活性石灰回转窑结圈原因分析及处理方法
回转窑窑内结球并且形成窑灰的解决方法

回转窑窑内结球并且形成窑灰的解决方法回转窑窑内结球是一种很常见的现象,水泥回转窑窑内结球的原因和处理时的相关措施,是每个用户所关心的问题。
窑内结球主要形成原因有:生料成分波动,液相量过多;加料不稳定,导致窑尾、分解炉温度时高时低,难以控制;设备故障率高,停机较为频繁;原、燃材料中,硫、氯、碱等有害成分含量较高;煤粉质量波动大,均化效果差;窑灰掺入不均匀;操作人员疏忽,温度控制不当或长时间打慢车等。
窑内结球可采取以下措施加以预防和处理。
(1)预防措施。
第一,可选择合适的配料方案,稳定生料成分。
一般采用高石灰饱和系数、高硅率的生料不易发生结球现象,且熟料质量比较好,但是这种料较耐火,对操作要求较高。
若低石灰饱和系数和低铝率的生料,它的烧结范围比较窄,而液相量偏多,结粒粗大,稍有不慎就会导致结球。
所以在生产中尽可能选择两高一中的配料方案,即高KH、高SM、中IM,这种配料易操作且熟料质量也相对较稳定。
第二,尽量选用含有害成分物质较低的原燃材料,特别是煤;要加强燃煤的均化,并在能够满足生产要求的同时尽可能的降低煤粉细度;煨烧过程中要加强风与煤混合,尽量避免煤粉过粗而引起的不完全燃烧;如使用挥发分较低的煤粉,因其着火速度慢、燃烧时间长,火力强度不集中,应尽量降低煤粉的细度和水分。
(2)处理措施。
若窑内已经形成料球,应对成球的原因进行全方位分析,取样化验,且要分别对球核、球壳进行化学全分析,找准原因,对症下药。
如料球比较小,操作上应适当增加窑内通风,使火焰顺畅,但必须注意窑尾温度的控制,使其不要过高;可略微减少窑头用煤,但必须保证煤粉的完全燃烧,并适当减少喂料量,稍降低窑速,让窑内的料球滚入烧成带;等料球到烧成带后,再降低一些窑速,用大火在短时间内将其烧垮或烧小,以免进入冷却机发生堵塞或砸坏篦板,但此时应特别注意窑皮的情况。
如果结球较大时,可采用冷热交替法进行处理;当料球在过渡带时不易前行进入烧成带,这时可将喷煤管伸进去,适当降低喂料量,烧1〜2h后将煤管拉出再烧1〜2h,周而复始,直到料球破裂;若实在不能使其破裂,便可停窑冷却1〜2h后点火升温,让料球因温差过大而破裂。
回转窑结圈的影响因素及解决措施

回转窑结圈的影响因素及解决措施-----龙仕连我司从11月23日开始窑内断断续续出现少量漏料,并出现了三次大料球,严重影响到窑的正常运转,公司及部门领导高度重视。
经分析是窑23米处结后圈导致窑尾漏料和结料球。
于25日开始处理后圈:1、窑减产到350 t/h煅烧;2、窑头煤管每个班移动两次,-200~+100冷热交替处理;3、每班清理煤管头部积料结焦4次,以保证头煤燃烧好,火焰集中;4、控制煤粉细度及水分,以保证煤粉燃烧效果(煤磨出磨温度控制在63~65度,入磨温度<300度。
内部控制煤粉细度<6.0);5、适当提高熟料KH。
通过3天的处理,23料处后圈薄了很多,并有缺口,于28日窑恢复了365 t/h正常生产。
出现这样的工艺事故,我们必须深度反思。
特别是工艺管理人员和窑操作员一定要密切关注窑皮的变化趋势及原燃材料的变化,及时调整窑参数,保证窑正常运转。
下面让我们再次学习一下窑内结圈的成因、危害及解决措施:结圈是指回转窑在正常生产中,由于原燃材料的变化,或者操作和热工制度的影响,窑内因物料过度粘结,在特定的区域形成一道阻碍物料运动的环形、坚硬的圈。
这种现象在回转窑内是一种不正常的窑况,它破坏了正常的热工制度,影响窑内通风,造成窑内来料波动很大,直接影响到回转窑的产量、质量、消耗和长期安全运转。
而且处理窑内结圈费时费力,严重时需停窑停产,危害极其严重。
结圈的成因及危害:结圈的形成: 结圈实际上是在烧成带末端与放热反应带交界处形成的窑皮,是回转窑内危害最大的结圈。
在熟料煅烧过程中,当物料温度达到1280℃时,其液相黏度较大,最容易形成结圈,而且冷却后比较坚固,不易除掉。
在正常的煅烧情况下,后结圈体的内径部分往往被烧熔而掉落,保持正常的圈体内径。
如果在1 250~l 280℃温度范围内出现的液相量偏多,往往会形成妨碍生产的后结圈。
后结圈一般结在烧成带的边界或更远,开始是烧成带后边的窑皮逐渐增长、增厚,发展到一定程度即形成后结圈。
宁钢石灰回转窑结圈的认识与处理分析

的, 同时使用 煤粉作 为 主要燃料 , 在操 作不 规范 时也
会加 速结 圈形 成 。首先石 灰石表 面 附带 的泥料在 石 灰石 物流 输送 阶段带 来易堵 料 、 污染 环境 、 磨 损胶 带
2 石 灰 回转 窑 结 圈主 要 危 害
回转 窑结 圈可 以形 成 任 意 形状 , 且 形 成 一定 厚 度 的窑皮 。一般 将 具 有一 定 高 度 的 、 由大 块 和燃 料
等 问题 。其 次 , 进入 预热 器 后这 些 泥 料 经过 高温 干 燥, 大部 分被 推杆 推 入 窑 内 。进 入 窑 内后 开始 受 抽
力 影 响悬 浮 在窑 内。再 与未完 全燃烧 的燃 料所 产生
的灰分 和石 灰石 内部 低熔 点杂 质 烧 结在 一 起 , 最 终 不 断 的翻滚 形成 大 块 或 泥饼 。为 判 断 其 主要 成 分 ,
c o mmi s s i o n e d i n J u n e 2 0 0 8, h a v e b e e n i n s t a b l e o p e r a t i o n a t p r e s e n t wi t h s o u n d e c o n o mi c a n d t e c h n i —
4 . 4 安 全 措 施
换, 该 过程 十分 重视 加 强 砌 筑 质量 的过 程 监 管 和 施
工 作业 人员 的安全监 管 。所 以如何 鉴别 和确 定清 理 的时 间和周 期 十分关 键 。
( 1 )护 目镜 、 手套 、 口罩 、 安 全标志 牌 。 ( 2 )高 温 隔热服 、 安全 帽 。 ( 3 )安 全 的走 行 通道 , 必要 的架子 和平 台 。 ( 4 )无关 人员 禁 止 停 窑 期 间进 入 窑 内, 必 要 时
窑内结圈、结球的原因及处理措施

窑内结圈、结球的原因及处理措施中控室侯素克结圈是指窑内在正常生产中因物料过度黏结,在窑内特定的区域形成一道阻碍物料运动的环形、坚硬的圈。
这种现象在回转窑内是一种不正常的窑况,他破坏正常的热工制度,影响窑内通风,造成来料波动很大,直接影响回转窑的产量、质量、消耗和长期安全运转。
尤其频繁结圈的回转窑,不仅破坏了窑内正常热工制度,而且损害操作人员的身体健康,给生产造成经济损失。
引起回转窑结圈的因素很多,它与原料性质、生料成分、燃料的灰分和细度、窑型、窑内还原气氛及热工制度等有关。
1 结圈的形成回转窑内形成结圈的因素很多,但液相的产生和固化是结圈的主要形成过程。
而衬料温度、物料温度、煤灰和生料组成又是决定液相的生成和固化的主要因素。
在正常情况下,窑皮保持在200mm左右的厚度,该温度条件及区域内若熔化和固化的过程达到平衡,窑皮就不会增厚。
当熔化的少固化的多,其厚度增长到一定程度,即形成圈。
当衬料与物料的温差大时,在足够液相的条件下,圈体越结越厚。
1.1前结圈的形成前圈结在烧成带和冷却带交界处,由于风煤配合不好,或者煤粉粒度过粗,煤灰和水分大,影响煤粉燃烧,使黑火头长,烧成带像窑尾方向移动,熔融的物料凝结在窑口处使“窑皮”增厚,发展成前圈,或者由于煤粉落在熟料上,在熟料中形成还原性燃烧,铁还原成亚铁,形成熔点低的矿物或者由于煤灰分中氧化铝含量高而使熟料液相量增加,黏度增大,当遇到入窑二次风温降温、冷却,就会逐渐凝结在窑口处形成圈。
前圈形成的主要原因是煤粉的质量,熟料中溶剂矿物含量过高或氧化铝含量过高,燃烧器在窑口断面的位置不合理,影响煤粉燃烧,使结圈速度加快,前温急烧,导致温差相差大,造成液相冷却凝固形成前圈,1.2熟料圈的形成原因熟料圈(又称后圈),是结在窑内烧成带与放热反应带之间的圈,也是回转窑内危害最大的结圈。
造成熟料圈的原因很多,主要有生料化学成分,熟料圈行成往往在物料刚出现液相的地方,物料在1200~1300度范围内为防止结圈,配料时应考虑液相不易过多,液相黏度不易过大;原燃材料中的有害成分,原燃材料中的有害成分过多,降低物料的熔点,结圈的可能性就增大,正常情况下,此类结圈大多发生在放热反应带以后的地方;煤的影响,煤灰中氧化铝的含量较高,当煤灰掺入物料中时,使物料液相量增加往往易结圈;操作和热工制度的影响,头煤加入量较多,产生还原气氛,形成低熔点矿物,使液相提前出现,容易结圈,二三次风配合不当,火焰过长,液相提前出现,特别是在分解率高的情况下,结圈的可能性更大。
回转窑窑后结圈原因分析及处理方法

回转窑窑后结圈原因分析及处理方法巩义市恒昌冶金建材设备厂生产的1000t/d熟料生产线是由天津水泥工业设计研究院有限公司设计的,主要包括TDF型分解炉、单系列五级旋风预热器、Φ3.2m×50m回转窑及TC-836篦式冷却机。
自2007年2月以来,窑后频繁发生结圈、结球的工艺事故,巩义市恒昌冶金建材设备厂技术人员现将原因分析及解决措施介绍如下,供同仁参考。
1、结圈情况2007年3月19日最为严重,窑前返火,窑尾有漏料现象,无法操作煅烧,迫使停窑处理。
从窑内看,主窑皮长达22m,副窑皮长到窑尾,35~37m处形成后结圈,结圈最小孔洞呈不规则状,直径约l.5m,进窑观察该圈明显分为两层,且层次明确、清晰,第一层厚约150mm,呈黄白色,第二层厚约460mm,呈黑色,圈体非常致密。
对圈体取样分析见表1。
表1 圈体取样分析结果从表l可以看出,第一层硫碱含量较高,是硫碱圈,第二层明显是煤粉圈,熟料液相出现过早、过多导致结圈。
2、原因分析(1)由于2006年煤价不断上涨,加之公路运输距离远,为了降低成本,采用当地劣质煤煅烧,煤质下降,灰分高,挥发分低,发热值低,煤工业分析如表2、3。
实际生产中,煤可燃性差,煤粉燃烧不完全,大量煤灰不均掺入生料中,液相在窑后面提前出现,而未燃尽的煤灰产生沉积及液相的提前出现结圈。
(2)2007年以来,由于机械原因,高温风机l号轴与密封圈强烈摩擦,产生局部高温,使轴侧曲,水平振动最高达6.4mm/s。
为了降低振动,不得不降低高温风机转速,由原来的1130r/min降至l060r/min,有时更低,严重影响了窑内通风,加上煤质又差,更多的窑头燃烧不完全的煤粉沉积在窑后燃烧,使窑内后部温度升高,液相量增加,加速了窑后结圈的形成。
(3)为了处理窑后结圈,我厂在迫不得已的情况下停窑烧后圈,由于煤质差,二、三次风温低,燃料不完全或未燃烧的煤粉落在圈上及圈后的积料上,不断燃烧,造成物料发粘,不但圈未烧掉,反而越结越厚,这也是第一层圈形成的主要原因。
回转窑结圈的原因
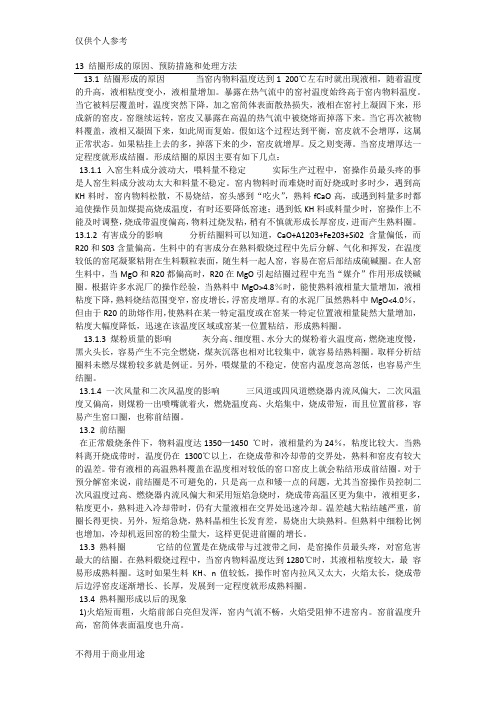
13 结圈形成的原因、预防措施和处理方法13.1 结圈形成的原因当窑内物料温度达到1 200℃左右时就出现液相,随着温度的升高,液相粘度变小,液相量增加。
暴露在热气流中的窑衬温度始终高于窑内物料温度。
当它被料层覆盖时,温度突然下降,加之窑简体表面散热损失,液相在窑衬上凝固下来,形成新的窑皮。
窑继续运转,窑皮又暴露在高温的热气流中被烧熔而掉落下来。
当它再次被物料覆盖,液相又凝固下来,如此周而复始。
假如这个过程达到平衡,窑皮就不会增厚,这属正常状态。
如果粘挂上去的多,掉落下来的少,窑皮就增厚。
反之则变薄。
当窑皮增厚达一定程度就形成结圈。
形成结圈的原因主要有如下几点:13.1.1 入窑生料成分波动大,喂料量不稳定实际生产过程中,窑操作员最头疼的事是人窑生料成分波动太大和料量不稳定。
窑内物料时而难烧时而好烧或时多时少,遇到高KH料时,窑内物料松散,不易烧结,窑头感到“吃火”,熟料fCaO高,或遇到料量多时都迫使操作员加煤提高烧成温度,有时还要降低窑速;遇到低KH料或料量少时,窑操作上不能及时调整,烧成带温度偏高,物料过烧发粘,稍有不慎就形成长厚窑皮,进而产生熟料圈。
13.1.2 有害成分的影响分析结圈料可以知道,CaO+A1203+Fe203+Si02含量偏低,而R20和S03含量偏高。
生料中的有害成分在熟料煅烧过程中先后分解、气化和挥发,在温度较低的窑尾凝聚粘附在生料颗粒表面,随生料一起人窑,容易在窑后部结成硫碱圈。
在人窑生料中,当MgO和R20都偏高时,R20在MgO引起结圈过程中充当“媒介”作用形成镁碱圈。
根据许多水泥厂的操作经验,当熟料中MgO>4.8%时,能使熟料液相量大量增加,液相粘度下降,熟料烧结范围变窄,窑皮增长,浮窑皮增厚。
有的水泥厂虽然熟料中MgO<4.0%,但由于R20的助熔作用,使熟料在某一特定温度或在窑某一特定位置液相量陡然大量增加,粘度大幅度降低,迅速在该温度区域或窑某一位置粘结,形成熟料圈。
石灰竖窑窑内结瘤及处理办法

石灰竖窑窑内结瘤及处理办法石灰回转窑结瘤石灰石生成石灰是一个简单的化学反应,热量输入过多造成温度过高或反应时间过长,就会出现过烧。
石灰相互粘连在一起,或与周围正常状态下的物料粘连起来,或粘附在窑壁上,形成结瘤。
一、轻微过烧粘连当窑温过高、频繁或大幅调产后会出现局部温度过高造成粘连,但采用敲打等方式很易破碎。
在窑底卸灰过程中观测到有个別烧融、粘连的情况。
降低产品活性度,影响窑体通透性,是结瘤的诱因。
解决办法:立即降低温度,检査设备,手工或自动卸料加速粘连物卸出,恢复窑体通透性,避免更严重的结瘤发生。
二、大面积结瘤轻微粘连如若未能及时发现,很快就会发展成大面积粘连结瘤,卡在窑底不能卸料,并在卸料区产生高温,损坏卸料平台和液压缸。
卸料平台温度急剧上升,窑顶料面出现倾斜,卸料平台动作次数明显增多。
损坏卸料平台、风帽和液压设备,严重影响石灰质量和产量,处理费时费力,短则10h以上,长则需要10~15日。
解决办法:1、立即降产降温避免结瘤。
2、打开卸料平台入孔,观测结瘤是否已经移动到卸料平台,如果没有就手动卸料,避免损坏卸料平台,加快结瘤的移动以避免粘结更大。
3、在结瘤凹陷处凿出小洞,用铁管引压缩空气直吹洞中,加速结瘤局部冷却。
产生的应力将结瘤分裂开,将较大的结瘤分裂成小块,顺利掏出。
如果是更大或多个结瘤,可将多个入孔打开,同时进行此操作。
4、如采结瘤块非常坚固,需要用风镐等工具,配合降温措施,将结瘤块打碎成小的结瘤块,从卸料平台掏出。
5、如果结瘤块过大,不能随着物料下降,则需停产,降至常温,进入窑内进行破碎。
三、粘在窑壁上这是较严重的结瘤,一般出现在煅烧带,往往伴随着大面积结瘤而产生,是不好处理的,属于严重的生产事故。
早期会出现窑顶料面倾斜,卸料不均衡,石灰生烧或过烧,质量严重分化,出现偏窑现象。
在窑壁外侧可测出高温点,严重时将外壁油漆烧毁,卸料平台处可见到红灰。
严重影响窑体寿命,处理不当会导致窑内耐材报废。
结圈形成的原因、预防措施和处理方法
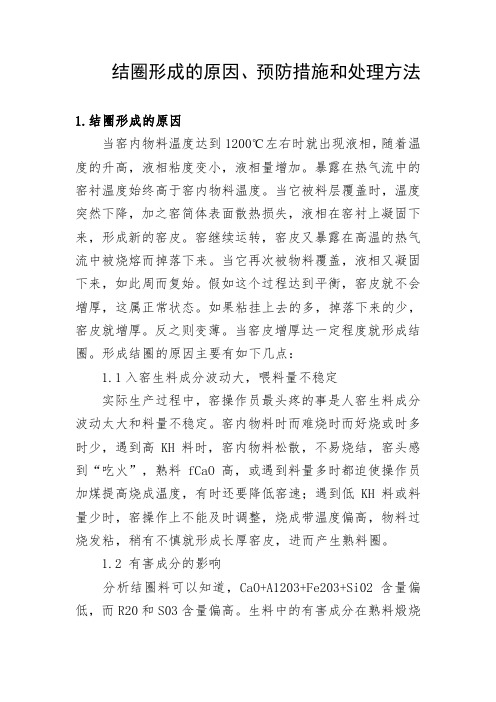
结圈形成的原因、预防措施和处理方法1.结圈形成的原因当窑内物料温度达到1200℃左右时就出现液相,随着温度的升高,液相粘度变小,液相量增加。
暴露在热气流中的窑衬温度始终高于窑内物料温度。
当它被料层覆盖时,温度突然下降,加之窑简体表面散热损失,液相在窑衬上凝固下来,形成新的窑皮。
窑继续运转,窑皮又暴露在高温的热气流中被烧熔而掉落下来。
当它再次被物料覆盖,液相又凝固下来,如此周而复始。
假如这个过程达到平衡,窑皮就不会增厚,这属正常状态。
如果粘挂上去的多,掉落下来的少,窑皮就增厚。
反之则变薄。
当窑皮增厚达一定程度就形成结圈。
形成结圈的原因主要有如下几点:1.1入窑生料成分波动大,喂料量不稳定实际生产过程中,窑操作员最头疼的事是人窑生料成分波动太大和料量不稳定。
窑内物料时而难烧时而好烧或时多时少,遇到高KH料时,窑内物料松散,不易烧结,窑头感到“吃火”,熟料fCaO高,或遇到料量多时都迫使操作员加煤提高烧成温度,有时还要降低窑速;遇到低KH料或料量少时,窑操作上不能及时调整,烧成带温度偏高,物料过烧发粘,稍有不慎就形成长厚窑皮,进而产生熟料圈。
1.2 有害成分的影响分析结圈料可以知道,CaO+A1203+Fe203+Si02含量偏低,而R20和S03含量偏高。
生料中的有害成分在熟料煅烧过程中先后分解、气化和挥发,在温度较低的窑尾凝聚粘附在生料颗粒表面,随生料一起人窑,容易在窑后部结成硫碱圈。
在人窑生料中,当MgO和R20都偏高时,R20在MgO引起结圈过程中充当“媒介”作用形成镁碱圈。
根据许多水泥厂的操作经验,当熟料中MgO>4.8%时,能使熟料液相量大量增加,液相粘度下降,熟料烧结范围变窄,窑皮增长,浮窑皮增厚。
有的水泥厂虽然熟料中MgO<4.0%,但由于R20的助熔作用,使熟料在某一特定温度或在窑某一特定位置液相量陡然大量增加,粘度大幅度降低,迅速在该温度区域或窑某一位置粘结,形成熟料圈。