回转窑结圈的原因及处理方法
处理氧化锌回转窑内结球宣传报道
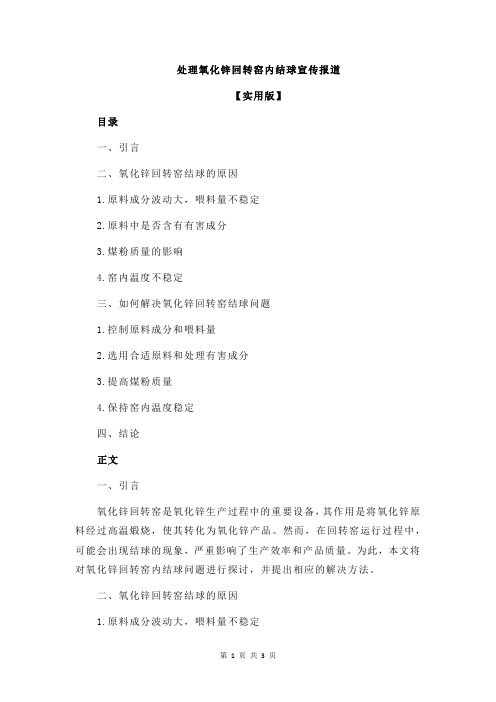
处理氧化锌回转窑内结球宣传报道【实用版】目录一、引言二、氧化锌回转窑结球的原因1.原料成分波动大,喂料量不稳定2.原料中是否含有有害成分3.煤粉质量的影响4.窑内温度不稳定三、如何解决氧化锌回转窑结球问题1.控制原料成分和喂料量2.选用合适原料和处理有害成分3.提高煤粉质量4.保持窑内温度稳定四、结论正文一、引言氧化锌回转窑是氧化锌生产过程中的重要设备,其作用是将氧化锌原料经过高温煅烧,使其转化为氧化锌产品。
然而,在回转窑运行过程中,可能会出现结球的现象,严重影响了生产效率和产品质量。
为此,本文将对氧化锌回转窑内结球问题进行探讨,并提出相应的解决方法。
二、氧化锌回转窑结球的原因1.原料成分波动大,喂料量不稳定回转窑内的原料成分波动大,喂料量不稳定,造成窑内热工制度混乱,容易导致物料在窑内结球。
2.原料中是否含有有害成分原料中是否含有大量的 R2O 和 SO3,会造成硫碱圈,是否含有 MgO 含量高时会产生熟料圈等,这些有害成分都会导致结球的产生。
3.煤粉质量的影响煤粉质量直接影响到回转窑内的燃烧情况,质量差的煤粉燃烧不充分,容易导致结球现象。
4.窑内温度不稳定窑内温度不稳定,也容易形成结圈。
温度过高,物料烧结,温度过低,物料不能充分燃烧。
三、如何解决氧化锌回转窑结球问题1.控制原料成分和喂料量要想解决结球问题,首先要控制好原料成分和喂料量,保持原料成分的稳定,喂料量的均匀,避免窑内热工制度的混乱。
2.选用合适原料和处理有害成分在选用原料时,要确保不含有或者少含有有害成分,如 R2O 和 SO3 等。
如果原料中含有这些有害成分,需要对原料进行处理,以降低其含量。
3.提高煤粉质量提高煤粉质量,保证煤粉的燃烧充分,可以减少结球现象的发生。
4.保持窑内温度稳定保持窑内温度稳定,避免温度过高或过低,可以有效防止结球现象的发生。
四、结论氧化锌回转窑结球问题的产生原因是多方面的,解决这个问题也需要从多方面入手。
回转窑窑内结球并且形成窑灰的解决方法

回转窑窑内结球并且形成窑灰的解决方法回转窑窑内结球是一种很常见的现象,水泥回转窑窑内结球的原因和处理时的相关措施,是每个用户所关心的问题。
窑内结球主要形成原因有:生料成分波动,液相量过多;加料不稳定,导致窑尾、分解炉温度时高时低,难以控制;设备故障率高,停机较为频繁;原、燃材料中,硫、氯、碱等有害成分含量较高;煤粉质量波动大,均化效果差;窑灰掺入不均匀;操作人员疏忽,温度控制不当或长时间打慢车等。
窑内结球可采取以下措施加以预防和处理。
(1)预防措施。
第一,可选择合适的配料方案,稳定生料成分。
一般采用高石灰饱和系数、高硅率的生料不易发生结球现象,且熟料质量比较好,但是这种料较耐火,对操作要求较高。
若低石灰饱和系数和低铝率的生料,它的烧结范围比较窄,而液相量偏多,结粒粗大,稍有不慎就会导致结球。
所以在生产中尽可能选择两高一中的配料方案,即高KH、高SM、中IM,这种配料易操作且熟料质量也相对较稳定。
第二,尽量选用含有害成分物质较低的原燃材料,特别是煤;要加强燃煤的均化,并在能够满足生产要求的同时尽可能的降低煤粉细度;煨烧过程中要加强风与煤混合,尽量避免煤粉过粗而引起的不完全燃烧;如使用挥发分较低的煤粉,因其着火速度慢、燃烧时间长,火力强度不集中,应尽量降低煤粉的细度和水分。
(2)处理措施。
若窑内已经形成料球,应对成球的原因进行全方位分析,取样化验,且要分别对球核、球壳进行化学全分析,找准原因,对症下药。
如料球比较小,操作上应适当增加窑内通风,使火焰顺畅,但必须注意窑尾温度的控制,使其不要过高;可略微减少窑头用煤,但必须保证煤粉的完全燃烧,并适当减少喂料量,稍降低窑速,让窑内的料球滚入烧成带;等料球到烧成带后,再降低一些窑速,用大火在短时间内将其烧垮或烧小,以免进入冷却机发生堵塞或砸坏篦板,但此时应特别注意窑皮的情况。
如果结球较大时,可采用冷热交替法进行处理;当料球在过渡带时不易前行进入烧成带,这时可将喷煤管伸进去,适当降低喂料量,烧1〜2h后将煤管拉出再烧1〜2h,周而复始,直到料球破裂;若实在不能使其破裂,便可停窑冷却1〜2h后点火升温,让料球因温差过大而破裂。
回转窑不正常情况
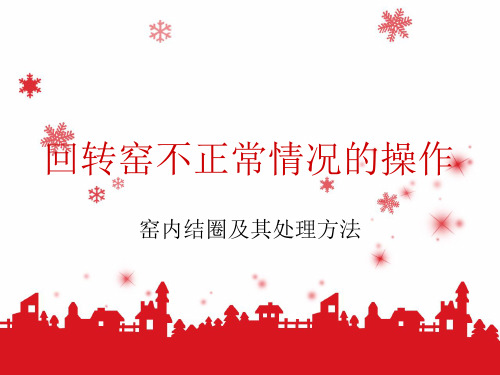
• 故障发生原因是喷入料浆不能及时烘干所 致。造成的原因有 :
(1)喷枪位置不当,直接将料浆喷在窑壁上或料浆 落点集中 (2)雾化器不好 (3)料浆水分过大 (4)后结圈严重,通风不良,使窑尾温度低 (5)喷枪头磨损 (6)收尘系统或窑灰系统有问题,使窑灰量少或缺 窑灰,没有及时减料
• 故障处理方法如下 : (1)调整喷枪位置,或更换雾化器; (2)当结圈严重时,应适当减料,提高窑尾 温度,但最高不超过400-450℃ (3)采取相应措施无效后,停窑处理
• 处理回转窑前圈的方法有慢烧和急烧两种 (1) 慢烧就是在较长的时间内把圈烧掉(一 般为4~8小时),适用于处理宽厚高的前圈 和圈内窑皮不好的情况。 (2)急烧就是在较短的时间内把圈烧掉(一 般为1~2个小时),此法适用于长得靠里的 前结圈。慢烧与快烧方法相似,只是烧圈 时间的长短和关风大小不同。
前结圈
• 在正常煅烧条件下,物料温度达 1350—14 50 ℃时,液相量约为 24%,粘度比较大 。当熟 料离开烧成带时,温度仍在 1300 ℃以上,在烧成带和冷却带的交界处,熟 料和窑皮有较大 的温差 ,带有液相的高温 熟料覆盖在温度相对较低的窑口窑皮上就 会粘结形成前结圈。
• 这种结圈的形成,一般都是由于火焰过长 ,烧成带后移,熟料慢冷或出回转窑烧成 带的物料含液相较多所致。由于前圈长在 回转窑烧成带与冷却带交界处,用火焰可 以直接烧到(小窑可以使用钎子捅掉),所以 变动火焰位置就可解决。
• 回转窑窑内结圈由于位置的不同,叫法也 不一样。结在链条带上的圈叫泥浆圈,又 名泥巴圈 结在回转窑窑皮末端的圈叫后结圈,又名熟 料圈。 结在窑皮前端的圈叫前结圈,又名窑口圈。 结在分解带预热带的圈叫硫碱圈。
泥浆圈
• 在回转窑尾部生料浆粘结在窑壁上,形成 一圈料浆层.其现象是 : (1)刮料器滚动声音不正常 (2)烘干带料样水分不均,潮湿多块 (3)窑尾负压升高 (4)烘干带窑壁温度低 (5)窑尾温度低
回转窑结圈的影响因素及解决措施

回转窑结圈的影响因素及解决措施-----龙仕连我司从11月23日开始窑内断断续续出现少量漏料,并出现了三次大料球,严重影响到窑的正常运转,公司及部门领导高度重视。
经分析是窑23米处结后圈导致窑尾漏料和结料球。
于25日开始处理后圈:1、窑减产到350 t/h煅烧;2、窑头煤管每个班移动两次,-200~+100冷热交替处理;3、每班清理煤管头部积料结焦4次,以保证头煤燃烧好,火焰集中;4、控制煤粉细度及水分,以保证煤粉燃烧效果(煤磨出磨温度控制在63~65度,入磨温度<300度。
内部控制煤粉细度<6.0);5、适当提高熟料KH。
通过3天的处理,23料处后圈薄了很多,并有缺口,于28日窑恢复了365 t/h正常生产。
出现这样的工艺事故,我们必须深度反思。
特别是工艺管理人员和窑操作员一定要密切关注窑皮的变化趋势及原燃材料的变化,及时调整窑参数,保证窑正常运转。
下面让我们再次学习一下窑内结圈的成因、危害及解决措施:结圈是指回转窑在正常生产中,由于原燃材料的变化,或者操作和热工制度的影响,窑内因物料过度粘结,在特定的区域形成一道阻碍物料运动的环形、坚硬的圈。
这种现象在回转窑内是一种不正常的窑况,它破坏了正常的热工制度,影响窑内通风,造成窑内来料波动很大,直接影响到回转窑的产量、质量、消耗和长期安全运转。
而且处理窑内结圈费时费力,严重时需停窑停产,危害极其严重。
结圈的成因及危害:结圈的形成: 结圈实际上是在烧成带末端与放热反应带交界处形成的窑皮,是回转窑内危害最大的结圈。
在熟料煅烧过程中,当物料温度达到1280℃时,其液相黏度较大,最容易形成结圈,而且冷却后比较坚固,不易除掉。
在正常的煅烧情况下,后结圈体的内径部分往往被烧熔而掉落,保持正常的圈体内径。
如果在1 250~l 280℃温度范围内出现的液相量偏多,往往会形成妨碍生产的后结圈。
后结圈一般结在烧成带的边界或更远,开始是烧成带后边的窑皮逐渐增长、增厚,发展到一定程度即形成后结圈。
窑内结圈、结球的原因及处理措施

窑内结圈、结球的原因及处理措施中控室侯素克结圈是指窑内在正常生产中因物料过度黏结,在窑内特定的区域形成一道阻碍物料运动的环形、坚硬的圈。
这种现象在回转窑内是一种不正常的窑况,他破坏正常的热工制度,影响窑内通风,造成来料波动很大,直接影响回转窑的产量、质量、消耗和长期安全运转。
尤其频繁结圈的回转窑,不仅破坏了窑内正常热工制度,而且损害操作人员的身体健康,给生产造成经济损失。
引起回转窑结圈的因素很多,它与原料性质、生料成分、燃料的灰分和细度、窑型、窑内还原气氛及热工制度等有关。
1 结圈的形成回转窑内形成结圈的因素很多,但液相的产生和固化是结圈的主要形成过程。
而衬料温度、物料温度、煤灰和生料组成又是决定液相的生成和固化的主要因素。
在正常情况下,窑皮保持在200mm左右的厚度,该温度条件及区域内若熔化和固化的过程达到平衡,窑皮就不会增厚。
当熔化的少固化的多,其厚度增长到一定程度,即形成圈。
当衬料与物料的温差大时,在足够液相的条件下,圈体越结越厚。
1.1前结圈的形成前圈结在烧成带和冷却带交界处,由于风煤配合不好,或者煤粉粒度过粗,煤灰和水分大,影响煤粉燃烧,使黑火头长,烧成带像窑尾方向移动,熔融的物料凝结在窑口处使“窑皮”增厚,发展成前圈,或者由于煤粉落在熟料上,在熟料中形成还原性燃烧,铁还原成亚铁,形成熔点低的矿物或者由于煤灰分中氧化铝含量高而使熟料液相量增加,黏度增大,当遇到入窑二次风温降温、冷却,就会逐渐凝结在窑口处形成圈。
前圈形成的主要原因是煤粉的质量,熟料中溶剂矿物含量过高或氧化铝含量过高,燃烧器在窑口断面的位置不合理,影响煤粉燃烧,使结圈速度加快,前温急烧,导致温差相差大,造成液相冷却凝固形成前圈,1.2熟料圈的形成原因熟料圈(又称后圈),是结在窑内烧成带与放热反应带之间的圈,也是回转窑内危害最大的结圈。
造成熟料圈的原因很多,主要有生料化学成分,熟料圈行成往往在物料刚出现液相的地方,物料在1200~1300度范围内为防止结圈,配料时应考虑液相不易过多,液相黏度不易过大;原燃材料中的有害成分,原燃材料中的有害成分过多,降低物料的熔点,结圈的可能性就增大,正常情况下,此类结圈大多发生在放热反应带以后的地方;煤的影响,煤灰中氧化铝的含量较高,当煤灰掺入物料中时,使物料液相量增加往往易结圈;操作和热工制度的影响,头煤加入量较多,产生还原气氛,形成低熔点矿物,使液相提前出现,容易结圈,二三次风配合不当,火焰过长,液相提前出现,特别是在分解率高的情况下,结圈的可能性更大。
煤基还原回转窑结圈
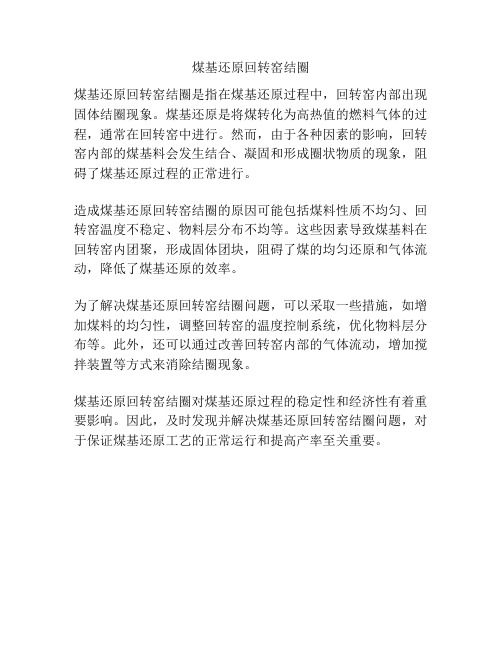
煤基还原回转窑结圈
煤基还原回转窑结圈是指在煤基还原过程中,回转窑内部出现固体结圈现象。
煤基还原是将煤转化为高热值的燃料气体的过程,通常在回转窑中进行。
然而,由于各种因素的影响,回转窑内部的煤基料会发生结合、凝固和形成圈状物质的现象,阻碍了煤基还原过程的正常进行。
造成煤基还原回转窑结圈的原因可能包括煤料性质不均匀、回转窑温度不稳定、物料层分布不均等。
这些因素导致煤基料在回转窑内团聚,形成固体团块,阻碍了煤的均匀还原和气体流动,降低了煤基还原的效率。
为了解决煤基还原回转窑结圈问题,可以采取一些措施,如增加煤料的均匀性,调整回转窑的温度控制系统,优化物料层分布等。
此外,还可以通过改善回转窑内部的气体流动,增加搅拌装置等方式来消除结圈现象。
煤基还原回转窑结圈对煤基还原过程的稳定性和经济性有着重要影响。
因此,及时发现并解决煤基还原回转窑结圈问题,对于保证煤基还原工艺的正常运行和提高产率至关重要。
回转窑窑后结圈原因分析及处理方法

回转窑窑后结圈原因分析及处理方法巩义市恒昌冶金建材设备厂生产的1000t/d熟料生产线是由天津水泥工业设计研究院有限公司设计的,主要包括TDF型分解炉、单系列五级旋风预热器、Φ3.2m×50m回转窑及TC-836篦式冷却机。
自2007年2月以来,窑后频繁发生结圈、结球的工艺事故,巩义市恒昌冶金建材设备厂技术人员现将原因分析及解决措施介绍如下,供同仁参考。
1、结圈情况2007年3月19日最为严重,窑前返火,窑尾有漏料现象,无法操作煅烧,迫使停窑处理。
从窑内看,主窑皮长达22m,副窑皮长到窑尾,35~37m处形成后结圈,结圈最小孔洞呈不规则状,直径约l.5m,进窑观察该圈明显分为两层,且层次明确、清晰,第一层厚约150mm,呈黄白色,第二层厚约460mm,呈黑色,圈体非常致密。
对圈体取样分析见表1。
表1 圈体取样分析结果从表l可以看出,第一层硫碱含量较高,是硫碱圈,第二层明显是煤粉圈,熟料液相出现过早、过多导致结圈。
2、原因分析(1)由于2006年煤价不断上涨,加之公路运输距离远,为了降低成本,采用当地劣质煤煅烧,煤质下降,灰分高,挥发分低,发热值低,煤工业分析如表2、3。
实际生产中,煤可燃性差,煤粉燃烧不完全,大量煤灰不均掺入生料中,液相在窑后面提前出现,而未燃尽的煤灰产生沉积及液相的提前出现结圈。
(2)2007年以来,由于机械原因,高温风机l号轴与密封圈强烈摩擦,产生局部高温,使轴侧曲,水平振动最高达6.4mm/s。
为了降低振动,不得不降低高温风机转速,由原来的1130r/min降至l060r/min,有时更低,严重影响了窑内通风,加上煤质又差,更多的窑头燃烧不完全的煤粉沉积在窑后燃烧,使窑内后部温度升高,液相量增加,加速了窑后结圈的形成。
(3)为了处理窑后结圈,我厂在迫不得已的情况下停窑烧后圈,由于煤质差,二、三次风温低,燃料不完全或未燃烧的煤粉落在圈上及圈后的积料上,不断燃烧,造成物料发粘,不但圈未烧掉,反而越结越厚,这也是第一层圈形成的主要原因。
窑内结圈形成原因及处理

• 2、减少原燃料带入的有害成分 • 一般粘土中碱含量高,煤中含硫量高。因此,如果窑上经常 • • • •
出现结圈时,视结圈料分析结果,最好能改变粘土或原煤的供 货矿点,以减少有害成分对结圈的影响。 3、控制煤粉细度,确保煤粉充分燃烧 。 4、调整燃烧器控制好火焰形状确保风、煤混合均匀并有一定的 火焰长度。经常移动喷煤管,改变火点位置。 5、提高快转率 三个班统一操作方法,稳定烧成系统的热工制度。在保持喂 料喂煤均匀,加强物料预烧的基础上尽量加快窑速。采取薄料 快转、长焰顺烧,提高快转率,这对防止煤、料量可以不变,只要把喷煤管往外拉出一定距离, •
就可以把前圈烧垮。 (2)如果前圈离下料口比较近,并在喷嘴口前则将喷嘴往里伸, 使圈体温度下降而脱落。如果圈体不垮,则有两种处理方法 ① 把喷煤管往外拉出,同时适当增加内流风和二次风温度,这 样可以提高烧成温度,使烧成带前移,把火点落在圈位上。一 般情况下,圈能在2~3h内逐渐被烧掉。但在烧圈过程中应根 据进入烧成带料量多少,及时增减用煤量和调整火焰长短,防 止损伤窑皮或跑生料。 ② 如果用前一种方法无法把圈烧掉时,则把喷煤管向外拉出并 把喷嘴对准圈体直接烧。待窑后预烧较差的物料进入烧成带后, 火焰会缩得更短,前圈将被强火烧垮。但是必须指出,采用这 种处理方法,由于喷煤管拉出过多,生
• 在高温的热气流中被烧熔而掉落下来。当它再次被物料覆盖,
•
液相又凝固下来,如此周而复始。假如这个过程达到平衡,窑 皮就不会增厚,这属正常状态。如果粘挂上去的多,掉落下来 的少,窑皮就增厚。反之则变薄。当窑皮增厚达一定程度就形 成结圈。形成结圈的原因主要有如下几点: 1、入窑生料成分波动大,喂料量不稳定 实际生产过程中,窑操作员最头疼的事是人窑生料成分波动太 大和料量不稳定。窑内物料时而难烧时而好烧或时多时少,遇 到高KH料时,窑内物料松散,不易烧结,窑头感到“吃火”, 熟料fCaO高,或遇到料量多时都迫使操作员加煤提高烧成温度, 有时还要降低窑速;遇到低KH料或料量少时,窑操作上不能及 时调整,烧成带温度偏高
- 1、下载文档前请自行甄别文档内容的完整性,平台不提供额外的编辑、内容补充、找答案等附加服务。
- 2、"仅部分预览"的文档,不可在线预览部分如存在完整性等问题,可反馈申请退款(可完整预览的文档不适用该条件!)。
- 3、如文档侵犯您的权益,请联系客服反馈,我们会尽快为您处理(人工客服工作时间:9:00-18:30)。
回转窑结圈的原因及处理方法
1、结圈的危害
回转窑“结圈”的部位一般在距窑口一定距离的固体燃料集中燃烧点附近的耐火窑衬上,厚度可达200-500 mm左右。
“结圈”对球团生产的危害有以下几方面:
(1)降低产量,增加劳动强度
窑圈一经形成,对燃料烧烧所产生的热气流势必起阻碍作用,如图-1所示。
热气流被部分阻挡在A区,影响了球团的焙烧效果。
同时,由于链篦机上生球的干燥、预热过程是利用窑尾废气进行的,故此,结圈也对生球的干燥、预热产生不良影响。
具体地说,就是透气性差,火焰不进,后部温度低,干燥时水分不易脱除,生球爆裂、粉化严重,成品率低,从而降低了劳动生产率。
另外,圈结形成后,如不及时处理,就会使圈的纵向长度、厚度增加,当圈掉下时,必然增加工人的劳动强度,有时甚至需停机处理,也影响了球团矿的产量。
(2) 增加了设备负荷
如图-1所示,一定面积及厚度的结圈使物料流被阻于B区,此时,被阻的料量要高出正常时许多,加之圈本身的重量,必然增加了托轮、轴承的磨损,同时,增加了电机的负荷,甚至烧毁。
(3) 浪费能源
在实际看火操作中,当出现“结圈”现象后,由于热气流被阻于A区,为保证链篦机的干燥和预热效果,看火工往往采用加大给煤
量的方式,这无疑造成了能源浪费。
2、结圈的原因
结圈的原因,在生产中主要可以归纳为操作不当。
具体地说,是由于上料量过大,干燥效果差,生球爆裂,粉化严重,致使透气性差,使得引风机抽动火焰的作用不明显,火焰只在窑内一定距离燃烧。
在大于1 200℃的高温下,未完全氧化的Fe3O4就与磁铁矿中一定数量的SiO2发生反应形成液相。
2Fe3O4+3SiO2+2CO=3Fe2SiO4+2CO2
2FeO+SiO2=Fe2SiO4
另外,当给煤量较大时,在1 150℃条件下,Fe2O3也会部分分解为Fe3O4,与SiO2作用而生成2FeO·SiO2,形成渣相粘结。
这就使得物料在流经焙烧带时,所产生的液相、渣相极易粘附在窑衬的表面,同时粘结物料而产生结圈现象。
3、处理方法
为减少或杜绝结圈现象,在生产中首先是要采取措施防止结圈,即采用正确的操作方法,稳定上料量,使料层厚度适宜,以保证干燥、预热效果,减少生球的爆裂和粉化,同时,控制喂煤量,不宜过大,使温度保持在较低范围内,避免出现渣相。
在出现结圈后,一定要及时处理,否则将出现窑壁加宽加厚的不良后果,这样就增加了处理难度,甚至影响生产正常进行。
去圈的方法有以下三种:
(1) 在窑内安设移动的合金刮刀;
(2) 加入适量的燃料,烧化粘结物;
(3) 改变高温区。
比较而言,第一种方法对刮刀材质要求较高,不易实现;第二种方法可行,但从节能角度考虑,也不太理想,而且难度较大;第三种方法,我们通过实践认为是一种可行的办法。
所谓适当改变高温区,就是通过调整后部链篦机引风机的风箱翻板开合程度,使燃烧点或火焰往复拉动,这样就易使粘结的窑圈掉下来而达到去圈的目的。
此法既节约了能源,又简便、易操作。