橡胶试验
橡胶耐低温试验标准

橡胶耐低温试验标准橡胶耐低温试验是评价橡胶材料在低温环境下性能的关键试验之一。
下面是相关的参考内容:一、橡胶耐低温试验的目的和意义:1. 评估橡胶材料在低温环境下的弹性性能和机械性能;2. 预测橡胶制品在低温环境下的导热性、耐疲劳性和耐裂纹扩展性;3. 检测橡胶材料的冷却塑性和低温脆性。
二、橡胶耐低温试验的常用方法:1. 低温弯曲试验:将试样在规定温度下进行弯曲,观察其表面是否有裂纹、开裂或其他变化。
2. 低温压缩变形试验:将试样在规定温度下进行压缩变形,观察其恢复程度和变形量。
3. 低温撕裂试验:在规定温度下进行撕裂试验,评估橡胶拉伸破坏时的变形和裂纹扩展情况。
4. 低温压缩硬度试验:通过测量试样在低温下的硬度变化,评估橡胶的变形性能。
5. 低温断裂拉伸试验:测定试样在低温下的拉伸强度和伸长率,评估橡胶在低温下的拉伸性能。
三、橡胶耐低温试验的相关标准:1. GB/T 1689-1998 橡胶耐低温试验方法该标准规定了用于评价橡胶和橡胶制品在低温下的耐冷却塑性和低温脆性的试验方法。
2. ISO 812-2000 橡胶和塑料凹版耐低温试验方法该标准规定了用于评价橡胶和塑料凹版在低温环境下的耐低温性能的试验方法。
3. ASTM D1329-2020 橡胶和乳胶耐低温试验方法该标准适用于评估橡胶和乳胶在低温下的耐低温特性,包括硫化橡胶、架桥橡胶、热塑性橡胶、乳胶和丁腈橡胶等。
4. JIS K 6263-2020 橡胶和塑料耐低温试验方法这是日本工业标准,规定了评价橡胶和塑料在低温下的耐低温特性的试验方法。
四、橡胶耐低温试验的结果和参数:1. 低温破坏温度:指在低温下橡胶的断裂温度,一般取试样断裂的温度作为该参数。
2. 低温拉伸强度:在低温下进行拉伸试验,测定试样的拉伸强度,以评价橡胶的抗拉能力。
3. 低温延伸率:在低温下进行拉伸试验,测定试样的伸长率,以评价橡胶的延展性。
4. 低温硬度:通过测量试样在低温下的硬度变化,评估橡胶的变形性能。
橡胶制品十五种常见试验测试项目和标准

橡胶制品十五种常见试验测试项目和标准1.胶料硫化特性GB/T 9869—1997橡胶胶料硫化特性的测定(圆盘振荡硫化仪法)GB/T16584—1996橡胶用无转子硫化仪测定硫化特性ISO 3417:1991橡胶—硫化特性的测定——用摆振式圆盘硫化计ASTMD2084-2001用振动圆盘硫化计测定橡胶硫化特性的试验方法ASTM D5289-1995(2001)橡胶性能—使用无转子流变仪测量硫化作用的试验方法DIN53529-4:1991橡胶—硫化特性的测定——用带转子的硫化计测定交联特性。
2.橡胶拉伸性能GB/T528—1998硫化橡胶或热塑性橡胶拉伸应力应变性能的测定ISO37:2005硫化或热塑性橡胶——拉伸应力应变特性的测定ASTMD412-1998(2002)硫化橡胶、热塑性弹性材料拉伸强度试验方法JISK6251:1993硫化橡胶的拉伸试验方法DIN 53504-1994硫化橡胶的拉伸试验方法。
3.未硫化橡胶门尼粘度GB/T1232.1—2000未硫化橡胶用圆盘剪切粘度计进行测定—第1部分:门尼粘度的测定GB/T1233—1992橡胶胶料初期硫化特性的测定—门尼粘度计法ISO289-1:2005未硫化橡胶——用剪切圆盘型黏度计—第一部分:门尼黏度的测定ISO289-2-1994未硫化橡胶——用剪切圆盘型黏度计测定—第二部分:预硫化特性的测定ASTMD1646-2004橡胶粘度应力松驰及硫化特性(门尼粘度计)的试验方法JISK6300-1:2001未硫化橡胶-物理特性-第1部分:用门尼粘度计测定粘度及预硫化时间的方法。
4.压缩永久变形性能GB/T 7759-1996硫化橡胶、热塑性橡胶在常温、高温和低温下压缩永久变形测定ISO815:1991硫化橡胶、热塑性橡胶在常温、高温和低温下压缩永久变形测定ASTM D395-2003橡胶性能的试验方法压缩永久变形JIS K6262:1997硫化橡胶及热塑性橡胶压缩永久变形试验方法。
橡胶材料力学性能测试方法

橡胶材料力学性能测试方法橡胶材料是一种具有高弹性和耐磨性的材料,广泛应用于汽车、电子、建筑等各行各业。
为了确保橡胶材料的质量和性能,需要对其进行力学性能测试。
本文将介绍一些常见的橡胶材料力学性能测试方法。
1. 拉伸试验拉伸试验是评估橡胶材料拉伸性能的常用方法。
该试验使用拉伸试验机,将橡胶样品固定在两个夹具之间,施加拉力逐渐增加,记录拉力和伸长率的变化。
通过拉伸试验可以获得橡胶的强度、伸长率、断裂强度等性能指标。
2. 压缩试验压缩试验用于评估橡胶材料的弹性和抗压性能。
该试验使用压缩试验机,将橡胶样品置于平板夹具之间,施加垂直压力逐渐增加,记录压力和变形的变化。
通过压缩试验可以获得橡胶的抗压强度、压缩模量等性能指标。
3. 硬度测试硬度测试用于评估橡胶材料的硬度和弹性特性。
常见的硬度测试方法有杜氏硬度测试和洛氏硬度测试。
杜氏硬度测试使用硬度计,通过测量针头对橡胶材料的穿透深度来判断硬度。
洛氏硬度测试使用硬度计,通过测量钢球的反弹高度来判断硬度。
硬度测试结果可用于比较不同橡胶材料的硬度和弹性特性。
4. 压痕测试压痕测试用于评估橡胶材料的耐磨性能和硬度。
常见的压痕测试方法有杜拉布试验和布氏硬度试验。
杜拉布试验使用杜拉布硬度计,在一定载荷下,将橡胶样品与砂纸接触并施加往复运动,记录橡胶样品的耐磨性能。
布氏硬度试验使用布氏硬度计,通过测量钻头在橡胶样品上产生的压痕直径来评估硬度和耐磨性能。
5. 动态力学分析动态力学分析用于评估橡胶材料的动态性能和频率响应。
常见的动态力学测试方法有动态拉伸试验和复合模量测试。
动态拉伸试验使用动态力学分析仪,施加连续变化的拉伸载荷,记录橡胶样品在不同频率下的力学性能。
复合模量测试使用复合模量测试仪,测量橡胶样品在不同温度和频率下的动态模量和耗散因子。
以上是几种常见的橡胶材料力学性能测试方法。
通过这些测试方法,可以客观评估橡胶材料的强度、弹性、硬度、抗压性能、耐磨性能等关键指标。
这些测试结果对于橡胶材料的选择、设计和质量控制具有重要意义,能够保证橡胶制品的性能和可靠性,满足各行各业的需求。
橡胶曲挠试验标准

橡胶曲挠试验标准
橡胶曲挠试验是衡量橡胶材料柔韧性和耐久性的重要方法之一。
该试验通常涉及将橡胶样本固定在两个支撑点之间,然后施加一定的荷载,以测量其曲挠程度和变形能力。
橡胶曲挠试验的标准可分为两类:基本试验和应用试验。
基本试验旨在确定橡胶样本的机械特性,包括弹性模量、强度、断裂延伸率等。
应用试验则更加关注橡胶材料在实际应用中的性能,例如耐久性、耐疲劳性、环境适应性等。
根据不同的标准,橡胶曲挠试验的具体方法和参数会有所不同。
一般来说,试验中需使用一定的荷载(如拉伸荷载或压缩荷载),并测量样本在荷载作用下的曲挠程度和变形能力。
同时,试验条件也应符合相关标准,如温度、湿度、试样几何形状等。
橡胶曲挠试验的标准对于评估橡胶材料的性能非常重要,也有助于制定相关的质量控制和产品设计标准。
因此,相关行业的研究人员和企业都应该熟悉并遵守这些标准。
- 1 -。
橡胶伸张疲劳试验

橡胶伸张疲劳试验橡胶伸张疲劳试验是材料力学试验中常用的试验之一,主要用于评估橡胶材料的强度和耐久性。
该试验能够模拟真实情况下橡胶材料反复拉伸的过程,从而获取材料在不同应力下的性能数据。
下面,我将详细介绍橡胶伸张疲劳试验的步骤。
步骤一:样品制备首先,我们需要准备好试验所需的橡胶样品。
样品的尺寸和形状应根据具体的试验要求进行设计。
通常,样品宽度为10mm左右,长度为100mm左右,厚度为2mm左右。
步骤二:装置搭建将样品安装到试验机的夹持装置中,确保夹具与样品牢固连接。
选择相应的试验参数,将试件放入试验机中。
一般来说,根据试验目的和要求,可以选择的参数包括拉伸速度、拉伸幅度、拉伸次数、温度等。
步骤三:试验执行试验机开始拉伸样品。
拉伸应保证逐渐递增直至疲劳断裂或达到最大载荷。
在拉伸过程中,试验机将材料牵伸到最大位移或道程,然后逐渐减小应力,使其回到初始坐标位置。
步骤四:数据记录在试验过程中,需要记录各种试验参数以及样品的应变、应力、位移等数据。
此外,在一些高级试验中,还需要通过图像计算或其他手段对材料的弹性、应力和应变等性能参数进行检测和计算。
步骤五:数据处理试验结束后,需要对试验所得数据进行处理和分析。
通过数据分析和图形绘制,可以得到橡胶材料在不同应力下的拉伸行为和疲劳寿命等相关信息。
总之,橡胶伸张疲劳试验是一项重要的材料力学试验,通过该试验可以评估橡胶材料的强度和耐久性。
试验流程划分为样品制备、装置搭建、试验执行、数据记录以及数据处理等几个步骤,每一步都需要仔细操作,以确保试验能够取得准确可靠的结果。
橡胶测试标准

橡胶测试标准橡胶是一种常见的弹性材料,广泛应用于汽车轮胎、橡胶制品、工业设备等领域。
为了确保橡胶制品的质量和性能,需要进行各种测试,以便评估其物理、化学和机械特性。
橡胶测试标准是指对橡胶材料进行测试时所遵循的一系列规范和程序,以确保测试结果的准确性和可比性。
本文将介绍橡胶测试标准的相关内容,包括常见的测试项目和标准规范。
一、拉伸试验。
拉伸试验是评估橡胶材料弹性和抗拉性能的重要方法。
根据ASTM D412标准,橡胶拉伸试验应在标准试样上进行,通过施加拉力来测定其拉伸强度、断裂伸长率和模量等指标。
这些指标能够反映橡胶材料的拉伸性能,对于不同用途的橡胶制品具有重要的参考价值。
二、硬度测试。
硬度是衡量橡胶材料硬度和弹性的重要参数。
常见的硬度测试方法包括 shore硬度测试和durometer硬度测试。
根据ISO 7619标准,shore硬度测试是通过在材料表面施加一定深度的压痕来测定橡胶的硬度,而durometer硬度测试则是通过测量材料在受力下的变形程度来评估其硬度。
这些测试方法能够帮助确定橡胶材料的硬度和弹性,对于材料选择和质量控制具有重要意义。
三、耐磨性测试。
橡胶制品通常需要具有良好的耐磨性能,以确保其在使用过程中不易磨损和老化。
根据ISO 4649标准,耐磨性测试是通过在一定条件下对橡胶材料进行磨损试验,以评估其耐磨性能。
这项测试能够帮助制造商了解橡胶制品的耐磨性能,从而进行材料改进和质量控制。
四、耐油性测试。
橡胶制品在工业设备和汽车等领域中经常接触到各种润滑油和化学品,因此需要具有良好的耐油性能。
根据ASTM D471标准,耐油性测试是通过将橡胶试样浸泡在不同种类的润滑油中,以评估其在不同介质中的耐油性能。
这项测试能够帮助制造商选择合适的材料,并确保橡胶制品在实际使用中具有良好的耐油性能。
五、老化性能测试。
橡胶制品在使用过程中会受到氧化、紫外线、温度等因素的影响,因此需要具有良好的耐老化性能。
橡胶voc成分试验

橡胶voc成分试验橡胶VOC成分试验是对橡胶制品中挥发性有机化合物(VOC)含量的检测方法。
VOC是一类具有挥发性的有机化合物,常见的有甲苯、二甲苯、苯、乙苯、丙烷等。
这些化合物对人体健康和环境都有一定的影响,因此对橡胶制品中的VOC含量进行检测至关重要。
橡胶制品广泛应用于汽车、建筑、电子、家居等领域,如轮胎、密封件、管道等。
在使用过程中,橡胶制品会释放出一些化合物,这些化合物可能对人体健康和环境造成污染。
因此,通过对橡胶制品中VOC成分的检测,可以评估其对环境和人体的潜在风险。
橡胶VOC成分试验的方法有多种,常见的包括热解吸附法、热脱附法和气相色谱法等。
其中,热解吸附法是一种常用的方法。
该方法是将橡胶样品加热,在一定的温度下,利用吸附剂吸附橡胶中的VOC成分,然后通过热脱附的方式将吸附的VOC成分释放出来,并利用气相色谱仪进行分析和定量。
在进行橡胶VOC成分试验时,首先需要准备好样品和试验设备。
样品应该是代表性的,可以根据实际使用情况选择。
试验设备包括加热装置、吸附剂、热脱附装置和气相色谱仪等。
在试验过程中,首先将样品放置在加热装置中,根据试验要求设置合适的温度和时间。
然后,将吸附剂放置在样品附近,使其吸附橡胶中的VOC成分。
在吸附完成后,将吸附剂取出,放置在热脱附装置中,通过升温的方式将吸附的VOC成分脱附出来。
最后,将脱附出来的VOC成分通过气相色谱仪进行分析和定量。
通过橡胶VOC成分试验,可以得到橡胶制品中VOC成分的含量。
根据不同的国家和行业标准,对VOC成分的含量有一定的限制。
通过与标准进行比较,可以评估橡胶制品是否符合相应的要求。
如果VOC成分超过了限制,可能会对环境和人体造成潜在的危害,需要采取相应的措施进行改进或替换。
橡胶VOC成分试验在橡胶制品的生产和质量控制中具有重要的意义。
通过对VOC成分的检测,可以帮助企业了解产品的质量状况,及时发现问题并采取措施进行改进。
同时,对于消费者来说,选择符合标准的橡胶制品也是保护自身健康和环境的重要手段。
橡胶耐低温试验标准
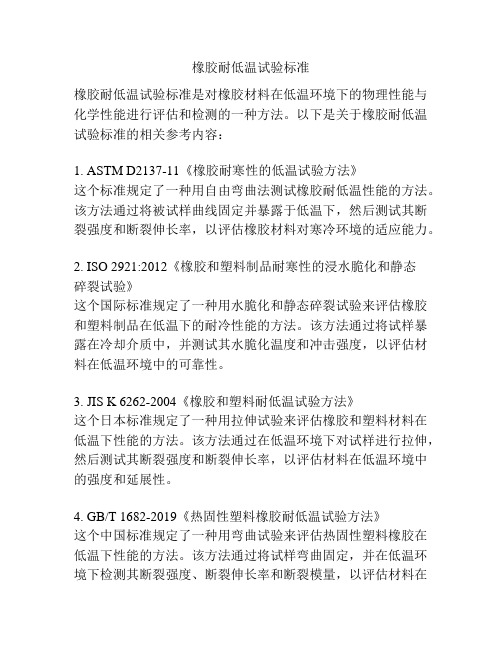
橡胶耐低温试验标准橡胶耐低温试验标准是对橡胶材料在低温环境下的物理性能与化学性能进行评估和检测的一种方法。
以下是关于橡胶耐低温试验标准的相关参考内容:1. ASTM D2137-11《橡胶耐寒性的低温试验方法》这个标准规定了一种用自由弯曲法测试橡胶耐低温性能的方法。
该方法通过将被试样曲线固定并暴露于低温下,然后测试其断裂强度和断裂伸长率,以评估橡胶材料对寒冷环境的适应能力。
2. ISO 2921:2012《橡胶和塑料制品耐寒性的浸水脆化和静态碎裂试验》这个国际标准规定了一种用水脆化和静态碎裂试验来评估橡胶和塑料制品在低温下的耐冷性能的方法。
该方法通过将试样暴露在冷却介质中,并测试其水脆化温度和冲击强度,以评估材料在低温环境中的可靠性。
3. JIS K 6262-2004《橡胶和塑料耐低温试验方法》这个日本标准规定了一种用拉伸试验来评估橡胶和塑料材料在低温下性能的方法。
该方法通过在低温环境下对试样进行拉伸,然后测试其断裂强度和断裂伸长率,以评估材料在低温环境中的强度和延展性。
4. GB/T 1682-2019《热固性塑料橡胶耐低温试验方法》这个中国标准规定了一种用弯曲试验来评估热固性塑料橡胶在低温下性能的方法。
该方法通过将试样弯曲固定,并在低温环境下检测其断裂强度、断裂伸长率和断裂模量,以评估材料在低温环境中的可靠性和适用性。
5. GB/T 10153-2015《橡胶和塑料脆化温度的浸水脆化试验方法》这个中国标准规定了一种用浸水脆化试验来评估橡胶和塑料材料在低温下性能的方法。
该方法通过将试样暴露在冷却介质中,并对试样进行弯曲测试,测试其断裂温度和冲击强度,以评估材料在低温环境中的耐寒性。
总之,橡胶耐低温试验标准是评估橡胶材料在低温环境下性能的重要依据。
通过这些试验标准,可以对橡胶材料在低温环境中的耐寒性能进行全面、客观和准确的评估,为材料的选择和应用提供科学的依据。
- 1、下载文档前请自行甄别文档内容的完整性,平台不提供额外的编辑、内容补充、找答案等附加服务。
- 2、"仅部分预览"的文档,不可在线预览部分如存在完整性等问题,可反馈申请退款(可完整预览的文档不适用该条件!)。
- 3、如文档侵犯您的权益,请联系客服反馈,我们会尽快为您处理(人工客服工作时间:9:00-18:30)。
橡胶轮胎企业物理试验培训教材第一章总则为更好的适应轮胎行业的发展,对轮胎企业生产过程中的原材料、半成品进行有效监控,以达到提高产品质量的目的,特制订本教材,以适应各企业物理实验室新入职员工的岗前培训需要。
本教材包含以下部分:(1)常用橡胶用原材料(2)半成品胶料的试验方法(3)硫化胶强伸性能试验方法(4)原材料物理试验(5)橡胶测试的一般要求第二章常用的橡胶用原材料轮胎生产中使用的原材料主要包括以下几大类:1、生胶2、活性剂3、补强填充剂4、防老剂5、硫化剂6、促进剂7、树脂和粘合剂8、防焦剂9、骨架材料1 生胶轮胎生产中使用的生胶包括天然橡胶和合成橡胶。
天然橡胶是由天然胶树上割取所得,天然橡胶以其优异的综合性能长期以来为轮胎生产企业广泛使用。
合成橡胶由人工合成,它们往往具有某种方面的显著特性而被轮胎生产利用。
1.1 天然橡胶天然橡胶可分为标准胶(又称颗粒胶)、烟胶片、浓缩胶、白绉胶片、浅色胶片、胶清橡胶和风干胶片等,最常用的是标准胶和烟胶片。
标准胶分为一级、二级、三级、四级四个等级,烟胶分成1~5号烟胶片(RSS1~RSS5)五个等级。
标准橡胶以其稳定的门尼粘度、良好的可塑性被大部分轮胎生产企业用作车间生产中。
如今轮胎企业中使用的标准橡胶的主要品种有:SVR(越南标准胶)、SIR(印尼标准胶)、SMR (马来西亚标准胶)、STR(泰国标准胶)。
标准橡胶是呈黄褐色的块状固体,一般每块重量为35或40千克。
对于天然橡胶的入厂检验,除了检验塑性初值及塑性保持率外,还要进行挥发份、灰分、含氮量等化学成分检测。
采用国标配方对天然橡胶进行小配合混炼操作后,对硫化胶进行拉伸性能的测定,注意衡量指标为拉伸强度、扯断伸长率。
1.2 合成橡胶合成橡胶多具有某一种方面的特性。
轮胎生产中使用的合成橡胶品种主要包括:苯乙烯-丁二烯橡胶(丁苯橡胶)、丁二烯橡胶(顺丁橡胶)、丁腈橡胶、异戊橡胶、丁基橡胶等。
1.2.1 苯乙烯-丁二烯橡胶(丁苯橡胶)苯乙烯-丁二烯橡胶(),英文简称为SBR。
SBR为苯乙烯和丁二烯聚合而成,是橡胶工业中使用量最大的合成橡胶。
常用的丁苯橡胶牌号主要包括SBR1500、SBR1502、SBR1705、SBR1712。
前两种为低温乳聚丁苯橡胶、后两种为低温乳聚充油丁苯橡胶。
丁苯橡胶具有以下优缺点:优点:硫化曲线平坦,胶料不易烧焦和过硫;耐磨性、耐热性、耐油性和耐老化性等均比天然橡胶好,高温耐磨性好,适用于乘用胎;在加工过程中相对分子质量降低到一定程度不再降低,因而不易过炼,可塑度均匀,硫化橡胶硬度变化小;提高相对分子质量可以实现高填充,充油橡胶的加工性能好;容易与其他高不饱和通用橡胶并用,尤其是与天然橡胶或顺丁橡胶并用,经配合调整可以克服丁苯橡胶的缺点。
缺点:纯丁苯橡胶强度低,需要加入高活性补强剂后方可使用;丁苯橡胶加配合剂比天然橡胶难度大,配合剂在丁苯橡胶中分散性差;反式结构多,侧基上带有苯环。
因而滞后损失大,生热高,弹性低,耐寒性也稍差,但充油后可以降低生热;收缩大,生胶强度低,粘性差;硫化速度慢;耐屈挠龟裂性天然橡胶好,但裂纹扩展速度快,热撕裂性能差。
(1)SBR1500为血红色块状固体,一般包装为25kg/块。
(2)SBR1502为乳黄色块状固体,一般包装为25kg/块。
(3)SBR1705为棕褐色块状固体,一般包装为25kg/块。
(4)SBR1712为灰褐色块状固体,一般包装为25kg/块。
1.2.2 丁二烯橡胶(顺丁橡胶)顺丁橡胶英文简称为BR。
顺丁橡胶是橡胶工业中用量仅次于丁苯橡胶的一种合成橡胶。
顺丁橡胶根据其顺式结构的含量可分为高顺丁橡胶、中顺丁橡胶和低顺丁橡胶。
顺丁橡胶的优缺点如下:1)优点(1)高弹性。
高顺式丁二烯橡胶是当前所有橡胶中弹性最高的一种橡胶,甚至在很低的温度下,分子链段都能自由运动,所有能在很宽的温度范围内保持高弹性,甚至在-40℃时还能保持,与天然橡胶或丁苯橡胶并用时,能改善它们的低温性能。
(2)滞后损失和生热小。
由于高顺式丁二烯橡胶分子链段的运动所需要克服的周围的分子链的阻力和作用力小,内摩擦小,当作用于分子的外力去掉后,分子能较快的恢复原状,因此滞后损失小,生热小。
这一性能对于使用时反复变形,且传热差的轮胎的使用寿命具有一定好处。
(3)低温性能好。
玻璃化温度低,为-105℃左右。
所以掺用高顺式丁二烯橡胶的胎面在寒带地区仍可保持较好的使用性能。
(4)耐磨性能优异。
(5)耐屈挠性优异(6)填充性好。
与丁苯橡胶和天然橡胶相比,高顺式丁二烯橡胶可填充更多的操作油和补强填料,有较强的炭黑湿润能力,可使炭黑较好的分散,因而可保持较好的胶料性能,有利于降低胶料成本。
(7)混炼时抗破碎能力强。
混炼过程中丁二烯橡胶门尼粘度下降的幅度比天然橡胶小得多,比丁苯橡胶也小,因此在需要压出混炼时间时,对胶料的口型膨胀及压出速度几乎无影响。
2)缺点(1)拉伸强度与撕裂强度低,因此,掺用顺丁橡胶的轮胎胎面多表现为不耐刺扎,较易刮伤。
(2)抗湿滑性差。
顺丁橡胶在胎面胶中掺用比例过高时,在车速高、路面平滑或湿滑路面时易打滑,使用至后期易崩花掉块。
(3)加工性能欠佳。
顺丁橡胶胶料在辊筒上的加工性能对温度较敏感,温度高时易产生脱辊。
(4)粘性较差。
在胎面胶中掺用比例大时,胎面接头较困难。
1.2.3 异戊橡胶异戊橡胶是以异戊二烯为单体经过配位聚合而得到的聚顺1,4-异戊二烯弹体的简称,又称为“合成天然橡胶”。
是世界上仅次于丁苯橡胶、顺丁橡胶而居于第三位的合成橡胶。
由于异戊橡胶具有与天然橡胶相似的化学组分、立体结构和物理性能,因此它是一种综合性能好的通用合成橡胶。
与天然橡胶相比,其结晶性能较差。
纯胶强度较低等缺点,但混炼加工简便,颜色浅,膨胀和收缩小,流动性好。
1.2.4 丁腈橡胶(NBR )丁腈橡胶具有良好的耐油性,但耐热老化性能差,常用作某些特殊工程轮胎的胎面胶中。
1.2.5 丁基橡胶常用的丁基橡胶品种为氯化丁基胶(CIIR )和溴化丁基胶(BIIR ),它们以其良好的气密性而被用作制造内胎或无内胎轮胎的气密层。
生胶门尼粘度是影响混炼胶可塑性的关键指。
因此,在生胶的入厂检验中,将生胶门尼粘度作为一个关键指标来控制。
天然胶、丁苯橡胶、顺丁橡胶、异戊二烯橡胶的试验方法为ML 10014+℃,氯化丁基胶的试验方法为ML 12518+℃。
2、活性剂2.1 ZnO :一种最通用的活性剂。
对于全钢子午胎来说,氧化锌的质量尤为重要,因为氧化锌在与钢丝粘合的胶料中,对橡胶与胶料的粘合起着重要的作用,用量也较其他胶料大。
氧化锌中的微量的变价金属,含量超标,对胶料的粘合、特别是轮胎使用中后期影响非常大。
因此在全钢子午胎中使用的氧化锌的质量要远远高于斜交胎。
2.2 ZnO-80:是由80%的ZnO 和20%填加剂的混合物。
其中填加剂(20%)是由15%的EVA (是一种低软化点能与橡胶匹配的一种聚合物)+5%无机物组成。
在胶料配方中使用ZnO-80的目的是它比普通ZnO 在胶料中容易分散,•以保证胶料获得好的物理机械性能和气密性,因此把它用在密封层胶料中。
3、补强填充剂3.1 炭黑随着国家产业政策对于环保的重视,干法炭黑将逐渐退出市场,湿法炭黑将占据市场的主导地位。
我公司使用的炭黑品种主要包括炭黑N220、N330、N234、N326、N375、N660、炭黑ECO 。
炭黑的关键指标是吸碘值、DBP 吸收值,另外还有检测炭黑的加热减量、灰分、筛余物。
除此之外,还要对炭黑进行胶料配合试验,检验配方生胶选用天然胶。
3.2 其他填料常用的填充剂还包括白炭黑、轻钙、活性硅粉等等。
4、防老剂轮胎胶料中防老剂品种的选择主要考虑轮胎的使用条件。
主要选用抗臭氧、抗热老化作用明显的防老剂,化学防老剂如防老剂RD(TMQ)、防老剂4020(6PPD)、防老剂DTPD(3100),物理防老剂主要包括微晶石蜡、防护蜡等。
5、硫化剂5.1不溶性硫黄所谓不溶性硫黄就是将普通的八角形硫黄加热到高温熔融,然后急速冷却,使硫黄形成线形大分子硫黄,而这种硫黄不溶于二硫化碳(普通硫黄溶于二硫化碳)所以称之为不溶性硫黄。
不溶性硫黄在橡胶中可以以任意比例混溶而不喷出,而普通硫黄若超过1.5PHR(PHR 含义是每100份橡胶所含有的配合剂的份数)则从橡胶中析出,俗称“喷霜”。
胶料喷霜后半成品没有任何粘性,这些半成品就成为了废料,会造成很大的浪费。
在全钢子午线轮胎的胶料中,为了增加橡胶与钢丝的粘合,通常要加入超过3.5PHR的硫黄;为防止胶料喷霜,在胶料配方中使用不溶性硫黄,是为了防止胶料喷霜。
在使用不溶性硫黄时,应注意不溶性硫黄Su的不稳定,很容易变成普通硫黄。
贮存不溶性硫黄时,温度应在100℃以下,不能放在有胺类原材料处,否则容易变成普通硫黄。
使用不溶性硫黄的胶料配方应注意:①存放温度不超过40~50℃;②存在地附近不能有胺类原材料;③胶料加工过程中温度绝对不能超过105℃;④混炼胶不能停放太长。
5.2 普通硫黄是橡胶中最常用的硫化剂,其硫含量、细度和酸值是重要的检验指标。
5.3 硅烷偶联剂TESPT这是一种混合物,其N330炭黑和Si69各50%。
检验TESPT中的•Si69•含量是否正确和均匀分散在炭黑的表面上,•是通过TESPT的硫含量加以鉴别。
该配合剂一般用于含有白炭黑的胶料中,它可以明显改善胶料的加工性能,同时对胶料的抗硫化返原起到重要的作用。
6、树脂和粘合剂按在配方中的作用,树脂可分为补强树脂和粘和树脂。
全钢子午胎中配方中使用的增粘树脂主要有TKM-M、C5树脂、SP1068(通用辛基酚/甲醛树脂)、T5000等。
补强树脂主要有SP6701(妥尔油改性酚醛树脂),它在配方中与促进剂HMT以10:1的比例并用,可提高硬度。
对于树脂主控制其软化点。
全钢胎中用于与钢丝粘合胶料中的粘合剂有钴盐、粘合剂RA、HMT、间苯二酚等,这几种原材料用量较少,但对轮胎质量影响至关重要。
1.HMT经油处理过的可防止炼胶时结团,容易分散在胶料中,并可减少飞扬。
HMT是由乌洛托品加以白炭黑改性而来,其本身也是橡胶的促进剂,在炼胶时在终炼加入。
该产品在储存过程中,极易吸潮结团,在炼胶过程中造成分散不均。
为此在供货时,要求每次进货量要少。
建议使用HMT-80替代HMT,改善HMT在储存过程中吸潮结块,及胶料混炼时HMT不易分散的问题。
2.HMMM含65%的HMMM和35%的SiO2,成粉末状物便于分散。
除控制外观和水份外游离甲醛也要严格控制,对人体有害。
HMMM在国内又称粘合剂RA ,由于该产品使用的载体是白炭黑,所以在夏季天气湿度大时极易出现水分超标现象。
3.癸酸钴要控制金属钴与癸酸的比例(一般为1:2),做成颗粒状。