电镀镍工艺
电镀镍工艺

1、作用与特性PCB(就是英文PrintedCircuieBoard印制线路板得简称)上用镀镍来作为贵金属与贱金属得衬底镀层,对某些单面印制板,也常用作面层。
对于重负荷磨损得一些表面,如开关触点、触片或插头金,用镍来作为金得衬底镀层,可大大提高耐磨性、当用来作为阻挡层时,镍能有效地防止铜与其它金属之间得扩散。
哑镍/金组合镀层常常用来作为抗蚀刻得金属镀层,而且能适应热压焊与钎焊得要求,唯读只有镍能够作为含氨类蚀刻剂得抗蚀镀层,而不需热压焊又要求镀层光亮得PCB,通常采用光镍/金镀层。
镍镀层厚度一般不低于2。
5微米,通常采用4—5微米。
PCB低应力镍得淀积层,通常就是用改性型得瓦特镍镀液与具有降低应力作用得添加剂得一些氨基磺酸镍镀液来镀制。
我们常说得PCB镀镍有光镍与哑镍(也称低应力镍或半光亮镍),通常要求镀层均匀细致,孔隙率低,应力低,延展性好得特点。
2、氨基磺酸镍(氨镍)氨基磺酸镍广泛用来作为金属化孔电镀与印制插头接触片上得衬底镀层。
所获得得淀积层得内应力低、硬度高,且具有极为优越得延展性、将一种去应力剂加入镀液中,所得到得镀层将稍有一点应力。
有多种不同配方得氨基磺酸盐镀液,典型得氨基磺酸镍镀液配方如下表。
由于镀层得应力低,所以获得广泛得应用,但氨基磺酸镍稳定性差,其成本相对高。
3、改性得瓦特镍(硫镍)改性瓦特镍配方,采用硫酸镍,连同加入溴化镍或氯化镍。
由于内应力得原因,所以大都选用溴化镍。
它可以生产出一个半光亮得、稍有一点内应力、延展性好得镀层;并且这种镀层为随后得电镀很容易活化,成本相对底、4、镀液各组分得作用:主盐──氨基磺酸镍与硫酸镍为镍液中得主盐,镍盐主要就是提供镀镍所需得镍金属离子并兼起着导电盐得作用。
镀镍液得浓度随供应厂商不同而稍有不同,镍盐允许含量得变化较大。
镍盐含量高,可以使用较高得阴极电流密度,沉积速度快,常用作高速镀厚镍。
但就是浓度过高将降低阴极极化,分散能力差,而且镀液得带出损失大。
电镀镍工艺技术
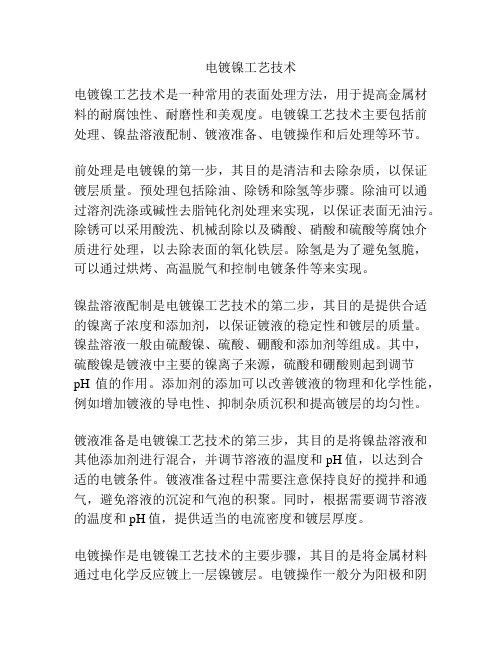
电镀镍工艺技术电镀镍工艺技术是一种常用的表面处理方法,用于提高金属材料的耐腐蚀性、耐磨性和美观度。
电镀镍工艺技术主要包括前处理、镍盐溶液配制、镀液准备、电镀操作和后处理等环节。
前处理是电镀镍的第一步,其目的是清洁和去除杂质,以保证镀层质量。
预处理包括除油、除锈和除氢等步骤。
除油可以通过溶剂洗涤或碱性去脂钝化剂处理来实现,以保证表面无油污。
除锈可以采用酸洗、机械刮除以及磷酸、硝酸和硫酸等腐蚀介质进行处理,以去除表面的氧化铁层。
除氢是为了避免氢脆,可以通过烘烤、高温脱气和控制电镀条件等来实现。
镍盐溶液配制是电镀镍工艺技术的第二步,其目的是提供合适的镍离子浓度和添加剂,以保证镀液的稳定性和镀层的质量。
镍盐溶液一般由硫酸镍、硫酸、硼酸和添加剂等组成。
其中,硫酸镍是镀液中主要的镍离子来源,硫酸和硼酸则起到调节pH值的作用。
添加剂的添加可以改善镀液的物理和化学性能,例如增加镀液的导电性、抑制杂质沉积和提高镀层的均匀性。
镀液准备是电镀镍工艺技术的第三步,其目的是将镍盐溶液和其他添加剂进行混合,并调节溶液的温度和pH值,以达到合适的电镀条件。
镀液准备过程中需要注意保持良好的搅拌和通气,避免溶液的沉淀和气泡的积聚。
同时,根据需要调节溶液的温度和pH值,提供适当的电流密度和镀层厚度。
电镀操作是电镀镍工艺技术的主要步骤,其目的是将金属材料通过电化学反应镀上一层镍镀层。
电镀操作一般分为阳极和阴极两个电极。
阳极为金属材料,阴极为镀液中的镍离子。
当施加合适的电压和电流密度后,镍离子会在金属材料的表面还原成镍金属,形成均匀的镀层。
电镀操作要求镀液中的溶解氧和杂质离子足够低,并控制镀液的温度和pH值。
后处理是电镀镍工艺技术的最后一步,其目的是除去镀液残留和提高镀层的性能。
后处理包括冲洗、烘烤和抛光等步骤。
冲洗可以去除镀液残留和残渣,烘烤可以提高镀层的结晶状态和硬度。
抛光则可以改善镀层的光泽度和平整度。
在后处理过程中需要注意严格遵守相关安全操作规程和环保要求,以确保操作的安全性和环保性。
电镀镍工艺流程

电镀镍工艺流程电镀镍是一种将镍沉积在金属表面上的技术,不仅能增加金属件的耐腐蚀性能,还可以提高其机械性能和外观。
下面是一个常用的电镀镍工艺流程。
首先,准备工作。
将需要电镀的金属件收集起来,并进行清洗。
清洗可以使用溶剂、碱性洗涤剂和酸性溶液,以去除金属表面的油污和其他杂质。
清洗后,用水冲洗干净,确保金属表面干净无尘。
接下来是抛光工艺。
将金属件放入抛光机中,使用抛光剂进行抛光。
抛光的目的是去除金属表面的氧化物和疏松层,使得金属表面更加光滑。
抛光时间和抛光剂的选择都需要根据具体的材料和要求来确定。
抛光完成后,可以进行电解洗净。
将金属件放入电解槽中,用碱性洗涤剂进行电解洗净。
电解洗净的目的是去除抛光过程中沾在金属表面的抛光剂和残留物质,使得金属表面干净无杂质。
洗净完毕后,进行活化处理。
将金属件放入酸性溶液中进行活化处理,活化剂可以是硫酸、酚醛树脂或其他物质。
活化处理的目的是增加金属表面的反应性,为后续的电镀提供更好的条件。
活化处理完成后,可以进行电镀。
将金属件放入电镀槽中,电流通过电解液使得镍离子在金属表面沉积形成镍层。
电镀液中通常含有镍盐、酸性溶液以及其他添加剂来调节电镀速度和镀层的均匀性。
电镀时间和电流密度都需要根据具体的要求进行调节。
电镀时间过短则无法获得均匀的镀层,电镀时间过长则可能会导致镀层过厚或者结构不均匀。
同样地,电流密度过低则电镀时间过长,电流密度过高则可能会引起电解液的变质。
电镀完毕后,需要进行烘干。
将金属件放入烘箱中,使用适当的温度和时间进行烘干,使得镀层完全干燥。
烘干的目的是去除镀层表面的水分,避免发生氧化或者脱落的情况。
最后,可以进行包装和质检。
将已经烘干的金属件包装起来,以避免镀层受到再次污染或者损伤。
同时,还需要进行质检,检查镀层的厚度、均匀性和附着力等指标是否符合要求。
总之,电镀镍工艺流程是一个复杂且精细的过程,需要经过清洗、抛光、洗净、活化、电镀、烘干等多个步骤。
只有在每个步骤都仔细操作,才能获得良好的镀层效果。
镀镍电镀工艺流程

镀镍电镀工艺流程镀镍电镀工艺流程是指通过电镀技术将金属表面镀上一层镍的过程。
镀镍工艺流程主要包括准备工作、预处理、电镀、后处理等几个步骤。
以下将分别进行详细描述。
首先是准备工作。
工作人员应将需要进行镀镍处理的金属材料准备好,检查其表面是否有污垢、油脂等,必要时进行清洗。
同时,要对镀镍设备进行检查和调试,确保其正常运行。
接下来是预处理步骤。
首先是酸洗。
将金属材料浸入酸水中,使其与金属表面发生化学反应,去除表面氧化物、皮膜和杂质,以提高镀层的附着力。
酸洗后,应进行中和清洗,将金属材料浸入碱溶液中进行清洗,以去除酸洗液和金属表面残留的酸性物质。
然后是电镀步骤。
首先是电解液配置。
将适量的镍盐溶解于水中,并加入适量的酸和添加剂,调整电解液的pH值和温度,以提高镍的析出速度和镀层的质量。
然后,将金属材料作为阴极放入电解槽中,与阳极相对放置,连接上电源。
在电镀过程中,电解液中的镍离子会在金属表面还原为金属镍,并沉积在金属材料上,形成一层均匀的镀层。
电镀时间应控制在一定范围内,以确保所得到的镍层厚度和质量符合要求。
最后是后处理步骤。
先是水洗。
将金属材料浸入清水中,将残留在金属表面的电解液和杂质冲洗净。
然后是烘干。
将金属材料放入烘干设备中,通过加热和脱湿,将金属表面的水分彻底除去。
最后是光洁处理。
通过打磨、抛光等方法,将金属表面的纹理和瑕疵消除,使其变得光滑、亮丽。
总结起来,镀镍电镀工艺流程包括准备工作、预处理、电镀、后处理等几个步骤。
其中,预处理包括酸洗和中和清洗;电镀步骤包括电解液配置和电镀操作;后处理步骤包括水洗、烘干和光洁处理。
通过这个工艺流程,可以将金属材料表面镀上一层均匀、光滑、耐腐蚀的镍层,提高金属的外观和性能。
电镀镍工艺流程
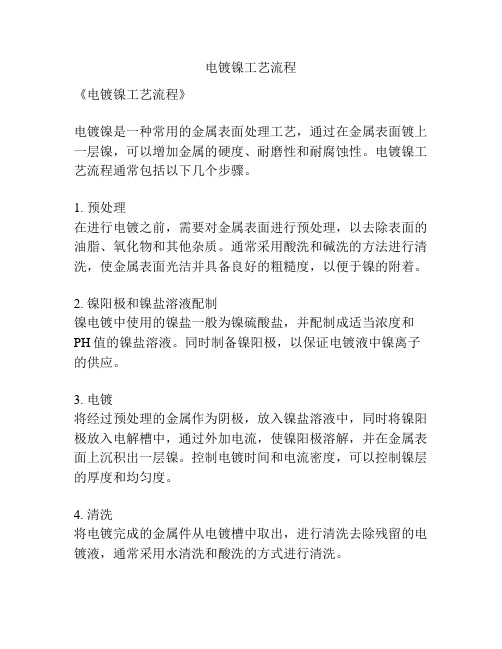
电镀镍工艺流程
《电镀镍工艺流程》
电镀镍是一种常用的金属表面处理工艺,通过在金属表面镀上一层镍,可以增加金属的硬度、耐磨性和耐腐蚀性。
电镀镍工艺流程通常包括以下几个步骤。
1. 预处理
在进行电镀之前,需要对金属表面进行预处理,以去除表面的油脂、氧化物和其他杂质。
通常采用酸洗和碱洗的方法进行清洗,使金属表面光洁并具备良好的粗糙度,以便于镍的附着。
2. 镍阳极和镍盐溶液配制
镍电镀中使用的镍盐一般为镍硫酸盐,并配制成适当浓度和PH值的镍盐溶液。
同时制备镍阳极,以保证电镀液中镍离子的供应。
3. 电镀
将经过预处理的金属作为阴极,放入镍盐溶液中,同时将镍阳极放入电解槽中,通过外加电流,使镍阳极溶解,并在金属表面上沉积出一层镍。
控制电镀时间和电流密度,可以控制镍层的厚度和均匀度。
4. 清洗
将电镀完成的金属件从电镀槽中取出,进行清洗去除残留的电镀液,通常采用水清洗和酸洗的方式进行清洗。
5. 表面处理
经过清洗的金属件需要进行表面处理,通常采用烘干、抛光和喷漆等方法,以提高表面的光泽度和美观度。
通过以上工艺流程,我们可以在金属件表面形成一层均匀、致密的镍层,有效提高金属的抗腐蚀性和耐磨性,从而延长金属件的使用寿命。
同时,镍电镀工艺也被广泛应用于各种金属制品的制造和加工过程中。
电镀工艺电镀镍
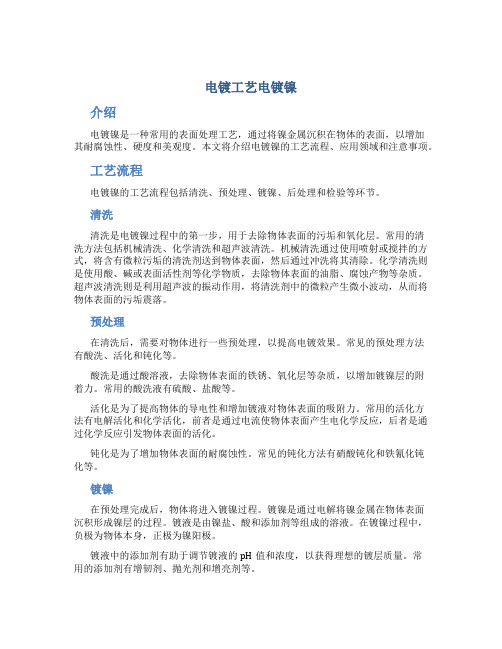
电镀工艺电镀镍介绍电镀镍是一种常用的表面处理工艺,通过将镍金属沉积在物体的表面,以增加其耐腐蚀性、硬度和美观度。
本文将介绍电镀镍的工艺流程、应用领域和注意事项。
工艺流程电镀镍的工艺流程包括清洗、预处理、镀镍、后处理和检验等环节。
清洗清洗是电镀镍过程中的第一步,用于去除物体表面的污垢和氧化层。
常用的清洗方法包括机械清洗、化学清洗和超声波清洗。
机械清洗通过使用喷射或搅拌的方式,将含有微粒污垢的清洗剂送到物体表面,然后通过冲洗将其清除。
化学清洗则是使用酸、碱或表面活性剂等化学物质,去除物体表面的油脂、腐蚀产物等杂质。
超声波清洗则是利用超声波的振动作用,将清洗剂中的微粒产生微小波动,从而将物体表面的污垢震落。
预处理在清洗后,需要对物体进行一些预处理,以提高电镀效果。
常见的预处理方法有酸洗、活化和钝化等。
酸洗是通过酸溶液,去除物体表面的铁锈、氧化层等杂质,以增加镀镍层的附着力。
常用的酸洗液有硫酸、盐酸等。
活化是为了提高物体的导电性和增加镀液对物体表面的吸附力。
常用的活化方法有电解活化和化学活化,前者是通过电流使物体表面产生电化学反应,后者是通过化学反应引发物体表面的活化。
钝化是为了增加物体表面的耐腐蚀性。
常见的钝化方法有硝酸钝化和铁氰化钝化等。
镀镍在预处理完成后,物体将进入镀镍过程。
镀镍是通过电解将镍金属在物体表面沉积形成镍层的过程。
镀液是由镍盐、酸和添加剂等组成的溶液。
在镀镍过程中,负极为物体本身,正极为镍阳极。
镀液中的添加剂有助于调节镀液的pH值和浓度,以获得理想的镀层质量。
常用的添加剂有增韧剂、抛光剂和增亮剂等。
镀液中的镍离子在电解过程中,会受到电流的作用,而在物体表面发生还原反应,从而产生镍金属沉积在物体表面。
镀液中的阳极则用于提供电子,以平衡电解过程。
后处理镀镍完成后,物体需要进行一些后处理,以提高镀镍层的质量和保护。
常见的后处理方法有洗涤、干燥和包装等。
洗涤是将镀液残留物和其他杂质从镀层中清洗出来,以防止残留物对镀层的影响。
化学镀镍与电镀镍工艺及相互之间的区别
化学镀镍与电镀镍工艺及相互之间的区别1 电镀镍电镀是一种电化学过程,也是一种氧化还原过程。
电镀镍是将零件浸入镍盐的溶液中作为阴极,金属镍板作为阳极,接通直流电源后,在零件上就会沉积出金属镍镀层。
电镀镍的配方及工艺条件见表1。
电镀镍的工艺流程为:①清洗金属化瓷件;②稀盐酸浸泡;③冲净;④浸入镀液;⑤调节电流进行电镀;⑥自镀液中取出;⑦冲净;⑧去离子水设备煮;⑨烘干。
表1 电镀镍的配方及工艺条件成分含量/g/L 温度/0C PH值电流密度/A/dm2硫酸镍硫酸镁硼酸氯化钠100-170 21-30 14-30 4-12 室温5-6 0.5电镀镍的优点是镀层结晶细致,平滑光亮,内应力较小,与陶瓷金属化层结合力强。
电镀镍的缺点是:①受金属化瓷件表面的清洁和镀液纯净程度的影响大,造成电镀后金属化瓷件的缺陷较多,例如起皮,起泡,麻点,黑点等;②极易受电镀挂具和在镀缸中位置不同的影响,造成均镀能力差,此外金属化瓷件之间的相互遮挡也会造成瓷件表面有阴阳面的现象;③对于形状复杂或有细小的深孔或盲孔的瓷件不能获得较好的电镀表面;④需要用镍丝捆绑金属化瓷件,对于形状复杂、尺寸较小、数量多的生产情况下,需耗费大量的人力。
2 化学镀镍化学镀镍又称无电镀或自催化镀,它是一种不加外在电流的情况下,利用还原剂在活化零件表面上自催化还原沉积得到镍层,当镍层沉积到活化的零件表面后由于镍具有自催化能力,所以该过程将自动进行下去。
一般化学镀镍得到的为合金镀层,常见的是Ni-P合金和Ni-B合金。
相较Ni-P合金而言,Ni—B合金的熔焊能力更好,共晶温度高,内应力较小,是一种更为理想的化学镀镍方式。
但本文着重讨论的是Ni-P合金镀层。
化学镀镍的配方及工艺条件见表2。
表2化学镀镍的配方及工艺条件成分含量/g/L 温度/0C PH值硫酸镍次磷酸钠柠檬酸钠氯化铵45-50 45-60 20-30 5-8 85 9.5化学镀镍的工艺流程为:①清洗金属化瓷件;②去离子水设备冲洗;③活化液浸泡;④冲净;⑤还原液浸泡;⑥浸入镀液并不时调节pH值;⑦自镀液中取出;⑧冲净;⑨去离子水设备煮;⑩烘干。
电镀镍工艺的优点
电镀镍工艺的优点电镀镍是一种常用的金属表面处理工艺,广泛应用于工业生产中。
电镀镍工艺具有以下几点优点:1. 优异的耐腐蚀性能:电镀镍具有良好的耐腐蚀性能,能有效地防止金属部件受到氧化、腐蚀和磨损等问题的侵害。
这使得电镀镍处理的金属零件能够更长时间地保持其原有的外观和性能。
2. 优异的硬度和耐磨性:电镀镍处理可以显著提高金属部件的硬度和耐磨性。
通过电镀镍,金属表面形成一层坚固的镍合金保护层,能够有效地防止因刮擦、摩擦、磨损等各种原因造成的损伤和破坏。
3. 良好的电导率:镍本身是一种良好的导电材料,电镀在金属表面后,能够保持金属原有的导电性能。
这对一些需要电流传导的金属部件非常重要,如电子元器件等。
4. 质量均匀:电镀镍的镀层均匀且稳定,能够保证金属部件的表面质量达到一定的标准。
这对于一些对表面要求较高的产品,如汽车零件、家电产品等非常重要。
5. 易于加工和修复:电镀镍处理后的金属部件,其表面光洁平滑,非常容易接受其他的加工处理,如研磨、抛光、及时修复等。
这使得电镀镍广泛应用于各种金属零件的加工和修复领域。
6. 可控性高:电镀镍的镀层厚度和性能可以通过调节电流密度等工艺参数来控制。
这使得电镀镍工艺非常灵活,能够满足不同的金属部件的不同需求。
7. 美观性好:电镀镍能够赋予金属部件一种光亮、金属质感的外观,使其看起来更加美观大方。
这使得电镀镍被广泛应用于一些要求外观精美的工业产品、装饰品等领域。
8. 环保性好:相比于其他一些金属表面处理工艺,电镀镍工艺相对环保。
在电镀镍时,不会产生或产生较少的有害的废气和废水,符合现代环保要求。
总结起来,电镀镍是一种广泛应用的金属表面处理工艺。
它具有优异的耐腐蚀性能、硬度和耐磨性,以及良好的电导率。
对金属部件的质量控制能力强,加工和修复方便,具有美观、环保等优点。
因此,电镀镍工艺在各种工业生产领域中得到了广泛的应用。
电镀镍工艺流程
电镀镍工艺流程
电镀镍是一种常见的金属表面处理工艺,通过在金属表面镀上一层镍,可以提高金属的耐腐蚀性能、增加光泽度和硬度,从而扩大其应用范围。
下面将介绍电镀镍的工艺流程。
首先,准备工件。
在进行电镀镍之前,需要对工件进行表面处理,包括去油、除锈、酸洗等工序,以确保工件表面干净、光滑,有利于电镀涂层的附着力和均匀度。
其次,进行预处理。
预处理是电镀镍工艺中的重要环节,包括活化、镍化前处理、中间层处理等步骤。
活化是指在工件表面形成一层活性金属层,以增强电镀层的附着力。
镍化前处理是为了改善工件表面的光洁度,增加电镀层的光泽度。
中间层处理是为了增强工件表面的附着力和耐腐蚀性能。
然后,进行电镀。
电镀镍工艺中的电镀环节是最关键的步骤,需要在镍盐溶液中进行电解,通过阳极和阴极的作用,在工件表面镀上一层均匀的镍层。
在电镀过程中,需要控制电流密度、温度、PH值等参数,以确保电镀层的厚度和质量。
最后,进行后处理。
电镀完成后,需要对工件进行后处理,包括清洗、烘干、抛光等工序,以去除电镀涂层表面的杂质和氢气,增加电镀层的光洁度和耐腐蚀性能。
总之,电镀镍工艺流程包括准备工件、预处理、电镀和后处理四个主要环节。
通过严格控制每个环节的工艺参数和质量要求,可以获得均匀、光滑、具有良好耐腐蚀性能的电镀镍涂层,满足不同工件的表面处理需求。
电镀镍的工艺流程
电镀镍的工艺流程电镀镍是一种常用的表面处理工艺,它可以使金属表面具有优良的耐蚀性、耐磨抗划伤性和装饰效果。
下面将介绍一下电镀镍的工艺流程。
首先,电镀镍的工艺流程包括准备工作、化学镀前处理、化学镀、电解沉镍、电解后处理和检验等环节。
我们将逐步进行详细介绍。
准备工作是工艺流程的前期准备,包括设备、材料和操作人员等方面的准备。
确保设备的正常运行和材料的充足供应对后续工作的顺利进行非常重要。
化学镀前处理是电镀镍工艺流程中非常重要的一环。
它的目的是通过去污、自脱脂和活化等工序,使金属表面达到理想的电镀条件。
常用的去污方法包括酸洗和碱洗,可以去除金属表面的氧化物、油脂和其他杂质。
脱脂的目的是去除金属表面的油脂和有机物,以保证电镀层的附着力。
活化是通过化学方法或电化学方法将金属表面转化为活性状态,为后续电解沉镍提供良好的基础。
化学镀是电镀镍工艺流程的核心环节。
化学镀是利用化学反应在金属表面沉积一层金属镍的方法。
这种方法可以获得非常均匀的电镀层,并具有很高的光亮度。
常用的化学镀方法有光学镀、电化学镀和滚涂镀等。
电解沉镍是让金属表面沉积一层金属镍的方法,它是金属去污和预处理后,将金属材料作为阴极加入电解槽中,通过电流的通入,使金属表面沉积出一层坚硬、耐磨的金属镍层。
电解沉镍可以在金属表面形成均匀致密的镀层,并且具有一定的耐腐蚀性和耐磨性。
电解后处理主要是对电解沉镍后的工件进行清洗和保护处理。
清洗可以去除沉积在镀层上的杂质和清理沉积槽,以便于下一次镀层的质量保证。
保护处理可以提高电镀层的抗氧化性和耐蚀性。
最后,进行检验工作,包括外观检验和性能检验。
外观检验主要是对电镀层的颜色、亮度和均匀度等方面进行检查。
性能检验主要是对电镀层的硬度、耐腐蚀性、耐磨性和附着力等进行测试。
只有通过了检验,才能确保镀层的质量达到要求。
综上所述,电镀镍的工艺流程包括准备工作、化学镀前处理、化学镀、电解沉镍、电解后处理和检验等环节,每个环节都非常重要。
- 1、下载文档前请自行甄别文档内容的完整性,平台不提供额外的编辑、内容补充、找答案等附加服务。
- 2、"仅部分预览"的文档,不可在线预览部分如存在完整性等问题,可反馈申请退款(可完整预览的文档不适用该条件!)。
- 3、如文档侵犯您的权益,请联系客服反馈,我们会尽快为您处理(人工客服工作时间:9:00-18:30)。
1、作用与特性PCB(是英文Printed Circuie Board印制线路板的简称)上用镀镍来作为贵金属和贱金属的衬底镀层,对某些单面印制板,也常用作面层。
对于重负荷磨损的一些表面,如开关触点、触片或插头金,用镍来作为金的衬底镀层,可大大提高耐磨性。
当用来作为阻挡层时,镍能有效地防止铜和其它金属之间的扩散。
哑镍/金组合镀层常常用来作为抗蚀刻的金属镀层,而且能适应热压焊与钎焊的要求,唯读只有镍能够作为含氨类蚀刻剂的抗蚀镀层,而不需热压焊又要求镀层光亮的PCB,通常采用光镍/金镀层。
镍镀层厚度一般不低于2.5微米,通常采用4-5微米。
PCB低应力镍的淀积层,通常是用改性型的瓦特镍镀液和具有降低应力作用的添加剂的一些氨基磺酸镍镀液来镀制。
我们常说的PCB镀镍有光镍和哑镍(也称低应力镍或半光亮镍),通常要求镀层均匀细致,孔隙率低,应力低,延展性好的特点。
2、氨基磺酸镍(氨镍)氨基磺酸镍广泛用来作为金属化孔电镀和印制插头接触片上的衬底镀层。
所获得的淀积层的内应力低、硬度高,且具有极为优越的延展性。
将一种去应力剂加入镀液中,所得到的镀层将稍有一点应力。
有多种不同配方的氨基磺酸盐镀液,典型的氨基磺酸镍镀液配方如下表。
由于镀层的应力低,所以获得广泛的应用,但氨基磺酸镍稳定性差,其成本相对高。
3、改性的瓦特镍(硫镍)改性瓦特镍配方,采用硫酸镍,连同加入溴化镍或氯化镍。
由于内应力的原因,所以大都选用溴化镍。
它可以生产出一个半光亮的、稍有一点内应力、延展性好的镀层;并且这种镀层为随后的电镀很容易活化,成本相对底。
4、镀液各组分的作用:主盐──氨基磺酸镍与硫酸镍为镍液中的主盐,镍盐主要是提供镀镍所需的镍金属离子并兼起着导电盐的作用。
镀镍液的浓度随供应厂商不同而稍有不同,镍盐允许含量的变化较大。
镍盐含量高,可以使用较高的阴极电流密度,沉积速度快,常用作高速镀厚镍。
但是浓度过高将降低阴极极化,分散能力差,而且镀液的带出损失大。
镍盐含量低沉积速度低,但是分散能力很好,能获得结晶细致光亮镀层。
缓冲剂──硼酸用来作为缓冲剂,使镀镍液的PH值维持在一定的范围内。
实践证明,当镀镍液的PH值过低,将使阴极电流效率下降;而PH值过高时,由于H2的不断析出,使紧靠阴极表面附近液层的PH值迅速升高,导致Ni(OH)2胶体的生成,而Ni(OH)2在镀层中的夹杂,使镀层脆性增加,同时Ni(OH)2胶体在电极表面的吸附,还会造成氢气泡在电极表面的滞留,使镀层孔隙率增加。
硼酸不仅有PH缓冲作用,而且他可提高阴极极化,从而改善镀液性能,减少在高电流密度下的“烧焦“现象。
硼酸的存在还有利于改善镀层的机械性能。
阳极活化剂──除硫酸盐型镀镍液使用不溶性阳极外,其它类型的镀镍工艺均采用可溶性阳极。
而镍阳极在通电过程中极易钝化,为了保证阳极的正常溶解,在镀液中加入一定量的阳极活化剂。
通过试验发现,CI—氯离子是最好的镍阳极活化剂。
在含有氯化镍的镀镍液中,氯化镍除了作为主盐和导电盐外,还起到了阳极活化剂的作用。
在不含氯化镍或其含量较低的电镀镍液中,需根据实际性况添加一定量的氯化钠。
溴化镍或氯化镍还常用来作去应力剂用来保持镀层的内应力,并赋与镀层具有半光亮的外观。
添加剂——添加剂的主要成份是应力消除剂,应力消除剂的加入,改善了镀液的阴极极化,降低了镀层的内应力,随着应力消除剂浓度的变化,可以使镀层内应力由张应力改变为压应力。
常用的添加剂有:萘磺酸、对甲苯磺酰胺、糖精等。
与没有去应力剂的镍镀层相比,镀液中加入去应力剂将会获得均匀细致并具有半光亮的镀层。
通常去应力剂是按安培一小时来添加的(现通用组合专用添加剂包括防针孔剂等)。
润湿剂——在电镀过程中,阴极上析出氢气是不可避免的,氢气的析出不仅降低了阴极电流效率,而且由于氢气泡在电极表面上的滞留,还将使镀层出现针孔。
镀镍层的孔隙率是比较高的,为了减少或防止针孔的产生,应当向镀液中加入少量的润湿剂,如十二烷基硫酸钠、二乙基已基硫酸钠、正辛基硫酸钠等,它是一种阴离子型的表面活性物质,能吸附在阴极表面上,使电极与溶液间的界面张力降低,氢气泡在电极上的润湿接触角减小,从而使气泡容易离开电极表面,防止或减轻了镀层针孔的产生。
5、镀液的维护a)温度——不同的镍工艺,所采用的镀液温度也不同。
温度的变化对镀镍过程的影响比较复杂。
在温度较高的镀镍液中,获得的镍镀层内应力低,延展性好,温度加致50度C时镀层的内应力达到稳定。
一般操作温度维持在55--60度C。
如果温度过高,将会发生镍盐水解,生成的氢氧化镍胶体使胶体氢气泡滞留,造成镀层出现针孔,同时还会降低阴极极化。
所以工作温度是很严格的,应该控制在规定的范围之内,在实际工作中是根据供应商提供的最优温控值,采用常温控制器保持其工作温度的稳定性。
b)PH值——实践结果表明,镀镍电解液的PH值对镀层性能及电解液性能影响极大。
在PH≤2的强酸性电镀液中,没有金属镍的沉积,只是析出轻气。
一般PCB镀镍电解液的PH值维持在3—4之间。
PH值较高的镀镍液具有较高的分散力和较高的阴极电流效率。
但是PH过高时,由于电镀过程中阴极不断地析出轻气,使阴极表面附近镀层的PH值升高较快,当大于6时,将会有轻氧化镍胶体生成,造成氢气泡滞留,使镀层出现针孔。
氢氧化镍在镀层中的夹杂,还会使镀层脆性增加。
PH较低的镀镍液,阳极溶解较好,可以提高电解液中镍盐的含量,允许使用较高的电流密度,从而强化生产。
但是PH过低,将使获得光亮镀层的温度范围变窄。
加入碳酸镍或碱式碳酸镍,PH值增加;加入氨基磺酸或硫酸,PH值降低,在工作过程中每四小时检查调整一次PH值。
c)阳极——目前所能见到的PCB常规镀镍均采用可溶性阳极,用钛篮作为阳极内装镍角已相当普遍。
其优点是其阳极面积可做得足够大且不变化,阳极保养比较简单。
钛篮应装入聚丙烯材料织成的阳极袋内防止阳极泥掉入镀液中。
并应定期清洗和检查孔眼是否畅通。
新的阳极袋在使用前,应在沸腾的水中浸泡。
d)净化——当镀液存在有机物污染时,就应该用活性炭处理。
但这种方法通常会去除一部分去应力剂(添加剂),必须加以补充。
其处理工艺如下;(1)取出阳极,加除杂水5ml/l,加热(60—80度C)打气(气搅拌)2小时。
(2)有机杂质多时,先加入3—5ml/lr的30%双氧水处理,气搅拌3小时。
(3)将3—5g/l粉末状活性在不断搅拌下加入,继续气搅拌2小时,关搅拌静置4小时,加助滤粉使用备用槽来过滤同时清缸。
(4)清洗保养阳极挂回,用镀了镍的瓦楞形铁板作阴极,在0.5—0.1安/平方分米的电流密度下进行拖缸8—12小时(当镀液存在无机物污染影响质量时,也常采用)(5)换过滤芯(一般用一组棉芯一组碳芯串联连续过滤,按周期性便换可有效延期大处理时间,提高镀液的稳定性),分析调整各参数、加入添加剂润湿剂即可试镀。
e)分析——镀液应该用工艺控制所规定的工艺规程的要点,定期分析镀液组分与赫尔槽试验,根据所得参数指导生产部门调节镀液各参数。
f)搅拌——镀镍过程与其它电镀过程一样,搅拌的目的是为了加速传质过程,以降低浓度变化,提高允许使用的电流密度上限。
对镀液进行搅拌还有一个十分重要的作用,就是减少或防止镀镍层产生针孔。
因为,电镀过程中,阴极表面附近的镀离子贫乏,氢气的大量析出,使PH值上升而产生氢氧化镍胶体,造成氢气泡的滞留而产生针孔。
加强对留镀液的搅拌,就可以消除上述现象。
常用压缩空气、阴极移动及强制循环(结合碳芯与棉芯过滤)搅拌。
g)阴极电流密度——阴极电流密度对阴极电流效率、沉积速度及镀层质量均有影响。
测试结果表明,当采用PH较底的电解液镀镍时,在低电流密度区,阴极电流效率随电流密度的增加而增加;在高电流密度区,阴极电流效率与电流密度无关,而当采用较高的PH电镀液镍时,阴极电流效率与电流密度的关系不大。
与其它镀种一样,镀镍所选取的阴极电流密度范围也应视电镀液的组分、温度及搅拌条件而定,由于PCB拼板面积较大,使高电流区与低电流区的电流密度相差很大,一般采用2A/dm2为宜。
6、故障原因与排除a)麻坑:麻坑是有机物污染的结果。
大的麻坑通常说明有油污染。
搅拌不良,就不能驱逐掉气泡,这就会形成麻坑。
可以使用润湿剂来减小它的影响,我们通常把小的麻点叫针孔,前处理不良、有金属什质、硼酸含量太少、镀液温度太低都会产生针孔,镀液维护及工艺控制是关键,防针孔剂应用作工艺稳定剂来补加。
b)粗糙、毛刺:粗糙就说明溶液脏,充分过滤就可纠正(PH太高易形成氢氧化物沉淀应加以控制)。
电流密度太高、阳极泥及补加水不纯带入杂质,严重时都将产生粗糙及毛刺。
c)结合力低:如果铜镀层未经充分去氧化层,镀层就会剥落现象,铜和镍之间的附着力就差。
如果电流中断,那就将会在中断处,造成镍镀层的自身剥落,温度太低严重时也会产生剥落。
d)镀层脆、可焊性差:当镀层受弯曲或受到某种程度的磨损时,通常会显露出镀层脆。
这就表明存在有机物或重金属什质污染,添加剂过多、夹带的有机物和电镀抗蚀剂,是有机物污染的主要来源,必须用活性炭加以处理,添加济不足及PH过高也会影响镀层脆性。
e)镀层发暗和色泽不均匀:镀层发暗和色泽不均匀,就说明有金属污染。
因为一般都是先镀铜后镀镍,所以带入的铜溶液是主要的污染源。
重要的是,要把挂具所沾的铜溶液减少到最低程度。
为了去除槽中的金属污染,尤其是去铜溶液应该用波纹钢阴极,在2~5安/平方英尺的电流密度下,每加仑溶液空镀5安培一小时。
前处理不良、低镀层不良、电流密度太小、主盐浓度太低、电镀电源回路接触不良都会影响镀层色泽。
f)镀层烧伤:引起镀层烧伤的可能原因:硼酸不足,金属盐的浓度低、工作温度太低、电流密度太高、PH太高或搅拌不充分。
g)淀积速率低:PH值低或电流密度低都会造成淀积速率低。
h)镀层起泡或起皮:镀前处理不良、中间断电时间过长、有机杂质污染、电流密度过大、温度太低、PH太高或太低、杂质的影响严重时会产生起泡或起皮现象。
I)阳极钝化:阳极活化剂不足,阳极面积太小电流密度太高。
①目的与作用:镀镍层主要作为铜层和金层之间的阻隔层,防止金铜互相扩散,影响板子的可焊性和使用寿命;同时又镍层打底也大大增加了金层的机械强度;②全板电镀铜相关工艺参数:镀镍添加剂的添加一般按照千安小时的方法来补充或者根据实际生产板效果,添加量大约200ml/KAH;图形电镀镍的电流计算一般按2安/平方分米乘以板上可电镀面积;镍缸温度维持在40-55度,一般温度在50度左右,因此镍缸要加装加温,温控系统;③工艺维护:每日根据千安小时来及时补充镀镍添加剂;检查过滤泵是否工作正常,有无漏气现象;每个2-3小时应用干净的湿抹布将阴极导电杆擦洗干净;每周要定期分析铜缸硫酸镍(氨基磺酸镍)(1次/周),氯化镍(1次/周),硼酸(1次/周)含量,并通过霍尔槽试验来调整镀镍添加剂含量,并及时补充相关原料;每周要清洗阳极导电杆,槽体两端电接头,及时补充钛篮中的阳极镍角,用低电流0。