注塑机比例流量、压力的调校
台中注塑机一二三四段调机技术

台中注塑机一二三四段调机技术注塑机一二三四段调机技术注塑机调机方法与技巧:注塑机又名注射成型机或注射机,很多工厂叫啤机(piji),注塑产品叫啤件。
它是将热塑性塑料或热固性料利用塑料成型模具制成各种形状的塑料制品的主要成型设备。
注塑机按照注射装置和锁模装置的排列方式,可分为立式、卧式和立卧复合式。
一、注塑机一二三四段调机技术注塑机1234段的调机技术一般,一段温度设置在90一100度,二段温度设置150一170多,三段温度设置230一270多,四段的温度设置120一150度。
二、注塑机调机方法与技巧1、注塑机模貝全透明法我们在调机的情况下,经常会想:假如模贝是全透明的就好了!那样就可认清熔胶的所有充型全过程,见到缺点是怎样造成的,也是什么时候造成的。
在我们设计方案出某一射胶加工工艺时,射胶全过程具体是不是依照构想的规定去进行,起始点位置设得对吗这些一系列难题,都期待可以见到。
可是要想直接看获得熔胶充型全过程沒有新科技机器设备是不太可能的,可是间接性的方式却有一个,便是大家将射胶時间一秒一秒提升,每提升一秒啤一啤,随后将每一啤未走齐的啤件按顺序排列起來,那样就可以很清晰地见到熔胶的充型全过程,直至填满凹模截止。
假如在重要的位置想再看得细心一点,就在这一重要位置每一只提升0.一秒。
假如只想看看起级点准不精确就更为简易。
只必须将后边一级的压力和速率所有调至0,你也就能够见到起级点的位置在哪儿,而不用应用一秒一秒提升的方式来渐渐地观察。
在这里要提示留意的是,因为射胶终止以后熔胶还会继续有一点惯性力澎涨全过程,因此具体脱模的件与终止射胶时的那一瞬间的样子会出现一点进出。
具体起级点应当比见到的件要早一些。
2、注塑机精准定位射胶法说白了“精准定位射胶”法,是大家常见的迅速射胶转下属慢速度射胶演化而成的一种调机技巧。
此方法是将后一级的慢速度和压力所有调节为零,促使前一级的迅速射胶到某一设置起级位置时马上终止,让凹模内存储的压力当然释放出来,根据它来作最终丰富凹模和保压。
注塑机的调校运行与保养
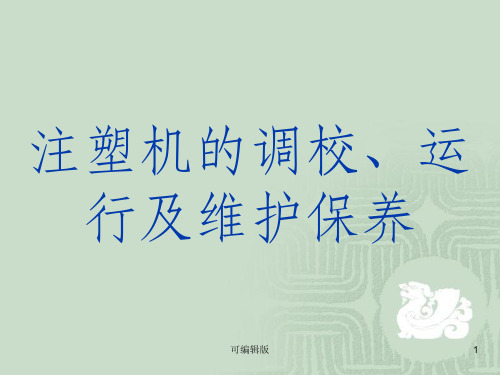
可编辑版
22
4 全自动操作
① 注塑机可以连续周期性生产。若设备测出故障或不正 常情况,注塑机会停止生产。由于停止引起注塑周期 超时,注塑机会发出警报(警号灯闪烁及警报发出鸣 响)。
② 按键选择全自动方式,其中有全自动时间方式和电眼 方式。
③ 关闭安全门,注塑机运作会自动产生由锁模及射胶至 开模及顶针等一连串动作。完成一个周期后,自动重 复下一循环周期。
※ 当更换新模具时,必须重新调整此装置,可按以下步骤调整:
a 在手动方式下,按手动开模键,开模至要求的距离; b 松开安全杆上的螺母; c 调整安全杆末端接近安全挡板; d 收紧安全顶杆上的螺母。
可编辑版
9
射胶部分
可编辑版
10
一、 射座移动及小嘴中心调节 ※ 装模定位采用法兰配合固定模板的定位孔,装模时发现有
③ 检查油脂润滑摩擦表面状况,不允许出现干摩擦,及 时加注润滑油脂。
可编辑版
27
3 液压系统
① 液压油箱必须经常存有足够的液压油,可从装置于油箱外的油尺检 查油位,如发现油位低于要求应及时通知相关部门补充。
② 注塑机正常运行时,液压系统温度不能超过55℃;在超过的情况下 工作,液压系统会产生以下现象:
可编辑版
23
5 停机
按以下步骤停机
① 关闭料斗挡板;
② 清除料筒内剩余的胶料,以下有三种方法清除余料:
※ 保持半自动方式或全自动方式直至缺料发出警报;
※ 手动操作射胶或溶胶,使剩余胶料完全清除;
※ 按键选择“自动清除”功能,注塑机会自动产生射 胶、
溶胶及到索动作循环五次,重复此功能可再按此 键。
③ 按键关掉电热。
接触.
可编辑版
19
一般的注塑机调校

一般的注塑机可以根据以下的程序作调校:根据原料供应商的资料所提供的温度范围,将料筒温度调至该范围的中间,并调整模温。
估计所需的射胶量,将注塑机调至估计的最大射胶量的三分之二。
调校倒索(抽胶)行程。
估计及调校二级注塑时间,将二级注塑压力调至零。
初步调校一级注塑压力至注塑机极限的一半(50%);将注塑速度调至最高。
估计及调校所需要的冷却时间。
将背压调至3.5bar。
清除料筒内已降解了的树脂。
采用半自动注塑模式;开始注塑程序,观察螺杆的动作。
就需要而适当调节射胶速度和压力,若要使充模时间缩短,可以增加注塑压力。
如前所述,由于十足充模之前会有一个过程,充模最终压力可以调至一级注塑压力的100%。
压力最终都要调得够高,使可以达到的最大速度不受设定压力限制。
若有溢料,可以把速度减低。
每观察一个周期之后,便把射胶量及转换点调节。
设定程序,使可以在第一级注塑时已能获得按射胶重量计算达到95-98%的充模。
当第一级注塑的注射量、转换点、注塑速度及压力均调节妥当后,便可进行第二级的保压压力的调校程序。
按需要适当调校保压压力,但切勿过份充填模腔。
调校螺杆速度,确保刚在周期完成之前熔胶已完成,而注塑周期又没有受到限制。
缩短周期时间予提高生产率对大部分的注塑厂商来说,注塑周期可直接影响以下两个主要目的:1、每天从机械中得到更多的制件;2、制件合乎客人的要求。
注塑周期由以下组成:周期开始--螺杆开始前进,注射;制件浇口冷却螺杆开始转动--塑化行程开始螺杆回位完成--螺杆转动停止如必要的话抽胶发生模具打开(可能包括模芯的拉出)制件充分冷却便可以顶出顶出模具闭合(可能包括模芯的回位)模具闭上--周期重新开始。
自动注塑周期是在持续的相同次序下,同样的事情一次又一次地重复。
周期有三个主要部分:开模时间;填充时间;模具闭合时间;保压时间提高生产力的目标是在极短时间内完成所有必要的动作,完成顶出,并确保模具得到保护(包括拉出和退回滑块和侧位模芯)。
注塑成型调校的主要参数

注塑成型调校的主要参数注塑加工上讲的调机是指根据某一具体模具、原材料不断的调整注塑机的各种参数及其它辅助参数,直到生产出合格的塑胶件的一系列调校方案,称为调机。
注塑机的主要参数有如下一些:1 综合参数1.1 容模尺寸:宽×高×厚1.2 最大射胶量:即为注塑机所能射出的最大胶量,重量一般用克(g )或安士(oz)表示(1oz=28.4g),由于各种胶料比重不同,一般都是以PS(比重约为1)来作参照的,啤作其它胶料时进行换算,所啤胶件的啤总重(包括水口)必须小于(或等于)最大射胶量的80%,同时不能小于最大射胶量的15%,否则会影响注塑效益。
1.3 锁模力:即是模具合模后所能受的最大分开力,一般啤机均有一个额定的锁模力,调得太大易使机器或模具产生变形。
锁模力的大小与啤件投影面积大致成正比例关系,粗略计算方法如下:锁模力(吨)=型腔的投影面积(cm 2 )×材料压力系数÷额定锁模力的90%2 温度参数注塑加工中涉及到温度限制有以下几方面:- 烘料干燥温度- 炮筒温度- 模具温度2.1 烘料干燥温度啤作时需要将原料中的水份含量干燥到一定百分比以下称之为焗料,因为原料水分含量过高会引起汽花、剥层、脱皮、发脆等缺陷。
2.2 炮筒温度螺杆从进料口到螺杆头可分为输送段、压缩段、计量段、每段对应的炮筒温度一般是由低到高分布;另:炮嘴温度通常略高于计量末端之温度,而加长射嘴则稍高于计量末端之温度。
2.3 模具温度模具温度指模腔表面温度,根据模具型腔各部分的形状不同,一般是难走胶的部位,模温要求高一点,前模温度略高于后模温度,当各部位设定温度后,要求其温度波动小,所以往往要使用模具恒温机,冷水机等辅助设备来调节模温。
3 位置参数3.1 低压锁模位置:低压锁模位置要在高压位置前30 mm左右,压力一般设定为0,(以刚好够力将前后模贴合为宜)时间不要超过1秒,要求当模具有杂物时能在设定时间内自动反弹开模。
注塑机压力和流量的关系

注塑机电器调试步骤

注塑机电器调试步骤
注塑机电器调试步骤
1、开机后开马达,按F9--F3压力50,速度,20/50切换一下,点动检察一下液压油路是否漏油,如无漏油就继续切换几次。
之后50/50让马达运转7.8分钟检查是否漏油,同时检查润滑油泵运转是否正常。
时间到后,50/99在运转一下,检查是否正常。
2、压力:140速度:20起压,调洩流阀听油泵声音,声音正常后,锁紧螺母。
之后,压力:140速度:99起高压,检查压力表指示是否正常(140)。
3、按F10--F10--F4(I0)在“调模使用”的状态下调座台,调好后试几次座进,座退,射出,射退观察是否有问题。
4、按F10--F10--F2:开模行程调到0,在“调模使用”的状态下调顶出电子尺(用托模进退调),上紧接近开关的感应块。
5、拔出主板上电子尺插件,开模行程调到上限,按F10--F10--F4,“手动模式”下(用开/关模)上推力座锁母。
紧好后开模到底,调锁模油缸的电子尺和调模电眼,来回开/关模几次检查电子尺是否正常。
在“调模使用”的状态下调模进/退检查方向是否正确,同时观察调模电眼是否有感应。
6、按后面急停安扭检查是否有作用。
7、锁模到底,调行程开关,检查07是否亮。
安F4试一下开模慢和警报是否正常。
8、插上电子尺插件,安F10--F3-输入密码66,电子尺位置清零。
注塑成型机的各项参数设定步骤
注塑成型机的各项参数设定步骤1、参数设定前需确认及预备设定参数⑴确认材料干燥、模温及加热筒温度是否被正确设定并达到可加工状态。
⑵检查开闭模及顶出的动作和距离设定。
⑶射出压力(P1)设定在最大值的60%。
⑷保持压力(PH)设定在最大值的30%。
⑸射出速度(V1)设定在最大值的40%。
⑹螺杆转速(VS)设定在约60RPM。
⑺背压(PB)设定在约10kg/cm2。
⑻松退约设定在3mm。
⑼保压切换的位置设定在螺杆直径的30%。
例如φ100mm的螺杆,则设定30mm。
⑽计量行程比计算值稍短设定。
⑾射出总时间稍短,冷却时间稍长设定。
2、手动运转参数修正⑴闭锁模具(确认高压的上升),射出座前进。
⑵以手动射出直到螺杆完全停止,并注意停止位置。
⑶螺杆旋退进料。
⑷待冷却后开模取出成型品。
⑸重复⑴~⑷的步骤,螺杆最终停止在螺杆直径的10%~20%的位置,而且成型品无短射、毛边及白化,或开裂等现象。
3、半自动运转参数的修正⑴计量行程的修正[计量终点] 将射出压力提高到99%,并把保压暂调为0,将计量终点S0向前调到发生短射,再向后调至发生毛边,以其中间点为选择位置。
⑵出速度的修正把PH回复到原水准,将射出速度上下调整,找出发生短射及毛边的个别速度,以其中间点为适宜速度[本阶段亦可进入以多段速度对应外观问题的参数设定]。
⑶保持压力的修正上下调整保持压力,找出发生表面凹陷及毛边的个别压力,以其中间点为选择保压。
⑷保压时间[或射出时间]的修正逐步延长保持时间,直至成型品重量明显稳定为明适选择。
⑸冷却时间的修正逐步调降冷却时间,并确认下列情况可以满足:1、成型品被顶出、夹出、修整、包装不会白化、凸裂或变形。
2、模温能平衡稳定。
肉厚4mm以上制品冷却时间的简易算法:①理论冷却时间=S(1+2S)…….模温60度以下。
②理论冷却时间=1.3S(1+2S)…….模具60度以上[S表示成型品的最大肉厚]。
⑹塑化参数的修正①确认背压是否需要调整;②调整螺杆转速,使计量时间稍短于冷却时间;③确认计量时间是否稳定,可尝试调整加热圈温度的梯度。
[讲解]注塑机的流量与压力
流量与压力压力油及熔融均为流体。
明白流体流量与压力的关系对使用、调校及维修注塑机有着莫大的帮助。
油泵油泵是个流量源,代表泵出的油流量(在恒定转速及排量下)是恒定的。
油泵本身只产生流量,不产生压力。
油的压力来自阻力,阻力阻止油的流动。
一个极端的例子是堵住油泵的出口。
此时阻力是“无限大”,压力因此也是“无限大”,结果便是油管爆裂。
为了保护油管,所有的油泵出口均设计了溢流阀。
此溢流阀设置的压力称为系统压力。
当压力达到系统压力时,油便经溢流阀流回油箱,达到保护油管的目标。
油路的压力因此亦不能超过系统压力。
唧筒唧筒提供线性动作,克服线性阻力。
阻力源于负载。
负载包括(1)重力,(2)摩擦力及(3)质量加速力。
如F = 阻力,A = 活塞面积,所需压力P = F/A注塑机的注塑,负载是熔融流过喷咀、流道及模腔的阻力。
注塑机的动板移动,主要的负载是质量加速力,还夹杂了少量的摩擦力。
油马达油马达提供旋转动作,克服旋转阻力(扭矩负载)。
如T = 扭矩负载,所需压力P = T/DD是油马达的设计参数。
油马达的排量越大,此参数越大。
在相同的负载下,大排量油马达所需压力便越小。
注塑机的塑化,克服粒状的塑料经螺杆的压缩段挤压的摩擦力,将机械能量变为热能,塑化塑料。
注塑机的调模,起步的阻力较大是由于动态摩擦力比静态磨擦力高,及起步时的尾板加速。
没有负载当唧筒没有负载时,如顶针唧杆未触及模具的顶针板时,便没有压力。
不要在唧筒移动而油表指示零压力时而惊讶。
没有阻力便没有压力。
最大负载当唧筒走到尽头时,便有“无限”阻力。
但由于溢流阀的保护作用,最大压力只限于系统压力。
顶针或注射走到尽头时,压力便显示溢流阀的设置压力。
比例压力阀比例压力阀其实是个用电磁铁控制的溢流阀。
注塑机多个动作有不同的最高工作压力需要,由操作员输入,电脑输出,达到“可调”最高工作压力的目标。
当然,“可调”最高压力都只能在系统压力之下。
注塑机的系统压力是在140-175 kg/cm2之间。
注塑机调机方法与技巧
注塑机调机方法与技巧注塑机调机是指在开始生产之前,对注塑机进行调整和设置,以确保注塑过程顺利进行。
以下是注塑机调机的方法和技巧:1. 清洁和维护:在调机之前,确保注塑机的各个部件干净并正常工作。
清洁模具和喷嘴,检查模具和机器是否有损坏或磨损的地方,并及时修复。
2. 温度调整:根据注塑材料的要求,调整注塑机的加热温度。
通常需要调整的温度有料筒和喷嘴的温度、模具温度和冷却系统的温度。
确保温度稳定且符合要求。
3. 压力和流量调整:根据注塑产品的尺寸和要求,调整注塑机的注射压力和射胶速度。
通常需要调整的参数有射胶速度、压力和背压等。
确保射胶速度和压力达到注射过程的要求。
4. 注塑时间和压力保持:根据注塑产品的尺寸和要求,调整注塑机的注塑时间和保压时间。
确保注塑时间足够长,以充分填充模具腔。
5. 调整喷嘴位置和喷嘴直径:根据注塑产品的要求,调整喷嘴位置和喷嘴直径,以确保注塑产品的尺寸和形状符合要求。
优化喷嘴位置可提高产品质量和生产效率。
6. 检查冷却系统和模温控制:确保冷却系统正常工作并能有效降低模具温度。
检查冷却水流量和温度,调整冷却时间和温度控制器。
7. 注塑机调整参数记录:在调机过程中,记录和调整各个参数的数值,以备将来参考和调整。
这些参数包括温度、压力、流量、时间、位置等。
8. 运行试验:在调机完成后,进行运行试验,生产少量样品,检查产品质量和机器性能。
根据试验结果调整参数,直到满足质量要求。
以上是注塑机调机的一般方法和技巧,具体操作还需根据具体机型和注塑产品的要求进行调整。
在调机过程中,需要根据实际情况进行调整,并不断优化参数,以确保注塑过程的稳定和产品质量的达标。
注塑机调机调试工艺一般分三个步骤
For personal use only in study and research; not for commercial use注塑机调机调试工艺一般分三个步骤:1、参数设定前需确认及预备设定参数⑴确认材料干燥、模温及加热筒温度是否被正确设定并达到可加工状态。
⑵检查开闭模及顶出的动作和距离设定。
⑶射出压力(P1)设定在最大值的60%。
⑷保持压力(PH)设定在最大值的30%。
⑸射出速度(V1)设定在最大值的40%。
⑹螺杆转速(VS)设定在约60RPM。
⑺背压(PB)设定在约10kg/cm2。
⑻松退约设定在3mm。
⑼保压切换的位置设定在螺杆直径的30%。
例如φ100mm的螺杆,则设定30mm。
⑽计量行程比计算值稍短设定。
⑾射出总时间稍短,冷却时间稍长设定。
2、手动运转参数修正⑴闭锁模具(确认高压的上升),射出座前进。
⑵以手动射出直到螺杆完全停止,并注意停止位置。
⑶螺杆旋退进料。
⑷待冷却后开模取出成型品。
⑸重复⑴~⑷的步骤,螺杆最终停止在螺杆直径的10%~20%的位置,而且成型品无短射、毛边及白化,或开裂等现象。
3、半自动运转参数的修正⑴计量行程的修正[计量终点] 将射出压力提高到99%,并把保压暂调为0,将计量终点S0向前调到发生短射,再向后调至发生毛边,以其中间点为选择位置。
⑵出速度的修正把PH回复到原水准,将射出速度上下调整,找出发生短射及毛边的个别速度,以其中间点为适宜速度[本阶段亦可进入以多段速度对应外观问题的参数设定]。
⑶保持压力的修正上下调整保持压力,找出发生表面凹陷及毛边的个别压力,以其中间点为选择保压。
⑷保压时间[或射出时间]的修正逐步延长保持时间,直至成型品重量明显稳定为明适选择。
⑸冷却时间的修正逐步调降冷却时间,并确认下列情况可以满足:1、成型品被顶出、夹出、修整、包装不会白化、凸裂或变形。
2、模温能平衡稳定。
肉厚4mm以上制品冷却时间的简易算法:①理论冷却时间=S(1+2S)…….模温60度以下。
- 1、下载文档前请自行甄别文档内容的完整性,平台不提供额外的编辑、内容补充、找答案等附加服务。
- 2、"仅部分预览"的文档,不可在线预览部分如存在完整性等问题,可反馈申请退款(可完整预览的文档不适用该条件!)。
- 3、如文档侵犯您的权益,请联系客服反馈,我们会尽快为您处理(人工客服工作时间:9:00-18:30)。
注塑机比例流量、压力的调校
阅读:1535次页数:3页 2014-08-04 举报
比例流量、压力的调校
1、比例阀与电子放大板
比例流量阀和比例压力阀统称比例阀。
它有阀体和油摯线圈组成。
它的主要作用是通过油摯线圈受电的大小来控制阀的流量开放多少。
而油摯线圈受电和阀体流量开放程度是按一定比例线性关系而变化的。
当注塑机注塑预置叁数后,通过CPU中央处理器的处理和电子放大板的处理后,注塑机的注塑工作压力和流量就由比例阀控制。
具体可以用电箱旁的DPCA和DSCA电流表来显示比例线性关系。
具体叁数如下。
当S=00时,比例流量DSCA电流电流表显示200Ma;
当S=99时,比例流量阀在DSCA表上显示680Ma
当P=00时,比例压力阀在CPCA表上显示0mA;
当P=99时,比例压力阀在DPCA表上显示800Ma。
而相对的压力表在15~145kg/CM2范围内呈现性变化。
DSCA电流表上和DPCA电流表上显示的电流叁数也就是比例流量、比例压力油摯阀线圈电压变化索取的。
它受控于电脑CPU中央处理器和电子放大板控制。
电子放大板输出电压控制比例流量、比例压力阀。
控制比例流量、比例压力阀的线圈吸合程度来控制油压和油流量。
2、比例阀与电脑CPU中央处理单元
比例阀与电脑CPU中央处理单元是紧密相连,密切相连,共为一体,共同来完成注塑工作。
其运行过程应当为:叁数预置——>电脑处理——>电子放大板——>比例流量——>注塑各动作。
了解比例阀与电脑CPU中央处理单元的关系,对维修工作提供依据。
预置叁数使得数据进入电脑CPU中央处理单元,经过对叁数的运算和处理,将数据量通过D/A变换器转换成模拟量信号。
而该模拟量信号又经比例放大处理后,输出再通压力、流量最高控制和压力、流量最低限额控制4电位器进行控制调校,输出信号的幅值实际中应在0~3V范围内变化。
在维修过程中,一般调校好后才可以上机工作,不宜调节压力最高限额控制电位器,否则会改变工作点,给下一级控制带来困难。
电脑输出的控制信号作为电子放大板的输入信号,经过整形、比较、反馈、放大和隔离传送去控制功率三极管,再去驱动油摯阀和比例流量、比例压力阀线圈。
而线圈受电大小又控制比例阀的流量开放程度即线圈电压与比例阀流量呈线性关系。
3.数控速度与压力的检验及调节方法
在正常情况下,注塑机的流量与压力已经过严格的调校,一般不需要再调。
在特殊情况下,才需要重新调校电脑CPU上的压力与流量限额控制电位器。
(1)数控压力线性比例控制的检验方法
1、电脑CPU单元上的四个“流量与压力限额控制”电位器的位置。
2、预置参数把四级射胶速度调到50,枕压压力调到00
3、启动油泵电机,在溶胶筒温度达到溶胶温度时,按手动射胶键,使螺杆到底,看油压压力表应指示一个低于20公斤的压力数值。
可用压力最低限额控制电位器来调节,反时针旋转,可使压力降低。
4、可预置参数将枕压按级增加,油压表指示应按比例增加,当压力数控值枕压压力到达50时,90时,油压表应在误差2.5公斤以下,超过调节最低限额电位器。
1/3页
5、停止输入射胶信号,重复上述2、4步骤,利用射胶压力数控数值作检查点。
常用50和99,当其中一个检查点99达到所需的压力指示,而另一个检查点50的压力指示误差不超过(所需压力指示)2.5kgf/cm2,则不用再调整。
但需要在射胶压力数控值为00时,油压表的压力指数不可高于20kgf/cm2,一般均在5~15kgf/cm2之间。
6、为避免在枕压99检查点内调整油压指示时间长,引起油温过热或电机过载,热继电器动作,调校要迅速正确。
如遇热继电器跳摯要等2min后,热机电器金属片复位后,把射胶压力数控值调低后,再按热机电器的复位按键,继续调整。
7、当
调整枕压叁数在05~10及90~99时,油压表可能有不符合线性比例的压力指示,这是正常的如果误差额不高于6kgf/cm2则不需要调整。
8、注塑机类型不同,最高系统压力也不同。
当最高系统压力为145kgf/cm2时,在数控压力达到50时油压表指示应在72.5kgf/cm2。
而误差不超过
2.5kgf/cm2则不需要调校。
(2)数控速度线性比例控制的检验方法
1、拆下模具,取消特快琐模操作
2、取消低压琐模。
3、关上安全门。
4、把数控高速琐模速度调到0的数值,把数控高速开模速度及数控低速开模速度均调到40的数值。
5、启动油泵电机,用手动操作方式开模。
开模终止后,再按琐模,这时动模板不应移动,在将数控高速琐模的速度调到10.在调时,动模板应有缓慢的移动。
6、在电脑CPU中央处理器电子板上,用速度最低限额控制电位器去调整,按上述步骤达到步骤5的要求。
数控速度调整适当时若把高速琐模调到10时,动模板会慢慢移动。
当调到00时,动模板会停止移动,再转回10时,动模板会慢慢开始移动。
如果动模板移动时,震动幅度大,应检查是否取消特快琐模。
7、如果高速琐模速度是00时,动模板移动,可以把W1反时针方向转动,直至模板停止移动为止。
如果琐模速度是10时,动模模板不移动,可以把W电位器顺时针方向转动,直至模板移动为止。
8、重新调整低压琐模的位置的预调时间。
4、更换电子放大板及调校方法
一般是将损坏板从插入式插座中拆下,换上新的电子放大板。
新板安装上后,还需要加以调校,以保持数控压力和速度的线性比例控制,方法如下: 1、拆下损坏电子放大板,换上新板,插入插座,固定电子电路板。
2、巡视电脑面板。
不开油泵,按手动射台按键,显示灯亮,看电箱旁DSCA和DPCA电流
表是否有电流,看面部压力表是否有压力。
正常DSCA表有400MA电流,DPCA表上
有450MA即可。
若达不到,可选用电子放大板中压力。
流量电位器粗调,使电流达到。
3、溶胶筒加温。
待达到料温时,开启油泵电机,按手动射胶,将螺杆顶底。
停掉油泵。
4、把数控四段射胶速度调到00,枕压压力预置00,再按手动射胶,看数控流量DSCA电
流表和DPCA电流表上的指示。
DSCA指示应为200MA;DPCA电流表上指示为0MA。
若有不符可用电子放大板上流量微调或压力微调电位器进行调校,顺时针方向转动可增
加电流表上的指示数值,反之侧降低指示数值。
5、把数控四级射胶速度调到99,枕压压力调到99(因设备不同,最大压力也不同。
这里
2/3页
的99为最大压力),按手动射胶,DSCA电流表电流指示应为680MA,DPCA电流表上
指示应为800MA。
若达不到可用电子放大板上的流量微调和压力微调进行调校。
6、若按上述步骤无法达到时侧可用重新调整电脑CPU的信号输出幅值,需重调。
7、若达到上述要求,则可将四级射胶速度调到50,枕压调到99。
启动油泵电机,按手动射胶,观察油压表压力指示是否在设备额定最大值上。
如达不到,可调整电脑CPU单
元上最大压力限额控制电位器,使其达到。
8、可再预置四级射胶速度50,枕压压力50(最大压力的一半),再按手动射胶,观看压力表油压指示是否再一半位置,校验一下压力控制线性度。
青岛塑料十一厂
3/3。