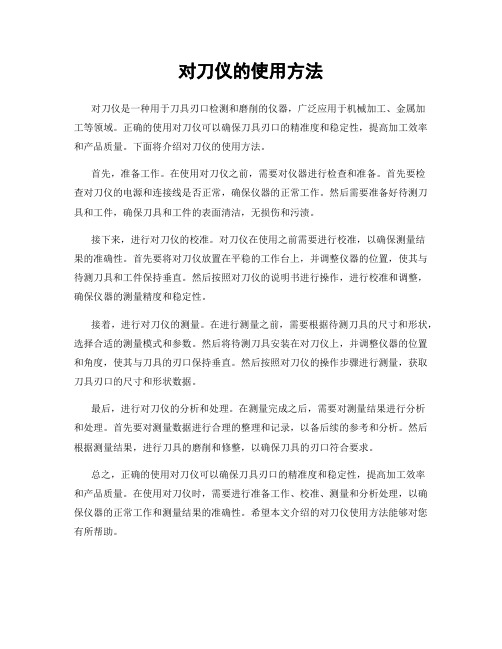
对刀仪的使用方法对刀仪是一种用于刀具刃口检测和磨削的仪器,广泛应用于机械加工、金属加工等领域。
正确的使用对刀仪可以确保刀具刃口的精准度和稳定性,提高加工效率和产品质量。
下面将介绍对刀仪的使用方法。
首先,准备工作。
在使用对刀仪之前,需要对仪器进行检查和准备。
首先要检查对刀仪的电源和连接线是否正常,确保仪器的正常工作。
然后需要准备好待测刀具和工件,确保刀具和工件的表面清洁,无损伤和污渍。
接下来,进行对刀仪的校准。
对刀仪在使用之前需要进行校准,以确保测量结果的准确性。
首先要将对刀仪放置在平稳的工作台上,并调整仪器的位置,使其与待测刀具和工件保持垂直。
然后按照对刀仪的说明书进行操作,进行校准和调整,确保仪器的测量精度和稳定性。
接着,进行对刀仪的测量。
在进行测量之前,需要根据待测刀具的尺寸和形状,选择合适的测量模式和参数。
然后将待测刀具安装在对刀仪上,并调整仪器的位置和角度,使其与刀具的刃口保持垂直。
然后按照对刀仪的操作步骤进行测量,获取刀具刃口的尺寸和形状数据。
最后,进行对刀仪的分析和处理。
在测量完成之后,需要对测量结果进行分析和处理。
首先要对测量数据进行合理的整理和记录,以备后续的参考和分析。
然后根据测量结果,进行刀具的磨削和修整,以确保刀具的刃口符合要求。
总之,正确的使用对刀仪可以确保刀具刃口的精准度和稳定性,提高加工效率和产品质量。
在使用对刀仪时,需要进行准备工作、校准、测量和分析处理,以确保仪器的正常工作和测量结果的准确性。
希望本文介绍的对刀仪使用方法能够对您有所帮助。
车床对刀的操作流程

车床对刀的操作流程
车床对刀是一项非常重要的车床操作工作,可以有效提高车削精度和效率,下面介绍一下操作流程:
1. 取下车床主轴套筒内的刀具,确定要进行对刀的切削刀具。
2. 用刀具边缘轻轻触到对刀仪中的感应棒,将对刀仪固定在车床滑板上。
3. 将感应棒置于对刀仪的中央,然后旋转主轴手轮,让刀具的端面轻轻触碰感应棒。
4. 用手拧动对调螺丝,将凸缘中心线与车床主轴中心线重合,并夹紧螺母锁定。
5. 用与车床主轴相垂直的方向垂直于对刀仪感应棒的方向,再次触碰刀具端面,确认是否对好。
6. 启动车床主轴,运行切削刀具,通过视觉判断切削刀具与工件表面的间隙是否相等,随时调整,直到达到需要的精度。
7. 对刀完成后,记得清理现场,注意安全!
注意事项:在对刀时,必须保证车床运行的精度和传动部件的完整性,同时注意切削刀具的安全使用,正确选择合适的刀具型号和切削条件。
数控车床的对刀操作步骤
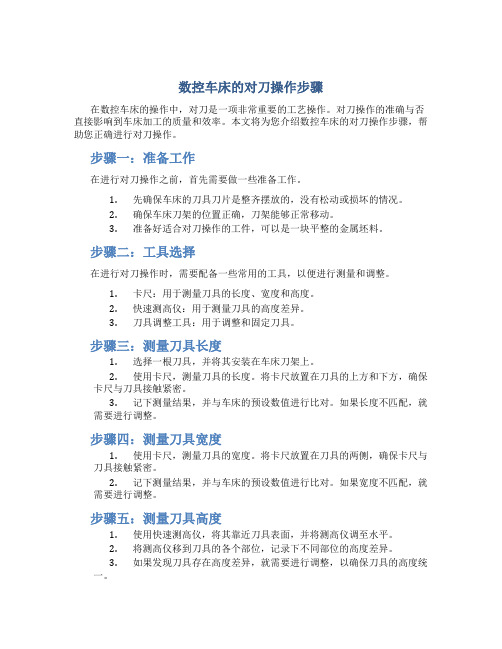
数控车床的对刀操作步骤在数控车床的操作中,对刀是一项非常重要的工艺操作。
对刀操作的准确与否直接影响到车床加工的质量和效率。
本文将为您介绍数控车床的对刀操作步骤,帮助您正确进行对刀操作。
步骤一:准备工作在进行对刀操作之前,首先需要做一些准备工作。
1.先确保车床的刀具刀片是整齐摆放的,没有松动或损坏的情况。
2.确保车床刀架的位置正确,刀架能够正常移动。
3.准备好适合对刀操作的工件,可以是一块平整的金属坯料。
步骤二:工具选择在进行对刀操作时,需要配备一些常用的工具,以便进行测量和调整。
1.卡尺:用于测量刀具的长度、宽度和高度。
2.快速测高仪:用于测量刀具的高度差异。
3.刀具调整工具:用于调整和固定刀具。
步骤三:测量刀具长度1.选择一根刀具,并将其安装在车床刀架上。
2.使用卡尺,测量刀具的长度。
将卡尺放置在刀具的上方和下方,确保卡尺与刀具接触紧密。
3.记下测量结果,并与车床的预设数值进行比对。
如果长度不匹配,就需要进行调整。
步骤四:测量刀具宽度1.使用卡尺,测量刀具的宽度。
将卡尺放置在刀具的两侧,确保卡尺与刀具接触紧密。
2.记下测量结果,并与车床的预设数值进行比对。
如果宽度不匹配,就需要进行调整。
步骤五:测量刀具高度1.使用快速测高仪,将其靠近刀具表面,并将测高仪调至水平。
2.将测高仪移到刀具的各个部位,记录下不同部位的高度差异。
3.如果发现刀具存在高度差异,就需要进行调整,以确保刀具的高度统一。
步骤六:刀具调整根据之前测量的结果,对刀具进行调整。
1.如果刀具的长度不匹配,可以通过添加刀夹片或者更换刀具来进行调整。
2.如果刀具的宽度不匹配,可以通过调整刀具的位置或者更换合适宽度的刀具来进行调整。
3.如果刀具的高度差异较大,可以通过调整刀架高度或者刀具位置来进行调整。
步骤七:验证对刀结果在完成刀具的调整后,需要进行对刀结果的验证,以确保调整准确。
1.将工件安装在车床上,并选择适当的加工程序。
2.运行加工程序,观察加工过程中切削刀具的表现。
对刀仪使用方法

对刀仪使用方法(总6页) -CAL-FENGHAI.-(YICAI)-Company One1-CAL-本页仅作为文档封面,使用请直接删除对刀仪使用方法随着加工中心的广泛使用,许多用户也开始使用刀具测量装置。
它不仅可以检测刀具的磨损情况,而且可实现自动补偿(通过修改刀补值实现),极大的提高了加工效率和精度。
另外,同时使用其刀具破损检测功能与刀具寿命管理功能,还可以实现自动寻找同组刀具的功能,节约了刀具检查和更换的时间。
但由于用户对测量原理不是很了解,使用时容易产生误区,有时补偿后的精度反而不如补偿前,这就使用户产生了迷惑,限制了测量装置的广泛使用。
本文以英国RENISH AW.html" target="_blank" class="keylink">雷尼绍(RENISHAW)公司TS27 R测头的安装调试为例,就如何更好的使用刀具测量装置做一详细介绍,供读者参考借鉴。
刀具测量的基本原理是利用系统的跳步功能(G31):在程序中指令“G31 Zx x x Fx x x”(与GO1的动作相同)。
但此时如果SKIP信号由“0”变为“1”时,Z轴将停止运动,再用宏程序控制坐标轴后退,然后再次碰触量块,反复测量并运算后得出刀具的实际长度和直径,最后修改系统宏变量从而达到修改刀补值的目的。
刀具测量装置的使用主要包括三个步骤:安装和接线;标定;测量。
1 安装和接线刀具侧量装置通常包括测头和信号转换装置(硬件)及相关的测量程序(软件包)。
测头(TS27R)安装在工作台上,并尽量远离加工区域,外部应加防护装置,使用前先将防护装置打开并将刀具用风吹干净(用M代码控制气动元件可实现自动),确保刀具表面无杂物,测量完成后关闭防护。
测头安装完成后,首先要调整测头接触面的平行度和直线度。
将一只百分表(或千分表DTI)吸在主轴头上,表头打在量块(圆形或方形)的上表面;用手轮控制X轴沿量块表面来回移动,观察表针变化,同时调整测头上的调节螺钉,使X向的直线度保证在0.010mm,调整好后紧固螺钉。
数控车床对刀操作步骤及主意事项

数控车床对刀操作步骤及主要注意事项引言数控车床是一种常用的自动化机床,它能够通过计算机程序控制切削刀具进行各种精密加工。
对刀操作是数控车床上的一项重要工作,不仅关系到加工质量,还关系到操作人员的安全。
本文将介绍数控车床对刀的操作步骤及一些需要注意的事项。
操作步骤1. 准备工作在进行对刀操作之前,需要进行一些准备工作:- 检查车床设备是否正常运行,确保各项安全保护设施功能正常; - 准备好合适的刀具,并检查刀具的磨损程度;- 确定加工工件的材料和尺寸,并将工件正确装夹在车床上。
2. 测量工件和刀具对刀操作的关键是准确测量工件和刀具的尺寸。
- 使用合适的测量工具(如卡尺、游标卡尺等)测量工件的尺寸,包括直径、长度等。
记录下测量结果; - 使用刀具测量仪(或编程装置)测量刀具的长度、直径等尺寸,并记录下测量结果。
3. 汇编刀具根据测量结果,正确选择刀具,并进行刀具的汇编。
- 根据加工要求选择合适的刀具,并将其正确安装在车床的刀架上; - 使用专用工具对刀具进行调整,确保刀具的位置、夹持力等参数符合要求。
4. 进行对刀操作对刀操作是一项技术性较高的工作,需要仔细操作。
- 打开数控车床的操作界面,选择对刀操作功能; - 根据测量结果输入刀具和工件的尺寸等参数,然后启动对刀操作; - 数控车床会根据输入的参数自动调整刀具的位置和补偿值,确保加工的准确性。
5. 对刀结果检验和调整完成对刀操作后,需要对对刀结果进行检验,确保加工的准确性和质量。
- 使用测量工具对加工后的工件进行检验,与加工要求进行对比,判断偏差是否在允许范围内; - 如果测量结果有偏差,需要根据实际情况进行调整,如重新测量,重新选择刀具等。
注意事项在进行数控车床对刀操作时,需要注意以下事项,以确保操作安全和加工质量:1. 熟悉数控车床的操作规程和安全操作要求,遵守相关的安全操作规定; 2. 选择合适的刀具,并保证其质量和磨损情况符合要求; 3. 对工件进行正确的装夹,保证工件与车床床身之间的配合间隙适当; 4. 准确测量工件和刀具的尺寸,确保测量结果准确无误; 5. 在对刀操作过程中,避免手部接近刀具,以免发生意外伤害;6. 在进行刀具调整时,切勿用力过度,以免损坏刀具和车床设备;7. 对刀完成后,及时清理工作区域和设备,保持车床的清洁和良好的工作环境。
- 1、下载文档前请自行甄别文档内容的完整性,平台不提供额外的编辑、内容补充、找答案等附加服务。
- 2、"仅部分预览"的文档,不可在线预览部分如存在完整性等问题,可反馈申请退款(可完整预览的文档不适用该条件!)。
- 3、如文档侵犯您的权益,请联系客服反馈,我们会尽快为您处理(人工客服工作时间:9:00-18:30)。
如对以下步骤不熟悉,请谨慎。
推荐在单段、快进倍率在5%状态下试用,确保不会撞机!
一、对刀仪的使用:
起亚的SKT15/21系列车床具有内置对刀仪,即便是新手,也可在1分钟内方便快捷地完成12把刀具的对刀。
对刀步骤如下:
1.停止主轴转动,取下零件,正确安装所有需要的刀具;
2.按下JOG或者X(HANDLE)或者Z(HANDLE)切换成手动模式或手轮模式;
3.打开防护门,放下对刀仪。
此时显示屏会自动切换到刀具补偿画面,光标停留在当
前刀号上;
4.用手动或手轮功能移动刀塔,使刀尖分别压下对刀仪的X向及Z向触点。
触点被压
下后会听到‘嘀’的一声响声,此时相应方向的刀具补偿数值已经被自动计算并输入到相应的刀补号中;
说明:对刀仪有4个触点,不同形状的车刀能碰到不同的触点,普通右手外圆车刀能碰到Z+和X+触点,普通右手内孔车刀能碰到Z+和X-触点。
对刀时无需刻意选择
触点,按照刀具形状压下任何一个触点均可完成对刀。
5.将刀塔移开,收回对刀仪;
6.刀塔X向回零,换下一把刀;
7.放下对刀仪,重复第4~6步,完成所有刀具的对刀。
Z向工件坐标原点设置步骤
按照以上方法对刀后并不能立刻进行加工,还需要确定工件的Z向零点。
步骤如下(以下步骤不是对刀仪使用所必须的步骤,即便不使用对刀仪,也需要掌握下列步骤以更好地进行加工):
1.随意选一把刀(最好选择要加工Z向零点平面的刀具),加上刀具补偿;
2.用试切、垫纸或测量的方法使刀尖移动到Z向零平面;
3.切换到位置(POS)画面的绝对坐标,记下Z值;
4.按OFF/SET按钮切换到偏置/设置画面,按屏底软键的翻页键找到‘工件移’(英文
或繁体中文显示为‘W.SHIFT’)画面并进入;
5.将第3步记下的Z值写入Z,然后切换到位置画面,如果上述步骤操作正确,此时
绝对坐标的Z值应该为零。
6.完成
说明:以上第4及第5步可以用FANUC的G10语句实现,格式如下:
语法:G10 P0 Xn Zn
含义:修改工件坐标系偏移值
参数说明:G10 G代码,可写入参数编程
P0 代表修改工件坐标系偏移
X & Z 坐标字
n 数值,与X及Z连用(即第3步记下的Z值)
例如:假设在上述第3步记录的Z值为185.7,则在程序开始加入下面程序段:G10 P0 X0 Z185.7;
其中X0最好不要省略,以免别人修改X的工件坐标偏移后发生意外。
强烈推荐在程序中使用G10确定零件的工件坐标系偏移,避免忘记更改偏移值而发生意外。
二、双主轴功能的使用:
1.主轴夹紧工件(手动上料);
2.启动主轴旋转(代码M3或M4)
3.执行M110代码;(切换到副主轴控制)
4.执行M118代码;(副主轴卡爪夹紧,因为卡爪松开时不能启动旋转)
5.执行M113代码;(旋转副主轴,转速自定)
6.执行G04代码;(暂停一段时间,大约1秒,使副主轴达到指定转速)
7.执行M160代码;(使副主轴与主轴转速、转向同步)
8.执行G04代码;(暂停一段时间,大约1秒,使副主轴达到主轴转速)
9.执行M162代码;(使副主轴与主轴相位同步,即旋转的角度相同)
10.执行G04代码;(暂停一段时间,大约1秒,使副主轴达到相位同步)
11.执行M119代码;(松开副主轴卡爪)
12.执行G0 B-nn代码;(使副主轴,即B轴向前运动到夹持位置,要确保工件不会碰
到副主轴的卡爪,且有足够的夹持长度)
13.执行M118代码;(副主轴卡爪夹紧,此时主轴、副主轴同时夹持工件旋转)
14.执行G04代码;(暂停一段时间,大约1秒,确保副主轴已夹紧)
15.执行M69代码;(松开主轴卡爪)
16.执行G0 B-nn代码;(使副主轴,即B轴退回,工件离开主轴)
17.执行M161代码;(副主轴退出同步模式,副主轴恢复原来设定的转速及转向)
18.执行G04代码;(暂停一段时间,大约1秒,使副主轴达到原转速,可根据情况省
略此步骤)
19.完成
程序举例:
%
O0001(SP-SYNCHRONOUSPRO);
G0G28U0;
G28W0B0;
N1;
M3S300;
M110;
M118;
G04U1.0;
M113S1000;
G04U1.0;
M3S500;
G04U1.0;
M160;
G04U1.0;
M162;
G04U1.0;
N2;
M119;
G4U1.;
G00B-600.0;
M118;
G04U1.0;
M69;
G00B-100.0;
N3;
M161;
G04U1.0;
M05;
M115;
M68;
G28B0;
M30;
%
注意:操作之前需要根据零件外径将主轴、副主轴软爪镗一下,以达到更高的同轴度及更好地夹持零件。
如对以上步骤不熟悉,请谨慎。
推荐在单段、快进倍率在5%状态下试用,确保不会撞机!。