压铸模具技术标准及要求
压铸模具制造标准

压铸模具制造标准为规范模具制造,保证模具质量,特制定此标准一、总体要求:1、所有零件按二维图纸尺寸、技术要求制作,检验依据二维图纸2、 CNC加工采用按3D编程,相关公差按二维图要求制作3、组立组要按总装图要求组合模具及配模4、发现二维图纸少尺寸、3D与2D不符、制作中出错、安装干涉等情况,及时上报质量组和设计组,由设计组及时做出解决方案,并下发新资料。
质量组确认后,有新资料时电脑上错误资料第一时删除。
5、所有零件热处理按图纸要求操作、6、所有零件表面处理按图纸要求操作7、所有零件上机加工分中、打表规定,打表要求打长面复查短面,分中要求在毎面中心分中(中心误差超10mm),同时用量具复查尺寸。
二、模芯、滑块1、材材为H13或DIEVR2、模芯应图纸硬度要求,要淬火处理。
淬火会造成变形及材料内部硬度达到要求,制作工艺路线为粗加工、淬火、精加工、去应力回火(高温腐蚀会造成应力),才能达图纸3、开粗前外形保证六面垂直度0.1mm、平行度0.02mm以内,4、外形淬火前放精加工余量,外形按最长面来计算,规定如下:长度宽度300mm以内长宽均放1mm,厚放1.2MM。
300~500mm长宽均放1~1.5mm,厚放1.5MM。
500~800mm长宽均放1.5~2mm,厚放2MM。
800mm以上长宽均放2~2.5mm,厚放2.5MM。
5、CNC编程按图编制合理精粗程序,保证质量同时缩短加工时间,减少不必要空刀(采用分段加工)。
CNC操机员按程序参数全部开到100%,不得改度参数,有问题向编程员反映。
6、CNC开粗留单边留1~1.5mm,厚1.5~2MM的淬火后精加工余量,注意不能产生内清角(最小不得小于R2),与外形贯通的槽深不足30mm,宽不足60的不做保护措施,超过时要求两侧底角最小为R15或口部连筋,具体分析后确认。
反面倒角C7,4个R角、分流锥(留有效高度30mm)、料筒等反面台阶处辟空淬火前加工到位。
铝合金压铸技术要求
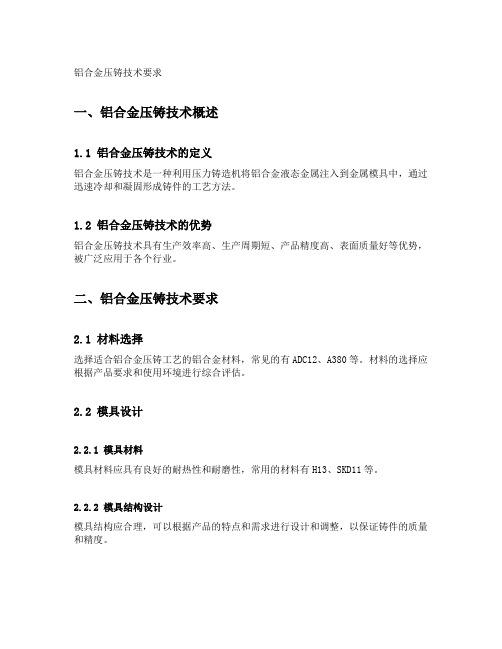
铝合金压铸技术要求一、铝合金压铸技术概述1.1 铝合金压铸技术的定义铝合金压铸技术是一种利用压力铸造机将铝合金液态金属注入到金属模具中,通过迅速冷却和凝固形成铸件的工艺方法。
1.2 铝合金压铸技术的优势铝合金压铸技术具有生产效率高、生产周期短、产品精度高、表面质量好等优势,被广泛应用于各个行业。
二、铝合金压铸技术要求2.1 材料选择选择适合铝合金压铸工艺的铝合金材料,常见的有ADC12、A380等。
材料的选择应根据产品要求和使用环境进行综合评估。
2.2 模具设计2.2.1 模具材料模具材料应具有良好的耐热性和耐磨性,常用的材料有H13、SKD11等。
2.2.2 模具结构设计模具结构应合理,可以根据产品的特点和需求进行设计和调整,以保证铸件的质量和精度。
2.3 注射设备2.3.1 压铸机选择根据产品的要求确定压铸机的型号和规格,包括锁力、注射压力等参数的选择。
2.3.2 注射系统注射系统包括注射缸、注射头、喷嘴等组成,其设计应合理,确保铝合金液态金属的注入和充填。
2.3.3 润滑系统润滑系统的设置对于铝合金压铸技术的稳定运行起着重要作用,应注意润滑剂的选择和使用。
2.4 工艺参数控制压铸工艺参数对于产品的质量和尺寸稳定性有很大的影响,应进行合理的控制和调整。
2.4.1 注射速度注射速度过快会导致铸件内部气孔、缺陷等问题,注射速度过慢会导致铝合金液态金属凝固不完全。
2.4.2 注射温度注射温度过高会导致铝合金液态金属粘度降低,流动性增强,但也会加快模具磨损。
注射温度过低则会导致液态金属凝固时间过长。
2.4.3 注射压力注射压力的控制对于铸件的密实性和表面质量有着重要影响,应根据产品要求进行精确控制。
2.4.4 注射时间注射时间应根据实际需要进行合理设置,以保证铝合金液态金属充填充实模腔。
2.5 热处理工艺铝合金压铸件在铸造成型后,经过热处理工艺可以改善其机械性能和物理性能,如固溶处理、时效处理等。
2.6 铸件表面处理铝合金压铸件的表面处理包括喷砂、喷涂、电镀等方法,以提高产品的外观质量和耐腐蚀性能。
压铸模材料选择及技术要求

压铸模材料选择及技术要求1.压铸模材料的选择:(1)钢材:钢材可以分为冷工作模具钢和热工作模具钢两种。
冷工作模具钢适用于生产小件、薄壁件和大批量生产的情况,例如铝合金压铸件;而热工作模具钢适用于生产大型、复杂的压铸件,例如汽车零部件。
常用的冷工作模具钢有CR12MOV、SKD-11等,常用的热工作模具钢有H13、H11等。
(2)铝材:铝材主要适用于生产大批量的铝合金压铸件。
铝材制作的压铸模具具有热导性好、导热均匀、加工性能好等优点。
常用的铝材有铝合金7075、6061等。
(4)合金材料:合金材料具有耐磨、耐腐蚀、高耐热性等优点,适用于生产特殊要求的压铸件。
常用的合金材料有钛合金、锥纳尔合金等。
2.压铸模材料的技术要求:(1)硬度要求:压铸模材料的硬度要适中,太硬会影响加工性能,太软则容易磨损。
一般要求模具材料的硬度为HRC40~50之间。
(2)机械性能要求:压铸模材料的机械性能直接影响到模具的使用寿命和生产效率。
一般要求模具材料具有较高的抗拉强度、屈服强度和冲击韧性。
(3)导热性要求:压铸模材料的导热性对产品的质量有着重要影响。
材料的导热性能越好,铸件凝固时间越短,产品质量越好。
因此,模具材料的导热性要求较高。
(4)耐磨性要求:压铸模材料需要具备耐磨性能,以防止在生产过程中产生磨损或磨损引起的划伤。
(5)耐腐蚀性要求:压铸模材料需要具备一定的耐腐蚀性能,以防止在铸造过程中与液态金属发生化学反应导致腐蚀和腐蚀引起的模具表面变形。
总之,压铸模材料的选择和技术要求需要综合考虑许多因素,如产品要求、生产批量、模具制造成本、机械性能、导热性、耐磨性和耐腐蚀性等。
合理选择和正确使用压铸模材料是确保压铸模具寿命、提高生产效率和产品质量的关键。
压铸件设计规范详解

压铸件设计规范详解压铸件是指利用压铸工艺将熔融金属注入模具中,经过凝固和冷却后得到的零件。
由于该工艺具有生产效率高、成本低、制造精度高等优点,被广泛应用于汽车、航空航天、电子等领域。
为了保证压铸件质量和安全性,需要遵循一系列的设计规范。
下面将详细介绍压铸件设计规范。
一、材料选择1.铝合金:常用的有A380、A383、A360等。
根据使用条件和要求,选择合适的铝合金材料,确保压铸件具有良好的强度和塑性。
2.压铸型腔材料:常用的有铜合金、热处理工具钢等。
要选择适当的材料,以耐高温和磨损。
二、模具设计1.模具设计必须满足压铸件的要求,保证铸件的尺寸精度和表面质量。
2.模腔设计要考虑到铸件收缩率、冷却速度等因素,以避免产生缺陷和变形。
3.合理安排模具冷却系统,保证压铸件内部和表面的冷却均匀。
三、尺寸设计1.压铸件的尺寸设计应符合产品技术要求和工艺要求,确保功能和安装的需要。
2.避免设计尺寸太小或太薄,以免产生破裂和变形。
3.设计保证良好的表面质量,避免设计中出现接触不良、挤压不足等问题。
四、壁厚设计1.壁厚不应过薄,以免影响产品的强度和刚性。
2.避免壁厚过大,以减少成本和缩短冷却时间。
3.边缘和角部应注意壁厚过渡,避免产生应力集中。
五、设计角度和半径1.设计时应根据铝合金的流动性选择合适的角度和半径。
2.避免设计尖锐角度和太小的半径,以免产生气孔和挤压不足。
3.设计角度和半径应保持一定的一致性,避免因设计不当导致铸件变形和收缩不均匀。
六、设计放射状构件1.当压铸件具有放射状构件时,要合理设计放射状梁的位置和数量,以充分利用材料,并减少成本。
2.注意放射状构件的设计不应影响整体结构的强度。
七、设计排气系统1.设计时要考虑到铸件内部的气孔、气泡等气体排出问题。
2.合理安排和设计排气道,以保证良好的注模效果和铸件质量。
八、设计孔和螺纹1.设计孔和螺纹时应遵循标准规范,确保质量和安装的可靠性。
2.孔和螺纹的位置和尺寸应符合产品要求,保证压铸件的功能和使用要求。
压铸模具标准
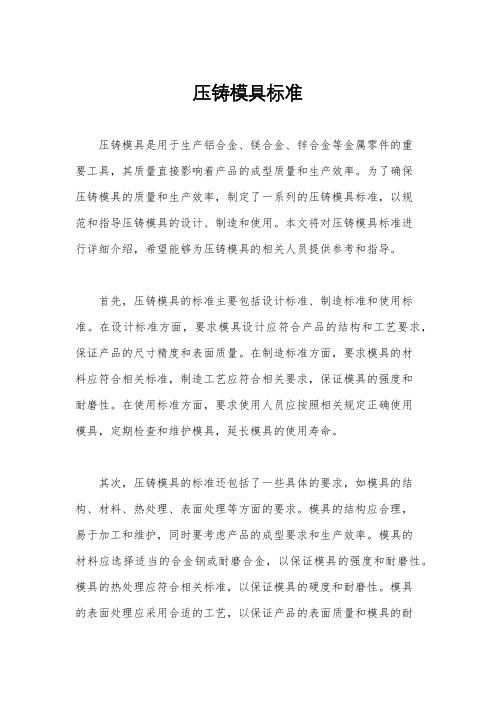
压铸模具标准压铸模具是用于生产铝合金、镁合金、锌合金等金属零件的重要工具,其质量直接影响着产品的成型质量和生产效率。
为了确保压铸模具的质量和生产效率,制定了一系列的压铸模具标准,以规范和指导压铸模具的设计、制造和使用。
本文将对压铸模具标准进行详细介绍,希望能够为压铸模具的相关人员提供参考和指导。
首先,压铸模具的标准主要包括设计标准、制造标准和使用标准。
在设计标准方面,要求模具设计应符合产品的结构和工艺要求,保证产品的尺寸精度和表面质量。
在制造标准方面,要求模具的材料应符合相关标准,制造工艺应符合相关要求,保证模具的强度和耐磨性。
在使用标准方面,要求使用人员应按照相关规定正确使用模具,定期检查和维护模具,延长模具的使用寿命。
其次,压铸模具的标准还包括了一些具体的要求,如模具的结构、材料、热处理、表面处理等方面的要求。
模具的结构应合理,易于加工和维护,同时要考虑产品的成型要求和生产效率。
模具的材料应选择适当的合金钢或耐磨合金,以保证模具的强度和耐磨性。
模具的热处理应符合相关标准,以保证模具的硬度和耐磨性。
模具的表面处理应采用合适的工艺,以保证产品的表面质量和模具的耐蚀性。
最后,压铸模具的标准还包括了一些检验和测试的要求,如模具的出厂检验、使用前检验、定期检验等。
模具的出厂检验应包括模具的尺寸检验、材料检验、热处理检验等,以保证模具的质量。
使用前检验应包括模具的装配检验、润滑检验、保养检验等,以保证模具的正常使用。
定期检验应包括模具的尺寸检验、磨损检验、裂纹检验等,以保证模具的使用寿命。
总之,压铸模具标准是保证压铸模具质量和生产效率的重要依据,对压铸模具的设计、制造和使用都有着重要的指导作用。
压铸模具的相关人员应严格按照相关标准执行,以保证产品质量和生产效率,推动压铸模具行业的健康发展。
希望本文所介绍的压铸模具标准能够为相关人员提供参考和指导,推动我国压铸模具行业的发展。
压铸模具的技术要求文档
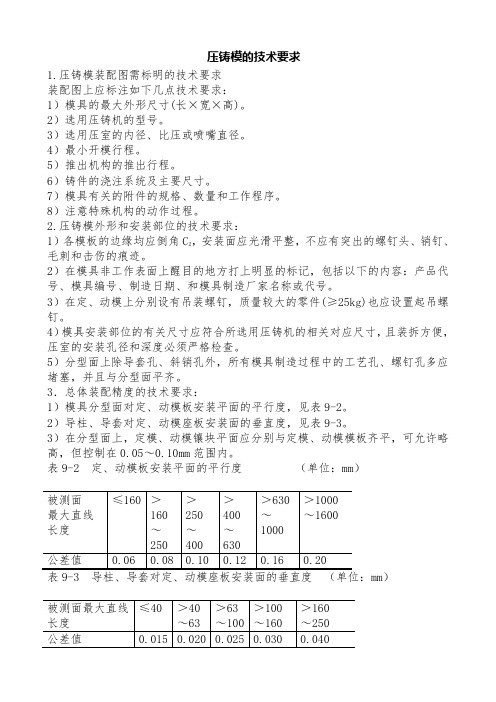
压铸模的技术要求1.压铸模装配图需标明的技术要求装配图上应标注如下几点技术要求:1)模具的最大外形尺寸(长×宽×高)。
2)选用压铸机的型号。
3)选用压室的内径、比压或喷嘴直径。
4)最小开模行程。
5)推出机构的推出行程。
6)铸件的浇注系统及主要尺寸。
7)模具有关的附件的规格、数量和工作程序。
8)注意特殊机构的动作过程。
2.压铸模外形和安装部位的技术要求:1)各模板的边缘均应倒角C2,安装面应光滑平整,不应有突出的螺钉头、销钉、毛刺和击伤的痕迹。
2)在模具非工作表面上醒目的地方打上明显的标记,包括以下的内容:产品代号、模具编号、制造日期、和模具制造厂家名称或代号。
3)在定、动模上分别设有吊装螺钉,质量较大的零件(≥25kg)也应设置起吊螺钉。
4)模具安装部位的有关尺寸应符合所选用压铸机的相关对应尺寸,且装拆方便,压室的安装孔径和深度必须严格检查。
5)分型面上除导套孔、斜销孔外,所有模具制造过程中的工艺孔、螺钉孔多应堵塞,并且与分型面平齐。
3.总体装配精度的技术要求:1)模具分型面对定、动模板安装平面的平行度,见表9-2。
2)导柱、导套对定、动模座板安装面的垂直度,见表9-3。
3)在分型面上,定模、动模镶块平面应分别与定模、动模模板齐平,可允许略高,但控制在0.05~0.10mm范围内。
表9-2 定、动模板安装平面的平行度(单位:mm)表9-3 导柱、导套对定、动模座板安装面的垂直度(单位:mm)4)推杆、复位杆应分别与型面平齐,推杆允许突出型面,但不大干0.1mm。
复位杆允许低于分型面,但不大于0.05mm。
5)模具所有活动部件,应保证位置准确,动作可靠,不得有卡滞和歪斜的现象,要求固定的零件不得相对窜动。
6)浇道的转接处应光滑连接,镶拼处应紧密,未注脱模斜度不小于5º,表面粗糙度R不大于0.4μm。
a7)滑块运动应平稳,合模后滑块与楔紧块应压紧,接触面积不小于3/4,开模后定位准确可靠。
压铸模具的技术要求文档

压铸模具的技术要求文档压铸模具是现代工业生产中常用的一种模具,用于制造各种金属制品。
压铸模具的技术要求非常高,对模具的设计、制造、使用等方面都有相应的要求。
本文将从几个方面详细介绍压铸模具的技术要求。
一、设计要求1.模具结构设计要合理,要考虑到产品的结构特点、工艺要求等因素,并保证在模具使用中有较高的稳定性和精度。
2.模腔的设计要充分考虑充型性、冷却性、顶出性等要素,确保产品成型质量稳定。
3.模具的开口方式、进料方式等设计要符合产品要求,并能保证模具的安全操作。
二、材料要求1.模具材料应具有良好的刚性、韧性和耐磨性,能够承受较大的冲击负荷和高温环境,如工具钢、合金钢等。
2.模具的热处理要求良好,能够使模具硬度均匀、稳定,延长使用寿命。
三、制造要求1.模具加工要求高精度、高质量,要保证模具的尺寸精度和表面质量。
2.维修和保养要定期进行,及时处理模具的磨损、损伤等问题,确保模具的正常使用和寿命。
四、使用要求1.模具的操作人员要具备一定的技能和经验,严格按照操作规程进行操作,保证操作的安全和准确性。
2.模具的使用环境要保持清洁、干燥,避免灰尘、水汽等对模具的损坏。
3.模具的顶出装置、冷却装置等要保持良好的工作状态,及时进行维修和更换。
五、质量控制要求1.模具的尺寸精度、表面质量等要进行严格的检测和控制,保证产品的准确性和一致性。
2.定期对模具进行检测和维修,及时发现并解决模具的问题,防止因模具问题引起的产品质量问题。
总结:压铸模具的技术要求非常高,对模具的设计、制造、使用等方面都有严格要求。
只有合理的设计,良好的材料和制造工艺,正确的使用和维护,才能保证模具的高质量和长寿命,从而保证产品的质量和生产效率。
因此,在实际应用中,需要充分重视压铸模具的技术要求,综合考虑各方面因素,确保模具的高效稳定运行。
压铸模具制造标准

压铸模具制造标准为规范模具制造,保证模具质量,特制定此标准一、总体要求:1、所有零件按二维图纸尺寸、技术要求制作,检验依据二维图纸2、 CNC加工采用按3D编程,相关公差按二维图要求制作3、组立组要按总装图要求组合模具及配模4、发现二维图纸少尺寸、3D与2D不符、制作中出错、安装干涉等情况,及时上报质量组和设计组,由设计组及时做出解决方案,并下发新资料。
质量组确认后,有新资料时电脑上错误资料第一时删除。
5、所有零件热处理按图纸要求操作、6、所有零件表面处理按图纸要求操作7、所有零件上机加工分中、打表规定,打表要求打长面复查短面,分中要求在毎面中心分中(中心误差超10mm),同时用量具复查尺寸。
二、模芯、滑块1、材材为H13或DIEVR2、模芯应图纸硬度要求,要淬火处理。
淬火会造成变形及材料内部硬度达到要求,制作工艺路线为粗加工、淬火、精加工、去应力回火(高温腐蚀会造成应力),才能达图纸3、开粗前外形保证六面垂直度0.1mm、平行度0.02mm以内,4、外形淬火前放精加工余量,外形按最长面来计算,规定如下:长度宽度300mm以内长宽均放1mm,厚放1.2MM。
300~500mm长宽均放1~1.5mm,厚放1.5MM。
500~800mm长宽均放1.5~2mm,厚放2MM。
800mm以上长宽均放2~2.5mm,厚放2.5MM。
5、CNC编程按图编制合理精粗程序,保证质量同时缩短加工时间,减少不必要空刀(采用分段加工)。
CNC操机员按程序参数全部开到100%,不得改度参数,有问题向编程员反映。
6、CNC开粗留单边留1~1.5mm,厚1.5~2MM的淬火后精加工余量,注意不能产生内清角(最小不得小于R2),与外形贯通的槽深不足30mm,宽不足60的不做保护措施,超过时要求两侧底角最小为R15或口部连筋,具体分析后确认。
反面倒角C7,4个R角、分流锥(留有效高度30mm)、料筒等反面台阶处辟空淬火前加工到位。
- 1、下载文档前请自行甄别文档内容的完整性,平台不提供额外的编辑、内容补充、找答案等附加服务。
- 2、"仅部分预览"的文档,不可在线预览部分如存在完整性等问题,可反馈申请退款(可完整预览的文档不适用该条件!)。
- 3、如文档侵犯您的权益,请联系客服反馈,我们会尽快为您处理(人工客服工作时间:9:00-18:30)。
压铸模具技术标准及要求
Page 1 5/17/2013
压铸模具制造过程执行标准及要求
1文档:
此标准及技术要求适用于模具制造商,对压铸模具制造,结构,及标准. 1.1在模具制造完成后,技术部门应提供模具试样书,模具组装图,模具零件图五份及软盘一份(模具备份).
2.模具制造:
2.1全部模腔,使用600号油石抛光,全部模腔表面粗糙度0.2以上. 2.2:全部
模腔应倒角或倒角以保证无尖角或刃边(零件特殊要求除外). 2.3点火花加工痕迹不须全部抛掉.
2.4:全部模芯使用最小600号油石沿轴向抛光并经表面氮化处理硬度HRC44-46,氮化处理深度0.1?以上.
2.5全部模芯位置度按图纸要求,模芯和模芯空间隙0,0(02?。
2.7:出特殊要
求外,所有的型腔镶块都应至少有100?的封料长度或以设计图纸为准.
2.8:侧抽芯与模腔配合精密,防止毛刺及飞边产生.
2.9:模具分型面应配合紧密,合模机上红粉配合,结合部分应大于60%以上动模
和定模的平行度应不大于0.05/200?.
,0.1根据模具检查标准确定. 2.10:动模和定模大镶块应高于模框架0.05
2.11:各模板的边缘应倒角3×45?安装表面光洁平整不应有的螺钉,销钉,毛刺,和磕碰伤等痕迹.螺钉凹下部分应封堵.
定模应大于80?以上,动模100?以上. 2.12:模具厚度符合压铸机设计要求,
2.13:所有滑动及动做部分要求,在正常压铸模温下正常工作,应灵活平稳,配合间隙良好.
2.14:除特殊需要外,模具上不许有焊接.
2.15:模具主装验收合格后分型面及动做部分应涂抹防锈油.浇口套应用干净棉丝封堵.
3.模具绘图:
3.1:模具图纸设计后应需要客户确定后生产.
3.2三维及二维模具设计图纸需经研讨,确认,批准后进行投入生产. 主要内容如下:
模具结构设计确认:浇排系统,顶出机构,冷却水位置,滑块等.
设计图纸及尺寸确认:
压铸机和模具相关性确认.
模具制造计划安排确认.
提出修改工作计划,修正书等.
模具各接口规格.客户标准及要求确认.
客户向我提供的企业标识的制作及位置和尺寸确认.
4(模具材料:
4(1:对客户要供应商提供材料化学分析报告,热处理,表面处理等相关检查报告及相关文件。
4(2:模具热处理硬度HRC44—46,对经过热处理模具部分提供确认数据,并加以判断。
4(3:在粗加工及电火花加工抛光后应进行消除应力回火处理,并且在真空回火炉进行次的消除应力回火处理,并提供相关厂家证明。
Page 2 5/17/2013
4(4:模框材料使用45#钢,进行调质处理HRC28—32,要求提供提供热处理证明。
5(模具标识:
5(1:标识应在合理位置设计,并且不能剥落,动,定模要求标明模具重量及产
品客户编号。
5(2:模具定模后标明压铸机及浇口套内径等客户要求。
6(加热及冷却系统:
冷却及加热系统设计进行热平衡分析后,图纸经审查及批准后投入生产。
6(1: 6(2:各部分水管必须接头和客户相配,进水管蓝色,出水管红色,4根水管以
上集中配置,水管应设置节门,供客户调整用。
集中配管高度需经客户确认为好。
6(3:水管设计时,考虑客户拆装方便,点式冷却应建立标准。
6(4:模芯上冷却水
管距离应大于12?以上。
铜管间隙应不小于1?。
6(5:水管经压力测试其压力0。
4MP,管路畅通,无泄露,试水检查规定压力下,保持10分钟以上,无漏水及卸
压。
6(6:为客户提供点试水管图纸,以便备件准备,和客户标准化。
7(顶出系统7(1:顶出系统及顶出位置,顶出位置平衡,顶杆痕迹客户确认,确认后进行生产。
7(2:顶杆与顶杆空配合间隙按H7工差配合。
7(3:成型顶杆须锁定,并确保其强度。
7(顶出板设四个导柱及导套,压铸工做状态下平稳正常。
4:
7(5:顶杆材料及顶杆尺寸需要确认并保存尺寸,硬度检查数据记录。
7(6:顶
杆配合长度不小于25?,可采用标准件设计。
7(7:顶杆和复位杆在顶出板内应转动自如。
7(8:各顶杆孔应铰孔保证尺寸,光洁度,同轴度。
7(9:客户提供压铸机动板尺寸图纸,以确定顶出位置设计。
8(模具模框
8(1:采用四对导柱,导套。
长度及直径需确认以确保其强度,包括模框配合段长度确认。
采用标准件设计为好。
8(2:模框吊装孔大小,深度,位置需确认以确保其平衡。
方便于搬运。
8(3:压板槽设计满足其强度,厚度应和客户确认,使客户统一压板便于管理。
8(4:模框应具有150以上的封料面,应建立设计标准。
8(5:模框采用球铁Q235或45#钢铸件,无铸造缺,加工与否经客户确认。
9(模具组装:
9(1:以模具检查成绩确认。
10(模具试模:
10(1:以连续生产厂200件为基准,提供样件为1,50,100,150,200,为检查样件。
10(2:试模时保留压铸参数及铸造条件标,调整记录。
10(3:模具合模前,应红粉涂在定模分型面,导柱,分流锥,顶杆部分。
分型面部分配合接触应达到60%以上并且分布均匀。
目视各部分配合确认情况。
10(4:确认模具吊装平衡及安装情况。
10(5:模具重点部位温度,记录。
(型腔,分流锥,浇口套,等)。
10(6:在试模中,应对存在的问提点,记录造册,记录产生条件,并逐一解决,Page 3 5/17/2013
决不能流到客户。
10(7:填写试模报告书。
11(检查及品质确认:
11(1:压铸毛坯件进行全尺寸检查,三坐标检查,壁厚检查。
记录全尺寸及判断合格与否,记录检查数据问题提出报告。
11(2:压铸件毛坯外观检查,判断压铸缺欠。
11(3:压铸件毛坯各孔位气孔断面检查。
判断是否良好,记录提出问提点。
12(问题点解决:
12(1:汇总全部问题点,分类,确定解决部门,分析原因,确定解决对策和方案,解决时间,谁来如何确认。
13(验收:
13(1:以不把问题,留给客户为原则。
不流出不良品内容为原则。
14(包装: 依客户要求进行包装。
以上管理要求建立文件。
系统科学地处理,以建立模具从开发设计制造,品质控制体系手段,以面对未来之发展。