环氧丙烷工艺技术概况
环氧丙烷生产工艺流程

环氧丙烷生产工艺流程
《环氧丙烷生产工艺流程》
环氧丙烷是一种重要的有机化工产品,广泛应用于涂料、树脂、粘合剂、增塑剂、表面活性剂等领域。
其生产工艺流程主要包括丙烷氧化、环氧化和裂解等步骤。
首先是丙烷氧化过程。
在该过程中,丙烷通过氧化反应转化为丙醛,并由丙醛进一步氧化生成环氧丙烷。
这一步骤是整个生产工艺的关键环节,需要在适当的温度和压力下进行催化反应,产物的纯度和收率受到反应条件的影响。
接着是环氧化过程。
在此阶段,通过环氧化反应将丙醛转化为环氧丙烷。
这一步骤需要催化剂的作用,同时在适当的温度和压力条件下进行,可以提高环氧丙烷的产率和纯度。
最后是裂解过程。
在这一步骤中,对环氧丙烷进行裂解,得到相应的产品和副产品。
裂解过程可以根据需要进行不同程度的控制,以得到理想的产物,同时避免副反应的发生。
整个生产工艺流程需要严格控制反应条件、催化剂的选择和使用、产物的分离和纯化等关键环节,以确保环氧丙烷的产率和质量。
同时,还需要考虑能源消耗、废物排放等环保问题,采取合适的措施减少对环境的负面影响。
在环氧丙烷生产工艺流程中,各个步骤之间的协调和配合至关
重要,只有全面优化生产工艺流程,才能达到高效、环保的生产目标。
环氧丙烷工艺

环氧丙烷工艺环氧丙烷是一种重要的有机化学品,广泛应用于化工、医药、农药等领域。
环氧丙烷工艺是生产环氧丙烷的过程,其主要原料为丙烯和过氧化氢,通过环氧化反应得到环氧丙烷。
本文将从环氧丙烷的性质、应用、工艺流程、反应机理等方面介绍环氧丙烷工艺。
一、环氧丙烷的性质和应用环氧丙烷是一种无色、透明、易挥发的液体,具有强烈的臭味。
其化学式为C3H6O,分子量为58.08。
环氧丙烷的密度为0.885 g/cm3,沸点为34.6℃,熔点为-119℃。
它是一种具有高活性的环氧化合物,具有许多优良的性质,如高反应活性、优异的化学稳定性、优良的物理性能等。
环氧丙烷的应用非常广泛,主要用于制造环氧树脂、表面活性剂、染料、药物、农药、金属腐蚀防护剂等。
其中,环氧树脂是一种具有优异性能的高分子材料,广泛应用于涂料、粘合剂、复合材料等领域。
环氧丙烷也是一种重要的医药中间体,可用于制造多种药物,如抗生素、止痛剂、麻醉剂等。
此外,环氧丙烷还可用作消毒剂、杀虫剂、杀菌剂等。
二、环氧丙烷工艺流程环氧丙烷工艺主要分为两个步骤,即环氧化反应和环氧丙烷的分离纯化。
下面将分别介绍这两个步骤的工艺流程。
1. 环氧化反应环氧化反应是将丙烯与过氧化氢在催化剂的作用下,发生环氧化反应,生成环氧丙烷的过程。
环氧化反应的工艺流程如下图所示:(1)原料处理:丙烯和过氧化氢为环氧化反应的主要原料,需要进行预处理。
丙烯需要去除杂质,保证其纯度达到99.5%以上。
过氧化氢需要进行稀释,以降低其浓度,同时加入稳定剂,以避免其分解。
(2)反应器:环氧化反应需要在反应器中进行。
反应器通常采用不锈钢材质,具有良好的耐腐蚀性和耐压性。
反应器内设置搅拌器和加热器,以保证反应物混合均匀和反应温度稳定。
(3)催化剂:环氧化反应需要使用催化剂。
常用的催化剂有过渡金属盐、离子交换树脂等。
催化剂的作用是加速反应速率,提高反应效率。
(4)分离纯化:反应结束后,需要对反应产物进行分离纯化。
环氧丙烷氯化法、共氧化法和直接氧化法技术路线解析
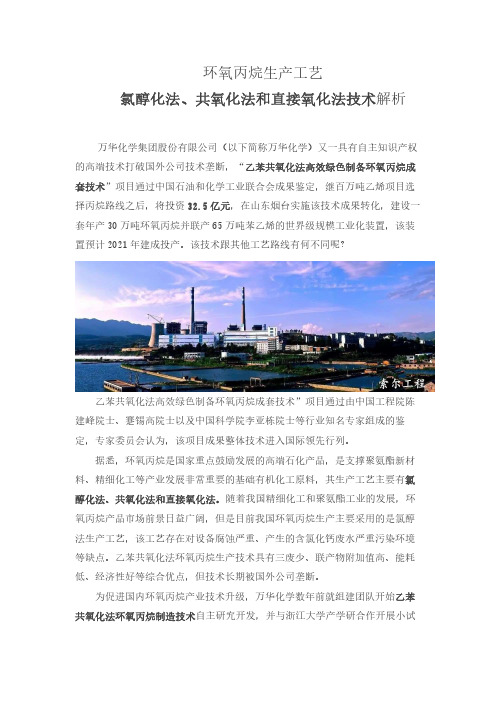
环氧丙烷生产工艺氯醇化法、共氧化法和直接氧化法技术解析万华化学集团股份有限公司(以下简称万华化学)又一具有自主知识产权的高端技术打破国外公司技术垄断,“乙苯共氧化法高效绿色制备环氧丙烷成套技术”项目通过中国石油和化学工业联合会成果鉴定,继百万吨乙烯项目选择丙烷路线之后,将投资32.5亿元,在山东烟台实施该技术成果转化,建设一套年产30万吨环氧丙烷并联产65万吨苯乙烯的世界级规模工业化装置,该装置预计2021年建成投产。
该技术跟其他工艺路线有何不同呢?乙苯共氧化法高效绿色制备环氧丙烷成套技术”项目通过由中国工程院陈建峰院士、蹇锡高院士以及中国科学院李亚栋院士等行业知名专家组成的鉴定,专家委员会认为,该项目成果整体技术进入国际领先行列。
据悉,环氧丙烷是国家重点鼓励发展的高端石化产品,是支撑聚氨酯新材料、精细化工等产业发展非常重要的基础有机化工原料,其生产工艺主要有氯醇化法、共氧化法和直接氧化法。
随着我国精细化工和聚氨酯工业的发展,环氧丙烷产品市场前景日益广阔,但是目前我国环氧丙烷生产主要采用的是氯醇法生产工艺,该工艺存在对设备腐蚀严重、产生的含氯化钙废水严重污染环境等缺点。
乙苯共氧化法环氧丙烷生产技术具有三废少、联产物附加值高、能耗低、经济性好等综合优点,但技术长期被国外公司垄断。
为促进国内环氧丙烷产业技术升级,万华化学数年前就组建团队开始乙苯共氧化法环氧丙烷制造技术自主研究开发,并与浙江大学产学研合作开展小试工艺技术研究。
为突破技术封锁,万华化学的近百名科技人员参与了该项目的研发,并在核心催化剂、反应器关键装备及相关工艺上申请国内外发明专利18件,形成了自主知识产权保护。
同时,万华化学自主设计建成的年产500吨环氧丙烷并联产1100吨苯乙烯工业化试验装置,也一次投料试车成功,并累计实现稳定运行超过90天。
未来,万华化学将投资32.5亿元,在山东烟台实施该技术成果转化,建设一套年产30万吨环氧丙烷并联产65万吨苯乙烯的世界级规模工业化装置,该装置预计2021年建成投产。
环氧丙烷生产工艺

环氧丙烷生产工艺环氧丙烷是一种重要的化工原料,被广泛用于合成树脂、乳液、涂料、胶水等产品。
本文将介绍环氧丙烷的生产工艺。
环氧丙烷的主要生产工艺是通过碱催化的环氧化反应。
具体步骤如下:首先是原料准备。
生产环氧丙烷所需要的原料主要有丙烯、过氧化氢、碱液等。
丙烯是碱催化环氧化反应的底物,过氧化氢是反应的氧化剂,碱液用来催化反应并调节反应的pH值。
接下来是反应过程。
首先,将丙烯和过氧化氢注入反应釜中,加入适量的碱液。
反应釜内有特殊的催化剂,催化剂能加速反应进程并提高产率。
在反应过程中,控制反应的温度和压力是十分关键的。
一般来说,反应温度在40-60摄氏度之间,反应压力在0.5-1.5兆帕之间。
反应时间一般较短,大约在几小时到十几小时不等。
反应完成后,得到的产物是环氧丙烷。
但是,反应中还会产生一些副产物和杂质,需要进行进一步的处理。
最常见的处理方法是蒸馏。
将反应混合物进行适当的加热,使其在不同的沸点下发生蒸发和冷凝,从而将环氧丙烷分离出来,得到纯净的产品。
生产环氧丙烷的工艺中还需要考虑的一个重要因素是安全性。
由于丙烯和过氧化氢具有较高的活性,容易引发爆炸和燃烧,因此在生产中需要严格控制操作条件和采取相应的安全措施。
例如,在反应设备上安装防爆设备,严格控制反应过程中的温度和压力。
除了上述的环氧化反应工艺外,还有其他一些工艺路线可以生产环氧丙烷。
例如,丙烯可以通过直接氧化反应转化为丙醛,然后再通过氧化裂解反应生成环氧丙烷。
或者利用丙烷进行催化裂化得到丙烯,再进行后续的环氧化反应。
这些工艺路线各有优缺点,可以根据实际需求和经济性进行选择。
总结起来,环氧丙烷的生产工艺主要是通过碱催化的环氧化反应,经过原料准备、反应过程和产物处理等步骤完成。
在实际生产中,需要严格控制操作条件和采取安全措施,同时考虑工艺的经济性和可行性。
环氧丙烷生产工艺及对比概要

环氧丙烷的几种生产工艺及对比环氧丙烷,又名氧化丙烯,英文名称propylene oxide (P0)。
它是一种无色、具有醚类气味的低沸易燃液体。
工业产品为两种旋光异构体的外消旋混合物。
凝固点一112.13℃,沸点34.24℃,相对密度0.859。
与水部分混溶,与乙醇、乙醚混溶,并与二氯甲烷、戊烷、戊烯、环戊烷、环戊烯等形成二元共沸物。
有毒,对人体有刺激性。
环氧丙烷(P0)是一种重要的有机化工产品,也是丙烯系列产品中仅次于聚丙烯和丙烯睛的第三大衍生物,同时也是一种重要的基本有机化工原料。
环氧丙烷具有广泛的用途,主要用于生产聚醚多元醇(PPG)、丙二醇(PG)、丙二醇醚、异丙醇胺、轻丙基甲基纤维素醚、轻丙基纤维素醚等,也是非离子表面活性剂、油田破乳剂、农药乳化剂、溶剂、增塑剂、润滑剂、阻燃剂等的主要原料。
广泛应用于化工、轻工、医药、食品和纺织等行业。
目前生产环氧丙烷的主要工业生产工艺有氯醇法,共氧化法和直接氧化法(HPPO)。
国内只有氯醇法和共氧化法,按年产量计算氯醇法占74%,共氧化法占24%。
国内目前还没有直接氧化法的装置。
国内环氧丙烷的年产能与需求对照表单位:万吨年份2007 2008 2009 2010产能90.5 115 130 155需求 75 101110 130环氧丙烷PO 的生产工艺较多,目前国内外已工业化的主要有:氯醇化法、共氧化法和过氧化氢氧化法(简称HPPO 法),其中共氧化法又可以分为乙苯法和异丁烷法两种。
根据2007年世界PO 生产能力统计,氯醇化法占总生产能力的40.3%,共氧化法占51.5%,HPPO 法占5%。
在共氧化法中,乙苯法占世界总生产能力的24.9%,异丁烷法占26.6%。
1、直接氧化法:丙烯用双氧水直接氧化制环氧丙烷。
催化剂为TS-1,钛硅分子筛。
2、共氧化法:以异丁烷或乙苯作为氧的载体,预先制成有机过氧化物,然后与丙烯反应制环氧丙烷。
OH C CH -33)(3、 氯醇法或氯碱法:丙烯通过氯醇化过程用卤素氧化制环氧丙烷。
环氧丙烷工艺

环氧丙烷工艺环氧丙烷是一种重要的有机化工原料,广泛应用于树脂、涂料、塑料、粘合剂等领域。
环氧丙烷工艺是生产环氧丙烷的关键技术之一,本文将就环氧丙烷工艺的原理、流程、设备和应用等方面进行详细介绍。
一、环氧丙烷工艺原理环氧丙烷是由丙烯和过氧化氢在催化剂存在下发生环氧化反应得到的。
反应式如下:CH2=CHCH3 + H2O2 → CH2OCHCH3 + H2O环氧丙烷工艺的核心是催化剂的选择和反应条件的控制。
目前常用的催化剂有碱式离子交换树脂、硫酸铵、硫酸亚铁等。
反应温度一般在20-40℃之间,反应压力一般为0.1-0.3MPa,反应时间为2-4小时。
二、环氧丙烷工艺流程环氧丙烷工艺流程包括原料处理、反应、分离、精馏等步骤。
1. 原料处理丙烯和过氧化氢是生产环氧丙烷的两个主要原料。
丙烯一般通过石油炼制或煤化工生产得到,过氧化氢则可以通过工业氧化剂的氢氧化法或电解法等途径制备。
2. 反应将丙烯和过氧化氢按一定比例加入反应釜中,加入催化剂后开始反应。
反应温度、压力、时间等参数需要根据催化剂的种类和反应条件进行调整。
反应后得到环氧丙烷和水。
3. 分离将反应后的混合物进行分离,将环氧丙烷和水分离开来。
4. 精馏将分离后的环氧丙烷进行精馏,得到纯净的环氧丙烷产品。
三、环氧丙烷工艺设备环氧丙烷工艺设备主要包括反应釜、分离器、精馏塔等。
反应釜一般采用不锈钢或玻璃钢材质,具有耐腐蚀、耐高温等特点。
分离器和精馏塔则需要具备良好的分离效果和传热效率。
四、环氧丙烷工艺应用环氧丙烷是一种重要的有机化工原料,广泛应用于树脂、涂料、塑料、粘合剂等领域。
其中,环氧树脂是环氧丙烷的重要应用之一。
环氧树脂具有优异的物理性能和化学稳定性,被广泛应用于电子、航空、汽车、建筑等领域。
总之,环氧丙烷工艺是生产环氧丙烷的关键技术之一。
本文介绍了环氧丙烷工艺的原理、流程、设备和应用等方面的内容,希望能对环氧丙烷工艺的研究和应用有所帮助。
(完整版)环氧丙烷工业应用和生产工艺(更新至2017年)
环氧丙烷应用和生产主要工艺路线一、环氧丙烷基础性质中文别称:氧化丙烯英文名称:Propylene Oxide(简称PO)分子式:C3H6O分子量:58.08相对密度:0.859 g/cm3(20℃)熔点:-112℃沸点:34℃环氧丙烷易溶于水,是无色透明的低沸易燃液体,具有类似醚类气味。
环氧丙烷在铁、锌等碱金属存在下易引起自聚反应,所以必须用干氮或者其他惰性气体贮存在容器内加以保护,使用不锈钢洁净容器进行贮存,不适宜长距离运输。
二、环氧丙烷的应用领域环氧丙烷(PO)是一种重要的有机化工原料,是除了聚丙烯和丙烯腈之外的第三大丙烯衍生物。
环氧丙烷主要用于聚醚多元醇以及丙二醇及丙二醇醚等的生产。
聚醚多元醇(PPG)主要用于生产聚氨酯塑料,其次用作表面活性剂(如泡沫稳定性、造纸工业消泡剂和原油破乳剂等),也可用作润滑剂和专用溶剂等。
丙二醇(PG)主要用作抗冻剂、有机溶剂等,也用于生产环氧树脂、不饱和聚酯树脂等,还用于生产医药等的重要中间体。
丙二醇醚是用途广泛的低毒性有机溶剂。
全球环氧市场主要是生产聚醚多元醇,约占70%;其次是生产丙二醇。
在我国约85%的环氧丙烷用于生产聚醚多元醇,约8%用于生产丙二醇,其次是生产丙烯酸酯(2%)和醚类(2%)。
因国内聚醚多元醇的厂家主要集中在山东、上海、江苏等地区,所以这些地区也是环氧丙烷最大的消费地。
二、环氧丙烷主要生产工艺1、氯醇法,(1931实现工业化)主要反应式:⏹氯醇化反应⏹皂化反应皂化是氯醇与碱反应制取环氧化物的过程。
氯醇法制环氧丙烷的原料消耗80年代,我国引进了日本旭硝子、日本三井、美国陶氏等公司的氯醇法技术,我国的生产企业不断对氯醇法工艺装置进行改扩建,使我国环氧丙烷的产能得到了较大的突破;但氯醇法工艺每生产1t环氧丙烷大约有40~60t含氯化物的废水和2~4t的废渣产生,这种工艺生产的废水处理非常困难,污染严重。
此外,氯醇法生产过程中产生的次氯酸也对设备有很大的腐蚀,因此,不管是从经济方面,还是环境保护方面,氯醇法生产工艺都已经不适应现代社会的发展。
环氧丙烷生产方法与工艺
环氧丙烷生产方法与工艺环氧丙烷是一种重要的有机合成原料,广泛应用于涂料、塑料、胶粘剂等化工领域。
下面将介绍环氧丙烷的生产方法和工艺。
环氧丙烷的生产方法主要有环氧化法和氯氧化法两种。
其中,环氧化法是目前应用最广泛的一种方法。
环氧化法的工艺流程如下:1.原料准备:将丙烷加入反应器中,并加入过量的过氧化氢作为氧化剂。
同时,加入催化剂,常用的催化剂有过硫酸铵或过硫酸钠。
2.氧化反应:在适宜的温度和压力下,将反应器中的丙烷和氧化剂反应,生成环氧丙烷。
3.分离纯化:将反应混合物通过蒸馏或吸附等方法进行分离纯化,得到高纯度的环氧丙烷。
环氧化法的反应条件需要控制得当。
适宜的反应温度通常在40-60℃范围内,较高的温度会导致副反应的发生,影响环氧丙烷的产率和纯度。
反应压力一般在1-2MPa之间,过高的压力会使反应剧烈,过低则会影响反应速率。
在环氧化法中,催化剂的选择也十分重要。
催化剂可以提高反应速率和环氧丙烷的产率。
目前,过硫酸铵或过硫酸钠是最常用的催化剂,在反应中起到氧化剂活化的作用。
相比之下,氯氧化法工艺相对较少应用。
该方法通过将丙烷和氯气反应,生成1,2-二氯丙烷,再经过脱氯反应生成环氧丙烷。
虽然氯氧化法原料较为简单,但由于氯气具有较高的毒性和危险性,操作风险较大,且生成的1,2-二氯丙烷需要通过脱氯反应去除氯原子,工艺相对繁琐,因此应用较少。
环氧丙烷的生产过程中有一些关键点需要注意。
首先是原料的选择和储存,丙烷的纯度和质量对于反应效果和产物纯度有很大影响。
其次是反应器的设计和选择,反应器需要耐压、抗腐蚀和优良的热传导性能。
最后是分离纯化工艺,通常采用蒸馏或吸附等方法进行分离纯化,以获取高纯度的环氧丙烷。
综上所述,环氧丙烷的生产方法主要有环氧化法和氯氧化法。
其中,环氧化法是目前应用较广泛的一种方法,具有工艺简便、原料易得等优点。
随着化工技术的不断发展,环氧丙烷的生产工艺也在不断改进,以提高产率和纯度,并减少对环境的影响。
环氧丙烷生产方法与工艺
一.环氧丙烷的简介:环氧丙烷,又名氧化丙烯、甲基环氧乙烷,是非常重要的有机化合物原料,是仅次于聚丙烯和丙烯腈的第三大丙烯类衍生物。
其结构式为:环氧丙烷在常温常压下为无色透明低沸易燃液体,具有类似醚类气味;环氧丙烷工业产品为两种旋光异构体的外消旋混合物。
凝固点-112.13℃,沸点34.24℃,相对密度(20/20℃)0.859,折射率(nD)1.3664,粘度(25℃)0.28 mPa?S。
与水部分混溶[20℃时水中溶解度40.5%(重量);水在环氧丙烷中的溶解度12.8%(重量)],与乙醇、乙醚混溶,并与二氯甲烷、戊烷、戊烯、环戊烷、环戊烯等形成二元共沸物。
有毒,对粘膜和皮肤有刺激性,可损伤眼角膜和结膜,引起呼吸系统疼痛,皮肤灼伤和肿胀,甚至组织坏死。
环氧丙烷主要用于生产聚醚多元醇、丙二醇和各类非离子表面活性剂等,其中聚醚多元醇是生产聚氨酯泡沫、保温材料、弹性体、胶粘剂和涂料等的重要原料,各类非离子型表面活性剂在石油、化工、农药、纺织、日化等行业得到广泛应用。
同时,环氧丙烷也是重要的基础化工原料。
我国环氧丙烷(PO)产业发展受技术水平、环保因素、原料供应等三方面影响,部分装置一直难以满负荷生产,2001年以后,国内PO产能、产量增幅均不是很大,而同期聚氨酯等下游消费领域需求则保持高速增长,国内供需缺口进一步拉大,见表1、表2。
表1 2005年我国PO消费结构%消费领域比例消费领域比例聚醚多元醇84.76醇醚1.87PG/DM C7.78表面活性剂等3.27碳酸丙烯酯2.33表2 2001-2005年我国PO市场供需状况统计万t/a年份产能/万t.a-1产量进口量出口量表观消费量自给率/%20 01 47.633.03.6忽略36.6 90.220 02 49.032.05.3忽略37.3 85.820 03 49.041.411.6 0.1 52.9 78.320 04 55.543.019.10.1 62.0 69.420 05 55.551.315.11.0 65.4 78.420 06E 95.569.012.1.0 80.0 85.0随着中海壳牌25万t/a装置、山东石大胜华4万t/a、天津大沽6万t/a扩建装置、山东东大3万t/a等装置的投产,截至2006年末我国PO产能已增长至95.5万t/a,同比增长72%。
(完整版)环氧丙烷工业应用和生产工艺(更新至2017年)
(完整版)环氧丙烷⼯业应⽤和⽣产⼯艺(更新⾄2017年)环氧丙烷应⽤和⽣产主要⼯艺路线⼀、环氧丙烷基础性质中⽂别称:氧化丙烯英⽂名称:Propylene Oxide(简称PO)分⼦式:C3H6O分⼦量:58.08相对密度:0.859 g/cm3(20℃)熔点:-112℃沸点:34℃环氧丙烷易溶于⽔,是⽆⾊透明的低沸易燃液体,具有类似醚类⽓味。
环氧丙烷在铁、锌等碱⾦属存在下易引起⾃聚反应,所以必须⽤⼲氮或者其他惰性⽓体贮存在容器内加以保护,使⽤不锈钢洁净容器进⾏贮存,不适宜长距离运输。
⼆、环氧丙烷的应⽤领域环氧丙烷(PO)是⼀种重要的有机化⼯原料,是除了聚丙烯和丙烯腈之外的第三⼤丙烯衍⽣物。
环氧丙烷主要⽤于聚醚多元醇以及丙⼆醇及丙⼆醇醚等的⽣产。
聚醚多元醇(PPG)主要⽤于⽣产聚氨酯塑料,其次⽤作表⾯活性剂(如泡沫稳定性、造纸⼯业消泡剂和原油破乳剂等),也可⽤作润滑剂和专⽤溶剂等。
丙⼆醇(PG)主要⽤作抗冻剂、有机溶剂等,也⽤于⽣产环氧树脂、不饱和聚酯树脂等,还⽤于⽣产医药等的重要中间体。
丙⼆醇醚是⽤途⼴泛的低毒性有机溶剂。
全球环氧市场主要是⽣产聚醚多元醇,约占70%;其次是⽣产丙⼆醇。
在我国约85%的环氧丙烷⽤于⽣产聚醚多元醇,约8%⽤于⽣产丙⼆醇,其次是⽣产丙烯酸酯(2%)和醚类(2%)。
因国内聚醚多元醇的⼚家主要集中在⼭东、上海、江苏等地区,所以这些地区也是环氧丙烷最⼤的消费地。
⼆、环氧丙烷主要⽣产⼯艺1、氯醇法,(1931实现⼯业化)主要反应式:氯醇化反应皂化反应皂化是氯醇与碱反应制取环氧化物的过程。
氯醇法制环氧丙烷的原料消耗80年代,我国引进了⽇本旭硝⼦、⽇本三井、美国陶⽒等公司的氯醇法技术,我国的⽣产企业不断对氯醇法⼯艺装置进⾏改扩建,使我国环氧丙烷的产能得到了较⼤的突破;但氯醇法⼯艺每⽣产1t环氧丙烷⼤约有40~60t含氯化物的废⽔和2~4t的废渣产⽣,这种⼯艺⽣产的废⽔处理⾮常困难,污染严重。
- 1、下载文档前请自行甄别文档内容的完整性,平台不提供额外的编辑、内容补充、找答案等附加服务。
- 2、"仅部分预览"的文档,不可在线预览部分如存在完整性等问题,可反馈申请退款(可完整预览的文档不适用该条件!)。
- 3、如文档侵犯您的权益,请联系客服反馈,我们会尽快为您处理(人工客服工作时间:9:00-18:30)。
环氧丙烷工艺技术概况
a)氯醇法
氯醇法是传统的环氧丙烷工业生产路线,该法自20世纪30年代由美国UCC公司开发并进行工业生产以来,一直是生产环氧丙烷的主要方法。
截止到2009年6月,全球环氧丙烷的总生产能力约810万吨/年,其中氯醇法占33.58%。
氯醇法分为以石灰为皂化原料的传统氯醇法和以电解液(NaOH)为皂化原料的改良氯醇法。
1)传统氯醇法
主要专利商:美国Dow Chemical、日本Asahi glass公司、Mitsui Chemicals和Showa denko 公司、意大利Enichem公司等。
主要工艺过程:
丙烯、氯气和水按一定配比送入氯醇化反应器中进行反应,未反应的丙烯与反应中产生的HCl及部分的二氯丙烷等自反应器顶部排出,经冷凝除去氯化氢和有机氯化物,丙烯循环回用。
反应器底部得到氯丙醇质量分数为4~5%的盐酸溶液。
将该溶液与过量约10%的石灰乳混合后送入皂化塔中皂化,再经精馏即可得到环氧丙烷。
优点:传统氯醇法具有流程比较短,工艺成熟,操作负荷弹性大,产品选择性好、收率高,生产比较安全,对原料丙烯纯度的要求不高,投资少,无引起市场干扰的联产产品,其产品具有较强的低成本竞争力等优点。
缺点:传统氯醇法存在的最大问题是设备易于腐蚀,在生产过程中产生大量含氯污水(每吨产品约产生45~60吨废水和2.1吨氯化钙)废渣,该废水具有温度、pH值、氯根含量、COD含量和悬浮物含量“五高”的特点,处理成本高,造成严重的环境污染。
世界上大多数发展中国家和地区采用传统氯醇法技术,装置规模都比较小。
例如:俄罗斯、东欧、巴西、印度和中国。
少数发达国家的老装置也在使用该技术(如日本、德国),面临被淘汰。
2)改良氯醇法
主要专利商:美国Dow Chemical和意大利Enichem公司。
主要工艺过程:
改良氯醇法是用烧碱代替石灰乳,在常压或减压条件下于80~130℃与氯丙醇发生皂化反应。
该法提高了氯丙醇的转化率和环氧丙烷的收率,同时抑制了皂化副反应的发生,提高了环氧丙烷的选择性。
优点:
(1)用NaOH溶液代替石灰乳作为皂化原料,避免了氯化钙的产生,从而消除了废渣的生成及其对环境的污染。
(2)避免了废水污染问题。
该工艺的废水总量并未减少,每生产1吨环氧丙烷仍伴随产出超过30吨的废水,其中含有7~8%的NaCl、10-4级的丙二醇以及其它微量有机物质。
但将此含盐水溶液经过精制处理,除去其中的有机物,再经重新饱和后可电解产生氯和碱,并可循环用于平衡环氧丙烷合成所需的氯和碱,实现了闭路循环,从而避免了废水污染。
(3)良好的经济效益。
上述说明该工艺具有良好的环境效益,同样它具有良好的经济效益。
该工艺在Dow 化学公司的一个40万吨/年环氧丙烷生产装置中运行,环氧丙烷的总收率较传统法提高5%,发挥了原料共用和规模化的优势,节能5%,生产成本降低且不产生公害。
提高了氯丙醇的转化率和环氧丙烷的收率,避免了氯化钙的产生,根除了废渣的来源和污染,消除了石灰皂化引起的弊端。
缺点:仍使用氯,耗电量大,生产成本难以降低,需和氯碱装置配套生产。
b)共氧化法
共氧化法又称间接氧化法、联产法、哈康法,根据原料和联产品的不同,又可分为乙苯共氧化法(PO/SM)、异丁烷共氧化法(PO/TBA)两种工艺。
共氧化法自1969年工业化以来,在世界范围发展迅速,截止到2009年6月,环氧丙烷/苯乙烯联产法占全球环氧丙烷生产能力的54.94%、环氧丙烷/叔丁醇联产法占7.78%。
1)乙苯共氧化工艺(PO/SM)
ARCO Chemical公司首先将此工艺工业化,目前该工艺是新建大规模环氧丙烷联产苯乙烯装置的首选工艺。
2006年,中国海洋石油总公司与Shell公司采用该工艺在广东惠州兴建了25万吨/年的环氧丙烷生产装置,打破了我国环氧丙烷生产单纯依赖氯醇法的格局。
2010年,中国石化镇海炼油化工股份有限公司和Lyondell共同投资建设的28.5万吨/年环氧丙烷项目于2010年6月试车成功,是目前世界上最大的PO/SM工艺生产装置。
主要专利商:美国Lyondell公司、Shell公司、美国ARCO Chem公司。
主要工艺过程:乙苯与空气中的氧反应生产乙苯过氧化物,乙苯过氧化物与丙烯进行环氧化反应生成环氧丙烷,同时副产α-苯乙醇。
α-苯乙醇在气相或液相中脱水生成苯乙烯,每吨环氧丙烷联产苯乙烯2.2~2.5吨。
优点:克服了氯醇法的设备腐蚀严重、生产污水量大等缺点,具有产品成本低(联产品分摊成本)和环境污染较小的优势。
可按产业的要求联产苯乙烯产品,适合在需要苯乙烯的地区建设。
缺点:工艺流程长、所需原料品种较多、对丙烯质量要求高、操作压力大、设备造价高、建设投资大,对规模化生产的要求较高。
同时,环氧丙烷在共氧化法生产中,产生较多的联产品,原料来源和产品销售相互制约因素较大,只有环氧丙烷和联产品市场需求匹配时才能显现出该工艺的优势。
此外,污水COD值也比较高,处理费用较大,约占总投资的10%。
Lyondell和Shell两个重要工艺之间的主要差异体现在丙烯环氧化催化剂方面。
Lyondell采用均相的Mo催化剂,而Shell采用非均相的Ti/SiO2催化剂。
2)异丁烷共氧化工艺(PO/TBA)
该工艺是由美国ARCO Chem公司开发的,主要以丙烯、异丁烷和氧气为原料进行生产,其反应过程分为过氧化和环氧化两步。
主要专利商:美国ARCO Chem公司、Texaco Chemical公司、Lyondell公司、Huntsman 公司。
主要工艺过程:纯氧在液相中与异丁烷反应生成叔丁基过氧化物,随后在钼催化剂催化下与丙烯进行环氧化反应,制得环氧丙烷并联产叔丁醇,每吨环氧丙烷副产叔丁醇2.5~3.0吨。
优点:克服了氯醇法的设备腐蚀严重、生产污水量大等缺点,具有产品成本低(联产品分摊成本)和环境污染较小的优势。
可按产业的要求联产叔丁醇或MTBE等产品,适合在需要叔丁醇或MTBE的地区建设。
缺点:具有与乙苯共氧化工艺(PO/SM)相同的缺点外,该工艺产生的叔丁醇(TBA)被转化为甲基叔丁基醚(MTBE)作为联产品用于汽油,由于MTBE涉及健康和水体污染风险,该工艺的应用受到一定限制。
c)单产法
单产法又称过氧化氢异丙苯共氧化工艺、异丙苯氧化法,是共氧化法的一种改进,与共氧化法的主要区别在于使用异丙苯替代了乙苯,并且异丙苯循环使用,不产生联产品。
2003年5月,日本Sumitomo chemical公司投资在日本千叶建成一套单产20万吨/年环氧丙烷装置。
2009年上半年,该公司与沙特阿拉伯-美国石油公司(Saudi Aramco)在沙特的合资企业采用此技术建设20万吨/年的环氧丙烷装置也已建成投产。
主要专利商:日本Sumitomo chemical公司。
主要工艺过程:异丙苯经氧化生成过氧化氢异丙苯(CHP)后,在装有钛基催化剂的固定床反应器中,以CHP为氧化剂,使丙烯环氧化得到环氧丙烷和二甲基苄醇,后者脱水为α-甲基苯乙烯,然后再加氢生成异丙苯循环使用。
优点:与共氧化法比,该工艺无副产物,也无需氯醇法工艺所需的防腐设备,投资低。
缺点:技术上尚不完善、产率偏低、装置运营成本较高、生产可变成本较高。
d)直接氧化法
该法包括过氧化氢直接氧化法(HPPO)和氧气直接氧化法。
1)过氧化氢直接氧化法(HPPO)
鉴于目前工业制备环氧丙烷工艺路线存在的弊端,近年来世界各大公司一直致力于流程简单、副产物少和绿色无污染的环氧丙烷新工艺的研究,其中丙烯直接氧化法成为研究热点,尤其是过氧化氢直接氧化法(HPPO)日趋成熟。
主要专利商:Degussa/Uhde、Dow/BASF。
主要工艺过程:甲醇、过氧化氢和丙烯(质量比约为64.5:15.5:20)在含沸石硅酸钛催化剂(TS-1)的反应器内进行反应。
该工艺中,过氧化氢转化率可达98%,环氧丙烷选择性可达95%,少量的未反应丙烯可循环回反应器。
优点:与其它工艺相比,具有装置设计简单、环境友好、生产过程中只产生终端产品环氧丙烷和水,副产品只有少量丙二醇。
此外,还具有装置占地面积小、配套设施少、投资较低等优点。
缺点:溶剂甲醇会使环氧丙烷开环,从而降低其收率;过氧化氢和催化剂价格相对较高,投资较高;过氧化氢溶液储运困难,现场生产费用高。
2)氧气直接氧化法
丙烯用氧气直接氧化制取环氧丙烷的工艺,同样因不生成副产物且无需使用高价试剂等特点,受到了人们的关注。
美国Lyondell公司正在开发将丙烯、氢气、氧气转化为环氧丙烷的直接氧化技术,使用一种由钯和钛的硅酸盐组成的双功能催化剂,用氢和氧产生过氧化氢后立即将丙烯转化为环氧丙烷,全部工艺过程在一台反应器内完成。
该公司在美国纽敦-斯奎尔建有一套实验装置,以进一步将此工艺推向工业化。
目前该工艺尚处于试验阶段。
优点:投资明显降低。
该工艺技术为一步法生产环氧丙烷,无需辅助原料设施,与过氧化氢直接氧化法(HPPO)技术相比具有很大优势,因后者需要就地建设过氧化氢装置。
目前美国Lyondell公司正在加紧产业化。