模具CAM实训报告
实习报告记录(共7篇)

实习报告记录(共7篇)CAD/CAM , ( .puter Aided Design )计算机辅助设计和(.puter Aided Manuf acturing )计算机辅助制造技术,是近些年出现的一种高效的先进工业生产技术,随着计算机技术的飞跃发展,近十多年来一些先进国家的模具制造行业,己广泛采用NC 和 .C 机床来加工模具,以提高模具精度和生产效率,在当前以信息工业为核心的新工业的兴起过程中,CAD/CAM 技术己成为新一代生产技术的核心,是实现自动化集成制造系统(CIMS)不可缺少的主要技术发展阶段。
1.CAD/CAM 的发展过程CAD/CAM 技术从出现到现在己经发展了50 多年了,无论是硬件技术还是软件技术都发生了很大的大变化,总的来说先后经历了三个阶段。
1.1单元技术的发展和应用阶段在这一阶段,分别针对一些特殊的应用领域开展了计算机辅助设计,分析,工艺,制造等单一功能的开发及应用,这些系统的通用性17差,应用不普及,系统之间的数据结构不统一,出现信息孤岛现象,系统之间不能进行数据交换。
1.2 CAD/CAM 集成阶段随着一些专业系统的应用普及,出现了通用的CAD/CAM 系统,而且系统的功能迅速增强,列如CAD 系统迅速从二维绘图发展到三维建模。
特征造型,参数化设计等先进技术被CAD 系统普遍采用,继而CAD, CAE, CAPP, CAM 系统实现集成或数据交换标准化,CAD/CAM 的应用取得显著成就。
l.3 C I M S技术推广应用阶段计算机技术除了在设计制造等领域截获与深入应用同时,几乎在企业生产的各个领域都获得应用,由于企业的开发活动与企业的其他经营活动是密切相关的,因此要求CAD/CAM 等计算机辅助系统与计算机管理系统实现进行信息交流,把正确的信息传递给正确的地方,这是一个高层次的企业内的信息集成,就是所谓的计算机集成应用系统。
1.4 我国CAD I CAM 技术的发展现状我国CAD/CAM 技术的开发应用水平与发达国家相比还有相当大的差距,我国的CAD I CAM 技术的开发是在7 0 年代末开始的,到目前为止先后通过国家有关部门进行鉴定的有 1 9 8 4 年华中工学院开发的精冲模CAD I CAM 系统,1985 年北京机电研究院开发的冲裁模CAD/CAM 系统,吉林大学开发的棍锻模和锤锻模CAD I CAM 系统,1 9 8 6 年华中工学院开发的冷冲模CAD/CAM 系统和上海交通大学模18具研究所开发的冷冲模CAD I CAM 系统,1 9 8 8 年华中工学院开发的塑压模CAD 系统等。
cam实训报告
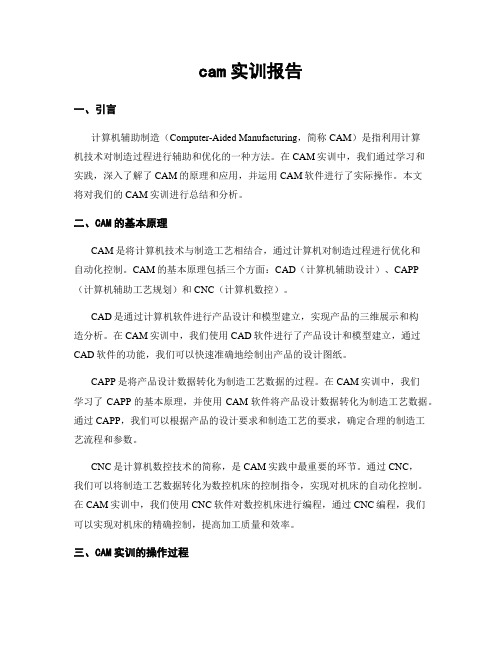
cam实训报告一、引言计算机辅助制造(Computer-Aided Manufacturing,简称CAM)是指利用计算机技术对制造过程进行辅助和优化的一种方法。
在CAM实训中,我们通过学习和实践,深入了解了CAM的原理和应用,并运用CAM软件进行了实际操作。
本文将对我们的CAM实训进行总结和分析。
二、CAM的基本原理CAM是将计算机技术与制造工艺相结合,通过计算机对制造过程进行优化和自动化控制。
CAM的基本原理包括三个方面:CAD(计算机辅助设计)、CAPP (计算机辅助工艺规划)和CNC(计算机数控)。
CAD是通过计算机软件进行产品设计和模型建立,实现产品的三维展示和构造分析。
在CAM实训中,我们使用CAD软件进行了产品设计和模型建立,通过CAD软件的功能,我们可以快速准确地绘制出产品的设计图纸。
CAPP是将产品设计数据转化为制造工艺数据的过程。
在CAM实训中,我们学习了CAPP的基本原理,并使用CAM软件将产品设计数据转化为制造工艺数据。
通过CAPP,我们可以根据产品的设计要求和制造工艺的要求,确定合理的制造工艺流程和参数。
CNC是计算机数控技术的简称,是CAM实践中最重要的环节。
通过CNC,我们可以将制造工艺数据转化为数控机床的控制指令,实现对机床的自动化控制。
在CAM实训中,我们使用CNC软件对数控机床进行编程,通过CNC编程,我们可以实现对机床的精确控制,提高加工质量和效率。
三、CAM实训的操作过程CAM实训的操作过程主要包括产品设计、工艺规划和数控编程。
在实际操作中,我们按照以下步骤进行:1. 产品设计:首先,我们使用CAD软件进行产品的三维建模和设计。
通过CAD软件的绘图功能,我们可以绘制出产品的外形和内部结构,并对产品进行构造分析和优化设计。
2. 工艺规划:在产品设计完成后,我们使用CAM软件进行工艺规划。
通过CAM软件的功能,我们可以将产品的设计数据转化为制造工艺数据,并确定合理的工艺流程和参数。
cam实训报告
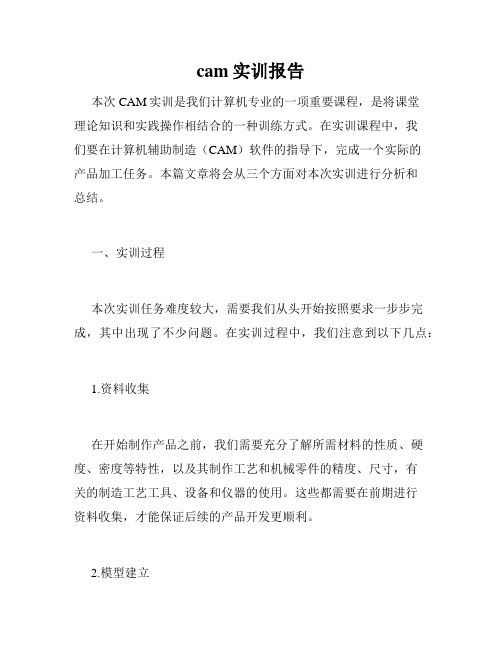
cam实训报告本次CAM实训是我们计算机专业的一项重要课程,是将课堂理论知识和实践操作相结合的一种训练方式。
在实训课程中,我们要在计算机辅助制造(CAM)软件的指导下,完成一个实际的产品加工任务。
本篇文章将会从三个方面对本次实训进行分析和总结。
一、实训过程本次实训任务难度较大,需要我们从头开始按照要求一步步完成,其中出现了不少问题。
在实训过程中,我们注意到以下几点:1.资料收集在开始制作产品之前,我们需要充分了解所需材料的性质、硬度、密度等特性,以及其制作工艺和机械零件的精度、尺寸,有关的制造工艺工具、设备和仪器的使用。
这些都需要在前期进行资料收集,才能保证后续的产品开发更顺利。
2.模型建立根据制作的产品要求,我们需要利用CAD软件进行模型建立。
在实际操作中,由于我们掌握了一定的基础知识和使用技巧,这一环节比较顺利,基本做到了精度和尺寸的控制。
3.加工路径规划和仿真路径规划对于整个实训过程非常重要,这是将CAD图纸转化为机床上加工参数的过程。
在规划路径时,需要根据实际情况考虑工件的方向、刀具的形状、尺寸等,否则可能会导致无法正确加工、损坏机床或刀具,影响产品的质量。
在路径规划完成后,需要进行仿真,通过模拟机床加工进行预估,以保证加工过程可行并且提高效率。
二、团队协作本次实训是以团队形式完成的,团队成员之间需要进行有效的通信和协作,以确保产品的按时完成。
在实训中,我们发现能与团队中人员直接进行有效的沟通能够提高生产效率。
同时,我们也学习到了聆听他人意见的重要性,哪怕是别人的想法与自己的不同,也应该认真考虑和尝试。
这能够使团队成员的工作更协调和高效,帮助我们达成共同目标。
三、技能提高本次CAM实训让我们有机会学习和使用了各种机械切削工具,同时,掌握了CAM软件的基本操作和加工路径的规划。
在实际操作中,我们也发现,学习CAM对于我们日后的职业生涯发展具有非常重要的意义。
在这个时代,CAM技术的广泛应用已经深刻影响了人类的生产和制造方式,而这种技术会在未来更广泛地应用于汽车、医疗、玩具、航空和机械等众多行业,具有非常大的市场前景。
模具CAM模拟仿真加工实习实训报告

模具 CAM 模拟仿真加工实习实训报告一、试验目的1、学习把握 CAITA 模具设计模块并学会用不同软件进展磨具设计。
2、学会用 CAITA 软件进展简洁的磨具设计过程和模拟加工过程。
3、进一步稳固模具构造及制造工艺方面的学问,提高模具设计力量,并提高自己的学习力量。
二、试验内容1.生疏 CAITA 软件的使用过程生疏绘图界面各个工具的使用,能够娴熟使用并进展操作。
1)翻开CAITA 软件,利用鼠标中键和左键或右键进展旋转,缩放和移动,生疏绘图界面工具的使用2)点击草绘进入界面,进展简洁零件的设计并在设计过程中学习各种工具的使用➢在翻开的 CAITA 软件上从菜单栏选择【开头】| 【机械设计】 |【零件设计】命令,弹出|【建零部件】对话框,设置好对话框按|【确定】按钮即可进入零件设计平台➢在草绘界面上会看到很多零件设计常用的工具栏有:基于草图特征工具栏、修饰特征工具栏、参考元素工具栏、基于曲面特征、转换特征、等。
通过【基于草图特征】工具栏上的【填充器】工具,可以将草图绘制器中生成的二维草图以多种方式拉伸为三维实体。
单击【填充器】工具的下拉箭头,即可开放全部的【填充器】工具。
通过【基于草图特征】工具栏上的【凹槽】工具,可以通过二维草图,以多种方式在三维实体上进展挖切操作。
单击【凹槽】工具的下拉箭头,即可开放全部的【凹槽】工具,共有三个,分别为凹槽,拔模圆角凹槽,多凹槽;这三个工具与【凸台】的三个工具相对应,各项设置也根本一样。
所不同的是这三项操作是从实体上挖切材料的。
在绘制简洁草图时如以下图:图一图二●对于这种单一平面内的简洁零件只需要依据二维视图照尺寸进展画图,图画完后退出草绘界面,点击凸台进展拉伸即可,但在图一的草绘时要首先确定一个长度在画图过程中要对其加以掌握。
●在画不同截面内的草图如画花瓶时要先建立不同的基准面利用工具栏中参考元素,【参考元素】是指在设计中用到的一些关心的点、线、面。
在【参考元素】工具栏中包含了三个工具【点】工具、【线】工具和【面】工具。
cam实训报告
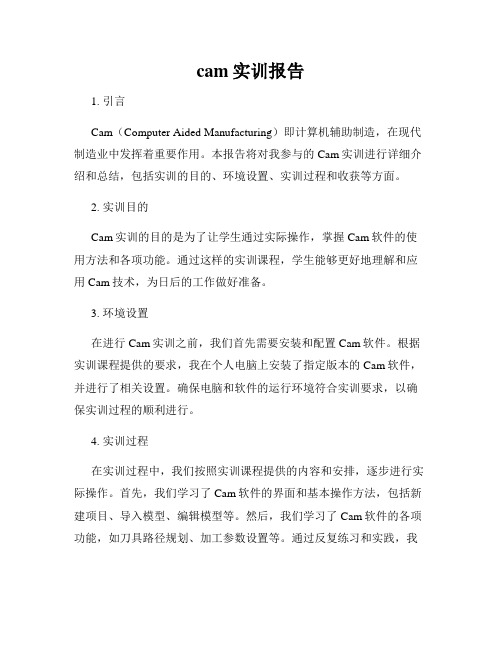
cam实训报告1. 引言Cam(Computer Aided Manufacturing)即计算机辅助制造,在现代制造业中发挥着重要作用。
本报告将对我参与的Cam实训进行详细介绍和总结,包括实训的目的、环境设置、实训过程和收获等方面。
2. 实训目的Cam实训的目的是为了让学生通过实际操作,掌握Cam软件的使用方法和各项功能。
通过这样的实训课程,学生能够更好地理解和应用Cam技术,为日后的工作做好准备。
3. 环境设置在进行Cam实训之前,我们首先需要安装和配置Cam软件。
根据实训课程提供的要求,我在个人电脑上安装了指定版本的Cam软件,并进行了相关设置。
确保电脑和软件的运行环境符合实训要求,以确保实训过程的顺利进行。
4. 实训过程在实训过程中,我们按照实训课程提供的内容和安排,逐步进行实际操作。
首先,我们学习了Cam软件的界面和基本操作方法,包括新建项目、导入模型、编辑模型等。
然后,我们学习了Cam软件的各项功能,如刀具路径规划、加工参数设置等。
通过反复练习和实践,我们逐渐熟悉了Cam软件的使用,并且能够灵活运用各项功能进行模型的加工和制造。
5. 实训收获通过参与Cam实训,我获得了以下收获:5.1 掌握Cam软件的使用方法和各项功能,能够熟练进行模型加工和制造。
5.2 提高了解决问题的能力和应变能力,能够在实际操作中灵活应对各种情况。
5.3 培养了团队合作意识和沟通能力,通过与同学的交流和讨论,我深刻认识到团队协作对于工作的重要性。
5.4 增进了对制造领域的了解,通过实际操作,我更好地理解了Cam技术在制造过程中的重要性和应用价值。
6. 总结通过本次Cam实训,我深刻体会到了理论与实践相结合的重要性。
通过实际操作,我不仅巩固了在课堂上学到的知识,还获得了更多的实际经验。
Cam技术的不断发展和应用,为制造业的发展带来了新的机遇和挑战。
我相信,在日后的工作中,我能够充分运用所学的Cam 技术,为工作的顺利进行做出贡献。
CAM实验报告
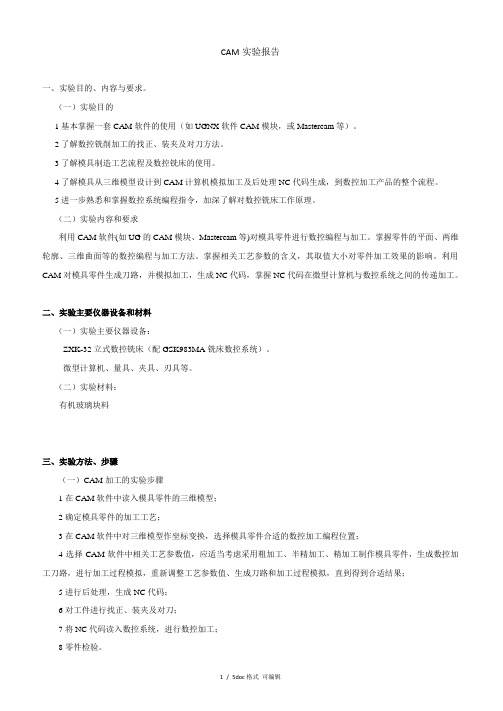
CAM实验报告一、实验目的、内容与要求。
(一)实验目的1基本掌握一套CAM软件的使用(如UGNX软件CAM模块,或Mastercam等)。
2了解数控铣削加工的找正、装夹及对刀方法。
3了解模具制造工艺流程及数控铣床的使用。
4了解模具从三维模型设计到CAM计算机模拟加工及后处理NC代码生成,到数控加工产品的整个流程。
5进一步熟悉和掌握数控系统编程指令,加深了解对数控铣床工作原理。
(二)实验内容和要求利用CAM软件(如UG的CAM模块、Mastercam等)对模具零件进行数控编程与加工。
掌握零件的平面、两维轮廓、三维曲面等的数控编程与加工方法。
掌握相关工艺参数的含义,其取值大小对零件加工效果的影响。
利用CAM对模具零件生成刀路,并模拟加工,生成NC代码,掌握NC代码在微型计算机与数控系统之间的传递加工。
二、实验主要仪器设备和材料(一)实验主要仪器设备:ZXK-32立式数控铣床(配GSK983MA铣床数控系统)。
微型计算机、量具、夹具、刃具等。
(二)实验材料:有机玻璃块料三、实验方法、步骤(一)CAM加工的实验步骤1在CAM软件中读入模具零件的三维模型;2确定模具零件的加工工艺;3在CAM软件中对三维模型作坐标变换,选择模具零件合适的数控加工编程位置;4选择CAM软件中相关工艺参数值,应适当考虑采用粗加工、半精加工、精加工制作模具零件,生成数控加工刀路,进行加工过程模拟,重新调整工艺参数值、生成刀路和加工过程模拟,直到得到合适结果;5进行后处理,生成NC代码;6对工件进行找正、装夹及对刀;7将NC代码读入数控系统,进行数控加工;8零件检验。
四、列出零件数控编程加工的方式及其主要工艺参数。
(一)零件数控编程加工的方式(1)型腔铣去除大量余料(2)平面铣削精加工(3)固定轮廓铣精加工(二)主要工艺参数表操作名刀具刀具选择类型切削方式主轴转速步进量吃刀深度进给率CA VITY_ MILL D12 mill_contour型腔铣1500rpm 刀具平直50%0.5mm 500mmpmFACE_MI LLING_A REA D12 mill_planar平面铣1750rpm 恒定10mm0.2mm 350mmpmFIXED_C ONTOUR B8 mill_contour固定轮廓铣750rpm 恒定0.25550mmpm五、模具零件的三维CAD模型及加工后的模具零件图片。
cam实训报告
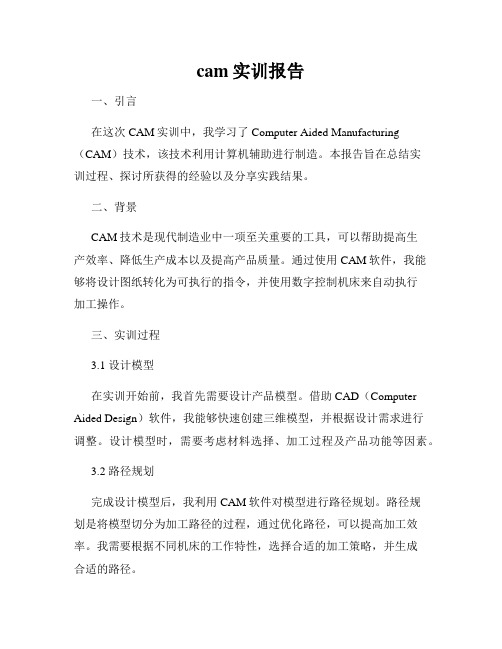
cam实训报告一、引言在这次CAM实训中,我学习了Computer Aided Manufacturing (CAM)技术,该技术利用计算机辅助进行制造。
本报告旨在总结实训过程、探讨所获得的经验以及分享实践结果。
二、背景CAM技术是现代制造业中一项至关重要的工具,可以帮助提高生产效率、降低生产成本以及提高产品质量。
通过使用CAM软件,我能够将设计图纸转化为可执行的指令,并使用数字控制机床来自动执行加工操作。
三、实训过程3.1 设计模型在实训开始前,我首先需要设计产品模型。
借助CAD(Computer Aided Design)软件,我能够快速创建三维模型,并根据设计需求进行调整。
设计模型时,需要考虑材料选择、加工过程及产品功能等因素。
3.2 路径规划完成设计模型后,我利用CAM软件对模型进行路径规划。
路径规划是将模型切分为加工路径的过程,通过优化路径,可以提高加工效率。
我需要根据不同机床的工作特性,选择合适的加工策略,并生成合适的路径。
3.3 制造过程经过路径规划后,我将路径数据导入数字控制机床,进行实际制造过程。
在实际操作中,我需要根据路径要求设置刀具和夹具,并在机床上进行操作。
通过数字控制系统,我能够直观地观察到加工过程,并对其进行调整和优化。
四、实践结果通过CAM实训,我成功完成了一项产品的制造过程。
在实际操作中,我发现CAM技术具有以下优点:1. 提高生产效率:CAM技术将机床操作自动化,减少人工操作时间,提高了加工效率。
2. 降低生产成本:相比传统手工加工,CAM技术大大减少了人力和耗材的使用,降低了生产成本。
3. 提高产品质量:CAM软件可以精确计算每一步操作,消除了人为错误的可能性,提高了产品质量。
4. 灵活性和可重复性:CAM技术可以根据产品设计的不同批次进行快速调整和大规模生产,提高了生产的灵活性和可重复性。
五、总结与展望通过这次CAM实训,我深刻理解了CAM技术对现代制造业的重要性,并获得了实操经验。
cam实训报告

cam实训报告前言近年来,随着机器人技术和智能制造技术的发展,计算机辅助制造(CAM)技术被广泛应用于各行各业。
而在工程领域中,CAM 技术也越来越得到重视。
为了提高学生的实践经验和技能,本文将介绍我在CAM实训课程中的学习和实践经历。
课程介绍CAM是指计算机辅助制造,也就是利用计算机相关软件来协助制造过程的技术。
在CAM课程中,我们学习了AutoCAD和SolidWorks等CAD软件的基础知识和技巧,用来绘制产品的三维模型。
然后我们学习了G代码,这是一种数字语言,用于告诉机床如何移动以制造物品。
最后我们使用MasterCAM软件将三维模型转换为对应的数字化CNC程序,并将其传输到数控机床进行加工。
学习过程在课程的初期,我们主要学习了CAD软件。
我们学习了如何使用SolidWorks创建三维模型,并学习了如何在AutoCAD中进行正交和透视投影。
这些基础知识是理解CAM技术的关键。
接下来,我们学习了数字控制技术。
我们学习了G代码,并了解了在G代码中如何定义坐标系、刀具半径和速度等参数。
我们在课堂上编写了一些简单的G代码程序,并将其上传到数控机床进行加工。
为了更深入地了解数字控制技术,我们分组进行了一个实验。
我们的任务是制作一个简单的立方体零件。
我们首先使用SolidWorks设计了立方体的三维模型,然后将其导出为STL文件,并将其导入到MasterCAM中生成CNC程序。
在数控机床上,我们将预先编写的程序上传到控制器中,并将工件夹在机床上。
经过加工,我们成功地制作了一个小零件。
整个过程都是无人值守的,我们只需等待机床完成加工。
最后,我们在课程的最后阶段使用CAM技术制作了一个大型的零件,其形状为一个大型螺旋体。
我们使用SolidWorks设计了螺旋体的三维模型,并在MasterCAM中编写了数字化CNC程序。
由于零件过于庞大,我们将其分为多个较小的部分,然后将其送到数控机床上进行加工。
整个加工过程持续了数小时,但最终我们成功地制造了一整个螺旋体。
- 1、下载文档前请自行甄别文档内容的完整性,平台不提供额外的编辑、内容补充、找答案等附加服务。
- 2、"仅部分预览"的文档,不可在线预览部分如存在完整性等问题,可反馈申请退款(可完整预览的文档不适用该条件!)。
- 3、如文档侵犯您的权益,请联系客服反馈,我们会尽快为您处理(人工客服工作时间:9:00-18:30)。
华东交通大学材料科学与工程学院模具CAM课程设计说明书题目:清新剂盖子数控加工专业:材料成型及控制工程班级:材料(模具)2013-2 学号:姓名:指导教师:目录第一章零件的三维造型 (3)第二章注塑模向导操作 (3)第三章工艺路线的规划 (4)第四章机械加工设备的选择 (6)第五章机械加工参数的确定 (7)第六章型腔数控加工过程及参数设置 (9)第七章数控加工程序后处理 (17)零件剖视图 (18)总结 (18)第一章零件的三维造型该制件为固体清新剂盒子上盖,外观主要尺寸为直径70mm、高5mm,零件主体厚度为1mm,如图1-1所示:图1-1零件图第二章注塑模向导操作通过注塑模向导进行初始化项目、定义工件、型腔布局、模具分型、加载模架(如图2-1)、建浇口、冷却水道、创建腔体等一系列操作,最终得到一模两腔型腔零件(这是转成stp格式之后的)如图2-2。
整个型腔零件包括浇口衬套、分流道孔、浇口、冷却水道孔、螺钉孔以及型腔。
图2-1图2-2第三章工艺路线的规划3.1 毛胚材料的选择和刀具材料的选择1.毛胚材料从零件的结构组成和几何形状来看,确定该工件为单件生产,主体为平面,局部有圆弧面、凸台及孔加工,主要加工方法为型腔铣和平面铣。
工件的长宽高为(120×110×20mm),采用长方体料,长宽高(122×122×22mm)。
本凹模零件的精度和表面质量要求高,所有采用模锻。
材料选用优质碳素结构钢(中碳钢),45号钢。
2. 刀具材料刀具的强度、刚度、硬度均要比毛坯材料更高,采用高速钢材料。
高速钢(HSS)是一种具有高硬度、高耐磨性和高耐热性的工具钢。
3.2 加工方法的选择⑴平面加工方法的选择:对于面型腔件来说,平面粗糙度要求最高的为Ra3.2,所以选择粗铣-半精铣-精铣这一加工方法就能达到要求。
(2)内外轮廓加工方法的选择:此零件轮廓中的表面粗糙度最高为Ra3.2所以可以采用粗铣-半精铣-精铣的加工方法-。
(3)孔表面加工方法的选择:此零件中因为孔的直径度小于20,且有精度要求,内孔表面采用钻-铰孔这一加工方法。
3.3 加工工序划分为了减小装夹次数,缩短定位时间,采取各表面集中进行加工。
机械加工工序的顺序原则为:基准先行,先主后次,先粗后精,先面后孔。
因此对该零件进行工序的划分为:(1)以粗基准定位铣上表面,因为上表面作为的设计基准和定位基准,表面粗糙度为3.2μm,粗铣-精铣。
(2)加工型腔内表面,粗糙度要求 3.2μm:粗铣--半精铣--精铣。
(3)加工上表面入水口圆孔,粗糙度要求 3.2μm,采用点钻—钻孔。
(4)加工四周表面上的水道圆孔,粗糙度要求 3.2μm,采用点钻—钻孔(5)加工上表面的浇口套孔,粗糙度3.2μm,采用点钻—钻孔(6)检验。
3.4.1型腔表面及孔和流道的加工以上表面进行定位,进行型腔表面的加工。
加工面如图所示:加工该面的各结构由以下工步内容组成:第四章机械加工设备的选择4.1加工机床选择数控铣床X8120。
基本参数如下表:4.2 刀具与量具的选择刀具的选择时数控加工工序设计的重要内容之一,它不仅影响机床的加工效率,而且直接影响加工质量。
所以在选择刀具时应考虑工件材质、加工轮廓类型及刀具的耐用度等因素。
一般情况下应优先选择标准刀具(特别是硬质合金可转位刀具),综合考虑之后决定铣刀、麻花钻的材料为高速钢。
量具的选择:对于双面型腔件在加工过程中测量及完成加工后检验的工具可以选择游标卡尺,游标卡尺是常用的一种量具,它能直接测量零件的外径、内径、长度、宽度、深度和孔径等。
使用简便。
所用的刀具有铣刀,钻刀。
查《机械加工工艺装备设计手册》表2-128和《金属切削手册》表6-2参数如下表:4.3铣床夹具和切削液的选择因为该零件为规则的板类零件,所以选用通用夹具——平口钳冷却方法有浇注法、高压冷却法、喷雾冷却法和二液冷却法,本次加工时选用溶化油水溶液冷却。
第五章机械加工参数的确定5.1加工余量的确定采用锻件、铸造毛坯时,因锻模时的欠压量与允许的错模量不等,铸造时也会因砂型误差、收缩量及毛坯的挠曲与扭曲变形量的不同也会造成加工余量不充分、不稳定,所以,除金属液体的流动性差不能充满型腔等造成余量的不等,此外,锻造、铸造后,毛坯无论锻件、铸件还是型材,只要准备采用数控加工,其加工表面均应有较充分的余量。
根据锻件毛坯余量表,可以查的毛坯在厚度方向的余量为2.1,长度和宽度上的余量为2.5.2铣削方式的确定由于铣床选用的是数控铣床,不具有专一性,且工件为锻件,硬度较高。
所以选择铣削方式为逆铣。
逆铣的方式是铣刀的旋转方向与工件的进给方向相反,铣刀切下的切削层由薄变厚,切削力由小变大。
在铣削力的作用下由于丝杆与螺母总保持接触,因而没有丝杆与螺母间隙对铣削的影响。
5.3切削用量的选择铣削时的铣削用量由切削速度、进给量、背吃刀量(铣削深度)和侧吃刀量(铣削宽度)四要素组成。
切削速Vc,切削速度Vc即铣刀最大直径处的线速度,可由下式计算:一般立铣刀粗铣时的背吃刀以不超过铣刀半径原则,一般不超过7mm ,以防止背吃刀量过大而造成刀具损坏,充分利用刀具的切削性能和铣床的功率、转矩等性能,在保证工序质量的前提下,获得高的生产率和低的加工成本的切削用量。
由《机械加工实用手册》表5.3.16确定粗铣后毛坯余量1.5mm ,半精铣后毛坯余量为1.0mm 。
剩下的由精加工去除。
5.4 切削速度和每齿进给量确定铣削速度V=πDn/1000.(D 为铣刀外径,n 为铣刀转速) 钻削速度V=πDn/1000.(D 为钻刀外径,n 为钻刀转速)铣削时S 齿=S 分/z*n (S 齿为每转过一个齿的走刀量,z 为齿数,n 为转速) 钻削时S 钻头前进的距离=(钻头每分钟前进距离/主轴转速) 计算得:(由5.3的图确定)D=20mm 主轴转速n=20*1000/3.14*20=318.47 r/min ,圆整取318r/min。
进给率=齿数x主轴转速x每齿进给率(看上表)D=24mm 主轴转速n=20*1000/3.14*24=265.39r/min,圆整取265 r/min。
D=6mm 主轴转速n=8*1000/3.14*6=424.63 r/min,圆整取425r/min。
D=4mm 主轴转速n=8*1000/3.14*3=636.94 r/min,圆整取637r/min。
d=6mm 孔加工主轴转速n=15*1000/3.14*6=796.18r/min,圆整取796r/min。
d=4mm 孔加工主轴转速n=15*1000/3.14*4=1194.27r/min,圆整取1194 r/min。
d=3mm 孔加工n=8*1000/3.14*3=849r/min,圆整取850 r/min。
第六章型腔数控加工过程及参数设置6.1型腔表面及四周粗加工过程及参数6.2型腔粗加工过程及参数设置6.3型腔表面粗加工过程及设置型腔表面精加工6.46.5型腔内面精加工过程及参数设置因为是精加工,所以余量为06.5 平面精工过程及参数设置加工效果如下6.6浇口衬套孔钻孔过程及参数设置6.7浇口衬套孔钻孔过程及参数设置6.8 水道钻孔水道加工与上平面螺钉孔加工方法相同,刀具直径同样选择3mm 和6mm 的,但是!定义坐标系时要将加工坐标系移动到侧面!这里不做赘述。
第七章数控加工后处理由于加工程序太长,这里只给出前一部分和后一部分前部分后一部分总结通过这次独立的完成课程设计,从模型设计的建立到最后的模型自动编程,让我更加清楚的认识到了对于UG软件本身及其操作的不足,激发了我玩好这个软件的态度。
并且通过这次课程设计课题的制作,我不仅学会了如何自主学习,如何在不知的情况下于别人合作并且学会了如何在大量的文字图书,电子图书中,如何快速有效的遭到自己所需的信息,从而解决问题。
现在,我敢大胆自信的说,我已经基本掌握了UG建模、自动编程方面的知识,生活中的日用品,只要给我点时间,我都能利用UG建出来。
综合这次实训中,零件图的审查、工艺的设计、刀具和机床夹具的选择、切削用量的选择、UG的建模和编程及后处理等,这一系列的操作完成对零件型腔的设计及加工任务。
在这次实训中,总结了一下几点教训和经验:1、建腔时提示发生错误,可能是目标体和工具体不小心选到了同样的部件:2、孔刀具选择后不能加工不在同一个平面的直径相同的孔:3、在加工处理看加工效果时,如果碰到需要定义毛胚的情况,可能是workpiece里没定义毛坯尺寸,导致后面一直出现需要定义毛胚的情况4、对于刀具的认识还有一些不足,目前知道了刀具加工面时刀具直径应占面的20%,刀具长度在50~70mm时通常选用50mm,产品公差在+-0.05时,刀具产生误差在+-0.01;产品公差在+-0.1时,误差在0.02。
选用多长的刀具,刀刃多长,他们之间的关系以及他们和加工板厚、加工深度之间的关系不清楚5、碰到新问题时,可以用以前做的零件进行试验,观察与现有零件的差别,从而找到解决问题的方法、。
6、加工孔的刀具和加工面的刀具带来的误差是不一样的,之前一直认为是一样的。
总的来说,这次课设让我加强了独立处理事情的能力、分析和解决问题的能力,这对于我的生活和学习都有很大的好处,在此感谢我的同学和老师,让我有了一次充实的课设之旅。