气密性试验氮气置换
氨回收系统氮气置换、气密方案

氨回收系统氮气置换、气密方案氨回收系统氮气置换、气密方案1. 编制依据PID图2. 编制目的氨回收系统的填料、管道、设备用消防水冲洗后,如不加以充氮保护,填料、管道、设备就会锈蚀;气密试验的目的是及早发现并排除隐患,为氨回收系统开车做好准备。
3. 氮置换、气密试验范围氨回收系统所有的设备管道4. 氮置换、气密试验具备条件4.1 氨回收系统填料已装,水冲洗合格,系统中残留水已用氮吹净。
4.2 氨回收系统中所有设备、管道、仪表、阀门按PID图检查无误。
4.3 氨回收系统所有仪表、安全阀处于投用状态。
4.4 有充足的合格氮气用来置换系统中氧。
5. 物资准备5.1 2″胶管两根,每根长30米。
5.2 活动扳手、钳子各一把,F扳手大小各二把,铁丝适量。
5.3 人员两人,手套两双。
6. 氨回收系统氮置换与气密试验步骤6.1 确认从合成冷冻系统来的驰放气、闪蒸气所有阀门关闭。
6.2 确认PV1029、PV1033A/B、PV1034、TV1414关闭。
6.3 确认氨回收系统所有导淋关闭。
6.4 打开LV1026及其截止阀、打开161J/JA泵进出口阀,打开NH1032-2″上止逆阀。
6.5 分别在124D出口1.5″导淋、NH1071-3″上导淋接入胶管,充入氮气到4~5kg/cm2,当PI1682、PI1685、PI1677平衡时,关闭充氮阀。
6.6 打开PV1033B、161J出口导淋进行排放到氨回收系统压力在0.5kg/cm2,关闭排放阀。
6.7 在连续充氮三次后,在各个分析点取样分析,若氧含量小于0.5%,氨回收系统氮置换合格。
6.8 氮置换合格后,确认所有排放点、取样点关闭,继续充氮至4~5kg/cm2,稳定此压力后关闭充氮阀,进行氨回收系统的气密试验。
6.9 在设备、管道、调节阀、流量孔板、设备封头等的法兰联接处用胶带纸密封后,弄一小孔,用肥皂水检查有无泄漏,若发现漏点,泄压处理后,重新充氮试验。
气密性实验方案
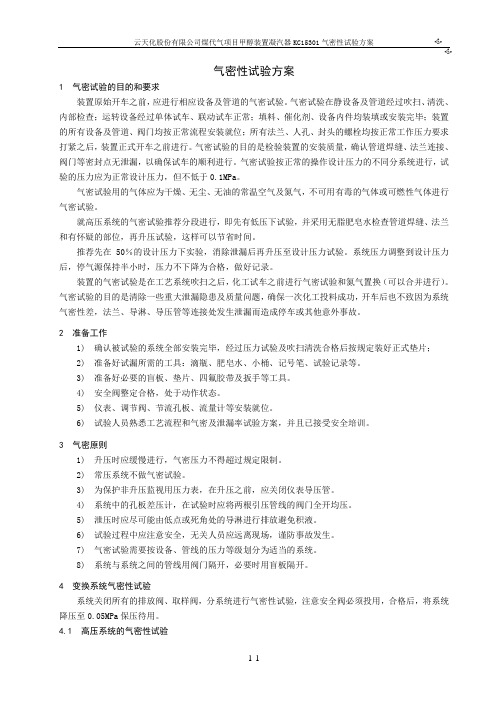
气密性试验方案1 气密试验的目的和要求装置原始开车之前,应进行相应设备及管道的气密试验。
气密试验在静设备及管道经过吹扫、清洗、内部检查;运转设备经过单体试车、联动试车正常;填料、催化剂、设备内件均装填或安装完毕;装置的所有设备及管道、阀门均按正常流程安装就位;所有法兰、人孔、封头的螺栓均按正常工作压力要求打紧之后,装置正式开车之前进行。
气密试验的目的是检验装置的安装质量,确认管道焊缝、法兰连接、阀门等密封点无泄漏,以确保试车的顺利进行。
气密试验按正常的操作设计压力的不同分系统进行,试验的压力应为正常设计压力,但不低于0.1MPa。
气密试验用的气体应为干燥、无尘、无油的常温空气及氮气,不可用有毒的气体或可燃性气体进行气密试验。
就高压系统的气密试验推荐分段进行,即先有低压下试验,并采用无脂肥皂水检查管道焊缝、法兰和有怀疑的部位,再升压试验,这样可以节省时间。
推荐先在50%的设计压力下实验,消除泄漏后再升压至设计压力试验。
系统压力调整到设计压力后,停气源保持半小时,压力不下降为合格,做好记录。
装置的气密试验是在工艺系统吹扫之后,化工试车之前进行气密试验和氮气置换(可以合并进行)。
气密试验的目的是清除一些重大泄漏隐患及质量问题,确保一次化工投料成功,开车后也不致因为系统气密性差,法兰、导淋、导压管等连接处发生泄漏而造成停车或其他意外事故。
2 准备工作1)确认被试验的系统全部安装完毕,经过压力试验及吹扫清洗合格后按规定装好正式垫片;2)准备好试漏所需的工具:滴瓶、肥皂水、小桶、记号笔、试验记录等。
3)准备好必要的盲板、垫片、四氟胶带及扳手等工具。
4)安全阀整定合格,处于动作状态。
5)仪表、调节阀、节流孔板、流量计等安装就位。
6)试验人员熟悉工艺流程和气密及泄漏率试验方案,并且已接受安全培训。
3 气密原则1)升压时应缓慢进行,气密压力不得超过规定限制。
2)常压系统不做气密试验。
3)为保护非升压监视用压力表,在升压之前,应关闭仪表导压管。
天然气管道干燥置换与气密性的运用【论文】
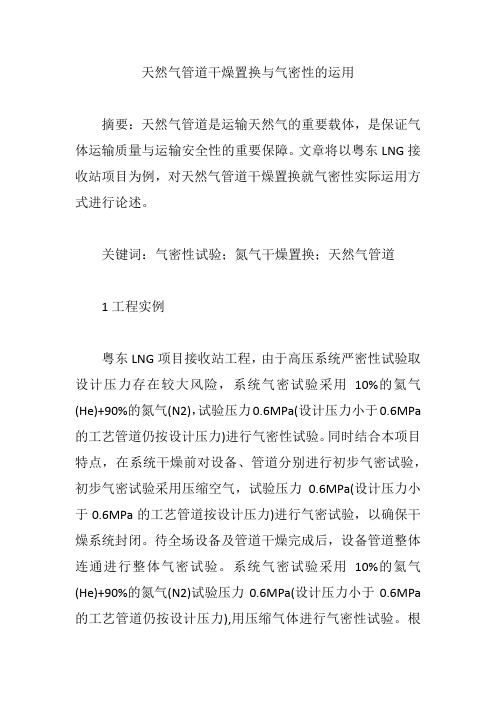
天然气管道干燥置换与气密性的运用摘要:天然气管道是运输天然气的重要载体,是保证气体运输质量与运输安全性的重要保障。
文章将以粤东LNG接收站项目为例,对天然气管道干燥置换就气密性实际运用方式进行论述。
关键词:气密性试验;氮气干燥置换;天然气管道1工程实例粤东LNG项目接收站工程,由于高压系统严密性试验取设计压力存在较大风险,系统气密试验采用10%的氦气(He)+90%的氮气(N2),试验压力0.6MPa(设计压力小于0.6MPa 的工艺管道仍按设计压力)进行气密性试验。
同时结合本项目特点,在系统干燥前对设备、管道分别进行初步气密试验,初步气密试验采用压缩空气,试验压力0.6MPa(设计压力小于0.6MPa的工艺管道按设计压力)进行气密试验,以确保干燥系统封闭。
待全场设备及管道干燥完成后,设备管道整体连通进行整体气密试验。
系统气密试验采用10%的氦气(He)+90%的氮气(N2)试验压力0.6MPa(设计压力小于0.6MPa 的工艺管道仍按设计压力),用压缩气体进行气密性试验。
根据本项目特点,干燥分初步干燥和系统干燥两个阶段进行,其中在初步干燥中应对所有检测点的露点检测合格并确保管道和阀门不带液,方可联通系统进行总体干燥。
系统气密试验至试验压力时,经检测氦气与氮气完全混合后进行保压30min,然后进行全面检查,对阀门填料函、法兰及螺纹连接处、放空阀、排气阀、排水阀等重点检查,采用氦气质谱仪进行漏点检测。
2干燥置换运用2.1系统干燥按照项目实际情况,主要采用电加热器、液氮汽化器联合干燥处理模式。
在实施初步干燥过程中,需要对检测点展开露点检测,在检测合格之后,需要确认阀门以及管道是否存在带液状况,在确定不带液之后,才可实施总体干燥。
本工程系统干燥采用的是管线、设备整体干燥模式,因此并不需要设置临时盲板,同时需要运用低温软管及法兰展开汽化器、液氮罐连接,通过对无缝钢管的运用做好加热炉到汽化器间的衔接。
实施氮气注入过程中,应保证每分钟注入流量数值可以保持在一次干燥分路系统总容量的0.5倍以上,且需要将进管氮气温度控制在55℃左右。
脱硝氨区系统气密性试验及氮气置换
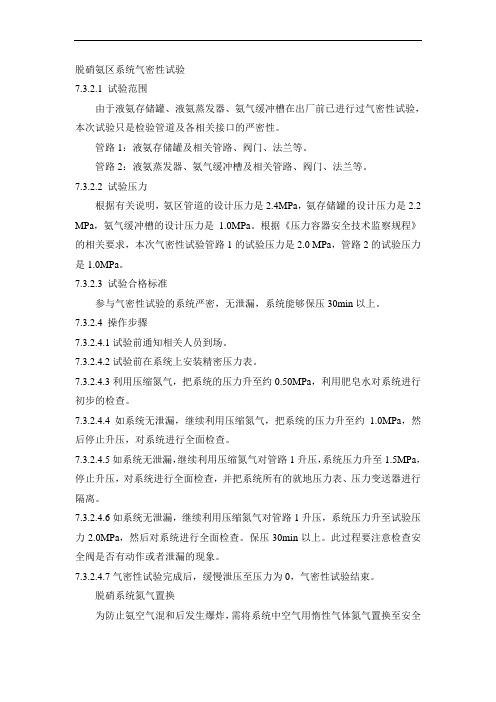
脱硝氨区系统气密性试验7.3.2.1 试验范围由于液氨存储罐、液氨蒸发器、氨气缓冲槽在出厂前已进行过气密性试验,本次试验只是检验管道及各相关接口的严密性。
管路1:液氨存储罐及相关管路、阀门、法兰等。
管路2:液氨蒸发器、氨气缓冲槽及相关管路、阀门、法兰等。
7.3.2.2 试验压力根据有关说明,氨区管道的设计压力是2.4MPa,氨存储罐的设计压力是2.2 MPa,氨气缓冲槽的设计压力是1.0MPa。
根据《压力容器安全技术监察规程》的相关要求,本次气密性试验管路1的试验压力是2.0 MPa,管路2的试验压力是1.0MPa。
7.3.2.3 试验合格标准参与气密性试验的系统严密,无泄漏,系统能够保压30min以上。
7.3.2.4 操作步骤7.3.2.4.1试验前通知相关人员到场。
7.3.2.4.2试验前在系统上安装精密压力表。
7.3.2.4.3利用压缩氮气,把系统的压力升至约0.50MPa,利用肥皂水对系统进行初步的检查。
7.3.2.4.4如系统无泄漏,继续利用压缩氮气,把系统的压力升至约1.0MPa,然后停止升压,对系统进行全面检查。
7.3.2.4.5如系统无泄漏,继续利用压缩氮气对管路1升压,系统压力升至1.5MPa,停止升压,对系统进行全面检查,并把系统所有的就地压力表、压力变送器进行隔离。
7.3.2.4.6如系统无泄漏,继续利用压缩氮气对管路1升压,系统压力升至试验压力2.0MPa,然后对系统进行全面检查。
保压30min以上。
此过程要注意检查安全阀是否有动作或者泄漏的现象。
7.3.2.4.7气密性试验完成后,缓慢泄压至压力为0,气密性试验结束。
脱硝系统氮气置换为防止氨空气混和后发生爆炸,需将系统中空气用惰性气体氮气置换至安全水平(小于14%)。
7.3.3.1脱硝系统氮气置换方法将氮气充入系统,压力升至0.5MPa,打开出口排放系统气体至压力降为0.1 MPa,再次充入氮气至压力为0.5MPa,打开出口排放系统气体至压力降为0.1 MPa,如此操作4到5次,置换结束。
氮气气密及置换施工方案

目录一、工程概况: (1)二、编制依据: (1)三、主要工作量: (1)四、流程简述: (2)五、流程示意简图:流程图见后页 (2)六、气密试验程序: (2)七、设备管线气密试验: (2)八、HSE措施 (6)九、试验所需设备材料: (7)一、工程概况:某某工程经过施工建设,工程基本完成后。
工艺进入最后的氮气气密试验阶段,氮气气密试验的目的是检验四台压缩机进出口管线无应力对接后的法兰连接密封性及仪表管嘴、设备以及在水压试验中无法参加试验的部位和设施的严密性要在本次气密试验中加以检测,根据设备公司要求确定本次气密试验的试验压力暂定为设计压力即12.0Mpa,试验用的介质为氮气。
参加气密试验的设备主要有空冷器、燃气压缩机组和密封气增压撬。
气密试验结束后还要进行设备公司提供的燃料气处理撬的气密试验以及管道氮气吹扫施工。
为顺利完成本次工程特编制本方案指导施工,请施工中队严格按技术方案进行施工。
二、编制依据:施工设计图纸:管-L674、管-L600、管-L601《石油天然气站内工艺管道工程施工及验收规范》(SY 0402-2000)《西气东输二线管道工程站场安装技术规范》Q/SY GJX 0120-2008《工业金属管道工程施工及验收规范》(GB 50235-97)《西气东输管道工程管道焊接施工及验收规范》(Q/SY XQ4-2003)《现场设备、工业管道焊接工程施工及验收规范》(GB50236-98)招标文件技术要求和双方签订合同相关条文三、主要工作量:3.1、设备包括:后空冷器、压缩机组4套、燃料气处理撬4台、密封气增压撬1台。
3.2、工艺管线:DN1000=164m、DN900=220m、DN200=580m、DN600=300m、DN750=20m。
DN50=182m.3.3、氮气气密容积计算:V=后空冷器+压缩机组4套+密封气增压撬1台+管线容积V=60+20+10+(132+145+22+88+9+1)V=487(m3)3.4 氮气使用量计算:Q=1.1(V/700*△T*120)=1.1(487/700*1.1*120)=101(吨)四、流程简述:氮气气密试验四台压缩机同时进行。
天然气系统吹扫试压气密置换方案-样本

天然气系统吹扫、气密、置换方案编制:审核:审批:目录一、工程概况 (3)1、工程简述 (3)2、初步方案 (3)二、编制依据 (3)三、吹扫、气密、置换目的 (3)四、系统图 (3)五、工作流程 (4)1、前期准备 (4)2、管线吹扫 (4)3、气密性试验 (5)4、管道置换 (6)(1)置换准备 (6)(2)氮气置换 (6)(3)天然气置换 (6)六、安全措施 (6)七、安全技术措施 (7)八、安全应急预案 (7)九、吹扫、气密、置换组织机构人员分工 (8)一、工程概况1、工程简述项目工程。
输气管线规格:DN200,DN150;管道设计压力:0.4Mpa;天然气运行压力:0.2~0.3 Mpa;设计温度:常温输送介质:天然气,热值37.6MJ/NM³。
2、初步方案吹扫试压的管为DN200、DN150。
规格为:DN200,起点为厂区主管网分支处,终点为减压阀后。
规格为:DN150,起点为减压阀后,终点为回转炉燃烧器和二燃室燃烧器。
管线长度超过500m,按照规范要求,拟分段进行吹扫试压工作。
二、编制依据1、《工业金属管道工程施工规范》(GB50235-2010)2、《天然气净化装置设备与管道安装工程施工技术规范》(SY/T化0460-2010)3、《石油天然气站内工艺管道工程施工规范》(GB50540-2009)4、施工图5、现场实际情况三、吹扫、试压、气密、置换目的为进一步加强公司安全生产管理工作,提高防范发生安全事故的能力,根据市政府有关文件的要求,结合公司实际,特制定本停气吹扫工作方案。
四、系统图潞安危废处理装置燃料气系统图V4,打开V6,然后打开V7、V8至管线吹扫干净五、工作流程施工程序:前期准备→管线吹扫→气密性试验→管道置换。
1、前期准备(1)工作准备①管线及管线附件安装完毕。
②所有的设备,资料齐全,质量证明书符合要求。
③用作吹扫气源的设备已完成准备工作。
④吹扫试压的进气和排气系统已安装完毕。
CNG操作说明书

CNG汽车改装管路氮气置换装置-------GBN-01型使用说明书一、CNG 汽车管路氮气置换装置GBN-01原理图氮气瓶真空泵减压阀真空表针阀接汽车管路卸荷阀二、操作程序1、将相应管路按原理图连接好。
2、做此试验前首先进行管路气密性试验,试验完后放掉高压气体,准备做抽真空和氮气置换。
3、抽真空:按原理图将管路连接好,关闭高压截止阀JF1,打开截止阀JF2、JF3,对管路进行抽真空,当真空度达到-0.1bar时,关闭截止阀JF2。
4、充氮气,将氮气瓶的压力减至1MPa后,将管路中的氮气压力充到1MPa,关闭氮气瓶瓶阀,打开截止阀JF1,将压力减至0.1MPa时关闭截止阀JF1;随后打开氮气瓶瓶阀,调整氮气减压阀的压力至0.5MPa,将管路充装氮气,压力到达0.5MPa时重复以上动作,即打开截止阀JF1,将压力减至0.1MPa时关闭截止阀JF1,氮气置换完毕。
CNG汽车改装气密性试验装置使用说明书前言CNG汽车改装管路气密性检测装置实际为气体增压装置,该装置是我公司根据从国外引进的气动试压装置的工作原理,结合我国的实际情况研制而成的一种新型试压装置。
一、特点它是使用压缩空气为动力源,以气体增压泵为压力源,输出气体压力与驱动气源压成比例。
通过对驱动气源压力的调整,便能得到相应的增压后的气体压力。
当驱动气源压力与增压后的气体压力平衡时,增压泵便停止充压,输出气体压力也就稳定在预调的压力上。
因而具有防爆、输出压力可调、体积小、重量轻、操作简单、性能可靠、适用范围广等特点。
它特别适用于阀门、管路、连接件、压力容器等受压设备的试压检验。
同时也适合科研、检验部门检测工具。
二、用途用于CNG改装汽车管路、阀门、连接件的气密性检验及耐压检验。
三、型号意义GBS40BGBS --- CNG改装汽车管路气密性试验装置代号40--- 表示该装置所使用的气体增压泵的增压比为40:1B --- 表示全封闭标准型四、产品工作原理注:所用元件介绍注意事项:高压截止阀为锥形针阀,关闭力不能大于18NM。
燃料气、氮气、火炬系统吹扫、气密、置换方案7.22

燃料气、氮气、火炬系统管线吹扫、气密和置换方案一、吹扫方案1.目的清除装置施工建设中残存于设备、管线内的泥沙、焊渣、铁锈等脏物,为装置试车贯通流程,检验装置的施工质量。
2.准备工作2.1吹扫介质的选择2.1.1工艺管线、设备吹扫所用介质应根据其工艺及设备的状况不同而选择不同的吹扫介质。
本方案作如下规定:2.1.1.1工艺管线及设备,首次吹扫原则上选用工业风。
部分管线根据现场实际情况可先用蒸汽吹扫后再用工业风吹干。
2.1.1.2原料油采用蒸汽吹扫。
2.1.2公用工程管线的吹扫介质确定如下:2.1.2.1氮气(20MPa、4.0MPa、0.6MPa、0.04 MPa)、燃料气(0.4 MPa、0.05MPa)系统用蒸汽吹扫后再用工业风吹干。
2.1.2.2火炬线在装置界区内用蒸汽吹扫。
2.2操作步骤●班长确认工作范围和工作条件●通讯器材完好可用●防爆扳手准备完毕,型号相配●准备盲板图,盲板表●联系施工单位,准备合适的短接、法兰、档板、垫片●准备相应的盲板●确认系统1.0MPa蒸汽已引入装置3.吹扫方案3.1、贯通吹扫的目的通过吹扫,清除施工过程中进入设备、管道中的焊渣、泥砂以及管道中的油污和铁锈。
对设备和管道中的法兰等静密封点进行初步试漏、试压。
贯通流程,熟悉基本操作,暴露有关管线、设备问题。
熟悉流程,提高操作人员技术素质和实际操作能力。
3.2、吹扫的方法及要求吹扫前要掌握每一条管道的吹扫流程、吹扫介质和注意事项,清楚吹扫介质的给入点或临时给入点,每条管道的排放点和临时排放点。
对排放点要做好遮挡工作,防止将污物吹入设备和后路管线。
引入蒸汽吹扫时,要注意防止水击,防止发生烫伤事故。
吹扫前应把调节阀、孔板、流量计、疏水器、限流孔板、过滤器滤芯、单向阀阀芯(或单向阀)拆除,调节阀、流量计上下游阀放空,吹扫干净后,以利于后续管道的吹扫。
吹扫前应将采样阀、压力表手阀、液面计等易堵塞阀门关闭。
待管线和设备吹扫干净后再吹扫。
- 1、下载文档前请自行甄别文档内容的完整性,平台不提供额外的编辑、内容补充、找答案等附加服务。
- 2、"仅部分预览"的文档,不可在线预览部分如存在完整性等问题,可反馈申请退款(可完整预览的文档不适用该条件!)。
- 3、如文档侵犯您的权益,请联系客服反馈,我们会尽快为您处理(人工客服工作时间:9:00-18:30)。
氨区气密性试验及氮气置换
试验对象:氨区内所有液氨和气氨管道
一、目的:
氨属于乙类可燃流体,必须进行气密性试验。
以确保试车投运的顺利、安全的进行。
二、技术要求:
在进行水压试验,管道吹洗合格之后才能气密性试验。
采用介质为99.9以上的氮气为试验介质。
试验压力为管道设计压力,详细参数见设计图纸中的“压力管道一览表”。
温度:常温。
不同的设计压力的管道应分段试压。
试压管路的为一个封闭系统。
试压合格后减压至0.05MPa,紧接着进行管路的氮气置换工作。
详细用气量及各步骤参数件附表“氨区气密性试验和氮气置换用气表”。
三、气密性试验应具备的条件
1、设备在安装前已试压合格,无泄漏点,管路上阀门已试压试漏无泄漏后安装
上系统。
2、安装单位已做过分段的试压试漏工作。
3、设备和管道已吹扫置换干净,且清洗合格。
4、仪表元件等已全部安装到位,且调试合格,并能投入运行。
5、试验用的盲板,压力表准备完毕。
压力表精度1.5级,量程为试验压力的2
倍。
6、安全阀已经隔离。
7、氨区氮气系统已准备就绪。
8、试验工作人员及安装维修人员已作好安排,试验人员已熟悉试验方案。
四、气密性试验步骤
1、根据工艺流程将试压分为三段试压:液氨卸车管至蒸发器出口调节阀(含卸
料压缩机),蒸发器调节阀至气氨界区出口,气氨回收系统。
2、对系统作全面检查,确认设备、管道、管件、仪表等有无缺损。
3、关闭各段试验管路的所有排气,导淋阀。
系统进出口阀门关闭,压力分界点
阀门关闭。
4、系统内部阀门全部开启;安全阀已经隔离。
5、压力表在充氮入口安装一块,试压管道末端安装一块。
4、缓慢开启进气阀,直至升至设计管道设计压力值,关闭进气阀保压。
5、如果发现压力下降,用涂肥皂水仔细检查整个系统(特别是法兰、阀门连接
处)是否泄漏。
如果压力下降,应及时消除泄漏,并重新升压到规定指标。
6、若压力不再下降,确认无泄漏后,记下起始时的温度、压力值,连续保压24
小时。
7、计算泄漏率,若泄漏率小于0.2%(每小时)则为合格。
(泄漏率是对试压管道较长的一个复核。
在气密性试压开始阶段升压到一定值的时候,关闭压力源之后由于管道有一定的膨胀率等因素,管道内的压力可能会下降。
若管道无泄漏,
下降到一定的值就不会再下降。
记录下降的压力和时间,与气密性压力的比值。
)8、填写试验记录表
五:氮气置换:
1、氮气置换条件:水压试验,管道吹洗,气密性试验都以结束;所有盲板拆除,
安全阀隔离拆除,液氨、气氨系统所有的阀门都已恢复。
2、置换氮气从液氨卸料口充入,从气氨出氨区阀门J0HSJ51/2-AA313排出。
3、气氨排放管线逐条管线置换,不允许有死角,漏项。
4、系统充压0.3MPa后从最后面排放,反复做几次,检测出口氧气含量,氧体
积含量≤3%为合格(≤1%为优良)。
关闭氨系统进出阀,封闭系统。
5、填写置换记录。
人员配置:
总负责人:1人
技术负责人;1人
安全负责人:1人
组长:1人
维修电工:1人
施工员:
氮气准备:3人(保证氮气连续供给);
气密性试验,置换操作人员:3人
巡回检查:2人
送检:1人
设备:
氮气:瓶装,外购
气密性试验压力表:2块(精度1.5级,量程5MPa;;安装在试压盲板上)
置换压力表:2块(精度1.5级,量程2MPa;;安装在试压盲板上)
护具,工具一套。
预计时间(7天)
气密性试验:72小时
氮气置换:96小时
气密性试验主要是检验容器的各联接部位是否有泄漏现象。
介质毒性程度为极度、高度危害或设计上不允许有微量泄漏的压力容器,必须进行气密性试验。
压力容器应按以下要求进行气密性试验:
(1)气密性试验应在液压试验合格后进行。
对设计要求作气压试验的压力容器,气密性试验可与气压试验同时进行,试验压力应为气压试验的压力。
(2)碳素钢和低合金钢制成的压力容器,其试验用气体的温度应不低于5℃,其它材料制成的压力容器按设计图样规定。
(3)气密性试验所用气体,应为干燥、清洁的空气、氮气或其他惰性气体。
(4)进行气密性试验时,安全附件应安装齐全。
(5)试验时压力应缓慢上升,达到规定试验压力后保压10分钟,然后降至设计压力,对所有焊缝和连接部位涂刷肥皂水进行检查,以无泄漏为合格。
如有泄漏,修补后重新进行液压试验和气密性试验。
气密性试验与气压试验是不一样的。
首先,它们的目的不同,气密性试验是检验压力容器的严密性,气压试验是检验压力容器的耐压强度。
其次试验压力不同,气密性试验压力为容器的设计压力,气压试验压力为设计压力的1.15倍。
气密性试验记录
氮气置换记录。