EPDM耐热橡胶制品配方的研究与设计
三元乙丙(EPDM)橡胶配方的配合体系介绍

三元乙丙(EPDM)橡胶配方的配合体系介绍三元乙丙橡胶可以采用二烯烃类橡胶用的普通硫化方法硫化,但由于硫化速度较慢,故近年发展了高不饱和度三元乙丙橡胶,其硫化速度不低于高不饱和橡胶的。
三元乙丙橡胶通常可用硫黄、过氧化物、醌肟和反应性树脂等多种硫化体系进行硫化。
不同的硫化体系对其混炼胶的门尼粘度、焦烧时间、硫化速度以及硫化胶的次联键型、物理机械性能(如应力-应变、滞后、压缩变形以及耐热等性能)亦有着直接的影响。
硫化体系的选择要根据所用乙丙橡胶的类型、产品物理机械性能、操作安全性、喷霜以及成等因素加以综合考虑。
一、硫化体系乙丙橡胶常见交联剂体系的适用性和特点1硫黄硫化体系硫黄硫化体系是三元乙丙橡胶使用最广泛最主要的硫化体系。
在硫黄硫化体系中,由于硫黄在乙丙橡胶中溶解度较小,容易喷霜,不宜多用。
一般硫黄用量应控制在1~2份范围内。
在一定硫黄用量范围内,随硫黄用量增加,胶料硫化速度加快,焦烧时间缩短,硫化胶拉伸强度、定伸应力和硬度增高,拉断伸长率下降。
硫黄用量超过2份时,耐热性有下降,高温下压缩永久变形增大。
为使胶料不喷霜,促进剂的用量亦必须保持在三元乙丙橡胶的喷霜极限溶解度以下。
实际上,在工业生产中,基于以下原因几乎都是采用二种或多种促进剂的并用体系。
(1)多种促进剂并用,容易达到硫化作用平衡。
(2)许多促进剂在较低浓度时,就会发生喷霜,因此用量不宜太高。
(3)促进剂这间的协同效应,有利于导致硫化时间的缩短和交联密度的提高。
硫黄硫化体系中,促进剂的用量还可以通过增加硬脂酸的用量来提高,当其它条件不变的情况下,硬脂酸用量增加会导致交联密度、单硫和双硫交联键增加。
氧化锌用量的增加亦有助于在交联时形成促进剂,从而提高胶料的交联密度及抗返原性,改善动态疲劳性能和耐热性能。
2硫黄给予体硫化采用硫黄给予体代替部分硫黄,可使其生成的硫化胶主要具有单硫键或双硫键,因而可以改善胶料的耐热和高温下的压缩变形性能,延长焦烧时间。
EPDM的种类及配方设计

35 45 45 55 57 67 65 75 45 55 48 58 48 58
100
100
100
100
100
100
100
灰分,% 水分,% 拉伸强度,MP a
0.5
0.3
0.3
0.3
0.5
0.5
0.5
0.5
8.2
9.3
7.5
10.0
0.3 0.5 13.7
0.3 0.5 10.0
0.3 0.5 10.0
积
胶或辊筒表面上没有游离炭黑才 割刀
在辊筒上均匀地加入促进剂和硫 磺
每边割刀三次,允许每次割刀之 间为
15 秒排下胶料,调节辊距后薄通 6 次
检查并记录批料重量,与理论值 之差
不能大于 0.5%,否则重炼
(二)企业检验标准摘要
我国曾生产或试制的乙丙橡胶有二元乙丙橡胶、DCPD-EPDM 和 ENB-EPDM。我国乙丙橡胶 商品牌号命名见表 5-17。美国 Exxon 公司三元乙丙橡胶技术规格见表 5-18,日本 JSR
一、基本配合和质量检验方法
三元乙丙橡胶的质量检验,除国际标准化组织(ISO)和美国材料试验学会(ASTM)制 定的三元乙丙橡胶硫化胶性能检验方法外,我国和其它国家目前尚无统一的国家级和部级乙 丙橡胶质量标准及检验方法,大多数生产者均采用其公司或厂家的企业检验方法和质量控制 标准。
(一) ISO 和 ASTM 三元乙丙橡胶硫化胶性能检验方法摘要
X韧塑料与弹性体论坛
三元乙丙橡胶(ethylene-Propylene terpolymer)是乙烯、丙烯和少量非共轭二烯烃的共 聚物,是乙丙橡胶的主要品种。它除保持二元乙丙橡胶优良的耐臭氧性、耐候性、耐热性等 特性外。在硫化速度、配合和硫化胶性能等方面又不完全同于二元乙丙橡胶。
配方体系对EPDM 耐热撕裂性能的影响
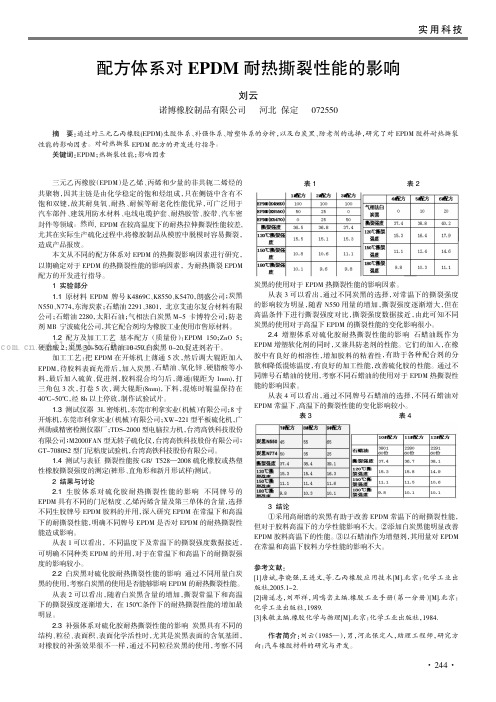
三元乙丙橡胶(EPDM)是乙烯、丙烯和少量的非共轭二烯烃的共聚物,因其主链是由化学稳定的饱和烃组成,只在侧链中含有不饱和双键,故其耐臭氧、耐热、耐候等耐老化性能优异,可广泛用于汽车部件、建筑用防水材料、电线电缆护套、耐热胶管、胶带、汽车密封件等领域。
然而,EPDM在较高温度下的耐热拉伸撕裂性能较差,尤其在实际生产硫化过程中,将橡胶制品从模腔中脱模时容易撕裂,造成产品报废。
本文从不同的配方体系对EPDM的热撕裂影响因素进行研究,以期确定对于EPDM的热撕裂性能的影响因素,为耐热撕裂EPDM 配方的开发进行指导。
1实验部分1.1原材料EPDM牌号K4869C、K8550、K5470,朗盛公司;炭黑N550、N774,东海炭素;石蜡油2291、3801,北京艾迪尔复合材料有限公司;石蜡油2280,太阳石油;气相法白炭黑M-5卡博特公司;防老剂MB宁波硫化公司,其它配合剂均为橡胶工业使用市售原材料。
1.2配方及加工工艺基本配方(质量份):EPDM150;ZnO5;硬脂酸2;炭黑30~50,石蜡油10~50,白炭黑0~20,促进剂若干。
加工工艺:把EPDM在开炼机上薄通5次,然后调大辊距加入EPDM,待胶料表面光滑后,加入炭黑、石蜡油、氧化锌、硬脂酸等小料,最后加入硫黄、促进剂,胶料混合均匀后,薄通(辊距为1mm),打三角包3次,打卷5次,调大辊距(8mm),下料,混炼时辊温保持在40℃~50℃,经8h以上停放,制作试验试片。
1.3测试仪器3L密炼机,东莞市利拿实业(机械)有限公司;8寸开炼机,东莞市利拿实业(机械)有限公司;XW-221型平板硫化机,广州勋威精密检测仪器厂;TDS-2000型电脑拉力机,台湾高铁科技股份有限公司;M2000FAN型无转子硫化仪,台湾高铁科技股份有限公司;GT-7080S2型门尼粘度试验机,台湾高铁科技股份有限公司。
1.4测试与表征撕裂性能按GB/T528—2008硫化橡胶或热塑性橡胶撕裂强度的测定(裤形、直角形和新月形试样)测试。
耐热内骨架EPDM密封圈的研制
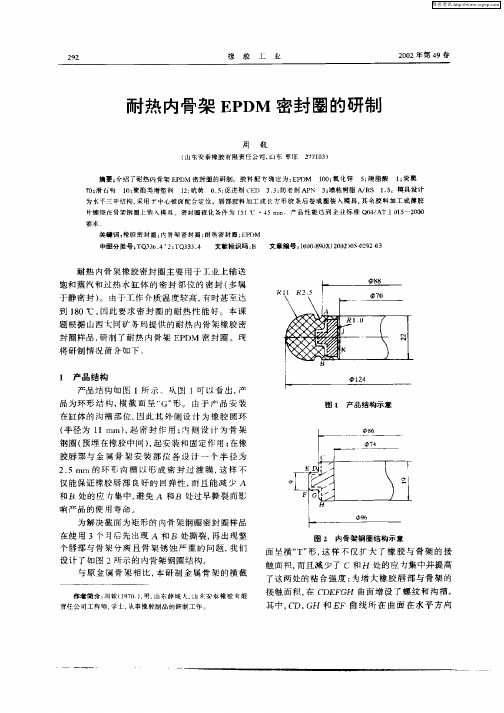
其 中, D, H 和 E 曲 线所 在 曲面 在水 平 方 向 C G F
7: 0 滑 粉
】{ 0 聚酯类增 塑剂 1 ; 2 硫黄
0 5 促进剂 C D 3 3 防老剂 A N ; .; E : P 3 增粘树脂 A R 1 5 / S .。模具设计
为水 - F三开 结 构 . 采用 7 心 锥 面 配 合 定 位 。 唇 部 腔 料 加 工 成 长 方 形 胺 蒹 后 卷 成 圈 装 ^ 模 具 , 余 腔 料 加 工 成 薄 胶 冲 其 片缠 绕 在骨 架钢 圈上 装 入 模具 密封 圈硫 化 条 件 为 1 1℃ ×4 n 产 品 性 能 选 到 企业 标 准 Q1/ 0 5 2 0 5 5 mi 4 ATJ 1 - 0 0 4
2 配 方设计
由于耐 热 内骨 架橡 胶 密封 圈的 使用 环境温 度 较高, 因此选 择 胶 料 主 体 材 料 时要 首 先考 虑 耐 热 性 能。EP M 是饱 和 度 较 高 的聚 合 物 , 耐 热 老 D 其 化性 能与 氯 磺 化 聚 乙烯 橡 胶 和 IR相 当, 般 能 I 一 在 1 0℃下 长期 使 用, 2 0℃ 下间歇 使 用 , 5 在 0 且物
位移, 在垂直 方 向没 有位 移 , 因而将这 2个 曲面 设 计 成 沟槽面 , 沟槽 的深 度和 间距均 为 1 5mm。 其 . 为安装 防 止 产 品轴 向窜 动 的 弹 力 张 紧 钢 圈 , 在图 1所示 的 J和 K 处预 留两个 半 径 为 1 0mm . 的张 紧孔 。
高硬度EPDM胶配方设计技巧分析
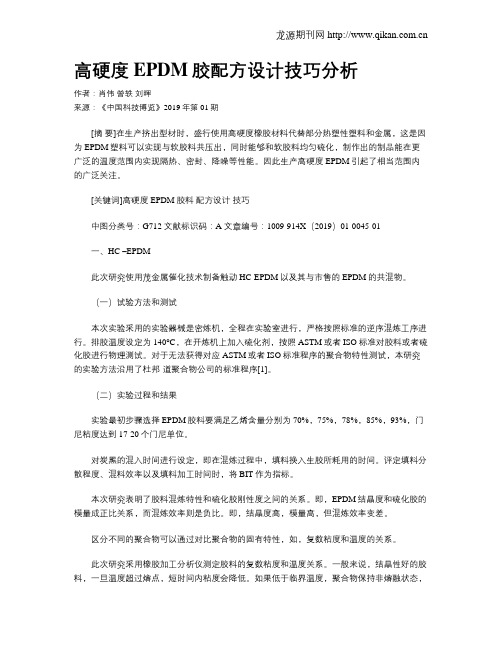
高硬度EPDM胶配方设计技巧分析作者:肖伟曾轶刘晖来源:《中国科技博览》2019年第01期[摘要]在生产挤出型材时,盛行使用高硬度橡胶材料代替部分热塑性塑料和金属,这是因为EPDM塑料可以实现与软胶料共压出,同时能够和软胶料均匀硫化,制作出的制品能在更广泛的温度范围内实现隔热、密封、降噪等性能。
因此生产高硬度EPDM引起了相当范围内的广泛关注。
[关键词]高硬度EPDM 胶料配方设计技巧中图分类号:G712 文献标识码:A 文章编号:1009-914X(2019)01-0045-01一、HC –EPDM此次研究使用茂金属催化技术制备触动HC-EPDM以及其与市售的EPDM的共混物。
(一)试验方法和测试本次实验采用的实验器械是密炼机,全程在实验室进行,严格按照标准的逆序混炼工序进行。
排胶温度设定为140°C,在开炼机上加入硫化剂,按照ASTM或者ISO标准对胶料或者硫化胶进行物理测试。
对于无法获得对应ASTM或者ISO标准程序的聚合物特性测试,本研究的实验方法沿用了杜邦·道聚合物公司的标准程序[1]。
(二)实验过程和结果实验最初步骤选择EPDM胶料要满足乙烯含量分别为70%,75%,78%,85%,93%,门尼粘度达到17-20个门尼单位。
对炭黑的混入时间进行设定,即在混炼过程中,填料换入生胶所耗用的时间。
评定填料分散程度、混料效率以及填料加工时间时,将BIT作为指标。
本次研究表明了胶料混炼特性和硫化胶刚性度之间的关系。
即,EPDM结晶度和硫化胶的模量成正比关系,而混炼效率则是负比。
即,结晶度高,模量高,但混炼效率变差。
区分不同的聚合物可以通过对比聚合物的固有特性,如,复数粘度和温度的关系。
此次研究采用橡胶加工分析仪测定胶料的复数粘度和温度关系。
一般来说,结晶性好的胶料,一旦温度超过熔点,短时间内粘度会降低。
如果低于临界温度,聚合物保持非熔融状态,刚性太大,无法进行混炼。
而乙烯含量达到70%的半结晶性EPDM,其Tc=36℃,在高于36℃的温度范围内,复数粘度和温度关系呈线性曲线关系,表明其能较快进入混炼加工状态[2]。
EPDM基耐高温耐老化橡胶材料的制备及性能研究

EPDM基耐高温耐老化橡胶材料的制备及性能研究摘要:文章主要介绍了EPDM基耐高温老化橡胶的制备和性能,先介绍了实验过程和性能测试,包括实验材料、实验设备、三元乙丙橡胶制备,随后对研究结果进行了讨论总结,包括防老剂类型和生胶体系对于EPDM基橡胶的影响,希望能给相关人士提供有效参考。
关键词:三元乙丙;橡胶;耐高温;耐老化;性能研究引言:通过对EPDM基耐高温耐老化橡胶材料在制备和应用性能进行系统研究,能够进一步了解生胶体系以及防老剂等不同材料对橡胶体系的影响,从而为后期橡胶制备提供有效参考信息,优化橡胶材料生产质量,提高橡胶应用性能。
1.实验过程和性能测试1.实验材料EPDM4050选自中国石油天然气公司,DCP化学纯,硫磺、TAIC分析纯,4010NA、化学纯,工业级,选自江苏圣奥化学公司。
RD工业级,选自天津茂丰橡胶助剂公司。
1.实验设备此次实验中的应用设备包括嘉尔橡塑机械公司生产的橡胶开炼机,华天鑫工贸有限公司生产的平板硫化机,型号为SLB-D305×305,精诚测试公司生产的无转子硫化设备。
温州一鼎仪设备制造企业生产的邵氏橡胶硬度计等。
三元乙丙橡胶制备此次实验工作主要分成三次实施,同时将各次总结出来的多种因素优化成果有效融入下次实验配方内。
选择不同防老剂类型,设置为2/3的比例,相关设置水平如表1所示:表1防老体系变量序号123防老剂防老剂固体石蜡/4010NA 防老剂固体石蜡/RD防老剂固体石蜡/DNPphr2/32/32/3调整EPDM与SBR的比例,相关设置如表2所示:表2补强体系变量序号123 EPDM/SBR140/10100/5120/3相关实验流程是合理配料、进行塑炼和混炼、下片、压片处理、硫化处理、制备试样和测试样品性能。
性能测试在实施老化测试过程中,主要是按照GB-T7762-2003标准实施老化试验,硬度测试中,按照GB/T531.1-2008标准对硫化试样进行硬度测试。
epdm橡胶制品符合fmvss 3032标准的配方
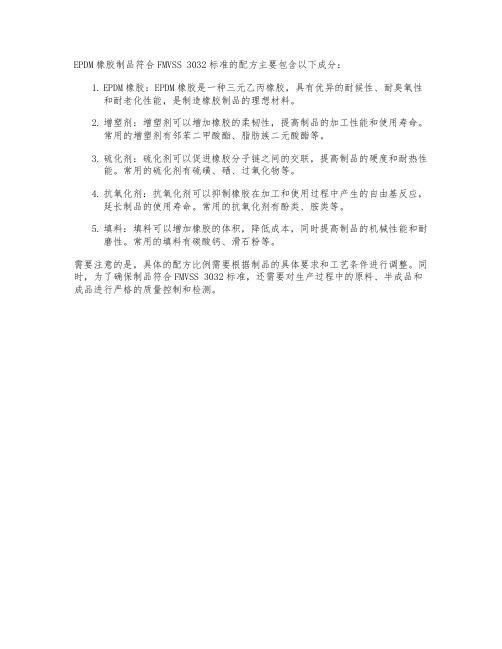
EPDM橡胶制品符合FMVSS 3032标准的配方主要包含以下成分:
1.EPDM橡胶:EPDM橡胶是一种三元乙丙橡胶,具有优异的耐候性、耐臭氧性
和耐老化性能,是制造橡胶制品的理想材料。
2.增塑剂:增塑剂可以增加橡胶的柔韧性,提高制品的加工性能和使用寿命。
常用的增塑剂有邻苯二甲酸酯、脂肪族二元酸酯等。
3.硫化剂:硫化剂可以促进橡胶分子链之间的交联,提高制品的硬度和耐热性
能。
常用的硫化剂有硫磺、硒、过氧化物等。
4.抗氧化剂:抗氧化剂可以抑制橡胶在加工和使用过程中产生的自由基反应,
延长制品的使用寿命。
常用的抗氧化剂有酚类、胺类等。
5.填料:填料可以增加橡胶的体积,降低成本,同时提高制品的机械性能和耐
磨性。
常用的填料有碳酸钙、滑石粉等。
需要注意的是,具体的配方比例需要根据制品的具体要求和工艺条件进行调整。
同时,为了确保制品符合FMVSS 3032标准,还需要对生产过程中的原料、半成品和成品进行严格的质量控制和检测。
epdm橡胶制品符合fmvss 3032标准的配方
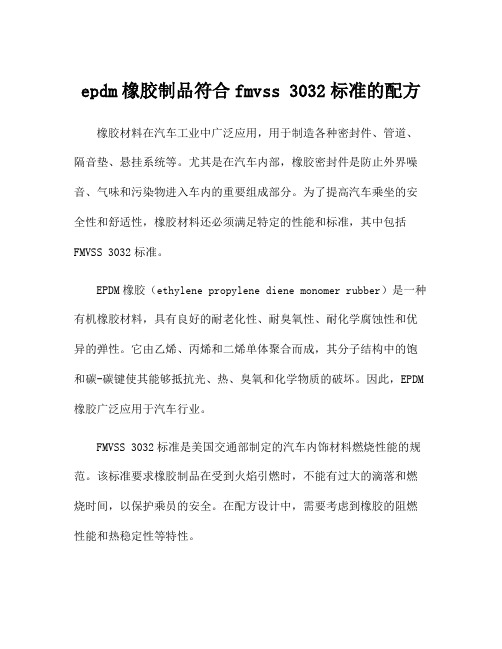
epdm橡胶制品符合fmvss 3032标准的配方橡胶材料在汽车工业中广泛应用,用于制造各种密封件、管道、隔音垫、悬挂系统等。
尤其是在汽车内部,橡胶密封件是防止外界噪音、气味和污染物进入车内的重要组成部分。
为了提高汽车乘坐的安全性和舒适性,橡胶材料还必须满足特定的性能和标准,其中包括FMVSS 3032标准。
EPDM橡胶(ethylene propylene diene monomer rubber)是一种有机橡胶材料,具有良好的耐老化性、耐臭氧性、耐化学腐蚀性和优异的弹性。
它由乙烯、丙烯和二烯单体聚合而成,其分子结构中的饱和碳-碳键使其能够抵抗光、热、臭氧和化学物质的破坏。
因此,EPDM 橡胶广泛应用于汽车行业。
FMVSS 3032标准是美国交通部制定的汽车内饰材料燃烧性能的规范。
该标准要求橡胶制品在受到火焰引燃时,不能有过大的滴落和燃烧时间,以保护乘员的安全。
在配方设计中,需要考虑到橡胶的阻燃性能和热稳定性等特性。
配方设计始于选择合适的橡胶材料。
EPDM橡胶本身是一种具有良好阻燃性能的材料,符合FMVSS 3032标准。
然而,为了进一步提高橡胶的阻燃性能,并满足其他性能要求,需要对其配方进行调整。
一种常见的EPDM橡胶配方包括以下主要组分:1. EPDM橡胶:EPDM在橡胶密封件中的含量通常在70-90%之间。
EPDM橡胶可以提供良好的弹性和耐久性,以及良好的抗老化性能。
2.填充剂:常见的填充剂包括碳黑和无机粉末。
碳黑可以增加橡胶的强度和硬度,而无机粉末可以提高橡胶的阻燃性能。
填充剂的含量通常在10-30%之间。
3.助剂:助剂主要包括硫化剂、活性剂、抗氧剂和阻燃剂等。
硫化剂可以促进橡胶交联,提高弹性和耐久性。
活性剂可以增加橡胶与填充剂之间的相互作用,提高橡胶的力学性能。
抗氧剂可以保护橡胶免受氧化损伤。
阻燃剂可以提高橡胶的阻燃性能。
这些助剂的含量通常在1-10%之间。
通过调整这些成分的含量,可以得到符合FMVSS 3032标准的EPDM 橡胶配方。