钢制弯管
冷弯管制作标准
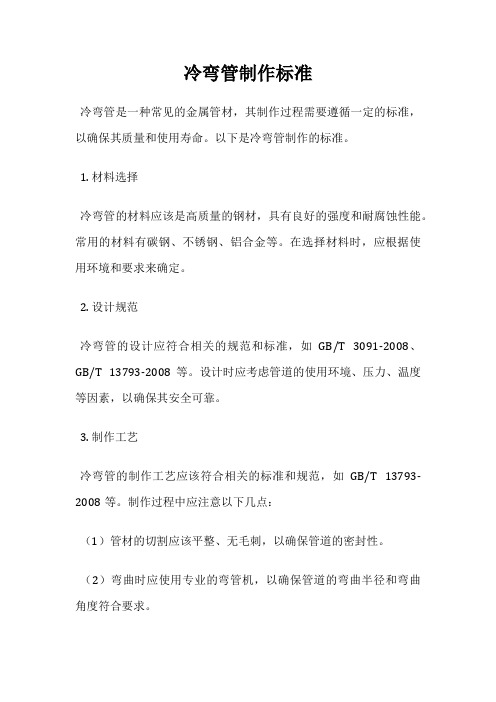
冷弯管制作标准
冷弯管是一种常见的金属管材,其制作过程需要遵循一定的标准,以确保其质量和使用寿命。
以下是冷弯管制作的标准。
1. 材料选择
冷弯管的材料应该是高质量的钢材,具有良好的强度和耐腐蚀性能。
常用的材料有碳钢、不锈钢、铝合金等。
在选择材料时,应根据使用环境和要求来确定。
2. 设计规范
冷弯管的设计应符合相关的规范和标准,如GB/T 3091-2008、GB/T 13793-2008等。
设计时应考虑管道的使用环境、压力、温度等因素,以确保其安全可靠。
3. 制作工艺
冷弯管的制作工艺应该符合相关的标准和规范,如GB/T 13793-2008等。
制作过程中应注意以下几点:
(1)管材的切割应该平整、无毛刺,以确保管道的密封性。
(2)弯曲时应使用专业的弯管机,以确保管道的弯曲半径和弯曲角度符合要求。
(3)焊接时应使用合适的焊接方法和材料,以确保焊缝的质量和强度。
(4)表面处理应符合相关的标准和规范,如GB/T 8923-1988等。
4. 检测标准
冷弯管制作完成后,应进行相关的检测,以确保其质量和使用寿命。
常用的检测方法有压力试验、水压试验、X射线检测等。
检测结果应符合相关的标准和规范,如GB/T 3091-2008、GB/T 13793-2008等。
冷弯管制作需要遵循一定的标准和规范,以确保其质量和使用寿命。
在制作过程中,应注意材料选择、设计规范、制作工艺和检测标准等方面,以确保制作出符合要求的冷弯管。
油气钢制管道冷弯管制作工艺研究

ASME B16.49-2000_用于输送和分配的管道系统中的工厂制造的钢制感应弯管(中文版)

4
ASME B16.49-2000
筒状材料(cylinder):由制造商(或者转包)通过卷板和焊接所生产出的管子,该方法不同于公认 的管子生产规范。
1 bend dimensional terms 弯管尺寸术语 2 test specimen locations and orientations 试样位置和方向 3 measurement of bend angle and out-of-squareness 弯管角度和垂直度的测量 Tables 表 1 maximum limits of chemical elements that may be used 许用的化学元素的最大极限 2 compliance factor, F, carbon equivalent formula , 符合系数,F, 碳当量公式 3 tensile properties 拉伸性能 Mandatory annex 强制性附录 1 references 参考文献 Nonmandatory annex 非强制性附录 A quality system program 质量体系程序
本标准中参考采用的标准和规范显示在强制附录Ⅰ中。在单个参考文献中表明每一标准和规范的具 体版本号是不现实的,但是附录Ⅰ中给出了具体的版本号。依据更高版本号的参考标准制造的产品并且 所有其它条件符合本标准的要求,将认为是符合本标准的要求。 1.6 规范和惯例
凡在引用标准规范或政府规程监察范围下使用的弯管,均受这些规范和规程的一切限制。这包括任 一最高温度极限或控制材料在低温下使用的规则。 1.7 使用条件
弯管公差标准

弯管公差标准
弯管公差标准是指在弯管加工过程中,允许管材尺寸和形状偏离设计要求的一定范围。
这些公差标准旨在确保弯管在满足使用要求的前提下,具有较高的尺寸稳定性和质量。
弯管公差标准主要包括以下几个方面。
1.弯曲半径公差:弯管的弯曲半径应符合设计要求。
在一般情况下,弯曲半径的公差应控制在±10%以内。
2.弯曲角度公差:弯管的弯曲角度允许偏差一般不大于±2°。
3.管径公差:管径的公差应符合国家标准GB/T15918-1994《钢制无缝钢管》的要求。
在一般情况下,管径的公差等级分为±0.5mm、±1mm、±1.5mm等。
4.壁厚公差:弯管的壁厚公差应符合国家标准GB/T13295-2013《焊接钢管》的要求。
壁厚公差等级分为±0.5mm、±1mm、±1.5mm等。
5.弯管长度公差:弯管的长度公差应根据客户要求和相关标准来确定。
一般情况下,长度公差为±10mm。
6.表面质量公差:弯管表面应光滑,无毛刺、裂纹、折叠等缺陷。
表面质量公差应符合相关标准的要求。
需要注意的是,以上公差标准仅作为一般参考。
实际生产中,弯管的公差要求会根据具体应用场景、客户要求以及
相关标准进行调整。
在实际操作中,应根据具体情况合理控制弯管的公差范围,以确保产品质量。
常用的弯管参数

常用的弯管参数常用的弯管参数是指在工业生产中常用的弯管的尺寸、材质和角度等参数。
弯管是一种常见的管道连接件,用于改变管道的流向和走向,广泛应用于石油、化工、冶金、电力、航空航天等领域。
1. 弯管尺寸:弯管的尺寸一般由其直径和壁厚决定,常见的弯管直径有1/2英寸、3/4英寸、1英寸等,壁厚通常为标准壁厚或加厚型。
弯管的尺寸与管道的尺寸相对应,需根据具体管道系统的设计要求进行选取。
2. 弯管材质:弯管的材质选择与管道系统的介质、压力和温度等因素有关。
常见的弯管材质有碳钢、不锈钢、合金钢、铸铁、黄铜等。
不同材质的弯管具有不同的耐腐蚀性、耐高温性和机械强度,应根据具体要求进行选择。
3. 弯管角度:弯管的角度是指弯管与管道轴线之间的夹角,常见的弯管角度有90度、45度、30度等。
不同角度的弯管适用于不同的管道走向和流体流动要求,根据具体的工程要求选择合适的角度。
4. 弯管半径:弯管的半径是指弯管曲线的半径,也称为弯曲半径或弯管曲率半径。
常见的弯管半径有1倍管径、1.5倍管径、2倍管径等。
弯管的半径决定了管道的曲率和流体的流动性能,应根据具体工程要求和流体特性进行选择。
5. 弯管厚度:弯管的厚度是指弯管壁的厚度,直接影响弯管的强度和耐压性能。
弯管的厚度应满足管道系统的工作压力和温度要求,一般应符合相关标准和规范的规定。
6. 弯管制造工艺:弯管的制造工艺主要有冷弯和热弯两种。
冷弯是指在室温下通过专用的弯管机械对管材进行弯曲成型,适用于制造小口径和壁厚较薄的弯管。
热弯是指在高温条件下将管材加热至一定温度后进行弯管,适用于制造大口径和壁厚较厚的弯管。
7. 弯管连接方式:弯管的连接方式与管道系统的设计和使用要求有关。
常见的弯管连接方式有焊接、螺纹连接、法兰连接等。
不同的连接方式具有不同的连接强度和密封性能,应根据具体情况选择合适的连接方式。
8. 弯管表面处理:弯管的表面处理一般包括酸洗、喷砂、喷漆等工艺,主要用于提高弯管的耐腐蚀性和外观质量。
弯管技术规范

弯管技术规范1) 根据管道材质和管径的不同,弯管制作有冷弯和热弯之分。
2) 弯管宜采用壁厚为正公差的管道制作。
3) 有缝钢管制作弯管时,焊缝应避开受拉(压)区。
4) 弯制钢管,弯曲半径应符合下列规定:热弯:应不小于管道外径的3.5倍;冷弯:应不小于管道外径的4倍;焊接弯头:应不小于管道外径的1.5倍;冲压弯头:应不小于管道外径。
5) 钢管应在其材料特性允许范围内冷弯或热弯。
6) 加热制作弯管时,铜管加热温度范围为500~600℃;铜合金管加热温度范围为600~700℃。
7) 弯管质量应符合下列规定:a 不得有裂纹(目测或依据设计文件规定);b 不得存在过烧、分层等缺陷;c 不宜有皱纹;d 测量弯管任一截面上的最大外径与最小外径差,应符合表4.2.3.2-3规定;e 各类金属管道的弯管,管端中心偏差值△不得超过3mm/m,当直管长度L大于3m时,其偏差不得超过10mm。
8) П形弯管的平面度允许偏差△应符合表4.2.3.2-4规定。
9) 钢塑复合管管径不大于50mm时可用弯管机冷弯,但其弯曲半径不得小于8倍管表4.2.3.2-3 弯管最大外径与最小外径之差表4.2.3.2-4 П形弯管的平面度允许偏差△(mm)径,弯曲角度不得大于10°。
10) 管道转弯处宜采用管件连接。
DN≤32的管材,当采用直管材折曲转弯时,其弯曲半径不应小于12 DN,且在弯曲时应套有相应口径的弹簧管。
管道弯曲部位不得有凹陷和起皱现象。
11) 铝塑复合管直接弯曲时,公称外径De不大于25mm的管道可采用在管内放置专用弹簧弯曲;公称外径De为32mm的管道宜采用专用弯管器弯管。
12) 铜管弯管:铜及铜合金管煨弯时尽量不用热煨,因热煨后管内填充物(如河砂、松香等)不宜清除。
一般管径在l00mm以下者采用弯管机冷弯;管径在100mm以上者采用压制弯头或焊接弯头。
铜弯管的直边长度不应小于管径,且不少于30mm。
a 热煨弯(一般用于黄铜管)a) 先将管内充人无杂质的干细沙,并用木锤敲实,然后用木塞堵住两端口,再在管壁上画出加热长度的记号,应使弯管的直边长度不小于其管径,且不小于30mm。
不锈钢管弯管器使用方法及操作流程

1.90°弯曲:
按照离目标点(管端、弯曲点等)所需的距离(X)在管件上进行标记。该距离即是弯角中心位置到目标点的距离。
将管道放置于弯管器中。
如果目标点在记号的左侧,则将管件上的标记对准挂钩上的“L”线。
在对齐管件上的标记后,移动挂钩,让“0”线对准刻度盘上的45度线。
四.回弹
所有材质的管道在完成弯管作业后均会产生一定的回弹量。较软材质管道(比如铜管)比较硬材质管道(比如不锈钢管)的回弹量较少。因此根据经验,建议在弯管时留取一定的管道回弹补偿,通常在1°~3°左右,具体可视管道材质及硬度而定。
五.600系列弯管器型号规格表
如果目标点在记号的右侧,则将管件上的标记对准挂钩上的“R”线。
在对齐管件上的标记后,移动挂钩,让“0”线对准成型盘上的90度线。
2.45°弯曲:
按照离目标点(管端、弯曲点等)所需的距离(X)在管件上进行标记。该距离即是弧段中心位置到目标点的距离。
将管道放置于弯管器中。
将管道上的标记对准滑块上的45°线
简介:
不锈钢钢管弯管通常使用到的工具是RIDGID600系列重负荷弯管器,以下为操作步骤和使用方法。
组成部件
一.常规弯管操作
1.握住弯管器成型手柄或将弯管器固定在台钳上。
2.松开挂钩,抬起滑块手柄。
3.将管道放置在成型盘槽中并用挂钩将其固定在成型盘中。
4.放下滑块手柄直至挂钩上的“0”刻度线对准成型盘上的0°位置。
5.绕着成型盘旋转滑块手柄直至滑块上的“0”刻度线对准成型盘上所需的度数。
二.90°到180°弯曲
钢管弯制通用工艺003

钢结构作业文件文件编号:WYZG-003版本号/修改次数:钢管弯制通用工艺受控状态:受控本发放序号:发布日期: 实施日期:目录1. 主体内容与适用范围 (3)2.编制依据 (3)3.钢管弯曲的一般要求 (3)4. 热煨弯工艺过程 (4)1. 主体内容与适用范围1.1 主体内容:钢管热煨弯的一般要求。
1.2 适用范围:适用于建筑钢结构钢管的弯曲制作。
2.编制依据《钢结构工程施工质量验收规程》 GB50205-2001《建筑钢结构施工手册》中国计划出版社3.钢管弯曲的一般要求(1) 钢管原材料进厂检验依据《结构用无缝钢管》GB/T8162和《直缝电焊钢管》GB/T13793。
此标准请参见《钢管桁架通用工艺》原材进厂检验部分。
(2) 钢管弯曲方法分为热煨弯和冷弯两种。
我公司通常采用热煨弯工艺,如果热煨弯工艺不能满足工程质量的要求,应考虑外协冷弯。
(3) 冷弯是在常温下进行弯制加工,加工外观质量较好。
(4) 热煨弯是将钢材加热至900-1000℃之间,使钢材在减小强度、增加塑性的基础上再到模具上进行弯制加工,本法适用于较厚板壁的钢管〔厚度大于6mm〕的弯制。
热弯管的制作难点在于:烤火温度不易控制,容易出现温度不够或过烧现象。
易出现旁弯和端头椭圆压扁。
(5) 弯曲过程是在材料弹性变形后再到达塑性变形的过程,拉伸和压缩使材料内部产生应力,从而引起材料的一定的弹性变形,一旦外力作用〔或同时降温〕消失,材料会产生一定的回弹,回弹量一般为0.04-0.06R(R为半径)。
影响回弹的因素主要有:* 材料的机械性能:屈服强度越大,回弹越大;* 变形程度:弯曲半径R和材料厚度T的比值越大,回弹越大;* 变形区域越大,回弹越大;* 材质为Q235的回弹量为0.05R,材质为Q345的回弹量为0.06R。
(6) 开始弯曲时首先选择较小的回弹量(比方:),煨制好第一根后,根据测量出的煨弯成型情况,重新确定较理想的回弹量。
(7) 圆管弯曲的圆角半径不宜过大,也不宜过小。
- 1、下载文档前请自行甄别文档内容的完整性,平台不提供额外的编辑、内容补充、找答案等附加服务。
- 2、"仅部分预览"的文档,不可在线预览部分如存在完整性等问题,可反馈申请退款(可完整预览的文档不适用该条件!)。
- 3、如文档侵犯您的权益,请联系客服反馈,我们会尽快为您处理(人工客服工作时间:9:00-18:30)。
钢制弯管.txt喜欢我这是革命需要,知道不?!你不会叠衣服一边呆着去!以后我来叠!我一定要给你幸福,谁也别想拦着。
主题内容与适用范围本标准规定了直径为Φ219~Φ1020mm ,壁厚为6~20mm的各种规格的钢制弯管(以下简称弯管)的型号、基本参数、技术要求、检验方法、检验规则和标志、贮存、包装等内容。
本标准适用于无缝、直缝、螺旋焊缝钢管热弯弯管。
2 引用标准GB 699 优质碳素结构钢技术条件GB 3087 低中压锅炉用无缝钢管GB 5310 高压锅炉用无缝钢管GB 9948 石油裂化用无缝钢管GB 2270 不锈钢无缝钢管GB 8163 输送流体用无缝钢管YB 234 直缝钢管SY 5036 承压流体输送用螺旋缝埋弧焊钢管GB 9711 石油天然气输送管道用螺旋缝埋弧焊钢管GBJ 235 工业管道工程施工及验收规范(金属管道篇)GB 1611 锅炉管子制造技术条件GB 6479 化肥设备用高压无缝钢管GB 231 金属布氏硬度试验法GB 150 钢制压力容器GB 2828 逐批检查计数抽样程序及抽样表GB 2829 周期检查计数抽样程序及抽样表3 符号p—中心距;R—曲率半径;β—空间角度;D—Q外径;t—壁厚;Dn—公称直径;h—起皱高度;Δα—平面度;d—弯曲角度;L—中间直管;Q—管端面垂直度;U—管端面平面度;f—波浪间距。
—4 型与号与基本参数4.1 型号弯管的型号用下面方法表示(略)示例:材质为20号钢,弯曲角度为90°,管子外径为Φ219mm,壁厚为8mm,曲率半径为4D的弯管可表示为90°Φ219×8-4D-204.2 基本参数弯管基本参数(见图1)(略)应符合表1(略)的规定。
5 技术要求5.1 弯管应符合本标准要求,并按经规定程序批准的图样及技术条件制造。
5.2 管材5.2.1 管材的质量应符合以下有关标准:a) 优质碳素结构钢应符合GB 699的有关规定;b) 低中压锅炉用无缝钢管应符合GB 3087的有关规定;c) 高压锅炉用无缝钢管应符合GB 5310的有关规定;d) 石油裂化用无缝钢管应符合GB 9948的有关规定;e) 不锈钢无缝钢管应符合GB 2270的有关规定;f) 无缝钢管应符合GB 8163的有关规定;g) 直缝钢管应符合YB 234的有关规定;h) 承压流体输送用螺旋缝埋弧焊钢管应符合SY 5036的有关规定;i) 石油天然气输送管道用螺旋缝埋弧焊钢管应符合GB 9711的有关规定;j) 化肥设备用高压无缝钢管应符合GB 6479的规定。
5.2.2 管材进厂应有制造厂质量证明书,同时由检验部门对规格、型号、外观和技术资料等进行检查验收。
5.2.3 管格实物的标记、炉批号与材质证明书相符合可不进行复检,管材无标记\无材质书或材质证明书不全时必须进行复检。
5.3 弯管表面应光滑,如有结疤、划痕、裂纹、重皮等缺陷时应进行修磨。
修磨处应圆滑过渡,并进行问着色或磁粉探伤、修磨后弯管的实际壁厚不能小于管材名义壁厚减去弯制减薄量与管材壁厚负偏差之和。
5.4 弯管不得有过烧存在。
5.5 高压弯管在弯制后应进行着色或磁粉探伤。
5.6 壁厚减薄率应不大于表2的规定:减薄率= t-t′×100%t式中:t′—弯管横断面上最薄处壁厚,mmt —管子实际壁厚的最小值,mm表2 %R/D 3 4 5 6 7 8 9 10减薄率 14.0 11.0 9.0 8.0 7.0 6.0 5.5 5.25.7 弯管圆度(见图2,略)应不大于表3(略)的规定。
中国水暖网圆度=Dmax—Dmin×100%D式中:Dmax—弯管横断面上的最大外径,mmDmin—弯管横断面上的最小外径,mm5.8 弯管弯曲角度和空间夹角的偏差应符合下列规定:a) 同一平面上弯管的弯曲角度偏差应超过±0.5°;b) 不在同一平面上二弯管夹角偏差:当夹角为90°(见图3,略)时,偏差应不超过±1°;夹角不是90°(见图4,略)时,偏差应不超过±1.5°。
5.9 曲率半径、中心距的极限偏差(见图5、图6,略)应符合表4(略)的规定。
5.10 弯管的平面度(见图7,略)应符合表5(略)的规定。
5.11 弯管的中间直管尺寸偏差(见图8,略)应符合表6(略)的规定。
5.12 弯管起皱高度和波浪间距(见图9,略)应符合表7(略)的规定。
5.13 弯管坡口(见图10,略)应符合以下要求:a) 当管子壁厚t<9 mm时,坡口角度为35°±2.5°,坡口钝边为1.6±0.8mm;b) 当管子壁厚9<t<20时,坡口角度为30°±2.5°,坡口钝边为1.6±0.8mm。
5.14 弯管管端面垂直度(见图11,略)应符合表8(略)的规定.5.15 弯管管端平面度(见图12,略)应不大于1 mm。
5.16 低碳钢、不锈钢管弯制后不进行热处理,不作硬度检查。
5.17 低合金钢、合金钢管弯制后,应进行热处理,并从每一批同时进行热处进的弯管中任意取出一个测定硬度。
热处理条件按GBJ 235标准中3.2.5条的规定执行。
硬度要求按GBJ 235标准中附表1.1的规定执行。
5.18 弯制直缝钢管时应将管子焊缝放在弯里弧45°位置。
5.19 按本标准制造并检验合格的弯一般不进行水压试验.在管线系统试压时,应能承受所规定的试验压力。
5.20 弯管的弯曲半径不是管子外径的整倍数时,圆度和减薄率应采用插入法计算。
6 检验方法6.1 硬度试验按GB 231的规定进行。
6.2 渗透探伤按GB 150的规定进行。
6.3 壁厚减薄率的检测6.3.1 检测需用量具:测厚仪6.3.2 检测方法将弯制完的管子外弧中心的表面清除干净,然后涂上机油,再用测厚仪进行测量,弯曲角度小于或等于90°时至少要均匀测量三点;弯曲角度大于90°小于或等于180°时,至少要测量五点。
6.4 弯曲部分圆度的检测6.4.1 检测需用量具500 mm卡尺或1100 mm卡尺6.4.2 检测方法在始端、中间、终端测量三处,测量时沿弯管水平方向和垂直方向测量,将同一截面上的垂直和水平方向所测得的数值按5.7条计算。
6.5 弯曲角度的检测6.5.1 检测需用量具角度尺、平台、2000 mm钢板尺、直角尺。
6.5.2 同一平面上弯曲角度的检测方法将弯管放在平台上,然后用直角尺在弯管两端的直管段分别找出N点(N>6)投影到平台上(图13,略),将弯管从平台上拿直,按照这些点找出两端直管段的中心线,交于A点,再用角度尺测量出弯曲角度。
6.5.3 不在同一平面上二弯管空间夹角的检测方法:先将二弯管组成的两个面中的任意一个紧贴于水平面,然后在空间的弯管直管段上用倾斜测定水准仪读出两相交平面的二面角,即为二弯管的空间夹角。
6.6 曲率半径极限偏差的检测6.6.1 检测需用量具15000mm钢卷尺、直角尺、2000mm钢板尺、平台6.6.2 用划规在平台上按所要求的弯曲半径减去管子外径的二分之一尺寸划弧,所划弧的角度要大于弯管本身的弯曲角度,然后将弯管放在平台上,使弯曲开始点、终止点的投影与所划弧线相重合,再用直角尺和钢板尺测量出△R,测量△R时要去掉弯管圆度(图14 略)的影响。
6.7 弯管中心距的检测6.7.1 检测需用量具15000mm钢卷尺、直角尺、平台6.7.2 检测方法将弯管放在平台上,分别将两面三刀个直角尽放在弯制起点和终点的直管段内侧和外侧,用15000mm钢卷尺测量出p1,然后再将内侧直角尺放在外侧,将外侧直角尺放在内侧,测量出p1,取两次测量数值的平均值p。
6.8 弯管平面度的检测6.8.1检测需用量具平台、塞尺或标准塞块。
6.8.2检测方法将弯管放在平台上,呈自然状态,用塞尺或塞块测Δα值,再将弯管翻转180°测出另一端的Δα。
6.9 起皱高度和波浪间距的检测6.9.1 检测需用量具15000mm钢板尺、1100mm卡尺或500mm卡尺6.9.2 检测方法6.9.2.1 起皱高度用1000mm卡尺测出波峰和波谷的尺寸(图16,略),然后将用相邻的波峰和波谷尺寸进行比较,找出相邻的差值最大的一对即为起皱高度(h= hmax—hmin)。
6.9.2.2 波浪间距将钢板尺水平放在两个相邻的波峰上,钢板尺和两个波峰相接触,接触点之间的距离即为波浪间距(图16,略)。
6.10 端面垂直度的检测6.10.1 检测需用量具直角尺、焊口检测器6.10.2 检测方法将直角尺放在直管端面,使其一端和直管段部分紧巾,再用焊口检测骂测出不接触部分“Q”值(图17,略)。
6.11 弯管管端面平面度的检测6.11.1 检测需用量具平台、塞尺。
6.11.2 检测方法将弯管管端紧靠在平台上,用塞尺检测平面度“t”值6.12 其它的尺寸检验按常规检验方法进行7 检验规则7.1 弯管检验分出厂检验和型式检验7.2 出厂检验7.2.1 弯管应经检验部门检验合格,并附有合格证、材质证明书和必要的试验报告方可出厂。
7.2.2 弯管出厂检验项目及各项质量指标的不合格分类见表9(略)。
7.2.3 抽样方案弯管出厂按GB2828G一次正常检查抽样方案(见表10,略)7.2.4 判定原则7.2.4.1 对样本检查后,若不合格数小于或等于合格判定数A,则属此批产品合格;若不合格数大于或等于不合格判定数RC,则判此批产品不合格。
7.2.4.2 一等品判定规则按表10(略)的规定。
7.3 型式检验7.3.1 弯管在遇到下列情况之一时,应进行型工检验。
A、正常生产时,每两年进行一次;B、停产一年后,恢复生产时;C、上级质量监督机构提出进行型式检验要求时。
7.3.2 型式检验项目全部按表9(略)进行。
7.3.3 抽样方案弯管型式检验按GB 2829 一次抽样方案随机抽取三种规格(见表11,略)。
7.3.4 型式检验提供的交检批规格不少于3种,每种规格不少于3件。
7.3.5 判定原则7.3.5.1若不合格数小于或等于合格判定数A,则判该批产品是合格的;若不合格数大于或等于RC,则判此批产品产不合格的。
7.3.5.2 一等品判定规则按表11(略)的规定。
8 标志、贮存、包装8.1 标志8.1.1 每个弯管在距管端100mm处用钢印或喷漆作出以下标志:a、生产批号;b、制造厂名称;c、型号;d、商标8.1.2 用钢印打标记时,其深度不应超过0.2mm。
8.2 贮存成品弯管除锈后,刷防锈漆放成品库贮存。
8.3 包装8.3.1 弯端坡口应用管箍或管帽保护。