回转窑结圈的原因
回转窑接圈原因分析

1 结圈的形成回转窑内形成结圈的因素很多,但液相的产生和固化是结圈的主要形成过程。
而物料温度、煤灰和原料组成又是决定液相的生成和固化的主要因素。
在煅烧过程中,料在1200℃左右出现液相,在1250℃左右液相粘度开始变小,液相量增加,由于料层覆盖温度突降,加之筒体表面散热,液相在窑壁上凝固下来,形成窑皮。
窑继续运转,窑皮又暴露在高温中而被熔掉下来,再次被物料覆盖,液相又凝固下来,如此周而复始。
如果粘挂上去的多,掉下来的小,窑皮就增厚,反之就变薄。
在正常情况下,窑皮可保持在200mm左右的厚度。
该温度条件及区域内若熔化和固化的过程达到平衡,窑皮就不会增厚。
当熔化的少固化的多,其厚度增长到一定程度,即形成圈。
当物料与液相的温差大时,在足够液相的条件下,圈体越结越厚。
1.1 前结圈的形成前结圈(又称窑口圈),是结在回转窑烧成带末端部位的圈。
在正常煅烧条件下,物料温度为1350~1450℃,液相量约为24%,其粘度较大。
当熟料离开烧成带时,液相开始冷却,进入冷却带的液相已基本固化。
在烧成带和冷却带的交界处存在着较大的温差,窑口物料温度高于窑皮温度。
当熟料进入冷却带时,带有液相的高温熟料覆盖在温度较低的末端窑皮上,就会很快粘结、越粘越厚,最后形成前结圈。
在煅烧过程中,当烧成带高温部分温度过于集中时,冷却带与烧成带交界处出现很大的温差,加之高温急烧液相量增多,粘度较小,熟料进入冷却带时,仍有大量液相迅速冷却在交界的附近,促进了前圈的增长。
1.2 熟料圈的形成熟料圈(又称二道圈),是结在窑内烧成带与放热反应带之间的圈,也是回转窑内危害最大的结圈。
在熟料煅烧过程中,当物料温度达到1280℃时,其液相粘度较大,熟料圈最易形成,冷却后比较坚固,不易除掉,在正常煅烧情况下,熟料圈体的内径部分,往往被烧熔而掉落,保持正常的圈体内径。
如果在1250~1280℃温度范围内出现的液相量偏多,往往形成妨碍生产的熟料圈。
熟料圈一般结在烧成带的边界或更远,开始是烧成带后边的窑皮逐渐增长,逐渐长厚,发展到一定程度即形成熟料圈。
煤基还原回转窑结圈
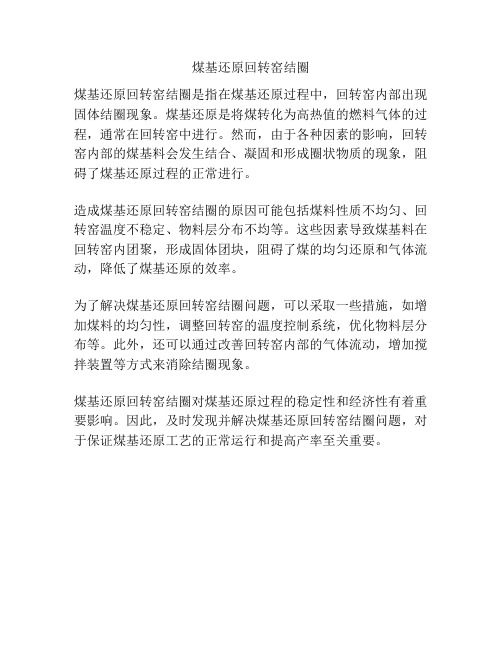
煤基还原回转窑结圈
煤基还原回转窑结圈是指在煤基还原过程中,回转窑内部出现固体结圈现象。
煤基还原是将煤转化为高热值的燃料气体的过程,通常在回转窑中进行。
然而,由于各种因素的影响,回转窑内部的煤基料会发生结合、凝固和形成圈状物质的现象,阻碍了煤基还原过程的正常进行。
造成煤基还原回转窑结圈的原因可能包括煤料性质不均匀、回转窑温度不稳定、物料层分布不均等。
这些因素导致煤基料在回转窑内团聚,形成固体团块,阻碍了煤的均匀还原和气体流动,降低了煤基还原的效率。
为了解决煤基还原回转窑结圈问题,可以采取一些措施,如增加煤料的均匀性,调整回转窑的温度控制系统,优化物料层分布等。
此外,还可以通过改善回转窑内部的气体流动,增加搅拌装置等方式来消除结圈现象。
煤基还原回转窑结圈对煤基还原过程的稳定性和经济性有着重要影响。
因此,及时发现并解决煤基还原回转窑结圈问题,对于保证煤基还原工艺的正常运行和提高产率至关重要。
回转窑窑后结圈原因分析及处理方法

回转窑窑后结圈原因分析及处理方法巩义市恒昌冶金建材设备厂生产的1000t/d熟料生产线是由天津水泥工业设计研究院有限公司设计的,主要包括TDF型分解炉、单系列五级旋风预热器、Φ3.2m×50m回转窑及TC-836篦式冷却机。
自2007年2月以来,窑后频繁发生结圈、结球的工艺事故,巩义市恒昌冶金建材设备厂技术人员现将原因分析及解决措施介绍如下,供同仁参考。
1、结圈情况2007年3月19日最为严重,窑前返火,窑尾有漏料现象,无法操作煅烧,迫使停窑处理。
从窑内看,主窑皮长达22m,副窑皮长到窑尾,35~37m处形成后结圈,结圈最小孔洞呈不规则状,直径约l.5m,进窑观察该圈明显分为两层,且层次明确、清晰,第一层厚约150mm,呈黄白色,第二层厚约460mm,呈黑色,圈体非常致密。
对圈体取样分析见表1。
表1 圈体取样分析结果从表l可以看出,第一层硫碱含量较高,是硫碱圈,第二层明显是煤粉圈,熟料液相出现过早、过多导致结圈。
2、原因分析(1)由于2006年煤价不断上涨,加之公路运输距离远,为了降低成本,采用当地劣质煤煅烧,煤质下降,灰分高,挥发分低,发热值低,煤工业分析如表2、3。
实际生产中,煤可燃性差,煤粉燃烧不完全,大量煤灰不均掺入生料中,液相在窑后面提前出现,而未燃尽的煤灰产生沉积及液相的提前出现结圈。
(2)2007年以来,由于机械原因,高温风机l号轴与密封圈强烈摩擦,产生局部高温,使轴侧曲,水平振动最高达6.4mm/s。
为了降低振动,不得不降低高温风机转速,由原来的1130r/min降至l060r/min,有时更低,严重影响了窑内通风,加上煤质又差,更多的窑头燃烧不完全的煤粉沉积在窑后燃烧,使窑内后部温度升高,液相量增加,加速了窑后结圈的形成。
(3)为了处理窑后结圈,我厂在迫不得已的情况下停窑烧后圈,由于煤质差,二、三次风温低,燃料不完全或未燃烧的煤粉落在圈上及圈后的积料上,不断燃烧,造成物料发粘,不但圈未烧掉,反而越结越厚,这也是第一层圈形成的主要原因。
链篦机回转窑结圈预防与控制冯景光天池球团

回转窑结圈原因分析回转窑结圈是链篦机一回转窑法球团生产中的常见故障之一,如果预防、处理不及时,将造成生产停产、减产甚至发生重大设备事故,处理时还要消耗大量劳动力,甚至损坏回转窑或环冷机的耐火材料。
通过分析和现场观测,对结圈具体原因分析如下。
窑内粉末含量高,高温下与煤灰中的SiO2形成低熔点化合物,生球强度低(2~3次/0.5 m),经倒运后破裂,形成粉末进入回转窑。
布料有时过厚,横向纵向布料不平,干燥不完全,生球在预热段产生粉化。
链篦机温度偏低,干燥固结不好,强度低于500N/个以上的要求,进入回转窑,在运动过程中破碎。
二、链篦机干球氧化不够干球强度差,料层透气性差,氧化率低,FeO含量偏高,在窑内高温下与SiO2形成低熔点化合物。
生产用煤热值(<29 MJ/kg)、灰熔点(≤1400℃)偏低,灰分较高(>14%)。
为保证工艺温度,煤用量偏大,煤灰在窑内聚集,容易与铁矿粉在窑内局部高温处(火陷附近,温度可达l 300℃以上)形成粘结相;喷煤量有时过大,窑内局部形成还原性气氛(CO含量高),磁铁矿氧化慢,形成一些低熔点化合物(如2FeO—SiO2),高温下产生液相使粉末粘结。
膨润土用量有时低,导致生球质量无法保证,大量粉末入窑,回转窑造成结圈;使用的膨润土配料秤偏差,膨润土添加的精度满足不了生产要求,致使有时膨润土添加量严重超标,且在球内分布不匀,在高温下形成粉末,局部反应生成粘结物。
粉煤燃烧必须达到以下三个基本要求:保证空气粉煤混合物呈紊流状态,以强化气流的扩散过程。
因回转窑内需要火焰较长,混合物喷出速度一般为40一75 m/s(喷煤风量为1200-1800 m3/h,此时火焰可达10~15 m)。
如果速度过低则可能引起粗的煤粉颗粒从火焰中沉降到窑壁(此现象有时在窑内十分明显),引起窑壁局部高温,保证火焰根部煤粉完全燃烧。
目前窑内火焰情况:根据现场观察,目前窑内火焰刚度差(火柱没劲),呈短促的棉团状,火焰边缘直接与窑壁或物料接触,特别是结圈物未清除干净时,该现象更为明显,这是结圈快速长大的根本原因所在。
回转窑结圈的原因
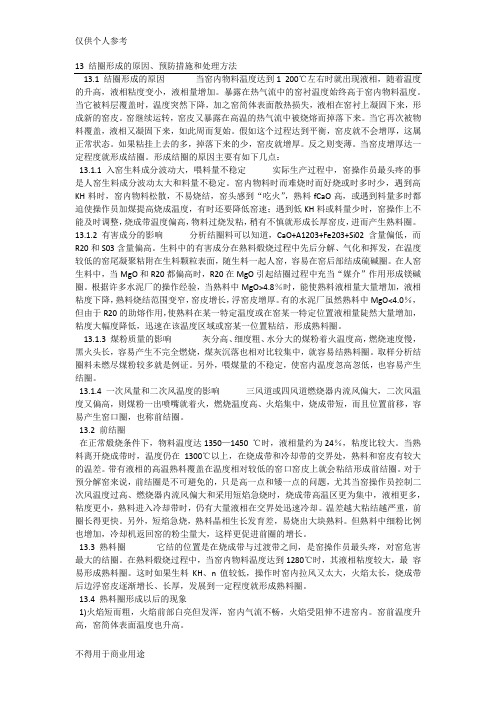
13 结圈形成的原因、预防措施和处理方法13.1 结圈形成的原因当窑内物料温度达到1 200℃左右时就出现液相,随着温度的升高,液相粘度变小,液相量增加。
暴露在热气流中的窑衬温度始终高于窑内物料温度。
当它被料层覆盖时,温度突然下降,加之窑简体表面散热损失,液相在窑衬上凝固下来,形成新的窑皮。
窑继续运转,窑皮又暴露在高温的热气流中被烧熔而掉落下来。
当它再次被物料覆盖,液相又凝固下来,如此周而复始。
假如这个过程达到平衡,窑皮就不会增厚,这属正常状态。
如果粘挂上去的多,掉落下来的少,窑皮就增厚。
反之则变薄。
当窑皮增厚达一定程度就形成结圈。
形成结圈的原因主要有如下几点:13.1.1 入窑生料成分波动大,喂料量不稳定实际生产过程中,窑操作员最头疼的事是人窑生料成分波动太大和料量不稳定。
窑内物料时而难烧时而好烧或时多时少,遇到高KH料时,窑内物料松散,不易烧结,窑头感到“吃火”,熟料fCaO高,或遇到料量多时都迫使操作员加煤提高烧成温度,有时还要降低窑速;遇到低KH料或料量少时,窑操作上不能及时调整,烧成带温度偏高,物料过烧发粘,稍有不慎就形成长厚窑皮,进而产生熟料圈。
13.1.2 有害成分的影响分析结圈料可以知道,CaO+A1203+Fe203+Si02含量偏低,而R20和S03含量偏高。
生料中的有害成分在熟料煅烧过程中先后分解、气化和挥发,在温度较低的窑尾凝聚粘附在生料颗粒表面,随生料一起人窑,容易在窑后部结成硫碱圈。
在人窑生料中,当MgO和R20都偏高时,R20在MgO引起结圈过程中充当“媒介”作用形成镁碱圈。
根据许多水泥厂的操作经验,当熟料中MgO>4.8%时,能使熟料液相量大量增加,液相粘度下降,熟料烧结范围变窄,窑皮增长,浮窑皮增厚。
有的水泥厂虽然熟料中MgO<4.0%,但由于R20的助熔作用,使熟料在某一特定温度或在窑某一特定位置液相量陡然大量增加,粘度大幅度降低,迅速在该温度区域或窑某一位置粘结,形成熟料圈。
结圈形成的原因、预防措施和处理方法
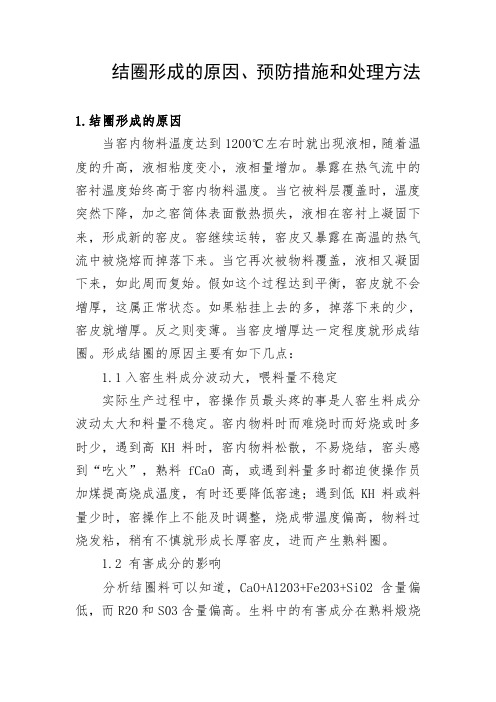
结圈形成的原因、预防措施和处理方法1.结圈形成的原因当窑内物料温度达到1200℃左右时就出现液相,随着温度的升高,液相粘度变小,液相量增加。
暴露在热气流中的窑衬温度始终高于窑内物料温度。
当它被料层覆盖时,温度突然下降,加之窑简体表面散热损失,液相在窑衬上凝固下来,形成新的窑皮。
窑继续运转,窑皮又暴露在高温的热气流中被烧熔而掉落下来。
当它再次被物料覆盖,液相又凝固下来,如此周而复始。
假如这个过程达到平衡,窑皮就不会增厚,这属正常状态。
如果粘挂上去的多,掉落下来的少,窑皮就增厚。
反之则变薄。
当窑皮增厚达一定程度就形成结圈。
形成结圈的原因主要有如下几点:1.1入窑生料成分波动大,喂料量不稳定实际生产过程中,窑操作员最头疼的事是人窑生料成分波动太大和料量不稳定。
窑内物料时而难烧时而好烧或时多时少,遇到高KH料时,窑内物料松散,不易烧结,窑头感到“吃火”,熟料fCaO高,或遇到料量多时都迫使操作员加煤提高烧成温度,有时还要降低窑速;遇到低KH料或料量少时,窑操作上不能及时调整,烧成带温度偏高,物料过烧发粘,稍有不慎就形成长厚窑皮,进而产生熟料圈。
1.2 有害成分的影响分析结圈料可以知道,CaO+A1203+Fe203+Si02含量偏低,而R20和S03含量偏高。
生料中的有害成分在熟料煅烧过程中先后分解、气化和挥发,在温度较低的窑尾凝聚粘附在生料颗粒表面,随生料一起人窑,容易在窑后部结成硫碱圈。
在人窑生料中,当MgO和R20都偏高时,R20在MgO引起结圈过程中充当“媒介”作用形成镁碱圈。
根据许多水泥厂的操作经验,当熟料中MgO>4.8%时,能使熟料液相量大量增加,液相粘度下降,熟料烧结范围变窄,窑皮增长,浮窑皮增厚。
有的水泥厂虽然熟料中MgO<4.0%,但由于R20的助熔作用,使熟料在某一特定温度或在窑某一特定位置液相量陡然大量增加,粘度大幅度降低,迅速在该温度区域或窑某一位置粘结,形成熟料圈。
回转窑后结圈的原因分析与解决措施

回转窑后结圈的原因分析与解决措施发布时间:2022-04-25T02:30:40.147Z 来源:《工程管理前沿》2022年1期作者:田硕[导读] 近年来,由于国家倡导节能减排的生产,从而加大了对一些浪费资源和污染比较大的企业改革田硕山东申丰水泥集团有限公司山东省枣庄市 277300引言:近年来,由于国家倡导节能减排的生产,从而加大了对一些浪费资源和污染比较大的企业改革,这就给了新型熟料回转窑一个重要的市场,让他们可以快速的发展起来。
熟料回转窑设备结构坚固、运转平稳、出窑产品质量高。
此外,在环保方面,利用熟料窑焚烧危险废物、垃圾,这不仅使废物减量化、无害化,而且将废物作为燃料利用,节省煤粉,做到废物的资源化。
关键词:回转窑后结圈解决措施摘要:熟料回转窑后结圈往往形成于烧成带和过渡带之间。
在熟料煅烧过程中,当窑内温度达到1280℃时,其液相粘度较大,此时,如果生料的KH、n率值较低,操作使窑内拉风较大,火焰太长,烧成带后边浮窑皮逐渐增长、增厚,发展到一定程度就形成了熟料回转窑的后结圈。
一、后结圈情况A企业配置一条5000t/d预分解熟料回转窑。
于2021年10月份在窑尾38米、43米处出现两道结圈,严重时窑尾出现漏料,窑投料量下降,熟料质量波动,窑况很不稳定。
二、原因分析2.1原煤内水偏高加剧了结圈的发生2021年煤价不断上涨,原煤库存为0吨,原煤随来随用,严重影响煤的均化效果。
煤粉内水偏高,窑头喷煤管燃烧速度慢、燃烧时间长,火焰的热力分散,燃烧时热力强度低,高温点后移,烧成带拉长,高温点不集中,熟料烧结不致密,二次风温偏低,恶性循环更加加剧了火焰燃烧速度。
物料预烧不好,容易产生不完全燃烧,没有燃尽的煤粉颗粒和CO不能在烧成带燃烧,部分聚集在窑尾燃烧,促使液相在过渡带提前出现,将未熔的物料黏结在一起,形成后结圈。
停窑后取结圈料化学分析结果发现:正常熟料烧失量为0.42%,结圈料为1.66%、2.06%也验证了这一点。
回转窑结圈的原因及处理方法
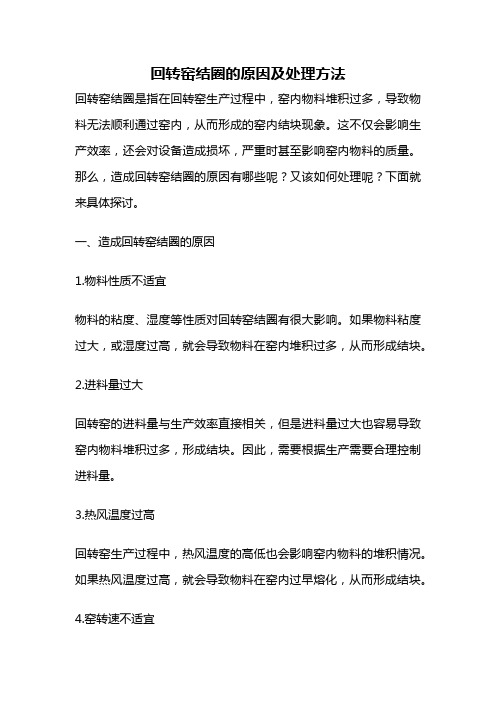
回转窑结圈的原因及处理方法回转窑结圈是指在回转窑生产过程中,窑内物料堆积过多,导致物料无法顺利通过窑内,从而形成的窑内结块现象。
这不仅会影响生产效率,还会对设备造成损坏,严重时甚至影响窑内物料的质量。
那么,造成回转窑结圈的原因有哪些呢?又该如何处理呢?下面就来具体探讨。
一、造成回转窑结圈的原因1.物料性质不适宜物料的粘度、湿度等性质对回转窑结圈有很大影响。
如果物料粘度过大,或湿度过高,就会导致物料在窑内堆积过多,从而形成结块。
2.进料量过大回转窑的进料量与生产效率直接相关,但是进料量过大也容易导致窑内物料堆积过多,形成结块。
因此,需要根据生产需要合理控制进料量。
3.热风温度过高回转窑生产过程中,热风温度的高低也会影响窑内物料的堆积情况。
如果热风温度过高,就会导致物料在窑内过早熔化,从而形成结块。
4.窑转速不适宜回转窑的转速也会影响窑内物料的堆积情况。
如果转速过快,就会导致物料在窑内无法均匀分布,从而形成结块。
二、回转窑结圈的处理方法1.减少进料量当回转窑结圈发生时,可以适当减少进料量,以缓解窑内物料堆积过多的情况。
2.调整热风温度如果回转窑结圈是由于热风温度过高导致的,可以适当降低热风温度,以减少窑内物料的过早熔化。
3.调整窑转速如果回转窑结圈是由于窑转速不适宜导致的,可以适当调整窑转速,以保证物料在窑内均匀分布。
4.清理窑内物料当回转窑结圈严重时,需要停窑清理窑内物料。
清理时需要注意安全,避免对设备造成损坏。
5.加入流化剂在窑内加入一定量的流化剂,可以有效地缓解回转窑结圈现象。
流化剂可以使物料在窑内均匀分布,减少结块的情况。
6.调整物料配比如果回转窑结圈是由于物料配比不合理导致的,可以适当调整物料配比,以保证物料在窑内均匀分布,减少结块的情况。
回转窑结圈是一种常见的生产问题,多种因素都可能导致其发生。
因此,在回转窑生产过程中,需要做好预防措施,保证物料在窑内均匀分布,避免结块的发生。
同时,一旦发生回转窑结圈,需要及时采取相应的处理措施,以保证生产效率和产品质量。
- 1、下载文档前请自行甄别文档内容的完整性,平台不提供额外的编辑、内容补充、找答案等附加服务。
- 2、"仅部分预览"的文档,不可在线预览部分如存在完整性等问题,可反馈申请退款(可完整预览的文档不适用该条件!)。
- 3、如文档侵犯您的权益,请联系客服反馈,我们会尽快为您处理(人工客服工作时间:9:00-18:30)。
13 结圈形成的原因、预防措施和处理方法13.1 结圈形成的原因当窑内物料温度达到1 200℃左右时就出现液相,随着温度的升高,液相粘度变小,液相量增加。
暴露在热气流中的窑衬温度始终高于窑内物料温度。
当它被料层覆盖时,温度突然下降,加之窑简体表面散热损失,液相在窑衬上凝固下来,形成新的窑皮。
窑继续运转,窑皮又暴露在高温的热气流中被烧熔而掉落下来。
当它再次被物料覆盖,液相又凝固下来,如此周而复始。
假如这个过程达到平衡,窑皮就不会增厚,这属正常状态。
如果粘挂上去的多,掉落下来的少,窑皮就增厚。
反之则变薄。
当窑皮增厚达一定程度就形成结圈。
形成结圈的原因主要有如下几点:13.1.1 入窑生料成分波动大,喂料量不稳定实际生产过程中,窑操作员最头疼的事是人窑生料成分波动太大和料量不稳定。
窑内物料时而难烧时而好烧或时多时少,遇到高KH料时,窑内物料松散,不易烧结,窑头感到“吃火”,熟料fCaO高,或遇到料量多时都迫使操作员加煤提高烧成温度,有时还要降低窑速;遇到低KH料或料量少时,窑操作上不能及时调整,烧成带温度偏高,物料过烧发粘,稍有不慎就形成长厚窑皮,进而产生熟料圈。
13.1.2 有害成分的影响分析结圈料可以知道,CaO+A1203+Fe203+Si02含量偏低,而R20和S03含量偏高。
生料中的有害成分在熟料煅烧过程中先后分解、气化和挥发,在温度较低的窑尾凝聚粘附在生料颗粒表面,随生料一起人窑,容易在窑后部结成硫碱圈。
在人窑生料中,当MgO和R20都偏高时,R20在MgO引起结圈过程中充当“媒介”作用形成镁碱圈。
根据许多水泥厂的操作经验,当熟料中MgO>4.8%时,能使熟料液相量大量增加,液相粘度下降,熟料烧结范围变窄,窑皮增长,浮窑皮增厚。
有的水泥厂虽然熟料中MgO<4.0%,但由于R20的助熔作用,使熟料在某一特定温度或在窑某一特定位置液相量陡然大量增加,粘度大幅度降低,迅速在该温度区域或窑某一位置粘结,形成熟料圈。
13.1.3 煤粉质量的影响灰分高、细度粗、水分大的煤粉着火温度高,燃烧速度慢,黑火头长,容易产生不完全燃烧,煤灰沉落也相对比较集中,就容易结熟料圈。
取样分析结圈料未燃尽煤粉较多就是例证。
另外,喂煤量的不稳定,使窑内温度忽高忽低,也容易产生结圈。
13.1.4 一次风量和二次风温度的影响三风道或四风道燃烧器内流风偏大,二次风温度又偏高,则煤粉一出喷嘴就着火,燃烧温度高、火焰集中,烧成带短,而且位置前移,容易产生窑口圈,也称前结圈。
13.2 前结圈在正常煅烧条件下,物料温度达1350—1450 ℃时,液相量约为24%,粘度比较大。
当熟料离开烧成带时,温度仍在1300℃以上,在烧成带和冷却带的交界处,熟料和窑皮有较大的温差。
带有液相的高温熟料覆盖在温度相对较低的窑口窑皮上就会粘结形成前结圈。
对于预分解窑来说,前结圈是不可避免的,只是高一点和矮一点的问题,尤其当窑操作员控制二次风温度过高、燃烧器内流风偏大和采用短焰急烧时,烧成带高温区更为集中,液相更多,粘度更小,熟料进入冷却带时,仍有大量液相在交界处迅速冷却。
温差越大粘结越严重,前圈长得更快。
另外,短焰急烧,熟料晶相生长发育差,易烧出大块熟料。
但熟料中细粉比例也增加,冷却机返回窑的粉尘量大,这样更促进前圈的增长。
13.3 熟料圈它结的位置是在烧成带与过渡带之间,是窑操作员最头疼,对窑危害最大的结圈。
在熟料煅烧过程中,当窑内物料温度达到1280℃时,其液相粘度较大,最容易形成熟料圈。
这时如果生料KH、n值较低,操作时窑内拉风又太大,火焰太长,烧成带后边浮窑皮逐渐增长、长厚,发展到一定程度就形成熟料圈。
13.4 熟料圈形成以后的现象1)火焰短而粗,火焰前部白亮但发浑,窑内气流不畅,火焰受阻伸不进窑内。
窑前温度升高,窑简体表面温度也升高。
2)窑尾温度降低,窑尾负压明显上升。
3)窑头负压降低,并频繁出现正压,发生倒烟现象。
4)烧成带来料不均匀,波动大。
5)窑传动电流负荷增加。
6)结圈严重时窑尾密封圈出现漏料。
13.5 结圈的预防措施13.5.1 选择适宜的配料方案,稳定入窑生料成分一般说烧高KH、高n的生料不易结圈,但熟料难烧,fCaO含量高,对保护窑皮和熟料质量不利;反之,熟料烧结范围窄,液相量多,熟料结粒粗,窑不好操作,易结圈。
但生产经验告诉我们,烧较高KH和相对较低的n,或较高的n和相对较低的KH的生料都比较好烧,又不容易结圈。
因此,窑上经常出现结圈时,应改变熟料配料方案,适当提高KH或n,减少熔剂矿物的含量对防止结圈有利。
13.5.2 减少原燃料带入的有害成分一般粘土中碱含量高,煤中含硫量高。
因此,如果窑上经常出现结圈时,视结圈料分析结果,最好能改变粘土或原煤的供货矿点,以减少有害成分对结圈的影响。
13.5.3 控制煤粉细度,确保煤粉充分燃烧13.5.4 调整燃烧器控制好火焰形状确保风、煤混合均匀并有一定的火焰长度。
经常移动喷煤管,改变火点位置。
13.5.5 提高快转率三个班统一操作方法,稳定烧成系统的热工制度。
在保持喂料喂煤均匀,加强物料预烧的基础上尽量加快窑速。
采取薄料快转、长焰顺烧,提高快转率,这对防止回转窑结圈都是有利的。
13.5.6 确定一个经济合理的窑产量指标通过一段时间的生产实践,每台回转窑都有自己特定的合理的经济指标。
这就是回转窑在某高产量范围内能达到熟料优质,煤耗最低,运转率最高。
所以回转窑产量不是越高越好。
经验告诉我们,产量超过一定限度以后,不是由于系统抽风能力所限致使煤灰在窑尾大量沉降并产生还原气氛,就是由于拉大排风使窑内气流断面风速增加,火焰拉长,液相提前出现,这都容易形成熟料圈。
13.6 结圈的处理方法不管是前结圈还是后结圈,处理结圈时一般都采用冷热交替法,尽量加大其温度差,使圈体受温度的变化而垮落。
也有用水枪打的,但前结圈一般太坚固,后结圈离窑头太远,处理效果大多不理想。
13.6.1 前结圈的处理方法前结圈不高时,一般对窑操作影响不大,不用处理。
但当结圈太高时,既影响看火操作,又影响窑内通风及火焰形状。
大块熟料长时间在窑内滚不出来,容易损伤烧成带窑皮,甚至磨蚀耐火砖。
这时应将喷煤管往外拉,调整好用风和用煤量,及时处理。
1)如果前圈离窑下料口比较远并在喷嘴口附近,则一般系统风、煤、料量可以不变,只要把喷煤管往外拉出一定距离,就可以把前圈烧垮。
2)如果前圈离下料口比较近,并在喷嘴口前则将喷嘴往里伸,使圈体温度下降而脱落。
如果圈体不垮,则有两种处理方法①把喷煤管往外拉出,同时适当增加内流风和二次风温度,这样可以提高烧成温度,使烧成带前移,把火点落在圈位上。
一般情况下,圈能在2~3h内逐渐被烧掉。
但在烧圈过程中应根据进入烧成带料量多少,及时增减用煤量和调整火焰长短,防止损伤窑皮或跑生料。
②如果用前一种方法无法把圈烧掉时,则把喷煤管向外拉出并把喷嘴对准圈体直接烧。
待窑后预烧较差的物料进入烧成带后,火焰会缩得更短,前圈将被强火烧垮。
但是必须指出,采用这种处理方法,由于喷煤管拉出过多,生料黑影较近,窑口温度很高,所以窑操作员必须在窑头勤观察,出现问题及时处理。
13.6.2 后结圈的处理方法处理后结圈一般采用冷热交替法。
处理较远的后圈则以冷为主。
处理较近的后圈则以烧为主。
1)当后圈离窑头较远时,这种圈的圈体一般不太坚固。
这时应将喷煤管向外拉出,使烧成带位置前移,降低圈体的温度,圈体会由于温度的变化而逐渐自行垮落。
2)当后圈离窑头较近时,这种圈体一般比较坚固。
处理这种圈应将喷煤管尽量伸人窑内,并适当向上抬高一些,加大一点外流风和系统排风使火焰的高温区移向圈体位置。
但排风不宜过大,以免降低火焰温度。
约烧3—4h左右后再将喷煤管向外拉出使圈体温度下降。
这样反复处理,圈体受温度变化产生裂纹而垮落。
不过,从总体来说,烧圈尤其是烧后圈不是一件容易的事。
有时圈体很牢固,烧圈时间过长容易烧坏窑皮及衬料或在过渡带结长厚窑皮进而在圈体后产生第二道后结圈。
所以处理时一定要小心。
我们厂用的4*56米的旋窑,现在有一个问题,想请教专家。
无论怎么调节风,总是长圈,火焰长时长后面35米左右,火焰短时长18米或23米,煤粉水分不大,细度不粗,生料碱含量不高,为什么会这样,而且尾温降不下来总在1150度左右,我们的火焰有时很短,也这样。
请问是何原因? 中国水泥技术网: 一般回转窑形成结圈的原因主要有如下几点:1、入窑生料成份波动大,喂料量不稳定入窑生料成份波动大,喂料量不稳定,势必造成窑内热工制度的紊乱,当成份高和喂料量大时,必须加头煤提高烧成温度,甚至降低窑速,当成份低或喂料量少时,操作上不能及时调整,烧成带温度过高,物料过烧发粘,容易形成长厚窑皮,进而形成熟料圈。
2、有害成分的影响R2O和SO3含量偏高,易形成硫碱圈。
MgO 高时特别是大于4.8%时,能使熟料液相量大量增加,液相粘度下降,熟料烧结范围变窄,窑皮增厚形成熟料圈。
3、煤粉质量的影响灰份高、细度粗、水分大的煤粉容易产生不完全燃烧,煤灰沉落相对比较集中,容易形成熟料圈。
另外,喂煤量的不稳定,使窑内温度忽高忽低,也易形成结圈。
结圈的预防措施1、选择适宜的配料方案,稳定入窑生料成分一般窑上经常出现结圈时,适当提高KH或n,减少熔剂矿物的含量。
2、减少原燃料带入的有害成分看结圈料分析结果,改变原燃料的供货矿点。
3、控制煤粉细度,确保煤粉的完全燃烧。
4、调整燃烧器控制好火焰形状,确保风、煤的混合均匀并有一定的长度。
经常移动喷煤管,改变火点的位置。
5、提高快转率,三班统一操作方法,采取簿料快转。
尾温降不下来,是不是窑内通风过大或头煤过多或燃烧器内外风比例不合理,如窑内通风过大可适当开大三次风管阀门的开度,如头煤过多,减少头煤量,燃烧器内外风比例不合理,加大内风,减少外风。
(南京凯盛水泥工程技术有限公司,顾亮。