回转窑结圈
回转窑内结圈结球的原因及处理方法

各种类型的水泥回转窑都遇到过结圈问题。
结圈使窑该处的横断面积显著减少,严重影响窑内通风,阻碍物料运动,对回转窑的产量、质量、安全运转、煤耗、电耗均有一定影响。
尤其频繁结圈的回转窑,不仅破坏了窑内正常热工制度,而且损害操作人员的身体健康,给生产造成经济损失。
Eg2jexl 引起回转窑结圈的因素很多,它与原料性质、生料成分、燃料的灰分和细度、窑型、窑内还原气氛及热工制度等有关。
在实际生产过程中,煅烧硅酸率高的熟料时,对减少结圈有好处,但是烧硅酸率很高的白水泥熟料也结圈。
至于说煤灰的影响,但所有烧油的水泥回转窑同样也结圈。
所以结圈问题比较复杂。
现结合生产中的体会和认识,谈谈水泥回转窑结圈的预防和处理。
t%k`)p7O1 结圈的形成 LtKR15h,回转窑内形成结圈的因素很多,但液相的产生和固化是结圈的主要形成过程。
而衬料温度、物料温度、煤灰和生料组成又是决定液相的生成和固化的主要因素。
在熟料煅烧过程中,生料在1200℃左右出现液相,在1250℃左右液相粘度开始变小,液相量增加,由于料层覆盖温度突降,加之筒体表面散热,液相在窑壁上凝固下来,形成窑皮。
窑继续运转,窑皮又暴露在高温中而被熔掉下来,再次被物料覆盖,液相又凝固下来,如此周而复始。
如果粘挂上去的多,掉下来的小,窑皮就增厚,反之就变薄。
在正常情况下,窑皮可保持在200mm左右的厚度。
该温度条件及区域内若熔化和固化的过程达到平衡,窑皮就不会增厚。
当熔化的少固化的多,其厚度增长到一定程度,即形成圈。
当衬料与物料的温差大时,在足够液相的条件下,圈体越结越厚。
ma) + G!1.1 前结圈的形成 Gb"kl .j前结圈(又称窑口圈),是结在回转窑烧成带末端部位的圈。
在正常煅烧条件下,物料温度为1350~1450℃,液相量约为24%,其粘度较大。
当熟料离开烧成带时,液相开始冷却,进入冷却带的液相已基本固化。
在烧成带和冷却带的交界处存在着较大的温差,窑口物料温度高于窑皮温度。
回转窑结圈的原因及处理方法

回转窑结圈的原因及处理方法1、结圈的危害回转窑“结圈”的部位一般在距窑口一定距离的固体燃料集中燃烧点附近的耐火窑衬上,厚度可达200-500 mm左右。
“结圈”对球团生产的危害有以下几方面:(1)降低产量,增加劳动强度窑圈一经形成,对燃料烧烧所产生的热气流势必起阻碍作用,如图-1所示。
热气流被部分阻挡在A区,影响了球团的焙烧效果。
同时,由于链篦机上生球的干燥、预热过程是利用窑尾废气进行的,故此,结圈也对生球的干燥、预热产生不良影响。
具体地说,就是透气性差,火焰不进,后部温度低,干燥时水分不易脱除,生球爆裂、粉化严重,成品率低,从而降低了劳动生产率。
另外,圈结形成后,如不及时处理,就会使圈的纵向长度、厚度增加,当圈掉下时,必然增加工人的劳动强度,有时甚至需停机处理,也影响了球团矿的产量。
(2) 增加了设备负荷如图-1所示,一定面积及厚度的结圈使物料流被阻于B区,此时,被阻的料量要高出正常时许多,加之圈本身的重量,必然增加了托轮、轴承的磨损,同时,增加了电机的负荷,甚至烧毁。
(3) 浪费能源在实际看火操作中,当出现“结圈”现象后,由于热气流被阻于A区,为保证链篦机的干燥和预热效果,看火工往往采用加大给煤量的方式,这无疑造成了能源浪费。
2、结圈的原因结圈的原因,在生产中主要可以归纳为操作不当。
具体地说,是由于上料量过大,干燥效果差,生球爆裂,粉化严重,致使透气性差,使得引风机抽动火焰的作用不明显,火焰只在窑内一定距离燃烧。
在大于1 200℃的高温下,未完全氧化的Fe3O4就与磁铁矿中一定数量的SiO2发生反应形成液相。
2Fe3O4+3SiO2+2CO=3Fe2SiO4+2CO22FeO+SiO2=Fe2SiO4另外,当给煤量较大时,在1 150℃条件下,Fe2O3也会部分分解为Fe3O4,与SiO2作用而生成2FeO·SiO2,形成渣相粘结。
这就使得物料在流经焙烧带时,所产生的液相、渣相极易粘附在窑衬的表面,同时粘结物料而产生结圈现象。
回转窑结圈的影响因素及解决措施

回转窑结圈的影响因素及解决措施-----龙仕连我司从11月23日开始窑内断断续续出现少量漏料,并出现了三次大料球,严重影响到窑的正常运转,公司及部门领导高度重视。
经分析是窑23米处结后圈导致窑尾漏料和结料球。
于25日开始处理后圈:1、窑减产到350 t/h煅烧;2、窑头煤管每个班移动两次,-200~+100冷热交替处理;3、每班清理煤管头部积料结焦4次,以保证头煤燃烧好,火焰集中;4、控制煤粉细度及水分,以保证煤粉燃烧效果(煤磨出磨温度控制在63~65度,入磨温度<300度。
内部控制煤粉细度<6.0);5、适当提高熟料KH。
通过3天的处理,23料处后圈薄了很多,并有缺口,于28日窑恢复了365 t/h正常生产。
出现这样的工艺事故,我们必须深度反思。
特别是工艺管理人员和窑操作员一定要密切关注窑皮的变化趋势及原燃材料的变化,及时调整窑参数,保证窑正常运转。
下面让我们再次学习一下窑内结圈的成因、危害及解决措施:结圈是指回转窑在正常生产中,由于原燃材料的变化,或者操作和热工制度的影响,窑内因物料过度粘结,在特定的区域形成一道阻碍物料运动的环形、坚硬的圈。
这种现象在回转窑内是一种不正常的窑况,它破坏了正常的热工制度,影响窑内通风,造成窑内来料波动很大,直接影响到回转窑的产量、质量、消耗和长期安全运转。
而且处理窑内结圈费时费力,严重时需停窑停产,危害极其严重。
结圈的成因及危害:结圈的形成: 结圈实际上是在烧成带末端与放热反应带交界处形成的窑皮,是回转窑内危害最大的结圈。
在熟料煅烧过程中,当物料温度达到1280℃时,其液相黏度较大,最容易形成结圈,而且冷却后比较坚固,不易除掉。
在正常的煅烧情况下,后结圈体的内径部分往往被烧熔而掉落,保持正常的圈体内径。
如果在1 250~l 280℃温度范围内出现的液相量偏多,往往会形成妨碍生产的后结圈。
后结圈一般结在烧成带的边界或更远,开始是烧成带后边的窑皮逐渐增长、增厚,发展到一定程度即形成后结圈。
煤基还原回转窑结圈
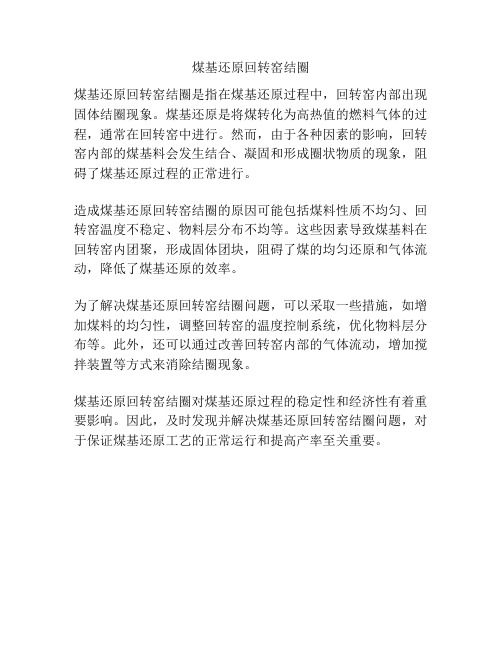
煤基还原回转窑结圈
煤基还原回转窑结圈是指在煤基还原过程中,回转窑内部出现固体结圈现象。
煤基还原是将煤转化为高热值的燃料气体的过程,通常在回转窑中进行。
然而,由于各种因素的影响,回转窑内部的煤基料会发生结合、凝固和形成圈状物质的现象,阻碍了煤基还原过程的正常进行。
造成煤基还原回转窑结圈的原因可能包括煤料性质不均匀、回转窑温度不稳定、物料层分布不均等。
这些因素导致煤基料在回转窑内团聚,形成固体团块,阻碍了煤的均匀还原和气体流动,降低了煤基还原的效率。
为了解决煤基还原回转窑结圈问题,可以采取一些措施,如增加煤料的均匀性,调整回转窑的温度控制系统,优化物料层分布等。
此外,还可以通过改善回转窑内部的气体流动,增加搅拌装置等方式来消除结圈现象。
煤基还原回转窑结圈对煤基还原过程的稳定性和经济性有着重要影响。
因此,及时发现并解决煤基还原回转窑结圈问题,对于保证煤基还原工艺的正常运行和提高产率至关重要。
回转窑窑后结圈原因分析及处理方法

回转窑窑后结圈原因分析及处理方法巩义市恒昌冶金建材设备厂生产的1000t/d熟料生产线是由天津水泥工业设计研究院有限公司设计的,主要包括TDF型分解炉、单系列五级旋风预热器、Φ3.2m×50m回转窑及TC-836篦式冷却机。
自2007年2月以来,窑后频繁发生结圈、结球的工艺事故,巩义市恒昌冶金建材设备厂技术人员现将原因分析及解决措施介绍如下,供同仁参考。
1、结圈情况2007年3月19日最为严重,窑前返火,窑尾有漏料现象,无法操作煅烧,迫使停窑处理。
从窑内看,主窑皮长达22m,副窑皮长到窑尾,35~37m处形成后结圈,结圈最小孔洞呈不规则状,直径约l.5m,进窑观察该圈明显分为两层,且层次明确、清晰,第一层厚约150mm,呈黄白色,第二层厚约460mm,呈黑色,圈体非常致密。
对圈体取样分析见表1。
表1 圈体取样分析结果从表l可以看出,第一层硫碱含量较高,是硫碱圈,第二层明显是煤粉圈,熟料液相出现过早、过多导致结圈。
2、原因分析(1)由于2006年煤价不断上涨,加之公路运输距离远,为了降低成本,采用当地劣质煤煅烧,煤质下降,灰分高,挥发分低,发热值低,煤工业分析如表2、3。
实际生产中,煤可燃性差,煤粉燃烧不完全,大量煤灰不均掺入生料中,液相在窑后面提前出现,而未燃尽的煤灰产生沉积及液相的提前出现结圈。
(2)2007年以来,由于机械原因,高温风机l号轴与密封圈强烈摩擦,产生局部高温,使轴侧曲,水平振动最高达6.4mm/s。
为了降低振动,不得不降低高温风机转速,由原来的1130r/min降至l060r/min,有时更低,严重影响了窑内通风,加上煤质又差,更多的窑头燃烧不完全的煤粉沉积在窑后燃烧,使窑内后部温度升高,液相量增加,加速了窑后结圈的形成。
(3)为了处理窑后结圈,我厂在迫不得已的情况下停窑烧后圈,由于煤质差,二、三次风温低,燃料不完全或未燃烧的煤粉落在圈上及圈后的积料上,不断燃烧,造成物料发粘,不但圈未烧掉,反而越结越厚,这也是第一层圈形成的主要原因。
回转窑结圈的原因及处理方法
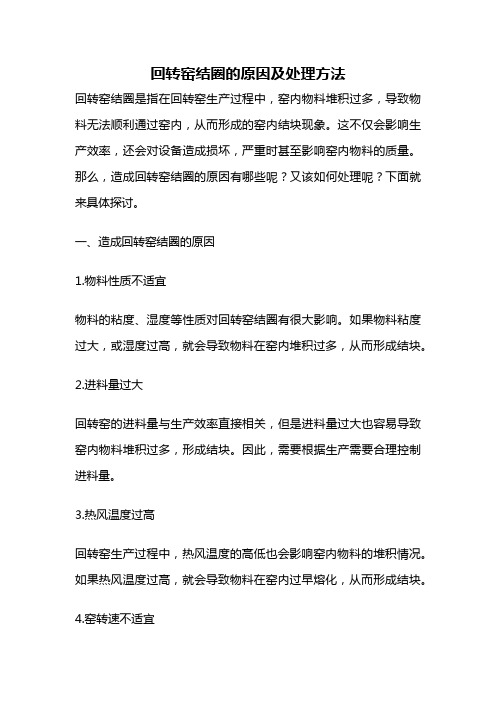
回转窑结圈的原因及处理方法回转窑结圈是指在回转窑生产过程中,窑内物料堆积过多,导致物料无法顺利通过窑内,从而形成的窑内结块现象。
这不仅会影响生产效率,还会对设备造成损坏,严重时甚至影响窑内物料的质量。
那么,造成回转窑结圈的原因有哪些呢?又该如何处理呢?下面就来具体探讨。
一、造成回转窑结圈的原因1.物料性质不适宜物料的粘度、湿度等性质对回转窑结圈有很大影响。
如果物料粘度过大,或湿度过高,就会导致物料在窑内堆积过多,从而形成结块。
2.进料量过大回转窑的进料量与生产效率直接相关,但是进料量过大也容易导致窑内物料堆积过多,形成结块。
因此,需要根据生产需要合理控制进料量。
3.热风温度过高回转窑生产过程中,热风温度的高低也会影响窑内物料的堆积情况。
如果热风温度过高,就会导致物料在窑内过早熔化,从而形成结块。
4.窑转速不适宜回转窑的转速也会影响窑内物料的堆积情况。
如果转速过快,就会导致物料在窑内无法均匀分布,从而形成结块。
二、回转窑结圈的处理方法1.减少进料量当回转窑结圈发生时,可以适当减少进料量,以缓解窑内物料堆积过多的情况。
2.调整热风温度如果回转窑结圈是由于热风温度过高导致的,可以适当降低热风温度,以减少窑内物料的过早熔化。
3.调整窑转速如果回转窑结圈是由于窑转速不适宜导致的,可以适当调整窑转速,以保证物料在窑内均匀分布。
4.清理窑内物料当回转窑结圈严重时,需要停窑清理窑内物料。
清理时需要注意安全,避免对设备造成损坏。
5.加入流化剂在窑内加入一定量的流化剂,可以有效地缓解回转窑结圈现象。
流化剂可以使物料在窑内均匀分布,减少结块的情况。
6.调整物料配比如果回转窑结圈是由于物料配比不合理导致的,可以适当调整物料配比,以保证物料在窑内均匀分布,减少结块的情况。
回转窑结圈是一种常见的生产问题,多种因素都可能导致其发生。
因此,在回转窑生产过程中,需要做好预防措施,保证物料在窑内均匀分布,避免结块的发生。
同时,一旦发生回转窑结圈,需要及时采取相应的处理措施,以保证生产效率和产品质量。
回转窑结圈的原因及处理方法

回转窑结圈的原因及处理方法回转窑是制造水泥的重要设备,而回转窑结圈是影响生产效率和质量的常见问题。
结圈的原因有很多,如窑内温度不均、烧成温度过低、原材料成分不合适等。
本文将从原因和处理方法两个方面详细介绍回转窑结圈问题。
一、结圈的原因1. 窑内温度不均:回转窑内部温度分布不均会导致部分区域的烧成程度不够,形成未熟料,容易粘在窑壁上,最终导致结圈。
2. 烧成温度过低:如果烧成温度过低,则无法将原材料完全反应,也容易导致未熟料粘附在窑壁上。
3. 原材料成分不合适:原材料中含有过多的游离SiO2、Al2O3等物质,会使得反应速率变慢,在高温下难以完全反应。
同时,如果含有过多的碱金属氧化物,则会使得产生大量液态相,增加了结圈的风险。
4. 进出料方式不当:进出料口位置设置不合理,或者进出料速度过快或过慢,都会导致窑内物料分布不均,从而增加结圈的风险。
二、处理方法1. 调整窑内温度:调整窑内温度是解决结圈问题的关键。
可以通过改变燃烧器位置、调整燃料供给量等方式来调整窑内温度分布,使得各个区域的温度均匀。
2. 提高烧成温度:提高烧成温度可以促进原材料反应,减少未熟料生成的可能性。
但是需要注意控制好温度,避免超出窑的承载能力。
3. 调整原材料成分:在生产过程中要严格控制原材料的成分,避免含有过多的游离SiO2、Al2O3等物质和碱金属氧化物。
如果发现原材料成分不合适,则需要及时停机清理,并重新投入符合要求的原材料。
4. 改善进出料方式:调整进出料口位置和速度可以改善窑内物料分布不均的问题。
可以采用多点进出料口、减缓进出料速度等方式来改善这一问题。
5. 定期清理窑壁:定期清理窑壁可以有效减少未熟料的积累,降低结圈的风险。
清理时需要注意安全,避免对设备造成损伤。
综上所述,回转窑结圈是影响水泥生产效率和质量的常见问题。
通过调整窑内温度、提高烧成温度、调整原材料成分、改善进出料方式和定期清理窑壁等方式可以有效解决这一问题。
回转窑结圈的影响

什么是结圈
• 结圈是指回转窑在正常生产中,由于原燃材料 的变化,或者操作和热工制度的影响,窑内因物料过 度粘结,在特定的区域形成一道阻碍物料运动的环 形、坚硬的圈。这种现象在回转窑内是一种不正常 的窑况,它破坏了正常的热工制度,影响窑内通风, 造成窑内来料波动很大,直接影响到回转窑的产量、 质量、消耗和长期安全运转。而且处理窑内结圈费 时费力,严重时需停窑停产,危害极其严重。
结圈的处理方法
无论是前结圈还是后结圈,处理 结圈时一般采用冷热交替法,尽量加 大其温差,使圈体受温度变化而垮落。
前结圈的处理方法
前结圈不高时,对煅烧操作的影响不大,尚 可增加烧成带料层厚度,延长物料在烧成带 的停留时间,使物料反应更完全并降低熟料 中的CaO含量,同时减少烧成带向窑前的辐 射散热。但当前结圈较高时,既影响看火操 作,又影响窑内通风及火焰形状,大块熟料 滚不出来,易损坏烧成带窑皮及衬料。这 时应及时调整风、煤或移动喷煤管进行处理。
后结圈的处理办法
从总体来讲,烧后圈不是一件容易的事, 有时圈体很牢固,若烧圈时间过长,容易 烧坏窑皮及衬料,或在过渡带结长厚窑皮 进而在圈体后产生第2道圈。所以,处理时 一定要小心。一定要在保护窑皮的前提下 进行,前后兼顾,精心操作,勿使火焰过 分集中,避免将窑皮及衬料烧坏,造成更 大的损失。
后结圈的处理办法
在处理后结圈时,要根据圈体的特点和远近,分 别采取不同的处理方法,才能达到较好的效果。 一般采用冷热交替法处理,烧远圈时以冷为主, 烧近圈时以热为主。 (1)当窑内窑皮长而厚或有轻度圈根时,将喷煤管 向外拉出,使烧成带位置前移,降低圈体的温 度,改变煤灰沉落位置,使厚长的窑皮逐渐垮 落。同时调整风煤配合,加速煤粉燃烧,使高 温带两端低温部分不拖长,防止圈根继续成长。
- 1、下载文档前请自行甄别文档内容的完整性,平台不提供额外的编辑、内容补充、找答案等附加服务。
- 2、"仅部分预览"的文档,不可在线预览部分如存在完整性等问题,可反馈申请退款(可完整预览的文档不适用该条件!)。
- 3、如文档侵犯您的权益,请联系客服反馈,我们会尽快为您处理(人工客服工作时间:9:00-18:30)。
回转窑结圈/治理清除预防回转窑结圈的设备/回转窑清圈机/窑结圈处理机/回转窑结圈觧
决措施
生产中使用回转窑设备的正常生产非常重要,关于回转窑结圈的问题原因,我们巳经探讨许多,也介绍了回转窑故障事故,回转窑结圈前结圈,窑后结圈的原因,以巳处理方法,现着介绍一下制理处理清除回转窑结圈的设备,名称回转窑清圈机别名窑结圈处理机/的创造发明过程,,用什么机械设备处理回转窑结圈解决回转窑结圈措施一、概述
由巩义市中佳节能设备制造公司研制的提高回转窑产能的高新技术产品.预防治理处理回转窑结圈的设备,快速处理回转窑结圈的设备,处理回转窑结大球大蛋设备,回转窑清圈机.窑内结蛋球打蛋机,窑内结圈处理机(窑内结圈打圈机铲圈机)是针对回转窑普遍存在的回转窑皮不均匀、回转窑厚窑皮、回转窑长窑皮、回转窑内结圈、回转窑内结瘤、回转窑内结蛋结大小球、等痼疾导致回转窑红窑、料层不均匀、回转窑系统阻力增大、回转窑内有效截面积缩小,严重影响回转窑产能和有郊预防回转窑结圈而设计的,一种机电一体化并具有智能化的中型机械,该机由、钎杆、冲击装置、行走自动退让系统、冷却系统和人工变频控制系统组成,一般规格长十至二十二米,宽一点五至二点二米,高一点八至三点五米。
实际大小、回转窑结圈快速清圈机长度根据用户现场要求设计和配置。
回转窑结圈、结瘤、结蛋、长厚窑皮和长长窑皮是各种回转窑普遍存在的现象,曾有人说过回转窑结圈是世界性难题。
无论是早期的湿法水泥回转窑系统,还是近年来兴起的链篦机-回转窑-环冷机氧化球团回转窑系统;无论是以煤为燃料的回转窑还是以气或油为燃料的回转窑;无论是各种水泥回转窑、红钒钠回转窑、氧化铝熟料回转窑、氧化镁回转窑、氧化球团回转窑、二氧化钛回转窑和活性石灰回转窑等氧化类回转窑,还是碳素回转窑、永磁铁氧体回转窑或还原钛铁矿回转窑等还原类回转窑;从小到直径不足1米的永磁铁氧体回转窑到直径6米以上的大型链篦机-回转窑-环冷机氧化球团回转窑等,几乎所有的回转窑都有结圈的问题。
回转窑结圈,严重的影响了回转窑的运转率,给企业带来巨大的经济损失,耗费了大量的人力物力。
如河南某企业的活性石灰回转窑,投资数千万元人民币,由于频繁结圈,严重影响正常的生产,导致长期不能达产,甚至长期停产。
国内某企业在投资活性石灰窑选型时,由于考虑活性石灰回转窑有结圈问题,居然决定放弃石灰活性度高的回转窑系统,转而选用石灰活性度较低的竖窑系统。
又如国内某红钒钠回转窑生产企业准备耗资数百万元建造煤气发生炉生产半水煤气,用来替代现有的煤粉作燃料,以减少结圈。
我国是煤炭大国,煤炭资源丰富,以煤为燃料,成本相对较低,我国大多数回转窑采用煤为燃料,然而,以煤粉为燃料的回转窑其结圈的频率大大高于以油和气为燃料的回转窑,因此有效预防和消除回转窑的结圈问题势在必行。
早在上世纪90年代初,河南巩义中佳节能设备有限公司李建坡总工在对回转窑进行自动化控制的同时,就开始致力于回转窑窑圈和厚窑皮的研究和治理,先后在氧化锌回转窑,水泥回转窑,铝酸钙粉回转窑、红钒钠回转窑、二氧化钛回转窑和活性石灰回转窑上实验,经历过多少次的失败和挫折,遭受过不少责难和非议,也最终得到过企业的理解和支持;耗费了大量的财力物力,取得了宝贵的经验教训;我们设计过多种多样的机型,特别是铲头的设计
费尽心血,只有当我们初步认识各种窑圈的共性和个性、初步认识到窑圈的本质后才取得进展,回转窑的用途是多样的,回转窑窑圈的形态和化学成分也是多样的,从一般性的角度来说,我们暂且把它分为“接近氧化带的结圈”和“接近干燥带的结圈”两大类,当然这种分类不一定很严谨。
众所周知,接近氧化带的窑圈具有一个共同的特征——“热变软,冷变硬”的特征。
分析窑圈在接近氧化带窑衬表面的形成过程得出的结论:窑内物料的化学成分是窑圈形成的一个重要因素,但不是决定因素,决定因素是温度,否则就无法解释几乎所有的、各种不同用途的回转窑都结圈。
显而易见,不同用途回转窑的窑圈有着不同的化学成分。
当然,同一用途的回转窑用气或油作燃料的比用煤作燃料的结圈机率要低得多,使用不同煤种的回转窑发生结圈的周期也明显不同,但是仍有结圈。
在普通硅酸盐水泥回转窑,通常用提高水泥生料的硅率来治理窑圈,而白水泥生料恰恰是含硅极高的,但仍然结圈,由此可见,窑内物料的化学成分只会影响发生结圈的周期。
根据接近氧化带的窑圈具有“热变软,冷变硬”
这一特征,抛开其化学成分的影响因素暂且不谈,以下仅从温度的影响因素来分析窑圈的形成过程。
接近氧化带窑圈的形成是一个缓慢的、逐渐加厚的形成过程,是一个由液态向固态逐步转化的过程。
窑内物料粘结物(或称液相物)不但有“热变软,冷变硬”的特性,而且在一定温度范围内有“越冷越硬、越热越软”的特性,同时,固态的窑圈在一定的高温条件下又可以逆向转化为液态。
最初形成结圈的窑内粘结物,其温度略高于窑衬(耐火砖)表面温度,即某一段窑衬的表面温度略低于窑内物料由固态转变为液态的临界点温度,这个略低于临界点温度的部位,又会因为燃烧机的火焰长度变化、窑内的燃烧气氛(燃烧充分与否)等因素而前后移动,因此窑内粘结物很容易粘结在这一段窑衬上,粘结在这一段窑衬上的窑内粘结物隔离了窑衬表面与窑内高温气体的接触,使这一部分窑衬表面温度开始下降,并导致窑衬和窑筒体温度的同步下。