生产线布局(超详细)
汽车件生产线布局规划

Hl汽车覆盖件冲玉生产工艺冲也件斥垛、淸机,證抽-恆料剤中.二洙冲堤顷形.取怜唸验.萝k 工空辭具开落斜线冲压门功化生开卷、洁洗、檢凸.勺汕溥料.w图汽车覆盖件冲压生产工艺流程汽车覆盖件冲压生产车间的规划与设计概述覆盖件冲压生产具有规模化、成批生产、多品种化的特点;冲压车间、冲压设备和冲压生产线一次性投资大,但适应产品发展变化的通用性较强,产品换型只需模具变化,设备可以通用。
冲压生产是一项规模效益递增型的产业,冲压车间规划要立足于长远和未来发展。
对于整车厂来说,覆盖件冲压生产车间的规划与设计显得尤为重要。
覆盖件冲压生产工艺流程卷料T 开卷剪切或落料(包括开卷、清洗、校平、剪切或落料、堆垛)-冲压成形(包括拆垛、清洗、涂油、板料对中、上料、冲压成形、取件)-检验-装入工位器具-入库,如图所示。
主要规划内容汽车覆盖件冲压车间规划的主要内容包括冲压车间工艺设计分析、生产设备及生产线选择、辅助设备(线)选择、总图设计、车间平面布置及功能区域设计、厂房设计等。
规划原则汽车覆盖件冲压车间规划是汽车整车厂四大工艺工厂规划的重要内容之一,应遵循“精益化”的设计原则,高质量、高效率、低投入。
采用经济、合理、实用、与生产纲领和生产批量相适应的先进技术,采用高性价比的工艺装备。
规划前提确定产品类型:轿车或卡车大中型覆盖件和关键梁类结构件;生产纲领:以万辆年生产纲领为例;辆天;工作制度:天年,班天,;产品种类及内外制冲压件确定:整车厂一般以生产白车身大型内外覆盖件及关键梁类结构件为主,此类件为内制件。
其它件由外部供应商协作生产,此类件为外制件。
内制件的确定原则()车身的核心零部件;()高附加值的零部件;()车身外表面覆盖件;()堆垛、运输较困难的大中型内覆盖件;()尺寸精度要求高的关键梁类结构件。
覆盖件冲压车间工艺设计分析以整车厂只生产内制件为设计前提,规划整车厂的冲压车间。
汽车覆盖件冲压生产线分类及主要生产零件)单机联线冲压生产线分类,见表。
生产线布局(超详细)
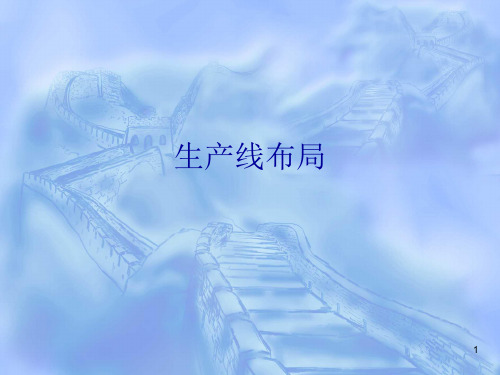
= 0.007 分钟/产品
换句话说,每分钟生产140单位的产品。
1/30/2019 40
产品原则布局
4.进行作业活动分配(作业活动分配到各工作站) 5.向工作站分配作业(作业活动在工作站内分配) 6.评估装配线平衡后的效率 E=T/(Na × Ct)
E——装配线平衡效率 T——完成作业所需的时间总量 Na——实际工作站数 Ct——生产节拍
就生产而言E是怎样的 数值较好?
7.如果不理想,重复第4步骤
1/30/2019 41
产品原则布局
作业 时间(S) 45 11 描述 安装后轮支架,拧紧四个螺 母 插入后轴 作业前提条件 —— A
案例 一玩具厂的玩具 车在流水线上 作业,每天需 生产500辆, 每天生产时间 为420分钟, 生产步骤及时 间如左表:
3 铸造 4 缝纫
5 小型玩具 转配线 6 大型玩具 转配线
7 喷漆 8 机械装配 线
20
工艺原则布局
次数
车 间 之 间 的 流 动 表
1/30/2019
1 1 2 3 4 5 6 7 8
2 3 175 50 0
4 0 100 17
5 30 75 88 20
6 200 90 125 5 0
7 20 80 99 0 180 347
6σ=?
4
6σ标准
PPM等于 多少?
σ
PPM 308,537 66,807 6,210 233 3.4
缺陷减少5倍
2 3 4 5 6
缺陷减少11倍
缺陷减少26倍
缺陷减少68倍
5
鉴别七大浪费
一、生产产生的不良引起的浪费
任何产品的不良都是浪费的一个主要来源。
工厂生产车间流水线布局的七种方式

⼯⼚⽣产车间流⽔线布局的七种⽅式单元装配线的理想布局之⼀是花瓣型布局1.流畅原则:各⼯序的有机结合,相关联⼯序集中放置原则,流⽔化布局原则。
2.最短距离原则:尽量减少搬运,流程不可以交叉,直线运⾏。
3.平衡原则:⼯站之间资源配置,速率配置尽量平衡.4.固定循环原则:尽量减少诸如搬运,传递这种Non-Value Added的活动。
5.经济产量原则:适应最⼩批量⽣产的情形,尽可能利⽤空间,减少地⾯放置原则6.柔韧性的原则:对未来变化具有充分应变⼒,⽅案有弹性。
如果是⼩批量多种类的产品,优先考虑“U”型线布局、环型布局等7.防错的原则:⽣产布局要尽可能充分的考虑这项原则,第⼀步先从硬件布局上预防错误,减少⽣产上的损失!1逆时针排布逆时针排布,主要⽬的是希望员⼯能够采⽤⼀⼈完结作业⽅式、能够实现⼀⼈多机。
⼀⼈完结与⼀⼈多机要求⼀个员⼯从头做到尾,因此员⼯是动态的,称之为“巡回作业”。
⼤部分作业员是右撇⼦,因此如果逆时针排布的话,当员⼯进⾏下⼀道加⼯作业时,⼯装夹具或者零部件在左侧,员⼯作业并不⽅便,这也正是逆时针的⽬的——员⼯就会⾛到下⼀⼯位——巡回的⽬的也就达到了。
2出⼊⼝⼀致出⼊⼝⼀致,是指原材料⼊⼝和成品出⼝在⼀起。
为什么要求出⼊⼝⼀致呢?⾸先,有利于减少空⼿浪费。
假设出⼊⼝不⼀致,作业员采⽤巡回作业,那么当⼀件产品⽣产完了,要去重新取⼀件原材料加⼯的话,作业员就会空⼿(⼿上没有材料可以⽣产)从成品产出⼝⾛到原材料投⼊⼝,这段时间是浪费。
如果出⼊⼝⼀致的话,作业员⽴刻就可以取到新的原材料进⾏加⼯,从⽽避免了空⼿浪费。
第⼆,有利于⽣产线平衡。
由于出⼊⼝⼀致,布局必然呈现类似“U”的形状,这使得各⼯序⾮常接近,从⽽为⼀个⼈同时操作多道⼯序提供了可能,这就提⾼了⼯序分配的灵活性,从⽽取得更⾼的⽣产线平衡率。
3避免孤岛型布局孤岛型布局把⽣产线分割成⼀个个单独的⼯作单元,其缺陷在于单元与单元之间互相隔离,⽆法互相协助。
生产线布局(超详细)全解
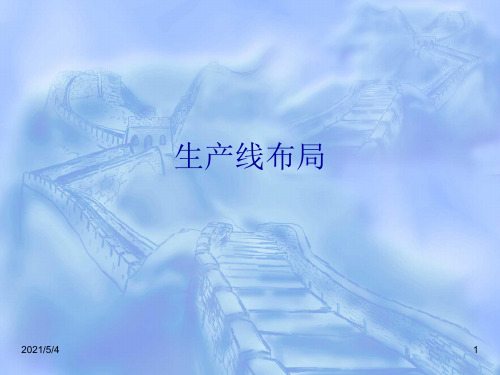
2021/5/4
44
产品原则布局
▪ 第四步:选择作业分配 工作
(以后续作业数量多少安 排作业)
2021/5/4
作业 A
B/D C/E F/G/H/I
J K
后续作业数量 6 5 4 2 1 0
45
产品原则布局
▪ 第五步对工作站安排作业,工作站周期:50.4秒
工作站 作业 时间(S)
工作站1 A
45
二、运输中的浪费
具有代表性的是,有些项目总是无工作性质地移动,时间 花费了在路途中,这是浪费。
2021/5/4
8
鉴别七大浪费
三、来自库存的浪费
库存代表着某些项目正等待某些事情的发生,这里的浪 费表现在:和保存着这些项目来等待有关联的成本,对 这些项目无增值而导致时间的损失。
安全库存是为了保证生产部门的正常运作和弥补不良品 的损失而存在的,但是安全库存不能够超出它们的正常 需要。
▪ 问:
• 金额如何计算出来的? • 组合布局方法或排列有多少种? • 如何排列的才是有效的?
2021/5/4
23
工艺原则布局
▪ 成本矩阵——方案一,总成本合计3474
11 2 3 4 5 6 7 82021/5/4
2
3
175 50
0
4
5
6
7
0
60 400 60
100 150 180 240
17 88 125 198
▪ 使用范围:
• 批量小 • 体积大
▪ 布局特点
• 以产品为中心 • 不考虑物流成本和复杂程度
2021/5/4
18
工艺原则布局
▪ 定义:
• 将相似的设备或功能集中放在一起的布局方式 • 也称车间布局,如车床车间
高效工厂生产线布局设计
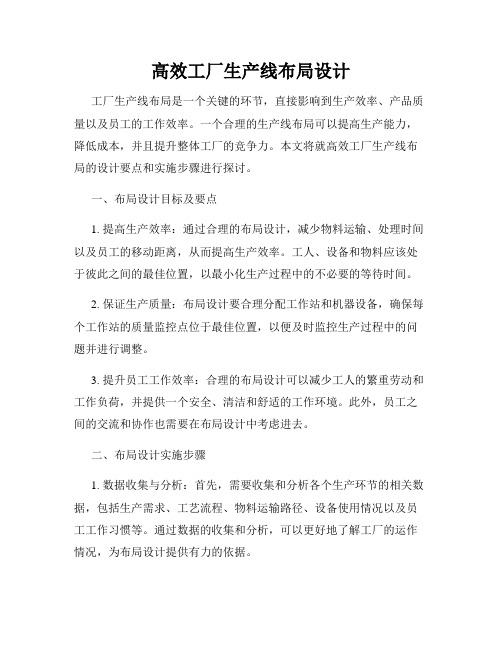
高效工厂生产线布局设计工厂生产线布局是一个关键的环节,直接影响到生产效率、产品质量以及员工的工作效率。
一个合理的生产线布局可以提高生产能力,降低成本,并且提升整体工厂的竞争力。
本文将就高效工厂生产线布局的设计要点和实施步骤进行探讨。
一、布局设计目标及要点1. 提高生产效率:通过合理的布局设计,减少物料运输、处理时间以及员工的移动距离,从而提高生产效率。
工人、设备和物料应该处于彼此之间的最佳位置,以最小化生产过程中的不必要的等待时间。
2. 保证生产质量:布局设计要合理分配工作站和机器设备,确保每个工作站的质量监控点位于最佳位置,以便及时监控生产过程中的问题并进行调整。
3. 提升员工工作效率:合理的布局设计可以减少工人的繁重劳动和工作负荷,并提供一个安全、清洁和舒适的工作环境。
此外,员工之间的交流和协作也需要在布局设计中考虑进去。
二、布局设计实施步骤1. 数据收集与分析:首先,需要收集和分析各个生产环节的相关数据,包括生产需求、工艺流程、物料运输路径、设备使用情况以及员工工作习惯等。
通过数据的收集和分析,可以更好地了解工厂的运作情况,为布局设计提供有力的依据。
2. 确定产品流程:在设计布局之前,需要明确产品的制造流程和生产线上的工序。
这有助于确定每个阶段的物料输入和输出,为后续的布局设计做好准备。
3. 制定布局方案:根据数据分析和产品流程,可以制定不同的布局方案。
应该综合考虑物料运输路径、设备配置、工作站设置以及人员安排等因素,选择最佳的布局方案。
4. 评估与调整:制定布局方案后,需要进行评估和调整。
可以借助计算机仿真软件对布局进行模拟,以评估生产线的效率和工作人员的负荷。
根据评估结果,对布局进行调整和优化。
5. 实施和监控:在确定最佳布局方案后,需要开始实施并监控生产线的运行情况。
监控应包括生产效率、产品质量和员工满意度等指标的跟踪和监测。
三、布局优化的策略1. 流程重组:通过重新组织和优化生产线上的工序,减少物料运输和处理时间,提升生产效率。
生产线布局(超详细)_图文
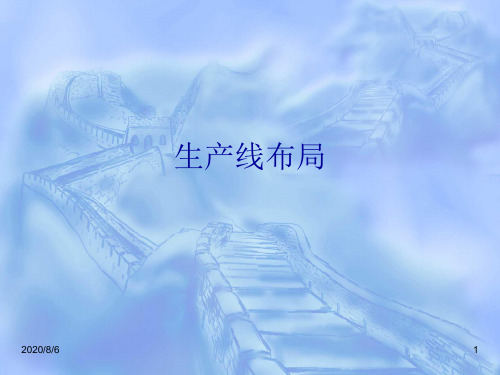
次数
1 1 2 3 4 5 6 7 8
23 175 50
0
45 0 30 100 75 17 88
20
678 200 20 25 90 80 90 125 99 180 5 0 25 0 180 187
347 103 7
21
▪ 玩具厂各车间年物流成本示意图
2020/8/6
22
工艺原则布局
2020/8/6
12
鉴别七大浪费
六、来自工序不当的浪费
工作本身产生的浪费,当机器不正常运作而使操作人员 需要花额外时间,或当操作人员出于习惯或花了过多的 时间使清洁工作超过了规格的要求。
多余的检查也是过程浪费的另一个表现形式。
2020/8/6
13
鉴别七大浪费
七、不需要的动作的浪费
人们在工作设置中经常将工作中的动作搞混乱,实际做的动 作和工作要求的动作往往是不同的。
2020/8/6
15
生产线布局类别
▪ 定位原则布局 ▪ 工艺原则布局 ▪ 产品原则布局 ▪ 成组技术(单元式)布局
2020/8/6
16
定位原则布局
▪ 定义:
• 将原材料和设备按照使用次序和移动的难易程度 在产品的四周进行生产
▪ 起源
• 19世纪初亨利福特的汽车装配线
2020/8/6
17
定位原则布局
2020/8/6
9
不合格品
率高
库
机器故障率高
调整时间太长
存
水
设备能力不平衡
缺勤率高
备件供应不及时
平
采购周期太长 技术服务 工人技能差 后勤服务差
不及时
图 17-1 库存水平高掩盖的管理问题多
生产线布局(超详细)PPT课件
产品特性
产品的工艺要求、生产流程、 物料特性等对生产线布局有直 接影响。
人力资源
员工的技能、经验和工作习惯 对生产线布局的效率和效果有 重要影响。
环境因素
生产环境的要求、法律法规、 环保要求等对生产线布局有制 约作用。
02
生产线布局的类型
直线式布局
总结词
简单明了,便于管理,适合小批量生产
详细描述
布局评估的方法
01
02
03
04
生产流程分析
通过分析生产流程,评估生产 线布局的合理性,找出瓶颈环
节和浪费。
设备利用率评估
计算设备的平均利用率,判断 是否存在设备闲置或使用不足
的情况。
空间利用率评估
评估生产线布局的空间利用率 ,判断是否充分利用了生产空
间。
物流效率评估
分析生产线上的物流效率,判 断是否存在物料搬运距离过长
收集生产线布局相关 的数据,包括设备布 局、设备参数、生产 流程、物流路径等。
分析问题
根据收集的数据,分 析生产线布局存在的 问题和瓶颈环节。
制定方案
根据问题分析结果, 制定相应的布局调整 方案。
实施调整
按照制定的方案,逐 步实施生产线布局的 调整。
效果评估
在布局调整后,对生 产线的运行情况进行 评估,判断调整效果。
详细描述
该电子产品制造企业采用精益的生产线布局,以提高生产效率和降低成本。生产线布局 高效,各工序之间衔接紧密,以减少浪费。同时,大量采用自动
总结词
安全、卫生、人性化
VS
详细描述
该食品加工企业注重生产线的安全性、卫 生和人性化设计。生产线布局合理,保证 清洁度和卫生标准。同时,充分考虑员工 操作的舒适性和安全性,提高生产效率和 工作质量。
生产岗位的生产线排布与工位布置要求
缩短运输距离
将相关设备和物料放置在 相邻位置,减少员工在取 用物料和设备时的行走距 离,提高作业效率。
合理安排作业空间
根据作业需求合理安排作 业空间,避免空间浪费和 拥挤,提高员工工作效率 。
确保操作安全
设备安全
安全防护
确保设备正常运行,及时维护和保养 ,避免因设备故障导致的安全事故。
个人防护
为员工提供合适的个人 防护用品,如耳塞、耳 罩等,降低噪音和振动 对员工的影响。
现场5S管理推进
01
整理(Seiri)
02
整顿(Seiton)
03 清扫(Seiso)
04
清洁(Seiketsu)
素养(S场整洁。
对物品进行分类、标识和定位,方便取用和归位。
定期清扫工作区域,保持环境清洁。 维持整理、整顿和清扫的成果,形成制度化、规范化的管理 。 提高员工素质,养成遵守规章制度和良好工作习惯的习惯。
06
生产线排布与工位布置实施计划
项目组成员分工及职责明确
项目经理
负责整体项目规划、进度控制、资源协调及风险 管理。
工艺工程师
负责生产线工艺流程设计、工位布置及作业标准 制定。
设备工程师
负责生产线设备选型、布局规划及设备维护保养 。
生产人员
参与生产线试运行,反馈实际生产过程中的问题 ,协助优化改进。
实施进度安排及关键节点控制
01 项目启动阶段 明确项目目标、范围及实施计划,完成项目组成员分 工。
02 生产线规划阶段 完成生产线工艺流程设计、设备选型及布局规划。
03
工位布置阶段
在必要的位置设置安全防护装置和警 示标识,提醒员工注意安全,防止意 外事故发生。
机械加工生产线的总体布局设计
机械加工生产线的总体布局设计
在进行机械加工生产线总体布局设计时,需确定工件的输送方式和装置,合理配置毛坯、半成品和成品的存放面积和存放地点,确定生产线上使用各种装备的布置形式和连接方式。
一、生产线的工件输送装置
工件输送装置是生产线中的一个重要组成部分,它将被加工工件从一个工序(工位)传送到下一工序(工位)。
为保证生产线按规定节拍连续工作供应条件,并从结构上把生产线上众多加工设备联接成为一个整体。
生产线的总体布局和结构形式往往取决于工件的输送方式。
常用工件输送装置的类型:1)输料槽和输料道;2)步伐式输送装置;3)转位装置。
二、生产线总体布局形式
机械加工生产线总体布局形式多种多样,它由生产类型、工件结构形式、工件输送方式、车间条件、工艺过程等因素打算。
生产线总体布局形式:1)直接输送方式;2)带随行夹具方式;3)悬挂输送方式。
生产线的连接方式:1)刚性连接;2)柔性连接。
三、生产线总体联系尺寸图
生产线总体联系尺寸图用于确定生产线上机床之间、机床与其他装备、以及其他装备之间的尺寸联系,是设计生产线各部件的依据,
也是检查各部件相互关系的重要资料。
当选用的机床和其他装备的形式和数量确定之后,依据拟定的布局就可绘制生产线总体联系尺寸图。
四、机械加工生产线其他装备的选择与配置
1)输送带驱动装置的布置;2)小螺纹孔加工检查装置;3)精加工工序的自动测量装置;4)装卸工位掌握机构;5)毛坯检查装置;6)液压站、电气柜及管路布置;7)桥梯、操纵台和工具台的布置;8)清洗设备布置。
生产线布局指南
生产线布局指南生产线布局指南1. 引言在制造业中,生产线布局的设计是一项关键任务。
正确的生产线布局可以提高生产效率、减少浪费和成本,并优化整个生产过程。
本文将为您介绍一份全面的生产线布局指南,帮助您了解如何设计一个高效的生产线布局。
2. 什么是生产线布局生产线布局是指将各个生产环节按照合理的顺序和空间位置进行安排,以最小化材料、能源和劳动力的浪费,并达到高产量和高质量的生产目标。
一个好的生产线布局应该充分考虑产品的工艺流程、设备的布置和人员的作业安排。
3. 生产线布局的重要性一个合理的生产线布局可以带来许多好处。
它可以减少作业时间和运输时间,提高产品的流动性,从而减少不必要的等待时间和库存。
通过将相关设备和工作站靠近,生产线布局可以最大限度地减少劳动力的移动和交通,提高工作效率。
一个优化的生产线布局会促进团队合作和沟通,提高整体生产效率和质量。
4. 生产线布局的基本原则为了设计一个优化的生产线布局,以下是几个基本的原则需要考虑:4.1 流程分析:首先要了解产品的工艺流程,确定每个环节所需的时间、资源和设备。
这将有助于确定合适的工作站数量和位置,以及设备和材料的流动路径。
4.2 空间利用率:考虑到生产场地的有限性,要最大限度地利用可用的空间。
确保每个工作站和设备之间有充足的空间,避免拥挤和交通阻塞。
4.3 关联性:将相关的工作站和设备放在一起,以便减少运输时间和劳动力的移动。
将需要经常协作的工作站放在相邻的位置,以提高沟通和协作效率。
4.4 人性化设计:考虑到员工的舒适和安全,设计工作站的高度、角度和布局。
确保工作站设有必要的人机工程学元素,以减少员工的疲劳和错误。
5. 生产线布局的类型在实际的生产线布局中,有几种常见的类型:5.1 直线式布局:产品按照顺序在一条直线上进行加工。
这种布局适用于生产规模较小、产品变化较少的情况。
5.2 U型布局:工作站围绕一个中央区域形成一个U形,以便员工更方便地移动和协作。
- 1、下载文档前请自行甄别文档内容的完整性,平台不提供额外的编辑、内容补充、找答案等附加服务。
- 2、"仅部分预览"的文档,不可在线预览部分如存在完整性等问题,可反馈申请退款(可完整预览的文档不适用该条件!)。
- 3、如文档侵犯您的权益,请联系客服反馈,我们会尽快为您处理(人工客服工作时间:9:00-18:30)。
安装前轴车把手,拧紧螺丝
9
上紧全部螺丝
195
作业前提条件 ——
A B —— D C
C
E
E F,G,H,L
42
产品原则布局
解题 第一步:画出流程图
A
B
C
G
D
E
F
I
J
K
H
11/6/2019
43
产品原则布局
第二步:计算工作站周期(节拍) Ct=每天的工作时间/每天的产量 =60秒×420分钟/500辆
1. 采用了看板管理,拉动生产方式 2. 车间布局U型布局; 3. 不同类型的机器摆放在一块; 4. 实现了单件流的生产; 5. 机器小型化 ; 6. 工序中间很少甚至没有库存; 7. 实现了作业标准化; 8. 对工人实行了多技能培训; 9. 具有完善的作业改善活动制度
11/6/2019
3
看谁摘的果子最多!
• 大批量、同质性生产 • 产品需求足够稳定 • 流水作业
11/6/2019
38
产品原则布局
生产平衡规划
• 作业工序和生产线节拍趋于一致,使流动速度最快
步骤:
1. 用流程表明确作业先后关系
就生产而言Ct越大越
2. 工作站(工序)周期——生产节拍 好?还是越小越好?
Ct=每天的工作时间/每天的产量
1 1 2 3
的4
流5
动6
表7
8 11/6/2019
23 175 50
0
45 0 30 100 75 17 88
20
678 200 20 25 90 80 90 125 99 180 5 0 25 0 180 187
347 103 7
21
玩具厂各车间年物流成本示意图
11/6/2019
22
工艺原则布局
=25200/500 =50.4秒/辆 第三步:计算理论工作站数 Nt =T/ Ct=195秒/50.4秒=3.87≈4站
11/6/2019
44
产品原则布局
第四步:选择作业分配 工作
(以后续作业数量多少安 排作业)
11/6/2019
作业 A
B/D C/E F/G/H/I
J K
后续作业数量 6 5 4 2 1 0
11/6/2019
9
²» ºÏ ¸ñ ·Æ
ÂÊ ¸ß
â¿
»ú ÷Æ ¹Ê ÕÏ ÂÊ ¸ß
µ÷Õû ʱ¼ä Ì« ³¤
æ´
®Ë
Éè ±¸ ÄÜ Á¦ ²» ƽ ºâ
ȱÇÚ ÂÊ ¸ß
±¸ ¼þ ¹© Ó¦ ²» ¼°Ê±
½Æ
²É ¹º ÖÜ ÆÚ Ì« ³¤ ¼ Êõ ·þ Îñ
¹¤ÈË ¼ ÄÜ ²î ºó ÇÚ ·þ Îñ ²î
11/6/2019
19
工艺原则布局
案例:玩具厂有8个车间,采用物料集中搬 运方式,每次只能搬运一个周转箱,车间之 间运输成本为1元,每隔一个车间增加1元
1 收发部
3 铸造
5
小型玩具 转配线
7 喷漆
2
4
6
8
塑模与冲 缝纫 大型玩具 机械装配
压
转配线
线
11/6/2019
20
工艺原则布局
次数
车 间 之 间
100
工艺原则布局
权重代码 密切程度
A
绝对必要
E
特别重要
I
重要
O
普通的
U
不重要的
X
不予考虑的
11/6/2019
线代号
29
工艺原则布局
医院相关图
1
3
5
2
4
6
11/6/2019
30
工艺原则布局
医院总体合理布局图
1
4
65
2
3
11/6/2019
31
工艺原则布局
布局方法 设部门或工艺有n个
无论什么原因,没有直接的需求就生产的产品都是浪费。
如果有些项目的需求没有了,那这时,这些项目将不得不被放弃或者 降价处理。
其间,它们储存在仓库里,造成成本的增加和库存的浪费。
11/6/2019
11
鉴别七大浪费
五、来自时间等待的浪费
时间等待的浪费是很容易被鉴别的,它有很多的表现形态, 包括有:
• 为定单而等待 • 为批准而等待 • 为零部件而等待 • 为物料而等待 • 为前面过程中叙述的项目而等待 • 为设备的维修而等待
布局方案=n!
11/6/2019
32
例:最初按工艺原则的布置
4
6
7
9
5
2
1
3
8
10
12
11
A
B
C 原材料
11/6/2019
33
零部件移动路线矩阵
机器
件
1 2 3 4 5 6 7 8 9 10 11 12
A
xx
x
x
x
B
x
x
x
C
x
x
x
D
xx
x
x
x
E
xx
x
F
x
x
x
G
x
x
x
x
H
x
xx
11/6/2019
34
问:
• 金额如何计算出来的? • 组合布局方法或排列有多少种? • 如何排列的才是有效的?
11/6/2019
23
工艺原则布局
成本矩阵——方案一,总成本合计3474
11 2 3 4 5 6 7 811/6/2019
2
3
175 50
0
4
5
6
7
0
60 400 60
100 150 180 240
17 88 125 198
7
5
B
36
产品原则布局
定义:
• 根据产品制造的步骤来安排设备或工作过程的方式 • 产品的加工(生产)过程的路径是直线型 • 也称装配线
布局特点:
• 物料的直线运动 • 连续的重复性生产 • 标准化、专业化生产 • 原材料、半成品、成品一致性高
11/6/2019
37
产品原则布局
适用范围
6
产生更严重的成本连锁反应……
更多的
“一人错误百人忙” 防火成本 的成本暴增曲线
更多的 救火成本
更多的 返工成本
正常成本
11/6/2019
救火、防火、多余监 督、过度控制、多余 检验、投诉处理、退 货维修、商誉损失、 顾客流失等效应连锁 扩大成本! 重工、返修、报废成本
日常管销/制造成本
7
鉴别七大浪费
6.评估装配线平衡后的效率
E=T/(Na × Ct)
E——装配线平衡效率
T——完成作业所需的时间总量
Na——实际工作站数 Ct——生产节拍
7.如果不理想,重复第4步骤
就生产而言E是怎样的 数值较好?
11/6/2019
41
产品原则布局
案例 一玩具厂的玩具
车在流水线上 作业,每天需 生产500辆, 每天生产时间 为420分钟, 生产步骤及时 间如左表:
二、运输中的浪费
具有代表性的是,有些项目总是无工作性质地移动,时间 花费了在路途中,这是浪费。
11/6/2019
8
鉴别七大浪费
三、来自库存的浪费
库存代表着某些项目正等待某些事情的发生,这里的浪 费表现在:和保存着这些项目来等待有关联的成本,对 这些项目无增值而导致时间的损失。
安全库存是为了保证生产部门的正常运作和弥补不良品 的损失而存在的,但是安全库存不能够超出它们的正常 需要。
使用范围:
• 批量小 • 体积大
布局特点
• 以产品为中心 • 不考虑物流成本和复杂程度
11/6/2019
18
工艺原则布局
定义:
• 将相似的设备或功能集中放在一起的布局方式 • 也称车间布局,如车床车间
使用范围
• 生产设备密集型 • 设备专业性 • 自动化程度高 • 资本密集型 • 产品重量轻
11/6/2019
12
鉴别七大浪费
六、来自工序不当的浪费
工作本身产生的浪费,当机器不正常运作而使操作人员 需要花额外时间,或当操作人员出于习惯或花了过多的 时间使清洁工作超过了规格的要求。
多余的检查也是过程浪费的另一个表现形式。
11/6/2019
13
鉴别七大浪费
七、不需要的动作的浪费
人们在工作设置中经常将工作中的动作搞混乱,实际做的动 作和工作要求的动作往往是不同的。
调整的零部件移动路线矩阵
部件 A D F C G B H E
机器
1 2 4 8 10 3 6 9 5 7 11 12
xxxxx
xxxxx
x
xx
xxx
xxx
x
xx
x
xxx
x
x
x
11/6/2019
35
按成组技术布置的方案
8
10
9
4 单元1
单元 2 6
2原Βιβλιοθήκη 料11/6/20191
3
A
C
12
11 单元 3
11/6/2019
作业 A
B C D E F
G
H
L
J K 总计
时间(S)
描述
45
安装后轮支架,拧紧四个螺
母
11
插入后轴
9
拧紧后轴支架螺栓
50