减速轴的设计实验报告带数据
减速器轴、键设计数据

轴的设计过程如下:一、轴的总体设计信息如下:轴的编号:001 轴的名称:阶梯轴轴的转向方式:单向恒定轴的工作情况:无腐蚀条件轴的转速:200r/min 功率:3.3kW 转矩:157575N·mm 所设计的轴是实心轴材料牌号:45调质硬度(HB):230抗拉强度:650MPa 屈服点:360MPa弯曲疲劳极限:270MPa 扭转疲劳极限:155MPa许用静应力:260MPa 许用疲劳应力:180MPa二、确定轴的最小直径如下:所设计的轴是实心轴A值为:115 许用剪应力范围:30~40MPa最小直径的理论计算值:29.28mm 满足设计的最小轴径:32mm三、轴的结构造型如下:轴各段直径长度:长度直径20mm 55mm10mm 67mm120mm 58mm40mm 55mm50mm 53mm100mm 52mm轴的总长度:340mm 轴的段数:6轴段的载荷信息:直径距左端距离垂直面剪力垂直面弯矩水平面剪力水平面弯矩轴向扭矩58mm 90mm -2259N -100200N·mm -6118N 0N·mm 0N·mm 52mm 340mm 1500N 0N·mm 2200N 0N·mm 620650N·mm 轴所受支撑的信息:直径距左端距离55mm 10mm55mm 170mm四、支反力计算距左端距离水平支反力Rh1 垂直支反力Rv110mm 5396.5N 3349.5N距左端距离水平支反力Rh2 垂直支反力Rv2170mm -1478.49N -2590.49N五、内力x/mm d/mm m1/N·mm m2/N·mm10 55 0 090 58 508118.81 463169.06170 55 452659.92 452659.92340 52 2.4 2.4340 52 2.4 2.4六、弯曲应力校核如下:危险截面的x坐标:30mm 直径:67mm危险截面的弯矩M:127029.7N·mm 扭矩T:620650N·mm 截面的计算工作应力:14.06MPa 许用疲劳应力:180MPa 30mm处弯曲应力校核通过结论:弯曲应力校核通过七、安全系数校核如下:疲劳强度校核如下:危险截面的x坐标:30mm 直径:67mm危险截面的弯矩M:127029.7N·mm 扭矩T:620650N·mm有效应力集中系数(弯曲作用):2.62 (扭转作用):1.89截面的疲劳强度安全系数S:5.47 许用安全系数[S]:2.030mm处疲劳强度校核通过结论:疲劳强度校核通过静校核计算:危险截面的x坐标:30mm 直径:67mm危险截面的弯矩M:127029.7N·mm 扭矩T:620650N·mm 截面的静强度安全系数:20.33 许用安全系数[Ss]:1.8 30mm处静强度校核通过结论:静强度校核通过八、扭转刚度校核如下:圆轴的扭转角:0.17(°) 许用扭转变形:0.9°/m扭转刚度校核通过九、弯曲刚度校核如下:挠度计算如下:x/mm νi/mm1 2.5 0.0117422 5 0.0078283 7.5 0.0039144 10 05 30 -0.0039146 50 -0.007577 70 -0.0103138 90 -0.0116839 110 -0.01122410 130 -0.00911511 150 -0.005368许用挠度系数:0.003最大挠度:-0.011683mm弯曲刚度校核通过十、临界转速计算如下:当量直径dv:60.43mm轴截面的惯性距I:654605.89mm^4支承距离与L的比值:0.47轴所受的重力:400N支座形式系数λ1:9.0轴的一阶临界转速ncr1:24934.97r/min轴的设计过程如下:一、轴的总体设计信息如下:轴的编号:002 轴的名称:阶梯轴轴的转向方式:单向恒定轴的工作情况:无腐蚀条件轴的转速:200r/min 功率:3.135kW 转矩:149696.25N·mm 所设计的轴是实心轴材料牌号:45调质硬度(HB):230抗拉强度:650MPa 屈服点:360MPa弯曲疲劳极限:270MPa 扭转疲劳极限:155MPa许用静应力:260MPa 许用疲劳应力:180MPa二、确定轴的最小直径如下:所设计的轴是实心轴A值为:115 许用剪应力范围:30~40MPa最小直径的理论计算值:28.78mm 满足设计的最小轴径:32mm三、轴的结构造型如下:轴各段直径长度:长度直径20mm 55mm10mm 67mm120mm 58mm40mm 55mm50mm 53mm100mm 52mm轴的总长度:340mm 轴的段数:6轴段的载荷信息:直径距左端距离垂直面剪力垂直面弯矩水平面剪力水平面弯矩轴向扭矩58mm 90mm -2259N -100200N·mm -6118N 0N·mm 0N·mm 52mm 340mm 1500N 0N·mm 2200N 0N·mm 620650N·mm 轴所受支撑的信息:直径距左端距离55mm 10mm55mm 170mm四、支反力计算距左端距离水平支反力Rh1 垂直支反力Rv110mm 5396.5N 3349.5N距左端距离水平支反力Rh2 垂直支反力Rv2170mm -1478.49N -2590.49N五、内力x/mm d/mm m1/N·mm m2/N·mm10 55 0 090 58 508118.81 463169.06170 55 452659.92 452659.92340 52 2.4 2.4340 52 2.4 2.4六、弯曲应力校核如下:危险截面的x坐标:30mm 直径:67mm危险截面的弯矩M:127029.7N·mm 扭矩T:620650N·mm 截面的计算工作应力:14.06MPa 许用疲劳应力:180MPa 30mm处弯曲应力校核通过结论:弯曲应力校核通过七、安全系数校核如下:疲劳强度校核如下:危险截面的x坐标:30mm 直径:67mm危险截面的弯矩M:127029.7N·mm 扭矩T:620650N·mm有效应力集中系数(弯曲作用):2.62 (扭转作用):1.89截面的疲劳强度安全系数S:5.47 许用安全系数[S]:2.030mm处疲劳强度校核通过结论:疲劳强度校核通过静校核计算:危险截面的x坐标:30mm 直径:67mm危险截面的弯矩M:127029.7N·mm 扭矩T:620650N·mm截面的静强度安全系数:20.33 许用安全系数[Ss]:1.830mm处静强度校核通过结论:静强度校核通过八、扭转刚度校核如下:圆轴的扭转角:0.17(°) 许用扭转变形:0.9°/m扭转刚度校核通过九、弯曲刚度校核如下:挠度计算如下:x/mm νi/mm1 2.5 0.0117422 5 0.0078283 7.5 0.0039144 10 05 30 -0.0039146 50 -0.007577 70 -0.0103138 90 -0.0116839 110 -0.01122410 130 -0.00911511 150 -0.005368许用挠度系数:0.003最大挠度:-0.011683mm弯曲刚度校核通过十、临界转速计算如下:当量直径dv:60.43mm轴截面的惯性距I:654605.89mm^4支承距离与L的比值:0.47轴所受的重力:400N支座形式系数λ1:9.0轴的一阶临界转速ncr1:24934.97r/min轴的设计过程如下:一、轴的总体设计信息如下:轴的编号:003 轴的名称:阶梯轴轴的转向方式:单向恒定轴的工作情况:无腐蚀条件轴的转速:200r/min 功率:2.98kW 转矩:142295N·mm 所设计的轴是实心轴材料牌号:45调质硬度(HB):230抗拉强度:650MPa 屈服点:360MPa弯曲疲劳极限:270MPa 扭转疲劳极限:155MPa许用静应力:260MPa 许用疲劳应力:180MPa二、确定轴的最小直径如下:所设计的轴是实心轴A值为:115 许用剪应力范围:30~40MPa最小直径的理论计算值:28.3mm 满足设计的最小轴径:32mm 三、轴的结构造型如下:轴各段直径长度:长度直径20mm 55mm10mm 67mm120mm 58mm40mm 55mm50mm 53mm100mm 52mm轴的总长度:340mm 轴的段数:6轴段的载荷信息:直径距左端距离垂直面剪力垂直面弯矩水平面剪力水平面弯矩轴向扭矩58mm 90mm -2259N -100200N·mm -6118N 0N·mm 0N·mm 52mm 340mm 1500N 0N·mm 2200N 0N·mm 620650N·mm 轴所受支撑的信息:直径距左端距离55mm 10mm55mm 170mm四、支反力计算距左端距离水平支反力Rh1 垂直支反力Rv110mm 5396.5N 3349.5N距左端距离水平支反力Rh2 垂直支反力Rv2170mm -1478.49N -2590.49N五、内力x/mm d/mm m1/N·mm m2/N·mm10 55 0 090 58 508118.81 463169.06170 55 452659.92 452659.92340 52 2.4 2.4340 52 2.4 2.4六、弯曲应力校核如下:危险截面的x坐标:30mm 直径:67mm危险截面的弯矩M:127029.7N·mm 扭矩T:620650N·mm截面的计算工作应力:14.06MPa 许用疲劳应力:180MPa30mm处弯曲应力校核通过结论:弯曲应力校核通过七、安全系数校核如下:疲劳强度校核如下:危险截面的x坐标:30mm 直径:67mm危险截面的弯矩M:127029.7N·mm 扭矩T:620650N·mm有效应力集中系数(弯曲作用):2.62 (扭转作用):1.89截面的疲劳强度安全系数S:5.47 许用安全系数[S]:2.030mm处疲劳强度校核通过结论:疲劳强度校核通过静校核计算:危险截面的x坐标:30mm 直径:67mm危险截面的弯矩M:127029.7N·mm 扭矩T:620650N·mm截面的静强度安全系数:20.33 许用安全系数[Ss]:1.830mm处静强度校核通过结论:静强度校核通过八、扭转刚度校核如下:圆轴的扭转角:0.17(°) 许用扭转变形:0.9°/m扭转刚度校核通过九、弯曲刚度校核如下:挠度计算如下:x/mm νi/mm1 2.5 0.0117422 5 0.0078283 7.5 0.0039144 10 05 30 -0.0039146 50 -0.007577 70 -0.0103138 90 -0.0116839 110 -0.01122410 130 -0.00911511 150 -0.005368许用挠度系数:0.003最大挠度:-0.011683mm弯曲刚度校核通过十、临界转速计算如下:当量直径dv:60.43mm轴截面的惯性距I:654605.89mm^4支承距离与L的比值:0.47轴所受的重力:400N支座形式系数λ1:9.0轴的一阶临界转速ncr1:24934.97r/min平键连接(静连接)校核计算结果传递的转矩T =157575 N·mm轴的直径d =60 mm键的类型sType =A型键的截面尺寸b×h =18x11 mm键的长度L =80 mm键的有效长度L0 =62.000 mm接触高度k =4.400 mm键的个数N =双键最弱的材料Met =钢载荷类型PType =静载荷许用应力[σp] =135 MPa计算应力σp =12.836 MPa校核计算结果:σ≤[σ] 满足平键连接(静连接)校核计算结果传递的转矩T =149696.25 N·mm轴的直径d =60 mm键的类型sType =A型键的截面尺寸b×h =18x11 mm键的长度L =80 mm键的有效长度L0 =62.000 mm接触高度k =4.400 mm键的个数N =双键最弱的材料Met =钢载荷类型PType =静载荷许用应力[σp] =135 MPa计算应力σp =12.194 MPa校核计算结果:σ≤[σ] 满足平键连接(静连接)校核计算结果传递的转矩T =142295 N·mm轴的直径d =60 mm键的类型sType =A型键的截面尺寸b×h =18x11 mm键的长度L =80 mm键的有效长度L0 =62.000 mm接触高度k =4.400 mm键的个数N =双键最弱的材料Met =钢载荷类型PType =静载荷许用应力[σp] =135 MPa计算应力σp =11.591 MPa校核计算结果:σ≤[σ] 满足。
实习报告范文-实验六减速器拆装及结构分析实验

实习报告范文-实验六减速器拆装及结构分析实验一、实验目的了解和熟悉各种减速器的结构,分析减速器中各零件的作用及装配关系。
测定减速器的主要参数和精度,培养和提高机械结构的设计能力。
二、实验设备与原理实验设备主要包括单级圆柱齿轮减速器、二级展开式圆锥-圆柱齿轮减速器、一级蜗杆蜗轮减速器等实物模型。
拆装和测量的工具主要有扳手、钢板尺、木棰、起子、内外卡钳、卡尺等。
三、实验要求1、按照正确的顺序拆开减速器和轴系,分析减速器中各个零件的功用;2、测定减速器的主要参数,画出减速器传动布置简图四、实验步骤1、减速器装配图参见附录。
仔细观察减速器外面各部分的结构,分析思考以下问题:判断传动方式、级数、输入、输出轴;了解铸造箱体结构,如何才能保证箱体支撑具有足够的刚度;轴承座两侧的上下箱体联接螺栓应如何布置,支撑该螺栓的凸台高度应该如何确定?如何减轻箱体的重量和减少箱体的加工面?对减速器的附件(如吊钩、定位销钉、启盖螺钉、油标、油塞、观察孔和通气器等)的结构位置要求和零件材料等进行分析。
2、用扳手拆下观察孔的盖板,观察观察孔的位置是否恰当,大小是否合适。
3、拧下箱盖和箱座联接螺栓以及轴承端盖螺钉,拔出定位销,借助起盖螺钉打开箱盖。
4、分析轴系结构:测量各段尺寸,了解轴的各部分结构作用;了解轴承的组合结构以及轴承的拆装、固定和轴向间隙的调整,了解轴承的润滑方式和密封装置。
分析轴承是如何进行润滑的?在什么条件下滚动轴承的内圈要用挡油环?其作用原理、构造和安装位置如何?如果箱座结合面上有油沟,则箱盖应该采取什么样的结构才能使箱盖上的油进入油沟?为了使润滑油经油沟后能进入轴承,则轴承盖的结构应该如何设计?为提高蜗杆轴的刚度,观察分析蜗杆轴承座的结构特点。
测绘低速轴和支撑部件的结构草图。
5、测定减速器的主要参数,记录在表中。
6、测量箱座上、下凸缘的宽度和厚度,箱壁厚度。
7、测量齿轮端面与箱体内壁的距离;大齿轮的顶圆与箱体内壁之间的距离;轴承内端面到箱体内壁之间的距离。
机械设计减速器零件测绘实验报告

实验三、机械设计课程减速器零件测绘实验报告
减速器名称齿轮减速器班级0 9 车工日期2012.06.26 姓名****
一、齿轮的测绘
(要求用CAD绘制)
二、轴的测绘
(要求用CAD绘制)
课后作业:
结合课堂教学中“齿轮的结构设计”与“轴的结构设计”部分相关知识回答下列问题
一、齿轮的结构设计应该注意哪些要点?
答:1、直径很小的钢制齿轮,当为圆柱齿轮时若齿根圆到键槽底部的距离e <2m t (m t 为端面模数);当为锥齿轮时,按齿轮小端尺寸计算而得的e <1.6m t 时均应将齿轮和轴做
成一体,叫做齿轮轴。
若e 值超过上述尺寸时,齿轮与轴分开制造合理。
2、当齿顶圆直径d a ≤160mm 时,可以做成实心结构的齿轮。
但航空产品中的齿轮,
虽说如此,也有做成腹板式的。
当齿顶圆直径d a ≤500mm 时,可做成腹板式的,腹板上
开孔的数目按结构尺寸大小及需要而定。
3、齿顶圆直径d a >300mm 的铸造锥齿轮,可以做成加强肋的腹板式结构,加强肋的
厚度C 1≈0.8C ,其他结构尺寸与腹板式相同。
4、当齿顶圆直径400mm <d a <1000mm 时,可做成轮辐截面为“十”字形的轮辐式结
构的齿轮。
5、为了节约贵重金属,对于尺寸较大的圆柱齿轮,可做成组装齿圈式的结构。
齿圈用钢制,而轮芯则用铸铁或铸钢。
6、齿轮和轴的连接设计,单键(常用)或双建连接。
二、轴的结构设计应该注意哪些要点?
答:1、拟定轴上零件的装配方案
2、轴上零件的定位
3、各轴段直径和长度的确定
4、提高轴的强度
5、轴的结构工艺性。
减速器实验报告

减速器实验报告减速器实验报告引言:减速器是一种常见的机械传动装置,广泛应用于各种机械设备中。
通过减速器的作用,可以降低旋转速度,增加扭矩输出。
本实验旨在通过对减速器的实验研究,探究其工作原理和性能特点。
实验目的:1. 了解减速器的结构和工作原理。
2. 测量减速器的扭矩输出和转速。
3. 分析减速器的效率和传动比。
实验装置和方法:本实验采用了一台带有减速器的电机作为实验装置。
实验过程中,我们固定电机的输入轴,通过改变减速器的输出轴负载,来观察减速器的性能变化。
实验步骤:1. 将电机固定在实验台上,并连接电源。
2. 将减速器的输入轴与电机轴相连。
3. 在减速器的输出轴上加装不同负载,如重物或弹簧。
4. 打开电机,记录减速器输出轴的转速和负载下的扭矩。
5. 根据测量数据计算减速器的效率和传动比。
实验结果与分析:通过实验测量,我们得到了一系列减速器在不同负载下的转速和扭矩数据。
根据这些数据,我们可以进行以下分析:1. 转速与负载关系:在实验中,我们发现减速器的输出轴转速随着负载的增加而降低。
这是因为减速器通过齿轮传动来降低转速,而增加负载会增加传动系统的摩擦和阻力,导致输出轴转速减少。
2. 扭矩与负载关系:我们还观察到减速器的输出轴扭矩随着负载的增加而增加。
这是因为减速器通过齿轮传动来增加扭矩输出,而增加负载会增加传动系统的阻力,从而使得输出轴扭矩增加。
3. 效率和传动比:通过测量数据的计算,我们可以得到减速器的效率和传动比。
效率是指减速器输出功率与输入功率之比,传动比是指减速器输出轴转速与输入轴转速之比。
通过计算,我们可以得到减速器的效率和传动比随着负载的变化情况。
实验结果显示,减速器的效率通常在80%左右,而传动比则根据不同型号的减速器而有所不同。
结论:通过本次实验,我们对减速器的结构、工作原理和性能特点有了更深入的了解。
我们发现减速器能够通过齿轮传动来降低转速、增加扭矩输出。
同时,减速器的效率和传动比也是影响其性能的重要指标。
减速器设计说明书实习报告
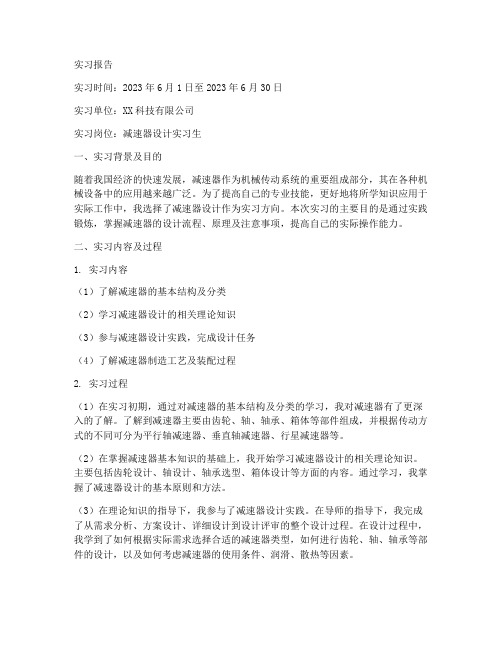
实习报告实习时间:2023年6月1日至2023年6月30日实习单位:XX科技有限公司实习岗位:减速器设计实习生一、实习背景及目的随着我国经济的快速发展,减速器作为机械传动系统的重要组成部分,其在各种机械设备中的应用越来越广泛。
为了提高自己的专业技能,更好地将所学知识应用于实际工作中,我选择了减速器设计作为实习方向。
本次实习的主要目的是通过实践锻炼,掌握减速器的设计流程、原理及注意事项,提高自己的实际操作能力。
二、实习内容及过程1. 实习内容(1)了解减速器的基本结构及分类(2)学习减速器设计的相关理论知识(3)参与减速器设计实践,完成设计任务(4)了解减速器制造工艺及装配过程2. 实习过程(1)在实习初期,通过对减速器的基本结构及分类的学习,我对减速器有了更深入的了解。
了解到减速器主要由齿轮、轴、轴承、箱体等部件组成,并根据传动方式的不同可分为平行轴减速器、垂直轴减速器、行星减速器等。
(2)在掌握减速器基本知识的基础上,我开始学习减速器设计的相关理论知识。
主要包括齿轮设计、轴设计、轴承选型、箱体设计等方面的内容。
通过学习,我掌握了减速器设计的基本原则和方法。
(3)在理论知识的指导下,我参与了减速器设计实践。
在导师的指导下,我完成了从需求分析、方案设计、详细设计到设计评审的整个设计过程。
在设计过程中,我学到了如何根据实际需求选择合适的减速器类型,如何进行齿轮、轴、轴承等部件的设计,以及如何考虑减速器的使用条件、润滑、散热等因素。
(4)在设计完成后,我了解了减速器的制造工艺及装配过程。
通过参观生产线,我了解了减速器制造的各个环节,包括铸造、加工、装配、调试等。
此外,我还学会了如何检查减速器的质量,确保其满足使用要求。
三、实习收获及反思通过本次实习,我收获颇丰。
首先,我掌握了减速器的设计流程、原理及注意事项,为自己的专业发展奠定了基础。
其次,我提高了自己的实际操作能力,学会了如何将理论知识应用于实际工作中。
减速及结构分析实验报告

一、实验目的本次实验旨在熟悉减速器的基本结构,了解减速器的用途、特点、装配关系及安装、调整过程。
通过观察、拆卸和测量,了解减速器中各组成零件的结构和功用,并分析其结构工艺性。
二、实验设备及工具1. 实验用展开式二级圆柱齿轮减速器2. 工具:游标卡尺、钢板尺、扳手、螺丝刀等三、实验方法及步骤1. 观察减速器的外形,用手同时转动输入轴和输出轴,体验减速增矩的感觉。
2. 用扳手旋开箱盖上的螺钉,打开减速器的上盖,详细分析各部分结构。
1)箱体结构:观察窥视孔、透气孔、油面指示器、放油塞、轴承座加强筋的位置和结构,定位销孔位置,螺钉凸台位置(注意扳手空间是否合理),吊耳和吊钩的形式,铸造工艺特性点(如分型面、底面及壁厚等)以及减速器箱体的加工方法。
2)轴及轴系零件的结构:分析传动零件所受的径向力和轴向力向机体基础传递的过程,分析轴上零件的轴向和周向定位的方法,分析由于轴的热胀冷缩时轴承预紧力的调节方法。
分析传动零件的结构、材料、毛坯种类。
3)润滑与密封结构:分析齿轮与轴承的调整方法,润滑方法,加油方式;放油塞和油面指示器的结构及作用。
3. 使用游标卡尺、钢板尺等工具,测量减速器各部件的尺寸和间隙,记录数据。
4. 拆卸减速器,对各个部件进行编号,登记名称和数量,分类、分组保管。
5. 分析拆卸过程中发现的问题,总结减速器结构的特点和优缺点。
四、实验结果与分析1. 箱体结构分析减速器箱体采用铸造工艺,壁厚均匀,加强筋分布合理,提高了箱体的强度和刚度。
窥视孔、透气孔、油面指示器等部件便于观察和调整,放油塞设计合理,方便加油和放油。
2. 轴及轴系零件结构分析轴及轴系零件的结构设计合理,轴承预紧力调节方法简单,便于安装和调整。
传动零件的结构、材料、毛坯种类满足减速器的工作要求。
3. 润滑与密封结构分析减速器采用油浴润滑方式,齿轮与轴承的调整方法简单,加油方式方便。
放油塞和油面指示器设计合理,有利于减速器的维护。
4. 实验中发现的问题在拆卸过程中,发现部分零件的装配间隙过大,影响了减速器的传动精度。
减速器实验报告

减速器实验报告
实验目的:通过实验研究减速器的静态特性,了解其传动比和效率的影响因素,并验证减速器的理论设计。
实验仪器:减速器、电机、转速表、负载。
实验原理:
减速器是将低速高扭矩的电机输出转速降低,扭矩增大的装置。
其传动比由输入轴的转速与输出轴的转速之比决定。
实验步骤:
1.先用电机驱动减速器,测量输入轴的转速和输出轴的转速,
计算传动比。
2.将一定负载加到输出轴上,测量输入轴的转速和输出轴的转速,计算负载转矩。
3.改变输入轴的转速,并重复步骤2,观察输入轴转速和输出
轴的转速的变化。
4.根据测得的数据,绘制输入轴转速与输出轴的转速、传动比
和负载转矩的关系曲线。
5.根据实验数据计算减速器的效率。
实验结果与分析:
根据实验数据计算得到不同输入转速下的传动比、负载转矩和效率,并绘制相应的曲线。
通过分析曲线可以得出以下结论:
1.传动比始终大于1,说明减速器具有降速的效果。
2.随着负载增加,输出轴转速降低,说明减速器输出扭矩增大。
3.随着输入转速增加,传动比减小,说明减速器的降速效果逐
渐减弱。
4.减速器的效率随着负载增加而降低。
实验结论:
通过实验验证了减速器的理论设计,得出了减速器的传动比、负载转矩和效率的变化规律。
实验结果与理论相符,说明减速器的设计和制造合理可靠。
减速器实验报告

减速器实验报告实验目的,通过对减速器的性能参数进行测试和分析,掌握减速器的工作原理和特性,为减速器的设计、选型和使用提供依据。
实验仪器,减速器实验台、电动机、转速传感器、扭矩传感器、温度传感器、数据采集系统等。
实验原理,减速器是一种用来降低旋转速度、增加扭矩的装置,通常由齿轮传动组成。
在实验中,我们将通过测量减速器的输入转速、输出转速、输入扭矩、输出扭矩以及温度等参数,来分析减速器的性能。
实验步骤:1. 将减速器实验台连接电动机、转速传感器、扭矩传感器和温度传感器,并启动电动机。
2. 通过数据采集系统记录减速器的输入转速、输出转速、输入扭矩、输出扭矩和温度等参数。
3. 分别改变电动机的转速,记录不同工况下减速器的性能参数。
4. 对实验数据进行处理和分析,得出减速器的性能曲线和特性。
实验结果与分析:通过实验数据的处理和分析,我们得到了减速器在不同工况下的性能参数。
首先,我们观察到随着输入转速的增加,输出转速呈线性减小,这表明减速器具有良好的减速效果。
其次,随着输入扭矩的增加,输出扭矩也相应增加,这说明减速器能够有效地增加扭矩。
另外,我们还发现在高速运转时,减速器的温度会明显升高,这需要在实际应用中加以注意。
结论:通过本次实验,我们深入了解了减速器的工作原理和性能特性。
减速器在工程领域中具有广泛的应用,如机械传动、工业生产等领域。
掌握减速器的性能参数对于减速器的设计、选型和使用具有重要意义。
在实际应用中,我们需要根据实际工况选择合适的减速器,并注意减速器的工作温度,以确保其正常运转和延长使用寿命。
总结:本次实验通过对减速器的性能参数进行测试和分析,增强了我们对减速器工作原理和特性的理解。
同时,也为今后的工程实践提供了重要的参考依据。
在未来的学习和工作中,我们将继续深入研究减速器及其应用,不断提高自身的专业能力和工程实践能力。
- 1、下载文档前请自行甄别文档内容的完整性,平台不提供额外的编辑、内容补充、找答案等附加服务。
- 2、"仅部分预览"的文档,不可在线预览部分如存在完整性等问题,可反馈申请退款(可完整预览的文档不适用该条件!)。
- 3、如文档侵犯您的权益,请联系客服反馈,我们会尽快为您处理(人工客服工作时间:9:00-18:30)。
机械设计基础课程设计计算说明书设计题目:设计带式输送机中的传动装置专业年级:学号:学生姓名:指导教师:机械工程系完成时间2019年7月5日机械设计基础课程设计任务书学生姓名:学号:专业:任务起止时间:年月日至年月日设计题目:设计带式输送机中的传动装置一、传动方案如图1所示:1—电动机;2—V带传动;3—单级圆柱齿轮减速器4—联轴器;5—带式输送机;6—鼓轮;7—滚动轴承图1 带式输送机减速装置方案图二、原始数据滚筒直径d /mm 400传送带运行速度v /(m/s) 1.5运输带上牵引力F /N 2300每日工作时数T /h 24传动工作年限 5 单向连续平稳转动,常温空载启动。
三、设计任务:1.低速轴系结构图1张(A2图纸);2.设计说明书1份。
在1周内完成并通过答辩参考资料:《机械设计》《机械设计基础》《课程设计指导书》《机械设计手册》《工程力学》《机械制图》指导教师签字:年月日目录(一)电机的选择 (1)(二)传动装置的运动和动力参数计算 (1)(三)V带传动设计 (2)(四)减速器(齿轮)参数的确定 (4)(五)轴的结构设计及验算 (5)(六)轴承根据 (7)(七)联轴器的选择 (8)(八)键连接的选择和计算 (8)(九)心得体会 (9)(一)电机的选择1.选择电机的类型和结构形式:依工作条件的要求,选择三相异步电机 封闭式结构 u=380v Y 型2.电机容量的选择工作机的功率P 工作机=F 牵×V 运输带/1000= 3.45 kW V 带效率η1: 0.96滚动轴承效率(一对)η2: 0.99闭式齿轮传动效率(一对)η3: 0.97 (一对) 联轴器效率η4: 0.99工作机(滚筒)效率η5(ηw ): 0.96 传输总效率η= 0.86则,电动机所需的输出功率P d =P 工作机/η= 4.01 kW3.电机转速确定工作机主动轴转速n 工作机== 71.62 r/minV 带传动比范围:2~4 一级圆柱齿轮减速器传动比范围:3~6 总传动比范围:6~24∴电动机转速的可选范围为: 429.72 ~ 1718.88 r/min在此范围的电机的同步转速有: 750r/min 、1000r/min 、1500r/min依课程设计指导书表18-1:Y 系列三相异步电机技术参数(JB/T9616-1999)选择电动机型 号: Y132M2-6 额定功率P ed : 5.5 kw 同步转速n : 1000r/min 满载转速n m : 960r/min(二)传动装置的运动和动力参数计算所选电机满载时转速n m = 960 r/min 总传动比:i 总=工作机n n m = 13.401.分配传动比及计算各轴转速i 总=i D ×i带传动的传动比i D = 2 (V 带传动比范围:2~4)一级圆柱齿轮减速器传动比i =i 总/i D 4.42 (单级齿轮传动比小于6)2.各轴输入功率,输出功率0轴(电动机轴)0d P P == 4.01 kW0m n n == 960 r/min009550P T n == 39.89 N ⋅m 1轴(高速轴) 101P P η=⋅= 3.85 kW10n n i == 320 r/min 1119550P T n == 114.90 N ⋅m 2轴(低速轴) 2123P P ηη=⋅⋅= 3.70 kW121n n i == 71.59 r/min 2229550P T n == 493.57 N ⋅m 3轴(滚筒轴) 3224ηη=⋅⋅=P P 3.63 kW32W ===n n n 71.59 r/min3339550==P T n 484.24 N ⋅m (三)V 带传动设计 1. 确定计算功率Pc根据已知条件结合教材《 机械设计基础 》由表 13-9 得到工作情况系数 K A = 1.3 ,故P ca =K A ⋅P d = 5.21 kW 。
2. 选择普通V 带型号已知P c ,n m ,结合教材《机械设计基础》,由图 13-4 确定所使用的V 带为 A 型。
3. 确定大小带轮基准直径d 1,d 2。
由《机械设计基础》表 13-4 取d 1= 140mm ,带传动比i D 已知,则d 2=i D·d 1=280mm ,取d 2= 300mm 4. 验算带速v 验算带速:d1mπ601000d n v ==⨯ 7.04 m/s ,( 是/否 )满足5m/s<v <30 m/s 。
5.求V 带基准长度和中心距(L0,a )(1) 根据d1d20d1d20.7()2()d d a d d +≤≤+,初定中心距a 0= 1000 mm 。
(2) 计算所需的带长()2d1d2d00d1d20π2()24d d L a d d a -≈+++= 2698 mm 。
由表 13-2 ,对 A 型带进行基准长度L d = 2700 mm 。
(3) 实际中心距d d00-2L L a a ≈+= 1001 mm 中心距的变化范围min dmax d0.0150.03a a L a a L =-⎧⇒⎨=+⎩ 960.5~1041.5 mm 。
6.验算小带轮包角=⨯--=01203.57180ad d α 170.832 >120°合格。
7.求V 带根数Z已知n 1,d 1 ,查表 13-4 ,得P 0= 0.78KW已知传动比i D ,查表 13-6 , 得ΔP 0= 0.05KW 已知α1,查表 13-8 得K α= 0.95 ,查表 13-2 得K L =1.10 则V 带根数Z==∆+LK K P P Pcα)(00 6.0068 ,取 6 根 。
8.求作用在带轮上的压力F Q由《机械设计基础》表13-1 ,可知 A 型带每米质量q=0.105Kg/m单根V 带的拉力F 0=qv K Zv Pc +-)15.2(500α2= 105.8 N 作用在轴上的压力F Q =2ZF 0 sin21α= 1265.54 (四)减速器(齿轮)参数的确定1. 选择材料及确定许用应力由《机械设计基础》表 11-1 得:小齿轮用: 40MnB ,热处理方式: 调质 ,齿面硬度为 241~286HBS 大齿轮用: 2G35SiMn ,热处理方式: 调质 ,齿面硬度为 241~269HBS 由表 11-5 ,取安全系数S H = 1.0 ,S F = 1.25 。
则许用应力为:[σH1]=σHlim1/S H = 655MPa . [σH2]= σHlim2/S H = 559MPa [σF1]=σFE1/S F = 476MPa . [σF2[= σFE2/S F = 408MPa2. 按齿面接触强度设计设齿轮按 8 级精度制造,按齿面接触强度设计。
由表 11-3 得载荷系数K = 1.5 ,由表 11-6 得齿宽系数Φd = 0.8 。
小齿轮输入功率P = 3.85KW , 转矩T 1=9.55×610×1n P= 1.15⨯105 , 由表 11-4 可得弹性系数Z E = 188.9√MPa 则小齿轮直径d 1≥[]32112⎪⎪⎭⎫ ⎝⎛+⨯H H E dZ Z u u KT σφ 齿数取Z 1= 50 ,Z 2=iZ 1= 223.5 模数m =d 1/z 1= 1.81mm按表 4-1 ,标准模数m = 2 ,实际传动比i =Z 2/Z 1= 4.47 传动比误差 3.8% ,是/否符合要求 。
实际标准中心距离a = 273.5 mm 齿宽=⋅=1d d b φ 73 (圆整)为补偿安装误差,取小齿轮齿宽b 1=b +5= 783.验算轮齿弯曲强度由图11-8,取齿形系数YFa1=2.56, YFa2=2.13.由图11-9,取外齿轮齿根修正系数YSa1=1.63,YSa2= 1.81判断:[]==12Sa1Fa111Y Y 2Z bm KT F σ 98.6 ≦[σF1]判断:[]==112212Sa Fa Sa Fa F F Y Y Y Y σσ 91.1 ≦ [σF2] 满足条件 合适4.齿轮的圆周速度=⨯=10006011n d v π 2.346m/s对照表 11-2 可知,选着 8 级精度是合适的。
(五)轴的结构设计及验算 1.高速轴及低速轴的材料选择根据表 14-1 得,高速轴材料为: 45钢 ,热处理方式: 调质 低速轴材料为: 45钢 ,热处理方式: 调质高速轴极限强度[σB1]= 650 ,低速轴极限强度[σB2]= 650 根据表 14-1 得,高速轴的许用弯曲应力[σ-1b ]= 300 低速轴的许用弯曲应力[σ-1b ]= 3002.轴颈初估初选小轮轴颈,根据扭转强度计算初估轴颈。
由表 14-2 得常数C= 1073111n d P C ≥= 24.52 ,结合大带轮轮毂内径,圆整后暂取d1= 25 大轮轴颈3222n d P C ≥= 39.6 ,结合联轴器内径,圆整后暂取d2= 413.轴的径向尺寸设计根据轴及轴上零部件的固定,定位,安装要求,初步确定轴的径向尺寸。
高速轴:(带尺寸的草图)各尺寸确定的依据:结合大带轮轮毂内径,圆整后取d1 =26 ;为满足大带轮的轴向定位,第一段右侧应该有轴肩,圆整后取d2= 36 ;根据选择的轴承,为便于轴承安装,圆整后取d3=40mm ;为便于齿轮安装,圆整后取d4= 42mm ;用轴肩对齿轮进行轴向固定,轴肩高度取h=2,圆整后取d5=50mm ;d6 =40 ;同一根轴上两个轴承型号相同,所以d7= d3=35 。
低速轴:(带尺寸的草图)各尺寸确定的依据:结合所选联轴器TL7的内径,取d1= 41mm;为满足大带轮的轴向定位,第一段右侧应该有轴肩,h=(2~3)c ,圆整后取d2=49mm;根据选择的轴承,为便于轴承安装,圆整后取d3=55mm;为便于齿轮安装,圆整后取d4=56mm;用轴肩对齿轮进行轴向固定,圆整后取d5=67mm;同一根轴上两个轴承型号相同,所以d6=d3=55mm.4.轴的轴向尺寸设计根据轴及轴上零部件的固定,定位,安装要求,初步确定轴的轴向尺寸。
高速轴:(带尺寸的草图)各尺寸确定的依据:结合公式和与低速轴的配合,圆整后取=42mm;2()l K e C B=++-∆-=62mm;长度= 30mm;根据选择的大齿轮的宽度,轴长比其小3mm得到= 62mm;=56mm ,= 37mm.低速轴:(带尺寸的草图)各尺寸确定的依据:结合所选联轴的毂长选择L1=110mm;长度L2=K+e+(C-△-B)= 52mm;长度l3=B+△+(2~3)+H= 47mm;根据选择的大齿轮的宽度,轴长比其小3mm得到L4=62mm;L5=1.4h =7mm,L6=H+△-L5=38mm.(六)轴承的选择轴承的主要参数(七)联轴器的选择根据轴孔直径d2= 41mm 输出转矩T= 493.57 依据《课程设计指导书》,选定联轴器型号:HL3联轴器选择表(八)键连接的选择和计算参考文献:1 机械设计基础课程设计指导书,2009年哈尔滨理工大学机械基础工程系编制;2 机械设计基础第2版,胡家秀主编(九)心得体会要求:实事求是,不少于100字。