PVC管材工艺流程
pvc管生产工艺流程
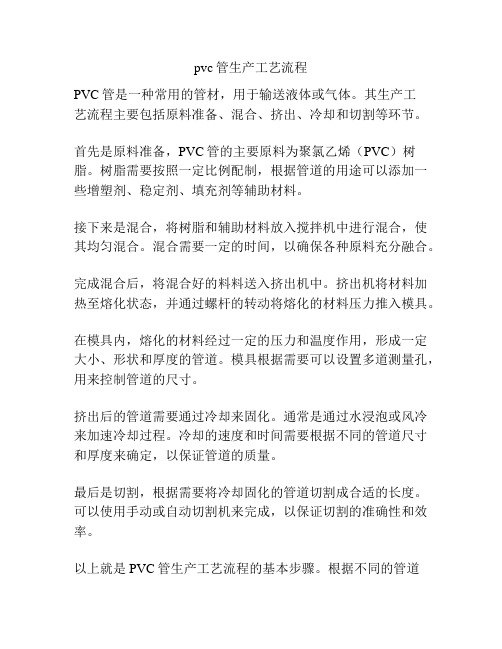
pvc管生产工艺流程
PVC管是一种常用的管材,用于输送液体或气体。
其生产工
艺流程主要包括原料准备、混合、挤出、冷却和切割等环节。
首先是原料准备,PVC管的主要原料为聚氯乙烯(PVC)树脂。
树脂需要按照一定比例配制,根据管道的用途可以添加一些增塑剂、稳定剂、填充剂等辅助材料。
接下来是混合,将树脂和辅助材料放入搅拌机中进行混合,使其均匀混合。
混合需要一定的时间,以确保各种原料充分融合。
完成混合后,将混合好的料料送入挤出机中。
挤出机将材料加热至熔化状态,并通过螺杆的转动将熔化的材料压力推入模具。
在模具内,熔化的材料经过一定的压力和温度作用,形成一定大小、形状和厚度的管道。
模具根据需要可以设置多道测量孔,用来控制管道的尺寸。
挤出后的管道需要通过冷却来固化。
通常是通过水浸泡或风冷来加速冷却过程。
冷却的速度和时间需要根据不同的管道尺寸和厚度来确定,以保证管道的质量。
最后是切割,根据需要将冷却固化的管道切割成合适的长度。
可以使用手动或自动切割机来完成,以保证切割的准确性和效率。
以上就是PVC管生产工艺流程的基本步骤。
根据不同的管道
规格和要求,可能会有些许不同,但整体流程是相似的。
通过这一流程,可以生产出质量稳定的PVC管,用于不同领域的应用。
pvc管道生产工艺流程及配方表
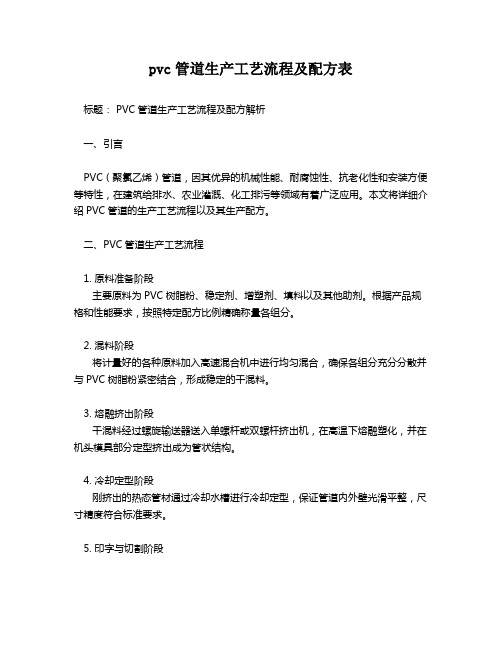
pvc管道生产工艺流程及配方表标题: PVC管道生产工艺流程及配方解析一、引言PVC(聚氯乙烯)管道,因其优异的机械性能、耐腐蚀性、抗老化性和安装方便等特性,在建筑给排水、农业灌溉、化工排污等领域有着广泛应用。
本文将详细介绍PVC管道的生产工艺流程以及其生产配方。
二、PVC管道生产工艺流程1. 原料准备阶段主要原料为PVC树脂粉、稳定剂、增塑剂、填料以及其他助剂。
根据产品规格和性能要求,按照特定配方比例精确称量各组分。
2. 混料阶段将计量好的各种原料加入高速混合机中进行均匀混合,确保各组分充分分散并与PVC树脂粉紧密结合,形成稳定的干混料。
3. 熔融挤出阶段干混料经过螺旋输送器送入单螺杆或双螺杆挤出机,在高温下熔融塑化,并在机头模具部分定型挤出成为管状结构。
4. 冷却定型阶段刚挤出的热态管材通过冷却水槽进行冷却定型,保证管道内外壁光滑平整,尺寸精度符合标准要求。
5. 印字与切割阶段定型后的管材表面可按需求印制相关标识信息,然后通过自动切割设备按设定长度进行切割。
6. 检验包装阶段对切割好的PVC管道进行严格的质量检验,包括外观质量、尺寸精度、力学性能等各项指标,合格产品进行包装入库。
三、PVC管道生产配方表以下是一个典型的PVC-U管道生产配方示例:- PVC树脂粉:100份- 稳定剂:3-5份- 增塑剂:10-20份(视管材硬度要求而定)- 钙锌复合稳定剂:1-3份- 内外润滑剂:1-2份- 填充剂(如碳酸钙):适量(以降低成本和提高刚性)- 抗冲改性剂:根据需要添加- 阻燃剂(如有防火要求时):适量请注意,以上配方仅为示例,实际生产过程中,各类助剂的种类和用量需根据具体的产品规格、性能要求以及生产环境条件等因素进行科学调整。
四、结语PVC管道的生产过程涵盖了从原料选择到成品检验的多个环节,每个环节都至关重要。
科学合理的配方设计和严谨精准的工艺控制是保证产品质量的关键,也是提升PVC管道市场竞争力的核心要素。
PVC管材生产工艺流程

PVC-U 、PP-R 管材生产工艺流程编号:QR —07—2011编制:批准:受控状态:分发号:1 总则为确保PVC-U、PP-R和PE管材生产操作规范化,保证管材产品质量,特制定本生产工艺程。
2 范围本生产工艺流程适用于以聚氯乙烯树脂(PVC)、聚丙烯树脂(PP-R )和聚乙烯树脂(P E )为主要原料,加入适当助剂,经挤出工艺成型的硬聚氯乙烯(PVC-U)给水管材、排水管材、排水芯层发泡管材、排水隔音降噪管材和建筑用绝缘电工导管管材、冷热水用聚丙烯管道系统(PP-R)管材及给水用聚乙烯(PE)管材的生产工艺流程。
3 生产工艺流程3.1 生产计划3.1.1 根据公司相关部门下达的生产计划通知书,生产部应根据生产计划通知书的要求制定相应的生产计划和作业指导书下达生产车间,有特殊要求的,按特殊要求制定生产计划和作业指导书。
3.1.2 车间主任按照生产部下达的生产计划和作业指导书通知班(组)长进行生产准备工作。
3.1.3 检查并核实班(组)长的生产准备工作是否符合生产计划和作业指导书的要求。
3.2 开机前的准备3.2.1 机器设备常规检查检查挤出机传动箱、齿轮箱是否加注润滑油,电路、气路、冷却系统、主机、牵引机、喷墨印字机、切割机、空气压缩机等空机运转是否正常,确定所有机器均属正常运转方可安装模具。
3.2.2 安装模具根据下达的生产计划,在挤出机的机头上安装相对应规格的管材挤出模具,在真空定型箱内装上相同规格的定径铜套和橡胶密封衬板,调整挤出模具壁厚均匀度,所有连接螺丝都要涂上二硫化钼锂基润滑脂并拧紧,安装模具加热圈、热电隅、温度计,接上加热电源线,准备升温。
323 升温升温前,先设置主机机筒和机头(模具)各段(区)加热温度,机筒和机头各段(区)加热温度的设置视加工产品的规格种类略有差异,PVC-U、PP-R、PE管材生产机筒和机头各段(区)加热温度的设置范围分别见表1、表2和表3。
表1 PVC-U管材加工机筒、机头各段(区)加热温度设置范围表2 PP-R管材加工机筒、机头各段(区)加热温度设置范围表3 PE管材加工机筒、机头各段(区)加热温度设置范围机筒和机头各段(区)加热温度的调整范围为±0 当各加热段(区)加热温度全部达到或超过设置温度时,应恒温90—150分钟,让各加热段(区)的真实温度接近或等于设置温度。
pvc管道生产工艺流程及配方表
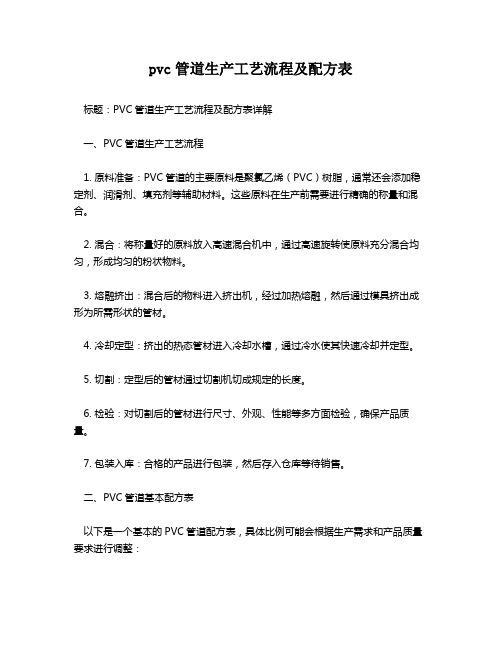
pvc管道生产工艺流程及配方表
标题:PVC管道生产工艺流程及配方表详解
一、PVC管道生产工艺流程
1. 原料准备:PVC管道的主要原料是聚氯乙烯(PVC)树脂,通常还会添加稳定剂、润滑剂、填充剂等辅助材料。
这些原料在生产前需要进行精确的称量和混合。
2. 混合:将称量好的原料放入高速混合机中,通过高速旋转使原料充分混合均匀,形成均匀的粉状物料。
3. 熔融挤出:混合后的物料进入挤出机,经过加热熔融,然后通过模具挤出成形为所需形状的管材。
4. 冷却定型:挤出的热态管材进入冷却水槽,通过冷水使其快速冷却并定型。
5. 切割:定型后的管材通过切割机切成规定的长度。
6. 检验:对切割后的管材进行尺寸、外观、性能等多方面检验,确保产品质量。
7. 包装入库:合格的产品进行包装,然后存入仓库等待销售。
二、PVC管道基本配方表
以下是一个基本的PVC管道配方表,具体比例可能会根据生产需求和产品质量要求进行调整:
- PVC树脂:100份
- 稳定剂:2-3份(如钙锌稳定剂)
- 润滑剂:0.5-1份(如硬脂酸钙)
- 填充剂:10-30份(如碳酸钙)
- 增塑剂:5-15份(如DOP)
- 抗冲击改性剂:0.5-1份(如CPE)
- 其他添加剂:如紫外线吸收剂、色粉等,根据需要适量添加。
以上配方中的“份”通常是按重量计的,具体比例需根据设备、工艺和产品要求进行优化。
请注意,PVC管道的生产涉及到复杂的化学反应和物理过程,因此在实际操作中,应由专业人员按照严格的标准和规程进行。
同时,配方的调整也需要在专业的实验室环境中进行,以保证产品的质量和稳定性。
PVC管材的生产工艺与设备操作介绍
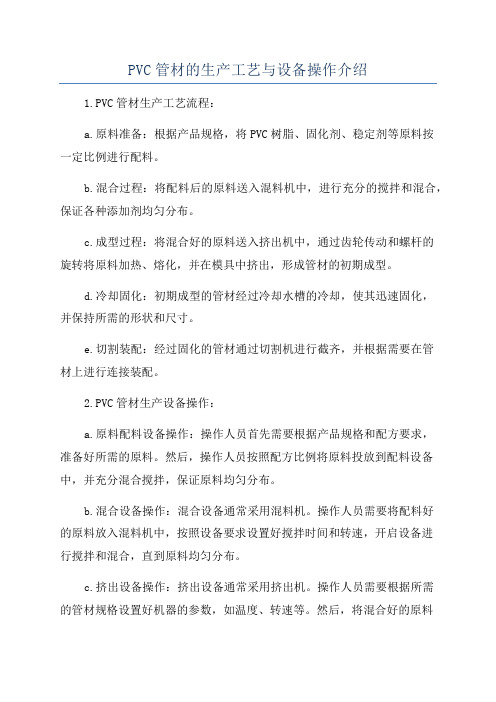
PVC管材的生产工艺与设备操作介绍1.PVC管材生产工艺流程:a.原料准备:根据产品规格,将PVC树脂、固化剂、稳定剂等原料按一定比例进行配料。
b.混合过程:将配料后的原料送入混料机中,进行充分的搅拌和混合,保证各种添加剂均匀分布。
c.成型过程:将混合好的原料送入挤出机中,通过齿轮传动和螺杆的旋转将原料加热、熔化,并在模具中挤出,形成管材的初期成型。
d.冷却固化:初期成型的管材经过冷却水槽的冷却,使其迅速固化,并保持所需的形状和尺寸。
e.切割装配:经过固化的管材通过切割机进行截齐,并根据需要在管材上进行连接装配。
2.PVC管材生产设备操作:a.原料配料设备操作:操作人员首先需要根据产品规格和配方要求,准备好所需的原料。
然后,操作人员按照配方比例将原料投放到配料设备中,并充分混合搅拌,保证原料均匀分布。
b.混合设备操作:混合设备通常采用混料机。
操作人员需要将配料好的原料放入混料机中,按照设备要求设置好搅拌时间和转速,开启设备进行搅拌和混合,直到原料均匀分布。
c.挤出设备操作:挤出设备通常采用挤出机。
操作人员需要根据所需的管材规格设置好机器的参数,如温度、转速等。
然后,将混合好的原料送入机器中,并通过齿轮传动和螺杆的旋转将原料加热、熔化,并通过模具挤出形成初期成型的管材。
d.冷却设备操作:冷却设备通常采用水槽。
操作人员需要将初期成型的管材送入水槽中,并调节水槽的温度和水流量,使管材能够迅速冷却、固化,并保持所需的形状和尺寸。
e.切割装配设备操作:切割装配设备通常采用切割机和连接装配机。
操作人员首先需要将固化好的管材送入切割机,并根据需要设置好切割长度。
然后,通过连接装配机将切割好的管材进行连接装配。
以上就是PVC管材的生产工艺与设备操作的详细介绍。
通过配料、混合、挤出、冷却固化和切割装配等环节,可以制造出符合要求的PVC管材。
这些管材在建筑、市政、电力等领域具有广泛的应用前景。
PVC管材生产工艺流程
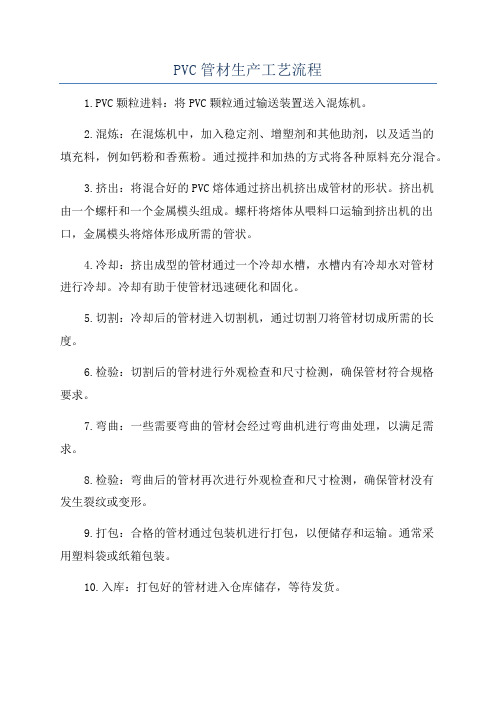
PVC管材生产工艺流程
1.PVC颗粒进料:将PVC颗粒通过输送装置送入混炼机。
2.混炼:在混炼机中,加入稳定剂、增塑剂和其他助剂,以及适当的
填充料,例如钙粉和香蕉粉。
通过搅拌和加热的方式将各种原料充分混合。
3.挤出:将混合好的PVC熔体通过挤出机挤出成管材的形状。
挤出机
由一个螺杆和一个金属模头组成。
螺杆将熔体从喂料口运输到挤出机的出口,金属模头将熔体形成所需的管状。
4.冷却:挤出成型的管材通过一个冷却水槽,水槽内有冷却水对管材
进行冷却。
冷却有助于使管材迅速硬化和固化。
5.切割:冷却后的管材进入切割机,通过切割刀将管材切成所需的长度。
6.检验:切割后的管材进行外观检查和尺寸检测,确保管材符合规格
要求。
7.弯曲:一些需要弯曲的管材会经过弯曲机进行弯曲处理,以满足需求。
8.检验:弯曲后的管材再次进行外观检查和尺寸检测,确保管材没有
发生裂纹或变形。
9.打包:合格的管材通过包装机进行打包,以便储存和运输。
通常采
用塑料袋或纸箱包装。
10.入库:打包好的管材进入仓库储存,等待发货。
以上是一种典型的PVC管材生产工艺流程,具体的工艺流程可能因厂家和管材产品的不同而有所变化。
但总体上,通过原料混炼、挤出成型、冷却、切割、检验、弯曲、检验、打包和入库等工艺步骤,可以得到高质量的PVC管材产品。
PVC管材工艺流程
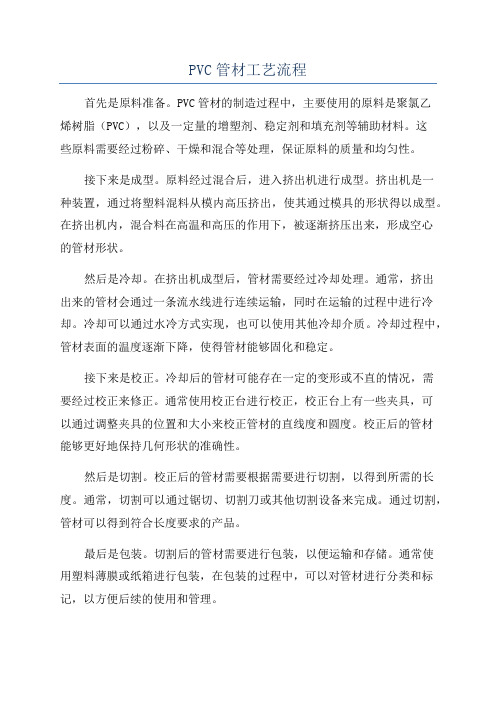
PVC管材工艺流程首先是原料准备。
PVC管材的制造过程中,主要使用的原料是聚氯乙烯树脂(PVC),以及一定量的增塑剂、稳定剂和填充剂等辅助材料。
这些原料需要经过粉碎、干燥和混合等处理,保证原料的质量和均匀性。
接下来是成型。
原料经过混合后,进入挤出机进行成型。
挤出机是一种装置,通过将塑料混料从模内高压挤出,使其通过模具的形状得以成型。
在挤出机内,混合料在高温和高压的作用下,被逐渐挤压出来,形成空心的管材形状。
然后是冷却。
在挤出机成型后,管材需要经过冷却处理。
通常,挤出出来的管材会通过一条流水线进行连续运输,同时在运输的过程中进行冷却。
冷却可以通过水冷方式实现,也可以使用其他冷却介质。
冷却过程中,管材表面的温度逐渐下降,使得管材能够固化和稳定。
接下来是校正。
冷却后的管材可能存在一定的变形或不直的情况,需要经过校正来修正。
通常使用校正台进行校正,校正台上有一些夹具,可以通过调整夹具的位置和大小来校正管材的直线度和圆度。
校正后的管材能够更好地保持几何形状的准确性。
然后是切割。
校正后的管材需要根据需要进行切割,以得到所需的长度。
通常,切割可以通过锯切、切割刀或其他切割设备来完成。
通过切割,管材可以得到符合长度要求的产品。
最后是包装。
切割后的管材需要进行包装,以便运输和存储。
通常使用塑料薄膜或纸箱进行包装,在包装的过程中,可以对管材进行分类和标记,以方便后续的使用和管理。
综上所述,PVC管材的制造工艺流程主要包括原料准备、成型、冷却、校正、切割和包装等环节。
通过这些工艺流程的处理,可以生产出质量稳定、几何形状准确的PVC管材产品,满足不同领域的使用需求。
pvc管材生产工艺流程
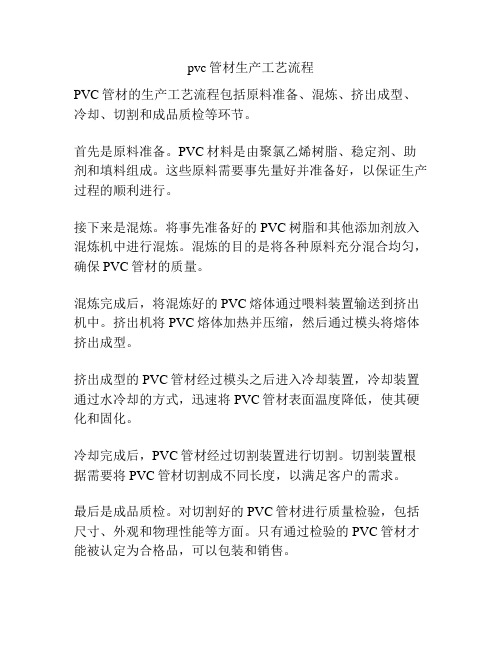
pvc管材生产工艺流程
PVC管材的生产工艺流程包括原料准备、混炼、挤出成型、冷却、切割和成品质检等环节。
首先是原料准备。
PVC材料是由聚氯乙烯树脂、稳定剂、助剂和填料组成。
这些原料需要事先量好并准备好,以保证生产过程的顺利进行。
接下来是混炼。
将事先准备好的PVC树脂和其他添加剂放入混炼机中进行混炼。
混炼的目的是将各种原料充分混合均匀,确保PVC管材的质量。
混炼完成后,将混炼好的PVC熔体通过喂料装置输送到挤出机中。
挤出机将PVC熔体加热并压缩,然后通过模头将熔体挤出成型。
挤出成型的PVC管材经过模头之后进入冷却装置,冷却装置通过水冷却的方式,迅速将PVC管材表面温度降低,使其硬化和固化。
冷却完成后,PVC管材经过切割装置进行切割。
切割装置根据需要将PVC管材切割成不同长度,以满足客户的需求。
最后是成品质检。
对切割好的PVC管材进行质量检验,包括尺寸、外观和物理性能等方面。
只有通过检验的PVC管材才能被认定为合格品,可以包装和销售。
总结起来,PVC管材的生产工艺流程包括原料准备、混炼、挤出成型、冷却、切割和成品质检。
每个环节都需要严格控制和监测,以确保PVC管材的质量和生产效率。
这样才能生产出符合标准的优质PVC管材产品。
- 1、下载文档前请自行甄别文档内容的完整性,平台不提供额外的编辑、内容补充、找答案等附加服务。
- 2、"仅部分预览"的文档,不可在线预览部分如存在完整性等问题,可反馈申请退款(可完整预览的文档不适用该条件!)。
- 3、如文档侵犯您的权益,请联系客服反馈,我们会尽快为您处理(人工客服工作时间:9:00-18:30)。
聚氯乙烯(PVC)管材生产工艺流程
聚氯乙烯(PVC)管材生产工艺流程见下图:PVC 树脂
助剂
一、混合工艺
在高速混合时,助剂渗入PVC树脂的空隙,使助剂在树脂中均匀分散,考虑到温度在100℃以上有利于物料中水蒸气蒸出,所以一般热混机的温度设在100—120℃。
为了让助剂充分地与PVC微粒接触,减少填充剂对助剂的吸附作用,应该在加入PVC树脂后即启动热混机,再按如下顺序投料:稳定剂、各种加工助剂、色料、填充剂。
在实际生产中,大都是将原辅料全都投入后再启动热混机。
热混机放出的混合料温度很高,需立即进行冷却,若散热不及时会引起物料分解和助剂挥发。
冷混一般控制在料温40℃左右时出料。
二、挤出成型工艺
挤出机螺杆分3个区段:加料段(送料段)、熔化段(压缩段)、计量段(均化段),这三段相应的对物料组成了3个功能区:固体输送区、物料塑化区、熔体输送区。
固体输送区的料筒温度一般控制在100—1400C 。
若加料温度过低,使固体输送区延长,减少了塑化区和熔体输送区的长度,会引起塑化不良,影响产品质量。
物料塑化区的温度控制在170—1900C。
控制该段的真空度是一个
重要的工艺指标,若真空度较低,会影响排气效果,导致管材中存有气泡,严重降低了管材的力学性能。
为了使物料内部的气体容易逸出,应控制物料在该段塑化程度不能过高,同时还要经常清理排气管路以免阻塞。
料筒真空度一般为0.08—0.09MPa。
熔体输送区的温度应略低一些,一般为160—1800C。
在该段提高螺杆转速、减小机头阻力及在塑化区提高压力都有利于输送速率的提高,对于PVC这样的热敏塑料,不应在此段停留时间过长,螺杆转速一般为20—30r/min。
机头是挤出制品成型的重要部件,它的作用是产生较高的熔体压力并使熔体成型为所需的形状。
各部分工艺参数分别为:口模连接器温度1650C,口模温度1700C、1700C、1650C、1800C、1900C。
三、定型工艺
从机头口模挤出来的管状物要经过冷却,使它变硬而定型。
定型一般用定径套进行外径定型和内径定型两种方式。
其中外径定型结构较为简单,操作方便,我国普遍采用。
外径定型的定径外套长度一般取其内径的3倍,定径套的内径应略大于(一般不超过2mm)管材处径的名义尺寸。
管材的冷却方法有水浸式冷却和喷淋式冷却,较常用的是喷淋式冷却。
真空冷却成型是借助于真空泵将真空槽抽成真空,使管坯外壁吸附在定型套的内壁上而达到冷却定型。
真空定型的工艺条件一般为:真空度20.0—53.3kPa,水温15—250C,真空槽中的水成雾状为最佳。
若真空度偏小,导致管外径偏小,小于标准尺寸;反之,若真空度偏大,管径偏大,甚至出现抽胀现象。
若水温过低,
定型不完全,且会使管材脆性增大;若水温过高,则会造成冷却不良,致使管材易发生变形。
四、牵引工艺
牵引装置的作用是给机头挤出的管材提供一定的牵引力和牵引速度,均匀地引出管材,并通过调节牵引速度调节管子的壁厚。
牵引速度取决于挤出速度,一般牵引速度比挤出速度快1%—3%。
五、切割工艺
由行程开关根据要求长度控制后,进行自动切割,并延时翻架,实行流水生产,切割机以定长工开关信号为指令,完成切割全过程,在切割过程中与管材运行保持同步,切割过程由电动和气动驱动完成,切割机设有吸尘装置,将切割产生的碎屑及时吸出,并回收。
六、助烤扩口工艺
翻料架翻动动作由气缸通过气路控制来实现,翻料架设有一个限位装置,将切割锯切断后的管材进行烘烤,烘烤结束后进行扩管,延时后,气缸进入工作,实现翻料动作,达到卸料的目的,卸料后经延时数秒自动复位,等待下一个循环。
技术部
2012年10月27日。