冷轧罩式退火工艺及原理201807
冷轧退火机组的工艺

冷轧退火机组的工艺
冷轧退火机组的工艺流程如下:
1. 原材料准备:选取合适的金属材料作为原材料,通常是钢材或者铝材。
2. 冷轧:将原材料通过冷轧机进行冷轧加工,可以将原材料加工成所需的形状和尺寸。
3. 退火:将冷轧加工后的材料进行退火处理。
退火是指将材料加热到一定温度,然后缓慢冷却,目的是改善材料的组织结构和性能。
退火温度和时间根据不同材料和要求有所不同。
4. 冷卷:将退火后的材料通过冷轧机进行再次冷轧加工,可以进一步提高材料的平整度和表面质量。
5. 剪切:将冷卷后的材料通过剪切机进行剪切,根据需要进行切割成所需的尺寸。
6. 包装和出库:将剪切后的材料按照客户要求进行包装,并完成出库准备,以便发货给客户。
以上就是冷轧退火机组的基本工艺流程,具体的工艺参数和操作细节可能会根据
不同的机组和产品有所差异。
罩式退火炉的退火工艺

罩式退火炉的退火工艺冷轧带钢退火工艺制度主要根据钢的化学成分、产品的技术标准、带钢的尺寸和卷重等因素确定。
工艺制度必须保证生产中卷层间不粘结,表面不出现氧化。
A. 加热速度的确定钢的加热速度主要决定于钢的导热系数的大小。
钢中碳含量和合金含量对热传导影响较大。
如它们的含量高,则导热系数小,加热速度就要适当慢一些,避免内外温度差过大而造成组织和性能的不均。
从室温到400℃,加热速度一般是不加限制的。
根据在结晶过程的原理,带钢从室温到400℃,带钢内部组织无显著变化,轧制过程中被拉长的晶粒刚刚获得恢复,尚未形成再结晶,因此在此区间钢的加热速度越快越好。
带钢由400℃加热到保温温度,加热速度对带钢的性能和表面质量都有相当大的影响。
一般规定升温速度以30~50℃/h为宜,带钢从400℃加热到保温温度723℃以下期间,正是再结晶形成阶段,因而在这个温度区间加热速度必须予以控制。
B. 保温温度和保温时间的确定钢的再结晶温度不是固定的某一温度,它同带钢内部组织状态有关,实际生产中的再结晶温度是在570~720℃范围内根据产品选择的。
保温温度及保温时间主要依据产品标准、技术条件及钢种和带钢的厚度来确定。
保温时间、保温温度还与卷重、带钢厚度有关,卷重大、钢板厚,则保温温度高,保温时间也要长。
对易产生层间粘结缺陷的钢质和薄规格的带钢,保温温度可适当低些,保温时间可短些。
C. 光亮退火要使带钢无脱碳、无氧化必须进行光亮退火。
退火钢卷防止氧化的关键性问题是必须使保护罩内的压力满足工艺要求。
另外,还要认真搞好冷吹和热吹。
冷吹和热吹的目的是利用保护气体驱走内罩中的空气和钢卷带进的油气水分。
热吹的作用是除了将内罩中的残余气体进一步赶尽之外,更重要的是将板卷带来的乳化液产生的油烟、水蒸气等有害物质全部驱走吹净,避免玷污钢板表面而降低钢板表面质量。
冷轧罩式退火工艺及原理(课堂PPT)

晶粒尺寸
退火温度/*c
图4再结晶后晶粒尺寸与退火温度的关 系
.
6
2、退火原因
钢材经过冷轧变形后金属内部组织产生晶粒拉长、 晶粒破碎和晶体缺陷大量存在现象,导致金属内部自由 能升高,处于不稳定状态,具有自发地恢复到比较完整 、规则和自由能低稳定状态的趋势。
在室温下,原子的动能少,扩散力差,扩散速度慢 ,导致这种倾向无法实现,须施加激活力,这种激活力 就是将钢加热到一定温度,使原子获得足够的扩散动能 ,消除晶格畸变,使组织、性能发生变化。
• 表面粗糙度方面:给罩退备料末机架采用大粗糙度辊,形成合适的表 面的Ra值和PPI值,降低粘结倾向;
程将使钢的各项性能再次下降。 所以再结晶退火可概括为:通过加热和
保温,既要使经冷轧后的钢发生再结晶,同时又要防止其晶粒过分长
大。
.
4
1、冷轧工序组织变化
酸轧工序压下率控制标准,以及带 钢组织演变机理和特点
.
5
1、冷轧工序组织变化
退火工序影响再结晶后晶粒大小的主要 因素是退火温度和保温时间:在一定的冷 变形条件下, 再结晶后的晶粒大小随退 火温度和保温时间的不同而变化,加热 温度越高,保温时间越长,晶粒越粗大 。
晶界上不稳定的原子由于热运动重 新排列,经过形核、长大这一过程
,形成新的等轴 晶粒,即产生再结晶现象。从而使钢的强硬度降低,
塑韧性增加,使得带钢获得良好的工艺及使用性能。再结晶的发生需
要一定的时间和温度,但随着温度的升高和时间的过分延长,已形成
的等轴晶粒其晶界之间会发生融合,新的等轴晶粒继 续长大,这一过
连续退火:经过脱脂清洗表面清洁,开卷加热带钢温度均匀,带 钢平直度,板形优良。适合生产表面要求较高的产品和薄规格 产品。
冷轧生产线退火工艺

冷轧生产线退火工艺本文档旨在介绍冷轧生产线的退火工艺,以帮助读者了解和掌握该工艺的基本原理和操作流程。
2.1 原料准备在退火工艺开始之前,需要对原料进行准备。
原料包括待退火的冷轧钢板、保护气体、冷却介质等。
这些原料的准备对于保证退火工艺的稳定性和产品质量至关重要。
2.2 加热加热是冷轧生产线退火工艺的关键步骤之一。
通过加热将冷轧钢板的温度升高至一定程度,以促进晶粒生长和内部应力的消除。
2.3 保温保温是在加热后将钢板保持在一定温度区间内的过程,在该温度区间内进行足够的时间,使得钢板的温度达到均匀稳定,并使晶粒生长得以完成。
2.4 冷却冷却是将钢板从退火温度迅速冷却至室温的过程。
冷却方式可以采用空冷、水冷、盐浴冷却等不同方式,具体的冷却方式需要根据产品需求和工艺要求进行选择。
2.5 质量检验退火后的钢板需要进行质量检验,包括外观质量检验、力学性能测试、化学成分分析等。
通过质量检验,可以确保产品符合相关标准和要求。
3.1 加热温度控制加热温度的控制对于退火工艺的成功至关重要。
需要根据不同钢种和产品要求确定适当的加热温度范围,并确保在加热过程中温度的均匀性和稳定性。
3.2 保温时间控制保温时间的控制也是冷轧生产线退火工艺的重要因素之一。
保温时间过短可能导致晶粒生长不完全,从而影响产品的性能;而保温时间过长则可能造成能源浪费和生产效率的降低。
3.3 冷却方式选择根据产品需求和工艺要求,选择合适的冷却方式对于保证产品质量具有重要意义。
不同冷却方式会对钢板的组织结构和性能产生不同的影响,需要进行合理选择和控制。
在进行冷轧生产线退火工艺时,必须严格按照相关安全规范操作,做好安全防护措施。
确保相关设备的运行安全,预防事故的发生,保障工人的人身安全。
冷轧生产线退火工艺是冷轧钢板制造过程中不可或缺的环节。
通过合理的工艺参数控制和操作流程控制,可以获得符合要求的产品。
在实际操作中,需要根据不同产品的要求和工艺特点进行灵活调整和改进,以提高产品质量和生产效率。
连退与罩退工艺
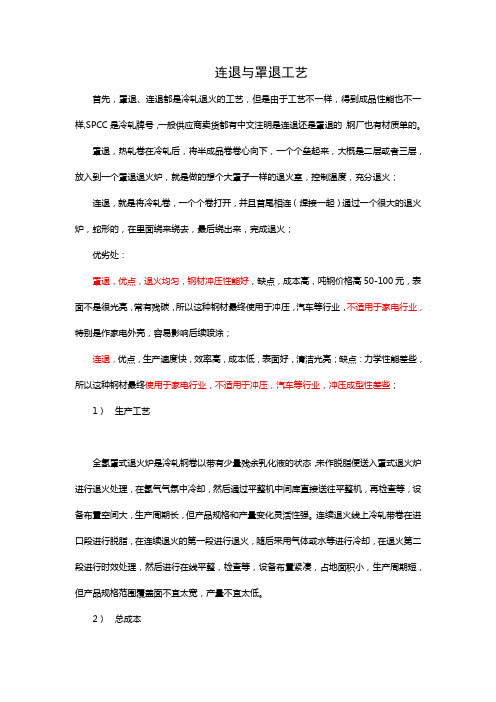
连退与罩退工艺首先,罩退、连退都是冷轧退火的工艺,但是由于工艺不一样,得到成品性能也不一样,SPCC是冷轧牌号,一般供应商卖货都有中文注明是连退还是罩退的,钢厂也有材质单的。
罩退,热轧卷在冷轧后,将半成品卷卷心向下,一个个垒起来,大概是二层或者三层,放入到一个罩退退火炉,就是做的想个大罩子一样的退火室,控制温度,充分退火;连退,就是将冷轧卷,一个个卷打开,并且首尾相连(焊接一起)通过一个很大的退火炉,蛇形的,在里面绕来绕去,最后绕出来,完成退火;优劣处:罩退,优点,退火均匀,钢材冲压性能好,缺点,成本高,吨钢价格高50-100元,表面不是很光亮,常有残碳,所以这种钢材最终使用于冲压,汽车等行业,不适用于家电行业,特别是作家电外壳,容易影响后续喷涂;连退,优点,生产速度快,效率高,成本低,表面好,清洁光亮;缺点:力学性能差些,所以这种钢材最终使用于家电行业,不适用于冲压,汽车等行业,冲压成型性差些;1)生产工艺全氢罩式退火炉是冷轧钢卷以带有少量残余乳化液的状态,未作脱脂便送入罩式退火炉进行退火处理,在氢气气氛中冷却,然后通过平整机中间库直接送往平整机,再检查等,设备布置空间大,生产周期长,但产品规格和产量变化灵活性强。
连续退火线上冷轧带卷在进口段进行脱脂,在连续退火的第一段进行退火,随后采用气体或水等进行冷却,在退火第二段进行时效处理,然后进行在线平整,检查等,设备布置紧凑,占地面积小,生产周期短,但产品规格范围覆盖面不宜太宽,产量不宜太低。
2)总成本所谓总成本包含工艺设备新建的投资费用再加上生产运行费用。
对于全氢罩式退火工艺途径来说,其投资、消耗与维修费用与连续退火线相比都要低,只有人员较多和材料损失比较高。
此外,对于连续退火线而言,还应累加冶炼深冲钢种所需的附加费用(用于真空脱气、微合金化等)以及较昂贵的酸洗费用(用于清除热轧卷取温度较高而形成的红色氧化铁皮)。
所以,从有关的资料评价估计全氢罩式退火炉的总成本比连续退火机组低。
冷轧罩式退火炉工艺

冷轧罩式退火炉工艺
冷轧罩式退火炉工艺是一种用于冷轧钢板的热处理工艺,目的是通过退火处理改善钢板的机械性能和表面质量。
该工艺主要分为以下几个步骤:
1. 预处理:将冷轧钢板进行预处理,包括除油、切割等工序,确保钢板表面干净。
2. 裂解和脱碳:将冷轧钢板放入罩式退火炉中,加热至高温,使钢板中的碳元素析出并迁移到钢板表面,从而减少钢板中的碳含量。
同时,通过裂解处理,使钢板内的应力得以释放。
3. 保温和冷却:在高温环境中保温一段时间,使钢板内部温度均匀分布,然后逐渐将炉温降低,进行冷却。
冷却速度可以根据需要进行调整,以控制钢板的组织和性能。
4. 清洗和抛光:冷轧钢板经过退火处理后,表面可能会出现一定程度的氧化和残余物,需要进行清洗和抛光,使钢板表面光洁。
5. 检验和包装:对退火后的钢板进行检验,包括尺寸、平直度、表面质量等指标的检测。
合格的钢板经过包装后,可以进行下一步的使用或销售。
冷轧罩式退火介绍

气体气氛露点、工作载荷空间的密封性三大方面
主要集中在以下几个方面:
人为错误提高出炉温度(使得出炉后,卷心温度高于氧化温度
160度)、热电偶检测错误、冷却速度过快、工作载荷空间内氢气循 环量不足、氢气氮气纯度不够、炉台表面不清洁不干燥、工作载荷空 间的设备表面有水分、炉台密封圈老化、内罩有裂缝、通往炉内的管 道不密封。
热应力在罩式退火机组肯定存在,不能避免,而热应力的影响 因素主要受加热冷却速度、板形(特别是中浪) 、卷取张力等; 氧化色:
氧化色是由于钢卷在高温下接触氧气而形成的钢卷表面与氧气 反应而生成的一种表面淡黄色或黄色的氧化现象, 氧化色缺陷给冷轧 产品出厂后给涂镀或外观带来一定量的损失; 氧化色是一种可逆缺陷, 如果发现及时,可修复;
粘结:粘接为罩式炉特有缺陷,其特征是形貌呈月牙形,是有 曲线形状的应变条纹带钢在退火过程中有时产生局部粘接, 造成平整 开卷时粘接处发生撕裂变形、凸起,经平整后形成弯月状、马蹄状或 弧形的凹印。因粘接处变形产生加工硬化、塑性降低、冲压性能差使 带钢产生部分或整卷的废次品。 因此,对于用罩式退火炉来进行消除 酸轧轧后带钢产生的内应力的冷轧产品生产厂家来说, 如何预防、 减 少粘接的产生,提高产品的合格率是各冷轧产品生产厂家所面临的重 要课题之一。
对于不同的材料来说,其再结晶温度不一样,没有固定值,在 实际生产中,可调整的影响因素是变形程度、加热速度;变形程序越 大,再结晶温度越底,加热速度极快或慢都会使再结晶温度升高。
罩式退火机构成:
全封闭炉台
内罩
加热罩
冷却罩
终冷台
对流板
目前,罩式退火机组所退的品种除原来所设计的CQ、DQ、DDQ
冷轧生产线退火工艺

冷轧生产线退火工艺引言退火是冷轧生产线中的重要工艺之一,它能提高材料的塑性和韧性,减少应力,并改善材料的微观组织结构。
本文将介绍冷轧生产线退火工艺的基本原理、步骤以及对材料性能的影响。
一、冷轧生产线退火的基本原理冷轧生产线退火的基本原理是通过升温、保温和冷却过程控制材料的晶粒尺寸和晶体结构,从而达到改变材料力学性能的目的。
具体来说,退火过程中材料的晶粒会逐渐长大并重新排列,同时消除或减少材料中的应力和缺陷,从而提高材料的塑性和韧性。
二、冷轧生产线退火的步骤1.清洗:首先将冷轧板材从前工序传送到退火工序,需要对板材进行清洗,以去除表面的油污、氧化皮等杂质。
2.升温:将清洗后的板材放入退火炉中,通过加热使其温度逐渐升高,一般升温速度控制在5℃/min左右。
3.保温:当板材达到指定温度后,需要进行保温一段时间,以使材料的晶粒逐渐长大、晶体结构重排并消除应力。
保温时间一般根据材料的性质和要求来确定。
4.冷却:保温结束后,将板材从退火炉中取出,进行快速冷却。
冷却方式可以是自然冷却、水冷却或气体冷却,根据具体情况选择合适的冷却方式。
三、冷轧生产线退火对材料性能的影响冷轧生产线退火可以显著改善材料的力学性能和物理性能,具体影响如下:1. 提高材料的塑性和韧性退火过程中,材料的晶粒逐渐长大,晶界移动,且晶体结构重排,从而降低了材料的内应力和缺陷,提高了材料的塑性和韧性。
退火后的材料更容易进行加工和成型。
2. 降低材料的硬度和强度冷轧板材在冷轧过程中通常会产生较高的硬度和强度,通过退火能够降低材料的硬度和强度,使其更加柔软和易于加工。
3. 改善材料的织构和微观组织结构退火能够改善材料的织构和微观组织结构,使其晶粒更为均匀和细小,晶粒内部的组织结构更加致密。
这种改善能够提高材料的均匀性、稳定性和耐腐蚀性能。
4. 消除材料中的残余应力冷轧生产线退火过程中的加热、保温和冷却能够消除或减少材料中的残余应力。
残余应力会对材料的形状稳定性和力学性能产生不良影响,因此通过退火能够提高材料的综合性能。
- 1、下载文档前请自行甄别文档内容的完整性,平台不提供额外的编辑、内容补充、找答案等附加服务。
- 2、"仅部分预览"的文档,不可在线预览部分如存在完整性等问题,可反馈申请退款(可完整预览的文档不适用该条件!)。
- 3、如文档侵犯您的权益,请联系客服反馈,我们会尽快为您处理(人工客服工作时间:9:00-18:30)。
应力过大造成的粘结风险,尤其对于特殊规格,根据实际温度差采用
相应时间的带罩缓慢冷却,降低冷却过程中的压应力,最大程度上减 少粘结风险;同时合理配炉,采用规格和卷位的合理搭配,减少易发
生粘结钢卷的粘结倾向。
• 平整生产的张力和速度控制:对于粘结较严重的钢卷在采用大张力和 高速生产,大于500m/min,使粘结情况减弱。
轧钢工培训材料
2018年7月
罩式退火工艺及原理
1、冷轧工序组织变化 2、退火原因 3、退火目的及作用 4、罩退与连续退火线比较 5、罩式退火工艺流程图 6、常用退火工艺曲线 7、罩式退火温度分布特点 8、退火粘结问题 9、钢卷在加热过程热应力分布
1、冷轧工序组织变化
酸轧工序压下率控制标准,以及带 钢组织演变机理和特点
加热过程的温度分布
冷却过程的温度分布
因钢卷整卷退火,在退火过程中温度存在差异。加热过程中,钢卷 外圈温度高芯部温度低,钢卷膨胀外圈受拉应力,内圈受压应力; 反之在冷却过程中外圈温度低芯部温度高,钢卷整体外圈受压应力 ,内圈受拉应力。
8、退火粘结问题
在冷硬卷的紧卷立卷再结晶退火过程中,经常发生相邻卷层间粘到一 起,增加了后道工序平整机的开卷张力,并且在开卷过程中会造成板 带撕裂,出现皱痕等情况,并且因同样的粘结力会造成不同程度板形 缺陷,这种缺陷就是我们通常称为的罩式炉粘钢。
4、罩退与连续退火线比较区别
• 罩式退火:生产周期长(几十个小时), 与清洗线、平整线分开布置,整体联成一条冷板生产流程,但 可选择的进行脱脂清洗,且钢种及规格对整体生产的影响较小, 可小批量灵活的组织生产,单炉台生产,炉台数量可根据产量 和品种变化随时增减,中间工序有库存缓冲,产量和品种适应 能力强,适合多品种,小批量生产及试验生产。 • 连续退火:生产周期短(几分钟),脱脂清洗、退火、平整联 成一条整体生产线,生产效率高,但受计划影响启停和规格品 种切换等成本高,产品规格覆盖范围不宜太宽, 产量不宜太低。 适合大批量,少品种生产。
9、钢卷在加热过程热应力分布
在加热过程中随加热时间的变缓和退火时间的延长,卷内心处的
应力一直向变小趋势发展,而随外径逐渐增大应力随退火时间的 延长,呈现处先变大后减小的趋势。且因退火时间的不同,应力
集中的位置会发生变化 。
钢卷在冷却过程热应力分布
在冷却过程中主要的应力出现在卷厚度的中心位置,且随 着时间的延长,压应力越大,就越可能造成粘结。
Thanks!
谢谢!
4、罩退与连续退火线比较区别
罩式退火:整卷退火,内外温度存在一定的不均匀容易发生粘结, 通过加热让板带表面残油挥发,如挥发不好易造成清洁度低 (可选择的进行脱脂清洗),适于生产太薄的产品规格,但对 中厚规格产品生产没有限制。
连续退火:经过脱脂清洗表面清洁,开卷加热带钢温度均匀,带 钢平直度,板形优良。适合生产表面要求较高的产品和薄规格 产品。
1、冷轧工序组织变化
酸轧工序压下率控制标准,以及带 钢组织演变机理和特点
1、冷轧工序组织变化
退火工序影响再结晶后晶粒大小的主要 因素是退火温度和保温时间:在一定的冷 变形条件下, 再结晶后的晶粒大小随退 火温度和保温时间的不同而变化,加热 温度越高,保温时间越长,晶粒越粗大。
晶粒尺寸
退火温度/*c
连退与罩退生产线
4、罩退与连续退火线比较区别
罩式退火:罩式炉退火加热和冷却速度慢,使得碳化物析出和晶 粒长大有充足的时间,这种再结晶退火方式有利于形成对深冲 性能有利的饼形晶粒,能获得较好的n值,r值,在生产深冲、 超深冲用钢方面可以方便的控制,有其优越性。 连续退火:加热和冷却速度快,保温时间短,为了再结晶尽可能 充分和得到良好的成形性,对化学成分和退火制度的要求较严 格,低碳钢产品性能与罩退相比硬度高,强度高,塑性低,更 适合生产汽车用高强度钢。
图 4再结晶后晶粒尺寸与退火温度的 关系
2、退火原因
钢材经过冷轧变形后金属内部组织产生晶粒拉长、 晶粒破碎和晶体缺陷大量存在现象,导致金属内部自由 能升高,处于不稳定状态,具有自发地恢复到比较完整、 规则和自由能低稳定状态的趋势。 在室温下,原子的动能少,扩散力差,扩散速度慢, 导致这种倾向无法实现,须施加激活力,这种激活力就 是将钢加热到一定温度,使原子获得足够的扩散动能, 消除晶格畸变,使组织、性能发生变化。 因此经过冷轧后的钢材必须经过热处理退火。
1、冷轧工序组织变化
经过冷轧加工后的钢卷,由于其晶粒被破碎拉长,晶格发生严重畸变,
使得钢的硬度增加,塑軔性降低,即产生加工硬化现象。通过将其加
热到再结晶温度以上,奥氏体转化温度以下,并保温一定时间,使晶 界上不稳定的原子由于热运动重 新排列,经过形核、长大这一过程,
形成新的等轴 晶粒,即产生再结晶现象。从而使钢的强硬度降低,塑
粘结缺陷
粘结的影响因素
• • • • • • • 酸轧的卷取张力 原料板形 鼓包缺陷 表面物理情况及粗糙度 退火工艺制度及热应力分布情况 表面清洁度及残留情况 平整生产开卷张力及生产速度
粘结解决措施
• 张力控制方面:酸轧采用阶梯张力控制,最大程度的降低卷曲张力,
尤其对于薄规格。对于品种钢及特殊规格、钢种等流向脱脂清洗线,
既能提高板面质量而且能降张力,增加防粘层等,使粘结几率降低; • 表面粗糙度方面:给罩退备料末机架采用大粗糙度辊,形成合适的表
面的Ra值和PPI值,降低粘结倾向;
• 板形控制:为了避免粘结在轧机为罩退备料采用微边浪控制,避免中 浪对粘结造成影响;
粘结解决措施
• 退火工艺优化:采用合适的退火升温和降温制度,避免因温度差异热
5、罩式退火工艺流程图
装料;内罩;加热罩;冷却
内
罩
加热罩
冷却风机
水
水
冷却 风机
喷淋冷却
罩 式 退 火 炉
Hale Waihona Puke 加热罩 内罩钢卷炉台
6、常用退火工艺曲线
6、常用退火工艺曲线
罩式退火工艺
退火工艺参数 400℃以前不控制加热速度;400℃-730℃加热时间不低 于12小时,730℃保温,保温时间不低于11.8小时(卷冷、 热点温差≤60℃),辐射冷却时间不低于1.5小时,喷淋开始温 度为370℃,出炉温度为80℃。具体方案见下表所示。 DC03 钢种退火工艺制度
3、退火目的及作用
退火的目的及作用 退火是将带钢加热到一定的温度保温后再冷却 的工艺操作。 冷轧板的退火是冷轧带钢生产中最主要的热处 理工序之一。冷轧带钢的退火因钢种的不同分初退 火、中间退火和成品退火,大多采用的是成品退火, 其目的是消除冷轧造成的内应力和加工硬化,使钢 板具有标准所要求的力学性能、工艺性能及显微结 构,这种热处理一般为再结晶退火。
韧性增加,使得带钢获得良好的工艺及使用性能。再结晶的发生需要 一定的时间和温度,但随着温度的升高和时间的过分延长,已形成的
等轴晶粒其晶界之间会发生融合,新的等轴晶粒继 续长大,这一过程
将使钢的各项性能再次下降。 所以再结晶退火可概括为:通过加热和保 温,既要使经冷轧后的钢发生再结晶,同时又要防止其晶粒过分长大。
厚度(mm) >、≤ 0.3-0.5 0.501-0.8 加热、保温制度(单位:小时) 1段 12 12 2段 13.16 12.3 带罩冷却(单位: 小时) 6 5
0.801-1.5 1.501-2.0
12 12
12 11.8
5 4.5
罩式退火工艺
均热
空气/水冷却
加热
冷却
7、罩式退火温度分布特点