飞机结构疲劳强度与断裂发展现状与发展趋势
航空设计中的结构强度与安全性分析

航空设计中的结构强度与安全性分析航空器是人类历史上最伟大的科技创造之一。
从莱特兄弟制造出第一架飞机,到如今各种类型的航空器在大气中飞行,航空技术的进步使得人类的生活质量得到了极大的提高,并促进了全球经济的发展。
在航空器的设计中,结构强度和安全性分析是非常重要的环节,它们保证了航空器在高空飞行中的稳定性和安全性。
1. 结构强度分析结构强度分析是指在设计和制造航空器时,考虑各个零部件和构件所需的强度及承受能力,避免任何强度不足的设计或制造错误。
因此,在航空器的设计中,结构强度分析是必不可少的。
首先,在结构强度分析中,需要考虑航空器外部所受的载荷。
载荷包括静载荷和动载荷两种。
静载荷是由于重力和悬挂负荷所产生的力,动载荷则是由于由风,加速度和其他运动因素产生的动态力。
对于静载荷,可以采用求和的方法来计算载荷总和从而得出最终的载荷。
而对于动载荷,则需要采用动态分析来计算。
其次,在结构强度分析中,应当考虑每个部件所承受的负荷。
这可以通过有限元分析方法来实现,从而确定每个部件的最大应力值和变形程度,以保证其能够承受设计所需的载荷和力。
如果任何一个部件在强度分析中出现了不足的情况,则需要重新设计或更换。
另外,结构强度分析还应考虑到材料的特性,例如弹性模量,疲劳寿命和裂纹扩展率。
这些因素被用来确定航空器部件的强度设计和使用寿命。
为了保证高度的结构强度和可靠性,航空器的每个部件都应该符合设计要求,并经过认真的测试和验证。
2. 安全性设计安全性设计是指在设计航空器时,应该将各个零部件的失效模式和失效可能性进行分析,以预防事故的发生。
在航空器设计过程中,安全性设计是同样重要的环节。
首先,需要识别和分析可能导致事故的因素。
例如,航空器过度重量或压力机械故障等。
下一步,需要评估这些因素所带来的风险。
如果这些风险超过设计标准,则必须采取必要的措施,如改变设计方法、提高组件质量等。
其次,安全性设计还应考虑到应对事故的应急措施。
《飞机疲劳强度计算》课件

通过进行疲劳试验获取材料的 S-N曲线和疲劳极限,进而评 估结构的疲劳寿命。
试验参数
需考虑加载模式、温度、湿度 等试验参数。
试验成本
试验成本较高,且需要大量时 间进行试验。
不同计算方法的比较与选择
比较
基于应力的方法简单易行,但精度有 限;基于损伤的方法考虑因素较为全 面,但计算复杂;基于循环特性的方 法依赖于试验数据,成本较高。
详细描述
针对某型飞机起落架,通过分析起落架在起降、滑行和刹车过程中的应力分布、循环次数和材料特性,采用疲劳 分析方法和安全系数法,评估起落架的疲劳性能和寿命,以确保起落架的结构安全。
05
飞机疲劳强度计算的发展趋势与展望
基于大数据和人工智能的疲劳强度预测
总结词
利用大数据技术,对飞机结构进行全面 的疲劳强度分析,通过人工智能算法预 测结构疲劳寿命,提高预测精度。
基于损伤的疲劳强度计算
80%
损伤容限方法
通过引入裂纹扩展速率模型,预 测裂纹在循环载荷下的扩展行为 ,从而评估结构的剩余寿命。
100%
裂纹闭合效应
考虑了裂纹在载荷循环过程中闭 合的现象,提高了预测精度。
80%
适用范围
适用于已知初始裂纹尺寸的情况 ,常用于飞机结构的定期检查和 维护。
基于循环特性的疲劳强度计算
01
根据飞机结构和材料特性,建立 详细的有限元模型,用于模拟飞 机的应力分布和变形情况。
02
有限元模型应包括飞机的所有主 要结构部件,如机身、机翼、尾 翼等。
计算应力应变
利用有限元模型,计算飞机在各种载荷条件下的应力应变分 布。
考虑材料的弹塑性、蠕变等特性,确保应力应变计算的准确 性。
军用飞机结构疲劳寿命分析
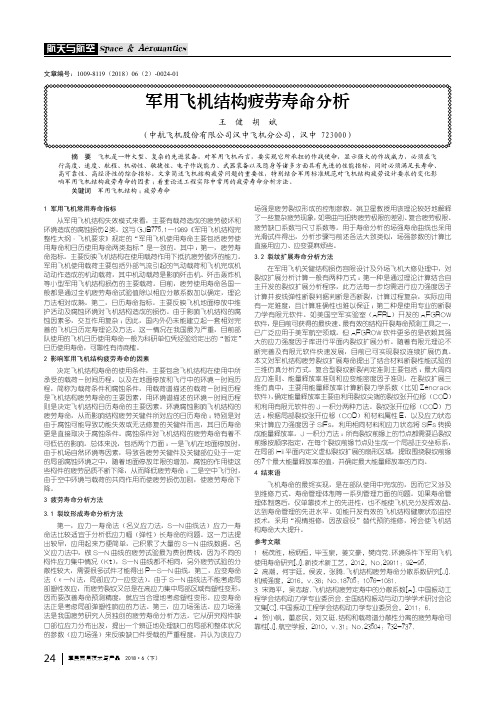
24 军民两用技术与产品 2018·6(下)文章编号:1009-8119(2018)06(2)-0024-011 军用飞机常用寿命指标从军用飞机结构失效模式来看,主要有载荷造成的疲劳破坏和环境造成的腐蚀损伤2类。
这与GJB775.1—1989《军用飞机结构完整性大纲·飞机要求》规定的“军用飞机使用寿命主要包括疲劳使用寿命和日历使用寿命两类指标”是一致的。
其中:第一,疲劳寿命指标。
主要反映飞机结构在使用载荷作用下抵抗疲劳破坏的能力。
军用飞机使用载荷主要包括外部气流引起的气动载荷和飞机完成机动动作造成的机动载荷,其中机动载荷是影响歼击机、歼击轰炸机等小型军用飞机结构损伤的主要载荷。
目前,疲劳使用寿命各国一般都是通过全机疲劳寿命试验值除以相应分散系数加以确定,理论方法相对成熟。
第二,日历寿命指标。
主要反映飞机地面停放中维护活动及腐蚀环境对飞机结构造成的损伤。
由于影响飞机结构的腐蚀因素多,交互作用复杂;因此,国内外仍未能建立起一套相对完善的飞机日历定寿理论及方法。
这一情况在我国最为严重,目前部队使用的飞机日历使用寿命一般为科研单位凭经验给定出的“暂定”日历使用寿命,可靠性有待商榷。
2 影响军用飞机结构疲劳寿命的因素决定飞机结构寿命的使用条件,主要包含飞机结构在使用中所承受的载荷-时间历程,以及在地面停放和飞行中的环境-时间历程,简称为载荷条件和腐蚀条件。
用载荷谱描述的载荷-时间历程是飞机结构疲劳寿命的主要因素,用环境谱描述的环境-时间历程则是决定飞机结构日历寿命的主要因素。
环境腐蚀影响飞机结构的疲劳寿命,从而影响结构疲劳关键件所对应的日历寿命;特别是对由于腐蚀可能导致功能失效或无法修复的关键件而言,其日历寿命更是直接取决于腐蚀条件。
腐蚀条件对飞机结构的疲劳寿命有着不可低估的影响。
总体来说,包括两个方面:一是飞机在地面停放时,由于机场自然环境等因素,导致各疲劳关键件及关键部位处于一定的局部腐蚀环境之中,随着地面停放年限的增加,腐蚀的作用使这些构件的疲劳品质不断下降,从而降低疲劳寿命;二是空中飞行时,由于空中环境与载荷的共同作用而使疲劳损伤加剧,使疲劳寿命下降。
腐蚀和疲劳对飞机结构的挑战及解决思路浅析

腐蚀和疲劳对飞机结构的挑战及解决思路浅析◎杨旭(作者单位:哈尔滨飞机工业集团有限责任公司)在飞机使用时限较长的情况下,易产生腐蚀或疲劳问题,因而飞机结构的安全性将会受到影响。
其中,结构腐蚀会导致飞机结构老化,并且飞机服役环境也会加快飞老的老化进程。
较之陆航与民航飞机,远海使用的飞机更易出现提前老化现象。
基于此,需要通过腐蚀及疲劳问题的分析与解决,延长飞机使用寿命,保障其运行安全。
一、影响飞机结构的因素分析1.腐蚀因素。
对于全世界而言,飞机腐蚀是飞机防护中面临的显著难题。
如航载飞机长期在海域上航行,受到高温天气的影响,加之海上湿度较大且空气中盐分含量较高,因而飞机结构会受到一定的腐蚀。
飞机大部分处于甲板停放状态,除了处于海洋大气环境包围之中,舰艇烟囱排出的废气和飞机起飞及着舰过程中排出尾气中的SO 2、SO 3、NO 与海洋盐雾组合成高酸性潮湿层,会在飞机机体结构表面形成pH 值为2.4~4.0的酸性液膜。
所以,相对于常规陆基飞机,舰载机的服役环境将更加严酷。
2.疲劳因素。
在交变载荷的作用下,疲劳是不可避免的。
结构的疲劳损伤不断累积,剩余强度降低,结构会出现裂纹并不断扩展。
更为严重的是腐蚀与疲劳的交互作用大大缩短裂纹的萌生时间,并且加快裂纹的扩展。
腐蚀使得飞机提前进入老龄化,产生多裂纹,特别是在一些搭接部位容易产生“枕垫效应”,产生附加应力,降低结构抗力。
二、腐蚀与疲劳对飞机结构带来的挑战及面临的解决困境1.结构腐蚀问题。
结构腐蚀是导致飞机结构损伤的主要形式,其是导致疲劳裂纹出现与扩大的直接原因,且腐蚀具有多发性特征。
除了结构腐蚀之外,还有应力腐蚀与腐蚀疲劳,这两种腐蚀损伤类型会对飞机的运行安全产生不利影响。
为此,需通过腐蚀控制措施的科学选用而提高飞机的安全飞行。
在防控措施制定之前,需对各种腐蚀类型出现的成因进行分析,以上三种腐蚀问题都应归类于电化学腐蚀之下,是由飞机服役环境所引起的,与飞机维护方式也有较大关联。
4.疲劳与疲劳断裂解析
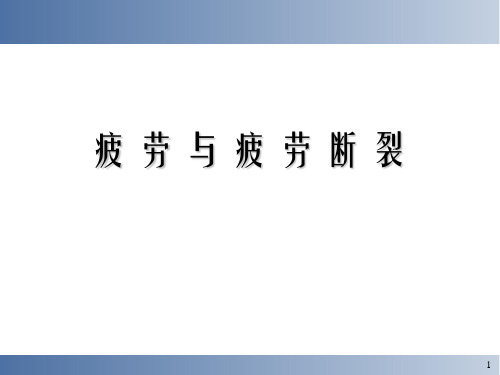
2
4
1 疲劳断裂的基本形式和特征
2
5
1 疲劳断裂的基本形式和特征
1、正断疲劳失效
正断疲劳的初裂纹,是由正应力引起的。 正断疲劳的特点是:初裂纹所在平面大致上与应力轴相垂直。 大多数的工程金属构件的疲劳失效都是以此种形式进行的。特别是 体心立方金属及其合金以这种形式破坏的所占比例更大;上述力学条件 在试件的内部裂纹处容易得到满足,但当表面加工比较粗糙或具有较深 的缺口、刀痕、蚀坑、微裂纹等应力集中现象时,正断疲劳裂纹也易在 表面产生。
2
7
1 疲劳断裂的基本形式和特征 1.2 疲劳断裂失效的一般特征
1、疲劳断裂的突发性
疲劳断裂虽然经过疲劳裂纹的萌生、亚临界扩展、失稳扩展三个元过程, 但是由于断裂前无明显的塑性变形和其它明显征兆,所以断裂具有很强的突发性 。即使在静拉伸条件下具有大量塑性变形的塑性材料,在交变应力作用下也会显 ~ 示出宏观脆性的断裂特征。因而断裂是突然进行的。
疲劳与疲劳断裂
1
绪言
金属在循环载荷作用下,即使所受的应力低于屈服强度,也会发
பைடு நூலகம்
生断裂,这种现象称为疲劳。
疲劳断裂,一般不发生明显的塑性变形,难以检测和预防,因而机
件的疲劳断裂会造成很大的经济以至生命的损失。
疲劳研究的主要目的:为防止机械和结构的疲劳失效。
2
疲劳断裂引起的空难达每年100次以上
国际民航组织 (ICAO)发表的
“涉及金属疲劳断裂的重大飞机失事调查”指出: 80年代以来,由金属疲劳断裂引起的机毁人亡重大事故, 平均每年100次。(不包括中、苏) 工程实际中发生的疲劳断裂破坏,占全部力学破坏的5090%,是机械、结构失效的最常见形式。
因此,工程技术人员必须认真考虑可能的疲劳断裂问题。
浅析飞机结构的一些疲劳破坏问题

29中国设备工程Engineer ing hina C P l ant中国设备工程 2019.01 (下)疲劳破坏是材料或结构的局部损伤,在交变应力下,损伤发展直至破坏的过程。
疲劳破坏往往产生于局部,尤其是应力应变集中处,因此疲劳对缺陷非常敏感。
影响结构疲劳强度的因素主要包括材料成分、微观组织结构和表面状况等内部因素以及环境温度、介质、载荷等外部因素。
疲劳破坏较隐蔽,发生时通常没有明显的塑性变形,事前不易察觉,这使得疲劳破坏成为了机械构件的“致命杀手”。
据统计,机械零部件的破坏中约有超过50%是由疲劳引起的。
本文将围绕飞机结构的疲劳破坏问题,首先讨论一些空难事故,分析这些空难事故中的飞机结构疲劳破坏现象;然后对这些易发生疲劳破坏的典型结构,简单总结国内外学者的研究进展和研究成果;最后将结合飞机结构设计方法的发展,讨论针对疲劳破坏问题的处理方法。
1 飞机结构的疲劳破坏现象飞机在服役过程中,不断重复着起飞-飞行-降落这一过程,飞机的结构将承受各种各样反复作用的疲劳载荷。
这些疲劳载荷主要包括:(1)飞机在机动飞行中承受的气动交变载荷。
(2)飞机在不稳定气流中飞行时受到的突风作用。
(3)飞机停放\滑行、起飞、降落过程中机翼承受的地-空-地循环载荷。
(4)飞机着陆接地后,起落架的弹性引起飞机颠簸加到飞机结构上的载荷。
(5)飞机在地面滑行时因跑道不平整引起颠簸或因转弯等多种操作加到飞机上的重复载荷。
(6)飞机在飞行周期中由于座舱增压和卸压而加给座舱周围构件的重复载荷。
在这些外部循环载荷作用下,飞机结构内部的应力也将是周期性变化的“循环应力”。
在服役环境下,飞机结构容易出现疲劳破坏,造成灾难性事故。
2 飞机典型结构的疲劳破坏研究从众多的空难事故来看,飞机结构中可能发生疲劳破坏的部位较多,如机翼、机身等,而复杂的服役环境,如腐蚀、高温、低温等,将可能加速疲劳破坏的发展。
为了确保飞机结构的安全,学者们对不同的典型结构在不同环境下的疲劳破坏问题开展了研究。
微动疲劳研究的现状与展望
第 35 卷第 6 期
杨茂胜等 微动疲劳研究的现状与展望
47
不同材料的的接触对 TI-6AL-4V 钛合金微动疲劳的影响。2006 年,M. Massingham 等[12]研究了 圆柱面接触条件下变幅加载对微动疲劳应力分布的影响。2007 年,M.S.D. Jacob 等[13]通过实验 和理论分析研究了 7075-T6 铝合金的微动疲劳裂纹形成问题, 在应力计算方面, 1997 年, Harish Ganapathy 等[14-15]建立了蒙皮/铆钉微动接触有限元模型,计算了应力分布并预测了裂纹萌生时 2006 年, Toshio Hattori 间及位置。 2003 年, C.L. Brooks 等[16]对航空结构件建立了微动疲劳模型。 等[17]研究了考虑微动磨损过程的微动疲劳强度,Sergio Munoz 等[18]用断裂力学方法估算了微动 疲劳强度。2007 年,J. Ding 等[19]用有限元法分析了磨屑对微动磨损的影响。
图 2 铆接件发生微动的位置 图 1 常见微动损伤模式示意图 (a)微动磨损
P D P P σ(t) D
Fatigue Load Corrosive Medium
P
(b)微动腐蚀
(c)微动疲劳
后参照现有理论成果归纳了减缓微动疲劳损伤的防护措施。
2
微动摩擦学发展历史
微动研究经历了三个阶段[3] 阶段 1:微动现象的发现及早期理论的建立(1911 年~20 世纪 50 年代) 。1911 年 Enden,
Rose 和 Cunningham 首次观察到微动和疲劳的联系,1927 年 Tomlinson 提出了一种微动机理, 并在其研究报告中首次出现“Fretting”一词。1949 年 Mindlin 首次将接触力学引入微动领域, 为微动力学分析奠定了基础;接着 1953 年和 1954 年分别由 Feng 和 Uhigh,提出了化学机械理 论和磨损速率变化理论,为微动疲劳研究的发展推进了一大步。 阶段 2:微动疲劳的发展阶段(20 世纪 60 年代~20 世纪 80 年代) ,1969 年 Nishioka 等, 提出了一种微动疲劳模型,预测了试件的微动疲劳寿命:1972 年 Waterhouse[4]在总结前人研究 的基础上发表了首部有关微动的专著《Fretting Corrosion》 。1988 年,Vincent 和 Godet[5]提出了 速度调节理论。在这一阶段,关于微动现象的研究才算真正的开始,有关微动损伤的研究论文 数量大大增加,对微动损伤机理的研究更加系统和深入,提出了一些微动疲劳理论。 阶段 3:微动疲劳的崭新阶段(20 世纪 90 年代~现在) ,这段时期,有关微动疲劳的研究 论文猛增,1990 年,Godet[6]提出了微动磨损的三体理论。值得一提的是 1992 年,zhou 等[7]提 出二类微动图理论,从而揭示了微动运行机制和材料损伤规律,对微动疲劳的发展做出了重要 贡献。在具体材料及结构的微动损伤分析方面:1998 年,Matthew P.Szolwinski 等[8]观察,分析 和预测了 2024-T351 铝合金的微动疲劳行为。 2000 年, K.Sat 等[9]研究了强磁场对微动磨损的影 响。2003 年 J.F. Matlik 等[10]通过实验分析了高频、高温对微动疲劳的影响,H. Lee 等[11]研究了
航空涡扇发动机结构强度试验技术发展
航空发动机
Aeroengine
Vol. 47 N术发展
安中彦
(中国航发沈阳发动机研究所,沈阳 110015)
摘要:航空涡扇发动机是军民用飞机的主要动力装置,航空发动机结构强度试验目的是验证发动机整机及零部件结构的强
为中国与国外先进水平在试验硬件设备、适航性专用试验技术和能力、先进试验技术的自研能力方面存在差距与不足,提出夯实
现有强度试验相关的技术基础、紧跟先进的强度试验技术发展、提升围绕发动机极端工况需求的研制能力的强度试验技术的发展
思路和方向。
关键词:强度试验;发展历程;结构完整性;航空涡扇发动机
中图分类号:V216.1
文献标识码:A
doi:10.13477/ki.aeroengine.2021.04.016
Development of Structural Strength Test Technology of Turbofan Aeroengine
AN Zhong-yan (AECC Shenyang Engine Research Institute,Shenyang 110015,China) Abstract:Turbofan aeroengine is the main powerplant of military and civil aircraft. The purpose of aeroengine structural strength test is to verify whether the strength,deformation,vibration,fatigue,creep,damage tolerance,life and structural reliability of the engine and its components meet the design specifications,standards and actual operation requirements. At present,the main types of relevant structural strength tests in China were vibration test,rotor test,static and fatigue test,thermal strength test. Based on the requirement analysis of strength test for turbofan aeroengine,the strength test technology of turbofan aeroengine was summarized. The requirements of strength test in terms of development specifications and technology development were summarized. The professional development status of strength test technology at home and abroad were described briefly. The analysis shows that there are gaps and deficiencies between China and western countries in test hardware equipment,airworthiness special test technology and capability,and self research capability of advanced test technology. The development strategy and direction of the strength test technology are presented,which is based on the technology related to the strength test,closely following the development of the advanced strength test technology,and improving the research and develop⁃ ment ability around the requirements of the aeroengine extreme operation conditions. Key words:strength test;development process;structural integrity;turbofan aeroengine
飞机机翼结构疲劳分析与改进
飞机机翼结构疲劳分析与改进一、引言随着飞机设计的不断发展,飞行安全一直是人们关注的话题。
而飞机机翼作为飞机内部重要组成部分之一,在飞行中所承受着的各种载荷和环境条件,也使得其成为了设计中需要重点关注的部分之一。
本文针对机翼疲劳问题开展探究与改进。
二、机翼疲劳问题分析在飞机飞行过程中,机翼所承受的各种载荷和环境条件,都会导致其产生疲劳问题。
机翼疲劳问题如果不得到及时发现和解决,会对飞行安全产生严重危害。
下面我们从材料、载荷等方面分析机翼疲劳问题:1. 材料的影响机翼疲劳问题与机翼材料有着密不可分的关系。
材料应力、应变、弹性模量、屈服强度等因素都与机翼的疲劳问题有关。
如果所选材料性能不合适,就会直接影响机翼的寿命。
2. 载荷的影响机翼肩负着整个飞机的重量,同时在飞行过程中还会受到各种不同的载荷作用。
比如飞机转弯、升降等动作所产生的载荷,都会对机翼的疲劳问题产生影响。
当载荷强度过大或者载荷类型变化过于频繁时,都会加剧机翼的疲劳问题。
三、机翼疲劳问题的检测方法为了及时发现机翼疲劳问题,需采取有效的检测方法。
目前,机翼疲劳问题的检测方法主要包括有损检测法、无损检测法、材料力学试验法等。
1. 有损检测法有损检测法是指对机翼进行部分拆卸,然后进行切割检测。
这种方法可以直接发现机翼内部的裂纹等疲劳问题。
但是,有损检测法的缺点在于检测过程中会破坏机翼表面,修复难度较大。
2. 无损检测法无损检测法是指利用电磁波、声波、超声波、磁粉探伤等技术对机翼进行检测。
这种方法不会对机翼造成任何损伤,但是检测结果有时可能会因探测设备灵敏度不够等因素影响准确性。
3. 材料力学试验法材料力学试验法是对所用材料进行实验检测。
这种方法可以验证所用材料的强度、疲劳寿命等参数是否符合要求。
但是,需要进行多次试验才能得到准确的数据。
四、机翼疲劳问题的解决方法针对机翼疲劳问题,需要采取有效的解决方法,以保证飞行安全。
1. 采用合适的材料机翼疲劳问题与所选材料有密切关系,选用高强度、低腐蚀性、疲劳寿命长的材料,可以有效减缓机翼的疲劳程度。
材料疲劳案例分析及设计
A. 减缓应力集中的措施
• 紧配合的轮毂与轴的配合面边缘处,有明显的应力集中。 若在轮毂上开减荷槽,并加粗轴的配合部分,以缩小轮毂与 轴之间的刚度差距,便可改善配合面边缘处应力集中的情况
飞机金属疲劳与腐蚀疲劳
• 统计数据表明,飞机结构中有半数以上的破坏形式与 腐蚀或腐蚀疲劳有关。
• 由于具有重量轻、强度好等优越性能的高强度铝合金
已成为航空领域中使用最为广泛的金属材料。然而从
目前对高强度铝合金腐蚀疲劳的研究成果来看,铝合
金对腐蚀引起的破坏是敏感的,腐蚀环境往往会使铝 合金结构的疲劳寿命大大缩短。
材料疲劳破坏案例
报告内容
波音747的疲劳开裂 摩托车发动机连杆断裂原因分析
波音747的主要尺寸
波音747的疲劳开裂
波音747外表皮的成分分析: • 设计师为了减轻飞机自身重量,使得飞机能减少耗油量能 飞得更远,表皮采用的是铝合金。 波音747飞行速度与常识:
• 波音747一经问世,便赢得了全世界乘客的青睐。747集先 进技术于一体,是世界上最先进、燃油效率最高的飞机。 747-400是目前生产的唯一747机型,在气动性能方面有了 许多重要的改进。波音747是目前世界上运用最广泛的客 运飞机,也是最快的亚音速飞机,其速度能达到音速的 85%,即900km/h。
A. 减缓应力集中的措施
• 在角焊缝处,采用坡口焊接,应力集中程度要比无坡口焊接 改善的多。
B. 增高表层强度
用机械法强化表层(如滚压、喷丸等),使构件表面形 成预压应力层,减弱易引起裂纹的表面拉应力,从而提高疲 劳强度。或采用热处理和化学处理 ,如高频淬火、渗碳、氮 化等。
- 1、下载文档前请自行甄别文档内容的完整性,平台不提供额外的编辑、内容补充、找答案等附加服务。
- 2、"仅部分预览"的文档,不可在线预览部分如存在完整性等问题,可反馈申请退款(可完整预览的文档不适用该条件!)。
- 3、如文档侵犯您的权益,请联系客服反馈,我们会尽快为您处理(人工客服工作时间:9:00-18:30)。
飞机结构疲劳强度与断裂发展现状与发展趋势
领空权对于任何一个国家都是非常重要的,飞机的先进,是领空权的保证.飞机更是国家的国防的重要力量,提高飞机的性能更是每个军事大国追求的目标.飞机的结构抗疲劳强度与断裂强度是飞机性能的重要体现.通过这学期的学习,和老师耐心的讲解,我对我国飞机结构疲劳强度与断裂发展现状与发展趋势有了更进一步的了解.
疲劳强度是指飞机结果在无限多次交变载荷作用下而不破坏的最大应力称为疲劳强度或疲劳极限。
实际上,飞机结构并不可能作无限多次交变载荷试验。
断裂是指飞机结构被断错或发生裂开.讨论的主要是脆性断裂情况,其断裂面是看得见摸得着的。
还有两类断裂的断裂面则是看得见却不一定摸得着的。
许多飞机结果,如轴、齿轮、轴承、叶片、弹簧等,在工作过程中各点的应力随时间作周期性的变化,这种随时间作周期性变化的应力称为交变应力(也称循环应力)。
在交变应力的作用下,虽然零件所承受的应力低于材料的屈服点,但经过较长时间的工作后会产生裂纹或突然发生完全断裂。
疲劳破坏是机械零件失效的主要原因之一。
据统计,在飞机结构失效中大约有80%以上属于疲劳破坏,而且疲劳破坏前没有明显的变形,所以疲劳破坏经常造成重大事故,所以对于轴、齿轮、轴承、叶片、弹簧等承受交变载荷的零件要选择疲劳强度较好的材料来制造。
疲劳失效是金属材料常见的失效形式,特别是轴类,连杆,轴承类等零件,长期在应力下工作的工件材料都要求较高的疲劳强度,这样的可以提高零件的使用寿命。
疲劳强度同时还与硬度、强度、韧性有较大关系,所以他是金属材料的重要力学性能指标
航空工业作为技术密集、知识密集的高技术产业,集材料、机械、发动机、空气动力、电子、超密集加工、特种工艺等各种前沿技术之大成。
目前,国际航空技术发达国家早已实施损伤容限耐久性规范,并成为国际适航性条例要求。
然而,在飞机结构的三维损伤容限耐久性预测设计方面,由于研究队伍严重萎缩,国际上的实质性进展非常缓慢,三维损伤容限耐久性技术的发展停滞不前。
与此同时,现代飞机大量使用三维整体结构,已有技术与需求的矛盾更加突出。
这一现状的存在,使得国内外的设计者们在已有技术基础上不得不依靠更加实际、但耗资巨大的全机试验和各级全尺寸部件试验来检验飞机结构的损伤容限和耐久性,虚拟试验的科学基础欠缺。
近年随着计算机容量逐渐满足三维断裂分析的需要,国际上三维试验和数值研究骤增,多尺度研究骤增,虚拟试验的概念形成并得以应用。
有影响和代表水平的工作主要出自美国NASA以Newman为主的研究组、英国Sheffield大学Code公司及其研究组、法国宇航院(ONERA)、瑞典航空研究实验室(FOI,德文首字)研究组,荷兰国防动力研究实验室、澳大利亚国防科技组织(DSTO)等[5-8]。
但是其损伤容限耐久性技术依据的理论基础仍然是二维疲劳断裂理论,未取得本质上的突破,考虑三维约束的疲劳寿命分析模型也都是建立在大量经验参数基础上的。
近年,我国某飞机设计行业以及相关单位已成功实现全数字化设计、制造,一些重点型号工程在设计阶段就已全面实施损伤容限与耐久性规范,开展了大量全尺寸静力、疲劳/耐久性和损伤容限试验,建立起宝贵的经验和高素质的队伍以及组织管理体系。
然而,基于试验来保证性能的经验设计方法存在明显的局限:全尺寸试验之前主要是经验估计,如各种安全系数法,对经验积累依赖严重,不利创新发展;试验或一定要设法满足设计要
求,否则发现问题后更改设计困难,代价很高;全尺寸试验只能检验最薄弱环节,不能真实考核整体结构的设计水平,尤其是优化程度;全机试验只能检验一种工况(如标准载荷谱、实验室环境和周期、抽取的单一的制造质量样本等,代价高昂但实际效果远不是人们认为的那么一锤定音式的决定一切。
因此,发展基于三维损伤容限与耐久性科学基础的预测设计技术已变得十分必要和迫切。
破飞机结构三维损伤容限和耐久性核心技术可望取得的突
发展基于先进的三维疲劳断裂理论和自主知识产权的三维损伤容限和耐久性关
键技术,解决从材料性能到三维复杂结构性能的跨越。
飞机制造技术正沿着生产工艺依赖经验型向工艺模拟、仿真、实时监控、智能化制造方向发展;零件加工成形连接技术向增量成形、高速切削、高能束加工、精密成形等低应力、小变形、长寿命结构制造方向发展;从单个零件制造,向整体结构制造技术及近无余量制造技术发展;飞机制造技术从手工劳动、半机械化、机械化向数控化、柔性化、自动化技术方向发展;从一般铝合金结构的制造向以钛合金为代表的高性能轻合金结构、复合材料结构制造技术方向发展;向材料制备与构件成形同时制造发展;制造技术向信息化、数字化及设计/制造一体化方向发展,现代飞机制造技术正处在一个新的变革时代,它将为新一代飞机研制提供更先进的技术。
参考资料: /view/6aae14c3d5bbfd0a7956736c.html。