陶瓷的烧成详细分析
陶瓷烧成缺陷及原因分析

陶瓷烧成缺陷及原因分析(一)变形:产品烧成变形是陶瓷行业最常见、最严重的缺陷,如口径歪扭不圆,几何形状有不规则的改变等。
主要原因是装窑方法不当。
如匣钵柱行不正,匣钵底或垫片不平,使窑车运行发生震动,影响到产品的变形。
另外,产品在烧成中坯体预热与升温快时,温差大易发生变形。
烧成温度过高或保温时间太长也会造成大量的变形缺陷。
使用的匣钵高温强度差、或涂料抹不平时也会造成烧成品的变形。
(二)开裂:开裂指制品上有大小不同的裂纹。
其原因是坯体入窑水分太高(大于2%以上),预热升温和冷却太快,导致制品内外收缩不匀。
有的是坯体在装钵前已受到碰撞有内伤。
坯体厚薄不匀,配件(如壶把、咀等)重量过大或粘结不良也会造成制品开裂。
防止的办法是:(1)入窑坯体水分小于2%,车速适当减少冷却量。
(2)装窑时套装操作谨慎,垫片与坯体配方一致。
配件大小、重量与粘接位置恰当。
有的在粘接泥浆中加入10-15%的釉料,可以使咀、把与主体牢固熔接一体,如此可克服开裂缺陷。
(三)起泡:烧制品起泡有坯泡与釉泡两种。
坯泡分为氧化泡与还原泡两种。
氧化泡指坯泡外面覆盖釉层,断面呈灰黑色,多形成于窑内低温部位。
主要是瓷胎与釉料中的分解物未能充分氧化,烧失物未完全排除所致。
予热升温快,氧化分解阶段时间短、氧化结束时窑内温度过低,上下温度差过大。
在坯釉料中,碳酸盐。
硫酸盐及有机杂质含量较多等都是造成产品起泡的主因。
此外时装车密度不当、入窑水份高等原因亦须注意。
还原泡又称过火泡,断而发黄,多发生于高温近喷火口处的制品。
主要由于坯体内硫酸盐与高价铁还原不足,强还原气氛不足及烧成温度过高造成。
釉泡系沉积炭及分解物在釉熔前未能烧尽挥发,气体被阻于釉面层中形成。
若延长釉熔时间或适当平烧即可解决。
(四)阴黄:制品表面发黄或斑状发黄,有的断面也有发黄现象,多出现在高火位处。
主要原因是升温太快,釉熔融过早,还原气氛不足、而使瓷胎中的fe2o3未能还原成feo。
此外,装钵柱太低,窑顶局部产品温度偏高而还原不足也会形成阴黄缺陷。
陶瓷烧成

烧成:陶瓷坯体通过高温热处理,发生一系列物理化学变化,矿物组成、显微结构发生变化,最终得到具有某种特定要求的陶瓷制品的工艺过程。
一次烧成:成形、干燥或施釉后的生坯,在陶瓷窑内一次烧成陶瓷产品的工艺路线。
二次烧成:即先素烧后施釉,再釉烧的工艺路线。
分为低温素烧高温釉烧和高温素烧低温釉烧。
坯体加热过程中的物理化学变化:(1)低温阶段——常温~300℃排除干燥残余水分和吸附水,少量收缩或不收缩,气孔率、强度略有增加;基本无化学变化。
(2)氧化分解阶段——300~950℃1化学变化(1)氧化反应:碳素和有机物氧化,黄铁矿(FeS2)等有害物质氧化(2)分解反应:结构水排除;碳酸盐、硫酸盐分解(3)石英晶型转变2 物理变化:(1)重量减轻,气孔率提高,有一定的收缩;(2)有少量液相产生,后期强度有一定提高。
(3)高温阶段——950℃~烧成温度一化学反应1在1050℃以前,继续上述的氧化分解反应并排除结构水;2硫酸盐的分解和高价铁的还原与分解(在还原气氛下);3形成大量液相和莫来石;→大量液相+一次莫来石生成+二次莫来石4新相的重结晶和坯体的烧结;晶粒长大,晶界移动,致密烧结。
二物理变化:气孔率降低,坯体收缩较大,强度提高,颜色变化。
(4)冷却阶段——烧成温度~室温烧成制度包括:温度制度(包括各阶段的升温速率、降温速率、最高烧成温度和保温时间)气氛制度(升温的高温阶段的气氛要求)(氧化、中性、还原)压力制度(对窑内压力的调节)注意:1坯体出现剧烈膨胀/收缩、化学反应、相变的温度区域——应缓慢升降温或适当保温2坯体形状复杂,厚度大,规格尺寸大,入窑水分高——应缓慢升降温或适当保温3低铁高钛坯料(北方)常用氧化气氛烧成;4高铁低钛坯料(南方)常用还原气氛烧成5对于普通陶瓷产品冷却制度一般为:高温阶段应当快速冷却,低温阶段相对缓慢,晶型转变温度附近最慢。
陶瓷胎体的显微结构:晶相、玻璃相、气相。
长石质瓷显微结构中各相:1 莫来石(10-30%)2 玻璃相(40-65%)3 石英(10-25%)4.气孔工艺因素对显微结构的影响:(一)陶瓷原料及配比;(二)原料粉末的特征1、颗粒大小影响成瓷后晶粒尺寸:一般规律:细颗粒粉料制成的陶瓷晶粒小,且均匀。
陶瓷烧成过程及影响因素

陶瓷烧成过程及影响因素一。
低温阶段温度低于300℃,为干燥阶段,脱分子水;坯体质量减小,气孔率增大。
对气氛性质无要求二中温阶段温度介于300~950℃1.氧化反应:(1)碳素和有机质氧化;(2)黄铁矿(FeS2)等有害物质氧化。
2.分解反应:(1)结构水脱出;(2)碳酸盐分解;(3)硫酸盐分解3.石英相变和非晶相形成。
影响因素加强通风保持良好氧化气氛,控制升温速度,保证足够氧化反应时间,减少窑内温差。
三。
高温阶段1.氧化保温阶段温度大于950℃,各种反应彻底;2.强还原阶段CO浓度3%~5% 三价铁还原成二价铁之后与二氧化硅反应形成硅酸铁。
3.弱还原阶段非晶态(玻璃相)增多,出现偏高岭石===模来石+ SiO2(非晶态)影响因素,控制升温速度,控制气氛,减小窑内温差四。
高温保温阶段烧成温度下维持一段时间。
物理变化:结构更加均匀致密。
化学变化:液相量增多,晶体增多增大晶体扩散,固液分布均匀五。
冷却阶段液相结晶晶体过冷强度增大急冷(温度大于850℃)→缓冷(850~400℃)→终冷(室温)一次烧成和二次烧成对比一次烧成又称本烧,是经成型,干燥或施釉后的生坯,在烧成窑内一次烧成陶瓷制品的工艺路线。
特点:1 工艺流程简化;2 劳动生产率高;3 成本低,占地少;4 节约能源。
二次烧成是指经过成型干燥的生坯先在素烧池中素烧,即第一次烧成然后拣选施釉在进入釉烧窑内进行釉烧第二次烧成特点:1 避免气泡,增加釉面的白度和光泽度;2 因瓷坯有微孔,易上釉;3 素烧可增加坯体的强度,适应施釉、降低破损率;4 成品变形小,(因素烧已经收缩);5 通过素检可降低次品率。
对批量大,工艺成熟质量要求不是很高的产品,可一次烧成,但一次烧成要求坯釉一起成熟,否则损失大,质量下降,应用二次烧成耐火材料的宏观性质1.气孔:开孔、闭孔和贯通孔;2.气孔率:体积百分比真气孔率Pt=(Vc+V o)/Vb×100%闭气孔率Pc= Vc/Vb×100%显气孔率Pa= V o /Vb×100%Vc---闭孔体积;Vo---开孔+贯通孔;Vb---材料总体积Pt= Pc+ Pa 3.密度(g/cm3)体积密度d=M/V视密度或表观密度da=M/(Vc+Vt)真密度dt=M/Vt Vc---闭孔体积;Vt---除气孔外的材料体积;V---总体积;M—质量4.吸水率(%)是指全部显气孔被水填满时,水的质量与干燥材料的质量之比。
陶瓷烧成工艺技术

陶瓷烧成工艺技术陶瓷烧成工艺技术是指将陶瓷原料经过成型、干燥等工序后,通过高温烧制,使其变为坚硬、致密、具有一定物理和化学性能的制品的过程和技术。
陶瓷烧成工艺技术主要包括烧成温度控制、烧成周期设计以及烧成气氛控制等方面。
首先,烧成温度控制是陶瓷烧成工艺中非常重要的一环。
陶瓷材料的烧成温度直接影响着制品的物理和化学性能。
过低的烧成温度无法使陶瓷材料充分熔化,从而导致制品的容易破碎和抗压强度低等问题。
而过高的烧成温度则会导致陶瓷制品变形、烧裂等问题。
因此,在烧成过程中,必须严格控制烧成温度,以确保陶瓷制品的质量。
其次,烧成周期的合理设计也对陶瓷制品的质量有着重要的影响。
烧成周期包括加热阶段、保温阶段和冷却阶段。
加热阶段是指将陶瓷原料从室温加热到烧成温度的过程。
在这一过程中,需要适当控制加热速率,避免因温度变化过快而导致制品破裂。
保温阶段是指将陶瓷制品在烧成温度下保持一定时间以使其均匀烧结的过程。
而冷却阶段则是将烧成完的陶瓷制品从高温环境中冷却下来的过程。
在这一过程中,需要逐渐降温,避免因温度变化过快而导致制品破裂。
最后,烧成气氛的控制也是影响陶瓷制品质量的重要因素之一。
烧成气氛是指在烧成过程中制造的气氛,包括氧气浓度、气氛性质等。
不同的陶瓷制品对烧成气氛有不同的要求。
例如,釉上瓷需要弱还原性的气氛,而瓷砖则需要强氧化性的气氛。
因此,在烧成过程中,需要控制燃烧炉内的气氛,并根据不同的陶瓷制品要求做出相应的调整。
综上所述,陶瓷烧成工艺技术是一门研究如何控制陶瓷材料在高温下进行烧结的技术。
通过合理设计烧成温度,烧成周期和烧成气氛,可以得到质量更加优良的陶瓷制品。
在实践中,还需要结合不同的陶瓷材料以及制品的特点,对烧成工艺技术进行进一步的优化和改进,以满足不断变化的市场需求。
陶瓷烧成的四个阶段
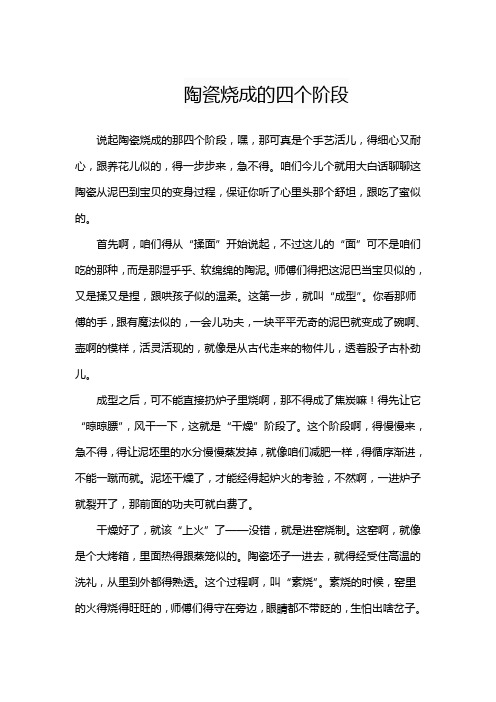
陶瓷烧成的四个阶段说起陶瓷烧成的那四个阶段,嘿,那可真是个手艺活儿,得细心又耐心,跟养花儿似的,得一步步来,急不得。
咱们今儿个就用大白话聊聊这陶瓷从泥巴到宝贝的变身过程,保证你听了心里头那个舒坦,跟吃了蜜似的。
首先啊,咱们得从“揉面”开始说起,不过这儿的“面”可不是咱们吃的那种,而是那湿乎乎、软绵绵的陶泥。
师傅们得把这泥巴当宝贝似的,又是揉又是捏,跟哄孩子似的温柔。
这第一步,就叫“成型”。
你看那师傅的手,跟有魔法似的,一会儿功夫,一块平平无奇的泥巴就变成了碗啊、壶啊的模样,活灵活现的,就像是从古代走来的物件儿,透着股子古朴劲儿。
成型之后,可不能直接扔炉子里烧啊,那不得成了焦炭嘛!得先让它“晾晾膘”,风干一下,这就是“干燥”阶段了。
这个阶段啊,得慢慢来,急不得,得让泥坯里的水分慢慢蒸发掉,就像咱们减肥一样,得循序渐进,不能一蹴而就。
泥坯干燥了,才能经得起炉火的考验,不然啊,一进炉子就裂开了,那前面的功夫可就白费了。
干燥好了,就该“上火”了——没错,就是进窑烧制。
这窑啊,就像是个大烤箱,里面热得跟蒸笼似的。
陶瓷坯子一进去,就得经受住高温的洗礼,从里到外都得熟透。
这个过程啊,叫“素烧”。
素烧的时候,窑里的火得烧得旺旺的,师傅们得守在旁边,眼睛都不带眨的,生怕出啥岔子。
素烧出来的陶瓷啊,虽然还是素白的,但已经变得坚硬结实了,就像咱们年轻人经历了社会的磨砺,变得更加成熟稳重了。
最后一步啊,就是“上色”了——不过陶瓷界可不这么叫,人家叫“釉烧”。
在素烧好的陶瓷上涂上一层釉料,再送进窑里烧一次。
这次烧啊,可不光是为了把釉料烧熟让它粘在陶瓷上那么简单了,还得让釉料和陶瓷融为一体呢!釉烧出来的陶瓷啊,那叫一个漂亮!釉面光滑如镜,色彩斑斓夺目,就像咱们精心打扮了一番去参加宴会似的,让人看了就挪不开眼。
这陶瓷烧成的四个阶段啊,就像咱们人生的四个阶段一样:从懵懂无知的孩童到青涩的少年再到成熟稳重的青年最后成为风华正茂的成年人。
陶瓷材料的高温烧成

陶瓷材料的高温烧成陶瓷是一种古老而重要的材料,广泛应用于建筑、制陶、电子、医疗器械等领域。
其中,高温烧成是制造陶瓷的关键步骤之一、本文将从高温烧成的目的、方法以及影响因素等方面进行阐述。
首先,高温烧成的目的是为了使陶瓷材料达到所要求的性能。
在高温下,陶瓷原料中的水分将被蒸发,有机物也将燃烧殆尽。
同时,由于高温使原料中的颗粒发生熔融,颗粒之间相互融合,形成致密的结构,提高了陶瓷的力学强度和化学稳定性。
因此,高温烧成既是一种物理过程,也是一种化学反应过程。
高温烧成过程中的方法有三种常见的类型,即干烧、烧结和熔融。
干烧是指将陶瓷成型坯料直接放入高温炉中进行加热,使其燃烧和结晶。
这种方法适用于耐火陶瓷等材料的制造。
烧结是将陶瓷粉末制成坯料后,在高温下加热使其颗粒间发生熔融和结晶。
烧结是陶瓷材料常用的烧结工艺,可以制造出各种类型的陶瓷制品。
熔融是将陶瓷原料加热至熔点以上,通过液相烧结使颗粒间形成致密的结构。
这种方法适用于玻璃等透明材料的制造。
高温烧成的影响因素包括烧成温度、烧成时间、加热速率和冷却速率等。
烧成温度是指陶瓷在高温炉中所达到的温度。
不同类型的陶瓷材料有不同的烧成温度要求,一般为800℃到1600℃之间。
烧成时间是指陶瓷在高温下保持的时间长度,通常为数小时到十数小时不等。
加热速率和冷却速率是指将陶瓷材料加热或冷却时的速度,对陶瓷的物理性能和组织结构有重要影响。
此外,高温烧成还需要考虑到材料的稳定性和环境污染等问题。
在高温下,陶瓷材料容易发生热膨胀和热应力破裂等问题,因此需要采取措施进行温度控制和应力释放。
同时,在烧成过程中产生的废气和废水也会对环境造成一定污染,需要进行处理和净化。
综上所述,高温烧成是陶瓷材料制造过程中不可或缺的步骤。
通过高温烧成,陶瓷材料可以达到所要求的性能,从而广泛应用于各个领域。
在实际应用中,还需要考虑烧成温度、时间、加热速率和冷却速率等因素,同时关注材料的稳定性和环境污染问题,以保证陶瓷制品的质量和生态可持续性。
烧成陶瓷原理

烧成陶瓷原理
烧成陶瓷是一种将陶瓷制品形成坚硬的原理。
在制造陶瓷过程中,陶瓷原料首先需要形成定形的模具或手工成型。
成型后的陶瓷制品需要进行烧成,以使其变得坚硬、耐磨和耐高温。
烧成过程中,陶瓷制品在高温下经历多个阶段。
第一阶段是干燥,陶瓷制品在室温下被放置一段时间,以去除残留的水分。
接下来是预烧阶段,使陶瓷制品在较低温度下逐渐失去其中的有机物质,减少烧结过程中产生的气泡和开裂。
随后是烧结阶段,陶瓷制品被加热到较高温度,使其中的颗粒逐渐结合,形成致密的结构。
在这个阶段,原子和分子之间发生了化学反应和离子迁移,使陶瓷制品逐渐变得坚硬。
温度的上升和保持时间的延长有助于提高陶瓷产品的致密度和力学性能。
最后是冷却阶段,陶瓷制品从高温环境中取出,并在室温下逐渐冷却。
冷却速度对于陶瓷制品的性能同样重要,过快的冷却可能导致开裂。
通过上述烧成过程,陶瓷原料中的颗粒之间得以结合并形成致密的结构,从而使陶瓷制品获得了较好的硬度、强度和耐用性。
烧成也有助于改变陶瓷原料的颜色和表面质感,使其具有更多的装饰性和艺术价值。
因此,烧成是制造陶瓷制品的至关重要的步骤。
瓷器的烧制方法

瓷器的烧制方法瓷器的烧制介绍瓷器的烧制是一门古老而精湛的工艺,历经千年的发展,形成了多种不同的烧制方法。
本文将详细介绍瓷器的烧制过程以及其中的各种方法。
烧制过程瓷器的烧制过程一般包括以下几个步骤:1.原料准备:瓷器的原料主要包括瓷土、石英和长石等,这些原料需要经过粉碎、筛选和混合等工序进行处理。
2.成型:成型是指将经过处理的原料按照设计要求塑造成器物的形状。
常见的成型方法包括手工捏制、轮盘成型和模具成型等。
3.修整:修整是指对成型后的器物进行细节的修整工作,如刮平表面、修整边角等。
这一步骤的目的是为了保证器物的整体美观和尺寸的准确。
4.干燥:成型完成后的器物需要进行干燥处理,使其内外逐渐失去水分。
常见的干燥方法有自然风干和人工加热干燥等。
5.烧制:烧制是整个瓷器制作过程中最重要的环节,它决定了瓷器的质量和外观效果。
常见的烧制方法有下面几种。
烧制方法瓷器的烧制方法主要有以下几种:1. 高温瓷高温瓷是指将瓷器在高温环境中进行烧制的方法。
这种方法烧制出的瓷器骨质坚实、致密,表面通常呈现出光亮的釉面。
高温瓷的烧制温度一般在1200℃以上。
2. 低温瓷低温瓷是指将瓷器在相对较低的温度下进行烧制的方法。
这种方法烧制出的瓷器多为亮彩艳丽、色调鲜明。
低温瓷的烧制温度一般在900℃左右。
3. 氧化烧氧化烧是指将瓷器在氧气充足的环境中进行烧制的方法。
这种方法可使瓷器呈现出明亮的釉色和纯净的质地。
4. 还原烧还原烧是指将瓷器在含氧量较低的环境中进行烧制的方法。
这种方法可使瓷器呈现出灰黑色的釉面和特殊的纹理效果。
雾化烧是一种将釉料雾化喷洒在瓷器表面,在高温下使其融化覆盖的烧制方法。
这种方法可使瓷器表面呈现出丰富的质感和艳丽的色彩。
结论瓷器的烧制是一个复杂而精细的过程,其中的不同烧制方法决定了瓷器的质地、颜色和纹理等特征。
选择合适的烧制方法对于创作出高质量的瓷器至关重要。
通过学习和实践,创作者可以不断完善瓷器的烧制技术,创造出更加出色的作品。
- 1、下载文档前请自行甄别文档内容的完整性,平台不提供额外的编辑、内容补充、找答案等附加服务。
- 2、"仅部分预览"的文档,不可在线预览部分如存在完整性等问题,可反馈申请退款(可完整预览的文档不适用该条件!)。
- 3、如文档侵犯您的权益,请联系客服反馈,我们会尽快为您处理(人工客服工作时间:9:00-18:30)。
陶瓷的烧成制度
陶瓷制品生产历史久远,产品种类繁多,原料来源广泛,窑炉类 型多样,生产地区分布各地,这些因素决定了陶瓷生产工艺过程的多 样性,包括用不同的烧成制度及烧成方法。 成功的烧成过程必须在合理的烧成制度下进行。对于普通陶瓷来 讲,烧成制度包括温度制度、气氛制度、和压力制度。在主要由气体 进行传热的窑炉中(如常用的固体、液体、气体燃料的窑炉,不包括 电炉)压力制度是保证温度制度及气氛制度实现的条件。 温度制度对产品性能的影响 制品烧成时,经历了 由常温加热到高温,再由高温冷却到常温的 过程。随着温度的变化,制品产生了一系列的物理化学变化(如脱水、 氧化、还原也在不断的发生变化,最终达到所需的性能指标。 我们通常所说的烧成温度,是指制品在烧成过程中所经受的最高 温度。对于具有一定原来组成、颗粒组成的坯体,都有一个对应于所 需烧结程度的煅烧阶段,此温度即为该陶瓷制品的烧成温度。
6、 1200~烧成温度,烧结阶段。 坯体中出现玻璃相,气、固、液相扩散而达致密化,该传质过程与坯 体的厚度平方成反比,故烧成时间与坯体厚度平方成正比。应据此确 定高火保温时间(1~2小时)进行高火保温。 要求:升温速度10~30 ℃/h,CO=1% 7、 烧成温度~700,急冷阶段。 产品处于热塑性阶段,可直接吹冷风急冷,冷却速度达120 ℃/h 8、 700~400,缓冷阶段。 石英晶型转化,体积收缩,而液相刚凝结,较脆弱,易惊釉、开裂, 降温速度:<80~90 ℃/h 9、 400~80,快冷阶段。 此时制品强度大,可直接鼓冷风快速冷却。
陶瓷的烧成过程及烧成制度
陶瓷的烧成过程
烧成过程实质上是若干过程的综合,一般来说,它包括下列五个过程: 1 物料的物理化学变化过程 2 物料的运动过程
3 气体流动过程 4 燃料燃烧的过程 5 传热过程 后四个过程是窑炉为了实现坯体的物理化学变化而建立外在条件(温 度、气氛)的需要。广义来说,烧成有熔制(液态)、煅烧(散料) 以及烧制(成型制品)。狭义来说,烧成就是指成型制品的烧制。
在不过烧的情况下,随着烧成温度的的升高,瓷坯的体积密度增大, 吸水率和显气孔率逐渐减小,釉面的光泽度不断提高,釉面的显微硬 度也随着温度的升高而不断增大。 在烧成温度范围内,适当提高烧成温度,有利于电瓷的机电性能 和细瓷的透光度的提高。 保温是指烧成过程中,达到最高烧成温度范围后,保持一段时间, 或在较低温度下保持一段时间,这段时间称为保温时间,随后进入冷 却阶段。在生产实践中,适当降低烧成温度,延长保温时间,有利于 提高产品品质,降低烧成损失率。保温时间及保温温度对希望釉面析 晶的产品(如结晶釉等艺术釉产品)更为重要。为了控制釉层中析出 晶核的速度、尺寸和数量,这类产品的保温温度往往比烧成温度低得 多,百问世间直接关系到晶体的形成率。 烧成过程中的升降温速度是否恰当,较直观地是看其对制品在烧 成过程中体积热胀冷缩带来的影响(有无变形、开裂)。
陶瓷烧成技术
烧窑实训
陶瓷烧成
• 陶瓷烧成是生产陶瓷制品的主要工序之一。 将生坯或半成品在高温下处理,使其发生 物理、化学变化而得产品的过程。 • 陶瓷的出现离不开窑炉。陶器的烧成温度 约800~1000℃,瓷器的烧成温度约 1200~1300℃。瓷器出现远远晚于陶瓷, 其中一个重要原因就是窑炉技术水平低, 窑炉温度不能达到瓷器烧成要求的温度。
坯体处于弹性状态时,如果加热或冷却过快,则造成坯体内外温 差过大,膨胀不一致,由此引起的热力效应达到了极限值,或因坯体 内外晶型转化不一致而产生的应力达到了极限值,(最常见的是石英 在573的晶型转化),就会使坯体开裂而变成废品。在残余物化结合 水排除阶段,因坯体水分一般都在临界水分以下,不会产生干燥收缩。 但如水分较多,升温过快,水分蒸发过急,则会使坯体炸裂。 坯体在塑性状态时,上述应力受到液相缓冲可能减小或消失。但 当存在较大重力负荷,或因坯体烧成收缩不一致时,坯体就会变形而 成废品,坯体温度愈高,其中液相粘度愈低,就越容易变形。由于烧 成温度不够高或过高,保温时间不足或过长,会导致产品生烧或过烧。 生烧表现为坯体烧结不够,坯体内物理化学变化不充分;过烧则表现 为坯体烧结过分,或发生不希望出现的变化,并常伴随有变形。
573 ℃时,体积膨胀,易变形干裂,升温应慢,升温速度:20~30 ℃/h 4 、 700~1050,氧化阶段 进行氧化反应和分解反应。硫化铁,有机物氧化,碳酸盐、硫酸盐、氢氧 化铁分解,放出二氧化 硫和二氧化碳及水蒸气等气体,应在釉面封闭以前氧清氧透,保证良好的氧化气氛和充分的氧化时 间,减少窑内温差,适当进行中火保温,否则易出现质量缺陷,如黑点、青边、发黄、气泡等。 气氛要求:O2=4~5%,CO<1% 5、 1050~1200,还原阶段 使氧化铁还原成氧化亚铁,褐色变为青色,改善制品色泽,达到白里泛青,即“白如玉”的效果。 要求:升温慢,使气体充分排除,减少坯泡 保证气氛,避免重新氧化,CO=2~4% 保证时间,以利于还原反应进行彻底
陶瓷品种多种多样,其烧成过程的物理化学变化及产品的化学矿物组成也各不相同。但从共性来看, 粘土质陶瓷的烧成过程物理化学变化大致可划分为9个阶段: 1、 20~200 ℃,排出残余水 入窑水分要求:<1%, 快烧<0.5%, 升温速度:20~30 ℃/h 2 、 200~500 ℃,排除结构水 指粘土矿物中的结晶水和层间水,安全阶段,可快烧,40~50 ℃/h 3 、 500~700 ℃,石英晶型转化