回转窑结圈
回转窑内结圈结球的原因及处理方法

各种类型的水泥回转窑都遇到过结圈问题。
结圈使窑该处的横断面积显著减少,严重影响窑内通风,阻碍物料运动,对回转窑的产量、质量、安全运转、煤耗、电耗均有一定影响。
尤其频繁结圈的回转窑,不仅破坏了窑内正常热工制度,而且损害操作人员的身体健康,给生产造成经济损失。
Eg2jexl 引起回转窑结圈的因素很多,它与原料性质、生料成分、燃料的灰分和细度、窑型、窑内还原气氛及热工制度等有关。
在实际生产过程中,煅烧硅酸率高的熟料时,对减少结圈有好处,但是烧硅酸率很高的白水泥熟料也结圈。
至于说煤灰的影响,但所有烧油的水泥回转窑同样也结圈。
所以结圈问题比较复杂。
现结合生产中的体会和认识,谈谈水泥回转窑结圈的预防和处理。
t%k`)p7O1 结圈的形成 LtKR15h,回转窑内形成结圈的因素很多,但液相的产生和固化是结圈的主要形成过程。
而衬料温度、物料温度、煤灰和生料组成又是决定液相的生成和固化的主要因素。
在熟料煅烧过程中,生料在1200℃左右出现液相,在1250℃左右液相粘度开始变小,液相量增加,由于料层覆盖温度突降,加之筒体表面散热,液相在窑壁上凝固下来,形成窑皮。
窑继续运转,窑皮又暴露在高温中而被熔掉下来,再次被物料覆盖,液相又凝固下来,如此周而复始。
如果粘挂上去的多,掉下来的小,窑皮就增厚,反之就变薄。
在正常情况下,窑皮可保持在200mm左右的厚度。
该温度条件及区域内若熔化和固化的过程达到平衡,窑皮就不会增厚。
当熔化的少固化的多,其厚度增长到一定程度,即形成圈。
当衬料与物料的温差大时,在足够液相的条件下,圈体越结越厚。
ma) + G!1.1 前结圈的形成 Gb"kl .j前结圈(又称窑口圈),是结在回转窑烧成带末端部位的圈。
在正常煅烧条件下,物料温度为1350~1450℃,液相量约为24%,其粘度较大。
当熟料离开烧成带时,液相开始冷却,进入冷却带的液相已基本固化。
在烧成带和冷却带的交界处存在着较大的温差,窑口物料温度高于窑皮温度。
回转窑结圈的原因及处理方法

回转窑结圈的原因及处理方法1、结圈的危害回转窑“结圈”的部位一般在距窑口一定距离的固体燃料集中燃烧点附近的耐火窑衬上,厚度可达200-500 mm左右。
“结圈”对球团生产的危害有以下几方面:(1)降低产量,增加劳动强度窑圈一经形成,对燃料烧烧所产生的热气流势必起阻碍作用,如图-1所示。
热气流被部分阻挡在A区,影响了球团的焙烧效果。
同时,由于链篦机上生球的干燥、预热过程是利用窑尾废气进行的,故此,结圈也对生球的干燥、预热产生不良影响。
具体地说,就是透气性差,火焰不进,后部温度低,干燥时水分不易脱除,生球爆裂、粉化严重,成品率低,从而降低了劳动生产率。
另外,圈结形成后,如不及时处理,就会使圈的纵向长度、厚度增加,当圈掉下时,必然增加工人的劳动强度,有时甚至需停机处理,也影响了球团矿的产量。
(2) 增加了设备负荷如图-1所示,一定面积及厚度的结圈使物料流被阻于B区,此时,被阻的料量要高出正常时许多,加之圈本身的重量,必然增加了托轮、轴承的磨损,同时,增加了电机的负荷,甚至烧毁。
(3) 浪费能源在实际看火操作中,当出现“结圈”现象后,由于热气流被阻于A区,为保证链篦机的干燥和预热效果,看火工往往采用加大给煤量的方式,这无疑造成了能源浪费。
2、结圈的原因结圈的原因,在生产中主要可以归纳为操作不当。
具体地说,是由于上料量过大,干燥效果差,生球爆裂,粉化严重,致使透气性差,使得引风机抽动火焰的作用不明显,火焰只在窑内一定距离燃烧。
在大于1 200℃的高温下,未完全氧化的Fe3O4就与磁铁矿中一定数量的SiO2发生反应形成液相。
2Fe3O4+3SiO2+2CO=3Fe2SiO4+2CO22FeO+SiO2=Fe2SiO4另外,当给煤量较大时,在1 150℃条件下,Fe2O3也会部分分解为Fe3O4,与SiO2作用而生成2FeO·SiO2,形成渣相粘结。
这就使得物料在流经焙烧带时,所产生的液相、渣相极易粘附在窑衬的表面,同时粘结物料而产生结圈现象。
回转窑结圈的影响因素及解决措施

回转窑结圈的影响因素及解决措施-----龙仕连我司从11月23日开始窑内断断续续出现少量漏料,并出现了三次大料球,严重影响到窑的正常运转,公司及部门领导高度重视。
经分析是窑23米处结后圈导致窑尾漏料和结料球。
于25日开始处理后圈:1、窑减产到350 t/h煅烧;2、窑头煤管每个班移动两次,-200~+100冷热交替处理;3、每班清理煤管头部积料结焦4次,以保证头煤燃烧好,火焰集中;4、控制煤粉细度及水分,以保证煤粉燃烧效果(煤磨出磨温度控制在63~65度,入磨温度<300度。
内部控制煤粉细度<6.0);5、适当提高熟料KH。
通过3天的处理,23料处后圈薄了很多,并有缺口,于28日窑恢复了365 t/h正常生产。
出现这样的工艺事故,我们必须深度反思。
特别是工艺管理人员和窑操作员一定要密切关注窑皮的变化趋势及原燃材料的变化,及时调整窑参数,保证窑正常运转。
下面让我们再次学习一下窑内结圈的成因、危害及解决措施:结圈是指回转窑在正常生产中,由于原燃材料的变化,或者操作和热工制度的影响,窑内因物料过度粘结,在特定的区域形成一道阻碍物料运动的环形、坚硬的圈。
这种现象在回转窑内是一种不正常的窑况,它破坏了正常的热工制度,影响窑内通风,造成窑内来料波动很大,直接影响到回转窑的产量、质量、消耗和长期安全运转。
而且处理窑内结圈费时费力,严重时需停窑停产,危害极其严重。
结圈的成因及危害:结圈的形成: 结圈实际上是在烧成带末端与放热反应带交界处形成的窑皮,是回转窑内危害最大的结圈。
在熟料煅烧过程中,当物料温度达到1280℃时,其液相黏度较大,最容易形成结圈,而且冷却后比较坚固,不易除掉。
在正常的煅烧情况下,后结圈体的内径部分往往被烧熔而掉落,保持正常的圈体内径。
如果在1 250~l 280℃温度范围内出现的液相量偏多,往往会形成妨碍生产的后结圈。
后结圈一般结在烧成带的边界或更远,开始是烧成带后边的窑皮逐渐增长、增厚,发展到一定程度即形成后结圈。
球团回转窑结圈诊断

球团回转窑结圈诊断1. 什么是球团回转窑结圈?球团回转窑是一种常用的矿石烧结设备,用于将粉末状物料(如铁矿石、焦炭等)在高温下进行结圈反应,制成球团。
然而,在使用过程中,由于各种因素的影响,常常会出现球团回转窑结圈问题。
球团回转窑结圈指的是物料在回转窑内部形成不可解开的块状物质,导致生产过程中停机维修、产量下降以及能源浪费等问题。
因此,对球团回转窑结圈进行诊断和解决具有重要意义。
2. 球团回转窑结圈诊断方法2.1 观察法通过观察球团回转窑内部情况,如物料流动状态、温度分布、气体排放等,可以初步判断是否存在结圈问题。
例如,如果发现物料流动不畅或者有大块物料积聚在某些区域,则可能存在结圈现象。
2.2 温度测量法利用红外测温仪等设备对回转窑内部进行温度测量,可以发现温度异常区域。
结圈通常会导致某些区域温度升高,或者出现局部温度过低的情况。
2.3 物料取样分析法通过在回转窑停机后,取出物料样品进行化学成分和物理性质的分析,可以确定结圈原因。
例如,如果发现物料中含有大量易熔成分或者粘结剂,则可能是由于成分不合理导致结圈。
2.4 球团形态观察法观察球团形态可以判断结圈程度和原因。
例如,如果球团形状不规则、表面粗糙,则可能是由于结圈导致球团形成不完整。
3. 球团回转窑结圈诊断结果分析根据以上诊断方法得到的结果,对球团回转窑结圈问题进行分析。
3.1 结圈原因分析根据物料取样分析结果,确定了结圈原因为成分不合理。
进一步观察球团形态,并参考温度测量结果,发现高温区域处的球团形状不规则、表面粗糙。
结合观察法得到的物料流动不畅的情况,可以推断结圈是由于粘结剂含量过高导致的。
3.2 结圈解决方案针对结圈原因,制定相应的解决方案。
首先,需要调整粘结剂配比,控制粘结剂含量在合理范围内。
其次,通过改变进料速度和角度等操作参数,改善物料流动性。
此外,还可以考虑增加通风设备、调整燃烧器位置等措施,以提高温度分布均匀性。
4. 结论球团回转窑结圈是生产过程中常见的问题,通过综合运用观察法、温度测量法、物料取样分析法和球团形态观察法等诊断方法,可以准确判断结圈原因,并制定相应解决方案。
回转窑结圈处理机

回转窑结圈处理机回转窑结圈处理机是一种用于处理回转窑结圈的设备,它在水泥生产过程中起到了重要的作用。
本文将从不同角度来描述回转窑结圈处理机,并探讨其在水泥生产中的作用。
一、回转窑结圈处理机的工作原理回转窑结圈处理机通过一系列的工作步骤来处理回转窑产生的结圈问题。
首先,它利用高温燃烧的方式将结圈烧解,并将其转化为可再利用的物料。
然后,通过机械装置将烧解后的物料输送到后续的处理工艺中,进一步进行处理和利用。
回转窑结圈处理机的工作原理简单而高效,能够有效解决回转窑结圈问题,提高水泥生产的效率。
1. 高效节能:回转窑结圈处理机能够将结圈物料烧解并转化为可再利用的物料,减少能源消耗和原材料浪费,实现节能环保的目标。
2. 自动化程度高:回转窑结圈处理机采用自动化控制系统,能够实现自动化操作和监控,减少人工干预,提高生产效率。
3. 适应性强:回转窑结圈处理机能够适应不同规模和工艺要求的水泥生产线,具有较强的适应性和灵活性。
4. 减少环境污染:回转窑结圈处理机能够有效减少水泥生产过程中的废气和废水排放,降低环境污染的程度。
三、回转窑结圈处理机的应用案例回转窑结圈处理机在水泥生产中得到了广泛的应用。
以某水泥厂为例,该厂引进了先进的回转窑结圈处理机,通过对回转窑结圈进行烧解和处理,成功解决了结圈问题,提高了水泥生产的效率和质量。
同时,该厂还充分利用回转窑结圈处理机产生的再利用物料,实现了资源的循环利用,进一步降低了生产成本和环境污染。
四、结语回转窑结圈处理机在水泥生产中发挥了重要的作用,通过高效烧解和处理回转窑结圈,实现了资源的循环利用和环境保护。
随着水泥产业的发展和技术的进步,回转窑结圈处理机将在未来得到更广泛的应用,并为水泥生产带来更大的效益和贡献。
煤基还原回转窑结圈
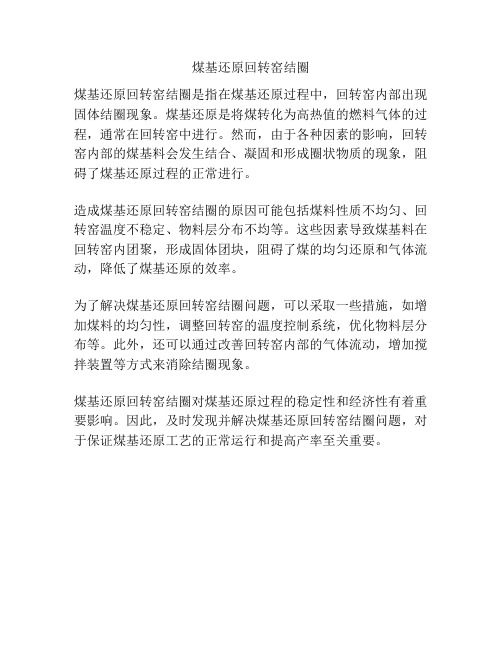
煤基还原回转窑结圈
煤基还原回转窑结圈是指在煤基还原过程中,回转窑内部出现固体结圈现象。
煤基还原是将煤转化为高热值的燃料气体的过程,通常在回转窑中进行。
然而,由于各种因素的影响,回转窑内部的煤基料会发生结合、凝固和形成圈状物质的现象,阻碍了煤基还原过程的正常进行。
造成煤基还原回转窑结圈的原因可能包括煤料性质不均匀、回转窑温度不稳定、物料层分布不均等。
这些因素导致煤基料在回转窑内团聚,形成固体团块,阻碍了煤的均匀还原和气体流动,降低了煤基还原的效率。
为了解决煤基还原回转窑结圈问题,可以采取一些措施,如增加煤料的均匀性,调整回转窑的温度控制系统,优化物料层分布等。
此外,还可以通过改善回转窑内部的气体流动,增加搅拌装置等方式来消除结圈现象。
煤基还原回转窑结圈对煤基还原过程的稳定性和经济性有着重要影响。
因此,及时发现并解决煤基还原回转窑结圈问题,对于保证煤基还原工艺的正常运行和提高产率至关重要。
回转窑窑后结圈原因分析及处理方法

回转窑窑后结圈原因分析及处理方法巩义市恒昌冶金建材设备厂生产的1000t/d熟料生产线是由天津水泥工业设计研究院有限公司设计的,主要包括TDF型分解炉、单系列五级旋风预热器、Φ3.2m×50m回转窑及TC-836篦式冷却机。
自2007年2月以来,窑后频繁发生结圈、结球的工艺事故,巩义市恒昌冶金建材设备厂技术人员现将原因分析及解决措施介绍如下,供同仁参考。
1、结圈情况2007年3月19日最为严重,窑前返火,窑尾有漏料现象,无法操作煅烧,迫使停窑处理。
从窑内看,主窑皮长达22m,副窑皮长到窑尾,35~37m处形成后结圈,结圈最小孔洞呈不规则状,直径约l.5m,进窑观察该圈明显分为两层,且层次明确、清晰,第一层厚约150mm,呈黄白色,第二层厚约460mm,呈黑色,圈体非常致密。
对圈体取样分析见表1。
表1 圈体取样分析结果从表l可以看出,第一层硫碱含量较高,是硫碱圈,第二层明显是煤粉圈,熟料液相出现过早、过多导致结圈。
2、原因分析(1)由于2006年煤价不断上涨,加之公路运输距离远,为了降低成本,采用当地劣质煤煅烧,煤质下降,灰分高,挥发分低,发热值低,煤工业分析如表2、3。
实际生产中,煤可燃性差,煤粉燃烧不完全,大量煤灰不均掺入生料中,液相在窑后面提前出现,而未燃尽的煤灰产生沉积及液相的提前出现结圈。
(2)2007年以来,由于机械原因,高温风机l号轴与密封圈强烈摩擦,产生局部高温,使轴侧曲,水平振动最高达6.4mm/s。
为了降低振动,不得不降低高温风机转速,由原来的1130r/min降至l060r/min,有时更低,严重影响了窑内通风,加上煤质又差,更多的窑头燃烧不完全的煤粉沉积在窑后燃烧,使窑内后部温度升高,液相量增加,加速了窑后结圈的形成。
(3)为了处理窑后结圈,我厂在迫不得已的情况下停窑烧后圈,由于煤质差,二、三次风温低,燃料不完全或未燃烧的煤粉落在圈上及圈后的积料上,不断燃烧,造成物料发粘,不但圈未烧掉,反而越结越厚,这也是第一层圈形成的主要原因。
回转窑结圈的原因及处理方法
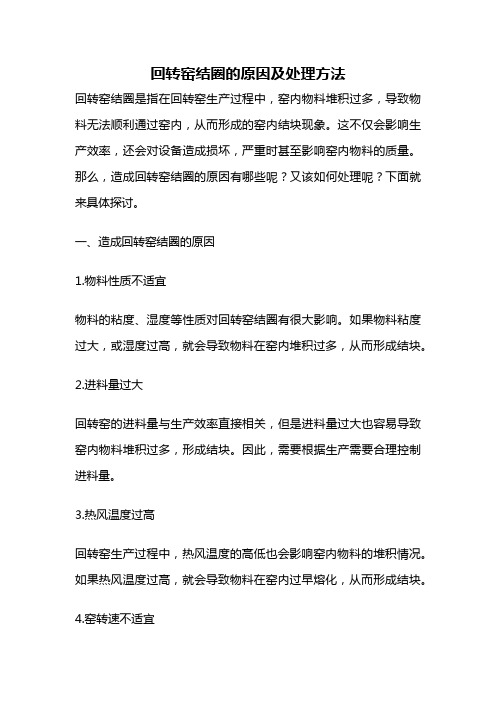
回转窑结圈的原因及处理方法回转窑结圈是指在回转窑生产过程中,窑内物料堆积过多,导致物料无法顺利通过窑内,从而形成的窑内结块现象。
这不仅会影响生产效率,还会对设备造成损坏,严重时甚至影响窑内物料的质量。
那么,造成回转窑结圈的原因有哪些呢?又该如何处理呢?下面就来具体探讨。
一、造成回转窑结圈的原因1.物料性质不适宜物料的粘度、湿度等性质对回转窑结圈有很大影响。
如果物料粘度过大,或湿度过高,就会导致物料在窑内堆积过多,从而形成结块。
2.进料量过大回转窑的进料量与生产效率直接相关,但是进料量过大也容易导致窑内物料堆积过多,形成结块。
因此,需要根据生产需要合理控制进料量。
3.热风温度过高回转窑生产过程中,热风温度的高低也会影响窑内物料的堆积情况。
如果热风温度过高,就会导致物料在窑内过早熔化,从而形成结块。
4.窑转速不适宜回转窑的转速也会影响窑内物料的堆积情况。
如果转速过快,就会导致物料在窑内无法均匀分布,从而形成结块。
二、回转窑结圈的处理方法1.减少进料量当回转窑结圈发生时,可以适当减少进料量,以缓解窑内物料堆积过多的情况。
2.调整热风温度如果回转窑结圈是由于热风温度过高导致的,可以适当降低热风温度,以减少窑内物料的过早熔化。
3.调整窑转速如果回转窑结圈是由于窑转速不适宜导致的,可以适当调整窑转速,以保证物料在窑内均匀分布。
4.清理窑内物料当回转窑结圈严重时,需要停窑清理窑内物料。
清理时需要注意安全,避免对设备造成损坏。
5.加入流化剂在窑内加入一定量的流化剂,可以有效地缓解回转窑结圈现象。
流化剂可以使物料在窑内均匀分布,减少结块的情况。
6.调整物料配比如果回转窑结圈是由于物料配比不合理导致的,可以适当调整物料配比,以保证物料在窑内均匀分布,减少结块的情况。
回转窑结圈是一种常见的生产问题,多种因素都可能导致其发生。
因此,在回转窑生产过程中,需要做好预防措施,保证物料在窑内均匀分布,避免结块的发生。
同时,一旦发生回转窑结圈,需要及时采取相应的处理措施,以保证生产效率和产品质量。
- 1、下载文档前请自行甄别文档内容的完整性,平台不提供额外的编辑、内容补充、找答案等附加服务。
- 2、"仅部分预览"的文档,不可在线预览部分如存在完整性等问题,可反馈申请退款(可完整预览的文档不适用该条件!)。
- 3、如文档侵犯您的权益,请联系客服反馈,我们会尽快为您处理(人工客服工作时间:9:00-18:30)。
回转窑结圈
1、安全因素:
所有的设备安全防护装置完好。
确保巡检通道畅通、干净。
保证所有区域有足够的照明。
所有人员必须正确配戴PPE。
各个观察孔门关闭,各处无热气、灰尘冒出。
压缩空气无泄漏。
窑尾出现漏料时及时调整,制止漏料,并设置警戒线等明显标志,以防高温物料烫伤
2、环境因素:
需考虑以下环境因素:
1. 严格执行国家相关的环保政策和法律法规。
2. 当发现有灰尘泄漏时,需及时汇报。
3. 按照要求,定期的监控和记录所有排气点的排气情况。
4. 除去外部可能产生灰尘的料堆。
5. 若发现润滑油、液压油、水火干物料有任何泄漏或漏料的话,需要及时汇报。
3、资源
可供参考的文件:
回转窑中控操作说明书。
功能分析。
4、窑结圈形成判断
4.1筒体扫描仪观察,结圈处筒体温度降低至150℃以下
4.2窑内通风变差,烟室氧含量下降4%以下
4.3系统阻力增加,烟室负压升高至-500以下
4.4窑负荷增大到1000A左右,窑负荷平均值高和波动幅度较大,波动幅度达200A—300A
4.5窑尾烟室密封处漏料
4.6窑内出料变少或来料不均匀
5、窑结圈原因分析
5.1窑口圈
5.1.1煤粉细度变粗
5.1.2二次风温异常波动
5.1.3火焰不顺畅
5.2烧成带尾部结圈
5.2.1烧成带起点波动,料的成分变化,分解率波动
5.2.2筒体冷却风机使用不当
5.2.3火焰不顺畅
5.3硫碱圈
5.3.1煤粉中的S含量高,
5.3.2窑内还原气氛,有害成份内循环富集
5.3.3入窑生料成分波动,导致热工制度的不稳定
5.3.4烧成带温度过高
5.3.5火焰不顺畅
6、窑结圈的处理
6.1窑口圈的处理
6.1.1调整火焰,煤管退至零位
6.1.2确保煤粉细度合格率达到90%以上
6.2烧成带尾部结圈
6.2.1稳定入窑分解率,稳定篦冷机运转、窑头罩压力和燃料加入量,以便稳定火焰
6.2.2稳定生料率值,将入窑生料的硅率提高0.1,控制熟料的液相量
6.2.3减少三次风门的开度并增加引风量,控制烟室的氧含量不低于4.0% 6.2.4如结圈继续恶化不能控制,则停窑打圈,执行该SOP操作程序
6.3硫碱圈的处理
6.3.1稳定煤的成份,降低煤粉中的S含量。
6.3.2稳定煅烧,保证煤粉完全燃烧,禁止出现CO。
6.3.3优化生料率值,适当提高硅率0.1,控制熟料的液相量
6.3.4减少三次风门的开度并增加引风量,控制烟室的氧含量不低于4.0% 6.3.5改善入窑生料的易烧性,控制生料的细度,降低煅烧温度
6.3.6如果高温风机已达到极限,烟室的氧含量仍低于4.0%,适当减料保证窑内通风
6.3.5如结圈继续恶化不能控制,,则停窑打圈,执行该SOP操作程序。