数控车床刀库设计参考文献英文
数控机床刀具设计论文中英文资料外文翻译文献综述
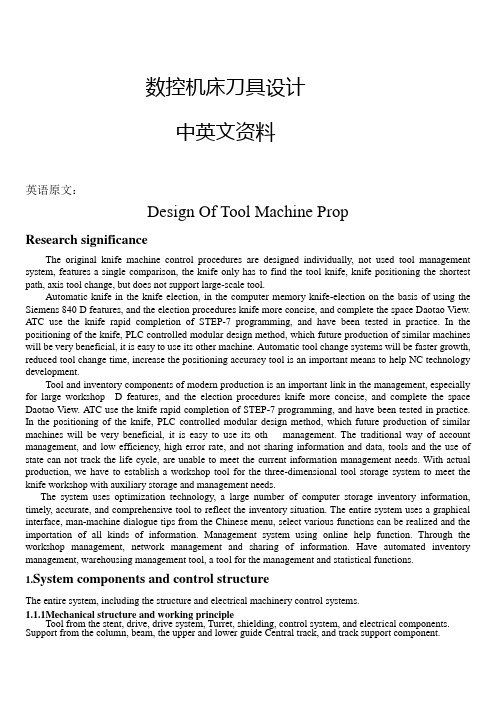
数控机床刀具设计中英文资料英语原文:Design Of Tool Machine PropResearch significanceThe original knife machine control procedures are designed individually, not used tool management system, features a single comparison, the knife only has to find the tool knife, knife positioning the shortest path, axis tool change, but does not support large-scale tool.Automatic knife in the knife election, in the computer memory knife-election on the basis of using the Siemens 840 D features, and the election procedures knife more concise, and complete the space Daotao View. ATC use the knife rapid completion of STEP-7 programming, and have been tested in practice. In the positioning of the knife, PLC controlled modular design method, which future production of similar machines will be very beneficial, it is easy to use its other machine. Automatic tool change systems will be faster growth, reduced tool change time, increase the positioning accuracy tool is an important means to help NC technology development.Tool and inventory components of modern production is an important link in the management, especially for large workshop D features, and the election procedures knife more concise, and complete the space Daotao View. ATC use the knife rapid completion of STEP-7 programming, and have been tested in practice. In the positioning of the knife, PLC controlled modular design method, which future production of similar machines will be very beneficial, it is easy to use its oth management. The traditional way of account management, and low efficiency, high error rate, and not sharing information and data, tools and the use of state can not track the life cycle, are unable to meet the current information management needs. With actual production, we have to establish a workshop tool for the three-dimensional tool storage system to meet the knife workshop with auxiliary storage and management needs.The system uses optimization technology, a large number of computer storage inventory information, timely, accurate, and comprehensive tool to reflect the inventory situation. The entire system uses a graphical interface, man-machine dialogue tips from the Chinese menu, select various functions can be realized and the importation of all kinds of information. Management system using online help function. Through the workshop management, network management and sharing of information. Have automated inventory management, warehousing management tool, a tool for the management and statistical functions.1.System components and control structureThe entire system, including the structure and electrical machinery control systems.1.1.1Mechanical structure and working principleTool from the stent, drive, drive system, Turret, shielding, control system, and electrical components. Support from the column, beam, the upper and lower guide Central track, and track support component.1) Drive for the system chosen VVVF method. Cone used brake motors, with VVVF by Cycloid reducer through sprocket drive.2) Drag a variable frequency drive system and control technology. VVVF adopted, will speed drive shaft in the normal range adjustment to control the speed rotary turret to 5 ~ 30mm in, the drive shaft into two, two under through sprocket, the two profiled rollers Chain driven rotating shelves. Expansion chain adopted by the thread tight regulation swelling, swelling the regular way. - Conditi D features, and the election procedures knife more concise, and complete the space Daotao View. ATC use the knife rapid completion of STEP-7 programming, and have been tested in practice. In the positioning of the knife, PLC controlled modular design method, which future production of similar machines will be very beneficial, it is easy to use its at six other Des V oeux a knife, can be categorized with some of knife auxiliary equipment, such as bits, such as turning tools.1.1.2.Electrical Control SystemThis tool storage systems is the main electrical control their shelves for operational control and position control. Operational control equipment, including operation of the start of braking control. Position Control is the main location and address of the shelves for testing.1) Electric Transmission horizontal rotary tool storage systems are the mechanical movements are repeated short-term work system. And the run-time system needs some speed, speed transmission needs, the system will use VVVF method can be used simple structure, reliable operation of the motor and frequency inverter.2) Control of the system is divided into two kinds of manual control and automatic control, manual control as a general reserve and debugging methods of work; ways to the system control computer (IPC) and the control unit (inverter contactor , etc.) consisting of a control system.3) location and positioning accuracy of the system automatically identify the site and location using a detection device tion, timely, accurate, and comprehensive tool to reflect the inventory situation. The entire system uses a graphical interface, man-machine dialogue tips from the Chinese menu, select various functions can be realized and the importation of all kinds of information. Management system using online help function. Through the workshop management, network management and sharing of information. Have automated inventory management, warehousing management tool, a tool for the management and statistical fu as proximity switches, relays through the plate-point isolation and the number plate recorded close to the switching signal acquisition and operation of Hutchison with a Optimal Path addressable identify the current location and shelves of the purpose of the shelf location. In order to enable a more accurate positioning system, adopted two photoelectric switches, to detect the two shelves of the two films.1.2.The functions of the knifeknife The is the role of reserves a certain number of tools, machine tool spindle in hand to achieve the fungibility a disc sc knife in the library with discoid knife, cutting tool along See how vertical arrangement (including radial and axial from knife from knife), along See how radial array into acute or arranged in the form of the knife. Simple, compact, more applications, but are ring-cutter, low utilization of space. Figure 2.7 a) to c). D features, and the election procedures knife more concise, and complete the space Daotao View. ATC use the knife rapid completion of STEP-7 programming, and have been tested in practice. In the positioning of the knife, PLC controlled modular design method, which future production of similar machines will be very beneficial, it is easy to use its. If the knife cutter knife is the type of library, the chain knives, and other means, in the form of the knifeand capacity according to the Machine Tool to determine the scope of the process.s, but are ring-cutter, low utilization of space. Figure 2.7 a) to c). D features, and the election procedures knife more concise, and com mon typesThe knife is a tool storage devices, the common knife mainly in the following forms:(1) the turret knifeIncluding the first level turret vertical turret and the first two, see Figure 2.6 a) and b):(2) the disc cutterDisc knife in the library with discoid knife, cutting tool along See how vertical arrangement (includingradial and axial from knife from knife), along See how radial array into acute or arranged in the form of theknife. Simple, compact, more applications, but are ring-cutter, low utilization of space. Figure 2.7 a) to c).D features, and the election procedures knife more concise, and complete the space Daotao View. ATC use theknife rapid completion of STEP-7 programming, and have been tested in practice. In the positioning of theknife, PLC controlled modular design method, which future production of similar machines will be verybeneficial, it is easy to use its. If the knife storage capacity must be increased to increase the diameter of theknife, then the moment of inertia also increased correspondingly, the election campaign long knife. Toolnumber not more than 32 general. Cutter was multi-loop order of the space utilization knife, but inevitablygiven the knife from complex institutions, applicable to the restricted space Machine Tool storage capacity andmore occasions. Two-disc structure is two smaller capacity knife on both sides of the sub-spindle place, morecompact layout, the number ofapply to small and medium-sizedprocessing center.(3) the chain knife Includingsingle-and multi-ring chain ringchain, chain link can take many forms change, see Figure 2.8 a) to c), the basic structure shown in Figure 2. 8 doFeatures: knife apply to the larger capacity of the occasion, the space of the small number of generally applicable to the tool in the 30-120. Only increase the length of the chain tool will increase the number should not be increased circumferential speed of its moment of inertia of the knife does not increase the disc as large.(4) linear combination knife and the knife libraryThe linear knife simple structure in Figure 2.9, tool single order, the capacity of small knife, used for CNC lathe and drill press on. Because the location of fixed knife, ATC completed action by the spindle without manipulator. The cutter knife is generally the turret combination turret with a combination of the disc cutter knife and the chain combination. Every single knife the knife certificates of smaller, faster tool change. There are also some intensive drum wheel, and the lattice-type magazine for the knife, the knife-intensive though.Small footprint, but because of structural constraints, basically not used for single processing center, the concentration used for FMS for the knife system.1.4 Tool storage capacityTool storage capacity of the first to consider the needs of processing, from the use of point of view,generally 10 to 40 knives, knife will be the utilization of the high, and the structure is compact.1.5 Tool options(1) choose to order processing tool according to the order, followed Add to the knife every knife in the Block. Each tool change, the order of rotation of a cutter knife on location, and remove the need knives, has been used by the cutter knife can be returned to the original Block, can also order Add Block, a knife. However, as the knife in the tool in different processes can not be repeated use of the knife must increase the capacity and lower utilization rate.(2) most of the arbitrary choice of the current system of using arbitrary NC election knives, divided into Daotao coding, coding and memory-cutter, three. Daotao coding tool code or knives or Daotao need to install the code used to identify, in accordance with the general principle of binary coding coding. Tool knife election coding method uses a special knife handle structure, and each of the coding tool. Each of the tool has its own code, thereby cutting tool can be in different processes repeatedly used, not to replace the tool back at the original knife, the knife capacity can be reduced accordingly. Memory-election this paper knife, in this way can knives and knife in the position corresponding to the Daotao memory of the PLC in the NC system, no matter which tool on the Inner knife, tool information is always there in mind, PLC . On the knife with position detection devices, will be the location of each Daotao. This tool can be removed and sent back to arbitrary. On the knife is also a mechanical origin, every election, the nearest knife selection.1.6.Control of the knife(1) the knife as a system to control the positioning axis. In the ladder diagram in accordance with the instructions for computing T code comparison of the output angle and speed of instructions to the knife the knife servo drive servo motor. Tool storage capacity, rotation speed, and / deceleration time, and other system parameters can be set in such a manner free from any outside influence positioning accurate and reliable but the cost is higher.(2) knife from the hydraulic motor drives, fast / slow the points, with proximity switches count and positioning. In comparison ladder diagram of the current storage system knife (knife spindle) and goals knife (pre-knife) and computing, then output rotation instructions, judging by the shortest path rotation in place. This approach requires sufficient hydraulic power and electromagnetic valve knife the rotational speed can be adjusted through the throttle. But over time may be oily hydraulic, oil temperature and environmental factors impact the change in velocity and accuracy. Not generally used in large and medium-sized machine tool change frequently.(3) the knife from AC asynchronous motor driven cam mechanism (Markov institutions), with proximity switches count, which means stable operation, and generally accurate and reliable positioning cam used in conjunction with a mechanical hand, ATC fast-positioning.2. ATC, the main types, characteristics, and the scope of application2.1 Auto Rotary ToolRotary Tool automatically on the use of CNC machine tool is a simpleinstallation of automatic tool change, the Quartet and 47.60 Turret Tool various forms, such as rotary turret were installed on four, six or more of the Tool , NCinstructions by ATC. Rotary Tool has two vertical and horizontal, relatively simple structure, applicable to economic CNC lathe.Rotary Tool in the structure must have good strength and stiffness, resistance to bear rough Cutting Tool in the cutting force and reduce the role of deformation and improve processing accuracy. Rotating Tool to choose reliable positioning programme structure and reasonable position, in order to ensure that each rotary turret to a higher position after repeated positioning accuracy (typically 0.001 to 0.005mm). Figure 2.1 shows the spiral movements of the Quartet Turret.Auto Rotary Tool in the simplest of ATC, is 180 º rotary ATC devices, as shown in Figure 2.2 ATC instructions received, the machine control system put ATC spindle control to the designated location at the same time, the tool movement to the appropriate location, ATC, with the rotary axis and at the same time, the knives matching tool; drawbars from Spindle Cutting Tools rip, ATC, will be the tool from their position removed; ATC, 180 º rotary tool spindle and the tool and tool away; ATC, the Rotary At the same time, thetool refocusing its position to accept Spindle removed from the cutting tool; Next, ATC, will be replaced with the cutter knives were unloaded into the spindle and tool: Finally, back to the original ATC, "standby" position. At this point, ATC completed procedures to continue to run. This ATC, the main advantage of simple structure,the less movement, fast tool change. The main disadvantage is that knives must be kept in parallel with the axis of the plane, and after the home side compared to the tool, chip and liquid-cutting knife into the folder, it is necessary to the tool plus protection. Cone knife folder on the chip will cause ATC error, or even damage knife folders, and the possibility of spindle. Some processing centre at the transfer, and the tool side. When the ATC command is called, the transfer-cutter knives will be removed, the machine go forward, and positioning with the ATC, in line with the position. 180 º "Rotary ATC devices can be used horizontal machine, can also be used for vertical machining centers.2. 2 ATC head-turret installedWith rotating CNC machine tool often used such ATC devices, with a few turret head spindle, each with a spindle on both knives, the first tower interim process can be automatic tool change-realization. The advantage is simple structure, tool change time is short, only about 2 s. However, due to spatial constraints, the number of spindle can not be too much, usually only apply to processes less, not to high precision machine tools, such as the NC drill, such as CNC milling machine. In recent years there has been a mechanical hand and the turret head with a knife for the automatic tool change ATC devices, as shown in Figure 2.3. It is in fact a turret head ATC, and the knife-ATC device combination. The principle is as follows:5 turret on the first two tool spindle 3 and 4, when using the tool spindle 4 processing tool, the manipulator 2 will be the next step to the need for the tool does not work on the tool spindle 3 until after the completion of this process , the first rotary turret 180 º, ATC completed. ATC most of their time and processing time coincidence, the only real tool change time turret transposition of the first time, this approach mainly used for ATC and NC NC drilling file bed.2. 3.Daidao system for the automatic tool changeFigure 2.4 shows the knife and the whole machine tool CNC machine tools for the appearance of Fig. Figure 2.5 shows the knife and split-type machine to the appearance of CNC machine tool plans.At this point, knife storage capacity, a heavier tool can, and often additional transport unit to complete the knife between the spindle and cutting tool transport.Daidao the knife from the ATC, the election knives, automatic loading and unloading machine tool and tool exchange institutions (manipulator), composed of four parts, used widely.Tool Automatic Tool Change When CNC tool code and the code in line with directives of the tool selected, the rotary cutter knives will be sent to the ATC position, waiting to grab manipulator. Random knife election is the advantage of the cutter knife in the order has nothing to do with the processing sequence, the same tool can be used repeatedly. Therefore, the relatively small number of knives, knife the corresponding smaller. Random elections knife on the tool must be coded to identify. There are three main coding.1. Tool coding. Adopt special knife handle structure coding, the drawbars on the knife handle back-endpackages such as spacing of the coding part of the lock-nut fixed. Coding diameter ring diameter of a size two,respectively, said that binary "1" and "0" to the two rings are different, can be a series of code. For example, there are six small diameter of the ring can be made to distinguish between 63 (26-1 = 63) of the coding tool. All of 0 normally not allowed to use the the manipulator system, the whole process more complicated ATC. We must first used in the processing of all installed in the standard tool on the knife handle in the machine outside the pre-size, according to a certain way Add to the knife. ATC, selected first in the knife knife, and then from ATC, from the knife from the knife or spindle, exchange, the new knife into the spindle, the old knife back into the knife.ATC, as the former two knives to accommodate a limited number can not be too many, can not meet the needs of complex parts machining, CNC machine tool Automatic Tool Change Daidao the use of the automatic tool change devices. The knife has more capacity, both installed in the spindle box side or above. As for the automatic tool change Daidao device CNC machine tool spindle box only a spindle, spindle components to high stiffness to meet the machining requirements. The number of establishments in larger knife, which can meet the more complex parts of the machining processes, significantly improving productivity. Daidao system for the automatic tool change applied to drilling centres and CNC machining centers. The comparison drawn Daidao automatic tool change system is the most promising.3.PLC control of the knife random mode of election3. 1Common methods of automatic election knifeAutomatic control of the knife CNC refers to the system after the implementation of user instructions onthe knife library automation process, including the process to find knives and automatic tool change [(63,71]. CNC Machining Center device (CNC) directive issued by the election knife , a knife, the tool required to take the knife position, said the election automatic knife. automatically elected knife There are two ways: randomsequence election knives and knife election method.3.1.1 order election knifeTool Selection order is the process tool according to the sequence of the insert knife, the use of knives in order to take place, used knives back at the original knife, can also order Add Block, a knife. In this way, no need Tool identification devices, and drive control is a relatively simple, reliable and can be used directly from the points of the knife machinery to achieve. But the knives in each of the tool in different processes can not be reused, if the tool is installed in accordance with the order of the knife, there will be serious consequences. Theneed to increase the number of knives and knife the capacity of the tool and reduce the utilization of the knife.3.1.2Random election knifeRandom election under the knife is arbitrary instructions to select the required tools, then there must be tool identification devices. Tool knife in the library do not have the processing in accordance with the order of the workpiece can be arbitrary storage. Each of the tool (or knife blocks) are for a code, automatic tool change, the rotary cutter, every tool have been the "tool identification device" acceptable identification. When CNCtool code and the code in line with directives of the tool selected, the rotary cutter knives will be sent to the ATC position, waiting to grab manipulator. Random knife election is the advantage of the cutter knife in the order has nothing to do with the processing sequence, the same tool can be used repeatedly. Therefore, the relatively small number of knives, knife the corresponding smaller. Random elections knife on the tool must be coded to identify. There are three main coding.1. Tool coding. Adopt special knife handle structure coding, the drawbars on the knife handle back-end packages such as spacing of the coding part of the lock-nut fixed. Coding diameter ring diameter of a size two, respectively, said that binary "1" and "0" to the two rings are different, can be a series of code. For example, there are six small diameter of the ring can be made to distinguish between 63 (26-1 = 63) of the coding tool. All of 0 normally not allowed to use the code, to avoid the cutter knife Block did not confuse the situation.2. Knife Block coding. On the knife Block coding, coding tool, and tool into line with the number of knives in the Block. ATC knife when the rotation, so that each knife seats followed through knowledge knife, knife found blocks, knives stopped the rotation. At this time there is no knife handle encoding part of the knife handle simplified.3. Annex coding methods. This style of coding keys, coded cards, coding and coding-disc, which is the most widely used coding keys. First to knives are attached to a tool of the show wrapped coding keys, and when the cutter knife to the store at knife in, so put the number of keys to remember knife Block Road, will be inserted into key to the coding Block next to the key hole in the seat for the knife to the numbers. ConclusionFocused on in today's manufacturing environment tool storage and management of new models and methods, practical application of good results in systems integration and optimization, and other aspects of operations will be further explored, so that it has a higher theoretical and practical level.译文:机床刀具设计课题研究意义机床原来的刀库控制程序是单独设计的,没有采用刀具管理系统,功能也比较单一,只实现了刀库刀具的找刀、刀库最短路径定位、主轴换刀,而且不支持大型刀具。
数控车床自动回转刀架英文文献以及翻译
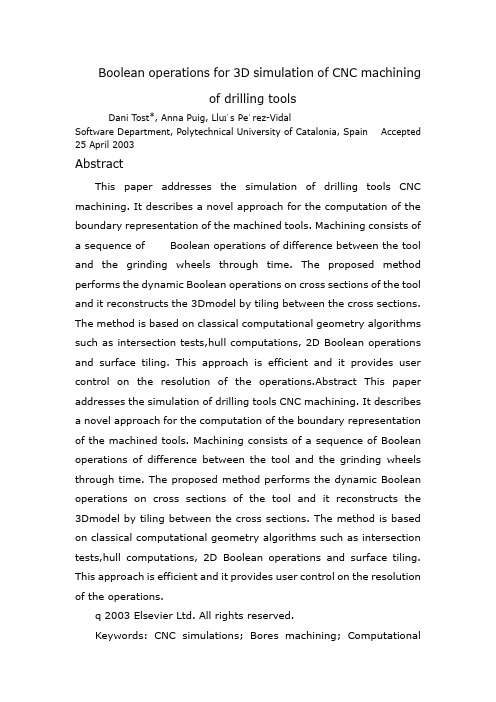
Boolean operations for 3D simulation of CNC machiningof drilling toolsDani Tost*, Anna Puig, Lluı´s Pe´rez-VidalSoftware Department, Polytechnical University of Catalonia, Spain Accepted 25 April 2003AbstractThis paper addresses the simulation of drilling tools CNC machining. It describes a novel approach for the computation of the boundary representation of the machined tools. Machining consists of a sequence of Boolean operations of difference between the tool and the grinding wheels through time. The proposed method performs the dynamic Boolean operations on cross sections of the tool and it reconstructs the 3Dmodel by tiling between the cross sections. The method is based on classical computational geometry algorithms such as intersection tests,hull computations, 2D Boolean operations and surface tiling. This approach is efficient and it provides user control on the resolution of the operations.Abstract This paper addresses the simulation of drilling tools CNC machining. It describes a novel approach for the computation of the boundary representation of the machined tools. Machining consists of a sequence of Boolean operations of difference between the tool and the grinding wheels through time. The proposed method performs the dynamic Boolean operations on cross sections of the tool and it reconstructs the 3Dmodel by tiling between the cross sections. The method is based on classical computational geometry algorithms such as intersection tests,hull computations, 2D Boolean operations and surface tiling. This approach is efficient and it provides user control on the resolution of the operations.q 2003 Elsevier Ltd. All rights reserved.Keywords: CNC simulations; Bores machining; Computationalgeometry; Boolean operations; Surface tiling1. IntroductionMost of the research on CNC in CAD is centered on theautomatic computation of tool paths [5,13]. Given a final tool design, the optimal trajectories of the tool and the grinding wheels must be computed yielding as final result the CNC code. Machining simulation and verification hasexactly the opposite goal: to calculate the tool starting from the CNC code and from a geometrical model of the machine, the wheels and the tool before machining. This simulation has three main applications [6]. First, it detects eventual collisions between the tool or any of the grinding wheels and the rest of the machine. It is important to avoid collisions because serious damages to the machines can follow. Next, simulation provides a means of visually verifying the efficiency of the trajectories, which may result in faster and cheaper processes. Finally, the simulation allows users to check if the surface of the resulting tool is effectively the desired one. In the routine practice of machining, experienced operators have enough skills to imagine the tool final shape by only reading the CNC code.However, they are generally not able to do so with new or non-standard designs. Therefore, the use of a simulation system decreases considerably the tool production cost because it avoids the trial and error process on the real machine with costly materials that is otherwise necessary.This paper addresses a particular type of CNC machining simulation: the grinding of bores and cutters. Conventional CAD systems do not provide a means of realizing this type of simulations and specific applications are needed. Until recently, most of thesimulation applications dealt only with the machining of 2D cross-sections of the tools and they were restricted to the main fluting operation [3]. Three dimensional applications are rather recent [4,23]. They provide a machining simulation for specific 5-axes machines and they are not applicable to general movements. This paper presents a novel approach for the computation of the external shape of the tools through a sequence of coordinated movements of the tool and the wheels on machines of up to 6-axes. The proposed method reduces the 3D problem to 2D dynamic Boolean operations followed by a surface tiling. The 2D solution involves different techniques of planar computational geometry: from intersections to hull computations.The paper is structured as follows. In Section 2 we review previous approaches on machining simulations.Section 3 describes briefly the contour conditions of the simulation. Finally, Section 4 describes the computation of Boolean operations and the results of the implementation are shown in Section 5.2. Previous workMachining can be considered a dynamic Boolean operation of difference between the grinding wheel and the tool. It is dynamic, because both the tool and the wheels move along time through rotations and translations.The Vector Cut [8,10], is probably the most referenced numerical control simulation method. It is an approximate solution that represents the frontier as a set of points and normal vectors that will be cut along the path of the grinding wheel. This method is effective for the simulation of sculptured surface polishing, but it is not extensible to complex motions of the tool and/or the grinding wheels. It is mainly useful to detect mistakes in the path suggestedby the presence of abnormally high or small cut vectors. Besides, except for the extension of Ref. [16], it does not yield directly a model of the bit to be machined.An alternative strategy for machining simulation consists of realizing a sequence of 3D static Boolean operations through time. The main drawback of this strategy is its high computational cost. According to Ref. [11], this is proportional to the number of discrete positions to the fourth. This puts it out of question, in practical terms.Another problem it shows is the granularity of the temporal discretization : it must be very fine if precision in the final tool is required. This means that very little material is cut off in each Boolean operation, and that may entail robustness problems in the computations. A possible method to avoid both problems is to discretize the initial tool model into a voxel or an octree model, [20], to perform all the sequence of Boolean operations on the discrete model and then reconstruct the machined surface, at the end. This approach benefits from the fact that the cost of discrete Boolean operations is much lower and the reconstruction phase at the end of the process is done as late as possible. This option requires the sequence of movements to be specified in terms of relative motion of the grinding wheel, while the tool and its discretization remain fixed. This prerequisite is not always valid and, in particular, it does not hold for the general case of 6-axes machines.Finally, another option taken into account is that of the computation of the volume swept by the tool and the grinding wheel in their motions. A geometric representation of this volume would allow performing only one Boolean difference operation between the two volumes. The main difficulty of this option is the computation of sweptvolumes. There are several references [1,2,21] on this subject, that contain methods generally applied in CAD for extrusions, collisiondetection, and other problems but none of them can be applied to the non-trivial case of simultaneous motion of the two solids in play.The strategy proposed herein overcomes the disadvantages of these methods. It consists of a double discretization of four dimensional space (3D þ time) that reduces the general problem to a sequence of 2D Boolean operations and 3D geometric reconstructions. This algorithm is fast and it provides user-control on simulation accuracy.3. Scene modelThere are different types of machine tools for the fabrication of bores and cutters. They share the same general structure but they differ in the number of degrees of freedom. The method proposed herein deals with machines up to six degrees of freedom. These machines have a static vertical axis (Z in Fig. 1 on which the grinding wheel set can move up and down. One tool is placed on a spindle (the toolholder), that may translate on three axes (X; Y and U) and rotate on two axes (W in relation to the wheel axis and A relative to its own axis). At the beginning of the process, a tool has a piecewise cylindrical or conical shape. Its final shape is the result of a sequence of machining operations consisting of simultaneous movements of the tool and the wheels. The wheel shape is also piecewise cylindrical or conical. It remains unchanged during the process.The machining process is divided into a set of operations, each one with a specific name in CNC jargon. Each operation is performed using a specific wheel. This information is written in the CNC file.Specifically, the main operations are (in their usual order):Fig. 1. 6-Axes machine tool.Fig. 2. Machining operations on a tool.* Fluting: performing the lateral helicoidal of straight grooves* Gashing: cuts in the tool head* Outer diameter sharpening: edge sharpening of the lateral grooves* End face sharpening: edge sharpening of the tool head cuts* Notching: direct cut in the tool head.Fig. 2 shows a real bore and it indicates the operations that have given its shape.Each operation performs several symmetrical cuts in the tool shape. The tool shown in Fig. 2, for instance, has three lateral grooves realized during the ‘Fluting’ operation. Each cut is performed through a sequence of movements. In the CNC code, each movement corresponds to a line instruction specifying the motion axes (X; Y;U; A; or W for the tool and Z for the wheel) along with the amount of rotation or translation to be performed for each edge.4. Machining simulation4.1. OverviewOur approach uses the fact that the tools have a tubular shape. It consists of discretizing the tool in axial sections, performing the machining operations on these crosssections and finally, reconstructing the surface of the tool by tiling between cross-sections. Before machining, the cross-sections are circles. Afterwards, they have a complex shape that may even have been split into separate connected shells at the tool end.The movements are divided into blocks, each one corresponding to an CNC operation or even to one cut within an operation. The machining process is performed sequentially for each block. Therefore, as many intermediate models are created as instruction blocks exist. The initial tool is taken as input of the first machining process. Theresulting tool is used in the second block processing and so on. The surface reconstruction step can be performed on any of these intermediate models or, alternatively only on the last one.Therefore, the simulation process of each instructions block is composed of two steps:* A 2D Boolean operation process, that receives as input: (i) the tool representation, (ii) the machining wheel representation, (iii) a list of movements and that gives as output a new representation of the tool cross-sections.* A tiling process that completes the tool representation with the triangulation between contours.The second step, surface tiling, is a classical subject in computer graphics [14]. It consists of two related problems: (i) establishing correspondences between contours (branching problem) and (ii) searching correspondent vertices to form tiles (correspondence problem). Several solutions have been published to solve both problems based on minimizing the distance between successive contours [7,17] and interpolating in between contours [12]. The method used herein is an extension of these algorithms that adds to these criteria the constraint of tiling between segments of the contour corresponding to the same machining operation. This extension is described in depth in Ref. [22].4.2. Machining of the tool cross-sectionsThe computation of the new shape of tool cross section consists of three steps:* Computation through time of the intersections of the wheel cross sections and the external contour of the tool section. Bothsections are circular and, due to their relative orientation, their intersection is a segment. Therefore, the result of this step is a set of segments.* Calculation of the hulls of the segments set. These hulls are polygonal approximations of wheel cuts on the tool section.* Reconstruction of the tool cross section contour given its original shape and the hull curves.The pseudo-code algorithm below illustrates this process. Let st be the tool cross section at the beginning of the process, where the wheel and ml the movements list. The wheel is discretized into a set of circular cross-sections switch (procedures FirtSectWheel and NextSectWheel). The movement of switch and st is decomposed into a a set of successive positions (inner loop). For each position, the intersection between sw and st is computed in the procedure InterSect. If there is intersection, then the corresponding segment segm is stored in the segments list seglist. Then, the geometry of st, sw and seglist is updated to next positions in the procedure UpdateGeom. The position of st is reset at its initial location for each new wheel section. After all the wheel sections have been processed, the hulls of the segment list are computed in CompHulls and then clipped against the initial contour of st with the procedure Reconstruct.procedure CrossSection Machining(st: tSection,wh: tWheel, ml: tMovList)varsw: tSectionsegm: tSegmentseglist: tSegmentListhulls: tHullListfvarInitSegList(seglist)sw U FirstSectWheel (wh)while ValidSection(sw) doendo f mov U FALSEwhile : endo f mov doInterSect(st,sw, &segm, &status)if status ! InsertSegment(segm, seglist) endifUpdateGeom(ml, &st, &sw, &seglist, &endo fmov)endwhilesw U NextSectWheel(wh,sw)ResetToolPosition(&st)endwhileCompHulls(slist, &hulls)Reconstruct(hulls, &st)fprocedure4.2.1. Updating geometryEach movement instruction is realized at constant speed. Therefore, a movement can be decomposed into n constant intervals of translation in X; Y; Z and U along with rotation in W and A : δA=ΔA/n,δW=ΔW/n,δX=ΔX/n,δY=ΔY/n,δU=ΔU/n andδZ=ΔZ/n.As mentioned in Section 3, a line movement can be composed of several simultaneous instructions. Most of the tool movements are composed of translations and axial rotations, which are independent. Therefore, the order in which the update of each movement is done is irrelevant. However for conical tools with a round end called ‘ball nose’, simultaneous axial translations and colum n angle rotations are necessary. These two movements are obviously not independent. Thiscan be a source of error (Fig. 3) because the real machine rotates the tool column angle at the same time as it translates it along its axis, while in the simulation, for each time interval, the tool is first rotated and next translated along its axis. However, in these cases the original CNC is already decomposed as a set of very small movements with a resolution very similar to the one needed in the machining. Therefore, these movements are not further decomposed in the machining.The global coordinate system in which the geometry is expressed along time is sketched in Fig. 4. The axis coincide with the machine axis X; Y and Z at the tool home position at the beginning of machining. Let ct(xtk, ytk;,0.0)be the coordinates of the tool section center at instant k: The components of the normal vector of the section are ntk(nxtk, nytk,0.0). It should be noted that nxtk =cos(ωk) and nytk= sin(ωk); being vk the column angle of the tool at instant k: The updated values of these coordinates at k +1.Fig. 3. Non equivalent transformations.Fig. 4. Coordinate system, axes and motion.5. Conclusions and future workThis paper describes a novel method for the simulation of drilling tools CNC machining. Our approach simplifies the 4D (space t time) Boolean operations between the tool and the wheels by reducing them to a sequence of intersections between 2D perpendicular cross-sections along time. Specifically, the method discretizes the toolinto cross-sections and simulates machining on the cross sections. Next, the shape of the tool is recomputed by tiling between contours.The primary advantage of this approach is its simplicity. It addition, it provides user-control on the resolution of the simulation: spacing between crosssections as well as time interval between consecutive intersections.Starting from this work, new research and development lines are opened. Specifically, we are working on global pipelines that would put into the same process automatic CNC computation and tool verification. With such pipelines, given a final tool description, theCNC code to create it would be automatically computed, next using the CNC code as input, tool machining would be simulated. Finally, differences between the input and the output model could be computed and shown.钻探工具数控加工三维仿真的布尔运算摘要本文旨在对钻探工具数控加工的仿真研究。
数控刀具专业英语书籍
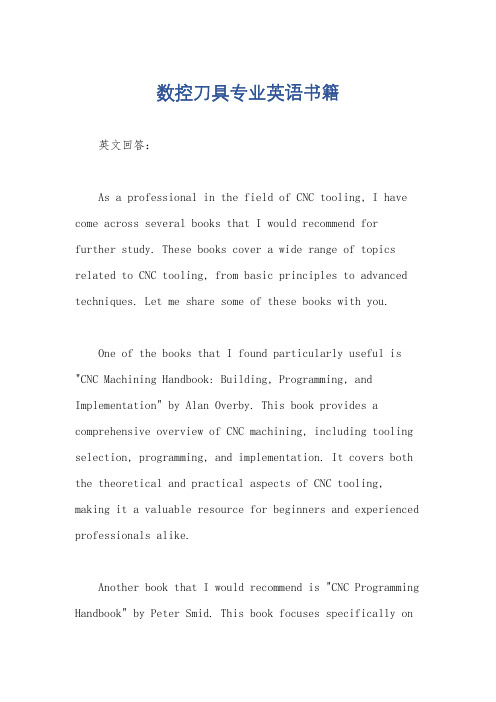
数控刀具专业英语书籍英文回答:As a professional in the field of CNC tooling, I have come across several books that I would recommend forfurther study. These books cover a wide range of topics related to CNC tooling, from basic principles to advanced techniques. Let me share some of these books with you.One of the books that I found particularly useful is "CNC Machining Handbook: Building, Programming, and Implementation" by Alan Overby. This book provides a comprehensive overview of CNC machining, including tooling selection, programming, and implementation. It covers both the theoretical and practical aspects of CNC tooling, making it a valuable resource for beginners and experienced professionals alike.Another book that I would recommend is "CNC Programming Handbook" by Peter Smid. This book focuses specifically onCNC programming, providing detailed explanations of various programming techniques and strategies. It also includes numerous examples and case studies to help readers understand and apply the concepts discussed.For those interested in the design and optimization of cutting tools, "Cutting Tool Technology: Industrial Handbook" by Graham T. Smith is an excellent choice. This book delves into the science behind cutting tool design, materials, and coatings, as well as the latest advancements in tooling technology. It also explores the principles of tool life and performance optimization, providing valuable insights for tooling engineers and researchers.In addition to these books, there are also numerous online resources and forums dedicated to CNC tooling. These platforms provide a wealth of information, including tutorials, discussions, and user experiences. Some popular online resources include CNCZone, Practical Machinist, and CNC Cookbook.中文回答:作为数控刀具领域的专业人士,我遇到了几本我推荐进一步学习的书籍。
数控技术英文参考文献(精选118个最新)

数控技术,英文名称:Numerical Control (简称NC),即采用电脑程序控制机器的方法,按工作人员事先编好的程式对机械零件进行加工的过程。
下面是搜索整理的关于数控技术英文参考文献,欢迎借鉴参考。
数控技术英文参考文献一:[1]Xing Li,Zhouhua Jiang,Xin Geng,Fubin Liu,Leizhen Peng,Shuai Shi. Numerical simulation of a new electroslag remelting technology with current conductive stationary mold[J]. Applied Thermal Engineering,2019,147.[2]Malgorzata Plaza,Wojciech Zebala. A decision model for investment analysis in CNC centers and CAM technology[J]. Computers & Industrial Engineering,2019,131.[3]Rui He,Guoming Chen,Che Dong,Shufeng Sun,Xiaoyu Shen. Data-driven digital twin technology for optimized control in process systems[J]. ISA Transactions,2019.[4]M.J. Zhan,G.F. Sun,Z.D. Wang,X.T. Shen,Y. Yan,Z.H. Ni. Numerical and experimental investigation on laser metal deposition as repair technology for 316L stainless steel[J]. Optics and Laser Technology,2019,118.[5]Andrew Tait,Jonathan G.M. Lee,Bruce R. Williams,Gary A. Montague. Numerical analysis of in-flight freezing droplets: Application to novel particle engineering technology[J]. Food and Bioproducts Processing,2019,116.[6]Gautier Laurent,Caroline Izart,Bénédicte Lechenard,Fabrice Golfier,Philippe Marion,Pauline Collon,Laurent Truche,Jean-Jacques Royer,Lev Filippov. Numerical modelling of column experiments to investigate in-situ bioleaching as an alternative mining technology[J]. Hydrometallurgy,2019,188.[7]. Information Technology; Researchers from University of Orebro Report New Studies and Findings in the Area of Information Technology (Data-driven Conceptual Spaces: Creating Semantic Representations For Linguistic Descriptions Of Numerical Data)[J]. Computers, Networks & Communications,2019.[8]. Energy; Findings from Beijing University of Technology Reveals New Findings on Energy (Numerical investigation of the thermal performance enhancement of latent heat thermal energy storage using longitudinal rectangular fins and flat micro-heat pipe ...)[J]. Energy Weekly News,2019.[9]. Numerical Modeling; Findings on Numerical Modeling Reported by Investigators at University of Shanghai for Science & Technology (Experimental and numerical study on loss characteristics of main steam valve strainer in steam turbine)[J]. Energy Weekly News,2019.[10]. Numerical Modeling; Studies from University of Science and Technology in the Area of Numerical Modeling Described (Modeling of electrochemical properties of potential-induced defects in butane-thiol SAMs by using artificial neural network and impedance ...)[J]. Computers, Networks & Communications,2019.[11]. Numerical Modeling; Study Findings from National University of Defence Science and Technology Provide New Insights into Numerical Modeling (Numerical simulation and structural optimization based on an elliptical and cylindrical raft wave energy conversion device)[J]. Energy Weekly News,2019.[12]. Materials Science - Composite Materials; Investigators at Norwegian University of Science and Technology (NTNU) Detail Findings in Composite Materials (Comparison of numerical modelling techniques for impact investigation on a wind turbine blade)[J]. Energy Weekly News,2019.[13]. Heat Transfer Research; Data on Heat Transfer Research Described by Researchers at AGH University of Science and Technology (A Numerical Analysis of Unsteady Transport Phenomena In a Direct Internal Reforming Solid Oxide Fuel Cell)[J]. Energy Weekly News,2019.[14]. Science - Combustion Science; Investigators at Indian Institute of Technology Describe Findings in Combustion Science (Numerical Simulations of Turbulent Lifted Jet Diffusion Flames In a Vitiated Coflow Using the Stochastic Multiple Mapping Conditioning Approach)[J]. Science Letter,2019.[15]. Science - Combustion Science; Findings from Swiss Federal Institute of Technology in Zurich Provides New Data about Combustion Science (Direct Numerical Simulations of Turbulent Catalytic and Gas-phase Combustion of H-2/air Over Pt At Practically-relevant Reynolds Numbers)[J]. Science Letter,2019.[16]. Science - Combustion Science; Findings from Indian Institute of Technology in Combustion Science Reported (Numerical Modeling of Turbulent Premixed Combustion Using Rans Based Stochastic Multiple Mapping Conditioning Approach)[J]. Science Letter,2019.[17]. Mining and Minerals - Mining Science and Technology; Data on Mining Science and Technology Described by Researchers at Centers for Disease Control and Prevention (Development of a fault-rupture environment in 3D: A numerical tool for examining the mechanical impact of a fault on underground ...)[J]. Medical Letter on the CDC & FDA,2019.[18]. Science - Scientific Computing; Study Results from Missouri University of Science and Technology in the Area of Scientific Computing Reported (A Second Order In Time, Decoupled, Unconditionally Stable Numerical Scheme for theCahn-hilliard-darcy System)[J]. Science Letter,2019.[19]. Science - Applied Sciences; Findings from University of Science and Technology in Applied Sciences Reported (Numerical Study of the Effect of Inclusions On the Residual Stress Distribution In High-strength Martensitic Steels During Cooling)[J]. Science Letter,2019.[20]. Science - Crystallography; New Crystallography Findings Has Been Reported by Investigators at Royal Institute of Technology (On Plowing Frictional Behavior During Scratch Testing: a Comparison Between Experimental and Theoretical/numerical Results)[J]. Science Letter,2019.[21]. Information Technology; Report Summarizes Information Technology Study Findings from University of Defense (Comparison of Static Aerodynamic Data Obtained In Dynamic Wind Tunnel Tests and Numerical Simulation Research)[J]. Computers, Networks & Communications,2019.[22]. Energy; New Findings from Hefei University of Technology Describe Advances in Energy (Numerical Study of the Effect of Combustion Chamber Structure On Scavenging Process In a Boosted Gdi Engine)[J]. Energy Weekly News,2019.[23]. Fuel Research; Study Results from Sahand University of Technology Update Understanding of Fuel Research (Advanced Numerical Analyses On Thermal, Chemical and Dilution Effects of Water Addition On Diesel Engine Performance and Emissions Utilizing Artificial ...)[J]. Energy Weekly News,2019.[24]. Energy - Energy and the Environment; Researchers from Iran University of Science and Technology Describe Findings in Energy and the Environment (Numerical Investigation of the Power Extraction Mechanism of Flapping Foil Tidal Energy Harvesting Devices)[J]. Energy Weekly News,2019.[25]. Energy; Findings from Cracow University of Technology Provide New Insights into Energy (Numerical and Experimental Study On the Thermal Performance of the Concrete Accumulator for Solar Heating Systems)[J]. Energy Weekly News,2019.[26]. Energy; Studies from Huazhong University of Science and Technology Yield New Information about Energy (Numerical Study On Heat Transfer Performance In Packed Bed)[J]. Energy Weekly News,2019.[27]. Energy; Studies from Jiangsu University of Science and Technology Describe New Findings in Energy (Numerical Study On Thermal Hydraulic Performance of Supercritical Lng In Zigzag-type Channel Pches)[J]. Energy Weekly News,2019.[28]. Energy; Studies from Harbin Institute of Technology Add New Findings inthe Area of Energy (A Numerical Study On the Development of Self-similarity In a Wind Turbine Wake Using an Improved Pseudo-spectral Large-eddy Simulation Solver)[J]. Energy Weekly News,2019.[29]. Science - Combustion Science; Studies from Massachusetts Institute of Technology Reveal New Findings on Combustion Science (Numerical Investigation of Strained Extinction At Engine-relevant Pressures: Pressure Dependence and Sensitivity To Chemical and Physical Parameters ...)[J]. Energy Weekly News,2019.[30]. Energy; Findings on Energy Discussed by Investigators at Federal University of Technology Parana (Numerical Two-dimensional Steady-state Evaluation of the Thermal Transmittance Reduction In Hollow Blocks)[J]. Energy Weekly News,2019.数控技术英文参考文献二:[31]. Geofluids; Investigators at China University of Mining and Technology Detail Findings in Geofluids (Numerical Simulations On the Front Motion of Water Permeation Into Anisotropic Porous Media)[J]. Science Letter,2019.[32]. Science - Combustion Science; Studies from National University of Defence Science and Technology Add New Findings in the Area of Combustion Science (Numerical Study of Cellular Detonation Wave Reflection Over a Cylindrical Concave Wedge)[J]. Energy Weekly News,2019.[33]. Energy; Reports Summarize Energy Findings from Darmstadt University of Technology (Numerical Investigation of an Oxyfuelnon-premixed Combustionusing a Hybrid Eulerian Stochastic Field/flamelet Progress Variable Approach: Effects of H-2/co2 Enrichment ...)[J]. Energy Weekly News,2019.[34]. Energy - Hydrogen Energy; Data on Hydrogen Energy Described by Researchers at King Mongkut's University of Technology Thonburi (Comparative Numerical Evaluation of Autothermal Biogas Reforming In Conventional and Split-and-recombine Microreactors)[J]. Energy Weekly News,2019.[35]. Food and Bioproducts; New Data from Indian Institute for Technology Illuminate Findings in Food and Bioproducts (Heat Transfer Analysis During Mixed-mode Solar Drying of Potato Cylinders Incorporating Shrinkage: Numerical Simulation and Experimental Validation)[J]. Food Weekly News,2019.[36]. Energy - Energy Materials; Findings from Dalian University of Technology Broaden Understanding of Energy Materials (Tailoring Active Sites In Mesoporous Defect-rich Nc/v-o-won Heterostructure Array for Superior Electrocatalytic Hydrogen Evolution)[J]. Energy Weekly News,2019.[37]. Science - Water Science and Technology; New Water Science and Technology Study Findings Recently Were Reported by Researchers at Zhejiang University (Numerical Study of the Collapse of Multiple Bubbles and the Energy Conversion During Bubble Collapse)[J]. Energy Weekly News,2019.[38]. Energy - Renewable Energy; Reports from Sharif University of Technology Advance Knowledge in Renewable Energy (A Numerical Study of Dust Deposition Effects On Photovoltaic Modules and Photovoltaic-thermal Systems)[J]. Energy Weekly News,2019.[39]. Science - Combustion Science; New Combustion Science Findings from Beijing Institute of Technology Discussed (Experimental and Numerical Studies On Detonation Reflections Over Cylindrical Convex Surfaces)[J]. Energy Weekly News,2019.[40]Maryann Valentine. CNC Technology at Fresno City College[J]. Tech Directions,2019,78(9).[41]. Science - Applied Sciences; Investigators at Czestochowa University of Technology Describe Findings in Applied Sciences (Numerical Analysis of Flow In Building Arrangement: Computational Domain Discretization)[J]. Science Letter,2019.[42]. Science; Reports Summarize Science Study Results from Indian Institute of Technology Madras (Numerical Modeling of Evaporation and Combustion of Isolated Liquid Fuel Droplets: a Review)[J]. Energy Weekly News,2019.[43]. Science - Fire Science; Dalian University of Technology Details Findings in Fire Science (Fire Resistance of Steel Beam To Square Cfst Column Composite Joints Using Rc Slabs: Experiments and Numerical Studies)[J]. Science Letter,2019.[44]. Energy; Researchers' Work from Sharif University of Technology Focuses on Energy (An Improved Actuator Disc Model for the Numerical Prediction of the Far-wake Region of a Horizontal Axis Wind Turbine and Its Performance)[J]. Energy Weekly News,2019.[45]. Engineering - Wind Engineering; Hefei University of Technology Details Findings in Wind Engineering (Numerical Simulation of Wind-driven Rain Distribution On Building Facades Under Combination Layout)[J]. Energy Weekly News,2019.[46]. Western Digital Technologies Inc.; Patent Issued for Switching Period Control Of Microwave Assisted Magnetic Recording For Pole Erasure Suppression (USPTO 10,283,159)[J]. Computers, Networks & Communications,2019.[47]. Energy - Wind Turbines; Investigators at Huazhong University of Science and Technology Describe Findings in Wind Turbines (Numerical Analysis of a CatenaryMooring System Attached By Clump Masses for Improving the Wave-resistance Ability of a Spar Buoy-type Floating ...)[J]. Energy Weekly News,2019.[48]. Energy - Nuclear Power; New Data from Karlsruhe Institute of Technology Illuminate Findings in Nuclear Power (Numerical Study of Thermal Hydraulics Behavior On the Integral Test Facility for Passive Containment Cooling System Using Gasflow-mpi)[J]. Energy Weekly News,2019.[49]. Energy - Energy Exploration; Researchers from Dawood University of Engineering & Technology Detail Findings in Energy Exploration (Numerical Simulation of Lignocellulosic Biomass Gasification In Concentric Tube Entrained Flow Gasifier Through Computational Fluid Dynamics)[J]. Energy Weekly News,2019.[50]. Fuel Research; Researchers at King Abdullah University of Science and Technology Have Reported New Data on Fuel Research (An Experimental/numerical Investigation of the Role of the Quarl In Enhancing the Blowout Limits of Swirl-stabilized Turbulent ...)[J]. Energy Weekly News,2019.[51]. Technology - Green Technology; Findings from National Institute of Technology Has Provided New Data on Green Technology (Influence of Thermal Energy Storage System On Flow and Performance Parameters of Solar Updraft Tower Power Plant: a Three Dimensional Numerical Analysis)[J]. Energy Weekly News,2019.[52]. Atmosphere Research; Studies from AGH University of Science and Technology Update Current Data on Atmosphere Research (Prediction of Air Temperature In the Polish Western Carpathian Mountains With the Aladin-hirlam Numerical Weather Prediction System)[J]. Science Letter,2019.[53]. Energy - Oil and Gas Research; Researchers at Amirkabir University of Technology Release New Data on Oil and Gas Research (Numerical Investigation for Determination of Aquifer Properties In Newly Developed Reservoirs: a Case Study In a Carbonate Reservoir)[J]. Energy Weekly News,2019.[54]. Science - Refrigeration Science; Findings from Indian Institute of Technology Kanpur Provides New Data about Refrigeration Science (Numerical Investigation of Isothermal and Non-isothermal Ice Slurry Flow In Horizontal Elliptical Pipes)[J]. Science Letter,2019.[55]. Energy - Renewable Energy; Researchers from Delft University of Technology Detail Findings in Renewable Energy (The Dynamic Wake of an Actuator Disc Undergoing Transient Load: a Numerical and Experimental Study)[J]. Energy Weekly News,2019.[56]. Energy; Researchers from Wroclaw University of Science and Technology Describe Findings in Energy (Theoretical and Numerical Analysis of Freezing RiskDuring Lng Evaporation Process)[J]. Energy Weekly News,2019.[57]. Geomechanics; Researchers from Chengdu University of Technology Report Findings in Geomechanics (Behavior and Numerical Evaluation of Cement-fly Ash-gravel Pile-supported Embankments Over Completely Decomposed Granite Soils)[J]. Science Letter,2019.[58]. Macromolecular Research; Investigators from Swiss Federal Institute of Technology Have Reported New Data on Macromolecular Research (Numerical Estimates of the Topological Effects In the Elasticity of Gaussian Polymer Networks and Their Exact Theoretical Description)[J]. Science Letter,2019.[59]. Food Processing; Findings from Institute of Chemical Technology Reveals New Findings on Food Processing (Comparison Between Multiresponse-robust Process Design and Numerical Optimization: a Case Study On Baking of Fermented Chickpea Flour-based Wheat Bread)[J]. Food Weekly News,2019.[60]. Technology; Studies from Sun Yat Sen University Yield New Information about Technology (Numerical Investigation of Influence of Reservoir Heterogeneity On Electricity Generation Performance of Enhanced Geothermal System)[J]. Energy Weekly News,2019.数控技术英文参考文献三:[61]. Energy - Solar Energy; Study Results from Izmir Institute of Technology in the Area of Solar Energy Reported (Experimental and Numerical Investigation of Forced Convection In a Double Skin Facade By Using Nodal Network Approach for Istanbul)[J]. Energy Weekly News,2019.[62]. Science - Earth and Space Science; Investigators at Massachusetts Institute of Technology Report Findings in Earth and Space Science (Esh3d, an Analytical and Numerical Hybrid Code for Full Space and Half-space Eshelby's Inclusion Problems)[J]. Science Letter,2019.[63]. Science - Forensic Science; New Findings from Beijing Institute of Technology in Forensic Science Provides New Insights (The Experimental and Numerical Investigation On the Ballistic Limit of Bb-gun Pellet Versus Skin Simulant)[J]. Science Letter,2019.[64]. Hydrodynamics; Research Conducted at Jiangsu University of Science and Technology Has Updated Our Knowledge about Hydrodynamics (Numerical Investigations of the Effects of Blade Shape On the Flow Characteristics In a Stirred Dead-end Membrane Bioreactor)[J]. Science Letter,2019.[65]. Technology - Fuel Technology; Data on Fuel Technology Reported by Researchers at Northeast Petroleum University (Numerical Simulation of the Air Injection Process In Low Permeability Reservoirs)[J]. Energy Weekly News,2019.[66]. Energy; New Energy Findings from Anhui University of Technology Described (Numerical Study On the Effect of Separated Over-fire Air Ratio On Combustion Characteristics and Nox Emission In a 1000 Mw Supercritical Co2 Boiler)[J]. Energy Weekly News,2019.[67]. Fuel Research; Findings from East China University of Science and Technology Broaden Understanding of Fuel Research (Numerical Study of Dynamic Response Analysis of Slag Behaviors In an Entrained Flow Gasifier)[J]. Energy Weekly News,2019.[68]. Energy; Findings from Babol Noshirvani University of Technology Has Provided New Data on Energy (Numerical Study of Heat Transfer On Using Lobed Cross Sections In Helical Coil Heat Exchangers: Effect of Physical and Geometrical Parameters)[J]. Energy Weekly News,2019.[69]. Energy; New Energy Study Results Reported from Nanjing University of Science and Technology (Numerical Investigation of the Effect of Sudden Expansion Ratio of Solid Fuel Ramjet Combustor With Swirling Turbulent Reacting Flow)[J]. Energy Weekly News,2019.[70]. Energy; Reports from Amirkabir University of Technology Add New Data to Findings in Energy (Numerical Study of Anode Side Co Contamination Effects On Pem Fuel Cell Performance; and Mitigation Methods)[J]. Energy Weekly News,2019.[71]. Science - Geoscience; Findings from China University of Mining and Technology Broaden Understanding of Geoscience (The Exhumation Along the Kenyase and Ketesso Shear Zones In the Sefwi Terrane, West African Craton: a Numerical Study)[J]. Science Letter,2019.[72]. Science - Refrigeration Science; Findings from Sirjan University of Technology Broaden Understanding of Refrigeration Science (A geometric model for a vortex tube based on numerical analysis to reduce the effect of nozzle number)[J]. Science Letter,2019.[73]. Science - Topography and Metrology; Researchers from Isfahan University of Technology Detail New Studies and Findings in the Area of Topography and Metrology (Numerical and experimental study on the effect of considering plastic and elastoplastic deformation of each asperity in ...)[J]. Science Letter,2019.[74]. Science; New Science Findings from Dalian University of Technology Outlined(Numerical research on the anti-sloshing effect of a ring baffle in an independent type C LNG tank)[J]. Science Letter,2019.[75]. Science - Terramechanics; Findings from National University of Defence Science and Technology in Terramechanics Reported (Development and numerical validation of an improved prediction model for wheel-soil interaction under multiple operating conditions)[J]. Science Letter,2019.[76]. Science - Textile Research; Findings from Lodz University of Technology Update Knowledge of Textile Research (Numerical Analysis of Free Folding of Flat Textile Products and Proposal of New Test Concerning Bending Rigidity)[J]. Science Letter,2019.[77]. Science - Technical Sciences; Findings from Warsaw University of Technology in the Area of Technical Sciences Reported (Pulse Powered Turbine Engine Concept - Numerical Analysis of Influence of Different Valve Timing Concepts On Thermodynamic Performance)[J]. Science Letter,2019.[78]. Energy - Energy Storage; Findings from Iran University of Science and Technology Has Provided New Data on Energy Storage (Numerical investigation of different PCM volume on cold thermal energy storage system)[J]. Energy Weekly News,2019.[79]. Science - Maritime Research; New Maritime Research Findings from Wuhan University of Technology Described (Numerical Simulation of Solid-fluid 2-phase-flow of Cutting System for Cutter Suction Dredgers)[J]. Science Letter,2019.[80]. Energy; Investigators at Swiss Federal Institute of Technology in Zurich Describe Findings in Energy (Numerical Optimization of Methane-based Fuel Blends Under Engine-relevant Conditions Using a Multi-objective Genetic Algorithm)[J]. Energy Weekly News,2019.[81]. Science - Refrigeration Science; Study Data from Jiangsu University of Science and Technology Update Understanding of Refrigeration Science (A Numerical Study On Condensation Flow and Heat Transfer of Refrigerant In Minichannels of Printed Circuit Heat Exchanger)[J]. Science Letter,2019.[82]. Information Technology; Researchers from Sao Paulo State University Provide Details of New Studies and Findings in the Area of Information Technology (Effective Force Area and Discharge Coefficient for Reed Type Valves: a Comprehensive Data Set From a Numerical Study)[J]. Computers, Networks & Communications,2019.[83]. Science - Applied Sciences; Findings on Applied Sciences Discussed by Investigators at Czestochowa University of Technology (A Sequential Approach toNumerical Simulations of Solidification with Domain and Time Decomposition)[J]. Science Letter,2019.[84]. Energy; New Energy Findings from National University of Defence Science and Technology Described (A 3D Numerical Study of Supersonic Steam Dumping Process of the Pressurizer Relief Tank)[J]. Energy Weekly News,2019.[85]. Science and Technology; Study Findings on Science and Technology Are Outlined in Reports from H. Yi and Colleagues (Simulations and error analysis of the CNC milling of a face gear tooth with given tool paths)[J]. Science Letter,2019.[86]. Energy - Wind Turbines; Data on Wind Turbines Reported by Researchers at Lulea University of Technology (Numerical Investigation of the Aeroelastic Behavior of a Wind Turbine with Iced Blades)[J]. Energy Weekly News,2019.[87]. Information Technology - Information and Data Aggregation; Studies from Marchuk Institute of Numerical Mathematics in the Area of Information and Data Aggregation Reported (Domain Decomposition Method for the Variational Assimilation of the Sea Level in a Model of Open Water Areas Hydrodynamics)[J]. Computers, Networks & Communications,2019.[88]. Energy; Investigators at Kaunas University of Technology Describe Findings in Energy (Field Measurements and Numerical Simulation for the Definition of the Thermal Stratification and Ventilation Performance in a Mechanically Ventilated Sports Hall)[J]. Energy Weekly News,2019.[89]. Geomechanics; Data from Wuhan University of Science and Technology Advance Knowledge in Geomechanics (Strength and Failure Characteristics of Rocklike Material Containing a Large-opening Crack Under Uniaxial Compression: Experimental and Numerical Studies)[J]. Science Letter,2019.[90]. Energy - Wind Turbines; Findings on Wind Turbines Reported by Investigators at Hong Kong University of Science and Technology (A Numerical Study On the Performance of a Savonius-type Vertical-axis Wind Turbine In a Confined Long Channel)[J]. Energy Weekly News,2019.数控技术英文参考文献四:[91]. Fuel Research; New Findings from Indian Institute for Technology Describe Advances in Fuel Research (Experimental and numerical investigations on the laminar burning velocity of n-butanol + air mixtures at elevated temperatures)[J]. Energy Weekly News,2019.[92]. Fuel Research; Findings in the Area of Fuel Research Reported from DalianUniversity of Technology (Experimental and numerical study of the effect of injection strategy and intake valve lift on super-knock and engine performance in a boosted GDI engine)[J]. Energy Weekly News,2019.[93]. Energy - Wind Turbines; New Data from Babol Noshirvani University of Technology Illuminate Findings in Wind Turbines (Numerical Investigation of the Savonius Vertical Axis Wind Turbine and Evaluation of the Effect of the Overlap Parameter in Both Horizontal and ...)[J]. Energy Weekly News,2019.[94]. Biosensors; Investigators at East China University of Science and Technology Detail Findings in Biosensors (Numerical and Experimental Assessment of a Miniature Bioreactor Equipped With a Mechanical Agitator and Non-invasive Biosensors)[J]. Biotech Week,2019.[95]. Science - Geoscience; Studies from Warsaw University of Technology Have Provided New Data on Geoscience (Selected components of geological structures and numerical modelling of slope stability)[J]. Science Letter,2019.[96]. Fuel Research; Reports from Huazhong University of Science and Technology Provide New Insights into Fuel Research (Experimental and Numerical Study of the Fuel-nox Formation At High Co2 Concentrations In a Jet-stirred Reactor)[J]. Energy Weekly News,2019.[97]. Energy; Studies from Darmstadt University of Technology Add New Findings in the Area of Energy (Numerical Investigation of Flow through a Valve during Charge Intake in a DISI -Engine Using Large Eddy Simulation)[J]. Energy Weekly News,2019.[98]. Energy; Studies from Shandong University of Technology Provide New Data on Energy (Experimental and Numerical Studies On the Effect of Packed Bed Length On Co and Nox Emissions In a Plane-parallel Porous Combustor)[J]. Energy Weekly News,2019.[99]Weijian Yu,Ze Liu,Baifu An,Fangfang Liu,Yunbo Wang. Numerical Calculation and Stability of the Yield and Enhanced Support Technology for Shaft[J]. Geotechnical and Geological Engineering,2019,37(4).[100]Jorge Manuel Mercado-Colmenero,Miguel Angel Rubio-Paramio,M? Dolores Rubia-Garcia,David Lozano-Arjona,Cristina Martin-Do?ate. A numerical and experimental study of the compression uniaxial properties of PLA manufactured with FDM technology based on product specifications[J]. The International Journal of Advanced Manufacturing Technology,2019,103(5-8).[101]Shuping Chen. Teaching Reform and Practice on Course of Numerical Computation Method in Applied Technology Undergraduate Institutes[P]. Proceedingsof the 2nd International Seminar on Education Research and Social Science (ISERSS 2019),2019.[102]Nouvet Elysée,Knoblauch Astrid M,Passe Ian,Andriamiadanarivo Andry,Ravelona Manualdo,Ainanomena Ramtariharisoa Faniry,Razafimdriana Kimmerling,Wright Patricia C,McKinney Jesse,Small Peter M,Rakotosamimanana Niaina,Grandjean Lapierre Simon. Perceptions of drones, digital adherence monitoring technologies and educational videos for tuberculosis control in remote Madagascar: a mixed-method study protocol.[J]. BMJ open,2019,9(5).[103]He Rui,Chen Guoming,Dong Che,Sun Shufeng,Shen Xiaoyu. Data-driven digital twin technology for optimized control in process systems.[J]. ISA transactions,2019.[104]Tatti Fabio,Petrangeli Papini Marco,Torretta Vincenzo,Mancini Giuseppe,Boni Maria Rosaria,Viotti Paolo. Experimental and numerical evaluation of Groundwater Circulation Wells as a remediation technology for persistent, low permeability contaminant source zones.[J]. Journal of contaminant hydrology,2019.[105]Revels Christy,Burris Christie. NC HealthConnex and Value-based Care: Statewide Health Information Exchange as a Technology Tool for All.[J]. North Carolina medical journal,2019,80(4).[106]Kubit Andrzej,Trzepiecinski Tomasz,?wi?ch ?ukasz,Faes Koen,Slota Jan. Experimental and Numerical Investigations of Thin-Walled Stringer-Stiffened Panels Welded with RFSSW Technology under Uniaxial Compression.[J]. Materials (Basel, Switzerland),2019,12(11).[107]董新峰,仇中柱,韩清鹏. 数控技术课程中超硬材料切削加工所涉及的关键问题的引入[J]. 教育进展,2019,09(03).[108]Hua Chen,Ke-Lun Xia,Zi-Jun Liu,Xun-Si Wang,Xiang-Hua Zhang,Yin-Sheng Xu,Shi-Xun Dai. Experimental and numerical investigation of mid-infrared laser in Pr<sup>3+</sup>-doped chalcogenide fiber Project supported by the Young Scientists Fund of the National Natural Science Foundation of China (Grant No. 61605095), the Natural Science Foundation of Zhejiang Province, China (Grant No. LY19F050004), the Natural Science Foundation of Ningbo City (Grant No. 2015A610038), the Open Fund of the Guangdong Engineering Technology Research and Development Center of Special Optical Fiber Materials and Devi[J]. Chinese Physics B,2019,28(2).[109]Zhengwei Yang,Xingyu Xie,Yin Li,Gan Tian. Numerical Analysis of Influencing Factors and Capability for Line Laser Scanning Thermography Nondestructive Testing Technology in Chemicals Corrosion Defect Detection[J]. IOP Conference Series: Materials Science and Engineering,2019,484(1).。
数控机床专业英语(超级棒).
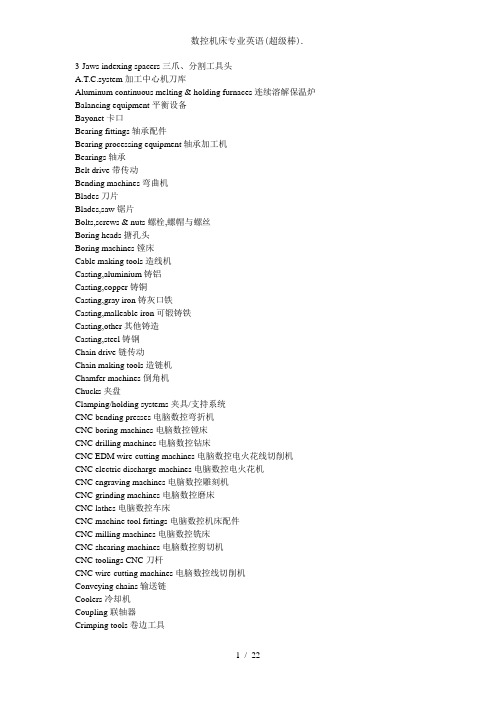
3-Jaws indexing spacers 三爪、分割工具头A.T.C.system 加工中心机刀库Aluminum continuous melting & holding furnaces 连续溶解保温炉Balancing equipment 平衡设备Bayonet 卡口Bearing fittings 轴承配件Bearing processing equipment 轴承加工机Bearings 轴承Belt drive 带传动Bending machines 弯曲机Blades 刀片Blades,saw 锯片Bolts,screws & nuts 螺栓,螺帽与螺丝Boring heads 搪孔头Boring machines 镗床Cable making tools 造线机Casting,aluminium 铸铝Casting,copper 铸铜Casting,gray iron 铸灰口铁Casting,malleable iron 可锻铸铁Casting,other 其他铸造Casting,steel 铸钢Chain drive 链传动Chain making tools 造链机Chamfer machines 倒角机Chucks 夹盘Clamping/holding systems 夹具/支持系统CNC bending presses 电脑数控弯折机CNC boring machines 电脑数控镗床CNC drilling machines 电脑数控钻床CNC EDM wire-cutting machines 电脑数控电火花线切削机CNC electric discharge machines 电脑数控电火花机CNC engraving machines 电脑数控雕刻机CNC grinding machines 电脑数控磨床CNC lathes 电脑数控车床CNC machine tool fittings 电脑数控机床配件CNC milling machines 电脑数控铣床CNC shearing machines 电脑数控剪切机CNC toolings CNC刀杆CNC wire-cutting machines 电脑数控线切削机Conveying chains 输送链Coolers 冷却机Coupling 联轴器Crimping tools 卷边工具Cutters 刀具Cutting-off machines 切断机Diamond cutters 钻石刀具Dicing saws 晶圆切割机Die casting dies 压铸冲模Die casting machines 压铸机Dies-progressive 连续冲模Disposable toolholder bits 舍弃式刀头Drawing machines 拔丝机Drilling machines 钻床Drilling machines bench 钻床工作台Drilling machines,high-speed 高速钻床Drilling machines,multi-spindle 多轴钻床Drilling machines,radial 摇臂钻床Drilling machines,vertical 立式钻床drills 钻头Electric discharge machines(EDM) 电火花机Electric power tools 电动刀具Engraving machines 雕刻机Engraving machines,laser 激光雕刻机Etching machines 蚀刻机Finishing machines 修整机Fixture 夹具Forging dies 锻模Forging,aluminium 锻铝Forging,cold 冷锻Forging,copper 铜锻Forging,other 其他锻造Forging,steel 钢锻Foundry equipment 铸造设备Gear cutting machines 齿轮切削机Gears 齿轮Gravity casting machines 重力铸造机Grinder bench 磨床工作台Grinders,thread 螺纹磨床Grinders,tools & cutters 工具磨床Grinders,ultrasonic 超声波打磨机Grinding machines 磨床Grinding machines,centerless 无心磨床Grinding machines,cylindrical 外圆磨床Grinding machines,universal 万能磨床Grinding tools 磨削工具Grinding wheels 磨轮Hand tools 手工具Hard/soft and free expansion sheet making plant 硬(软)板(片)材与自由发泡板机组Heat preserving furnaces 保温炉Heating treatment funaces 熔热处理炉Honing machines 搪磨机Hydraulic components 液压元件Hydraulic power tools 液压工具Hydraulic power units 液压动力元件Hydraulic rotary cylinders 液压回转缸Jigs 钻模Lapping machines 精研机Lapping machines,centerless 无心精研机Laser cutting 激光切割Laser cutting for SMT stensil 激光钢板切割机Lathe bench 车床工作台Lathes,automatic 自动车床Lathes,heavy-duty 重型车床Lathes,high-speed 高速车床Lathes,turret 六角车床Lathes,vertical 立式车床Lubricants 润滑液Lubrication Systems 润滑系统Lubricators 注油机Machining centers,general 通用加工中心Machining centers,horizontal 卧式加工中心Machining centers,horizontal & vertical 卧式与立式加工中心Machining centers,vertical 立式加工中心Machining centers,vertical double-column type 立式双柱加工中心Magnetic tools 磁性工具Manifolds 集合管Milling heads 铣头Milling machines 铣床Milling machines,bed type 床身式铣床Milling machines,duplicating 仿形铣床Milling machines,horizontal 卧式铣床Milling machines,turret vertical 六角立式铣床Milling machines,universal 万能铣床Milling machines,vertical 立式铣床Milling machines,vertical & horizontal 立式与卧式铣床Mold & die components 模具单元Mold changing systems 换模系统Mold core 模芯Mold heaters/chillers 模具加热器/冷却器Mold polishing/texturing 模具打磨/磨纹Mold repair 模具维修Molds 模具Nail making machines 造钉机Oil coolers 油冷却器Overflow cutting machines for aluminium wheels 铝轮冒口切断机P type PVC waterproof rolled sheet making plant P型PVC高分子防水PCB fine piecing systems 印刷电器板油压冲孔脱料系统Pipe & tube making machines 管筒制造机Planing machines 刨床Planing machines vertical 立式刨床Pneumatic hydraulic clamps 气油压虎钳Pneumatic power tools 气动工具Powder metallurgic forming machines 粉末冶金成型机Presses,cold forging 冷锻冲压机presses,crank 曲柄压力机Presses,eccentric 离心压力机Presses,forging 锻压机Presses,hydraulic 液压冲床Presses,knuckle joint 肘杆式压力机Presses,pneumatic 气动冲床Presses,servo 伺服冲床Presses,transfer 自动压力机Pressing dies 压模Punch formers 冲子研磨器Quick die change systems 速换模系统Quick mold change systems 快速换模系统Reverberatory furnaces 反射炉Rollers 滚筒Rolling machines 辗压机Rotary tables 转台Sawing machines 锯床Sawing machines,band 带锯床Saws,band 带锯Saws,hack 弓锯Saws,horizontal band 卧式带锯Saws,vertical band 立式带锯shafts 轴Shapers 牛头刨床Shearing machines 剪切机Sheet metal forming machines 金属板成型机Sheet metal working machines 金属板加工机Slotting machines 插床spindles 主轴Stamping parts 冲压机Straightening machines 矫直机Switches & buttons 开关与按钮Tapping machines 攻螺丝机Transmitted chains 传动链Tube bending machines 弯管机Vertical hydraulic broaching machine 立式油压拉床Vises 虎钳Vises,tool-maker 精密平口钳Wheel dressers 砂轮修整器Woven-Cutting machines 织麦激光切割机Wrenches 扳手Assembly line组装线Layout布置图Conveyer流水线物料板Rivet table拉钉机Rivet gun拉钉枪Screw driver起子Electric screw driver电动起子Pneumatic screw driver气动起子worktable 工作桌OOBA开箱检查fit together组装在一起fasten锁紧(螺丝)fixture 夹具(治具)pallet栈板barcode条码barcode scanner条码扫描器fuse together熔合fuse machine热熔机repair修理operator作业员QC品管supervisor 课长ME制造工程师MT制造生技cosmetic inspect外观检查inner parts inspect内部检查thumb screw大头螺丝lbs. inch镑、英寸EMI gasket导电条front plate前板rear plate后板chassis 基座bezel panel面板power button电源按键reset button重置键Hi-pot test of SPS高源高压测试Voltage switch of SPS电源电压接拉键sheet metal parts 冲件plastic parts塑胶件SOP制造作业程序material check list物料检查表work cell工作间trolley台车carton纸箱sub-line支线left fork叉车personnel resource department 人力资源部production department生产部门planning department企划部QC Section品管科stamping factory冲压厂painting factory烤漆厂molding factory成型厂common equipment常用设备uncoiler and straightener整平机punching machine 冲床robot机械手hydraulic machine油压机lathe车床planer、plein刨床miller铣床grinder磨床driller床linear cutting线切割electrical sparkle电火花welder电焊机staker=reviting machine铆合机position职务president董事长general manager总经理special assistant manager特助factory director厂长department director部长deputy manager、vice manager副理section supervisor课长deputy section supervisor、vice section superisor副课长group leader/supervisor组长line supervisor线长assistant manager助理to move, to carry, to handle搬运be put in storage入库pack packing包装to apply oil擦油to file burr 锉毛刺final inspection终检to connect material接料to reverse material 翻料wet station沾湿台Tiana天那水cleaning cloth抹布 to load material上料to unload material卸料to return material/stock to退料scraped 报废scrape 刮;削deficient purchase 来料不良 manufacture procedure 制程rotating speed, revolution 转速deficient manufacturing procedure 制程不良delivery deadline交货期oxidation 氧化scratch 刮伤dents 压痕defective upsiding down抽芽不良defective to staking 铆合不良embedded lump 镶块feeding is not in place 送料不到位stamping-missing 漏冲production capacity 生产力education and training 教育与训练proposal improvement 提案改善spare parts、buffer 备件forklift叉车trailer、long vehicle拖板车compound die合模die locker锁模器pressure plate、plate pinch压板bolt螺栓name of a department部门名称administration/general affairs dept总务部automatic screwdriver电动启子thickness gauge厚薄规gauge(or jig)治具power wire电源线buzzle蜂鸣器defective product label不良标签identifying sheet list标示单screwdriver holder起子插座pedal踩踏板stopper阻挡器flow board流水板hydraulic handjack油压板车forklift叉车pallet栈板glove(s)手套glove(s) with exposed fingers割手套thumb大拇指forefinger食指midfinger中指ring finger无名指little finger小指band-aid创可贴garbage can垃圾箱garbage bag垃圾袋chain链条jack升降机production line流水线chain链条槽magnetizer加磁器lamp holder灯架to mop the floor拖地to clean the floor扫地to clean a table擦桌子air pipe 气管packaging tool打包机packaging打包missing part漏件wrong part错件excessive defects过多的缺陷critical defect极严重缺陷major defect主要缺陷minor defect次要缺陷not up to standard不合规格dimension/size is a little bigger尺寸偏大(小) cosmetic defect外观不良slipped screwhead/slippery screw head螺丝滑头slipped screwhead/shippery screw thread滑手speckle斑点mildewed、moldy、mouldy发霉rust生锈deformation变形burr(金属)flash(塑件)毛边poor staking铆合不良excesssive gap间隙过大grease/oil stains油污inclusion杂质painting peel off脏污 shrinking/shrinkage缩水 mixed color杂色scratch划伤 poor processing 制程不良poor incoming part事件不良fold of pakaging belt打包带折皱painting make-up补漆discoloration羿色water spots水渍polishing/surface processing表面处理exposed metal/bare metal金属裸露 garbage container灰箕cost成本engineering工程die repair模修enterprise plan、enterprise expansionprojects企划QC品管die worker模工production, to produce生产equipment设备 to start a press开机stop/switch off a press关机classification整理regulation整顿cleanness清扫conservation清洁culture教养qualified products, up-to-grade products良品defective products, not up-to-grade products不良品waste废料board看板feeder送料机sliding rack滑料架defective product box不良品箱die change 换模to fix a die装模to take apart a die拆模to repair a die修模packing material包材basket蝴蝶竺plastic basket胶筐isolating plate baffle plate; barricade隔板 carton box纸箱to pull and stretch拉深to put material in place, to cut material, to input落料to impose lines压线to compress, compressing压缩character die字模to feed, feeding送料transportation运输(be)qualfied, up to grade合格not up to grade, not qualified不合格material change, stock change材料变更feature change 特性变更manufacture management制造管理abnormal handling异常处理production unit生产单位lack of painting烤漆不到位safety安全quality品质evaluation评估prepare for, make preparations for 准备parameters参数vaccum cleaner吸尘器rag 抹布lots of production生产批量steel plate钢板roll material卷料manufacture procedure制程operation procedure作业流程to revise, modify修订to switch over to, switch、to throw、over switching over切换engineering, project difficulty 工程瓶颈stage die工程模automation自动化to stake, staking, reviting铆合add lubricating oil加润滑油shut die架模shut height of a die架模高度analog-mode device类模器die lifter举模器argon welding氩焊vocabulary for stampingiudustrial alcohol工业酒精alcohol container沾湿台head of screwdriver起子头sweeper扫把mop拖把pneumatic 气动的,空气的,pneumatic control 气动控制electromechanical 机电的governor 操纵杆,控制器electronic governor 电子调速器screw machine 车丝机relay 继电器timer定时器counter 计数器inherent固有的,本质的,inherent problem本质问题versatile通用,多用途的filter out过滤ladder diagram梯形图symbology符号体系contact dot接点,触点instantaneously瞬时地magnet-opened contact switch 电磁触点开关architecture构造,结构,组织implementation工具,仪器,实现thumbwheel switch指轮(微调)开关breadboard实验电路板Hardwired relay panel分立(硬连线)延时,控制面板relay module继电模块capability性能,耐受力category分类single throw单掷开关double throw switch双掷开关double-pole双极(刀开关)double-pole single throw双刀单掷开关selector switch选择开关push-button switch按钮开关proximity switch接近开关level switch (信号)液位开关thumbwheel拨轮debug调试be population for……application在……应用很广泛electromechanical control机电控制exce pt that ……除……之外be available可利用的wiring out布线图milling cutter铣刀profile轮廓,外形,断面machine tool机床perforated tape穿孔带mature成熟hard-wire硬线连接punched tape冲孔带magnetic tape磁带lathe车床turning machine车削中心punch冲床significant显著encoder编码器resolve分解,决定utilize利用magnetic磁的photoelectric光电的binary code二进制码execution cycle执行循环electronic pulse脉冲spindle主轴,转轴lead screw丝杠,螺杆turret转台,转塔刀架servomotor伺服电机machining center加工中心electric discharge machine (EDM) 电火花机床grinder磨床testing and inspection equipment测试和检测设备conventional machining常规加工recommendation for…… 关于……推荐值scrap rate废品率incorporate插(引,加,编)入quality assurance质量保证spot check点检,抽查set up安装set up method安装方法set up time按照时间assembly装配,组装件notation符号,符号表示法binary二进制accomplish完成,实现sensing传感graduate刻度backlash后座力adjacent毗连的radius半径,范围intersection交叉,交集slide刀架,滑板,滑移fluid servomotor液压伺服器open-loop开环close-loop闭环direct current (DC) 直流电alternative current (AC)交流电gear mechanism齿轮机构pneumatic motor气动马达(气泵)processed with继续(更新)discrepancy偏(误)差,不同speed discrepancy转速差transducer传感器,转换器magazine链式刀库,杂志magazine feed自动传输带(送料带)magazine tool刀库magazine attachment机床送料装置retrieve检索,查询retrieval data检索数据retrieval program检索程序。
机械类数控车床外文翻译外文文献英文文献数控
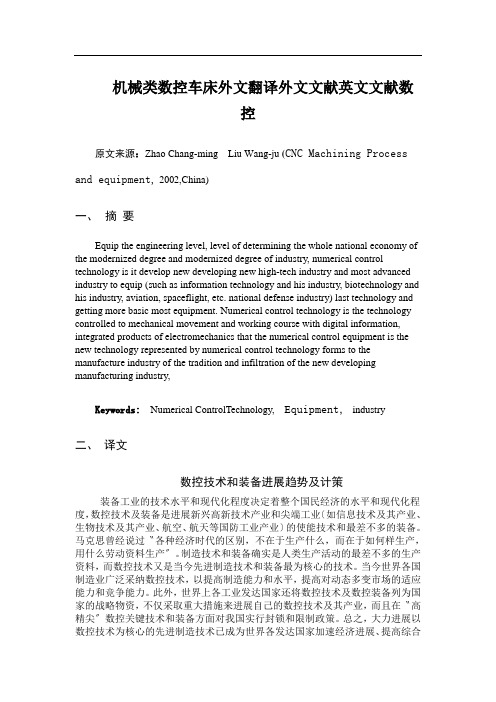
机械类数控车床外文翻译外文文献英文文献数控原文来源:Zhao Chang-ming Liu Wang-ju (CNC Machining Process and equipment, 2002,China)一、摘要Equip the engineering level, level of determining the whole national economy of the modernized degree and modernized degree of industry, numerical control technology is it develop new developing new high-tech industry and most advanced industry to equip (such as information technology and his industry, biotechnology and his industry, aviation, spaceflight, etc. national defense industry) last technology and getting more basic most equipment. Numerical control technology is the technology controlled to mechanical movement and working course with digital information, integrated products of electromechanics that the numerical control equipment is the new technology represented by numerical control technology forms to the manufacture industry of the tradition and infiltration of the new developing manufacturing industry,Keywords:Numerical ControlTechnology, E quipment,industry二、译文数控技术和装备进展趋势及计策装备工业的技术水平和现代化程度决定着整个国民经济的水平和现代化程度,数控技术及装备是进展新兴高新技术产业和尖端工业〔如信息技术及其产业、生物技术及其产业、航空、航天等国防工业产业〕的使能技术和最差不多的装备。
自动换刀与刀库--外文翻译(1)

刀库为数控卧式加工中心带盘式自动换刀装置的设计MUSTAFA ILHAN GOKLERt~ and MURAT BJLGJN KO~t(1996年4月12日)摘要-自动换刀装置(ATC)均是在数控机床设备交换中的刀具主轴与刀具在刀库。
在本文中,设计的ATC的电脑数控卧式加工中心,实现了数控机床制造商。
经过几个检查的替代品,它决定实施圆盘式ATC。
一本刀库的设计与24与刀具最大刀具直径为150毫米,最大刀具重量8公斤力。
ATC设计可以改变在4秒内,并在6秒内距离最远刀具最接近的刀具。
©1997 EL〜VIER科技有限公司保留所有战斗1。
简介任何机床制造商必须支付任何特定的数控专利机床,或设计自己的系统,以生产数控机床。
买一个新技术是一种昂贵的替代方案,并且一般不进行任何所购买的系统的修改和发展。
机床制造商不销售自行开发的新技术,他们一般都愿意出售他们的被遗弃的技术。
因此,一个特定的数控机床制造商已经开始研究和开发研究的一个新的数控卧式加工中心的设计和生产。
它需要设计一个新的空管系统,这个特殊的机床。
航管可以被定义为一个装置,可以选择和改变从刀具的刀具存储刀库根据由机器控制单元给出的命令。
ATC 具有相当不同的工作原理的不同类型的已被用于在水平不同的机床制造商生产的加工中心[1-17]。
一个刀具“存储”刀库一般是链型或光盘(旋转木马)类型。
然而,时下,还有一些其他类型的刀库,如球形,磁带等[17]。
根据光盘的功能,可以分为圆盘型刀库。
(1)在“一换臂”型刀库光盘,通过一个刀具改变从刀库和交流刀具,与一个在手臂主轴。
因此,该光盘具有索引的功能和存储的刀具[1-5]。
这种类型的一些例子示于图中。
升(一)[1],图升(二)[1]和图升(三)[5]。
(2)“光盘不换臂”型刀库就像换刀臂。
该刀具改变光盘本身的[2,6- 8]。
这种类型的一个例子示于图。
2[1]。
如该图所示,两个盘刀库和两个主轴安装在炮塔存在于这个应用程序。
数控加工工艺 外文文献

英文原文CNC Machining ProcessFirst, our country's history of the development of numerical control system1. Our country since 1958, by a group of research institutes, colleges and universities and a few started to CNC Machine Tool Plant of the research and development system. At that time, due to the low level of domestic electronic components, such as the department of economic constraints, lack of a larger development.2. In the reform and opening up, China's numerical control technology gradually achieve substantial development. After "65" (81 ---- 85 years) the introduction of foreign technology, "75" (86 ------ 90 years) of the digestion and absorption and the "Eighth Five-Year Plan" (91 ~ 1 -95 years) National Organization of scientific and technological, that makes our country's CNC technology has a qualitative leap in acceptance at that time, through research and identification of country products including Beijing Everest's Chinese I, central China's central NC I and a few high-end Shenyang National Engineering Research Center for Control of Blue-I, as well as other through the "National Quality Supervision and Test Center machine" test NC system of qualified domestic companies such as Nanjing, four products.3. China's CNC machine tool manufacturing industry in the 80's had the stage of rapid development, many machine tool plant products from traditional products to the NC transition. But, generally speaking, the technological level is not high, the quality of the poor, so in the early 90's facing the country's economy from a planned economy to a market economy and adjust the transfer went through the most difficult years of the Depression period, the production capacity at that time down to 50 %, more than four month inventory. From 1995, "Ninth Five-Year Plan" to expand domestic demand from the country after the machine tool market to start, so as to reinforce the approval of imports of CNC equipment, investment focused on support for key numerical control system, equipment, technologies of CNC equipment has played a significant role, especially in 1999, the country's defense industry to civilian industry and the key to putting in a lot of technical department funds, to enable CNCequipment manufacturer market thriving. Three, CNC Technology and Equipment of cars cut CNC Lathe Machining Lathe technology and processing technology similar to, but because of CNC lathe is a fixture, for automatic processing of all finish turning process, which should pay attention to the following aspects.1. A reasonable selection cutting for the high-efficiency metal-cutting processing, the processed materials, cutting tools, cutting conditions is the three major elements. These determine the processing time, tool life and processing quality. Cost-effective processing methods must be a reasonable choice of the cutting conditions. Three elements of cutting conditions: cutting speed, feed rate and cutting depth of the damage directly caused by the tool. With the increase in cutting speed, tool tip temperature will rise; will have mechanical, chemical, thermal wear and tear. 20% increase in cutting speed; tool life will reduce the 1 /2. Feed conditions and the relationship between tool wear and tear at the back of a very small area of. However, the feed rate, cutting temperature rise, wear big behind. Than the impact of cutting speed on tool small. Depth of cut on the tools did not affect the cutting speed and feed rate, but at small cutting depth of cut when cutting materials have been hardened layer, which will affect the tool life. The user is processed according to the material, hardness, cutting status, material type, feed rate, cutting depth, such as the option of using the cutting speed. The most appropriate selections of processing conditions are at the basis of these factors is selected. Have rules, stability, worn and tear is to achieve the ideal conditions for life. However, in actual operation, the selection tool life and tool wear, the size of changes in processing, surface quality, cutting noise, heat processing and so on. In determining the processing conditions required to study the actual situation. The heat-resistant alloys such as stainless steel and hard materials, the coolant can be used best to use rigid blade.2. Reasonable selection tool1) when rough, it is necessary to choose high strength, good durability tool, in order to meet the rough knife when eating large back volume, the feed requirements.2) Fine car, it is necessary to choose high precision, durability good tool to ensure that the requirements of machining accuracy.3) In order to reduce tool change time and convenience of the knife should be used machines and machine folder knife blade.3. A reasonable selection Fixture1) General selection try the work piece clamping fixture to avoid the use of a dedicated fixture;2) positioning the base parts overlap so as to reduce the positioning error.4. To determine the processing routeprocessing route is the index-controlled machining process, tool parts relative trajectory and direction of Sports.1) Should be able to ensure the machining accuracy and surface roughness requirements;2) should try to shorten the processing route, reducing travel time and air knives.5. Processing route of contact with allowanceAt present, CNC lathes have not yet achieved the universal access to conditions, the general should be put on too much rough margin, especially with forging, casting hard cushion cortex in general lathe processing. Must be such as CNC lathe, the need to pay attention to process flexibility.6. Fixture to install the main pointsat present, the hydraulic clamping chuck and hydraulic cylinder are connected by the rod of the implementation, in Figure 1. Hydraulic clamping chuck as follows: First of all, by moving on hand to unload the nut hydraulic cylinder, the discharge of SLIDE, and back-end from the spindle out, and then move the hands to unload screw chuck can be disposed of under the chuck. Four, effectively turning a reasonable Save processing time Index Turning Center's G200 integrated processing unit with a modular, high-power two-axis linkage axis function, thus further shortening the processing time. With other means of job-axis opposite to the concept of clamping, the use of the product can be integrated intelligent processing unit in place so that the work piece clamping and automatic processing. In other words, the automatic setup will not be affected by the processing of another axis, a feature that can be shortened about 10% of the processing time. In addition, the Four processing very quickly, youcan simultaneously have two processing tool. When the machine is put into use in pairs, the efficiency becomes more apparent. In other words, the conventional hard turning and setting two cars can parallel machine. Turning conventional vehicles and hardware differences between the tool and focused only in the coolant system thermostat. However, conventional processing is different: both can be used conventional processing and a tool carrier for processing Tailstock; and hardware when using a tool only. In both types of machine tools can be carried out on the hard dry processing, only the manufacturer's technology program designed to balance the need to beat time, and Index of the module structure of machine tools to provide them with greater flexibility. To improve the productivity of high-precision with the continuous improvement of production efficiency, the user also made for a very high accuracy requirements. Turning Center G200 used for processing, the cold start up to four parts processing required to achieve tolerances of 卤6mm. Processing process, the accuracy is usually maintained at 2mm. Index so made available to the company's clients are high-precision, high efficiency, the integrity of the program, and programs to provide such high precision, requiring careful choice of spindle, bearings and other features. G200 Turning Center Landshut, Germany, BMW car factory in the application of the company achieved good results. The plant is not only the production of engines, but also by the production of cast light metal parts, plastic decorative items inside the vehicle and steering axis. Consider the quality of supervisory staff, and its very precise machining accuracy: tolerance bands for 卤15mm, for bearing tolerance 卤6.5mm. In addition, the processing of the universal joints of the Index companies use automatic intelligent processing unit. The first two parts are used for turning centers before playing pre-processing, post-processing line measurement, and then sent through the conveyor belt for hobbling, cleaning and quenching treatment. The last process using the second processing system Index. G200 Turning Center by two steering knuckle on the car bearing hard. In the machine tool to complete the online survey, then to the discharge unit. Processing unit fully integrated into the layout of the workshop, and in line with ergonomic requirements, covers an area of greatly reduced, and only two staff members to the custody ofmanufacturing cells. Friday, CNC turning and G00 in the magical effect of the skills to ensure dimensional accuracy CNC turning processing technology has been widely used in mechanical manufacturing industry, how efficient, reasonable, and completed by the quality of the work piece by the amount of processing, each engaged in the trade of engineering and technical personnel more or less have their own experience. I engaged in CNC teaching, training and processing for many years, accumulated a certain amount of experience and skills, is to CNC Equipment Factory Guangzhou GSK980T series of machine tool production, for example, introduce a few skills in CNC turning. First, the program first sentence skills G00 We now have access to textbooks and CNC turning technical books, procedures are set up the first sentence of work piece coordinate system, that is, G50 X,Z in the first sentence as a process. According to the directive, a coordinate system can be set so that the tool at a point in this coordinate system as coordinates (X, Z) (In this paper, the origin of work piece coordinate system are set at the right end of the work piece surface). Programming using this method, the knife, the knife must be moved to the established position of G50 can be set for processing, identify the location of the process is as follows.1. of a knife, the rough work piece clamping good;2. Spindle is to hand round the base right side knife flat work piece surface A;3. Z-axis fixed, the release of the tool along the X axis points to C, type G50 Z0, the point of computer memory;4. Program entry mode, type G01 W-8 F50, turning out to be one step work piece;5. X-axis fixed, the release of the tool along the Z-axis points to C, stop turning out measuring the diameter of the work piece level, the importation of G50 X, computer memory that point;6. Program entry mode, enter the G00 X伪Z尾, programming tool runs the specified procedure to the starting point, and then enter the G50 X,Z, procedures for the origin of the computer memory. The above-mentioned steps, the steps that the tool 6 at X,Z Office location is essential; otherwise, the work piece coordinate system will be modified, not the normal processing of the work piece. Processing has been theexperience of the people all know that the above position will be the tool to the cumbersome process of X,Z Department, in the event of an accident, X or Z-axis without servo, tracking error, power outages happen, etc., the system can restart, after restart system loss of G50 work piece coordinate values set by the memory, "reset back to zero run" is no longer working, will need to re-run the tool and reset to X,Z location G50. If it is production, processing, after the End of a return to the starting point for continued processing under the G50 is, in the process some errors on the work piece coordinate system may be modified. In view of the first sentence of the above procedures using G50 work piece coordinate system set up many defects, I will want to approach the work piece coordinate system fixed on the machine will process the first sentence changed to G50 X,Z after G00 X,Z, problem solved. The course of its operation only to find G50 using the above-mentioned five-step process before, that is, 1,2,3,4,5 steps to achieve, it will run the tool to a safe location, out of process, and can run automatically. Even if power outages and other unforeseen circumstances occur, restart the system, in the Edit mode to move the cursor without affecting the safe processing of the work piece processing process program segment, according to automate the processing can continue. First sentence of the above procedure to replace G50 with G00 is the substance of the work piece coordinate system fixed on the machine, no longer limited to the origin G50 X,Z process constraints, without changing the work piece coordinate system, easy operation, reliability, and received an unexpected effect. Chinese metal processing onlineSecond, control of dimensional accuracy skills1. To amend the value of a knife up to ensure dimensional accuracyFirst on the knife because of error or other causes beyond the work piece work piece error tolerance, can not meet the processing requirements, can be added by modifying the knife so that the work piece size to meet the requirement to ensure that the radial dimensions are as follows:a. absolute coordinate input methodAccording to the "big decrease, a small increase" principle, a knife up at 001 ~ 004 modified. Such as cut off on the 2nd slot at a big size work piece 0.1mm, and 002showed up knives are X3.8, may enter the X3.7, to reduce the knife on the 2nd meeting.b. the relative coordinate method as in the previous case, enter 002 knife fill U-0.1, also the same result.Similarly, the axial size of the control also and so on. Such as cylindrical with a knife on the 1st axis somewhere above processing, size, long 0.1mm, can be completed at 001 knife enter W0.1.2. Semi-finishing to ensure that the impact of the elimination of screw gap dimensional accuracyFor the majority of CNC lathe using a longer time, because of the effects of screw space and processing of the work piece dimensions are often unstable situation. At this time, we can rough after finishing a half-space to eliminate the effects of screw. 1, such as a knife with G71 cylindrical rough, you can fill in the 001 knife enter U0.3, call the G70 a fine car, parking measurements, and then fill in the 001 knife enter U-0.3, once again calling a G70 Finish . Finish a half after this time, eliminating the effects of screw clearance to ensure the stability of the dimensional accuracy.3. To ensure dimensional accuracy Programmer a. to ensure dimensional accuracy absolute programming there is an absolute and relative programming. Programming refers to the relative curve in the processing, the location of the end of the line segment to the starting point for the coordinates of the segment and to determine the origin of the coordinate system. In other words, programming is relatively often at the origin of the coordinates transform, continuous displacement is bound to result in a cumulative error, the absolute programming are in the processing of the whole process, have a relatively unified reference point, that is, coordinates of the origin, so the accumulated error over the relative Programming small. CNC turning work piece, the work piece precision radial dimension than the axial size of the general high precision, it is in the preparation of procedures, the use of the radial size of the absolute best programming, taking into account the processing and the convenience of programming, often used sizes of axial relative programming, but the essential axial size, the use of the absolute best programming.b. to ensure dimensional accuracy numerical conversionA lot of cases, the pattern on the size of the baseline and benchmark the size of the required programming inconsistent and should be first on the base pattern size coordinates converted to programming in size. Figure 2b, in addition to size of 13.06mm, the rest is marked directly by Figure 2a and size to be converted by the program size. One of,Φ29.95mm, Φ16mm and the three dimensions of 60.07mm respectively limit the size of two average size after the programming.4. Modify the program and control the size of premium knivesCNC Machining, we often encounter such a situation: the procedure to run automatically after stopping measurement and found that fail work piece size, size irregular Change. Such as a knife with 1 cylindrical work piece processing as shown in Figure 3, the post-roughing and semi-finishing parking measurements, the size of the radial axis paragraph as follows: Φ30.06mm, Φ23.03mm and Φ16.02mm. In this connection, I used a knife to amend the procedures and methods make up the remedy, as follows: a. modify the program X30 original program unchanged, X23 changed X23.03, X16 changed X16.04, As a result, are in excess of the shaft above the name of tolerance uniform size 0.06mm; b. knife to fill Knife on the 1st at 001 imported premium U-0.06. After these procedures and a two-pronged knife revised up, and then call the refined procedures, the general size of the work piece can be effectively guaranteed. CNC Turning CNC program is based on automated processing, the actual processing, and the operator only has a strong ability to use the program instructions and a wealth of practical skills in order to produce high-quality processing, processing high-quality work piece.Six, CNC machine tool troubleshooting methods and their attention to matters Missions usually take part in because of repair, some repair experience, combined with the relevant theories are described in the following list, to initiate. First, troubleshooting methods(1) initialization reset Law: Under normal circumstances, because of instantaneous alarm system failure can be hardware reset or system power switch in order to remove the fault, if the system is down because of the storage area, plug thecircuit board or battery less pressure lead to confusion, it must be clear to initialize the system, removing the former should pay attention to make copies of recorded data, if initialization can not be ruled out after the failure remains, were carried out in hardware diagnosis.(2) Parameters to change, actual procedures: system parameters are determined based on system functions, parameter settings may cause system errors or failures of a functional null and void. Sometimes, because of procedural errors can be caused by user downtime, this system can be used to block search function to check and correct all errors, in order to ensure its normal operation.(3) Regulation, the best method of adjustment: adjustment is one of the simplest ways. By adjusting the potentiometer to amend system failures. Repair such as in a factory, the system displays chaotic scene, with normal post-conditioning. Such as in a factory, the spindle brake at start-up and skidding when belt because of its large spindle load torque, and drives set the ramp-up time is too small, the normal post-conditioning. Optimize the system to adjust servo drive system with mechanical drag system the best way to match the General regulation, the approach is very simple, with a multi-line recorder or dual trace storage oscilloscope, respectively, observe instructions and the speed of feedback or response to the relationship between current feedback. By adjusting the ratio of the speed regulator factors and integration time to achieve servo system so that there are high dynamic response characteristics, but not the best job status oscillation. NOT at the scene of the oscilloscope or recorder circumstances, based on experience, that is, adjust so that the electrical start-up, and then slowly adjust to the reverse, until you can eliminate the shock.(4) spare parts to replace the Law: The best diagnosis of spare parts to replace bad circuit board, and start to do the initialization, so that the normal operation of machine tools quickly, and then repair or rework bad board, which is currently the most commonly used anti - approach it.(5) To improve the quality of the power law: the use of the existing power supply, to improve the power supply fluctuations. For high-frequency interference filteringcapacitor can be used by these preventive measures to reduce the power supply board failure.(6) Maintenance of information-tracking: some large manufacturing company based on actual work because of design defects caused by accidental failure, continuously modify and improve the system software or hardware. These changes to the form of constant repair information available to maintenance personnel. Used as the basis for troubleshooting can be completely right troubleshooting.Second, the repair should pay attention to matters(1) removed from a whole block on the circuit board, the Record should be noted that the relative position should be to connect the cable number, for fixed installation of the circuit board, it should be removed before and after the press-fit parts and screws for the record. Demolition under the pressure parts and screws should be placed on a dedicated box, so as to avoid loss, the assembly, the box should be all things to use, or incomplete assembly.(2) Electric iron should be placed on the front easily, away from the circuit board repair. Jerdonii Dressing should be appropriate in order to adapt to the welding circuit and to avoid bumps when welding other components.(3) Measuring the resistance between lines should be off the power, measured resistance should be measured the exchange of red and black table pen twice a year toa large value for the reference value.(4) Circuit board has solder brush most films, it should be measured to find the corresponding point of the solder joint as a test, not to eradicate the solder film, there is some insulation board all the brush layer, only in the spot with a blade scratch Department insulating layer.(5) Should not be arbitrarily cut off the printed circuit. Some maintenance personnel must have experience in repair of household appliances, used to check the line, but the numerical control equipment on the circuit boards are double-sided or multi-hole metal plate of plate, printing and dense fine-line, once cut off the hard welding, and easy to cut off tangent when the adjacent line, again some point, a cut off at one line, and should not make it and line out, need to do to cut off a few lines.(6) Should not be removed components. Some maintenance personnel to determine fault components in the absence of circumstances that is the seat of your pants a component breaks down, removed immediately, so that a higher rate of miscarriage of justice, human element removed have a higher failure rate.(7) Should be used to demolish suction devices and suction devices tin rope, should not have the hardware check. Long time heating pad should not be the same and repeat the demolition in order to avoid pad damage.(8) Replacement of the device, the pin should be the appropriate treatment, welding should not be used in welding acidic oil.(9) Record on the circuit switch, the jumper position, it should not be changed. Control for more than two inspections, or swap components on-board when the attention of the components of the tag in order to avoid confusion, which can not work well plate.中文译文数控加工工艺一,我国数控系统的发展史1.我国从1958年起,由一批科研院所,高等学校和少数机床厂起步进行数控系统的研制和开发。
- 1、下载文档前请自行甄别文档内容的完整性,平台不提供额外的编辑、内容补充、找答案等附加服务。
- 2、"仅部分预览"的文档,不可在线预览部分如存在完整性等问题,可反馈申请退款(可完整预览的文档不适用该条件!)。
- 3、如文档侵犯您的权益,请联系客服反馈,我们会尽快为您处理(人工客服工作时间:9:00-18:30)。
数控车床刀库设计参考文献英文DESIGN OF AN AUTOMATIC TOOL CHANGER WITH DISCMAGAZINE FOR A CNC HORIZONTAL MACHININGCENTERAbstract--Automatic tool changers (ATCs) are devices used in CNC machine tools to exchange the tool in the spindle with the tool in the magazine. In this paper, the design of the ATC of a CNC horizontal machining center which was realized for a CNC machine tool manufacturer is introduced. After examination of several alternatives, it was decided to implement the disc-type ATC. A magazine was designed with 24 tools with a maximum tool diameter of 150 mm and a maximum tool weight of 8 kgf. The designed ATC can change the closest tool within 4 s and thetool farthest away within 6 s. ? 1997 El~vier Science Ltd. All fights reserved 1. INTRODUCTIONAny machine tool manufacturer must either pay for the patent of any particular CNC machine tool, or design its own system to manufacture CNC machine tools. Buying a new technology is an expensive alternative, and it is not generally allowed to make any modifications and developments on the purchased system. The machine tool manufacturers refrain from selling new technologies developed by themselves, and they are generally willing to sell their abandoned technologies.Therefore, a particular CNC machine tool manufacturer has started research and development studies for the design and production of a newCNC horizontal machining center. It was required to design a new systemof ATC for this particular machine tool.An ATC can be defined as a device which can select and change tools from a tool storage magazine according to the commands given by the machine control unit.Various types of ATC with quite different working principles havebeen used in horizontal machining centers produced by the different machine tool manufacturers [1-17]. A tool storage magazine is generally either a chain type or a disc (carousel) type. However, nowadays, there are some other types of magazines such as spherical, cassette, etc. [17].Disc-type magazines may be categorized according to the functions of the discs.(1) In a "disc with a changer arm"-type magazine, the tools are changed by means of an arm which takes the tool from the magazine and exchanges it with the one in the spindle. Therefore, the disc has the functions of indexing and storing the tools only [1-5]. Some examples of this type are shown in Fig. l(a) [1], Fig. l(b) [1] and Fig. l(c) [5].(2) A "disc without a changer arm"-type magazine acts like a tool changer arm. The tools are changed by the disc itself [2, 6--8]. An example of this type is shown in Fig. 2 [1 ]. As shown in the figure,two disc magazines and two spindles mounted on a turret exist in this application.In an ATC with chain-type magazines [9-16], the tool is changed by a changer arm. Chain-type magazines may be categorized according to theorientation of the tools in the magazine with respect to the spindle axis as follows.(1) The axes of the tools on the magazine are perpendicular to the spindle axis and the magazine is on either the right- or left-hand side of the column. Therefore, in order to change the direction of the tools, an arm takes the tool and makes a rotation about a vertical axis to bring the new tool to the position parallel to the spindle axis as shown in Fig. 3(a) [13]. In another version of this type, the tool pots, where the tools are located, are rotated about their own axis to become parallel to the spindle axis, as shown in Fig. 3(b) [12]. The changer arm exchanges the tools between the tool pot and the spindle axis.(2) The axes of tools on the chain magazine are in a plane parallel to the spindle axis. As shown in Fig. 3(c) [12], there is only one position of the tool at which the cutting tool becomes parallel to the spindle axis, and the tool is changed at that position. There is an arm which exchanges the tools between the spindle and the magazine.(3) The axes of tools on the magazine are parallel to the spindle axis. The arm which is in between the spindle and the magazine takes the tool and does a linear motion to approach the spindle and exchange the tools as shown in Fig. 3(d) [16].In Table l, different ATCs and their minimum "tool to toolchange times" (T/T) are given based on the trade literature [2-5, 7-14]. In Table 1, "D+A", "D" and "C+A" designate "disc-type magazine with changer arm", "disc-type magazine without changer arm", and "chain-type magazine with changer arm", respectively. In disc magazines, as the number of tools increases, the diameter of the disc increases, which is an undesirable situation from the space point of view. However, in a chain type, the number of tools is approximately 1.5 times that of the tools in the disc type in the same space [18]. The ATC of the chain typecan store many tools in a very small space. However, the chain-type magazines are expensive compared with the disc-type magazines.2. DESIGN OF ATCIn the stage of clarifying the design specifications for a CNC machine tool, supply and demand in the particular market, potential customers' preferences, specifications of competitors' products which can be obtained from the related trade literature, price of CNC machine tools, etc. should be considered. In accordance with the desired features of the CNC machine tool, the design specifications of ATC are determined.By considering the basic design criteria as simplicity, relatively low cost, relative ease of manufacture, assembly, disassembly, maintenance, and availability of spare parts, a "disc magazine without changer arm"-type ATC was considered to be designed for the particular CNC horizontal machining center [19].Table I. Tool mass and tool change time data for automatic tool changers of various machine tools available in the marketAs shown in Fig. 4, the tool-changing cycle of the designed ATC includes the following basic steps.Step 1. The spindle approaches the magazine to insert the old tool into the tool pocket (Fig. 4(a)).Step 2. After the drawbar releases the old tool, the magazine goes forward along the A-A direction (Fig. 4(b)).Step 3. To bring the new tool into the tool changing position as soon as possible, the magazine is rotated in a clockwise or counterclockwise direction about its axis, depending on the relative position of the tool on the magazine (Fig. 4(c)).Step 4. The magazine is retracted back to insert the new tool into the spindle (Fig. 4(c)).Step 5. When the control unit takes the message from the spindle that the drawbar has been operated to draw the new tool safely, the spindle is let go to start the new machining cycle (Fig. 4(d)).After the decision concerning the type of ATC and the workingprinciple to be used, the specifications for the "disc magazine without changer arm"-type ATC were determined as follows [20]. 1. The number of tools stored (i.e. number of tool stations) in the magazine is 24.2. The maximum tool diameter is 100 mm when the adjacent tool pockets are full.3. The maximum tool diameter is 150 mm when the adjacent tool pockets are empty.4. The maximum weight of the tool including that of the tool holder is 8 kgf.5. The tool holder type is BT40 [21].6. Tool changing times are 4 s and 6 s for the closest and farthest tool on the magazine, respectively.In the following subsections, basic components of the particular ATC are presented.2.1. Disc magazineThe minimum diameter of the disc-type magazine is calculated by considering the specified number of tools to be stored and the maximum tool diameter. A distance between successive tools to be stored in the magazine should be left. The diameter of the disc magazine was calculated as 812 mm by leaving 6 mm between successive tools [19]. After the diameter of the disc magazine has been calculated, the shape of the disc magazine is determined. Low inertia has primary importancebecause of the frequency of acceleration and deceleration of the disc magazine. This can beobtained by using a light material. Aluminium is selected as the material for the disc magazine. A thin walled disc geometry with appropriate webbing which ensures necessary stiffness should be considered.The structure of the disc magazine was made as simple as possible to reduce the cost of the pattern to be used for casting the magazine. A simple sketch is shown in Fig. 5 [19].2.2. Sliding bodyIn any of the ATC systems, there have to be extraction andretraction motions to take the tool holder out of the spindle or to insert a new one. In the "disc without changer arm"-type ATC, the magazine should make a back and forth motion. This necessitates asliding body. These motions can easily be achieved by either a hydraulic or a pneumatic piston. In fact, there are some other methods of having a linear motion such as using a ball screw toconvert the rotary motion into linear motion. However, this methodis extremely expensive when only a simple repetitive motion cycle is required.As seen in Fig. 6, the sliding body was designed hollow to reduce the weight [19]. At the rear, there is a space for the encoder and the coupling inside the body. A pneumatic piston was selected and implemented to push and pull the sliding body. The very back of the body was closed with a lid to which the pneumatic piston was assembled. The slides of the sliding body were designed as square edge but not of dovetail type. The reason for using the square edge type of slide is the ease of manufacturing, price and limited space advantages.2.3. Shock absorbersFor each tool-change cycle, the magazine performsforward-backward motion by the sliding body, which takes up most of the cycle time. To reduce this time. higher traverse speeds are preferred. However, a problem arises concerning the deceleration, where an extremely high level of kinetic energy must be absorbed over a very short distance to stop the system without causing excessive shock loads or vibration. Shock absorbers can be used for this purpose.In the design, a pneumatic piston was used. Owing to the compressibility of the air, pneumatic pistons have sharply rising force characteristics towards the end of the stroke during the cushioning operation. Most of the energy is absorbed near the end of the stroke [22]. Therefore, shock absorbers are required. The pressure generated in front of the particular shock absorber piston remains constant throughout the entire stroke, as the velocity is reduced to zero owing to the specific spacing of the orifices. Consequently, the resisting force remains constant and uniform, and therefore linear deceleration is achieved [22].2.4. Clamping of the toolsThe tools on the disc magazine are kept in the pockets with clamps. The tool may be held between clamping jaws. The clamp is designed in such a way that a tool with a maximum weight can be safely held. Since the disc magazine rotates about its axis, the centrifugal force adds up to the weight of the tool. This is consideredduring the design of the clamping system. The tool pocket and clamping jaws are designed according to the tool-holder type specified. Clamping jaws should have appropriate mating surfaces which fit into the specified tool holder.The tools are kept in the pockets by a combination of leaf andhelical springs which have been designed to hold a tool with a maximum weight of 8 kgf safely [19]. The jaws have tapered surfaces which fit the tool holder of the BT40 [21].2.5. A shield to protect the tool holders from chipsIn design of an ATC, some protective measures are necessary. Ifany chip sticks on to the tapered surface of the tool holder beforeitis inserted into the spindle shaft, it will not be accurately seated in the spindle shaft and will cause run-out, inaccuracy and repeat-ability problems, and the chip may damage the spindle taper. To prevent these, the tool holders should be protected from the chips by a shield which opens just before the spindle reaches the tool change position (Fig. 7) [19]. The shield is kept closed during the machining processes.2.6. Motor and speed reductionThe rotation of the disc can be provided by using a motor and speed reducer combination. After the decision has been made for the type ofmotor, the power and torque requirements are calculated to select an appropriate motor.By considering the positional accuracy and the repeatability, an AC brushless servo motor was used for the rotation of the disc magazine [19]. The motor was selected which can give 4.5 Nm and 0.94 kW rated torque and rated power values, respectively, for At=60 K and 5.5 Nm and1.2 kW for At=-100 K. The motor has a rotational speed of 2000 rpm [23].2.7. Speed reductionSpeed reduction between the magazine and the motor may be provided through worm gear, planetary gear train, harmonic drive, etc. Abacklash-free reduction is necessary for accurate positioning of the tools relative to the spindle bore center while changing the tools. A timing belt is another method which can ensure a zero backlash power transmission. However, high reduction is very difficult to obtain with timing belts in a very small area. Very high reduction ratios canbe obtained with worm-gear sets in a very small area. However, wormgears have back lash problems. Moreover, for high reductions, the efficiency of the system decreases abruptly. If the reduction is done with a very low efficiency worm gear, the required capacity of the motor size gets bigger, which in turn increases the cost of the motor and its control system. In zero backlash worm gears, the worms are of split type and their tooth profiles are special [24].In planetary-gear systems of low prices, the back lash eliminationis obtained by just decreasing the center distance between the gearsuntil a minimum clearance condition is reached without too much noise or heating up. This normally causes high starting torque because of interference, and much lower running efficiency than the same with a normal backlash condition. There are only a few companies in the world which manufacture zero backlash planetary gear trains [25].The harmonic drive is another way of having a zero backlash reduction. The advantages of harmonic drive can be stated as follows[26].(1) The positional accuracy is quite good. The harmonic drivegearing's design ensures that approximately 10% of the total teeth are engaged at any point in time, which minimizes the effect of tooth-to-tooth error.(2) Because of the simple structure of the harmonic drive, it isvery easy to incorporate into a housing which is easy to manufacture, since the machining required is simple in-line boring and turning operations.(3) Since the harmonic drive has a very compact structure and very light weight, the assembly and disassembly are very easy. (4) It is cheaper than any other zero backlash gearing. Because of the above advantages and after the necessary calculations, the harmonic drive was selected and implemented in the ATC [26]. Assuming that half rotation of the disc magazine, including the time elapsed for acceleration and deceleration of it, is completed in 2 s, the rotational speed of the magazine is calculated as 16.67 rpm. This requires a 120:1 reduction toreduce the 2000 rpm motor output to 16.67 rpm magazine rotation. The harmonic drive was selected to obtain 50:1 reduction together with a spur gear pair providing 2.4:1reduction. The output shaft of the harmonic drive is connected to a pinion with the pitch circle diameter of 125 mm which meshes to a gear with a diameter of 300 ram. The gear is bolted on to the disc magazine [19].2.8. Encoder and control switchesThe position of the magazine is very important to insert the right tool into the spindle. This can be provided by using an absolute or incremental encoder. An encoder can also be used for counting the tool stations, which is necessary to index the required tool. Encoders are very sensitive devices which are capable of giving very precise output. If the cables of the encoder are affected by some means from the environment (i.e. interference), the message that is sent to the control unit will be different from its real value. Therefore, another method of counting the tools is recommended to support the encoder as a safety precaution. A switch to count the tools can be used for this purpose. The signals sent by the switch and the encoder are compared to prevent any mistake while indexing the tools. Absolute encoders are expensive when compared to theincremental encoders. As shown in Fig. 6, the positioning of the magazine was achieved by using an incremental encoder directly assembled on the axis of the disc magazine and not on the motor as is normal withservo drive. The angular positioning backlash problem was overcome by placing an incremental encoder directly connected to the disc magazine and situated within the sliding body.The incremental encoder was selected with 3600 lines per revolution.A proximity switch was placed on the sliding body near the disc magazine as a safety precaution. The switch is actuated by 24 dogs mounted on the disc magazine. So, for each tool, there is one dog which actuates the switch, thus enabling both counting of the tool stations and providing a signal to the control unit.Several switches are also required for control purposes. Since the ATC has a rotation axis, the control unit should be capable of recognizing the reference point of the rotation. Otherwise, the control unit does not know the positions of the reference tool and the other tools. Since an incremental encoder was used, a proximity switch was placed on the sliding body to set the home position. If an absolute encoder were used, there would be no need for a home switch since the absolute encoders know at which absolute position they are.A drawbar is a drawing unit, which is used in spindles to pull the tool holder. The ATC and drawbar should work sequentially, otherwise serious problems may occur. To synchronize the operation of the drawbar, the sliding body and rotation of the magazine, two limit switches were used for the front and rear positions of the sliding body to give reliability while changing tools. Anotherproximity switch was placed within the spindle which senses whether the drawbar unit is in its clamp position or not. If the switch is not actuated, it means that either the tool holder is not clamped or it is improperly clamped.The tool pocket which will pick the tool in the spindle must be unoccupied before the approach of the spindle, otherwise a crash occurs, which causes damage to the tools, spindle and magazine. To prevent such damage, a proximity switch was used to check whether the particular tool pocket was occupied (Fig. 7) [19]. 3. IMPLEMENTATION AND TEST OF AUTOMATIC TOOLCHANGERThe particular CNC horizontal machining center wasmanufactured and assembled. Each system was tested and runseparately or as a whole of the machine tool by the CNC machine tool manufacturer. At the end of the tests, it was reported that everything within the ATC was running without any problems. The designed ATC was tested for which the T/T for the closest tool is 4 s, whereas it is 6 s when the farthest tool is of concern. The particular machine tool was used in the production line in the particular CNC machine tool manufacturer without any reported problems relating to the designed ATC system.4. CONCLUSIONIn this paper, the working principle and the design criteria of an ATC with a disc magazine without a changer arm has been presented. This type of ATC has been found to be suitable for the particular CNC machine tool manufacturer when considering the design period,the compulsion being to enter the market as quickly as possible. The minimum T/T for the designed ATC, which is 4 s, is quite reasonable when compared with those given in Table 1. Therefore, the realized ATC system has provided a competitive position for the machining center in the market.Acknowledgements—The authors wish to express theirappreciation to TAKSAN Machine Tool Industry and Trade Co., Kayseri, Turkey, for support in the design and manufacturing of the particularATC. The authors also thank METU Prof. Dr Mustafa N. Parlar Education and Research Foundation, and METUCAD/CAM/ROBOTICS Center, Ankara, Turkey, for allowing theirfacilities to be used in this study.REFERENCES[1] A.N. Kobuladze and L.M. Prupis, Automatic tool changers for machining centers with horizontal spindles, Machines and Tooling 45(5), 56 (1974).[2]Sidepalsa Trade Literature. Sidepalsa Sistemas De Paletizacion, S.A., Spain.[3] NTC Trade Literature. NTC Nippei Toyama Corporation, Japan.[4] Olivetti Trade Literature. Olivetti Controllo Numerico SpA, Italy.[5] Mandelli Trade Literature. Mandelli SpA, Piacenza, Italy. [6] Bridgeport Trade Literature. Bridgeport Machine Tools, U.K. [7] White--Sundstrand Trade Literature. White-Sundstrand, White Consolidated Machine Tool Group, IL,U.S.A.[8] Leadwell Trade Literature. Leadwell Machine Tools, Taiwan.[9] Mazak Trade Literature. Yamazaki Mazak Corporation, Japan.[10]Burkhard+Weber Trade Literature. Burkhard+Weher GmbH Werkzeugmachinenfabrik, Reutlingen, Germany.[11]Matsuura Trade Literature. Matsuura Machinery Corporation,Fukui-City, Japan.[12] Mauser-Werke Trade Literature. Mauser-Werke GmbH, Oherndorf, Germany.[131 Hitachi Seiki Trade Literature. Hitachi Seiki Co. Ltd, Japan.[14] Mechanicy Trade Literature. Mechanicy, Czechoslovakia. [I 5] Cincinati Milacron Trade Literature, Cincinati Milacron, Cincinati, OH, U.S.A.[16] Hwacheon Trade Literature. Hwacheon Machinery, Seoul, South Korea.[17] Starrfrdsmachinen Trade Literature. Starrfrllsmachinen AG, Larigidesa Rigid Ltd, Switzerland.[18] Fudow Tool Pots Trade literature. Fudow Chemical Co. Ltd, Japan.[19] M.B. Ko~, Design of automatic tool changer for CNC machines.M.Sc. thesis, Mechanical EngineeringDepartmet, METU, Ankara, Turkey 1995.[20] TAKSAN Machine Tool Industry and Trade Co., Turkey,Private communication.。