生产线平衡分析和改善模板表
现场IE改善案例分析--生产线平衡分析改善案例
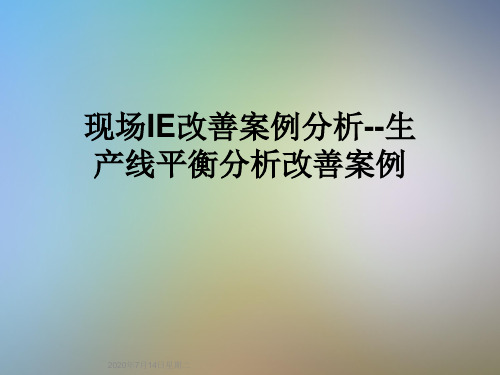
生产线平衡定义
对生产的全部工序进行均衡,调整作业 负荷和工作方式,消除工序不平衡和工 时浪费,实现“一个流”。
出料
入料
平衡生产线的意义
通过平衡生产线可以综合应用到程序分析、动作分析 、layout分析,搬动分析、时间分析等全部IE手法,提 高全员综合素质
在平衡的生产线基础上实现单元生产,提高生产应变 能力,对应市场变化实现柔性生产系统
(4) 4种增值的工作
站在客户的立场上,有四种增值的工作
1、使物料变形 2、组装 3、改变性能 4、部分包装
物料从进厂到出厂,只有不到 10% 的时间是增值的!
工序
符 号
内容
作业内容
分类
加工 作业
○
加工 作业
■产生附加价值的工序及作 业
卖得掉
检查
□
数量检查 ■虽然有必要,但需要进行 品质检查 改善的工序及作业
现场IE改善案例分析--生 产线平衡分析改善案例
2020年7月14日星期二
内容安排
一、线平衡定义 二、生产线平衡分析方法 三、B值、F值的定义与计算 四、线平衡案例分析
一、线平衡定义
生产线平衡定义
什么是生产线平衡
生产线平衡是指构成生产线各道工序所需的 时间处于平衡状态,作业人员的作业时间尽 可能的保持一致,从而消除各道工序间的时 间浪费,进而取得生产线平衡。
减少人手(1)
將工序3里的工作时 间分配至工序2﹑4 及5之內﹐从而工序 3里的人手可调配其 它生产线去
可行性﹕須工序 2﹐4及5內均有足夠 时间接受额外工作。
ቤተ መጻሕፍቲ ባይዱ
生产线平衡-例3﹕减少人手(2人)
降低线体速度,减少生产产量
工作時間
生产线平衡-模板

10.29 实测工时(S) 平均工时 (S) 39.3 34 36 41 36 42 45 38 40 40 38 35 36 50 36 45 51 39 37 40 41 34 35 44 37 41 46 40 39 38 35 34.3 35.7 43.8 35.8 40.2 46.3 38.7 38.3 37.8 37.7 瓶颈解决方法:员工作业2小 时,组长及时进线清包15分 钟;
41.4 43 47 39.4 39 88.87%
36.3 42.6 42.6 39.4 39.0 86.02%
36.7 42.6 42.6 39.4 39.0 82.23%
36.7 42.6 42.6 39.4 39.0 84.16%
36 86
37 88
34 85
38 86
39 91
36 82
36.7 42.6 42.6 39.4 39.0
三组工时统计表
10.22
序号 1 2 3 4 5 6 7 8 9 10 11 作业员 胡会群 叶斌 陈玉竹 郑晓艳 刘雨 胡龙海 宋玲丽 张群 郑裕锋 叶雅 吴尤琼 工序名称 返间袋布1/4单 线,四线及后幅 1/4双线拉后袋口 双线拉前袋口 订前袋位、洗水 唛套胶袋 装后袋边线 落钮牌、间单线 落拉链、转钮牌 落钮子、 埋小浪 装后袋内线 四线及前幅,三 线及前浪 五线及合底浪 三线及钮子钮牌 车后中主唛 间底浪单线 , 五线及合侧骨 三线及钮子钮牌 打侧骨暗枣 间侧骨1/8双线, 修止口 订耳仔*3,缩折 腰头,订后中吊唛 拉腰头 剪咀,挑线,封 咀 剪咀,挑线,封 咀 烫后袋、烫开侧 骨 翻裤脚,车脚口 42 38 39 40 37 37 40 38 39 42 44 37 47 48 43 43 50 40 47 39 49 实测工时(S) 43 34 44 50 45 45 48 45 49 40 45 46 37 45 48 43 45 51 43 50 42 48 45 38 49 51 46 43 48 44 49 40 47 45 38 48 50 45 48 52 45 48 43 49 平均工时 (S) 44.6 36.8 46.6 49.4 44.4 44.8 49.8 43.4 48.6 40.8 47.6
生产线平衡分析图表

序号
1 2 3 4 5 6 7 8
工序名称
工序1 工序2 工序3 工序4 工序5 工序6 工序7 工序8
示意图
○ ○ ○ ● ○ ○ ○ ○
工序内容
标准要求
使用设备/工具 岗位人数
2 1 1 1 1 1 2 1
标准工时 (s)
9.0 4.5 4.0 6.0 5.0 4.5 10.0 5.0
标准产能 (pcs/h)
400 800 900 600 720 800 360 720
平衡工时 (s)
4.5 4.5 4.0 6.0 5.0 4.5 5.0 5.0
平衡产能 (pcs/h)
800 800 900 600 720 800 720 720
利用率 (%)
75% 75% 67% 100% 83% 75% 83% 83%
600
核准
总标准工时
人均产出(pcs/人 *h)
72.50 40 审核
平衡率 损失率
80.56% 19.44%
制表
9
工序9
○
10
工序10○Βιβλιοθήκη 11 工序11检验△
12 工序12装箱
◇
注:○表示一般生产作业工序,●为瓶颈工序,△表示检测工序,◇表示包装。
1
4.5
800
4.5
800
75%
1
4.0
900
4.0
900
67%
1
5.0
720
5.0
720
83%
2
11.0
327
5.5
655
92%
生产线总人力
15
生产线每小时产能 (pcs/h)
生产线平衡分析改善案例(PPT53张)

工位间和工位内的多余的WIP为零。
B值=1
一 物 流
物流
顺畅流动 没有停滞
物留
中间停滞 隐藏问题
“一个流”的益处
1. 内建品质管理; 2. 创造真正的灵活弹性; 3. 创造更高的生产力; 4. 腾出更多厂房空间; 5. 改善安全性; 6. 改善员工士气; 7. 降低存货成本。
生产线平衡定义
对生产的全部工序进行均衡,调整作业 负荷和工作方式,消除工序不平衡和工 时浪费,实现“一个流”。
入料
出料
平衡生产线的意义
通过平衡生产线可以综合应用到程序分析、动作分析 、layout分析,搬动分析、时间分析等全部IE手法,提 高全员综合素质 在平衡的生产线基础上实现单元生产,提高生产应变 能力,对应市场变化实现柔性生产系统 减少单件产品的工时消耗,降低成本(等同于提高人 均产量) 减少工序的在制品,真正实现“一个流” 提高作业及设备工装的工作效率
5、生产线平衡的计算
各工程净时间总计 生产线平衡率(%)= 时间最长工程*人员数 *100% 如上图表中,生产线平衡率= 1505 90*19 不平衡率(%)= 100% —平衡率(%) *100% = 88%
对生产线来说,不平衡率越小越好,一般控 制5%-13%之间,至少要控制在15%以下。
案例:工时测定和线平衡计算
降低线体速度,减少生产产量
减少人手(2) 工 作 時 間
因生产需求量降低而 可降低线体速度
将工序3﹑4的工作时 间分配至工序 1﹑2﹑5里﹐从而工 序3﹑4工作岗位的人 手可调配至其它生产 线去。
工序 1
生产车间线平衡分析表

平衡率
= #REF! 校 对:
目标达成率
=
#REF!
平衡率目标值
≧
85%
审 核:
分布示意图
T/T=18秒
工序合并后的时间(S)
2 8.0 6.0 4.0 2.0 0.0 工序
备注: T/T--->(单位产品所需要的时间)=1天的工作时间/生产数量 C/T--->单位个人以单位产品的量完成单位工序的循环时间
S01 S02 S03 S04 S05 S06 S07 S08 S09 S10 S11 S12 S13 S14 S15 S16
生产线平衡状态分析表
(版本:A/0 工序 编号
S01 S02 S03 S04 S05 S06 S07 S08 S09 S10 S11 S12 S13 S14 S15 S16
测试日期:2015.11.26 定子型号:ACSH-7030M12系列
线别:NO.D Line)
工序名称
#REF! #REF! #REF! #REF! #REF! #REF! #REF! #REF! #REF! #REF! #REF! #REF! #REF! #REF! #REF! #REF! 引出线加工
返修
1
TMAX N CT TOTAL Take Time(T/T) OPERATORS 制 作:
#REF! 14 #REF! 18.0 #REF!
Sec Pcs Sec Sec Unit
平衡率= (各工程的作业时间<CT TOTAL>的合计×100%)÷(全工程中最大作业时间 TMAX × 工序数 N) 目标达成率=(各工程的作业时间<CT TOTAL>的合计×100%)÷(单位产品所需要的时间 T/T × 工序数 N)
【案例】某机械加工厂的生产线平衡改善
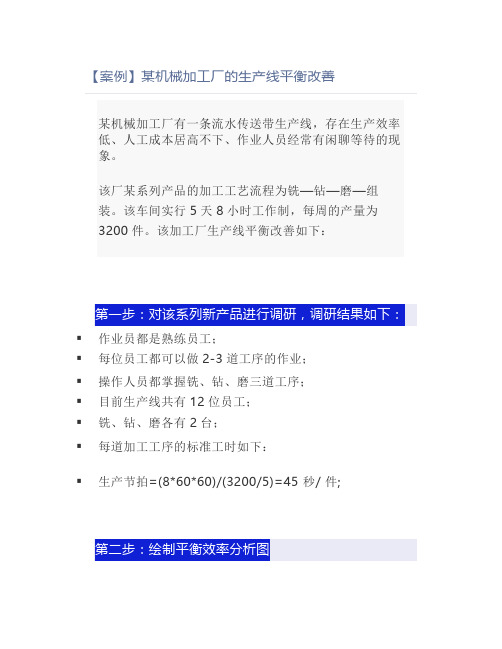
【案例】某机械加工厂的生产线平衡改善某机械加工厂有一条流水传送带生产线,存在生产效率低、人工成本居高不下、作业人员经常有闲聊等待的现象。
该厂某系列产品的加工工艺流程为铣—钻—磨—组装。
该车间实行5天8小时工作制,每周的产量为3200件。
该加工厂生产线平衡改善如下:▪作业员都是熟练员工;▪每位员工都可以做2-3道工序的作业;▪操作人员都掌握铣、钻、磨三道工序;▪目前生产线共有12位员工;▪铣、钻、磨各有2台;▪每道加工工序的标准工时如下:▪生产节拍=(8*60*60)/(3200/5)=45 秒/ 件;▪稼动损失率分析稼动损失率=(节拍时间-瓶颈时间)/节拍时间*100% =(45-40)/45*100% =11%▪平衡效率分析平衡效率=各工序标准工时总和/(瓶颈时间*人员总数)*100%=[(23+23+15+15+40+40+40+35+35+40+30+30)/(40*12)]*100%=76.3%▪生产效率分析生产效率=(合格品数量*该产品标准工时)/出勤时间= [3200*366/(12*8*3600*5)]*100%=67.8%▪由平衡率分析图及稼动损失率、平衡效率可知,要想提高生产效率、降低人工成本,可以先消除稼动损失率,然后利用ECRS法则改善平衡效率。
消除稼动损失率的核心手段是提高生产量,使生产节拍时间与瓶颈时间相同或接近,即每周产量由3200件提高至3600件。
提高后的生产节拍=实际出勤时间/实际生产数量=8*60*60/(3600/5)=40秒/件,这样可以直接减少人员等待时间,大大提高生产效率,改善后的生产效率为:生产效率=(3600*366) / (12*8*3600*5 )*100%=76.3%▼▼由于铣、钻的标准时间为23+23+15+15=76秒<2个生产节拍,因为作业员熟知操作铣、钻、磨工序,所以可以减少一台钻,由4人变为2人操作。
(改善后的分析图如上所示)改善后的平衡效率=(各工序标准时间总和/瓶颈时间*人员总数)*100%=366/(40*10)*100%=91.5%改善后的生产效率=3600*366/ (10*8*3600*5 )*100%=91.5%改善前后的生产线布局如下所示:▼由此可以看出,如果生产节拍 >瓶颈时间,首先要想尽办法使生产节拍时间与瓶颈时间相同或接近,否则就会造成人员的稼动损失,使生产节拍时间无限趋向瓶颈时间的主要思想有:o提高生产量;o缩短正常上班时间,把腾出的时间用来培训操作技能。
生产线平衡分析与改善最全面的IE分析生产线平衡
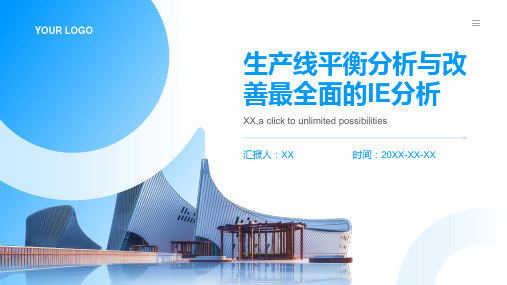
最全面的IE分 析生产线平衡 案例分析
PART 1
单击添加章节标题
P生A产R线T平2衡分析的概念和重要
性
生产线平衡分析的定义
定义:生产线平衡分析是指对生产线上的各个工 序进行平衡,使各工序的工作时间尽可能相近, 从而提高生产效率的过程。
目的:通过对生产线平衡进行分析,可以找出生 产过程中的瓶颈工序,优化生产流程,提高生产 效率,降低生产成本。
跨部门协作:加强各部门之间的沟通与协作,共同推进生产线平衡改善的实施和监控工作。
PIEA分R析T在5生产线平衡改善中的
Hale Waihona Puke 应用IE分析的基本概念和原则
IE分析的定义:工业工程分析, 旨在提高生产效率和降低生产成 本。
IE分析在生产线平衡改善中的应 用:通过分析生产线上的瓶颈、 浪费和不合理之处,提出改善方 案。
注意事项3:考虑人机配合 和作业节拍
注意事项1:分析前要明确 目标和范围
注意事项4:注意设备维护 和保养
PART 4
生产线平衡改善的策略和措施
生产线平衡改善的目标和原则
提高生产效率:通过优化生产线布局和作业分配,降低生产成本,提高产出效率。 降低不良品率:通过平衡生产线上的作业,减少生产过程中的波动和异常,降低不良品率。 提高员工满意度:通过合理分配工作量和减轻员工负担,提高员工的工作积极性和满意度。
生产线平衡分析的工具和技术
作业分析:确定每个作业步骤的时间和顺序,识别瓶颈和浪费。 工艺流程图:可视化生产线流程,找出潜在的改进点。 动作分析:研究工人操作,优化动作,提高效率。 生产计划与调度:合理安排生产计划,确保生产线的平衡。
生产线平衡分析的注意事项
注意事项2:充分了解生产 流程和工艺要求
生产线平衡分析和瓶颈改善表模板

合计 组作业人數 统计工時 標準工時 11 54.5 57.2
54.5
说明:流水线线速:18,实际产能会在平衡率产能上下浮动10%左右
寬放係數
平衡率 小时产能
5%
不平衡率 508
26.6%
不良率
0% 46.2
單人單時產出
1.4月25日,皮-2组11人(其中600个产品未上弹簧),每小时产量=5000/11.5=435个;人均小时产量=435/11=40个. 2.现有标准产能45个/小时,达成率=40/45=88.9%.
1.3 0.9 1.1 1.5 1.0 0.7 0.7 1.0 2.7
1 1 1 2 1 1 1 1 2 11
-0.3 0.1 -0.1 0.5 -0.0 0.3 0.3 -0.0 -0.7
6.5 4.5 5.5 3.8 5.0 3.5 3.5 5.0 6.8 平衡率
空闲时装塔簧 瓶颈工序 73.4%
XX安装车间-皮2组 工作說明
产品名称
制作时间
XX 備 註 次瓶颈工序
工具设备 測試工時 平均時間 需求人力 標準配置 人力差異 平均工時
尖锥 无 无 无 无 无 无 无 手啤机
6.5 4.5 5.5 7.5 5.0 3.5 3.5 5.0 13.5
5.0 5.0 5.0 5.0 5.0 5.0 5.0 5.0 5.0
XX开关-11人生产线平衡图[改善前]
8
7 6.5 6 5.5 5 4.5 4 3.8 5.0 5.0
6.8
3.5
3.5
3
2
1
0
底座装静触片 装扣板和扣簧 装联锁片*2 装长动触片*2 装长动触片*1 装卡板*2 装卡板+零档卡板 装盖板 分塔簧+装塔簧+压 塔簧
- 1、下载文档前请自行甄别文档内容的完整性,平台不提供额外的编辑、内容补充、找答案等附加服务。
- 2、"仅部分预览"的文档,不可在线预览部分如存在完整性等问题,可反馈申请退款(可完整预览的文档不适用该条件!)。
- 3、如文档侵犯您的权益,请联系客服反馈,我们会尽快为您处理(人工客服工作时间:9:00-18:30)。
240 1
240 360
266.7
300
8
打拼孔
9
攻牙
540 1 60 1
540
60
60 540
266.7
266.7
200
10
去毛刺
120 1
120 480
266.7
100
合
3200 12 2000 4000 44.4% 55.6% 60
5
MAX
600 4000 44.4% 55.6%
0
工序
备注
秒7(0S0)
1
下料
120 1
120 480
266.7
2
粗车1
50 1
50 550
266.7
600
改善后生产线工序(节拍)平衡图
3
粗车2
4
精车1
130 1 60 1
130 470 60 540
266.7 266.7
500
5
精车2
6
开窗
80 1
80 520
1800 3 600
0
266.7
400
266.7
1
2
3
4
5
6
7
8
9
10
说
明
1.
不
平
衡
损
生产率
失
平衡率
=(
=所有
最
工序标
高 的 节
准时间 之和÷ (瓶颈
平衡损失率=1平衡率
拍
站节拍
时
时间×
间
工作站
×
总数)
合
计
人
数)
60 1740
320.0 320.0 320.0
1400 1200
5
精车2
80 1
80 1720
320.0
1000
6
开窗
7
磨外圆
8
打拼孔
1800 1 1800
0
240 1
240 1560
540 1
540 1260
320.0
800
320.0 320.0
600
9
攻牙
60 1
60 1740
320.0
400
生产线平衡改善
现
状
秒20(S0)0
工 序
工序名称
作业时 间(S)
人数
人均时 (S)
不平衡 损失
生产线 平衡率
平衡损 产量 失率 (PCS)
人均
备注
1800
原生产线工序(节拍)平衡图
1
下料
120 1
120 1680
320.0
1600
2
粗车1
3
粗车2
4
精车1
50 1 130 1
60 1
50 1750 130 1670
10
去毛刺
120 1
120 1680
320.0
200
合
3200 10
14800 17.8% 82.2% 20
2
0
MAX
1800 14800 17.8% 82.2%
工序
1
2
3
4
5
6
7
8
9
10
改
善
后
工 序
工序名称
作业时 间(S)
人数
人均时 (S)
不平衡 损失
生产线 平衡率
平衡损 产量 失率 (PCS)
人均