电机端盖成形工艺及模具设计
端盖冲压工艺与模具设计综述

端盖冲压工艺与模具设计综述引言端盖是一种常见的机械设备零件,广泛应用于汽车、摩托车、工程机械等领域。
而端盖的成型过程中,冲压工艺和模具设计起着至关重要的作用。
本文将对端盖冲压工艺和模具设计进行综述,以帮助读者更全面地了解并掌握相关知识。
一、端盖冲压工艺概述1.1 端盖冲压工艺的定义冲压工艺是一种利用模具对金属材料进行变形、分离和加工的方法,通过冲击或压力使材料产生塑性变形,从而得到所需形状的工件。
端盖冲压工艺即指在冲压工艺中,针对端盖的加工特点进行的工艺处理。
1.2 端盖冲压工艺的优势端盖冲压工艺具有以下优势:•高效率:冲压工艺可以实现连续生产,提高生产效率;•高精度:冲压工艺可以获得高度精确的工件尺寸和形状;•节约材料:冲压工艺可以最大限度地利用材料,减少废料产生;•适应性强:冲压工艺适用于多种材料和复杂形状的加工。
二、端盖模具设计概述2.1 端盖模具设计的意义模具是冲压工艺中的关键设备,直接影响到冲压工艺的质量和效率。
端盖模具设计是为实现端盖冲压工艺提供必要的技术支持,保证工艺能够正常进行。
2.2 端盖模具设计的基本要求端盖模具设计需要满足以下基本要求:•合理性:模具设计应考虑到冲压工艺的特点,采取合理的设计方案,以确保工艺能够稳定、高效地进行;•易制造性:模具设计应考虑到模具的制造和维修难度,尽量采用标准化部件和加工工艺,以降低制造成本;•高可靠性:模具设计应确保模具在长期使用过程中具有较高的可靠性和寿命,减少故障和损坏的可能性。
2.3 端盖模具设计的关键技术端盖模具设计涉及到许多关键技术,包括但不限于以下几个方面:•模具结构设计:确定模具的整体结构,包括顶模、底模、导向机构等;•模具材料选择:选择适合冲压工艺的模具材料,考虑到材料的强度、硬度和耐磨性等;•模具零件设计:设计各个模具零件的形状和尺寸,包括模腔、模板、导向柱等;•模具热处理:对关键部件进行适当的热处理,提高模具的硬度和耐磨性;•模具装配和调试:对完成的模具进行装配和调试,确保模具的正常工作。
毕业设计论文端盖零件的冲压成形工艺及模具设计

毕业设计论文论文题目:端盖零件的冲压成形工艺及模具设计系部材料工程系专业模具设计与制造班级学生姓名学号指导教师毕业设计(论文)任务书系部:材料工程系专业:模具设计与制造学生姓名:学号:设计(论文)题目:起迄日期: 4月1日~ 5月9日指导教师:发任务书日期:年 4 月 1 日毕业设计(论文)任务书目录绪论 (1)第1章任务来源及设计意义 (3)1.1 设计任务来源 (3)1.2 设计目的及意义 (3)第2章冲压工件的工艺性分析 (4)2.1 冲压及冲裁件的工艺性的感念 (4)2.2 零件工艺性分析 (4)第3章冲压工艺方案的确定 (6)3.1 确定工艺方案的原则 (6)3.2 工艺方案的确定 (6)第4章模具结构形式及冲压设备的选择 (9)4.1 模具结构形式的选择 (9)4.2 冲压设备的选择 (10)第5章主要工艺参数计算 (11)5.1 排样设计与计算 (11)5.2 计算工序压力 (13)5.3 计算模具压力中心 (14)5.4 计算凸、凹模工作部分尺寸并确定其制造公差 (16)5.5 弹性元件的选取与设计 (19)第6章选择与确定模具的主要零部件的结构与尺寸 (22)6.1 确定工作零件 (22)6.2 定位零件的设计 (24)6.3 导料板的设计 (25)6.4 卸料部件的设计 (25)6.5 模架及其他零部件设计 (25)第7章模具的总体装配 (29)第8章模具工件零件的加工工艺 (30)8.1 冲裁模凸、凹模的技术要求及加工特点 (30)8.2 凸、凹模加工的工艺路线有以下几种方案 (30)8.3 本副模具工件零件加工方案的确定 (30)第9章模具的装配与调试 (32)9.1 模具的装配 (32)9.2 模具的调试 (33)设计总结 (35)致谢 (36)参考文献 (37)绪论改革开放以来,随着国民经济的高速发展,市场对模具的需求量不断增长。
近年来,模具工业一直以15%左右的增长速度快速发展,模具工业企业的所有制成分也发生了巨大的变化,除了国有专业模具厂外,集体、合资、独资和私营也得到了快速的发展。
端盖冲压工艺及模具设计

端盖冲压工艺及模具设计端盖冲压工艺及模具设计端盖是一种常见的零部件,广泛应用于机械、电子、汽车等领域。
端盖的冲压工艺是一种重要的加工方法,它可以通过模具将金属板材快速成形为具有一定形状和尺寸的端盖。
在端盖冲压过程中,模具是起着重要作用的工具,模具的设计和加工质量是决定产品质量的关键。
一、端盖冲压工艺流程端盖的冲压过程一般分为下料、模具调试、冲压成形、清洁、涂装等几个环节。
1. 下料:下料是冲压工艺的第一步,它是根据产品图纸,按照板材的尺寸进行的。
下料可以采用剪板机、切割机等设备进行,将整张金属板分割成具有所需形状和尺寸的板材。
2. 模具调试:模具调试是为了适应端盖的尺寸和形状要求。
模具调试包括刀模的套装、修正,以及调整模具中央孔的大小等。
调试完成后,需要进行冲压测试,以确保成形品的尺寸、形状、表面质量等达到要求。
3. 冲压成形:冲压成形是将板材置于模具之间,施加一定的压力,使板材在模具的形状下变形,形成所需形状和尺寸的端盖。
在冲压过程中,需要对板材的表面进行保护,以免划伤或磨损。
4. 清洁:清洁是为了去除端盖上的铁锈、污渍等,制备好产品的表面。
清洁过程包括浸泡、刷洗、喷洒清洁剂等。
5. 涂装:涂装是为了提高端盖的容基性,增强其耐用性和耐腐蚀性。
涂装方式可以采用喷涂、浸涂、静电喷涂等。
二、端盖冲压模具设计1. 模具结构设计端盖冲压模具的结构设计要根据端盖的形状和尺寸进行模拟和分析。
具体的设计应该包括切口、冲头、冲模、定位、夹紧等结构。
切口、冲头和冲模是需要特别关注的部分,需要保证其准确度和可靠性。
定位和夹紧结构是为了保证制品的准确度和稳定性。
2. 材料选择模具材料需要具有足够的强度和硬度,以满足生产要求。
现在,常用的模具材料有高速钢、硬质合金、陶瓷、钢、塑料等。
需要注意的是,模具材料的选择要考虑到材料的性能、使用寿命、制造成本等因素。
3. 表面处理模具表面处理是为了提高其耐磨性和耐腐蚀性,延长模具使用寿命的关键。
端盖冲压成形工艺与模具设计
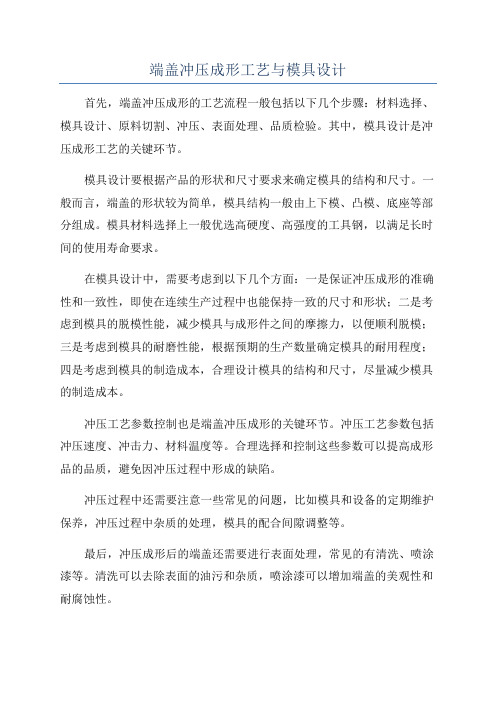
端盖冲压成形工艺与模具设计
首先,端盖冲压成形的工艺流程一般包括以下几个步骤:材料选择、模具设计、原料切割、冲压、表面处理、品质检验。
其中,模具设计是冲压成形工艺的关键环节。
模具设计要根据产品的形状和尺寸要求来确定模具的结构和尺寸。
一般而言,端盖的形状较为简单,模具结构一般由上下模、凸模、底座等部分组成。
模具材料选择上一般优选高硬度、高强度的工具钢,以满足长时间的使用寿命要求。
在模具设计中,需要考虑到以下几个方面:一是保证冲压成形的准确性和一致性,即使在连续生产过程中也能保持一致的尺寸和形状;二是考虑到模具的脱模性能,减少模具与成形件之间的摩擦力,以便顺利脱模;三是考虑到模具的耐磨性能,根据预期的生产数量确定模具的耐用程度;四是考虑到模具的制造成本,合理设计模具的结构和尺寸,尽量减少模具的制造成本。
冲压工艺参数控制也是端盖冲压成形的关键环节。
冲压工艺参数包括冲压速度、冲击力、材料温度等。
合理选择和控制这些参数可以提高成形品的品质,避免因冲压过程中形成的缺陷。
冲压过程中还需要注意一些常见的问题,比如模具和设备的定期维护保养,冲压过程中杂质的处理,模具的配合间隙调整等。
最后,冲压成形后的端盖还需要进行表面处理,常见的有清洗、喷涂漆等。
清洗可以去除表面的油污和杂质,喷涂漆可以增加端盖的美观性和耐腐蚀性。
总结来说,端盖冲压成形工艺与模具设计需要综合考虑材料选择、模
具设计、冲压工艺参数控制等多个因素。
通过合理的选择和控制这些因素,可以保证冲压成形的准确性和一致性,提高产品的质量,减少缺陷的发生。
同时,还需要重视模具和设备的定期维护保养,以延长模具的使用寿命,
减少生产中的故障。
端盖冲压工艺及模具设计说明书

端盖冲压工艺及模具设计说明书一、引言端盖是一种常用的金属制品,广泛应用于机械设备、汽车等领域。
端盖的生产过程中,冲压工艺和模具设计起着至关重要的作用。
本文档旨在介绍端盖的冲压工艺流程和模具的设计要点,以帮助读者了解并应用于实际生产。
二、冲压工艺流程端盖的冲压工艺流程主要包括材料准备、模具设计、冲压操作和零件加工。
1.材料准备材料准备是冲压工艺的第一步。
一般情况下,端盖的制作材料为金属板材,常用的材料有冷轧钢板、不锈钢板等。
在材料准备阶段,需要根据设计要求选择合适的材料,并进行切割、平整等处理。
2.模具设计模具设计是冲压工艺的关键。
模具的设计应根据端盖的形状和尺寸要求进行。
一般情况下,模具应包括上模、下模和导向装置。
上模和下模的设计要考虑到端盖的形状,确定冲模的凹线和凸线,以确保冲压过程中的精度和质量。
3.冲压操作冲压操作是将模具设计的零件在冲压机上进行加工的过程。
在冲压操作中,需要将材料放置在冲床上,并通过冲压动作将材料加工成端盖的形状。
操作时要注意材料的位置和冲压的速度、力度,以避免材料变形或断裂。
4.零件加工零件加工是冲压工艺的最后一步。
在冲压操作完成后,需要对端盖进行修整和整理,以达到要求的尺寸和表面质量。
同时,还需要进行表面处理,如喷涂、镀锌等,以提高端盖的耐腐蚀性能。
三、模具设计要点模具设计是冲压工艺的核心,合理的模具设计可以提高生产效率和产品质量。
以下是一些模具设计的要点:1.模具材料选择模具的材料应选择硬度高、耐磨损、耐腐蚀的材料。
常用的模具材料有合金工具钢、硬质合金等。
选择合适的材料可以延长模具的使用寿命,并提高模具的加工精度和稳定性。
2.模具结构设计模具的结构设计要简单、合理。
需要考虑到冲压力度和速度等因素,确定模具的构造强度,并确保模具的刚性和稳定性。
模具的上模和下模应配合良好,确保冲压过程中的精度和质量。
3.凸模和凹模设计凸模和凹模的设计要根据端盖的形状和尺寸要求进行。
在设计凸模和凹模时,需要考虑到材料的弹性变形和回弹等因素,以确保冲压过程中的形状和尺寸精度。
电机端盖冲压工艺与模具结构设计

电机端盖冲压工艺与模具结构设计摘要:文章通过对电机端盖冲压成型工艺的分析,确定该端盖的冲压工艺的方案。
并进行压力工位的设计,选择合适的拍样方案,画出了相应的拍样图,最后设计出模具的结构图。
通过端盖设计的整体思路,为模具设计者提供了一个设计的思路及方向。
关键词:端盖;排样;拉深;工艺引言:为了提高端盖加工的效率,减少劳动力,降低加工费用等问题,提出了一张电机端盖冲压工艺及其模具结构设计,对电机端盖进行了工艺的分析。
通过排样分析、拉深次数计算、翻边力计算及压力中心位置的确认来设计出整体模具的结构,并利用CAD对模具进行结构绘制。
一、电机端盖冲压工艺分析(一)毛坯直径的确定此零件的凸缘直径为44mm,相对凸缘直径为144/120=1.2,可取修边余量≤3.5mm。
即实际凸缘直径dF=df+2≤151mm。
按等面积法求得毛坯下料直径D为248mm。
(二)冲压工艺分析此零件属于复杂冲压件,主要包括拉伸和冲裁两类工艺,首先完成拉伸类工艺,待成型后再进行冲裁类工艺,从而完成整个零件的冲压加工。
根据工艺分解原则,此零件拉伸类工艺包括拉伸、反拉伸、整形等工序;冲裁类工艺包括下料、切边、冲孔、冲侧孔、冲侧舌等工序。
(三)冲裁工艺设计由冲压工艺分析可知,此零件冲裁类工艺主要包括凸缘轮廓切边,冲凸缘上孔为4.5mm、中心孔为16mm和顶部6处腰形孔及冲侧面出线孔、侧面腰形孔及4处均布的侧面止口。
凸缘上孔为4.5mm的孔口到凸缘边缘为144mm的距离a=1.75mm工位来完成,同时应位于整个模具的后4个工位。
因此可确定7工位到10工位的加工内容为:第7工位:切边。
切凸缘外形轮廓。
第8工位:冲孔。
冲凸缘平面上的为4.5mm、中心为16mm和顶部平面6个腰形孔。
第9工位:冲侧孔。
冲出线孔为14mm和5处侧向腰形孔。
第10工位:冲侧。
冲侧面4处均布的止口。
(四)拉伸工艺设计此零件拉伸类工艺比较复杂,包括拉伸、反拉伸、整形等工序。
模具毕业设计34电机端盖压铸模设计说明书

一、零件图如图1-1所示制件为电机端盖,材料为锌合金,属大批量生产。
图1-1一、该压铸件的材料分析和工艺性分析1. 材料分析该产品的成型材料是锌合金,该材料密度大,铸造性能好,可压铸复杂的零件,压铸时不粘模,压铸件表面易镀Cr、Ni等金属,机械切削性能好,但易老化,抗腐蚀性能不高。
2. 工艺性分析1)锌合金压铸,其锌不容易就粘在模具表面上。
2)该压铸件壁厚比较均匀,各个孔小且浅,工艺性好。
3)为了方便加工与成型及脱模,型腔、型芯均采用组合式结构。
4)该压铸件是一般精度等级。
为降低设计难度和设计周期,应采一模一腔,且需要对压铸件去除浇口废料。
二、拟定的成型工艺1.成型方法该压铸件采用冲头下压式全立式压铸机压铸。
2.各工艺参数1)经查教材(压铸成型工艺与模具设计)第32页表3.2可知压射比压为30Mpa2)经查教材第33页表3.4可知压射冲头空行程压射速度为0.3~0.5m/s 3)经查教材第34页表3.5可知充填速度为15 m/s 4)经查教材第36页表3.7可知持压时间3~4s5)经查教材第36页表3.8可知留模时间推荐值为7~12s 6)经查教材第37页表3.9可知浇注温度为410~540C 。
7)经查教材第38页表3.10可知模具预热温度130~180C 。
和工作温度180~200C 。
3. 确定型腔数目1)为降低设计难度和设计周期,应采单型腔,且需要对压铸件去除浇口废料。
2)计算压铸的体积和重量通过三维制图PRO/E 软件测量得:单件压铸件投影面积S=14257㎜2;体积V=153645㎜3查有关资料可知Al 的密度为6.8g/cm 3则压铸件重量m=1044.8g三、初选压铸机1.压铸机的锁模力模具型腔胀型力中心与压铸机压力中心重合时压铸机锁模力 S F K ≥Z N (F +F )式中 S F —压铸机锁模力,N ;Z F —作用于模具型腔且垂直与分型面方向的胀型力,N ; N F —作用于滑快楔紧块面上的法向压力,N ;K —安全系数(一般取K=1~1.3)型腔胀型力Z F =P (123A +A +A )式中 P —最终的压射比压,Pa ;1A —铸件在分型面上的投影面积,㎡;2A —浇注系统在分型面上的投影面积与压铸件投影面积不重叠部分,㎡;3A —溢流槽在分型面上的投影面积,㎡;压铸机所容许的压射比压20.785n Fp D=式中 n p —压铸机所容许的压射比压,Pa ; F —压射力,N ; D —压室直径,m 。
电动机端盖注塑模具设计

摘要根据塑料制品的要求,了解塑件的用途,分析塑件的工艺性、尺寸精度等技术要求,考量塑件制件尺寸。
本模具采用一模二腔,直浇口进料,注射机采用HTF80XB 型号,设置冷却系统,CAD和UG绘制二维总装图和零件图,选择模具合理的加工方法。
附上说明书,系统地运用简要的文字,简明的示意图和和计算等分析塑件,从而作出合理的模具设计。
关键词:塑料制品;模具设计;CAD绘制二维图;塑件。
AbstractTo understand the use of plastic parts in accordance with the requirements of the plastic products, analysis of the technical requirements of the plastic parts of the process, dimensional accuracy, select the workpiece size of the plastic parts. The mold using a sprue gate feed injection machine adopts TOSHIBA the EC40-Y models, and set a cooling system, CAD and UG drawing two-dimensional assembly diagram and parts diagram, reasonable mold processing methods. Attach a manual, use brief text, a concise diagram and calculated analysis of plastic parts, in order to make a reasonable mold design.Keywords: mechanical design; mold design; CAD drawing two-dimensional map; molde目录第1章绪论 (1)1.1 塑料简介 (1)1.2 注塑成型及注塑模 (2)第2章塑料材料分析 (3)2.1 塑料材料的基本特性 (4)第3章塑件的工艺分析 (6)3.1 塑件的结构设计 (3)3.2 塑件尺寸及精度 (3)第4章注射成型工艺方案及模具结构的分析确定 (9)4.1 浇口种类的确定 (9)4.2 型腔数目的确定 (10)4.3 注射机的选择和校核 (10)4.3.1注射量的校核 (11)4.3.2塑件在分型面上的投影面积与锁模力的校核 (12)4.3.3模具与注射机安装模具部分相关尺寸校核 (12)第5章注射模具结构设计 (12)5.1 分型面的设计 (12)5.2 型腔的布局 (12)5.3 浇注系统的设计 (13)5.3.1浇注系统组成 (13)5.3.2主流道的设计 (14)5.3.3分流道的设计 (14)5.3.4浇口的设计 (15)5.3.5冷料穴的设计 (15)5.4注射模成型零部件的设计[7] (16)5.4.1成型零部件结构设计 (17)5.4.2成型零部件工作尺寸的计算 (17)5.5排气结构设计 (17)5.5.1 凹模宽度尺寸的计算 (17)5.5.2 凹模长度尺寸的计算 (18)5.5.3 凹模高度尺寸的计算 (18)5.5.4 凸模宽度尺寸的计算 (19)5.5.5 凸模长度的计算 (20)5.5.6凸模高度尺寸的计算 (21)5.6脱模机构的设计 (21)5.6.1脱模机构的选用原则 (22)5.6.2脱模力 (23)5.6.3推板机构具体设计 (24)5.7直向抽芯机构类型选择 (25)5.7.1滑块直抽芯机构设计 (26)总结 (27)致谢 (28)参考文献 (29)第一章绪论模具制造是国家经济建设中的一项重要产业,振兴和发展我国的模具工业,日益受到人们的重视和关注。
- 1、下载文档前请自行甄别文档内容的完整性,平台不提供额外的编辑、内容补充、找答案等附加服务。
- 2、"仅部分预览"的文档,不可在线预览部分如存在完整性等问题,可反馈申请退款(可完整预览的文档不适用该条件!)。
- 3、如文档侵犯您的权益,请联系客服反馈,我们会尽快为您处理(人工客服工作时间:9:00-18:30)。
1、
一 —
—
万方数据
=4 2%
由图1 该零件属有凸 可知, 缘带中 心局部凸 起
的回转体拉伸件。首先选取修边余量, 再将端盖零 件分解成几段简单的回转体,并分别求出各回转体 表面中性层的面积。 根据拉伸前后零件面积相等的 原则, 可计算出零件的毛坯尺寸为 07m o 10 m
22 工艺方案分析 .
收稿 日期 20 年 1 ,日 00 0月
sr c u e lc l so t n t e n e . tu t r o o a d t ri i h c tr f i o n e
K y od fr n ; csig h o g ; w n ; ud ew rs mig poes tcn l y da ig mol o r n e o r
图 3 拉伸模结构 1 推件杆 2 凸模 3 凹模 4 压料板 5 顶杆 . . . . .
R=甲 a =冰咬而蔽a 7 . A/ =1 则预成形变形区的面积应为: A A 二R 一 2 + ( 2 r : x = ) = . +t1= 33 2 1.5) 26耘 , 7 一 8 (
预成形面积为:
Ae t 5 =3 7 2f 5 e =A x9 % 9 . x % 7 9 二3 7 3 mm2 7 . n
价 于 一)! 叼 i下 今 卜
图 a 反拉伸模结构
推板 2 凹模 .
3 凸模 4 顶件器 5 顶杆 .
设预成形球头高度 H o m,利用球头面 , m F 二l 积计算公式可得预成形球头半径 R 1m o e 9m = 为保证最后球头部分成形质量与模具结构的 合理性,预成形球面应向内凹进, 使最后球头部分
薛启翔 . 复杂形状零件引伸 、 北京: 机械工业出版社,
18 99
08 m 以保证零件重要部位的精度要求。 . , p
零件的工艺方案确定为:落料 ̄拉伸 ( 球头预 成形)  ̄反拉伸( 球头成形)  ̄冲孔 ̄整形 ̄切边。
拉伸檬结构如图 3所示 。反拉伸模结构加图 4
6 - 。 一
夏 华等 . 风扇电机端盖成形工艺及模具结构 . 金属
( 摸具工业}2 0 . . 2 3 0 1 No 5 总 4
电机 端 盖 成 形 工 艺 及模 具 设 计
株洲工学院( 湖南株洲 420) 108 王菊槐
〔 摘耍】 介绍了 屯机端盖冲压成形工艺 及其模具设计, 对中心带局部变形结构的拉仲件提供
丁工 艺分析 与模具设计的范例。 关.词 成形 工 艺 拉仲 模具
一
根据资料, 8 0F材料的最大变形程度 8 0 =3%, 其许用变形程度比 司= 25 0 2.% 因为 8 > 8 故球头部分不能 1 讨, , 直接成形,
万方数据
( 模具工业)20 . 5总 23 0 1N . 4 o
只 能先预成形一个较大的球头, 再收缩成一个小的 球头。 假设预成形变形区的尺寸扩大到图2 所示 中 3 点位置. 点的横坐标值 R应等于球头部分的 则3 展开毛坯半径, R值求解如下。 利用图 2 先算出各线段重心横坐标。 , a 段: 上 26m b 段 X 二85m , = .9 m, : : .9 m c b r e d
参 考 文 献 王孝培 . 冲压手册工艺 . 长沙: 湖南科技出版社,
18 98
3 工艺方案确定 通过上述分析计算可知, 端盖零件的关键工序 是拉伸及球头部分的预成形, 并将其复合在 1 副模 具上完成。另外, 圆角半径凸缘部分 R m和球头 l m 部分 R m均较小, 2 m 应通过整形获得。整形模凸、 凹 模之间单边间晾应小于料厚( 料厚09 m) . , m 制造 精度分别取 I 7和 I 8级 ,表面粗糙度 R = T T a
成形工艺.99() 18,3
朱敏君 . 徽电机端盖拉伸工艺及模具 模具工业,
19 ,2 95 ()
份今 伪, 。, 一 。 .。 ‘ 令。
。洲洲 脚 减 代 K ,加 吠 心伽。 份) 。。 份火心伪,  ̄ 。 。 ,沙 护。  ̄ 识, 伽。 俐)  ̄ 伪沙  ̄ 一
书 讯 ( 模具工业 存有少f 》 合订本,96 7 , 本.97 7 i/ 19 年 8 i/ 19 年 8 元/ 19 年 0t/ 19 年 5 本.98 0 本.99 5 本. t , t , 币蛤 元/ 欢迎直袂汇次到偏桥郑订的J 址: 本。 也 广西桂林市辰1路 1 邮绷:404 奥 4 号 510 姆满 离 { 7 ,0 3 7)
} A 3
[ bt c] h fr ig cs ad in te fr cvr it dcd tippr I A s atT e mn poes ds o h d o te e ae r ue i hs e. r o r n e g f i e h o r no n a t poie a ea l fr oes ayig d o l d s n da ig mpn ns t te rvds xmpe p cs a lz a m ud i o rwn c o e t w h n o r n n n e g f o i h
由零件图可知, 直径 0 m与 0 m之间阶 8m 8 9m 0 梯较小,经计算可以一次拉伸成形。零件总的拉伸 图1 是某电机端盖零件, 料厚为 15 m, . 材料 m 系数 二n 05, = . 根据资料 0F 2 8 钢在同等条件下的 为0F冷轧钢板。根据零件的技术要求可知, 8 尺寸 , 50 0 . >m,因此阶梯形圆 , 0 m的公差值为 01m ,表面粗糙度 R = 9m 0 . m 4 a 首次拉伸系数 m = 1 , a 筒主体部分可一次拉伸完成。 32m 属 . , 尺寸精度和表面质量 p 要求较高的 部位。 本零件的主要难点在于球头部分的成形。若球 尺寸 S l R m和 0 m具有较高的同轴要求, O m 9m 0 同 头部分采用直接局部成形工艺, 根据塑性变形理论, 轴度公差为 t . m。 1 0m 同时, 04 端盖所有表面要求平 材料的变形量不应超过其许用变形程度,利用图 2 滑, 不得有影响外观质量的划伤、 擦痕等缺陷。 01 0 可计算出局部成形时的变形程度。
段 x =1. , 17 mo m 根据久里金法则, 球头面积 A = 艺I , 0 2 x 得 2 c
所示 。
A. 2 (, 22 aO =2(, 26 + = l , X +l n X +1 X 7 53 x 9 r 8 . 96 x 9 . 1. 264m 2 . 85 + 1 17 = . m 0 6 . 39 x ) 8 7 i 又根据面积相等原则 A . 2有: * R。 =
=3 7 2 mm2 9 . a
考虑到球头部分成形实际上是拉伸与胀形两 种变形方式的叠加。 为了 保证零件尺寸精度和表面 质量,在球头最后一道工序里应有一定的胀形成 分。为此, 应使预成形面积稍小于零件实际变形区 的面 根据资料, 积。 取预成形面积为AI 5 则 的9%。
呈反向拉伸成形。
4 结柬语 端盖零件工艺方案的关铭是球头部分的预成形 设计与分析。如在球头最后成形时出现小皱纹现 象, 则应减小预成形球头高度及球头半径, 用以增大 末次球头成形中的胀形成分,从而保证其尺寸精度 及表面质量。生产实践证明,该设计达到了预期的 目的,它对中心带局部变形结构的拉伸件的工艺分 析及模具设计具有指导意义。
1 引 言
S 1 R 0
刻 y l R l 3
4S } }
B5 _'
C
ol
I d / 0: 9"
01 0 2
图 2 球面中性层尺寸分析
图 1 电机端盖
经分析, 图中各线段长度计算如下: 2 工艺计算与分析 21 毛坯尺寸计A .
a . m b段:, 3m L=5 8 b 段: = 6 96mm e l . = c . m d段: =39m 1 , 1 o 33m k段: =1. m r 5 球头直接局部成形时的变形程度为: 8 2 1+1+1) r/ r 0 % x =[(, , , 一2 12 X 0 1 =[(.8 96 39) 2 1.5/2 1.5 53 + . + .1 一 x 31(x 3) 2 6 3 3