IE生产线平衡分析表范例
合集下载
现场IE改善案例分析--生产线平衡分析改善案例
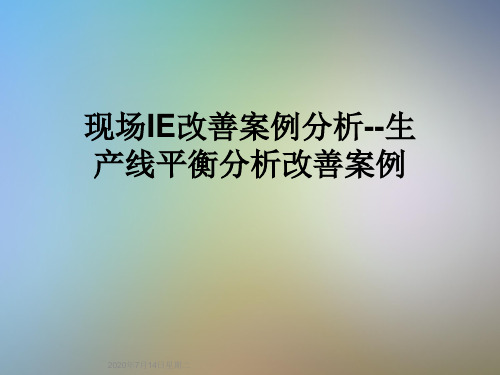
生产线平衡定义
对生产的全部工序进行均衡,调整作业 负荷和工作方式,消除工序不平衡和工 时浪费,实现“一个流”。
出料
入料
平衡生产线的意义
通过平衡生产线可以综合应用到程序分析、动作分析 、layout分析,搬动分析、时间分析等全部IE手法,提 高全员综合素质
在平衡的生产线基础上实现单元生产,提高生产应变 能力,对应市场变化实现柔性生产系统
(4) 4种增值的工作
站在客户的立场上,有四种增值的工作
1、使物料变形 2、组装 3、改变性能 4、部分包装
物料从进厂到出厂,只有不到 10% 的时间是增值的!
工序
符 号
内容
作业内容
分类
加工 作业
○
加工 作业
■产生附加价值的工序及作 业
卖得掉
检查
□
数量检查 ■虽然有必要,但需要进行 品质检查 改善的工序及作业
现场IE改善案例分析--生 产线平衡分析改善案例
2020年7月14日星期二
内容安排
一、线平衡定义 二、生产线平衡分析方法 三、B值、F值的定义与计算 四、线平衡案例分析
一、线平衡定义
生产线平衡定义
什么是生产线平衡
生产线平衡是指构成生产线各道工序所需的 时间处于平衡状态,作业人员的作业时间尽 可能的保持一致,从而消除各道工序间的时 间浪费,进而取得生产线平衡。
减少人手(1)
將工序3里的工作时 间分配至工序2﹑4 及5之內﹐从而工序 3里的人手可调配其 它生产线去
可行性﹕須工序 2﹐4及5內均有足夠 时间接受额外工作。
ቤተ መጻሕፍቲ ባይዱ
生产线平衡-例3﹕减少人手(2人)
降低线体速度,减少生产产量
工作時間
【实用文档】IE工程之产能分析表精华版

XX公司
流水线平面图
线别
6线
适用品名:
xx208 xx208b
序号
工序名
1 涂黄油
2 压中盘轴承
3 套装中上盘
4 安装中盘铆钉
5 安装手柄
6 装弹簧
7 安装旋钮
8 旋旋钮
9 铆铆钉
10 检查平度并矫正
11 绞锥度孔
12 吹铁屑
13 检锥度孔 上油
14 铆马车螺丝
15 表面擦试
16 铆接面涂油漆,贴标
0 2011/11/26
REV 改定日
新规作成
更改内容
朱球
作成
承认
装箱 打包
维修
送
检查
绞深
平度
度孔
并
整平
帶
安装 旋钮
目視總檢
装弹 簧
安装 中盘 铆钉
压中 盘轴 承
压中 盘轴 承
涂黄 油
设备名
压入工装夹具
铆钉机 矫正夹具 绞孔机
ST 3.28 4.60 4.02 5.02 2.67 4.23 5.00 2.67 3.74 3.69 3.85 3.58 3.80 3.71 3.39 5.80 5.50 3.90 5.00 3.58 3.80
17 外观检查
18 维修
19 包装
20 装箱
21 封箱
产能分析表
品名
xx208AA
作业人数
25
生产能力/8H
4220
管理号码: xx-LY-0001
承认
确认
作成
朱球
包装
铆马 车螺 丝
检锥 度孔
/ 上油
吹铁 屑绞深 度孔铆铆旋紧钉旋钮
安装 手柄
流水线平面图
线别
6线
适用品名:
xx208 xx208b
序号
工序名
1 涂黄油
2 压中盘轴承
3 套装中上盘
4 安装中盘铆钉
5 安装手柄
6 装弹簧
7 安装旋钮
8 旋旋钮
9 铆铆钉
10 检查平度并矫正
11 绞锥度孔
12 吹铁屑
13 检锥度孔 上油
14 铆马车螺丝
15 表面擦试
16 铆接面涂油漆,贴标
0 2011/11/26
REV 改定日
新规作成
更改内容
朱球
作成
承认
装箱 打包
维修
送
检查
绞深
平度
度孔
并
整平
帶
安装 旋钮
目視總檢
装弹 簧
安装 中盘 铆钉
压中 盘轴 承
压中 盘轴 承
涂黄 油
设备名
压入工装夹具
铆钉机 矫正夹具 绞孔机
ST 3.28 4.60 4.02 5.02 2.67 4.23 5.00 2.67 3.74 3.69 3.85 3.58 3.80 3.71 3.39 5.80 5.50 3.90 5.00 3.58 3.80
17 外观检查
18 维修
19 包装
20 装箱
21 封箱
产能分析表
品名
xx208AA
作业人数
25
生产能力/8H
4220
管理号码: xx-LY-0001
承认
确认
作成
朱球
包装
铆马 车螺 丝
检锥 度孔
/ 上油
吹铁 屑绞深 度孔铆铆旋紧钉旋钮
安装 手柄
现场IE改善案例分析.pptx
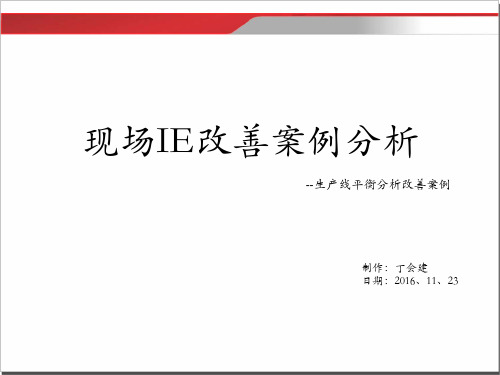
4、工时测定分析(蓝色为作业的时间红色为失去平
衡的时间)
5、生产线平衡的计算
生产平衡率(%)=各工程净时间总计/(时间最长工程*人 员数)*100%
如上图表中,生产线平衡率=1505/(90*19)*100%=88% 不平衡率%=100%-平衡率(%) 对生产线来说,不平衡率越小越好,一般控制5%-13%之间,
有多少岗位是不增值的
扑克牌游戏规则
1、每个分厂安排4个人(厂长、工艺、作业长、班长) 2、小组内部自己安排4个人的工作 3、要求是将52张扑克牌按同一花色、从大到小的排成一排 4、时间最少的小组获胜 5、开始和结束计时以固定的人员手敲桌子为准 6、游戏开始由工作人员将牌洗好
评分标准
1.2.3.4名分别100.80.60.40分错 一张牌,扣10分
(2)IE动作改善的4原则:
• ECRS原则 1.Eliminate —取消 2、Combine —合并 3、Rearrange —重排 4、Simplify —简化
(3)ECRS法运用图示ห้องสมุดไป่ตู้介
生产线平衡—例1:缩短生产节拍
提升生产速度,维持人手不变
缩短生产节拍 将工序2里一部 分可抽离的时间 转至3工序里, 以缩短整体的生 产节拍
降低线体速度,减少生产产量
减少人手(2) 因生产需求量降低而可 降低线体速度
将工序3.4的工作时间 分配至工序1.2.5里,从 而工序3.4工作岗位的 人手可调配至其它生产 线去。
(4)4种增值的工作
站在客户的立场上,有四种增值的工作
1、使物料变形 2、组装 3、改变性能 4、部分包装
现在请大家思考一下…… 我们的生产线上
电装7人线标准工时
请 计 算 平 衡 率
IE生产线平衡资料

工時测量(秒表)
工具: 秒表 ❖ 观测板、铅笔 时间记录表、计算器 山积表
方式: 一般测时法 ❖ 连续测时法
2021/6/7
11
时间测量流程
作业內容
选定测试工站
选定工站,阅读SOP和观察作业员操作,了解 該工站的全部操作內容;并询问作业员加以 确认;
拆解动作
将工站动作拆解成若干个单一的操作內容, 并填入<<时间记录表>>
时间
T1 T2 T3 T4 T5
等待时间
单个产品平衡损失 =等待时间之和
S1 S2 S3 S4 S5
工站
概念7:平衡率100%代表﹕ 1.工站之间无等待,前后产能一致﹔ 2.工站节拍相同,动作量相同(动作量是指工站中各种必要动
素的时间总量); 3.平衡损失时间为零; 4.设计效率最大化; 5.前后流程的设计可以更完善(如下图).
t1
当S1-1不需等 S1-2就能开始, S1工站时间为﹕ S1-2的时间
S1-1 S1-2 S1-1 S1-2 S1-1 S1-2 工站
2021/6/7
28
平衡的步驟
Steps 4: 山积表平衡 联合操作的工站时间(S1-1>S1-2)
时间
t4 t3 t2
S1标准时间为﹕t2+t3; S1工站时间为﹕t4
4. 六大步骤:
5.
选择—确定研究对象
❖ 记录—用程序图/路线图等记录工作
分析—用5W1H、ECRS分析改进
建立—建立新方法的模拟图
实施—按模拟图实施新方法
维持—将有效的方法标准化
2021/6/7
19
損失分析
1. 目的:计算分析生产中的所发生的损失,並加以停止. 2. 损失的种类:
IE标准工时及线平衡

61.8
65.77
40.00
12.7
0.00 1 2 3 4 5 6 7 8 9 10 11 12 13 14 15 16
备注:
产线布局图(Line Layout)
工序 2-2
宽放率:人工8%,设备(治具)10%
TOTAL工序时间:'Tc'=Σ Tc' 节拍时间(s):'Ts'=Max('C/T') 标准工时(s/PCS):'ST'='Ts'*'N' 22547.9 156.26 39845.1 23.0 255.0 0.1 0.4
23 29 37 40 43 53 58
160.00
156.3
151.3
140.00 123.8 120.00 100.5 90.5 83.8 80.00 68.5
61.8 60.00 43.1 70.8 93.4
104.0
100.00
98.0
51 39 36 58 84 283 35 24 55
20.00
生产线平衡率计算表
Doc. NO.文件编号 Schedule Qty 数量(PCS/11Hr): NO.of pro工序编号 1 2 3 4 5 6 7 8 9 10 11 12 13 14 15 16 ProcessName 工序名称 253.4 Time of Pro工序时间(S) TC 1562.6 5324.7 784.0 1266.8 1257.3 205.5 247.1 2972.0 373.4 1708.1 803.2 560.3 229.0 3537.4 1058.8 657.70 No.of Operators 人员安排 Model (型号): T/T (节拍): Cycle time 周期时间 (S)C/T 156.3 UPH 每小时产量 (PCS/Hr) Labour(人力) Machine Requirement 设备 需求
最新IE生产线平衡资料

IE生产线平衡资料
相关的概念
产出的速度取决于时间 最长的工站,称之瓶颈 瓶颈在哪里? 了解加工的过程
2020/10/22
2
相关的概念
概念1: 平衡率
用语衡量流程中各工站节拍符合度的一個综
合比值;
单件标准时间
平衡率= ----------------------100%
瓶颈时间工位数
时
T2
瓶颈时间
测试样本大小計算
山积表
山积表的使用: [图表生成方法]
山积表:将各分解动作时间,以叠加式直方图表现 的一种研究作业时间结构的手法.
样式:
產品xxx工時山積表
秒
10
8 6
0
0 1.5
1.5 0.5
1.5
10 2
1.5 2
10
0.5 1.3
2
10 3
0 4
4
4
6
1
3
1.5 3
2
2
3.5
3.5
2
2
2020/10/22
4
相关的概念
概念4:设定产能 设定产能(H) =3600(S)/瓶颈时间(S) 设定产能(班)=投入時間/瓶颈时间(S)
思考:1)为什么设定产能(班) =投入工时/总工时 总工时=瓶颈时间*作业人数
2)总工时 VS 单件标准时间
概念5:实际产量 实际产量是可供时间內所产出的良品数 1)人均产能=实际产量/投入时间/人数 2)单机台产能=实际产量/投入时间/机台数
时间测试
分解动作时间量测,一般每个动作测量5 次为宜; ❖ 量测人员应站在作业员斜后面1米以外, 以能看清楚全部操作动作为准则; 测试中不能打扰作业员的正常操作和引 起作业员的紧张;
相关的概念
产出的速度取决于时间 最长的工站,称之瓶颈 瓶颈在哪里? 了解加工的过程
2020/10/22
2
相关的概念
概念1: 平衡率
用语衡量流程中各工站节拍符合度的一個综
合比值;
单件标准时间
平衡率= ----------------------100%
瓶颈时间工位数
时
T2
瓶颈时间
测试样本大小計算
山积表
山积表的使用: [图表生成方法]
山积表:将各分解动作时间,以叠加式直方图表现 的一种研究作业时间结构的手法.
样式:
產品xxx工時山積表
秒
10
8 6
0
0 1.5
1.5 0.5
1.5
10 2
1.5 2
10
0.5 1.3
2
10 3
0 4
4
4
6
1
3
1.5 3
2
2
3.5
3.5
2
2
2020/10/22
4
相关的概念
概念4:设定产能 设定产能(H) =3600(S)/瓶颈时间(S) 设定产能(班)=投入時間/瓶颈时间(S)
思考:1)为什么设定产能(班) =投入工时/总工时 总工时=瓶颈时间*作业人数
2)总工时 VS 单件标准时间
概念5:实际产量 实际产量是可供时间內所产出的良品数 1)人均产能=实际产量/投入时间/人数 2)单机台产能=实际产量/投入时间/机台数
时间测试
分解动作时间量测,一般每个动作测量5 次为宜; ❖ 量测人员应站在作业员斜后面1米以外, 以能看清楚全部操作动作为准则; 测试中不能打扰作业员的正常操作和引 起作业员的紧张;
生产线平衡分析与改善(最全面的IE分析,生产线平衡)ppt课件
0.1
0.2 0.5 1.0 2.0 5.0 ≥10
<1.0 100 50 20 10 5 2 1
1.0~2.0 50 20 20 10 5 2 1
2.0~5.0 20 20 10 5 2 2 1
5.0~10 10 10 5 2 2 1 1
13
三、流水生产线平衡的设计方法
3、 单品种流水线平衡方法 ● 案例:生产线平衡分析案例(直流式流程序为例)
10 A
工序1
工序2 11 B
工序3 12 E
C5
4 D
工序4 3
F
11 H
7
工序6
G
3 I
工序5 34
五、生产线平衡的其它案例
装配流水线平衡的方法很多,这里介绍一种简便而又能取得 满意效果的方法——阶位法。 阶位法的工作步骤如下
① 作图表示装配工艺过程中各作业元素的先后关系,并标 明每项作业元素的时间。 ② 从作业元素先后关系图找出每项作业元素的后续作业 元素,计算它们的时间总和,即每项作业元素的阶位值。 ③ 按阶位值的大小,由大到小,将作业元素排队,制成 作业元素阶位表。 ④ 从阶位值最高的作业元素开始,向工作地分配作业要 素。每分配一项作业元素,计算一次在节拍时间内的剩余 时间。若剩余时间足够安排另一项作业元素,从阶位表中 找出阶位值次高的作业元素分给该工作地。若剩余时间不 够安排其它作业元素,就向下一个工作地分配,直到全部 作业要素都被安排入工作地为止。
比较B、C两个工作站,将可发现B工作站的产能为C工作站的 2.69倍,B、C两个工作站将积压大量的半成品。若以传统追求 各工作站提升效率的方式进行管理,B工作站的效率提升,只会 恶化B、C站的半成品积压的浪费,而无助于整体产量的提高 (假设B工作站经训练生产效率达100%,则B工作站每小时产量 将达702.35个,产量为C工作站的3.36倍)。
IE生产线平衡
資料分析與處理
對量測記錄之所有資料進行分析,對比ST的
差異程度,解決發現的問題;
❖ 若分析發現標準時間制定不當,應及時修
改,必要時調整制程.
13
2006-4-14
第十三页,共38页。
13
工時測量的作用﹕
獲取各工站的實際操作時間﹐為山積表制作﹐時間平衡作准備 ﹔
通過時間觀測﹐分析作業價值﹐發現問題和改善空間﹔
19
2006-4-14
第十九页,共38页。
19
損失分析
1. 目的:計算分析生產中的所發生的損失,並加以停止.
2. 損失的種類:
平衡損失(流程排位所造成的損失)
❖操作損失(生產中異常及不良造成的損失)
稼動損失(計劃停線損失)
總損失=稼動損失+平衡損失+操作損失
平衡損失 =(瓶頸作業人數-單件標准時間)設定產能
測試中不能打擾作業員的正常操作,和引 起作業員的緊張;
12 12
第十二页,共38页。
時間測量流程
數據與信息記錄
作業內容
測試中判斷作業員的速度水平,並作如實記
錄,不可修改量測數據;
❖ 若有其他特殊情況,也應加以實錄;
數據整理和計算
測試完畢,對數據進行整理和計算,補充測
量有懷疑或錯漏的數據;
❖ 計算可信度95%所需的樣本數量,補測差異樣 本數量
2006-4-14
第五页,共38页。
5
相關的概念
概念4:設定產能 設定產能(H) =3600(S)/瓶頸時間(S)
設定產能(班)=投入時間/瓶頸時間(S)
思考:1)為什么設定產能(班) =投入工時/總工時 總工時=瓶頸時間*作業人數
2)總工時 VS 單件標準時間
生产线平衡分析与改善最全面的IE分析生产线平衡
最全面的IE分 析生产线平衡 案例分析
PART 1
单击添加章节标题
P生A产R线T平2衡分析的概念和重要
性
生产线平衡分析的定义
定义:生产线平衡分析是指对生产线上的各个工 序进行平衡,使各工序的工作时间尽可能相近, 从而提高生产效率的过程。
目的:通过对生产线平衡进行分析,可以找出生 产过程中的瓶颈工序,优化生产流程,提高生产 效率,降低生产成本。
跨部门协作:加强各部门之间的沟通与协作,共同推进生产线平衡改善的实施和监控工作。
PIEA分R析T在5生产线平衡改善中的
Hale Waihona Puke 应用IE分析的基本概念和原则
IE分析的定义:工业工程分析, 旨在提高生产效率和降低生产成 本。
IE分析在生产线平衡改善中的应 用:通过分析生产线上的瓶颈、 浪费和不合理之处,提出改善方 案。
注意事项3:考虑人机配合 和作业节拍
注意事项1:分析前要明确 目标和范围
注意事项4:注意设备维护 和保养
PART 4
生产线平衡改善的策略和措施
生产线平衡改善的目标和原则
提高生产效率:通过优化生产线布局和作业分配,降低生产成本,提高产出效率。 降低不良品率:通过平衡生产线上的作业,减少生产过程中的波动和异常,降低不良品率。 提高员工满意度:通过合理分配工作量和减轻员工负担,提高员工的工作积极性和满意度。
生产线平衡分析的工具和技术
作业分析:确定每个作业步骤的时间和顺序,识别瓶颈和浪费。 工艺流程图:可视化生产线流程,找出潜在的改进点。 动作分析:研究工人操作,优化动作,提高效率。 生产计划与调度:合理安排生产计划,确保生产线的平衡。
生产线平衡分析的注意事项
注意事项2:充分了解生产 流程和工艺要求
生产线平衡IE教材
估算
分支定界—举例
第3步:可能的方案
方案3-1:{(3), (8)} 方案3-2:{(7)} T31 = 5+3 = 8, S31 = [(46-10-8-8)/10]+3=5 T32 = 6, S31 = [(46-10-8-6)/10]+3=6 选方案3-1进行
估算
分支定界—图示
(1), (2), (5)
(4), (5) (3), (8) (7) (10) (7)
(1), (2), (6)
(3), (5) (4) (7), (5) (3), (9)
(4), (8)
(9), (10)
(10), (11)
(11)
COMSO 2) A为当前所有没有分配的作业集合 3) B为A中从顺序约束的要求的意义上说可选 择的作业集合 4) 如果iB, 且tiT,那么将i置于F, 如果B中没 有任何i能满足, 则T=C 5) 从F中随机选取一个作业i, A=A-i, T=T-ti, 此时,如果A为空,算法停止, 否则转3).
COMSOAL—例子
节拍C=70秒
计算过程
位置排序法
对所有作业i计算它本身和它所有的后续作业 的加工时间的和,记为Pwi, 将Pwi按大小排序 按照排序先后和分配工序。
位置排序法—例
作业
a b
PW
138 118
序号
1 3
作业
g h
PW
102 87
序号
5 7
c
d e f
112
123 85 97
A A A A B B B B i i C C C i i A 0 A A B 0 B B C 0 C C A B