水平轴风力机风轮叶片优化设计模型研究
水平轴风力发电机组风轮叶片优化设计探讨

1风力发 电机组 的工作原理
2 . 2 . 】 额 定 功 率
风 力发 电机 组 的工 作原 理十 分简 单 ,将 状 态 下 , 风 轮 叶 片 最 大 的 输 出效 率 , 当风 轮 叶 风能转化为机 械能,再将机械能转化为 电能, 片处于 最佳 的工作状态则表示机组达到 了额定 实现风力发 电的 目的。风轮叶片在发 电的过程 功率 。额定功率数值的确定决定 了整个机组 的 中发挥十分重 要的作用,通过带动 叶片旋转而 工作状 态和质量 ,科学合 理的数 值设计才能更 加快机组运动 的速度 ,使得发 电机发 电。风力 好地 发挥风力发 电机组本身 的优 势,创造更 大 发 电机 的结构 只要 分为 以下五个部分 :一 是风 的价 值。 轮 ,由多个不 同的叶片组成 ,是带动发 电机 工 2 . 2 . 2额 定 风 速 作的关键部件 ,能够很好地将风能转化为机械 风俗 在 叶片 设计 中十 分关 键,风 力发 电 能 ;二 是机 头 , 支 撑 发 电机 其 他 零 件 , 与机 组 机组的工作原理就 是借助 叶片的转动来产生机 的水平轴有很 大的关系,直接决定 了整个机组 械 能 , 最 终 转 化 为 电能 , 因此 设 计 阶 段 要 重 视 的正常工作 :三是机尾,安装在机头 的后 半部 额定风速的计算 。额定风Байду номын сангаас简单 地说就是额定 分 ,主要 的 目的是保证风轮 的方 向,避 免在风 功率时叶片转动的速度 ,应该 随着额 定功率 的 向发生变化 时出现异常情况 ;四是 回转体 ,这 变化而变化。 个零件 的运转 需要借 助机尾 的力量 五是塔架 , 简单地说就是将风 力发电机组置于 高空 ,减少 外界环境的影响 。
风力发电与风轮机优化设计

三、未来展望
随着科技的不断发展,未来的风轮机优化设计将更加注重智能化、自动化的 设计方法。例如,利用人工智能和机器学习技术对风轮机进行优化设计已经成为 当前的研究热点。此外,随着数字化和智能制造技术的发展,未来的风轮机制造 将更加高效和精准。例如,采用增材制造技术可以显著缩短制造周期,提高生产 效率。
参考内容
随着全球对可再生能源需求的日益增长,风能作为一种重要的清洁能源,其 开发与利用越来越受到人们的。水平轴风力发电机组作为风能利用的主要形式, 其性能的优劣直接影响到风能的转换效率和发电成本。而风轮叶片作为水平轴风 力发电机组的核心部件,其设计优化对于提高机组性能具有至关重要的意义。
一、水平轴风力发电机组概述
参考内容二
随着全球能源结构的转变,可再生能源在能源供应中的地位日益重要。风力 发电作为一种清洁、可再生的能源,在全球范围内得到了广泛的应用。然而,风 力发电的功率输出受到多种因素的影响,如风速、风向、温度等,这些因素的变 化使得风力发电的功率输出具有很大的不确定性。因此,如何提高风力发电系统 的功率预测精度,优化功率预测策略,对于提高风力发电系统的运行效率、降低 运行成本、提高电力系统的稳定性具有重要意义。
3、控制策略优化:风轮机的控制策略对其性能有着重要影响。通过对控制 策略进行优化,可以实现风轮机的自适应调节,以适应不同的风速和风向条件。 例如,采用先进的控制算法,可以实现风轮机的最优控制,提高其发电效率。
4、可靠性提升:在优化设计的过程中,还需要考虑提高风轮机的可靠性。 通过对风轮机的结构和控制系统进行可靠性分析,可以找出潜在的问题和风险, 并采取相应的措施进行改进和预防。例如,采用冗余设计和故障诊断技术,可以 显著提高风轮机的可靠性。
4、实时监测与调整
水平轴风力机风轮叶片优化设计模型研究

本 文建立 了风力 机 风 轮 叶 片 的优 化 设 计模 型 ,在模 型 中考 虑 了风 场 风 速 的概 率 分 布 ,设计 目标 为在 满足额 定 功率 的要求 下 ,年能 量输 出最 大 .在 寻优算 法 中采用 改进 的
遗传 算法 E G E t dd Cmpc G nt C A( x n e o at eei e c
摘
要 :提 出 了 风 力 机 风 轮 叶 片 的 优 化 设 计 模 型 ,该 模 型 考 虑 了 风 场 风 速 的 概 率 分 布 , 以
风 力 机 年 能 量输 出 最 大 为 设 计 目标 ,使 用 遗 传 算 法 进 行 搜 索 寻 优 .利 用 开 发 的 优 化 设 计 程
序 ,设 计 了 13 . MW 风 力 机 的 叶 片 .与 已有 风 力机 相 比 ,设 计 结 果 显 示 了明 显 的优 越 性 ,从
维普资讯
2O O6年 2月
F b. 0) b 2 ( 6
汕 头大学 学报 ( 自然科 学版 )
J u n l t 眦 U ies y ( au a d 眦 ) or a a 叫 nv ri N tr l e t S
第2 卷 l
第 1 期
基 金项 目 : 国家 高 技 术 发 展 (6 ) 划资 助 项 目 ( o 2 A 5 24 ) 8 3计 N :20 A 100 ;广 东 省 科 技 攻 关 资 助 项 目 ( o 05 1212 。 N :20 B 0004
20 B MOO 4 0 5 3 I0 )
维普资讯
优化 设计 程序 .
收 稿 日期 :20 - -2 0 50 0 9
)
进 行 搜 索 寻 优 ,较 之 传 统 算 法 ,
风力发电水平轴叶片设计及动态过程仿真研究
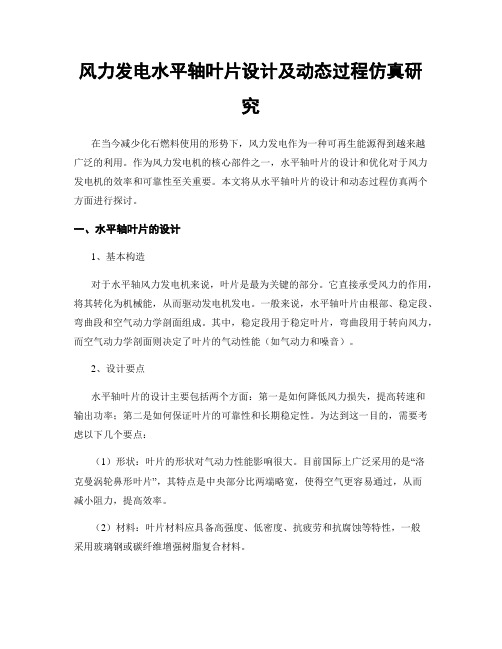
风力发电水平轴叶片设计及动态过程仿真研究在当今减少化石燃料使用的形势下,风力发电作为一种可再生能源得到越来越广泛的利用。
作为风力发电机的核心部件之一,水平轴叶片的设计和优化对于风力发电机的效率和可靠性至关重要。
本文将从水平轴叶片的设计和动态过程仿真两个方面进行探讨。
一、水平轴叶片的设计1、基本构造对于水平轴风力发电机来说,叶片是最为关键的部分。
它直接承受风力的作用,将其转化为机械能,从而驱动发电机发电。
一般来说,水平轴叶片由根部、稳定段、弯曲段和空气动力学剖面组成。
其中,稳定段用于稳定叶片,弯曲段用于转向风力,而空气动力学剖面则决定了叶片的气动性能(如气动力和噪音)。
2、设计要点水平轴叶片的设计主要包括两个方面:第一是如何降低风力损失,提高转速和输出功率;第二是如何保证叶片的可靠性和长期稳定性。
为达到这一目的,需要考虑以下几个要点:(1)形状:叶片的形状对气动力性能影响很大。
目前国际上广泛采用的是“洛克曼涡轮鼻形叶片”,其特点是中央部分比两端略宽,使得空气更容易通过,从而减小阻力,提高效率。
(2)材料:叶片材料应具备高强度、低密度、抗疲劳和抗腐蚀等特性,一般采用玻璃钢或碳纤维增强树脂复合材料。
(3)重量:重量是影响叶片转速和输出功率的因素之一。
一般来说,重量越轻,转速就越高、输出功率就越大。
但是过轻的叶片可能导致振动和损耗加剧,因此需要在轻量化和强度之间找到平衡点。
(4)噪音:噪音是一项重要的考虑因素。
为了减少音量,需要采用优化的叶片形状和节距,并尽可能使叶片转速低于音速。
(5)制造工艺:叶片的制造工艺对于成本和质量至关重要。
传统的手工制造已经逐渐被自动化和数字化制造所代替,使得叶片的生产效率和精度得到了大幅提高。
二、动态过程仿真研究水平轴叶片作为动力机械的核心部件之一,在运行过程中其受力和受力状态会不断发生变化。
为了进一步了解叶片在实际使用中的性能表现和损伤情况,需要通过动态过程仿真研究来模拟叶片的运动过程和受力变化。
水平轴风力机叶片的结构设计与有限元分析
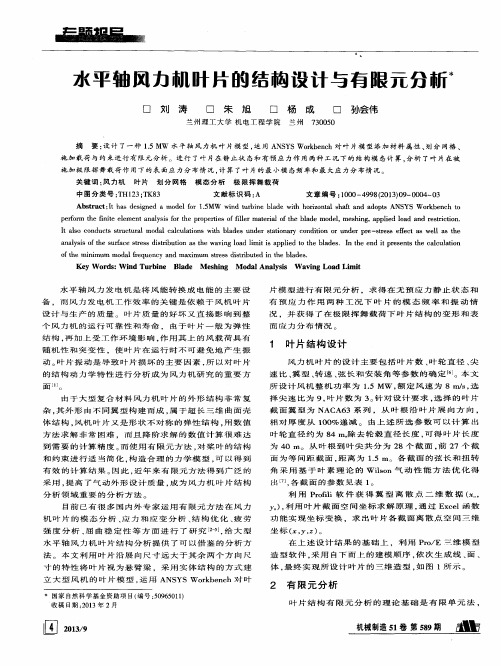
水 平 轴 风 力 发 电 机 是 将 风 能 转 换 成 电 能 的 主 要 设 备 ,而 风 力 发 电机 工 作 效 率 的 关 键 是 依 赖 于 风 机 叶 片 设 计 与 生 产 的 质 量 。 叶 片 质 量 的 好 坏 又 直 接 影 响 到 整 个 风 力 机 的 运 行 可 靠 性 和 寿 命 , 由 于 叶 片 一 般 为 弹 性 结构 , 再 加上 受 工作环 境 影响 , 作 用 其 上 的 风 载 荷 具 有 随 机 性 和 突 变 性 ,使 叶 片 在 运 行 时 不 可 避 免 地 产 生 振 动。 叶 片 振 动 是 导 致 叶 片 损 坏 的 主 要 因素 , 所 以 对 叶 片 的结构 动力 学特 性进 行分 析 成为 风力 机研 究 的重 要方
水平轴风力i I i 几 叶 片 的 结 构 设计 与 有 眼 元 分 新术
口 刘 涛 口 朱 旭 口 杨 成 口 孙会伟
兰 州 理 工 大 学 机 电 工 程学 院 兰州 7 3 0 0 5 0
摘 要 : 设 计 了一 种 1 . 5 MW 水 平 轴 风 力 机 叶 片模 型 , 运用 A N S Y S Wo r k b e n c h对 叶 片 模 型 添 加 材 料 属 性 、 划 分 网格 、 施 加 载 荷 与 约 束进 行 有 限 元 分析 。进 行 了叶 片 在静 止 状 态和 有 预 应 力作 用 两种 工 况 下 的 结 构 模 态计 算 , 分 析 了叶 片在 被 施 加 极 限挥 舞 栽 荷 作 用下 的 表 面 应 力 分 布 情 况 . 计 算 了叶 片 的 最 小模 态频 率 和 最 大应 力 分布 情 况
截 面 翼 型 为 NACA 6 3系 列 , 从 叶 根 沿 叶 片 展 向 方 向 ,
水平轴风力发电机叶片结构设计与优化

水平轴风力发电机叶片结构设计与优化引言水平轴风力发电机作为一种可再生能源发电设备,近年来受到了广泛关注和应用。
而叶片作为水平轴风力发电机的核心组成部分,其结构设计和优化对于提高发电效率和性能至关重要。
本文将探讨水平轴风力发电机叶片结构设计与优化的相关问题,旨在为该领域的研究者和工程师提供一些有益的指导和思路。
叶片设计原则水平轴风力发电机的叶片设计需要考虑多个因素,包括气流特性、风速、轴转速等。
首先,叶片的形状和尺寸应该能够最大程度地捕捉风力,并将其转化为机械能。
其次,叶片应该具备一定的强度和刚度,以抵抗外界风力的作用。
最后,叶片的设计还应该考虑制造成本和可维护性。
叶片结构优化方法在水平轴风力发电机叶片的结构优化过程中,采用计算机辅助工程(CAE)方法可以显著提高效率和准确性。
常见的CAE方法包括有限元分析、计算流体力学、参数化设计等。
有限元分析是一种基于数值计算的方法,通过将叶片分割成有限数量的小元素,对其进行力学和流体力学分析。
这种方法可以帮助工程师评估叶片的应力和变形情况,并根据结果进行结构调整。
通过优化有限元模型,可以使叶片更加均匀地承受载荷,从而提高其强度和稳定性。
计算流体力学方法可以模拟风力对叶片的作用,预测叶片的气动性能。
通过对流场的数值模拟,可以研究叶片在不同风速和攻角下的气动特性,进而优化叶片的形状和构造。
此外,计算流体力学方法还可以预测叶片的阻力和升力系数,以更好地预测水平轴风力发电机系统的性能。
参数化设计是一种基于数学模型的设计方法,通过定义一组变量和参数,对叶片的形状和结构进行系统地优化。
这种方法可以帮助工程师在设计的过程中快速评估多个设计方案,并根据预先设定的优化目标选择最佳方案。
参数化设计方法的优势在于能够显著减少设计和优化的时间成本,提高设计效率。
结论水平轴风力发电机叶片的结构设计和优化是提高发电效率和性能的关键。
合理的叶片设计应考虑气流特性、风速、轴转速等多个因素,并采用计算机辅助工程方法进行优化。
基于水平轴风力机的风能利用技术优化研究

基于水平轴风力机的风能利用技术优化研究在近些年来,随着全球环保意识的不断提升,风能作为一种可再生的绿色能源逐渐受到关注并得到广泛应用。
而在众多风能发电设备中,水平轴风力机因其具有的结构简单、制造成本低、易于维修等优势,成为广大厂家在大规模生产上的首选。
然而,目前市面上普遍采用的水平轴风力机存在着转速慢、能量转换率低、短寿命等问题。
为了进一步提高水平轴风力机的发电效率,从而促进绿色能源的可持续发展,需要对其进行技术优化研究。
一、转速的优化转速是影响水平轴风力机发电效率的主要因素之一。
一般来说,风轮转速越高,则其发电量也越大。
但是,高速旋转不仅会增加机器的摩擦损耗,还会导致飞出物风险等问题的出现。
因此,目前许多研究者尝试采用新型材料、新型设计等方式对风轮进行优化,从而实现转速的提高。
例如,一些研究者提出采用复合材料制造风轮,通过轻量化和提高材料强度等措施,达到提升风轮转速的效果。
另外,还有研究者考虑采用最佳比转速控制策略,即在不损害风力机稳定性的前提下,通过设计合理的控制算法,使风轮保持在最佳转速范围内运行,从而进一步提高风能的利用效率。
二、叶片的设计与优化叶片是水平轴风力机中最核心的组成部分,其设计优化与否直接影响着风能转换的效率。
目前,市面上大部分水平轴风力机采用的叶片结构为传统的三片叶片结构。
但是,由于这种结构存在的支撑强度不足、制造难度大等问题,限制了其发电效率的进一步提升。
因此,目前一些新型的叶片结构逐渐被研究者所关注。
例如,采用柔性悬挂结构的叶片可以在高速旋转时更加稳定,而采用板式或膜式结构的叶片可以减小叶轮制造的难度和成本。
另外,还有部分研究者考虑采用可变叶片结构,通过调整叶片角度和形状,适应不同风速和风向,从而提高发电效率。
三、提高风机的启动和获得风能的能力由于风速的波动和不可控性,风力机的启动和稳定性一直是研究者们关注的重点之一。
为了提高风力机实现对风能点对点的精准捕捉的能力,许多研究者考虑采用新型的启动方式和结构设计。
风力发电机组的优化设计研究

风力发电机组的优化设计研究风力发电是一种十分重要的可再生能源,而风力发电机组的设计优化是提高风能利用效率的关键。
本文将探讨风力发电机组的优化设计研究,并重点关注如何提高发电效率、降低噪音和减少对环境的影响。
第一部分:介绍风力发电机组的基本原理和组成风力发电是利用风能将其转化为电能的过程。
通常,风力发电机组由风轮、发电机和控制系统组成。
风轮通过捕捉风能并将其转换为机械能,再通过发电机将机械能转化为电能。
控制系统用于监控和调节风力发电机组的运行状态。
第二部分:现有风力发电机组存在的问题尽管风力发电技术已经取得了重大突破,但仍然存在一些问题。
首先,发电效率有待提高。
由于风速和风向的变化,风力发电机组在实际运行中可能无法始终进行最有效的风能转化。
其次,噪音问题也需要解决。
风力发电机组在高速旋转时会产生噪音,给周围环境和居民带来困扰。
此外,风力发电机组对鸟类和其他动物的影响也受到广泛关注。
第三部分:发电效率的优化设计研究为了提高风力发电机组的发电效率,可以从多个角度进行优化设计研究。
首先,设计最佳的风轮叶片形状和材料。
借鉴鸟类和海洋动物的形态,可以设计出具有更好气动特性和更高效的风轮叶片。
其次,改进风轮的转动机构。
采用直接驱动发电机而不是传统的机械传动方式,可以减少能量损失和维护成本。
此外,通过智能化控制系统,将风能转化为电能的效率也可以得到提高。
第四部分:噪音控制的优化设计研究为了解决风力发电机组产生的噪音问题,可以采取多种方法进行优化设计研究。
首先,改进风轮的叶片设计。
通过优化叶片的形状和角度,可以减少风轮旋转时产生的气流噪音。
其次,减少机械噪音。
采用低噪音的材料和先进的润滑技术,可以降低机械部件间的摩擦噪音。
此外,合理安排风力发电机组的布局,可以最大程度地减少噪音向周围环境传播。
第五部分:对环境的影响的优化设计研究为了减少风力发电机组对环境的影响,可以从多个方面进行优化设计研究。
首先,合理选择风电场的建设地点。
- 1、下载文档前请自行甄别文档内容的完整性,平台不提供额外的编辑、内容补充、找答案等附加服务。
- 2、"仅部分预览"的文档,不可在线预览部分如存在完整性等问题,可反馈申请退款(可完整预览的文档不适用该条件!)。
- 3、如文档侵犯您的权益,请联系客服反馈,我们会尽快为您处理(人工客服工作时间:9:00-18:30)。
收稿日期:2005_09_02作者简介:刘雄(1975~),男,湖南衡阳人,助理研究员,博士研究生.E_mail:lx@.c n基金项目:国家高技术发展(863)计划资助项目(No:220AA512040);广东省科技攻关资助项目(No:2005B10201024,2005B33401004)文章编号:1001-4217(2006)01-0044-06水平轴风力机风轮叶片优化设计模型研究刘 雄,陈 严,叶枝全(汕头大学能源研究所,广东 汕头 515063)摘 要:提出了风力机风轮叶片的优化设计模型,该模型考虑了风场风速的概率分布,以风力机年能量输出最大为设计目标,使用遗传算法进行搜索寻优.利用开发的优化设计程序,设计了113MW 风力机的叶片.与已有风力机相比,设计结果显示了明显的优越性,从而说明了该优化设计模型的有效性和实用性.关键词:风力机;优化设计;遗传算法;片条理论中图分类号:TK 83 文献标识码:A0 引 言风力机风轮叶片的外形决定了风能转换的效率,因而风轮叶片气动外形的优化设计技术在风力机设计制造中占有相当重要的地位[1-3].早期的优化设计方法是Glauert 方法和Wilson 方法[2,4],其缺点是没有考虑实际风速的概率分布,因而并不能使所设计风力机的年能量输出最大,另外设计结果需大幅修正,设计效果难以控制[2,5].风力机的叶片设计涉及到复杂的气动性能计算及搜索寻优过程,气动性能计算模型的准确度和优化算法的选择直接决定了设计结果的优劣[6].出于技术保密的考虑,国外知名的叶片生产商不对外公开其设计方法,商品化的风力机分析和设计软件也都不包含叶片设计模块[7].因此很有必要研究并掌握风力机叶片设计技术,建立通用的叶片设计软件.本文建立了风力机风轮叶片的优化设计模型,在模型中考虑了风场风速的概率分布,设计目标为在满足额定功率的要求下,年能量输出最大.在寻优算法中采用改进的遗传算法ECG A(Extended C ompact Genetic Algorithm)[8-9]进行搜索寻优,较之传统算法,EC GA 具有更快的寻优速度,并能保证收敛于全局最优解,因而有利于建立通用的叶片优化设计程序.2006年2月Feb .2006汕头大学学报(自然科学版)Jou rnal of Shantou Univers ity (Natu ral Science )第21卷 第1期Vol 121No 111 优化设计数学模型111 设计变量叶片的气动外形由各截面的翼型、弦长和扭角所决定,当使用的翼型系列确定之后,就需要根据设计目标确定每个截面的最佳弦长和扭角.为使叶片主要功率输出段的截面弦长和扭角沿展向连续光滑分布,将弦长c 和扭角t 都定义为按贝塞尔曲线分布,如图1所示,R 为风轮回转半径,r 为截面所在位置的半径.图1 叶片外形的弦长和扭角分布弦长和扭角分布所对应的贝塞尔曲线,都使用了4个控制点,所以总共有16个设计变量,分别为弦长曲线控制点的坐标(x c p i ,y c p i ),i =1,2,3,4;扭角曲线控制点的坐标(x t p i ,y t p i ),i =1,2,3,4.112 适应度函数因为风力机的年能量输出等于风力机的年平均功率和年总时间的乘积,而年总时间为常数,所以在计算中可以使用年平均功率作为设计目标.因此定义适应度函数f (x )为:f (x )= P =Q U out Uinfw(U )P (U )d U(1)式中 P 为平均功率(kW),U 为风速(m #s -1),U in 为切入风速(m #s -1),U ou t 为切出风速(m #s -1),f w (U )为风速的Weibull 分布密度函数,P (U )为风轮在风速为U 时的输出功率(kW).113 约束方程叶片的气动性能计算及搜索寻优,采用了改进的遗传算法ECGA.遗传算法将设计变量称为基因,一般对基因采用二进制编码,所有基因的编码组合起来形成染色体,设计变量的约束条件决定了染色体的长度[10].因为是通用的优化设计程序,所以染色体的长度由用户指定设计变量的约束条件之后由程序自动确定.对于叶片的设计变量采用以下约束方程:45第1期刘 雄等:水平轴风力机风轮叶片优化设计模型研究r min [x c p1<x c p2<x c p3<x c p4[r maxc max \y c p1>y c p2>y c p3>x c p4\c min r min [x t p 1<x t p2<x t p3<x t p 4[r max t max \y t p 1>y t p2>y t p 3>x t p4\t min(2)其中r min ,r max 分别为用户定义的叶片优化设计段的截面最小半径和最大半径,c min ,图2 优化设计程序流程图c max 分别为用户定义的允许的最小和最大弦长,t min ,t max 分别为用户定义的允许的最小和最大扭角.2 优化设计程序在求解个体的适应度函数时,需要计算个体的气动性能,所以气动性能的准确度对优化设计结果影响较大.本文采用片条理论[1-2,6,11-12]计算气动性能,计算模型考虑了叶尖损失、轮毂损失、叶栅理论及失速状态下动量理论失效的修正,并且考虑了风剪、偏航、风轮结构参数和风力机安装参数的影响,保证了气动性能计算的精确性.其计算结果与英国Garrad Hassa n &Partners 公司开发的风力机全方位气动性能分析和载荷计算的商业软件包Bladed for Windows[7,13-14]良好吻合[12].所设计的叶片优化设计程序基本流程如图2所示.3 优化设计实例应用优化设计程序,参考合作单位提供的113MW 风力机的基本参数,设计了113MW 风力机的叶片,设计叶片的对比对象是合作单位为113MW 风力机设计并制造的叶片.311 设计参数风轮、风况参数及ECGA 指定的参数如表1所示.表1 风轮、风况及EC GA 参数风轮直径P m 桨叶数量额定风速P (m #s -1)额定功率P MW 风轮转速P (r #mi n -1)风轮中心高度P m 603151131960桨叶安装角P (b )风轮锥角P (b )转轴倾角P (b )轮毂中心到塔架中心距离P m轮毂直径P m 翼型系列04122NACA63_446汕头大学学报(自然科学版)第21卷空气密度P (kg #m -3)经验风剪指数参考高度P m 染色体长度切出风速P (m #s -1)切入风速P (m #s -1)1122501166676095255种群大小竞争规模Weibull 形状参数Wei bull 标度参数P (m #s -1)10001611851115312 设计结果叶片的气动外形设计结果可参看图4所示的气动外形对比图,所设计风力机的功率P 和功率系数C P 曲线如图3所示.图3 风力机功率和功率系数曲线4 与已有叶片的比较图4显示了所设计的叶片与合作单位提供的113MW 风力机叶片的气动外形对比.图4 弦长、扭角和相对厚度分布的对比分别对所设计的风力机与合作单位的风力机进行气动性能计算,功率及功率系数的计算结果如表2所示.47第1期刘 雄等:水平轴风力机风轮叶片优化设计模型研究表2功率和功率系数对比风速P(m#s-1)尖速比功率P kWP1(已有叶片)P2(设计叶片)功率系数已有叶片设计叶片(P2-P1)P P151119431128062120801144501287498187%691951121120143145101299701383527194%781532211079249119601372201419512172%87146355125437715970140070142596129%96163502135951814180139790141063120% 105197654187966612650137810138471174% 115143800185681613990134740135421194% 124197927115895812780130980132023136% 13415910291000108510000127040128525144% 14412611031000119610000123200125178143% 153198114610001278100001196001218711152% 163173117210001315100001165201185312120% 17315111861000129910000113940115279153% 18313211561000125110000111450112388122% 19311410761000117410000109060109899111% 20219897310441090100001070201078712102% 21218489013321002100001055501062512154% 2221718401045938117601045601050911168% 232160827100490212270103920104289110% 242149829148788615820103460103706188% 252139832137989019010103080103297103%从表2可以看出,在整个工作风速范围内,所设计的叶片性能明显优于合作单位提供的叶片.起动风速处所设计风力机的功率几乎两倍于已有的风力机,说明所设计的叶片具有良好的起动性能.假设当风速在工作范围内时风力机不停机,那么设计风力机的年能量输出为5116@106kWh,而合作单位风力机的年能量输出为418@106kWh,相比之下年能量输出提高了715%。
5结论1)考虑风场风速的概率分布,以年能量输出最大为设计目标,使用遗传算法执行搜索寻优过程,建立了风力机风轮叶片的优化设计模型;2)设计了113MW风力机叶片,与已有的113MW风力机叶片的对比,显示了设计结果明显的优越性,从而说明了该优化设计模型的有效性与实用性.48汕头大学学报(自然科学版)第21卷参考文献:[1]Det Norske Veritas and Ris <National Laboratory.Guidelines for design of wind Turbines [M ].Norway:Det Norske Veri tas and Ris <National Laboratory,2002.[2]Spera D A.Wind turbine technology[M].New York:AS ME Press,1994.[3]Fuglsang P L,Madsen H A.A design study of a 1MW s tall regulated rotor[R].Denmark:Ris <National Lab -oratory,1995.[4]Robert E W,Peter B S,Stel N W.Aerodynamic performance of wind turbines[M].US A:Oregon State Un-i versity,1976.[5]刘雄,陈严,叶枝全.风力机桨叶总体优化设计的复合形法[J].太阳能学报,2001,2(2):157-161.[6]刘雄.水平轴风力机气动与结构C AD 系统集成研究[D].汕头:汕头大学,1999.[7]David P M,Sjoerd Dijkstra.State_of_the_art of wind turbine design codes:main features overview for cost_effec -tive generation[J].Wind Engineering,1999,23(5):295-311.[8]Georges Harik.Linkage learnin g via probabilistic modeling in the ECGA[R].IlliGAL Rep ort:99010,1999.[9]Fernando Lobo,Georges Harik.Extended compact genetic algorithm in C++[R].IlliGAL Report:99016,1999.[10]Mitsuo Gen,Run wei Cheng.Genetic algori thms and engineering opti mization(engineering desi gn and automation)[M].Wiley_In terscience,1999.[11]刘雄,陈严,叶枝全.风力机气动与结构CAD 软件[J].太阳能学报,2001,22(3):346-350.[12]刘雄,陈严,叶枝全.水平轴风力机气动性能计算模型[J].太阳能学报,2005,26(6):792-800.[13]Garrad Hassan &Partners.Bladed [EB P OL].[2005_07_03].http:P P P bladed P bladed.htm.[14]Bossanyi E A.Bladed for Windows _theory manual[Z].England:Garrad Hassan &Partners Li mited,1999.Research on the HA WT Rotor Blades Optimization(LIU Xiong ,C HE N Yan ,YE Zhi _quan )(Institute of Energy Scie nce,Shantou Universi ty,Shantou 515063,Guangdong,China)Abstract :An optimization model for rotor blades of horizontal axis wind turbines is presented in this paper.The model refers to the wind speed distribution function on the specific wind site with the ob -jective to satisfy the maximum annual energy output,using genetic algorithm to carry on the search process.Based on the developed optimization program,the blades of a 113MW wind turbine are de pared with an existing 113MW wind turbine,the design sho ws obvious advantages,which verifies effec tivities and functionalities of the optimization model.Key words :wind turbine;optimal design;genetic algorithm;strip the ory49第1期刘 雄等:水平轴风力机风轮叶片优化设计模型研究。