直缝埋弧焊钢管焊缝横向裂纹产生原因分析
焊缝横向裂纹产生的原因和解决方法
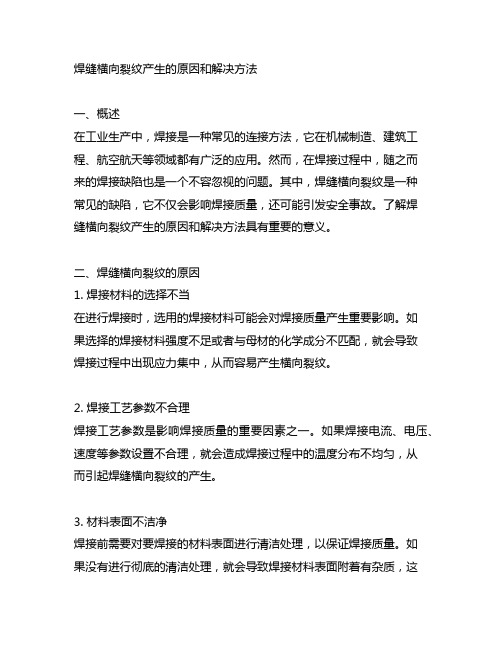
焊缝横向裂纹产生的原因和解决方法一、概述在工业生产中,焊接是一种常见的连接方法,它在机械制造、建筑工程、航空航天等领域都有广泛的应用。
然而,在焊接过程中,随之而来的焊接缺陷也是一个不容忽视的问题。
其中,焊缝横向裂纹是一种常见的缺陷,它不仅会影响焊接质量,还可能引发安全事故。
了解焊缝横向裂纹产生的原因和解决方法具有重要的意义。
二、焊缝横向裂纹的原因1. 焊接材料的选择不当在进行焊接时,选用的焊接材料可能会对焊接质量产生重要影响。
如果选择的焊接材料强度不足或者与母材的化学成分不匹配,就会导致焊接过程中出现应力集中,从而容易产生横向裂纹。
2. 焊接工艺参数不合理焊接工艺参数是影响焊接质量的重要因素之一。
如果焊接电流、电压、速度等参数设置不合理,就会造成焊接过程中的温度分布不均匀,从而引起焊缝横向裂纹的产生。
3. 材料表面不洁净焊接前需要对要焊接的材料表面进行清洁处理,以保证焊接质量。
如果没有进行彻底的清洁处理,就会导致焊接材料表面附着有杂质,这些杂质会影响焊接的质量,增加裂纹的产生可能性。
4. 焊接残余应力在焊接过程中,由于温度的变化和热量的不均匀分布,容易产生残余应力。
这些残余应力会导致焊接部位的局部变形,最终导致焊缝横向裂纹的产生。
5. 设计缺陷在一些情况下,焊接工件的设计本身存在缺陷,比如焊缝的设计不合理、板材的厚度悬殊等,都会增加焊缝横向裂纹的发生。
三、焊缝横向裂纹的解决方法1. 优化焊接材料的选择在进行焊接前,需对焊接材料进行严格的选择,确保其与母材的化学成分匹配,且具有足够的强度。
对于使用对焊材料的情况,需要对搭铁焊接材和母材的化学成分及性能进行检测。
2. 合理设置焊接工艺参数合理设置焊接工艺参数是避免焊缝横向裂纹产生的重要手段。
在进行焊接前,需要根据具体的情况合理地设置焊接电流、电压、速度等参数,确保温度的均匀分布和焊接的质量。
3. 加强材料表面清洁处理在进行焊接前,需要对焊接材料表面进行严格的清洁处理。
直缝埋弧焊钢管焊缝横向裂纹产生原因分析
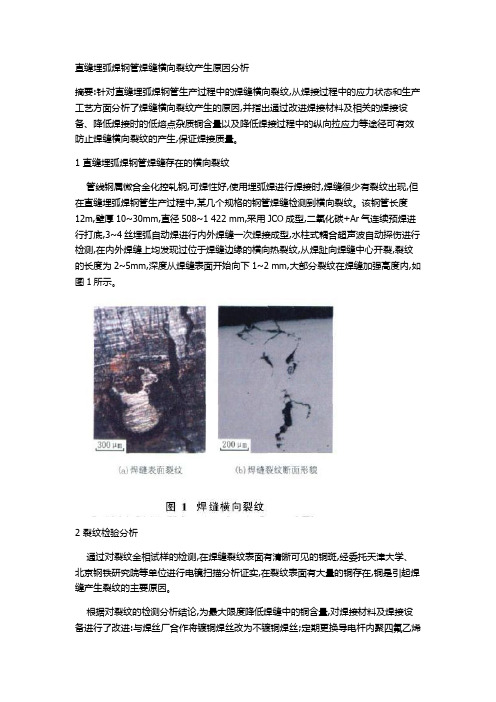
直缝埋弧焊钢管焊缝横向裂纹产生原因分析摘要:针对直缝埋弧焊钢管生产过程中的焊缝横向裂纹,从焊接过程中的应力状态和生产工艺方面分析了焊缝横向裂纹产生的原因,并指出通过改进焊接材料及相关的焊接设备、降低焊接时的低熔点杂质铜含量以及降低焊接过程中的纵向拉应力等途径可有效防止焊缝横向裂纹的产生,保证焊接质量。
1 直缝埋弧焊钢管焊缝存在的横向裂纹管线钢属微合金化控轧钢,可焊性好,使用埋弧焊进行焊接时,焊缝很少有裂纹出现,但在直缝埋弧焊钢管生产过程中,某几个规格的钢管焊缝检测到横向裂纹。
该钢管长度12m,壁厚10~30mm,直径508~1 422 mm,采用JCO成型,二氧化碳+Ar气连续预焊进行打底,3~4丝埋弧自动焊进行内外焊缝一次焊接成型,水柱式耦合超声波自动探伤进行检测,在内外焊缝上均发现过位于焊缝边缘的横向热裂纹,从焊趾向焊缝中心开裂,裂纹的长度为2~5mm,深度从焊缝表面开始向下1~2 mm,大部分裂纹在焊缝加强高度内,如图1所示。
2 裂纹检验分析通过对裂纹金相试样的检测,在焊缝裂纹表面有清晰可见的铜斑,经委托天津大学、北京钢铁研究院等单位进行电镜扫描分析证实,在裂纹表面有大量的铜存在,铜是引起焊缝产生裂纹的主要原因。
根据对裂纹的检测分析结论,为最大限度降低焊缝中的铜含量,对焊接材料及焊接设备进行了改进:与焊丝厂合作将镀铜焊丝改为不镀铜焊丝;定期更换导电杆内聚四氟乙烯软管,防止导电杆磨损;改用硬质合金导电嘴,减少导电嘴因磨损产生的铜屑;使用新焊剂并定期清理焊接机头等。
采用以上措施后,焊缝横向裂纹的数量明显减少,但仍有少量的裂纹产生。
3焊接应力状态对产生裂纹的影响从理论上分析,引起焊缝热裂纹的原因有两点:一是低熔点杂质,二是焊接过程中的拉应力。
将低熔点杂质铜的来源降到最低后仍有裂纹产生,需要从焊接应力方面寻找解决办法。
钢管生产过程中出现的焊缝横向裂纹的统计情况表明,裂纹的分布规律是:薄壁管和厚壁管较少、中间壁厚(12~16mm)较多;大管径较少,小焊管管径较多。
焊接裂纹产生原因及防治措施

以下为焊接裂纹产生原因及防治措施,一起来看看吧。
1、焊接裂纹的现象在焊缝或近缝区,由于焊接的影响,材料的原子结合遭到破坏,形成新的界面而产生的缝隙称为焊接裂缝,它具有缺口尖锐和长宽比大的特征。
按产生时的温度和时间的不同,裂纹可分为:热裂纹、冷裂纹、应力腐蚀裂纹和层状撕裂。
在焊接生产中,裂纹产生的部位有很多。
有的裂纹出现在焊缝表面,肉眼就能观察到;有的隐藏在焊缝内部,通过探伤检查才能发现;有的产生在焊缝上;有的则产生在热影响区内。
值得注意的是,裂纹有时在焊接过程中产生,有时在焊件焊后放置或运行一段时间之后才出现,后一种称为延迟裂纹,这种裂纹的危害性更为严重。
2、焊接裂纹的危害焊接裂缝是一种危害大的缺陷,除了降低焊接接头的承载能力,还因裂缝末端的尖锐缺口将引起严重的应力集中,促使裂缝扩展,最终会导致焊接结构的破坏,使产品报废,甚至会引起严重的事故。
通常,在焊接接头中,裂缝是一种不允许存在的缺陷。
一旦发现即应彻底清除,进行返修焊接。
3、焊接裂纹的产生原因及防治措施由于不同裂缝的产生原因和形成机理不同,下面就热裂缝、冷裂缝和再热裂缝三类分别予以讨论。
3.1、热裂纹热裂缝一般是指高温下(从凝固温度范围附近至铁碳平衡图上的A3线以上温度)所产生的裂纹,又称高温裂缝或结晶裂缝。
热裂缝通常在焊缝内产生,有时也可能出现在热影响区。
原因:由于焊接熔池在结晶过程中存在着偏析现象,低熔点共晶和杂质在结晶过程中以液态间层存在形成偏析,凝固以后强度也较低,当焊接应力足够大时,就会将液态间层或刚凝固不久的固态金属拉开形成裂缝。
此外,如果母材的晶界上也存在有低熔点共晶和杂质,则在加热温度超过其熔点的热影响区,这些低熔点化合物将熔化而形成液态间层,当焊接拉应力足够大时,也会被拉开而形成热影响区液化裂缝。
总之,热裂缝的产生是冶金因素和力学因素综合作用的结果。
防治措施:防止产生热裂缝的措施,可以从冶金因素和力学因素两个方面入手。
控制母材及焊材有害元素、杂质含量限制母材及焊接材料(包括焊条、焊丝、焊剂和保护气体)中易偏析元素及有害杂质的含量。
直缝埋弧焊管横向裂纹探伤分析
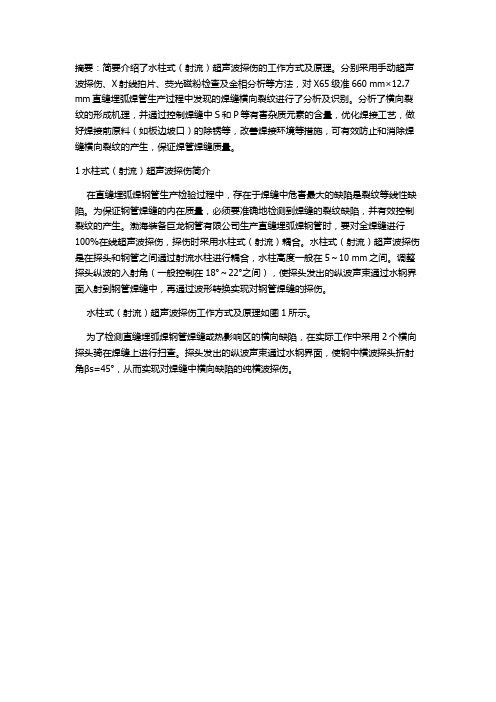
摘要:简要介绍了水柱式(射流)超声波探伤的工作方式及原理。
分别采用手动超声波探伤、X射线拍片、荧光磁粉检查及金相分析等方法,对X65级准660 mm×12.7 mm直缝埋弧焊管生产过程中发现的焊缝横向裂纹进行了分析及识别。
分析了横向裂纹的形成机理,并通过控制焊缝中S和P等有害杂质元素的含量,优化焊接工艺,做好焊接前原料(如板边坡口)的除锈等,改善焊接环境等措施,可有效防止和消除焊缝横向裂纹的产生,保证焊管焊缝质量。
1水柱式(射流)超声波探伤简介在直缝埋弧焊钢管生产检验过程中,存在于焊缝中危害最大的缺陷是裂纹等线性缺陷。
为保证钢管焊缝的内在质量,必须要准确地检测到焊缝的裂纹缺陷,并有效控制裂纹的产生。
渤海装备巨龙钢管有限公司生产直缝埋弧焊钢管时,要对全焊缝进行100%在线超声波探伤,探伤时采用水柱式(射流)耦合。
水柱式(射流)超声波探伤是在探头和钢管之间通过射流水柱进行耦合,水柱高度一般在5~10 mm之间。
调整探头纵波的入射角(一般控制在18°~22°之间),使探头发出的纵波声束通过水钢界面入射到钢管焊缝中,再通过波形转换实现对钢管焊缝的探伤。
水柱式(射流)超声波探伤工作方式及原理如图1所示。
为了检测直缝埋弧焊钢管焊缝或热影响区的横向缺陷,在实际工作中采用2个横向探头骑在焊缝上进行扫查。
探头发出的纵波声束通过水钢界面,使钢中横波探头折射角βs=45°,从而实现对焊缝中横向缺陷的纯横波探伤。
2 超声波自动探伤时发现的问题对X65级准660 mm×12.7 mm直缝埋弧焊管焊缝进行超声波自动探伤时,连探横向探头报警,连探图形显示横向缺陷,如图2所示。
此类缺陷有以下特点:①缺陷在扩径、水压前的1#超声波自动探伤检测过程中被发现,表明该缺陷在焊接后就已存在;②在检测焊缝内表面时,横向探头发现该缺陷,缺陷波形独立并超出报警极限;③受此类缺陷自身深度或角度以及透照方向的影响,X射线拍片有时能发现,但拍出的底片影像模糊,失去缺陷的基本特征。
弧焊开裂的原因
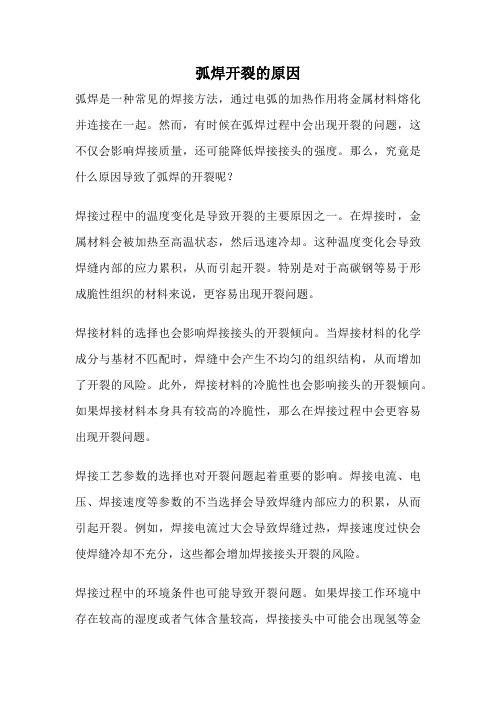
弧焊开裂的原因弧焊是一种常见的焊接方法,通过电弧的加热作用将金属材料熔化并连接在一起。
然而,有时候在弧焊过程中会出现开裂的问题,这不仅会影响焊接质量,还可能降低焊接接头的强度。
那么,究竟是什么原因导致了弧焊的开裂呢?焊接过程中的温度变化是导致开裂的主要原因之一。
在焊接时,金属材料会被加热至高温状态,然后迅速冷却。
这种温度变化会导致焊缝内部的应力累积,从而引起开裂。
特别是对于高碳钢等易于形成脆性组织的材料来说,更容易出现开裂问题。
焊接材料的选择也会影响焊接接头的开裂倾向。
当焊接材料的化学成分与基材不匹配时,焊缝中会产生不均匀的组织结构,从而增加了开裂的风险。
此外,焊接材料的冷脆性也会影响接头的开裂倾向。
如果焊接材料本身具有较高的冷脆性,那么在焊接过程中会更容易出现开裂问题。
焊接工艺参数的选择也对开裂问题起着重要的影响。
焊接电流、电压、焊接速度等参数的不当选择会导致焊缝内部应力的积累,从而引起开裂。
例如,焊接电流过大会导致焊缝过热,焊接速度过快会使焊缝冷却不充分,这些都会增加焊接接头开裂的风险。
焊接过程中的环境条件也可能导致开裂问题。
如果焊接工作环境中存在较高的湿度或者气体含量较高,焊接接头中可能会出现氢等金属元素的吸收,进而引起氢脆性开裂。
因此,在焊接过程中要注意保持焊接环境的干燥和清洁。
焊接过程中的焊接顺序和焊接方式也会对开裂问题产生影响。
如果焊接顺序不合理,焊缝内的应力可能无法得到充分的释放,从而导致开裂。
同时,焊接方式的选择也应根据具体情况进行调整,以减少焊接接头的应力集中,进而降低开裂的风险。
弧焊开裂的原因主要包括焊接温度变化、焊接材料选择、焊接工艺参数、环境条件和焊接顺序、焊接方式等多个方面。
为了避免开裂问题的发生,我们应该在焊接过程中注意控制焊接温度,选择合适的焊接材料,合理选择焊接工艺参数,保持良好的焊接环境,合理安排焊接顺序和选择适当的焊接方式。
通过这些措施的综合应用,可以有效降低弧焊开裂的风险,提高焊接接头的质量和强度。
直缝埋弧焊管常见缺陷产生原因及预防措施

我国自西气东输以来大口径直缝埋弧焊管的用量就不断开始攀升,各个生产线也相继投入生产。
有资料显示我国的大口径直缝埋弧焊管年生产量已超过500万吨,存在产能过剩的现象,而其中很多都属于低端产品,总体质量亟待提升[1]。
关乎直缝埋弧焊管质量的标准主要有两个,就是钢管的理化性能和是否存在缺陷,理化性能主要由钢板、焊丝和焊剂以及相关生产工艺决定,之后再进行专业的理化性能检测;而钢管的缺陷与钢板质量和焊材质量以及生产设备相关。
缺陷会引发应力集中从而降低钢管的使用寿命,甚至有可能出现泄漏或爆炸。
文章旨在研究钢管的生产质量,对常见缺陷进行分析,从而找到相应的预防措施,以期更进一步提升目前的钢管质量。
1 外部可视的常见缺陷钢管的外部可视缺陷主要包括以下几种。
其一,不够笔直,指的是钢管存在弯曲现象。
主要由直缝埋弧焊管在单侧焊缝后导致、或是钢管在扩径时存在受力不均匀、亦或者是水压时应力与钢管的屈服度之间存在较大差异。
其二,椭圆,指钢管存在不规则圆形,原因:钢管成型参数和扩径参数存在不合理现象。
其三,内翻或外翻,指钢管的轮廓线存在局部误差,出现内翻或是外翻现象。
原因:钢管的预弯或者成型曲率存在不合理。
其四,压坑,指钢管外部存在外物导致的凹形痕迹。
原因:钢板铣边、成型和预弯以及扩径中可能有铣屑或异物进入。
其五,划伤,指钢管表面存在较深的划痕。
原因:钢板运输时误伤、生产过程中在纵向或横向时有尖锐异物出现。
其六,摩擦伤痕,表现为中间较深而两侧较浅的划痕,偶尔会对称出现。
产生原因为输送时辊道转动所导致。
2 焊接常见缺陷(1)咬边。
咬边指焊缝金属在靠近焊趾母材时造成的卡槽或未填满现象。
原因:焊接时熔池受力出现异常所导致。
预防措施主要为保证熔池的热量供应、通过调节送丝系统和焊接工艺参数来确保电弧处于稳定状态、让焊接坡口处于平焊状态、查找外力源并将其消除;还需要让焊丝轴线和坡口横截面处于垂直状态或者是选用细丝来焊接,尽可能减少其他磁场带来的干扰。
埋弧焊纵焊缝终端裂纹原因分析及预防措施(正式)

埋弧焊纵焊缝终端裂纹原因分析及预防措施(正式)Deploy The Objectives, Requirements And Methods To Make The Personnel In The Organization Operate According To The Established Standards And Reach The Expected Level.编订:__________________单位:__________________时间:__________________Word格式 / 完整 / 可编辑文件编号:KG-AO-7530-73 埋弧焊纵焊缝终端裂纹原因分析及预防措施(正式)使用备注:本文档可用在日常工作场景,通过对目的、要求、方式、方法、进度等进行具体、周密的部署,从而使得组织内人员按照既定标准、规范的要求进行操作,使日常工作或活动达到预期的水平。
下载后就可自由编辑。
一、概述在压力容器制造中,当采用埋弧焊焊接筒体纵焊缝时,经常会在纵焊缝的端部或靠近端部处产生裂纹(以下简称终端裂纹)。
对此问题已有不少人进行了研究,认为产生终端裂纹的主要原因是当焊接电弧接近纵焊缝终端时,焊缝在沿轴向膨胀变形的同时,还伴随有垂直轴向方向的横向张开变形;而筒体在卷制及制作装配过程中也存在着冷作硬化应力和组装应力;在焊接过程中,因终端定位焊缝及引弧板的拘束作用,在焊缝终端产生较大的拉伸应力;当电弧移动到终端定位焊缝和引弧板上时,由于该部位受热膨胀变形,使焊缝终端的横向拉伸应力得到松弛,拘束力减小,便使焊缝终端刚刚凝固的焊缝金属受到较大的拉应力而形成终端裂纹。
根据上述原因分析提出了两项解决的对策:一是增加引弧板的宽度以增加其拘束力;二是采用开槽的弹性拘束引弧板。
但是我们在实践中采取上述对策后,问题还是没有得到有效解决:如虽然采用了弹性拘束引弧板,但仍然会产生纵焊缝的终端裂纹,且在焊接厚度较小,钢性较小而经强制装配的筒体时也常有终端裂纹发生等;然而,当在筒体纵焊缝的延长部位带有产品试板时,虽然定位焊等情况与未带产品试板时相同,却很少产生纵缝产生终端裂纹。
焊缝横向裂纹产生的原因和解决方法
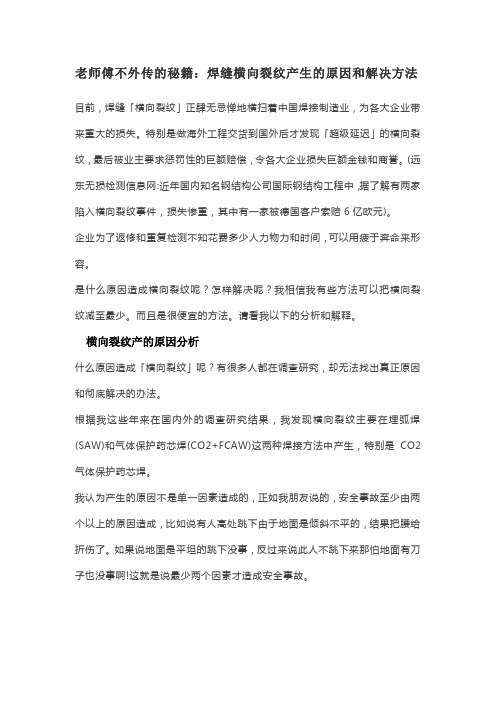
老师傅不外传的秘籍:焊缝横向裂纹产生的原因和解决方法目前,焊缝「横向裂纹」正肆无忌惮地横扫着中国焊接制造业,为各大企业带来重大的损失。
特别是做海外工程交货到国外后才发现「超级延迟」的横向裂纹,最后被业主要求惩罚性的巨额赔偿,令各大企业损失巨额金钱和商誉。
(远东无损检测信息网:近年国内知名钢结构公司国际钢结构工程中,据了解有两家陷入横向裂纹事件,损失惨重,其中有一家被德国客户索赔6亿欧元)。
企业为了返修和重复检测不知花费多少人力物力和时间,可以用疲于奔命来形容。
是什么原因造成横向裂纹呢?怎样解决呢?我相信我有些方法可以把横向裂纹减至最少。
而且是很便宜的方法。
请看我以下的分析和解释。
横向裂纹产的原因分析什么原因造成「横向裂纹」呢?有很多人都在调查研究,却无法找出真正原因和彻底解决的办法。
根据我这些年来在国内外的调查研究结果,我发现横向裂纹主要在埋弧焊(SAW)和气体保护药芯焊(CO2+FCAW)这两种焊接方法中产生,特别是CO2气体保护药芯焊。
我认为产生的原因不是单一因素造成的,正如我朋友说的,安全事故至少由两个以上的原因造成,比如说有人高处跳下由于地面是倾斜不平的,结果把腰给折伤了。
如果说地面是平坦的跳下没事,反过来说此人不跳下来那怕地面有刀子也没事啊!这就是说最少两个因素才造成安全事故。
横向裂纹则何止两个因素,它是多种因素造成的,我觉得用癌症的癌字来比喻横向裂纹最恰当。
我们的老祖宗在创造这个癌字时就告诉我们,癌症的癌字本身就是个病,它是由三个口吃进大量的毒素堆积如山才形成癌症的。
横向裂纹在我们常规的焊接中是很少见的,例如:气孔、夹渣、未熔合、咬边等是常见的,好象我们经常会有点伤风感冒和拉肚子;偶尔也会出现纵向裂纹和焊趾边冷裂纹,也像我们在体育运动时不小心发生断手断脚的意外,这也是容易理解和防范的,而癌症是很少见的,但是见到它时已经是为时已晚了,判若死刑了几乎是没得救了。
横向裂纹也像癌细胞会扩散转移一样,返修时真是越修越裂,跟着气刨跑,遍地开花没办法修理。
- 1、下载文档前请自行甄别文档内容的完整性,平台不提供额外的编辑、内容补充、找答案等附加服务。
- 2、"仅部分预览"的文档,不可在线预览部分如存在完整性等问题,可反馈申请退款(可完整预览的文档不适用该条件!)。
- 3、如文档侵犯您的权益,请联系客服反馈,我们会尽快为您处理(人工客服工作时间:9:00-18:30)。
直缝埋弧焊钢管焊缝横向裂纹产生原因分析
摘要:针对直缝埋弧焊钢管生产过程中的焊缝横向裂纹,从焊接过程中的应力状态和生产工艺方面分析了焊缝横向裂纹产生的原因,并指出通过改进焊接材料及相关的焊接设备、降低焊接时的低熔点杂质铜含量以及降低焊接过程中的纵向拉应力等途径可有效防止焊缝横向裂纹的产生,保证焊接质量。
1 直缝埋弧焊钢管焊缝存在的横向裂纹
管线钢属微合金化控轧钢,可焊性好,使用埋弧焊进行焊接时,焊缝很少有裂纹出现,但在直缝埋弧焊钢管生产过程中,某几个规格的钢管焊缝检测到横向裂纹。
该钢管长度12m,壁厚10~30mm,直径508~1 422 mm,采用JCO成型,二氧化碳+Ar气连续预焊进行打底,3~4丝埋弧自动焊进行内外焊缝一次焊接成型,水柱式耦合超声波自动探伤进行检测,在内外焊缝上均发现过位于焊缝边缘的横向热裂纹,从焊趾向焊缝中心开裂,裂纹的长度为2~5mm,深度从焊缝表面开始向下1~2 mm,大部分裂纹在焊缝加强高度内,如图1所示。
2 裂纹检验分析
通过对裂纹金相试样的检测,在焊缝裂纹表面有清晰可见的铜斑,经委托天津大学、北京钢铁研究院等单位进行电镜扫描分析证实,在裂纹表面有大量的铜存在,铜是引起焊缝产生裂纹的主要原因。
根据对裂纹的检测分析结论,为最大限度降低焊缝中的铜含量,对焊接材料及焊接设备进行了改进:与焊丝厂合作将镀铜焊丝改为不镀铜焊丝;定期更换导电杆内聚四氟乙烯
软管,防止导电杆磨损;改用硬质合金导电嘴,减少导电嘴因磨损产生的铜屑;使用新焊剂并定期清理焊接机头等。
采用以上措施后,焊缝横向裂纹的数量明显减少,但仍有少量的裂纹产生。
3焊接应力状态对产生裂纹的影响
从理论上分析,引起焊缝热裂纹的原因有两点:一是低熔点杂质,二是焊接过程中的拉应力。
将低熔点杂质铜的来源降到最低后仍有裂纹产生,需要从焊接应力方面寻找解决办法。
钢管生产过程中出现的焊缝横向裂纹的统计情况表明,裂纹的分布规律是:薄壁管和厚壁管较少、中间壁厚(12~16mm)较多;大管径较少,小焊管管径较多。
根据这个分布特点,对钢管焊接应力状态进行分析。
直缝埋弧焊管焊接时先进行预焊,再进行内焊,最后进行外焊。
对不同管径、不同壁厚钢管内焊时的焊接情况进行比较发现:薄壁管内焊时,焊缝背面红线呈亮白色;厚壁管内焊时,焊缝背面红线呈暗红色;中间壁厚管内焊时,焊缝背面红线亮度介于两者之间。
这种现象说明不同壁厚的钢管内焊时焊缝背面的温度有较大差异,这个差异将引起在钢管壁厚方向纵向应力分布状态不同。
钢管焊接时的应力分布与平板焊接时不同,钢管纵向焊接时由于受到管体的拘束,产生的纵向拉应力比平板焊接时大。
当焊缝冷却时,在不考虑环境温度影响的情况下,焊缝正面的冷却速度大于焊缝反面的冷却速度,当焊缝反面冷却到产生压缩塑性变形的温度区间时,反面的收缩将使焊缝正面产生弯曲变形,并在正面产生附加的纵向拉应力,若焊缝正面的温度仍处于固-液相间的脆性温度区间,则在双重拉应力的作用下焊缝可能产生横向裂纹,且由于弯曲变形的影响,越接近焊缝表面拉应力值越大,这也是横向裂纹出现在焊缝表面或加强焊缝内的主要原因。
影响拉应力大小的因素主要是焊接时焊缝正反两面最高温度和焊缝的冷却速度。
由于正面焊接熔池的温度远远高于金属的熔点,焊缝反面的温度远低于金属的熔点,冷却时焊缝正面的热量通过热传导的方式传递给反面,所以焊缝反面的冷却速度低于焊缝正面的冷却速度。
当焊缝反面的温度较高时,正反两面接近于同时伸缩,产生的纵向拉应力较小;当焊缝反面温度较低时,反面处于接近弹性变形状态,能够自由伸缩,产生的纵向拉应力也较小;当焊缝反面的温度处于中间区域时,产生的纵向拉应力较大,是比较容易产生横向裂纹的区间。
焊缝正反面冷却曲线如图2所示。
当焊缝反面温度高于T1低于T2时,焊缝反面的冷却温度曲线通过阴影部分即焊缝正面脆性温度区与焊缝背面塑性温度区相交的区域时,焊缝正面可能产生横向裂纹;当焊缝反面温度低于T1或高于T2时,焊缝反面的冷却温度曲线不通过阴影部分即脆性温度区与塑性温度区相交的区域时,焊缝正面不会产生横向裂纹。
当钢管的规格(如管径和壁厚)变化时,焊缝图2焊缝正反面冷却曲线示意图的冷却速度会改变,即图2中焊缝正面冷却曲线的斜率会改变。
当考虑环境温度时,由于内焊缝的辐射散发的热量散在钢管内部导致钢管内温度升高,而外表面的热量散在车间内,对环境温度的影响可以忽略,所以钢管实际焊接过程中内表面的冷却速度要略有减小。
在钢管管径和壁厚不变时,焊缝反面温度的高低与焊接线能量的大小、焊缝坡口尺寸有关(生产中使用的是X形坡口,带钝边)。
在相同条件下,线能量越大,焊缝反面的温度越高;线能量越小,焊缝反面的温度越低。
在其他条件相同时,焊缝坡口越深,反面温度越高;钝边越小,反面温度越高;反面坡口越深,反面温度越高。
4 避免横向裂纹的工艺措施
通过调整焊接工艺,改变焊接线能量的输入或改变坡口尺寸,如:减小内焊坡口和电流,使内焊时焊缝反面温度降低、红线变暗;加大外焊坡口和电流,使外焊时反面温度升高、红线变亮;加大钝边尺寸,使内焊时焊缝反面温度降低,外焊时加大电流使焊缝反面温度升高。
这样,既可以保证内外焊缝有足够的重合量,又可以降低焊接时焊缝正面的拉应力,避免横向裂纹的产生。
5 结论
直缝埋弧焊管的横向裂纹虽然尺寸较小,但存在较大的危害性,采取以下措施可有效防止焊缝横向裂纹的产生:(1)改进焊接材料及焊接设备,将焊接时的低熔点杂质铜含量
降到最低;(2)在制定钢管的焊接工艺时应充分考虑到钢管焊接时的特殊性,使焊缝反面的冷却温度曲线避开焊缝正面脆性温度区与焊缝反面塑性温度区相交的区域,以降低焊接过程中的纵向拉应力。