常减压蒸馏过程
《常减压蒸馏》课件

详细描述
在常减压蒸馏过程中,产品质量受到多种因素的影响,如原料的性质、工艺参数的选择 和控制等。为了确保产品质量达标,需要定期对产品进行化验分析,并根据分析结果对 工艺参数进行调整。此外,加强生产过程中的质量监控和质量管理也是提高产品质量的
重要措施。
05
常减压蒸馏的优化与改进
工艺参数优化
01
02
03
04
温度控制
通过精确控制加热温度,优化 蒸馏过程,提高产品质量和收
率。
压力调节
合理调节系统压力,改善传热 效果和分离效率,降低能耗。
液位控制
保持塔内液位稳定,防止溢流 和抽空现象,确保生产稳定。
进料流量与组成
优化进料流量和组成,提高轻 重组分的分离效果,降低能耗
原理
基于物质沸点的不同,通过加热 和冷凝的方式将石油中的不同组 分分离出来。
历史与发展
历史
常减压蒸馏技术起源于19世纪中叶 ,随着技术的不断发展和改进,已成 为石油工业中的重要工艺。
发展
近年来,随着环保要求的提高和能源 结构的调整,常减压蒸馏技术也在不 断优化和升级,以实现更加高效、环 保的生产。
分馏塔和冷凝器
分馏塔
是常减压蒸馏的核心设备,通过精馏原理将原料油分离成不同沸点的组分。
冷凝器
用于将蒸馏出的轻组分冷凝成液体,同时将过热蒸汽进行冷却和回收。
回流罐和产品罐
回流罐
用于收集和储存回流液,为蒸馏塔提 供回流热源,保持塔内温度稳定。
产品罐
用于储存不同沸点组分的油品,方便 后续处理和运输。
04
原料加热
通过加热使原料软化,降 低粘度,便于后续加工。
三段汽化的常减压蒸馏工艺流程

三段汽化的常减压蒸馏工艺流程
常减压蒸馏是一种常用的汽化工艺,用于将混合物分离成不同组分。
其工艺流程通常包括以下三段:
第一段:汽化段
在这一段中,混合物首先被加热到汽化温度,使其中的液体部分转变为气体。
这可以通过加热器或者换热器实现。
汽化段的目的是将混合物分离为气体和液体两个相态。
第二段:减压段
在这一段中,汽化后的气体进入减压塔,通过降低压力,使其中的轻质组分蒸发出来。
减压段的目的是根据组分的沸点差异,将混合物中的不同组分分离出来。
分离效果取决于减压塔的设计和操作条件。
第三段:冷凝段
在这一段中,减压塔中蒸发出来的气体经过冷凝器冷却,转变为液体,从而得到纯净的组分。
冷凝段的目的是回收和收集分离出来的组分。
常减压蒸馏的工艺流程包括汽化段、减压段和冷凝段。
通过控制温度和压力等操作条件,可以实现混合物中不同组分的分离和回收。
常减压蒸馏工艺流程
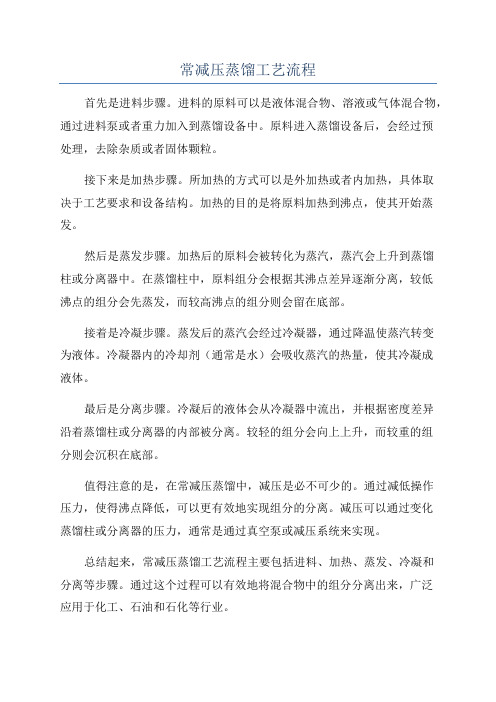
常减压蒸馏工艺流程
首先是进料步骤。
进料的原料可以是液体混合物、溶液或气体混合物,通过进料泵或者重力加入到蒸馏设备中。
原料进入蒸馏设备后,会经过预
处理,去除杂质或者固体颗粒。
接下来是加热步骤。
所加热的方式可以是外加热或者内加热,具体取
决于工艺要求和设备结构。
加热的目的是将原料加热到沸点,使其开始蒸发。
然后是蒸发步骤。
加热后的原料会被转化为蒸汽,蒸汽会上升到蒸馏
柱或分离器中。
在蒸馏柱中,原料组分会根据其沸点差异逐渐分离,较低
沸点的组分会先蒸发,而较高沸点的组分则会留在底部。
接着是冷凝步骤。
蒸发后的蒸汽会经过冷凝器,通过降温使蒸汽转变
为液体。
冷凝器内的冷却剂(通常是水)会吸收蒸汽的热量,使其冷凝成
液体。
最后是分离步骤。
冷凝后的液体会从冷凝器中流出,并根据密度差异
沿着蒸馏柱或分离器的内部被分离。
较轻的组分会向上上升,而较重的组
分则会沉积在底部。
值得注意的是,在常减压蒸馏中,减压是必不可少的。
通过减低操作
压力,使得沸点降低,可以更有效地实现组分的分离。
减压可以通过变化
蒸馏柱或分离器的压力,通常是通过真空泵或减压系统来实现。
总结起来,常减压蒸馏工艺流程主要包括进料、加热、蒸发、冷凝和
分离等步骤。
通过这个过程可以有效地将混合物中的组分分离出来,广泛
应用于化工、石油和石化等行业。
常减压蒸馏工艺流程
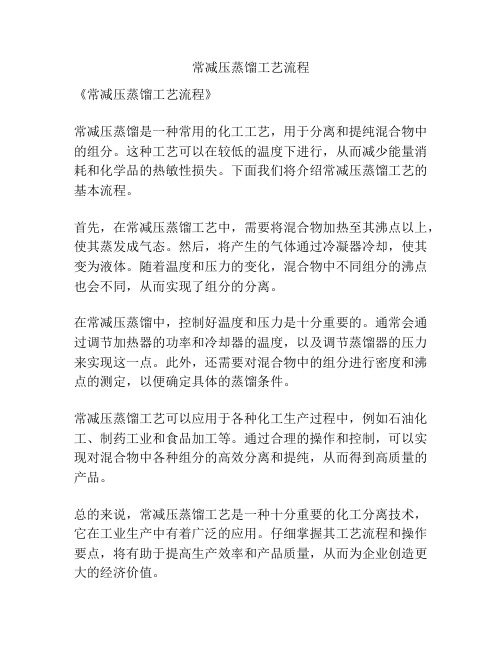
常减压蒸馏工艺流程
《常减压蒸馏工艺流程》
常减压蒸馏是一种常用的化工工艺,用于分离和提纯混合物中的组分。
这种工艺可以在较低的温度下进行,从而减少能量消耗和化学品的热敏性损失。
下面我们将介绍常减压蒸馏工艺的基本流程。
首先,在常减压蒸馏工艺中,需要将混合物加热至其沸点以上,使其蒸发成气态。
然后,将产生的气体通过冷凝器冷却,使其变为液体。
随着温度和压力的变化,混合物中不同组分的沸点也会不同,从而实现了组分的分离。
在常减压蒸馏中,控制好温度和压力是十分重要的。
通常会通过调节加热器的功率和冷却器的温度,以及调节蒸馏器的压力来实现这一点。
此外,还需要对混合物中的组分进行密度和沸点的测定,以便确定具体的蒸馏条件。
常减压蒸馏工艺可以应用于各种化工生产过程中,例如石油化工、制药工业和食品加工等。
通过合理的操作和控制,可以实现对混合物中各种组分的高效分离和提纯,从而得到高质量的产品。
总的来说,常减压蒸馏工艺是一种十分重要的化工分离技术,它在工业生产中有着广泛的应用。
仔细掌握其工艺流程和操作要点,将有助于提高生产效率和产品质量,从而为企业创造更大的经济价值。
常减压蒸馏工艺流程常减压工艺流程的原理
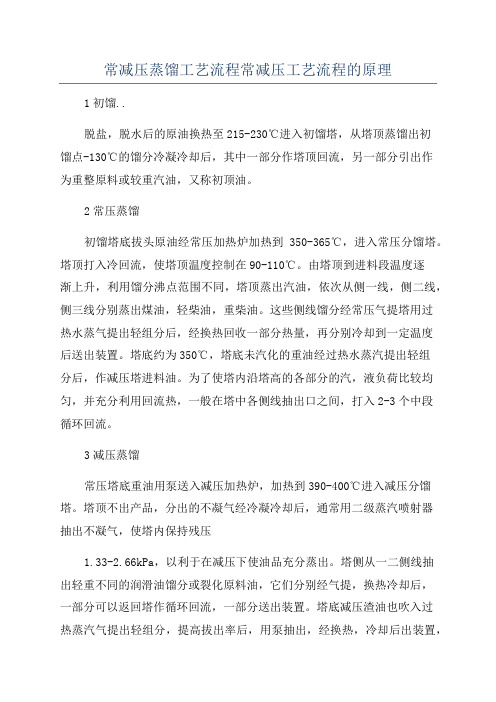
常减压蒸馏工艺流程常减压工艺流程的原理1初馏..脱盐,脱水后的原油换热至215-230℃进入初馏塔,从塔顶蒸馏出初馏点-130℃的馏分冷凝冷却后,其中一部分作塔顶回流,另一部分引出作为重整原料或较重汽油,又称初顶油。
2常压蒸馏初馏塔底拔头原油经常压加热炉加热到350-365℃,进入常压分馏塔。
塔顶打入冷回流,使塔顶温度控制在90-110℃。
由塔顶到进料段温度逐渐上升,利用馏分沸点范围不同,塔顶蒸出汽油,依次从侧一线,侧二线,侧三线分别蒸出煤油,轻柴油,重柴油。
这些侧线馏分经常压气提塔用过热水蒸气提出轻组分后,经换热回收一部分热量,再分别冷却到一定温度后送出装置。
塔底约为350℃,塔底未汽化的重油经过热水蒸汽提出轻组分后,作减压塔进料油。
为了使塔内沿塔高的各部分的汽,液负荷比较均匀,并充分利用回流热,一般在塔中各侧线抽出口之间,打入2-3个中段循环回流。
3减压蒸馏常压塔底重油用泵送入减压加热炉,加热到390-400℃进入减压分馏塔。
塔顶不出产品,分出的不凝气经冷凝冷却后,通常用二级蒸汽喷射器抽出不凝气,使塔内保持残压1.33-2.66kPa,以利于在减压下使油品充分蒸出。
塔侧从一二侧线抽出轻重不同的润滑油馏分或裂化原料油,它们分别经气提,换热冷却后,一部分可以返回塔作循环回流,一部分送出装置。
塔底减压渣油也吹入过热蒸汽气提出轻组分,提高拔出率后,用泵抽出,经换热,冷却后出装置,可以作为自用燃料或商品燃料油,也可以作为沥青原料或丙烷脱沥青装置的原料,进一步生产重质润滑油和沥青。
(1)认真巡回检查。
及时发现和消除炉、塔、贮槽等设备管线的跑、冒、滴、漏。
禁止乱排乱放各种油品和可燃气体,防止火灾发生。
(2)常减压蒸馏过程中许多高温油品一旦泄漏,遇空气会立即自燃着火,火灾危险很大。
造成热油跑料着火的原因主要有:①法兰垫刺开跑料;②年久腐蚀漏油;③液面计、热电偶套管等漏油着火;④原油含水多,塔内压力过高,安全阀起跳喷油着火;⑤减压操作不当,空气进入减压塔内引起火灾爆炸;⑥压力过大,造成爆炸着火;⑦压力和真空度剧烈变化引起漏油等。
常减压蒸馏的工艺流程
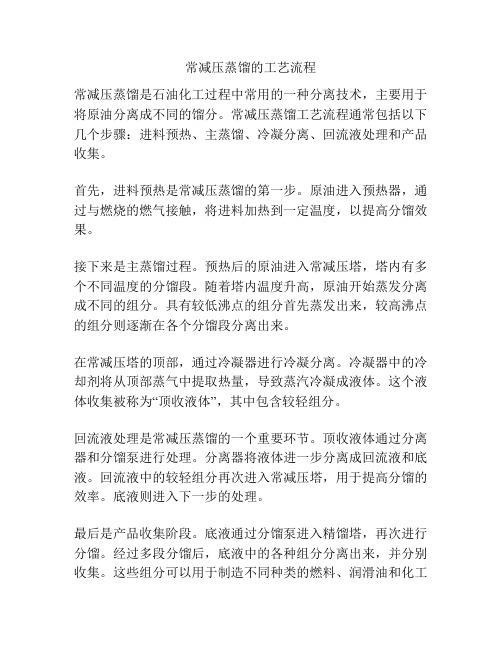
常减压蒸馏的工艺流程
常减压蒸馏是石油化工过程中常用的一种分离技术,主要用于将原油分离成不同的馏分。
常减压蒸馏工艺流程通常包括以下几个步骤:进料预热、主蒸馏、冷凝分离、回流液处理和产品收集。
首先,进料预热是常减压蒸馏的第一步。
原油进入预热器,通过与燃烧的燃气接触,将进料加热到一定温度,以提高分馏效果。
接下来是主蒸馏过程。
预热后的原油进入常减压塔,塔内有多个不同温度的分馏段。
随着塔内温度升高,原油开始蒸发分离成不同的组分。
具有较低沸点的组分首先蒸发出来,较高沸点的组分则逐渐在各个分馏段分离出来。
在常减压塔的顶部,通过冷凝器进行冷凝分离。
冷凝器中的冷却剂将从顶部蒸气中提取热量,导致蒸汽冷凝成液体。
这个液体收集被称为“顶收液体”,其中包含较轻组分。
回流液处理是常减压蒸馏的一个重要环节。
顶收液体通过分离器和分馏泵进行处理。
分离器将液体进一步分离成回流液和底液。
回流液中的较轻组分再次进入常减压塔,用于提高分馏的效率。
底液则进入下一步的处理。
最后是产品收集阶段。
底液通过分馏泵进入精馏塔,再次进行分馏。
经过多段分馏后,底液中的各种组分分离出来,并分别收集。
这些组分可以用于制造不同种类的燃料、润滑油和化工
产品等。
总的来说,常减压蒸馏是一种重要的分离技术,广泛应用于石油化工行业。
通过进料预热、主蒸馏、冷凝分离、回流液处理和产品收集等步骤,可以将原油分离成不同的组分,从而获得具有不同属性的产品。
这种工艺流程能够有效地减压蒸馏原油,提高产品的纯度和品质,满足人们对燃料和化工产品的需求。
简述常减压蒸馏工艺流程
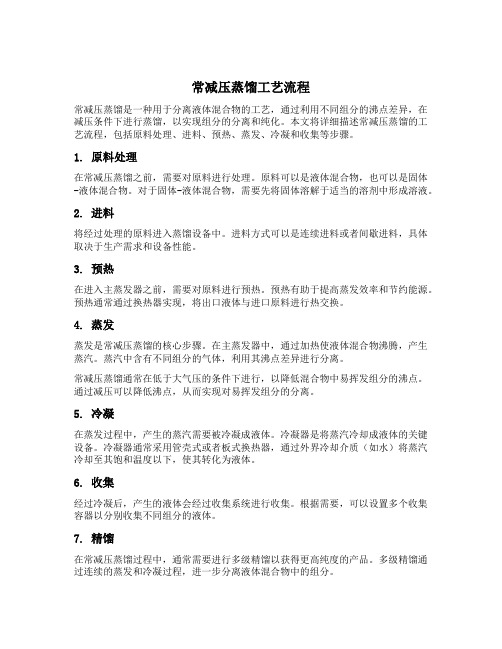
常减压蒸馏工艺流程常减压蒸馏是一种用于分离液体混合物的工艺,通过利用不同组分的沸点差异,在减压条件下进行蒸馏,以实现组分的分离和纯化。
本文将详细描述常减压蒸馏的工艺流程,包括原料处理、进料、预热、蒸发、冷凝和收集等步骤。
1. 原料处理在常减压蒸馏之前,需要对原料进行处理。
原料可以是液体混合物,也可以是固体-液体混合物。
对于固体-液体混合物,需要先将固体溶解于适当的溶剂中形成溶液。
2. 进料将经过处理的原料进入蒸馏设备中。
进料方式可以是连续进料或者间歇进料,具体取决于生产需求和设备性能。
3. 预热在进入主蒸发器之前,需要对原料进行预热。
预热有助于提高蒸发效率和节约能源。
预热通常通过换热器实现,将出口液体与进口原料进行热交换。
4. 蒸发蒸发是常减压蒸馏的核心步骤。
在主蒸发器中,通过加热使液体混合物沸腾,产生蒸汽。
蒸汽中含有不同组分的气体,利用其沸点差异进行分离。
常减压蒸馏通常在低于大气压的条件下进行,以降低混合物中易挥发组分的沸点。
通过减压可以降低沸点,从而实现对易挥发组分的分离。
5. 冷凝在蒸发过程中,产生的蒸汽需要被冷凝成液体。
冷凝器是将蒸汽冷却成液体的关键设备。
冷凝器通常采用管壳式或者板式换热器,通过外界冷却介质(如水)将蒸汽冷却至其饱和温度以下,使其转化为液体。
6. 收集经过冷凝后,产生的液体会经过收集系统进行收集。
根据需要,可以设置多个收集容器以分别收集不同组分的液体。
7. 精馏在常减压蒸馏过程中,通常需要进行多级精馏以获得更高纯度的产品。
多级精馏通过连续的蒸发和冷凝过程,进一步分离液体混合物中的组分。
多级精馏中,可以设置多个塔板或者填料层来增加接触面积,并利用液体和蒸汽之间的传质传热过程进行分离。
8. 废料处理在常减压蒸馏过程中,会产生一些废料。
这些废料可能包含有毒、有害或者不需要的组分。
为了环境保护和资源利用,废料需要经过相应的处理和处置。
废料处理可以包括中和、沉淀、过滤、焚烧等步骤,以确保废料的安全处理和环境友好。
3常减压蒸馏

(二)原油脱酸的机理
由于原油中的环烷酸为油溶性,用一般的方法难以脱除,通过向原油中加入适当的中和剂及增溶剂,使原油中的环烷酸和其他酸与中和剂反应,将其先转化为水溶性或亲水的化合物即生成盐进人溶剂相及水相,在破乳剂的共同作用下,在一定的电场强度和温度下将原油中的环烷酸除去。环烷酸脱除及回收的流程示意图如图3-4所示。
第三章 原油蒸馏过程
第一节 概述
原油是极其复杂的混合物,通过原油的蒸馏可以按所制定的产品方案将其分割成直馏汽油、煤油、轻柴油或重柴油馏分及各种润滑油馏分和渣油等。原油蒸馏是石油加工中第一道不可少的工序,故通常称原油蒸馏为一次加工,其他加工工序则称为二次加工。蒸馏过程得到的这些半成品经过适当的精制和调合便成为合格的产品,也可以按不同的生产方案分割出一些二次加工过程所用的原料,如重整原料、催化裂化原料、加氢裂化原料等,以便进一步提高轻质油的产率或改善产品质量。
5原油脱酸温度
原油粘度降低,油水界面张力减小,水滴膨胀使乳化膜强度减弱。水滴热运动增加,碰撞结合机会增多,乳化剂在油中溶解度增加,所有这些均导致原油中乳化水滴破乳聚结,有利于脱酸。合适的脱酸温度为110~130℃。
6 注水量
原油注水的目的是为了溶解油中的环烷酸盐类,从而使其随着水分的脱除而脱除,因此,注水量的选择非常关键,太大会导致脱盐电耗增加,甚至跳闸,造成脱后含水高,太小则不能将油中的环烷酸盐洗除。
使用中和剂时,随着中和剂用量的增大,中和率的提高,原油乳化程度加重,如果采用一些性能优良的破乳剂,可以有助于原油破乳脱水。因此,需要选择合适的破乳剂。
- 1、下载文档前请自行甄别文档内容的完整性,平台不提供额外的编辑、内容补充、找答案等附加服务。
- 2、"仅部分预览"的文档,不可在线预览部分如存在完整性等问题,可反馈申请退款(可完整预览的文档不适用该条件!)。
- 3、如文档侵犯您的权益,请联系客服反馈,我们会尽快为您处理(人工客服工作时间:9:00-18:30)。
复合塔
恒分子流假设不能成立
原因:
(1)侧线抽出
(2)分子汽化潜热相差很大
( 3 ) 全 塔 温 度 梯 度 大 : 塔 底 300℃, 塔 顶
100℃
节能措施
210 两塔 三塔:初馏塔温度低( ~ 250C),拔出轻汽油馏分 初馏塔侧线 常压塔液相回流 中段回流:合理利用高 温位热量(代价:分离 效果变差) 凝量 顶循回流:减少塔顶冷 改进流程(根本) 减少水蒸气用量:采用 干式减压蒸馏 减少工艺用能 条件:分离要求低、阻 力降低 方法:提高真空度( ~ 20m m Hg 10 ) 措施:用填料塔代替板 式塔,以降低塔板压降 ; 用机械真空泵代替蒸汽 喷射器 不一步到位 加强换热网络优化 开发低温余热利用,提 高热回收率 60 加热炉: % 90% 提高设备效率 换热效率 减少热损失
石油常减压蒸馏过程
一、概述 ——“龙头”
原理:蒸馏 目的:准备原料 要求:最大限度地节约能源
二、 常减压流程
原 脱 、 水 油 盐 脱
三、石油常减压的主要特点
1. 产品大多由塔顶及侧线采出(一般化工分离塔 n个组份需n-1个塔) 2. 无塔底再沸器,塔内只有精馏段,无提馏段, 提馏用汽提代替 3. 复合塔:简化生产 4. 恒分子流假设不能成立 5. 气液负荷不均 6. 处理能力大
合理设计精馏塔,增加塔板,平稳操作 l 提高拔出率(切割深度):主要是针对减压塔 关键:提高真空度; 优化操作; 加入添加剂; 改变油的分散状态
四、原油加工方案对常减压装置的影响
1. 燃料型
2. 润滑油型
3. 化工型
燃料型
润滑油型
化工型
五பைடு நூலகம் 技术进展
1. 防腐蚀
2. 提高拔出率与分馏精度
3. 节能降耗
防腐蚀
腐蚀源:无机盐、硫化物、有机酸
措施:“一脱四注:
——脱盐、注碱、注中和剂、注缓蚀剂、注水
提高拔出率与分馏精度
合理解决好提高拔出率与分馏精度的矛盾 l 提高常压塔分离精度的方法