硅溶胶工艺的简介
硅溶胶快干工艺
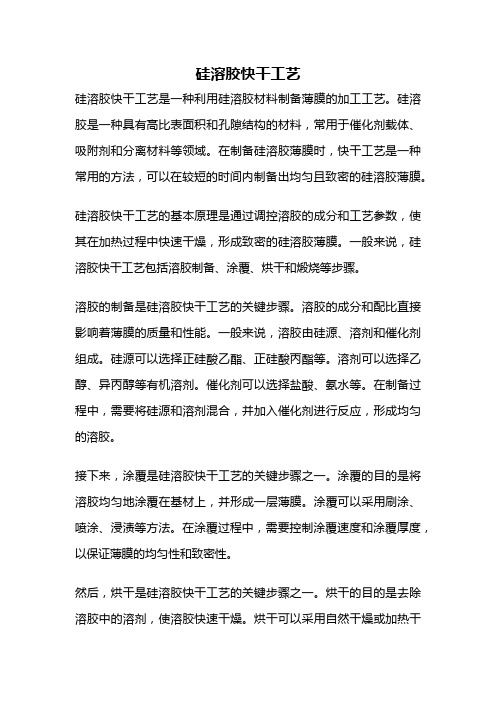
硅溶胶快干工艺硅溶胶快干工艺是一种利用硅溶胶材料制备薄膜的加工工艺。
硅溶胶是一种具有高比表面积和孔隙结构的材料,常用于催化剂载体、吸附剂和分离材料等领域。
在制备硅溶胶薄膜时,快干工艺是一种常用的方法,可以在较短的时间内制备出均匀且致密的硅溶胶薄膜。
硅溶胶快干工艺的基本原理是通过调控溶胶的成分和工艺参数,使其在加热过程中快速干燥,形成致密的硅溶胶薄膜。
一般来说,硅溶胶快干工艺包括溶胶制备、涂覆、烘干和煅烧等步骤。
溶胶的制备是硅溶胶快干工艺的关键步骤。
溶胶的成分和配比直接影响着薄膜的质量和性能。
一般来说,溶胶由硅源、溶剂和催化剂组成。
硅源可以选择正硅酸乙酯、正硅酸丙酯等。
溶剂可以选择乙醇、异丙醇等有机溶剂。
催化剂可以选择盐酸、氨水等。
在制备过程中,需要将硅源和溶剂混合,并加入催化剂进行反应,形成均匀的溶胶。
接下来,涂覆是硅溶胶快干工艺的关键步骤之一。
涂覆的目的是将溶胶均匀地涂覆在基材上,并形成一层薄膜。
涂覆可以采用刷涂、喷涂、浸渍等方法。
在涂覆过程中,需要控制涂覆速度和涂覆厚度,以保证薄膜的均匀性和致密性。
然后,烘干是硅溶胶快干工艺的关键步骤之一。
烘干的目的是去除溶胶中的溶剂,使溶胶快速干燥。
烘干可以采用自然干燥或加热干燥的方法。
在烘干过程中,需要控制烘干温度和时间,以避免薄膜开裂或变形。
煅烧是硅溶胶快干工艺的关键步骤之一。
煅烧的目的是在高温下使薄膜中的有机物热解和硅源结晶,形成致密的硅溶胶薄膜。
煅烧可以采用气氛煅烧或真空煅烧的方法。
在煅烧过程中,需要控制煅烧温度和时间,以保证薄膜的结晶度和致密度。
硅溶胶快干工艺是一种制备硅溶胶薄膜的有效方法。
通过调控溶胶的成分和工艺参数,可以制备出均匀且致密的硅溶胶薄膜。
硅溶胶薄膜具有高比表面积和孔隙结构,广泛应用于催化剂载体、吸附剂和分离材料等领域。
在今后的研究中,可以进一步优化硅溶胶快干工艺,提高薄膜的性能和应用范围。
硅溶胶的生产工艺
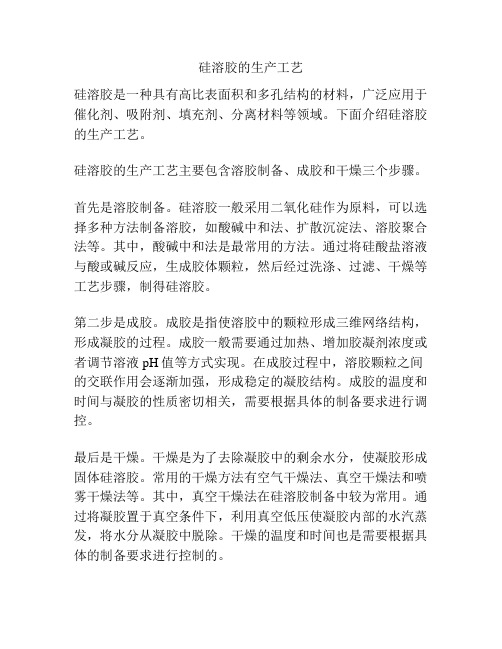
硅溶胶的生产工艺
硅溶胶是一种具有高比表面积和多孔结构的材料,广泛应用于催化剂、吸附剂、填充剂、分离材料等领域。
下面介绍硅溶胶的生产工艺。
硅溶胶的生产工艺主要包含溶胶制备、成胶和干燥三个步骤。
首先是溶胶制备。
硅溶胶一般采用二氧化硅作为原料,可以选择多种方法制备溶胶,如酸碱中和法、扩散沉淀法、溶胶聚合法等。
其中,酸碱中和法是最常用的方法。
通过将硅酸盐溶液与酸或碱反应,生成胶体颗粒,然后经过洗涤、过滤、干燥等工艺步骤,制得硅溶胶。
第二步是成胶。
成胶是指使溶胶中的颗粒形成三维网络结构,形成凝胶的过程。
成胶一般需要通过加热、增加胶凝剂浓度或者调节溶液pH值等方式实现。
在成胶过程中,溶胶颗粒之间的交联作用会逐渐加强,形成稳定的凝胶结构。
成胶的温度和时间与凝胶的性质密切相关,需要根据具体的制备要求进行调控。
最后是干燥。
干燥是为了去除凝胶中的剩余水分,使凝胶形成固体硅溶胶。
常用的干燥方法有空气干燥法、真空干燥法和喷雾干燥法等。
其中,真空干燥法在硅溶胶制备中较为常用。
通过将凝胶置于真空条件下,利用真空低压使凝胶内部的水汽蒸发,将水分从凝胶中脱除。
干燥的温度和时间也是需要根据具体的制备要求进行控制的。
总结来说,硅溶胶的生产工艺主要包括溶胶制备、成胶和干燥三个步骤。
通过合理选择原料和工艺参数,可以制备出具有理想性能的硅溶胶材料。
不同的制备方法和条件会影响硅溶胶的结构、孔径和比表面积等性质,因此在工艺过程中需要根据具体的应用要求进行调整和优化。
硅溶胶生产工艺
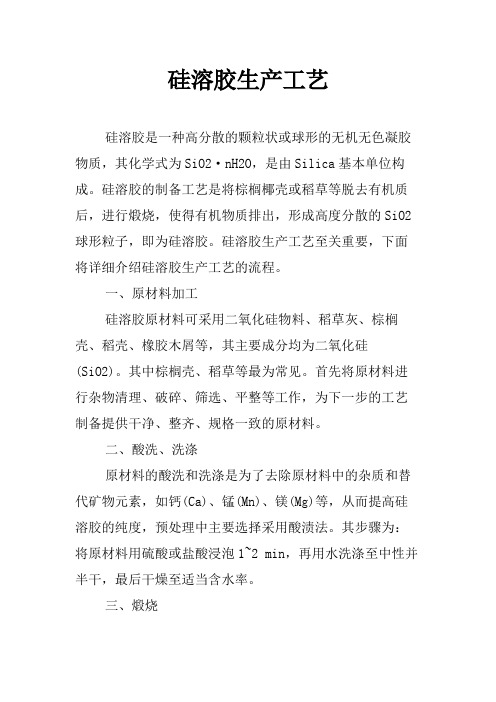
硅溶胶生产工艺硅溶胶是一种高分散的颗粒状或球形的无机无色凝胶物质,其化学式为SiO2·nH2O,是由Silica基本单位构成。
硅溶胶的制备工艺是将棕榈椰壳或稻草等脱去有机质后,进行煅烧,使得有机物质排出,形成高度分散的SiO2球形粒子,即为硅溶胶。
硅溶胶生产工艺至关重要,下面将详细介绍硅溶胶生产工艺的流程。
一、原材料加工硅溶胶原材料可采用二氧化硅物料、稻草灰、棕榈壳、稻壳、橡胶木屑等,其主要成分均为二氧化硅(SiO2)。
其中棕榈壳、稻草等最为常见。
首先将原材料进行杂物清理、破碎、筛选、平整等工作,为下一步的工艺制备提供干净、整齐、规格一致的原材料。
二、酸洗、洗涤原材料的酸洗和洗涤是为了去除原材料中的杂质和替代矿物元素,如钙(Ca)、锰(Mn)、镁(Mg)等,从而提高硅溶胶的纯度,预处理中主要选择采用酸渍法。
其步骤为:将原材料用硫酸或盐酸浸泡1~2 min,再用水洗涤至中性并半干,最后干燥至适当含水率。
三、煅烧预处理后的原材料放入煅炉中进行大量的干燥、煅烧。
该步骤主要是制备出凝胶球体原料,通常采用一体化煅炉,将原材料放在煅炉内部360度旋转煅烧,温度通常在1000℃左右,时间线上03小时至10小时不等。
该步骤不仅要求包括煅炉的温度、时间、料量及搅拌风速等设备因素,还需要对原材料进行充分预处理、煅炉退火速率要控制得当,以保证其具有均匀、完整的球形外形。
四、粉碎、湿法分散下面的步骤是打破这些球体原料,制备出高度分散的二氧化硅,主要是通过粉碎和分散两个步骤来完成的。
粉碎可以采用氧气气流粉碎,目的是使大球体逐渐变为小球体。
分散则是采用HCl和硅酸钠,将球体原料在罐体内充入一定的水,使其形成悬浮液,加入酸性和碱性物质,通过光学显微镜在悬浮液中观察,可以得到粒子分布的情况。
然后通过细胞破碎机或者砂磨机将分散后的原料充分乳化,得到纯净的硅溶胶液,使用过滤压滤将微细SiO2胶体拍打成一片硬盘。
五、干燥、研磨制备出的硅溶胶液通过喷雾干燥、真空干燥、半干式干燥来制备成粉末样。
硅溶胶精密铸造工艺
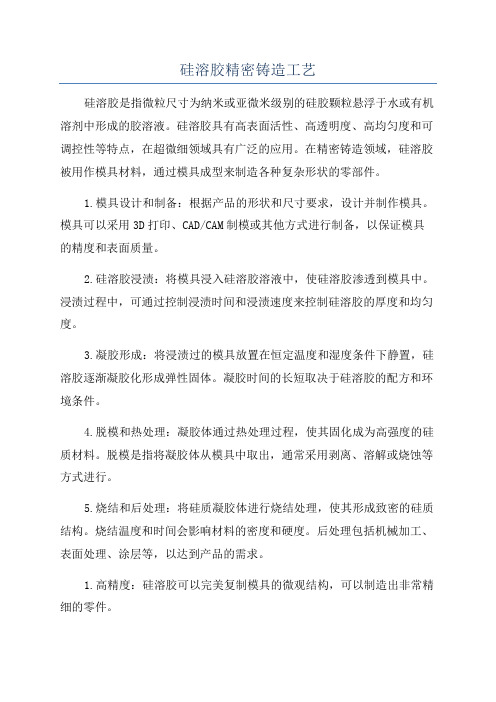
硅溶胶精密铸造工艺硅溶胶是指微粒尺寸为纳米或亚微米级别的硅胶颗粒悬浮于水或有机溶剂中形成的胶溶液。
硅溶胶具有高表面活性、高透明度、高均匀度和可调控性等特点,在超微细领域具有广泛的应用。
在精密铸造领域,硅溶胶被用作模具材料,通过模具成型来制造各种复杂形状的零部件。
1.模具设计和制备:根据产品的形状和尺寸要求,设计并制作模具。
模具可以采用3D打印、CAD/CAM制模或其他方式进行制备,以保证模具的精度和表面质量。
2.硅溶胶浸渍:将模具浸入硅溶胶溶液中,使硅溶胶渗透到模具中。
浸渍过程中,可通过控制浸渍时间和浸渍速度来控制硅溶胶的厚度和均匀度。
3.凝胶形成:将浸渍过的模具放置在恒定温度和湿度条件下静置,硅溶胶逐渐凝胶化形成弹性固体。
凝胶时间的长短取决于硅溶胶的配方和环境条件。
4.脱模和热处理:凝胶体通过热处理过程,使其固化成为高强度的硅质材料。
脱模是指将凝胶体从模具中取出,通常采用剥离、溶解或烧蚀等方式进行。
5.烧结和后处理:将硅质凝胶体进行烧结处理,使其形成致密的硅质结构。
烧结温度和时间会影响材料的密度和硬度。
后处理包括机械加工、表面处理、涂层等,以达到产品的需求。
1.高精度:硅溶胶可以完美复制模具的微观结构,可以制造出非常精细的零件。
2.高表面质量:硅溶胶的流动性好,可以填充模具的细小空隙,不会出现气孔和缺陷,从而得到高质量的表面。
3.复杂结构还原能力强:硅溶胶可以铸造出复杂的薄壁结构、镂空结构和内外复杂曲面结构,且能保持高精度。
4.可批量生产:硅溶胶工艺可以批量生产相同或不同的零件,提高生产效率。
5.环保且节能:硅溶胶精密铸造工艺无需模具,减少了材料浪费,省去了模具订制的时间和费用,减少了能源消耗。
尽管硅溶胶精密铸造工艺具有很多优点,但也存在一些限制,如硅溶胶成本较高,工艺流程复杂,对环境条件要求较高等。
但随着技术的不断发展和改进,这些限制将逐渐得到解决。
总之,硅溶胶精密铸造工艺以其优质的成品和高效的生产工艺,在各个领域得到了广泛应用。
硅溶胶快干工艺
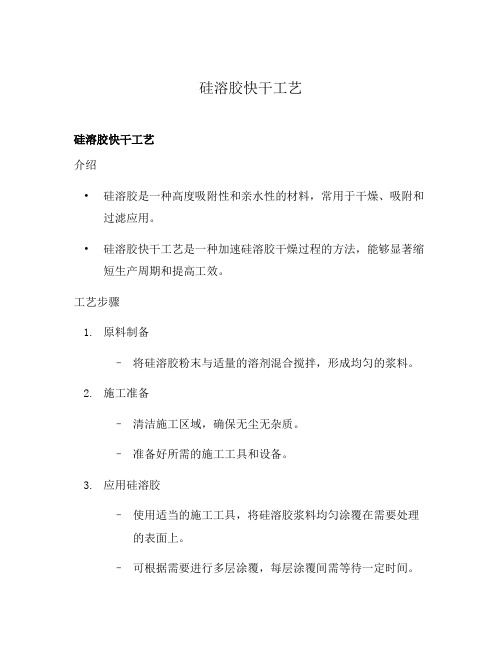
硅溶胶快干工艺硅溶胶快干工艺介绍•硅溶胶是一种高度吸附性和亲水性的材料,常用于干燥、吸附和过滤应用。
•硅溶胶快干工艺是一种加速硅溶胶干燥过程的方法,能够显著缩短生产周期和提高工效。
工艺步骤1.原料制备–将硅溶胶粉末与适量的溶剂混合搅拌,形成均匀的浆料。
2.施工准备–清洁施工区域,确保无尘无杂质。
–准备好所需的施工工具和设备。
3.应用硅溶胶–使用适当的施工工具,将硅溶胶浆料均匀涂覆在需要处理的表面上。
–可根据需要进行多层涂覆,每层涂覆间需等待一定时间。
4.快速干燥–使用专业的干燥设备对涂覆的硅溶胶进行快速干燥处理。
–快速干燥可以通过加热或利用特殊的干燥剂实现。
5.结果检测–对干燥后的硅溶胶进行检测,确保其质量和效果。
–可使用相关测试仪器进行物理机械性能测试,如吸附性能、孔隙率等。
6.后续处理–根据实际需求,对处理后的硅溶胶进行进一步加工、处理或应用。
快干工艺的优势•提高生产效率:快速干燥能够显著缩短硅溶胶的干燥周期,大幅提高生产效率。
•节约能源:快速干燥过程中,通过恰当的加热方式和干燥剂的使用,能够有效节约能源。
•保证质量:快干工艺可以有效减少干燥时间,避免了长时间暴露在环境中对硅溶胶质量造成的不良影响。
应用领域•干燥剂:硅溶胶快干工艺广泛应用于制造各类干燥剂,如食品干燥剂、药材干燥剂等。
•吸附剂:硅溶胶在快干工艺下制备的吸附材料被广泛应用于气体吸附、有机物吸附等领域。
•过滤材料:利用硅溶胶快干工艺制备的硅胶膜用于微滤、纳滤等过滤应用。
硅溶胶快干工艺的应用范围广泛,不仅提高了生产效率,同时也扩展了硅溶胶的应用领域。
这一工艺的出现为相关行业带来了巨大的便利,有望在未来得到进一步的发展和应用。
快干工艺的发展趋势随着科技的不断发展和工艺的不断创新,硅溶胶快干工艺也在不断进步和完善。
以下是一些快干工艺的发展趋势:1.环保型工艺:目前,一些较传统的快干工艺中可能存在一些有害物质的使用,对环境和人体健康造成潜在风险。
硅溶胶工艺铸铝件
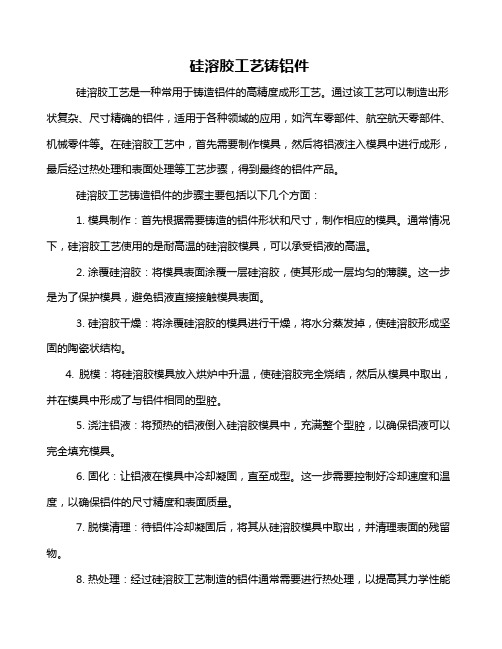
硅溶胶工艺铸铝件硅溶胶工艺是一种常用于铸造铝件的高精度成形工艺。
通过该工艺可以制造出形状复杂、尺寸精确的铝件,适用于各种领域的应用,如汽车零部件、航空航天零部件、机械零件等。
在硅溶胶工艺中,首先需要制作模具,然后将铝液注入模具中进行成形,最后经过热处理和表面处理等工艺步骤,得到最终的铝件产品。
硅溶胶工艺铸造铝件的步骤主要包括以下几个方面:1. 模具制作:首先根据需要铸造的铝件形状和尺寸,制作相应的模具。
通常情况下,硅溶胶工艺使用的是耐高温的硅溶胶模具,可以承受铝液的高温。
2. 涂覆硅溶胶:将模具表面涂覆一层硅溶胶,使其形成一层均匀的薄膜。
这一步是为了保护模具,避免铝液直接接触模具表面。
3. 硅溶胶干燥:将涂覆硅溶胶的模具进行干燥,将水分蒸发掉,使硅溶胶形成坚固的陶瓷状结构。
4. 脱模:将硅溶胶模具放入烘炉中升温,使硅溶胶完全烧结,然后从模具中取出,并在模具中形成了与铝件相同的型腔。
5. 浇注铝液:将预热的铝液倒入硅溶胶模具中,充满整个型腔,以确保铝液可以完全填充模具。
6. 固化:让铝液在模具中冷却凝固,直至成型。
这一步需要控制好冷却速度和温度,以确保铝件的尺寸精度和表面质量。
7. 脱模清理:待铝件冷却凝固后,将其从硅溶胶模具中取出,并清理表面的残留物。
8. 热处理:经过硅溶胶工艺制造的铝件通常需要进行热处理,以提高其力学性能和耐腐蚀性能。
9. 表面处理:最后对铝件进行表面处理,如喷涂、阳极氧化等工艺,以提高其表面硬度和耐磨性。
总的来说,硅溶胶工艺铸造铝件具有成形精度高、表面光洁度好、尺寸一致性高等优点,适用于制造需要高精度铝件的领域。
虽然硅溶胶工艺的成本相对较高,但是其成形效果和制造效率却是得到广泛认可的,因此在汽车、航空航天、机械等领域得到了广泛应用。
铸造硅溶胶工艺
铸造硅溶胶工艺硅溶胶铸造工艺,也称为熔模精密铸造,是一种高精度、高质量的铸造方法,广泛应用于不锈钢及其他合金的铸造领域。
以下是硅溶胶铸造工艺的主要步骤和特点:一、工艺流程1. 蜡模制作- 蜡料处理:包括静置脱水、搅拌蒸发脱水、静置去污等步骤,以确保蜡料的质量。
- 压制蜡模:在特定温度和压力下,将蜡料注入模具中,形成与铸件形状相同的蜡模。
2. 模组制作- 蜡模修整:对蜡模进行修整,确保表面平整光滑、无缺陷。
- 模组焊接:将多个蜡模焊接到浇口杯上,形成模组,便于后续操作。
3. 制壳- 沾浆:将模组浸入硅溶胶与石英砂制成的浆料中,形成初步型壳。
- 撒砂:在型壳上撒上石英砂,增强型壳的强度。
- 干燥:将型壳进行干燥,确保固化效果。
- 重复沾浆、撒砂和干燥过程,形成多层型壳。
4. 脱蜡- 使用蒸汽或热水将型壳中的蜡模熔掉,留下型腔。
5. 焙烧- 将型壳置于焙烧炉中,进行高温焙烧,以去除残留的水分和有机物,提高型壳的强度。
6. 浇注- 将熔融的金属液注入焙烧后的型壳中,待金属液冷却凝固后,形成铸件。
7. 清壳- 清理铸件表面的型壳,得到最终的铸件。
二、工艺特点1. 高精度:硅溶胶铸造工艺可以生产出尺寸精度和表面质量都非常高的铸件,其尺寸精度一般可达CT4-6级,表面粗糙度可达Ra1.6-3.2μm。
2. 少切削或无切削:由于铸件精度高,通常只需进行少量的机械加工或无需加工即可直接使用,大大节省了材料和加工成本。
3. 复杂形状:硅溶胶铸造工艺能够生产形状复杂、难以用其他方法加工的铸件,如喷气式发动机的叶片等。
4. 耐高温:硅溶胶铸造工艺能够生产高温合金铸件,这些铸件在高温环境下仍能保持良好的性能。
三、应用领域硅溶胶铸造工艺广泛应用于航空、汽车、机床、船舶、内燃机、气轮机、电讯仪器、武器、医疗器械以及工艺美术品等领域。
综上所述,硅溶胶铸造工艺是一种高精度、高质量的铸造方法,其工艺流程复杂但具有显著的优势和应用价值。
硅溶胶水玻璃复合工艺易出现的问题
一、对硅溶胶水玻璃复合工艺的介绍硅溶胶水玻璃复合工艺是一种常见的玻璃加工工艺,通过将硅溶胶涂覆在玻璃表面后再进行固化处理,形成一层具有耐磨、防水、耐腐蚀等特性的材料。
这种工艺广泛应用于建筑、玻璃工艺制品、家居用品等领域。
二、硅溶胶水玻璃复合工艺易出现的问题1. 硅溶胶选择不当:硅溶胶的选择直接影响着复合后的玻璃表面性能,如果选择不当,可能导致复合膜的附着力不足、耐磨性差等问题。
2. 复合厚度不均匀:在复合过程中,如果涂覆的硅溶胶层厚度不均匀,可能导致玻璃表面出现凹凸不平的情况,降低美观度和使用寿命。
3. 固化温度不足:硅溶胶水玻璃复合后需要进行固化处理,如果固化温度不足,可能导致复合膜的硬度不足,影响其耐磨、耐腐蚀性能。
4. 固化时间不足:固化时间不足会导致硅溶胶水玻璃复合层未完全固化,使得其性能不稳定,容易出现开裂、剥离等问题。
5. 操作流程不规范:在硅溶胶水玻璃复合工艺中,如果操作人员在操作过程中存在疏忽大意、操作流程不规范等问题,可能导致复合效果不理想。
三、解决硅溶胶水玻璃复合工艺易出现的问题的建议1. 选择合适的硅溶胶:在进行硅溶胶水玻璃复合工艺时,应根据玻璃的具体用途和要求选择合适的硅溶胶,保证复合后的性能满足需求。
2. 控制涂覆厚度:在复合过程中,要严格控制涂覆厚度,确保复合膜的厚度均匀,避免出现凹凸不平的情况。
3. 严格控制固化条件:在固化过程中,要严格控制固化温度和固化时间,确保复合膜能够充分固化,保证其性能稳定。
4. 规范操作流程:在进行硅溶胶水玻璃复合工艺时,要制定规范的操作流程,严格按照操作规程进行操作,避免出现疏忽大意导致的问题。
四、结语硅溶胶水玻璃复合工艺是一种常见的玻璃加工工艺,在实际应用中容易出现一些问题。
通过选择合适的硅溶胶、严格控制涂覆厚度、固化条件和规范操作流程,可以有效解决这些问题,保证复合后的玻璃具有良好的性能和稳定的质量。
在进行硅溶胶水玻璃复合工艺时,除了上述提到的问题和解决建议外,还有一些其他容易出现的问题需要引起注意。
硅溶胶工艺流程
硅溶胶工艺流程
《硅溶胶工艺流程》
硅溶胶是一种具有优异的耐热、耐寒、耐老化、耐水等特性的新型无机材料,广泛应用于建筑、汽车制造、电子、化工等领域。
硅溶胶制品的制作工艺流程如下:
1. 原料选材:选择优质的硅溶胶原料,保证产品的质量稳定和性能优良。
2. 混合成型:将硅溶胶原料与其他添加剂按比例混合,经过搅拌、分散等工艺过程,形成均匀的浆料。
3. 成型制备:根据产品的不同形状和规格,采用注塑、浇铸、压延等方式将浆料进行成型制备。
4. 原型固化:经过成型制备后,将原型进行固化处理,使得产品在表面和内部均能得到充分的固化和稳定,确保产品的质量和性能。
5. 烘干处理:对固化的硅溶胶制品进行烘干处理,除去水分和其它挥发物,提高产品的稳定性和耐久性。
6. 表面处理:硅溶胶制品经过烘干后,进行表面处理,如喷涂、涂覆、抛光等工艺,使其外观光滑、清洁。
7. 检测包装:对成品进行严格的质量检测,确保产品符合相关
标准和要求,然后进行包装和运输。
通过上述工艺流程,硅溶胶制品能够保证其质量稳定、性能优良,广泛应用于各个领域,为各行各业提供高品质的产品和解决方案。
硅溶胶生产工艺
硅溶胶生产工艺硅溶胶是由水合硅酸与硅酸盐溶液经过特殊工艺处理而成的一种无机胶体材料。
它具有高渗透性、高韧性、高孔率等优点,广泛应用于电子、建筑、化工、冶金等领域。
下面将介绍硅溶胶的生产工艺。
硅溶胶的生产工艺主要分为三个步骤:溶胶制备、凝胶形成和干燥处理。
首先是溶胶制备。
一般采用的原料是硅酸钠和硅酸铵。
这两种物质在水中溶解后,可以形成硅酸根离子和氨气。
将硅酸铵和硅酸钠逐渐混合,控制pH值在9-10之间,生成溶胶液。
溶胶液中包含不同粒径的团聚体,它们通过调节溶液中的温度和浓度来控制。
接下来是凝胶形成。
将溶胶液转移到高温反应釜中,在一段时间内保持一定的温度和压力。
在这个过程中,溶胶中的硅酸根离子和氨气逐渐结合,形成硅氧键,产生凝胶。
凝胶的形成时间与温度和压力相关,通过调节这些参数可以控制凝胶的成型速度和形态结构。
最后是干燥处理。
将凝胶转移到干燥室中,通过控制温度和湿度,将凝胶中的水分蒸发出去。
干燥的过程通常分为自然干燥和热空气干燥两种方法。
自然干燥是将凝胶放置在通风良好的环境中,让水分通过自然蒸发来干燥。
热空气干燥则是通过加热和通风的方式来加快水分的蒸发速度。
干燥的时间和温度要根据产品的要求和材料的特性进行调整,以保证获得理想的硅溶胶产品。
在硅溶胶的生产过程中,需要注意以下几个问题。
首先是原料的选择和配比。
不同的硅酸钠和硅酸铵的比例会影响溶胶的粒径和稳定性。
其次是溶胶的混合和成型过程。
需要利用搅拌设备来保持溶胶的均匀性,并采取适当的温度和压力控制凝胶的形成时间和结构。
最后是干燥过程的控制。
干燥温度和湿度的变化会直接影响溶胶中水分的蒸发速度和产品的孔结构。
总结起来,硅溶胶的生产工艺包括溶胶制备、凝胶形成和干燥处理三个步骤。
在每个步骤中,都需要严格控制温度、湿度和时间等因素,以获得具有理想性能的硅溶胶产品。
此外,根据不同的应用领域和产品要求,还需要进行相关的后续处理,如表面改性、印刷加工等,以满足不同客户的需求。