氮化硅性能原理
lpcvd氮化硅原理
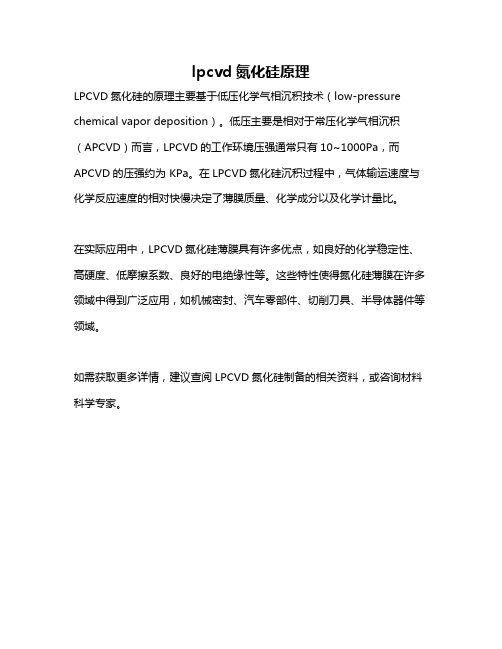
lpcvd氮化硅原理
LPCVD氮化硅的原理主要基于低压化学气相沉积技术(low-pressure chemical vapor deposition)。
低压主要是相对于常压化学气相沉积(APCVD)而言,LPCVD的工作环境压强通常只有10~1000Pa,而APCVD的压强约为 KPa。
在LPCVD氮化硅沉积过程中,气体输运速度与化学反应速度的相对快慢决定了薄膜质量、化学成分以及化学计量比。
在实际应用中,LPCVD氮化硅薄膜具有许多优点,如良好的化学稳定性、高硬度、低摩擦系数、良好的电绝缘性等。
这些特性使得氮化硅薄膜在许多领域中得到广泛应用,如机械密封、汽车零部件、切削刀具、半导体器件等领域。
如需获取更多详情,建议查阅LPCVD氮化硅制备的相关资料,或咨询材料科学专家。
氮化硅负极

氮化硅负极氮化硅(Si3N4)是一种重要的材料,被广泛应用于电池、半导体器件、磁性材料等领域。
作为一种负极材料,氮化硅在高性能电池中发挥着重要的作用。
氮化硅具有优异的化学稳定性和电化学性能。
相比于传统的石墨负极材料,氮化硅可以提供更高的比容量和更长的循环寿命。
这得益于氮化硅的特殊结构和化学稳定性。
氮化硅是由氮原子和硅原子构成的,其结构稳定且不易发生化学反应。
这使得氮化硅在充放电过程中不易发生结构变化,从而保持了较高的电化学性能。
氮化硅具有较高的离子导电性能。
在电池中,离子在正负极之间的迁移是电池的基本工作原理。
氮化硅由于其独特的结构和成分,具有较高的离子迁移速率和较低的内阻。
这使得电池可以更快地充放电,提高了电池的能量密度和功率密度。
氮化硅还具有良好的机械性能和热稳定性。
在电池中,负极材料需要能够承受反复的膨胀和收缩,而不会出现结构破坏或松动。
氮化硅具有较高的抗膨胀性和机械强度,能够有效地抵御电池循环过程中的应力和变形。
总的来说,氮化硅作为一种负极材料,在高性能电池中具有广阔的应用前景。
它的优异性能和稳定性使得电池可以具备更高的能量密度、更长的循环寿命和更快的充放电速率。
随着电池技术的不断发展和应用的扩大,氮化硅负极将在电池领域发挥越来越重要的作用。
然而,目前氮化硅负极材料的制备和应用仍面临一些挑战。
首先,氮化硅的制备工艺相对复杂,需要高温和高压的条件。
其次,氮化硅的成本相对较高,限制了其大规模应用。
此外,氮化硅的导电性能还有待进一步提高,以满足电池对高功率输出的需求。
为了克服这些挑战,科研人员正在不断探索氮化硅负极材料的制备方法和性能调控策略。
他们通过改变材料的成分、结构和微观形貌,来提高氮化硅的性能。
同时,他们还研究了氮化硅与其他材料的复合应用,以进一步提高电池的性能和稳定性。
氮化硅作为一种负极材料,在电池领域具有广泛的应用前景。
它的优异性能和稳定性使得电池可以具备更高的能量密度、更长的循环寿命和更快的充放电速率。
氮化硅键合工艺

氮化硅键合工艺氮化硅(Si3N4)是一种具有特殊性能的陶瓷材料,其在高温、高压和化学腐蚀等恶劣环境下具有出色的性能。
氮化硅键合工艺是一种常用的方法,用于将氮化硅与其他材料进行牢固的结合。
本文将介绍氮化硅键合工艺的原理、应用和优势。
氮化硅键合工艺是一种将氮化硅与其他材料结合的方法,通过在氮化硅表面形成化学键,实现材料的结合。
这种工艺主要包括前处理、键合和后处理三个步骤。
首先是前处理。
在进行氮化硅键合之前,需要对氮化硅表面进行处理,以提高其键合性能。
常用的方法包括表面清洗、表面氧化和表面改性等。
表面清洗可以去除表面的杂质和污染物,提高键合的质量。
表面氧化可以形成一层氧化硅薄膜,增加键合的强度和稳定性。
表面改性可以通过在氮化硅表面引入其他元素或化合物,改变其表面性质,提高键合的效果。
接下来是键合过程。
在进行氮化硅键合时,一般需要使用高温和高压条件下的键合设备。
常用的键合设备包括热压设备、等离子键合设备和电子束键合设备等。
在键合过程中,通过加热和施加压力,使氮化硅与其他材料接触,从而实现键合。
键合温度和压力的选择要根据材料的性质和键合要求进行调整,以获得最佳的键合效果。
最后是后处理。
在进行氮化硅键合后,需要对键合界面进行处理和修饰,以进一步提高键合的质量和性能。
常见的后处理方法包括表面抛光、界面涂层和热处理等。
表面抛光可以去除键合界面的不平整和残留杂质,提高键合的平整度和密封性。
界面涂层可以在键合界面上形成一层保护膜,提高键合的耐腐蚀性和耐磨性。
热处理可以改变键合界面的晶体结构和性能,进一步提高键合质量。
氮化硅键合工艺在许多领域都有广泛的应用。
在电子器件领域,氮化硅键合可以用于制备高温、高频和高功率电子器件。
在光电子器件领域,氮化硅键合可以用于制备高亮度LED和高效光伏电池。
在航天航空领域,氮化硅键合可以用于制备高温结构和耐热材料。
此外,氮化硅键合还可以应用于化学工业、生物医学和新能源等领域。
氮化硅键合工艺具有许多优势。
高强韧高导热氮化硅陶瓷弹簧的制备及性能研究方案(二)
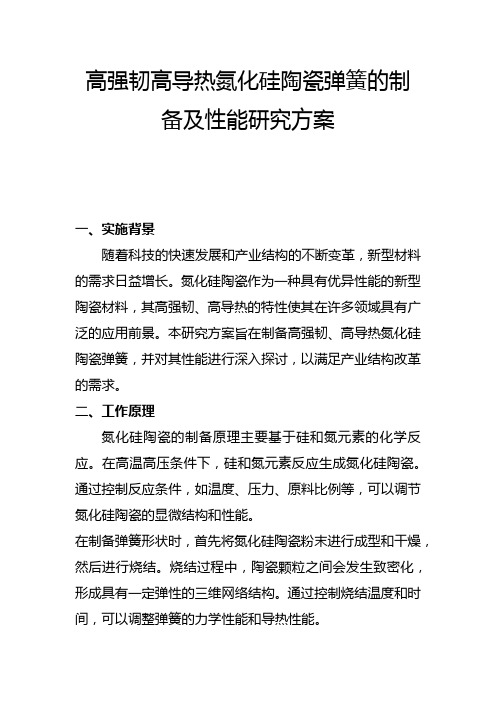
高强韧高导热氮化硅陶瓷弹簧的制备及性能研究方案一、实施背景随着科技的快速发展和产业结构的不断变革,新型材料的需求日益增长。
氮化硅陶瓷作为一种具有优异性能的新型陶瓷材料,其高强韧、高导热的特性使其在许多领域具有广泛的应用前景。
本研究方案旨在制备高强韧、高导热氮化硅陶瓷弹簧,并对其性能进行深入探讨,以满足产业结构改革的需求。
二、工作原理氮化硅陶瓷的制备原理主要基于硅和氮元素的化学反应。
在高温高压条件下,硅和氮元素反应生成氮化硅陶瓷。
通过控制反应条件,如温度、压力、原料比例等,可以调节氮化硅陶瓷的显微结构和性能。
在制备弹簧形状时,首先将氮化硅陶瓷粉末进行成型和干燥,然后进行烧结。
烧结过程中,陶瓷颗粒之间会发生致密化,形成具有一定弹性的三维网络结构。
通过控制烧结温度和时间,可以调整弹簧的力学性能和导热性能。
三、实施计划步骤1.原料准备:选择纯度较高的硅粉和氮气作为原料,确保原料中杂质含量较低,以获得高质量的氮化硅陶瓷。
2.成型和干燥:将硅粉和氮气混合并成型为弹簧形状,然后进行干燥,以去除原料中的水分。
3.烧结:将干燥后的样品在高温下进行烧结,使硅粉和氮气发生化学反应,生成氮化硅陶瓷。
通过控制烧结温度和时间,调节陶瓷的显微结构和性能。
4.性能测试:对制备得到的氮化硅陶瓷弹簧进行力学性能和导热性能的测试,包括弹性模量、抗拉强度、导热系数等。
5.数据分析:根据测试结果,分析氮化硅陶瓷弹簧的力学性能和导热性能与制备条件的关系,优化制备工艺。
四、适用范围本研究的成果可应用于以下领域:1.机械工程:高强韧、高导热的氮化硅陶瓷弹簧可用于制造高性能机械部件,如轴承、齿轮等。
其优良的力学性能和导热性能可以提高机械设备的稳定性和使用寿命。
2.汽车工业:氮化硅陶瓷弹簧在汽车工业中具有广泛的应用前景,如发动机部件、传动系统等。
其高导热性能有助于提高发动机效率,同时高强韧性能可以提高汽车的安全性。
3.航空航天:在航空航天领域,氮化硅陶瓷弹簧因其高强韧性和轻质特性,可用于制造航空航天器中的高性能弹性元件。
氮化硅点火技术原理

氮化硅点火技术原理氮化硅点火技术是一种常用的点火技术,广泛应用于燃气燃烧器、燃气轮机、内燃机等领域。
本文将从氮化硅点火器的工作原理、结构特点以及应用范围等方面进行详细介绍。
一、氮化硅点火技术的工作原理氮化硅点火技术是利用高压电场使氮化硅材料产生击穿放电,从而产生高温火花,点燃可燃气体。
其工作原理主要包括以下几个步骤:1. 高压电场形成:通过点火电源提供高压电源,将电场施加在氮化硅材料上。
高压电场的形成是实现点火的基础。
2. 氮化硅材料的击穿放电:当电场达到一定电压时,氮化硅材料会发生击穿放电,产生高能火花。
这种击穿放电的形成是点火技术的核心。
3. 火花的传播:高能火花会迅速传播到可燃气体周围,形成可燃气体的点火源。
火花的传播速度非常快,可以在极短的时间内点燃大范围的可燃气体。
4. 可燃气体的点燃:可燃气体在火花的作用下发生燃烧,产生火焰。
点火过程完成后,点火器停止工作。
二、氮化硅点火器的结构特点氮化硅点火器主要由电源、氮化硅材料和点火电极等组成。
其结构特点主要包括以下几个方面:1. 氮化硅材料:氮化硅材料是氮化硅点火器的核心部件,具有较高的击穿电压和击穿电场强度。
氮化硅材料具有优异的电学性能和热学性能,能够在高温、高压的环境下稳定工作。
2. 点火电极:点火电极是将高压电场施加在氮化硅材料上的重要部件。
其形状和排列方式可以根据具体应用场景进行设计,以实现最佳的点火效果。
3. 点火电源:点火电源提供高压电场所需的电能。
点火电源的设计应考虑到电压、电流和频率等因素,以满足氮化硅点火器的工作要求。
4. 点火控制系统:点火控制系统用于控制点火器的启动和停止,以及点火时火花的能量和频率等参数的调节。
三、氮化硅点火技术的应用范围氮化硅点火技术由于其稳定可靠、响应速度快等特点,被广泛应用于各个领域。
主要应用范围包括以下几个方面:1. 燃气燃烧器:氮化硅点火技术能够快速点燃燃气燃烧器,提高燃烧效率和可靠性,减少尾气排放。
氮化硅 深度

氮化硅深度1. 介绍氮化硅(Si3N4)是一种重要的无机材料,具有许多优异的性能。
它是由硅和氮元素组成的化合物,具有高硬度、高熔点、高耐热性和优良的电绝缘性能。
由于这些优点,氮化硅在许多领域得到了广泛的应用,如半导体、陶瓷、涂层和高温材料等。
2. 物理性质2.1 密度和晶体结构氮化硅具有高密度,其晶体结构类似于石英。
它是一种非金属材料,具有非常高的硬度和刚性。
这使得氮化硅在高温、高压和腐蚀性环境下具有出色的稳定性。
2.2 热性能氮化硅具有优异的耐热性能,可以在高温下稳定工作。
它的熔点约为1900°C,比许多金属和合金的熔点要高得多。
这使得氮化硅成为一种理想的高温材料,可以用于制造高温炉、耐火材料和高温电子器件等。
2.3 电性能氮化硅是一种优良的电绝缘材料,具有较高的介电常数和低的电导率。
这使得氮化硅在电子器件中具有重要的应用,如绝缘层、电介质和电隔离等。
氮化硅还具有优异的耐电弧击穿性能,可以防止电器设备因电弧而损坏。
3. 化学性质3.1 化学稳定性氮化硅具有良好的化学稳定性,可以抵抗酸、碱和其他化学物质的侵蚀。
这使得氮化硅在化学工业中有广泛的应用,如制造化学反应器、催化剂载体和化学传感器等。
3.2 氧化性尽管氮化硅具有较高的化学稳定性,但在高温下,它会与氧气反应生成二氧化硅。
这种氧化反应会导致氮化硅的性能下降,因此在使用时需要注意控制氧气的接触。
4. 应用领域4.1 半导体氮化硅在半导体行业中有广泛的应用。
它可以作为绝缘层、电介质和传感器等组件的材料。
氮化硅具有优异的电绝缘性能和耐高温性能,可以提高半导体器件的稳定性和可靠性。
4.2 陶瓷氮化硅具有优良的耐热性能和硬度,使其成为一种理想的陶瓷材料。
它可以用于制造高温炉、耐火材料和陶瓷部件等。
4.3 涂层氮化硅可以作为涂层材料,用于提高材料的耐磨性和耐腐蚀性。
它可以在金属表面形成坚硬的保护层,提高材料的使用寿命和性能。
4.4 高温材料由于氮化硅具有优异的耐热性能,它可以用于制造高温材料,如高温炉、耐火材料和高温电子器件等。
氮化硅结构
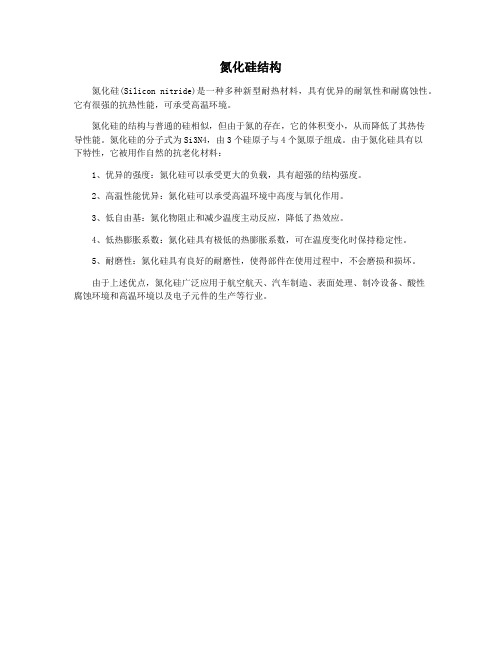
氮化硅结构
氮化硅(Silicon nitride)是一种多种新型耐热材料,具有优异的耐氧性和耐腐蚀性。
它有很强的抗热性能,可承受高温环境。
氮化硅的结构与普通的硅相似,但由于氮的存在,它的体积变小,从而降低了其热传
导性能。
氮化硅的分子式为Si3N4,由3个硅原子与4个氮原子组成。
由于氮化硅具有以
下特性,它被用作自然的抗老化材料:
1、优异的强度:氮化硅可以承受更大的负载,具有超强的结构强度。
2、高温性能优异:氮化硅可以承受高温环境中高度与氧化作用。
3、低自由基:氮化物阻止和减少温度主动反应,降低了热效应。
4、低热膨胀系数:氮化硅具有极低的热膨胀系数,可在温度变化时保持稳定性。
5、耐磨性:氮化硅具有良好的耐磨性,使得部件在使用过程中,不会磨损和损坏。
由于上述优点,氮化硅广泛应用于航空航天、汽车制造、表面处理、制冷设备、酸性
腐蚀环境和高温环境以及电子元件的生产等行业。
氮化硅点火技术原理
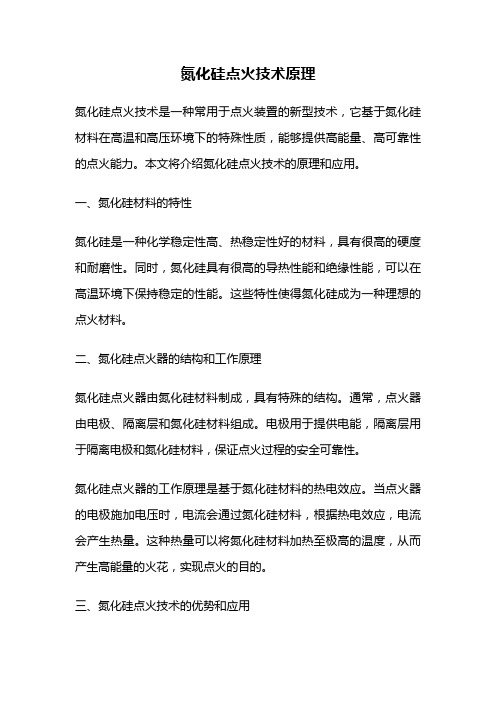
氮化硅点火技术原理氮化硅点火技术是一种常用于点火装置的新型技术,它基于氮化硅材料在高温和高压环境下的特殊性质,能够提供高能量、高可靠性的点火能力。
本文将介绍氮化硅点火技术的原理和应用。
一、氮化硅材料的特性氮化硅是一种化学稳定性高、热稳定性好的材料,具有很高的硬度和耐磨性。
同时,氮化硅具有很高的导热性能和绝缘性能,可以在高温环境下保持稳定的性能。
这些特性使得氮化硅成为一种理想的点火材料。
二、氮化硅点火器的结构和工作原理氮化硅点火器由氮化硅材料制成,具有特殊的结构。
通常,点火器由电极、隔离层和氮化硅材料组成。
电极用于提供电能,隔离层用于隔离电极和氮化硅材料,保证点火过程的安全可靠性。
氮化硅点火器的工作原理是基于氮化硅材料的热电效应。
当点火器的电极施加电压时,电流会通过氮化硅材料,根据热电效应,电流会产生热量。
这种热量可以将氮化硅材料加热至极高的温度,从而产生高能量的火花,实现点火的目的。
三、氮化硅点火技术的优势和应用氮化硅点火技术具有以下几个优势:1. 高能量:氮化硅点火器能够提供高能量的点火火花,能够可靠地点燃燃料混合物,适用于高压和高温环境下的点火需求。
2. 高可靠性:氮化硅材料具有良好的热稳定性和化学稳定性,能够在恶劣的工作环境下保持稳定的性能,确保点火器的可靠工作。
3. 长寿命:氮化硅材料具有很高的硬度和耐磨性,能够长时间保持稳定的点火性能,延长点火器的使用寿命。
氮化硅点火技术广泛应用于各种燃烧设备和燃气发动机中。
例如,氮化硅点火技术可以应用于汽车发动机、航空发动机和工业燃烧炉等。
在这些应用中,氮化硅点火技术能够提供高可靠性的点火能力,提高燃烧效率和燃烧稳定性。
四、氮化硅点火技术的发展趋势随着科技的不断进步,氮化硅点火技术也在不断发展。
未来,氮化硅点火器将进一步提高点火能量和可靠性,使其适用于更高压、更高温的工作环境。
此外,随着对环境友好型能源的需求增加,氮化硅点火技术也将应用于新能源领域,如燃料电池和氢能源。
- 1、下载文档前请自行甄别文档内容的完整性,平台不提供额外的编辑、内容补充、找答案等附加服务。
- 2、"仅部分预览"的文档,不可在线预览部分如存在完整性等问题,可反馈申请退款(可完整预览的文档不适用该条件!)。
- 3、如文档侵犯您的权益,请联系客服反馈,我们会尽快为您处理(人工客服工作时间:9:00-18:30)。
氮化硅性能原理
(1)、作为人工合成材料之一的氮化硅陶瓷材料,具有高比强、高比模、耐高温、抗氧化和耐磨损以及抗热震等优良的综合性能,广泛应用于机械、化工、海洋工程、航空航天等重要领域。
对多晶材料而言,晶界状态是决定其电性能、热性能和力学等性能的一个极其重要的因素。
对于氮化硅陶瓷来说,晶界强度是决定其能否作为高温工程材料应用的关键(2)、由于氮化硅分子的si—N键中共价键成分为70%,离子键成分为30%t引,因而是高共价性化合物,而且氮原子和硅原子的自扩散系数很小,致密化所必需的体积扩散及晶界扩散速度、烧结驱动力很小,只有当烧结温度接近氮化硅分散温度(大于1850℃)时,原子迁移才有足够的速度。
这决定了纯氮化硅不能靠常规固相烧结达到致密化,所以除用硅粉直接氮化的反应烧结外,其它方法都需采用烧结助剂,利用液相烧结原理进行致密化烧结(3)、因此,研究烧结助剂对氮化硅陶瓷致密化烧结的影响显得尤为重要。
氮化硅陶瓷作为新型的结构材料,受到越来越广泛的重视。
氮化硅工程陶瓷-家电领域
一、材料特性
抗弯强度kg/cm2 1700-2000 1600-1900 2100-2700 2200-2880
抗压kg/cm2 6500-9500 6000-8700 11000-14000 11000-15000
硬度HRA 78-82 76-80 83-85 85-87
热膨胀系数
(1/℃)
(20~800℃) 2.3-2.9 x 10-6 2.3-2.9 x 10-6 2.3-2.9 x 10-6 2.3-2.9 x 10-6
摩擦系数 0.1 0.1 0.1 0.1
抗金属熔体浸蚀铝、锌、锡、铅等
适用范围:
适用于机械、化学与耐火材料、军事工业。
已适用情况:
可作为机械密封用的密封件、耐腐蚀泵体、熔融铝液中的热电偶保护管,适用效果良好。
二、企业接产条件
所有的原材料和设备全部国产化,生产线、建筑面积、劳动定员、水、电等随生产规模而定。
三、经济效益分析
该产品是一种新型的高温结构陶瓷材料,特别是注浆成型工艺的关键技术,填补了国内空白,另外,该材料为陶瓷发动机的首选材料,具有一定的社会效益。
前言
氮化硅陶瓷今天被视为结构陶瓷的先行材料,这种材料在各种温度下具有极高的强度和抗破坏韧性,还具有较高的热稳定性、硬度、耐磨性、抗氧化抗腐蚀性等,因此它是一种具有广阔发展前景的结构陶瓷。
目前,使用氮化硅陶瓷生产的发动机部件、切削工具、轴承、自动气焊工作件等产品己显示出了优异的使用性能,产生了巨大的经济效益。
但是,氮化硅陶瓷的潜力还远未得到挖掘,在制约氮化硅陶瓷结构和性能的众多因素中,氮化硅粉体和添加剂占有重要位置。
1 对氮化硅粉体的要求
1.1 粒子的分散性高,均质性好
对于大多数工艺而言,均需要亚微米尺寸的粉体,即表面积为10~25m2/g,这样可制得高密度微粒结构材料。
1.2 a-相含量
现在,还没有质量完全符合各种要求的粉体。
就自身而言,用等离子体化学法合成的粉体可用于生产最优质量的氮化硅陶瓷。
其粒子的较高分散性和缺陷程度可以保障粉体的高度活性和良好的烧结性。
这是因为:氮化硅陶瓷的烧结和结构形成过程与伴随的a-Si3N4→β-Si3N4相变有关,且这种变化是依据通过液相再结晶的机理发生的。
虽然该项要求是公认的,但成功使用的氮化硅粉体还有非晶形成的,或含一些结晶相的。
1.3 氧量可控
氧作为基本杂质以被吸附形式参与氮化硅粉体,还以覆盖Si3N4粒子表面的SiO2和Si2N2O 形式参与。
氧的含量决定烧结时的液相量,并影响材料的相组成、结构和性能。
1.4 金属杂质和碳量极少
氮化硅粉体中存有铁、钙、镁会降低烧结时的液相粘度,将最终密度增加1﹪~5﹪,但可促进Si3N4晶粒发育和陶瓷较粗粒结构的形成,降低机械应力作用下的高温强度和加快变形速度。
有碳参与会减少液相量并改变其组成,抑制烧结和促进结构凝聚。
氮化硅粉体的性能取决于其合成方法和初始反应剂的质量。
表1中列出了采用不同合成方法制得的氮化硅粉体的基本特性。
表1 氮化硅粉体的性能
2 常用添加剂的作用
通过引入专用添加剂(通常为氧化物添加剂)可以在烧结氮化硅时达到调整液相量及其形成温度的目的。
这类能活化烧结的添加剂参与氮化硅陶瓷的相形成和显微结构形成过程,从而对烧结材料的使用性能产生重要影响。
2.1 MgO添加剂
引入MgO作添加剂,可以保障液相形成和制得高密度热压氮化硅材料。
液相的形成是由于氧化镁与二氧化硅(始终以Si3N4粒子表膜形成参与)相互作用的结果。
起初人们认为,所形成液相的组成大致与Mg SiO3 - SiO2共晶体相符,但后来确定:它具有包括四种成分Mg-Si-O-N 的较复杂组成。
冷却时,这种液相在Si3N4晶界上形成软化温度低(1000℃)的玻璃相,并决定了该材料的较低高温强度和抗蠕变能力。
2.2 Y2O3添加剂
在烧结或相对低温热压时于氮化硅中引入Y2O3可形成促进烧结的液相。
该相于最终烧结的较高温下与氮化硅反应,形成较热强的粘结相。
根据Y2O3和参与氮化硅粉末的表面的
SiO2数量,在该系统中可形成四种不同的氮化氧化物结晶相——Y2Si3O3N4、YsiO2N、Y4Si2O7N2、Y10(SiO4)6N2。
这些相沿Si3N4晶界配置,一方面保障材料的较高耐高温强度,另一方面降低其抗氮化性。
后者是因为所有这些相的氧化伴随有极大的体积效应,如当Y2Si3O3N4相氧化时,体积增大30﹪,于是陶瓷于氧化介质中工作时,它在晶界处损坏。
2.3 Y2O3——Al2O3复合添加剂
使用Y2O3——Al2O3复合添加剂可使氮化硅达到最佳烧结。
因为这种添加剂可保障形成Y—Si——Al——O——N液相,在该相参与下氮化硅烧结得最充分。
在引入Y2O3——Al2O3添加剂的情况下,可制得高强度氮化硅陶瓷。
2.4 土元素氧化物(La2O3、Sm2O3、 Nd2O3、 Yb2O3等)添加剂
引入稀土元素氧化物添加剂可因复杂氧化氮化物的形成而在陶瓷结构中产生热强晶间相。
含这种添加剂的氮化硅材料在较高温度下具有极高的强度。
2.5 ZrO2添加剂
使用ZrO2(20﹪之内)添加剂的材料通常经热压法制得,这种材料的特点是抗氧化性高,热稳定性好。
2.6 碳化物、氮化物、硅化物添加剂
由于Si3N4粒子上存有 SiO2表膜,可以采用氮化物添加剂(AiN、BeSiN4、YN等)实施氮化硅陶瓷的液相烧结,但是此时所形成液相的组成对有效烧结可能不是最佳的。
热压氮化硅时也可使用非氧化物添加剂。
例如:为了改善 Si3N4工具陶瓷的使用性能,可引入碳化物(TiC、WC)、氮化物(TiN、Bn)、硅化物(WSiO2)添加剂。
为此目的最常用的是能大大提高刀具稳定性的碳化钛,也可使用氮化钛和氮化碳化钛。