生产线平衡分析
生产线平衡分析简介

生产线平衡分析简介一、生产线平衡的定义流动的作业中上下工序之间,存在供应关系,一旦工序作业时间相差太大,就会造成某些用时短的工序,出现等待的现象,其中工时损失相当客观,当工序之间的作业时间差距很少,生产中等待的时间很少,生产效率达到最高时,我们称为生产线平衡率。
二、生产线平衡分析的目的1短短生产一个产品的组装时间〈增加单位时间的生产量>2.提高生产线的工作效率〈包括作业人员,设备>3.减少工作间的准备工作4.提高生产线的平衡5.对新的流程作业方式改善制造方法三、生产线平衡分析方法生产线平衡分析是对改善流程作业的最适用的方法,在改善之前必须对工序进行分析。
1先确认分析对象,生产线和对象工程的范围。
6.实施对象生产线的工程分析把握现状。
7.实施各工程的时间分析<如设定标准时间就灵活运用》8.制作速度图表9.计算生产线平衡率。
四、改善生产线平衡的方法1对作业长的工序进行改善,其改善方法有:11分割作业,把一部分作业分配到作业短的工序中去。
12进行作业改善,缩短作业时间1.3作业机械化1.4提高机械化的能力1.5增加作业员或替换技能水平更高的作业员2.对作业时间短的工序进行改善2.1分割那部份的作业,将其分配到其他时间短的工序中去,省略那一工序。
2.2可从作业长时间的工序中抽一部分工作过来。
2.3可以与其他作业时间之工序相结合。
2.4分配至两个以上的工序,尽量让一个人去作。
五、生产线平衡率的计算1.平衡率的计算方法:生产平衡率二各工程净时间的总和/时间最长的工程作业时间经XIO0%2.不平衡的计算方法不平衡率=Io0%-平衡率(%)如:生产一个产品的总时间为136秒,人力为19人,时间最长的工序为10秒,那他的生产平衡率为:生产平衡率=136S∕(10SX19人)X100%=71.6%不平衡率=IO0%-716%=28.4%。
SMT生产线平衡分析

SMT生产线平衡分析SMT生产线平衡分析是指通过分析和优化表面贴装技术(Surface Mount Technology,简称SMT)生产线的各个工作站(Workstation)之间的工作内容和流程,以实现生产线的平衡和高效性。
这是一项非常重要的任务,因为SMT生产线的效率直接影响到产品的生产速度和质量。
一般来说,SMT生产线由多个工作站组成,每个工作站负责不同的任务,例如元件精确贴装、焊接、测试等。
不同工作站之间的工作内容和时间必须协调一致,以保证整个生产线的平衡和流畅运行。
首先,要进行SMT生产线平衡分析,需要对整个生产线进行详细的分解和描述。
这包括每个工作站的工作内容、工作时间和工作顺序等。
通过对生产线进行分析,可以发现其中的瓶颈和问题点,从而制定相应的优化措施。
其次,要对每个工作站的工作时间进行评估和优化。
每个工作站的工作时间应该尽量稳定和合理,以避免工作站之间的阻塞和等待。
如果一些工作站的工作时间过长,可以考虑增加人力或者优化工艺,以提高工作效率。
如果一些工作站的工作时间过短,可能需要增加工作内容或者平衡其他工作站的负荷,以避免生产线的不平衡。
另外,要对工作站之间的流程进行分析和优化。
每个工作站之间的物料传递和信息传递应该尽量简化和快速,以避免生产线的堵塞和延迟。
可以考虑采用自动化设备和系统来提高物料传递的速度和准确性,同时优化信息传递的方式,以保证整个生产线的高效运行。
此外,还需要对SMT生产线的节拍进行控制和调整。
节拍是指每个工作站所需的工作时间,它直接影响到整个生产线的生产速度。
如果节拍过快,可能导致工作站无法及时完成任务;如果节拍过慢,可能导致生产线的闲置和低效。
因此,需要根据实际情况和需要,合理设置每个工作站的节拍,以平衡生产线的速度和质量。
最后,为了保证SMT生产线的平衡和高效性,需要对生产线进行定期的监控和分析。
可以使用数据收集和分析系统,实时监测和分析生产线的状态和性能。
生产线平衡分析与改善(最全面的IE分析-生产线平衡)

2023/12/24
8
二、流水生产线概述
1、 流水生产的基本概念 ● 流水线生产的分类
➢单人单产品式 ➢单产品固定式 ➢多产品固定式 ➢自由流水式 ➢连续传动流水式 ➢ 间歇传动流水式 ➢分组式
设某一产品从原料到成品,需经过A、B、C、D四个工序,其基本标 准工时(秒/个)及相关生产效率、良率、投入机台/人员数分别见表11: 可以求各工序每小时产量为: A工序每小时产量=(3600秒÷6.90)×90%×95%×1=470.87个 B工序每小时产量=(3600秒÷5.1)×80%×99.5%×1=470.87个 C工序每小时产量=(3600秒÷34.40)×100%×99.9%×2=209.09个 D工序每小时产量=(3600秒÷30.40)×100%×99.5%×2=238.8个 。
IE工业工程
-----生产线平衡
主讲:
课 程 内容
生产线平衡 一、生产线平衡的概述 二、流水生产线概述 三、生产线平衡的设计 四、生产线平衡的方法及改善原则 5、案例分析
2023/12/24
2
1.概念
一、生产线平衡的概述
生产线平衡即对生产的全部工序进行平均化,调整作业 负荷,以使各作业的时间尽可能相近的技术手段与方法,它 是生产流程设计及作业标准化中最重要的方法,是通过平衡 生产线使现场真正实施生产同步化,从而达到“一个流”的 理想。
2023/12/24
。
28
四、生产线平衡的改善方法与原则
2、平衡率改善的图示。
2023/12/24
29
四、生产线平衡的改善方法与原则
生产线平衡案例分析过程

生产线平衡案例分析过程1. 引言生产线平衡是一种优化生产过程的方法,旨在确保生产线上的工作站之间的工作负载均衡,以提高生产效率和产品质量。
本文将以一个实际案例为例,分析生产线平衡的过程。
2. 案例背景假设某公司生产手机,并且生产线上有三个关键工作站:组装、测试和包装。
每个工作站的工人数量不同,导致工作负载不均衡,组装工作站负责最多的工作量,而测试和包装工作站的工作负载较少。
3. 数据收集为了分析生产线平衡的问题,首先需要收集一些关键数据。
包括每个工作站的工作时间、工人数量以及每个工作站的工作量。
工作站工作时间(分钟)工人数量工作量(数量)组装工作站30 3 200测试工作站25 2 150包装工作站20 2 100通过收集这些数据,可以计算出每个工作站的单位时间工作量,即每分钟能完成的工作量。
根据上表数据,可以得出以下结果:•组装工作站的单位时间工作量为6.67件/分钟(200件/30分钟)•测试工作站的单位时间工作量为6件/分钟(150件/25分钟)•包装工作站的单位时间工作量为5件/分钟(100件/20分钟)4. 分析和优化通过计算每个工作站的单位时间工作量,可以判断哪个工作站是生产线上的瓶颈工作站。
在这个案例中,组装工作站的工作量最大,成为瓶颈,会导致生产线的工作负载不平衡。
为了平衡工作负载,可以采取以下优化措施:•调整工人数量:增加组装工作站的工人数量,以减轻其工作负荷。
•优化工作时间:分析工作时间,寻找减少生产时间的方法,例如改进工艺或引入自动化设备。
•转移工作量:将部分组装工作转移到其他工作站,以平衡各工作站的负载。
5. 优化结果评估经过优化措施的实施后,重新计算每个工作站的单位时间工作量,以评估结果。
工作站工作时间(分钟)工人数量工作量(数量)单位时间工作量(件/分钟)组装工作站30 4 200 5测试工作站25 2 150 6包装工作站20 2 100 5通过调整组装工作站的工人数量,将其增加到4人,重新计算单位时间工作量之后,可以看到组装和包装工作站的工作量现在已经达到了平衡,测试工作站的工作量仍然保持不变。
生产线平衡分析
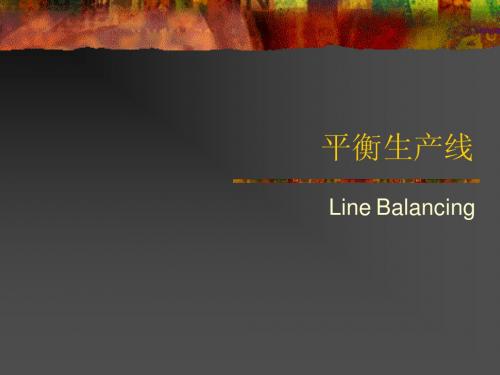
拉平
Line balancing 改善案例
现状调查
现状分析:从作业时间及平衡率看,生产 线的平衡损失比较严重,且作业分工过细, 造成作业内容调整困难。因此在作业改善 上所采取的较直接简便的方法即是合并工 序的内容,调整并取消时间过短工序,以 达到提高平衡,减少工时损失,提高人均 效率的目的。
Line balancing 与“一个流”生产
在生产现场,无论是分工的皮带生产线, 还是手工传递,当平衡率达到85%以上时, 就可以基本实现一个流的生产方式了。
•
Line balancing 的改善原则
平衡率改善的基本原则是通过调整工序的 作业内容来使各工序作业时间接近或减少 这一偏差。 方法 首先应考虑对瓶颈工序进行作业改善,作 业改善的方法,请按照程序分析的改善方 法及动作分析,工装自动化等工程方法与 手段。
将瓶颈工序的作业内容分担给其他工序。 增加各作业人员,只要平衡率提高了,人 均产量就等于提高了,单位产品成本也随 之下降。 合并相关工序,重新排布生产工序,相对 来讲,在作业内容相对较多的情况下容易 拉平衡。 分解作业时间较短的工序,把该工序安排 到其也工序中去。
平衡生产线
Line Balancing
平衡生产线的意义
• • • •
目的 提高作业员及设备工装的工作效率 减少单件产品的工时消耗,降低成本(等 同于提高人均产量); 减少工序的在制品,真正实现“一个流”; 在平衡的生产线基础上实现单元生产,提 高生产应变能力,对应市场变化实现柔性 生产系统;
通过平衡生产线可以综合应用到程序分析、 动作分析、LAYOUT分析,搬运分析、时 间分析等全部IE手法,提高全员综合素质。 Line balancing 的计算 要衡量生产线平衡状态的好坏,我们必须设 定一个定量值来表示,即生产线平衡或平 衡捐失率,以百分率表示。
工业工程中的生产线平衡分析

工业工程中的生产线平衡分析工业工程是一门涉及到人、机、料、法、环境等多个要素的学科,旨在优化和提高生产流程和工业系统的运营效率。
其中,生产线平衡分析是工业工程中的重要环节,对于确保生产线的高效运转至关重要。
本文将深入探讨工业工程中的生产线平衡分析,并介绍其实施过程和影响因素。
一、生产线平衡分析的定义和目的生产线平衡分析是指通过对生产线的各项工作任务进行评估和平衡,使得每个工位的工作时间和工作量能够合理分配,从而保持生产线的高效运行。
其目的是实现优化的生产线布局,提高生产效率,降低生产成本,并确保最终产品的质量及时间交付。
二、生产线平衡分析的实施过程在进行生产线平衡分析之前,首先需要收集大量的相关数据,包括生产线的结构和工艺流程、各个工位的工作内容和标准工作时间、员工的技能水平和工作能力等。
接下来,可以采用以下步骤进行生产线平衡分析:1. 定义工作元素:将整个生产流程细化成若干个工作元素,每个工作元素代表一个独立的工作任务或操作。
2. 评估工作时间:通过观察和测量,准确评估每个工作元素的标准工作时间。
这一步需要考虑到不同员工的工作速度和技能水平,以避免过于理想化的时间评估。
3. 分配工作量:根据每个工作元素的工作时间和工作内容的复杂度,合理分配工作量给各个工位。
工作量的分配要基于员工的能力和适应性,以确保每个员工能够承担适量的工作任务。
4. 平衡生产线:通过调整工作元素的安排和工作量的分配,使得各个工位的工作时间和工作量能够平衡。
这一步需要尽量避免出现瓶颈环节,即某个工位的工作量过大,导致整个生产线速度受限。
5. 设置合理的生产节拍:根据生产线的实际情况和产品的需求,设定合理的生产节拍,即每小时生产的产品数量。
要考虑生产线的稳定性和员工的工作强度,确保生产节拍既不过快导致质量问题,也不过慢导致生产效率降低。
三、影响生产线平衡的因素生产线平衡受到许多因素的影响,以下列举几个主要因素:1. 工作内容和复杂度:不同的工作任务所需的工作时间和工作量不同,而工作内容的复杂度也会影响员工完成工作的效率和速度。
生产线平衡案例分析PPTPPT课件
时
1﹑2﹑5里﹐从而工
间
序3﹑4工作岗位的人
手可调配至其它生产
线去。
(4) 4种增值的工作
站在客户的立场上,有四种增值的工作
1、使物料变形 2、组装 3、改变性能 4、部分包装
物料从进厂到出厂,只有不到 10% 的时间是增值的!
工序
符 号
内容
作业内容
分类
加工 作业
○
加工 作业
■产生附加价值的工序及作 业
3
温管 插室温管温7
温 打胶水
2
24
1
4
插线 插变压器线7
37
1
插线
30
插线
20
5
功能 功能检验 16
检 拆线
5
45
2
贴断电标贴4
外观检验 8
6
外观 检 贴条码
2
包装
6
16
1
生产线平衡的改善实例
电子电装7人柔性线,改善前各工位的作业时间如下所示:
50 45 40 35 30 25 20 15 10
one piece flow 是指单件的进行生产, 即工人每次 只加工一件产品或组件,理想状态下,任何操作 工位间和工位内的多余的WIP为零。
B值=1
一物流
物流
顺畅流动 没有停滞
物留
中间停滞 隐藏问题
“一个流”的益处
1. 内建品质管理; 2. 创造真正的灵活弹性; 3. 创造更高的生产力; 4. 腾出更多厂房空间; 5. 改善安全性; 6. 改善员工士气; 7. 降低存货成本。
工 作 時 間 工序 1 2 3 4 5
减少人手(1)
將工序3里的工作时 间分配至工序2﹑4 及5之內﹐从而工序 3里的人手可调配其 它生产线去
生产线平衡分析改善案例
生产线平衡分析改善案例引言生产线平衡是指在生产过程中,通过合理分配各个工序的工作量,使得各个工序的产能能够实现平衡,从而提高生产效率、降低成本,并确保产品质量。
本文将以一个实际案例为例,介绍生产线平衡分析和改善的具体过程。
案例背景某电子产品制造公司拥有一条生产线,生产一种电子产品,该产品的组装工序分为A、B、C、D四个子工序。
在目前的生产线上,工序A的生产能力远超其他三个工序,导致A工序成为瓶颈工序,无法满足后续工序的需求,从而影响了整个生产线的效率和产量。
因此,公司决定进行生产线平衡分析,并制定改善方案,以提高生产线的平衡度。
生产线平衡分析1. 数据收集首先,需要收集工序A、B、C、D的工作时间数据,包括每个工序的加工时间、准备时间和等待时间。
这些数据将作为分析的基础。
2. 流程图绘制根据数据收集到的各个工序的时间,并结合实际生产情况,可以绘制出生产线的流程图。
流程图可以清晰地展示每个工序的工作时间和流程顺序,有助于进一步分析。
3. 生产线平衡计算根据流程图,可以计算出每个工序的工作时间总和。
然后,根据目标产量,计算出每个工序的标准工作时间,即每个工序应该占用的时间比例。
通过比较实际工作时间和标准工作时间,可以评估生产线的平衡度。
4. 分析结果根据生产线平衡计算的结果,可以看出工序A的工作时间远超其他工序,导致生产线的不平衡。
这也解释了为什么A工序成为瓶颈工序。
改善方案1. 调整工序A的产能由于工序A是瓶颈工序,可以考虑通过增加设备或优化工艺,提高工序A的产能,以满足后续工序的需求。
这可以通过增加工序A的设备数量、提高工段效率或优化工艺流程等手段实现。
2. 优化其他工序除了调整工序A的产能外,还可以进一步优化其他工序的流程,减少每个工序的工作时间。
例如,可以通过流程改进、工艺优化、培训员工等方式,提高其他工序的效率,从而平衡整个生产线。
3. 调整生产计划根据生产线平衡分析的结果,可以对生产计划进行合理调整。
生产线平衡分析计划书范文
生产线平衡分析计划书范文
一、问题描述
公司A生产线存在平衡问题,产能利用率较低。
经分析,主要原因在于生产线各工序产能不均衡,可能导致生产线瓶颈,影响生产效率。
二、分析目的
针对公司A生产线平衡问题,开展深入分析,查明各工序产能水平,识别瓶颈工序,为平衡生产线提供依据。
三、分析方法
1. 了解生产线流程和各工序情况。
2. 统计历史数据,确定每个工序产能和产出效率。
3. 建立生产线任务分配模型,模拟生产线运行情况。
4. 计算各工序生产时间和工作量,识别瓶颈工序。
5. 提出改进措施,平衡生产线各工序产能。
四、分析内容
1. 调研生产线流程及工艺
2. 统计各工序历史产能数据
3. 建立生产线运行模型
4. 分析各工序产能水平以及产能利用率
5. 确定瓶颈工序
6. 计算平衡后各工序负荷情况
五、预期效果
通过对生产线进行深入分析,识别瓶颈工序,平衡各工序产能,使生产线达到均衡状态,提高整体产能利用率,为公司增加产值提供依据。
六、时间安排
1月:数据收集及分析模型建立
2月:分析报告初稿完成
3月:报告定稿及改进方案呈报
以上就是生产线平衡分析计划书的内容大纲,希望能为您的分析提供参考。
如果需要,还可根据实际情况进行 detail 调整完善。
生产线平衡分析计划书范文
生产线平衡分析计划书范文1. 项目概述
1.1 项目背景
1.2 项目目标
1.3 项目范围
2. 现有生产线状况分析
2.1 生产线布局
2.2 工序流程
2.3 生产能力评估
2.4 瓶颈工序识别
3. 生产线平衡方法
3.1 理论基础
3.2 数据收集
3.3 分析工具
4. 生产线平衡实施计划
4.1 工序重新排列
4.2 人员调配
4.3 设备优化
4.4 平衡目标及预期效果
5. 项目进度安排
5.1 阶段划分
5.2 关键里程碑
5.3 风险评估
6. 资源需求
6.1 人力资源
6.2 设备资源
6.3 经费预算
7. 监控与评估
7.1 关键绩效指标
7.2 监控机制
7.3 持续改进
8. 附件
8.1 现有数据统计
8.2 相关图纸
8.3 其他支持文件
以上是一个生产线平衡分析计划书的标准框架结构,具体内容需要根据企业实际情况进行修改和补充。
该计划书旨在全面分析现有生产线的状况,制定合理的平衡方案,优化生产流程,提高生产效率,为企业创造更大的经济效益。
- 1、下载文档前请自行甄别文档内容的完整性,平台不提供额外的编辑、内容补充、找答案等附加服务。
- 2、"仅部分预览"的文档,不可在线预览部分如存在完整性等问题,可反馈申请退款(可完整预览的文档不适用该条件!)。
- 3、如文档侵犯您的权益,请联系客服反馈,我们会尽快为您处理(人工客服工作时间:9:00-18:30)。
电子分厂主控板装配线体生产线布局与人员配置
板面终检2人 下线 IC扫油 功能测试
板面检查3人 插件12人
锡炉
板底扫油 撕边加胶 板底终检3人 ICT2人 板底检查4人
电子分厂主控板装配线体各工位时间分析1
1
13.63 12.72 15.53 16.18 14.43 14.50 ###### ######
3
2
4
3
5
4
5
6
7
8
9
10
*72 终检(1)
装阀母
装堵母
紧固顶盖
No.
作业要素
装顶盖/贴商标 贴生产日期标贴、贴铭牌、注意标 贴 装阀母(2个) 装堵母(3个)
1 读 时间 10.9 读
2 时间 9.0 读
3 时间 9.3 读
4 时间 10.1 读
5 时间 9.2
合计
平均
1
48.4
9.7
2
15.5
3
倒片、检查修复翅片
5.22
12.23 8.72 8.72 6.37 3.63 3.58
6.35
13.46 8.26 8.26 6.13 3.01 3.67
5.34
13.48 9.01 9.01 6.51 3.27 3.21
5.01
10.83 8.95 8.95 6.20 4.01 4.15
6.18
12.66 9.67 9.67 5.81 3.25 2.98
5.62
12.53 8.92 8.92 6.20 3.43 3.52 13.16 8.92
合计
004 插输出管 1 插输出管 合计 1 005 插输入管 2 充氮 插输入管 合计 006 焊接一 1 焊接4处 1.0 1.0 1.0
13.58
5.39
4.69
生产线平衡分析图表
35
32.87
30
25
20.33
20
16.67 16.54
18.02
15
12.24
10
8.72 6.52
8.50
7.41 5.39
5
0
插件 板面检查 板底检查 ICT测试 功能测试 IC扫油 撕边加胶 板面终检 板底终检 板底扫油 打包
522.91 生产线平衡效率= 32.87 × 31
20.33
17.68 14.39 ###### ######
003
板底检 查
2 3 合计 1
4.0
10.09 16.63 14.12 15.59 14.06 15.50 15.22 15.16 18.44 15.47
16.54
14.39 15.67 ###### ######
004
ICT测试
2 3 合计 1
18.18
15.47
16.24
13.34
15.47 78.7
15.7
10.0
12.0
14.0
16.0
18.0
0.0
2.0
4.0
6.0
8.0
装顶盖/贴商标
贴生产日期标贴、贴铭牌、注 意标贴
装阀母(2个)
装堵母(3个)
紧固顶盖后
生产线平衡图表
紧固顶盖前
贴纸箱条码条、贴机身条码
部装大把手电路图
装大把手、接水盖
32.87
28.58 6.44 ######
010
板底 扫油
2
1.0 合计
4.78 3.37 5.85 4.38 6.28 5.50 7.56 6.12 7.75 4.07
3
7.41
######
6.44 4.69 ###### ######
1
011
打包
2 3 合计
1.0
3.37 4.38 5.50 6.12 4.07
16.13
15.33 15.33
15.26
16.01 16.01
15.24
15.93 15.93
15.38
16.03 16.03 16.03
总装分厂部装室内线体各工位时间分析2
008 焊接三
1 焊接感温套筒 合计 上输出管螺 母
1.0
11.93 11.93
11.50 11.50
12.01 12.01
a、分割作业,把一部分作业分配到时间短的工序中去; b、作业改善,缩短作业时间,如制作夹具、灵活运用工具等; c、作业机械化,提高机械的能力; d、替换技能水平更高的作业人员;
e、增加作业员。
B、对时间短的工序的改善方法:
a、分割作业,把这一工程的作业分配到其它工程,省去这一工程;
b、从作业时间长的工程拿一部作业过来;
10.93 10.93
12.18 12.18
11.71 11.71
11.71
009
1
合计 1
上输出管螺母
1.0
17.87
17.87
19.03
19.03 5.56 5.56 26.60 26.60 15.62 4.82 20.44 10.01 92.06 9.82
18.01
18.01 5.63 5.63 22.97 22.97 15.49 4.93 20.42 8.92 73.89 11.01
1.确定测定对象与范围
2、用工序分析把握现状
3、测定各工序的净时间 4、制作生产线平衡图表 5、计算生产线平衡率 6、分析结果,制定改善计划
生产线平衡PDCA
制定改善计划
P
执行改善方案
A C
D
检查改善进程
改善计划实做
生产线平衡方法
主要采取ECRS方法,简而言之如下:
A、对时间长的工序的改善方法:
8.23
9.32
8.13
8.49 44.0
8.8
7
贴纸箱条码条、贴机身条码
8.23
9.93
10.1
9.76
9.18 47.2
9.4
8
部装大把手电路图
7.19
7.38
5.53
6.25
7.13 33.5
6.7
9
装大把手、接水盖
12.22
13.19
12.47
13.68
14.58 66.1
13.2
10 清洁机身
各工位净时间总和 生产线平衡率(%)
=
时间最长工位(MAX)*工位数
×100%
3. 生产线平衡的目的
a、缩短生产一个产品组装时间(增加单位时间的生产量);
b、提高生产线的工作效率(包括人员与设备);
c、减少工序间生产准备工作;
d、改善生产线的平衡;
e、对新的流程作业方式改善制造方法。
4. 生产线平衡分析步骤
2.具体各个工位的时间分析测量
3.根据时间分析图表制定生产线平衡图表
4.计算生产线平衡效率后进行分析改善
生产线布局与人员配置图
修理线
20000
贴铭牌、注意标贴
检漏二(2) *62
大把手贴电路图 装大把手、接水盖 清洁机身
8 9 10 *73
装顶盖/贴商标
1 2
紧固顶盖 贴机身条码
6 7
终检(2)
1
013
18.48
010
装快速接头
装快速接头 合计
1.0
6.15 6.15 17.35 17.35
6.09
011
检大漏
1 合计 1
检大漏
1.0Байду номын сангаас
22.69
抽真空 充氦气 1.0
16.01 4.44 20.45
012
充氦气
2 合计 1 2 3
20.57
搬运到真空箱 检测(1次2个) 搬运到皮带线上
9.92 85.64 10.15
氦质 检电 源柜
主 通 道
通 道
通 道
制 图 姜宇超 日 期 06.5.16 单 位 审 核 批 准 日 期 日 期
比 例 1:10 总装一分厂部装 室内1线布置图
总装分厂部装室内线体各工位时间分析1
1 001 搬运、倒片 2 搬前蒸上线、检查修复翅片 搬后蒸上线 1.0 合计 002 组装蒸发器 1 组装前、后蒸发器(每人1颗螺钉) 合计 1 003 搬运、上线 2 3 上环形线 上固定卡 上皮带线 1.0 2.0 3.91 3.10 4.13 2.98 5.12 3.02 3.26 2.56 3.02 3.46 3.89 3.02 12.53
10.64 ######
008
板面 终检
2
2.0
3 合计
13.06 9.03 9.56 10.44 11.13 ###### 10.64
12.24
1
26.34
31.88
28.06
27.53
29.10
28.58
###### ######
009
板底 终检
2 3 合计 1
3.0
26.34 4.78 31.88 5.85 28.06 6.28 27.53 7.56 29.10 7.75
18.59
18.59 6.72 6.72 23.59 23.59 16.03 5.01 21.04 12.03 74.12 8.64
18.92
18.92 6.39 6.39 22.93 22.93 15.68 4.83 20.51 10.58 91.06 9.24
18.48
18.48 6.09 6.09 22.69 22.69 15.77 4.81 20.57 10.29 83.35 9.77
组装前、 (5) (4) (2) 氦气 (2) 插输入管 插输出管 折弯机 后蒸发器 回收 设备 (1) 搬运、倒片