化工原理新型分离技术-膜分离
膜分离技术 概念

膜分离技术概念膜分离技术是一种利用半透膜作为选择障碍层,以膜两侧的化学位差或压力差作为驱动力,实现对液体混合物进行分离的纯化和分离的技术。
膜可以是固态的或液态的,其孔径范围在几纳米至微米之间。
膜分离技术的核心在于半透膜的选择性。
不同的物质在膜中的透过速率不同,从而实现分离。
在分离过程中,混合物中的一种或多种组分可以通过膜,而其他组分则被膜阻隔。
膜的选择性可以根据被分离物质的大小、形状、性质以及扩散能力等进行调整。
根据驱动力的不同,膜分离技术可以分为压力驱动型和浓度驱动型两类。
压力驱动型膜分离技术包括反渗透、纳滤、超滤和微滤等,这些技术利用压力差作为驱动力,使水或其他溶剂通过膜,而溶质或悬浮物被阻隔。
浓度驱动型膜分离技术包括渗透汽化、正渗透等,这些技术利用膜两侧的化学位差作为驱动力,使水或其他溶剂通过膜,而溶质或悬浮物被膜阻隔。
膜分离技术在许多领域都有广泛的应用。
在食品工业中,膜分离技术可用于果汁的澄清和浓缩、乳制品的加工和纯化等。
在医药领域,膜分离技术可用于制备注射用水、血液透析、药物提取和纯化等。
在环保领域,膜分离技术可用于污水处理、海水淡化、工业废水处理等。
此外,膜分离技术还在能源、化工、生物工程等领域得到广泛应用。
与其他分离技术相比,膜分离技术具有许多优点。
首先,膜分离技术在常温下进行,不会引起热敏物质的降解和变质。
其次,膜分离技术具有高效、节能、环保等特点,可以连续化操作,易于自动化控制。
此外,膜分离技术可以用于处理各种类型的液体混合物,适用范围广泛。
然而,膜分离技术也存在一些局限性。
首先,半透膜的制作难度较大,成本较高。
其次,膜通量会受到多种因素的影响,如温度、压力、浓度差等,需要定期维护和清洗。
此外,对于某些特定物质的处理效果不佳,需要进行预处理和后处理。
为了克服这些局限性,科研人员不断进行新型膜材料的研发和制备技术的改进。
同时,多种新型膜分离技术也不断涌现出来,如正渗透、渗透汽化等。
化工原理分离工程知识点

化工原理分离工程知识点化工原理分离工程是化学工程中的一个重要分支,涉及到物质的分离、提纯和纯化等工艺。
分离工程的目的是通过物理或化学手段,将混合物中的不同成分分开,以满足产品质量要求,并实现资源的合理利用。
下面将介绍一些关于化工原理分离工程的知识点。
1.分离工程的分类:-相平衡分离工程:利用物理性质(如沸点、溶解度等)不同的物质在相平衡时的差异进行分离,包括蒸馏、萃取、结晶、吸附等。
-膜分离工程:利用半透膜对混合物进行分离,包括逆渗透、超滤、气体渗透等。
-色谱分离工程:利用分子在固定相上的吸附与解吸作用的不同,进行分离,包括气相色谱、液相色谱等。
-离子交换分离工程:利用离子交换剂对混合物中的离子进行选择性吸附和解吸,包括离子交换层析、电渗析等。
-超临界流体分离工程:利用超临界流体对混合物进行溶解和脱溶,包括超临界流体萃取、疏水液相色谱等。
2.蒸馏:-原理:利用混合物中组分的不同沸点差异,将其在不同温度下从液相转变为蒸汽相,再通过冷凝收集纯净的成分。
-分类:常压蒸馏、减压蒸馏、精馏、萃取蒸馏等。
-应用:石油分馏、酒精提纯、药物合成等。
-原理:利用两个不相溶液体相之间的互溶性差异,将所需组分从一个相转移到另一个相中,实现分离和纯化。
-分类:液液萃取、固液萃取、溶剂萃取等。
-应用:食用油提取、天然产物提纯、有机物合成等。
4.结晶:-原理:利用溶液中物质浓度的变化,在适当的条件下使溶质以晶体形式析出,实现分离和纯化。
-分类:汽提结晶、真空结晶、冷结晶等。
-应用:糖类、盐类、有机物的制备和纯化等。
5.吸附:-原理:利用固体表面对一些组分的选择性吸附作用,实现分离和纯化。
-分类:气相吸附、液相吸附、离子交换等。
-应用:含油气分离、环保废气处理、污水处理等。
6.膜分离:-原理:利用半透膜对混合物进行分离,使其中的一些组分通过膜而其他组分被截留。
-分类:逆渗透、超滤、气体渗透等。
-应用:海水淡化、废水处理、气体分离等。
膜分离的操作方式

膜分离的操作方式1. 膜分离的基本原理膜分离是一种通过膜的选择性通透性实现物质分离的技术。
膜分离的基本原理是利用膜的孔隙结构或表面性质,使得不同成分的物质在膜上发生不同的传质、传递现象,从而实现物质的分离。
2. 膜分离的操作步骤膜分离的操作步骤主要包括前处理、膜分离过程和后处理三个部分。
2.1 前处理前处理是指在膜分离过程之前对原料进行的处理步骤,主要目的是去除悬浮物、颗粒物、胶体物等杂质,以保护膜的使用寿命和效果。
常见的前处理方法包括沉淀、过滤、调节pH值等。
2.2 膜分离过程膜分离过程是指将前处理后的原料通过膜分离设备进行分离的步骤。
根据不同的分离机理和应用需求,膜分离过程可以分为压力驱动式、浓度差驱动式和电场驱动式三种方式。
2.2.1 压力驱动式膜分离压力驱动式膜分离是指通过施加一定的压力差,使原料液体在膜上发生渗透和分离的过程。
常见的压力驱动式膜分离包括微滤、超滤、纳滤和逆渗透等。
压力驱动式膜分离的操作步骤: 1. 将前处理后的原料液体通过泵送至膜分离设备。
2. 施加一定的压力差,使原料液体在膜上发生渗透和分离。
3. 收集通过膜的纯净产物,将未通过膜的浓缩物排出。
2.2.2 浓度差驱动式膜分离浓度差驱动式膜分离是指通过维持两侧溶液的浓度差,使溶质通过膜进行传质和分离的过程。
常见的浓度差驱动式膜分离包括电渗析和渗透气体分离等。
浓度差驱动式膜分离的操作步骤: 1. 将前处理后的原料液体分为两侧,分别放置在膜分离设备的两侧。
2. 维持两侧溶液的浓度差,通过膜进行溶质的传质和分离。
3. 收集通过膜的纯净产物,将未通过膜的浓缩物排出。
2.2.3 电场驱动式膜分离电场驱动式膜分离是指通过在膜上施加电场,利用离子的电荷特性进行传质和分离的过程。
常见的电场驱动式膜分离包括电渗析和电吸附等。
电场驱动式膜分离的操作步骤: 1. 将前处理后的原料液体通过泵送至膜分离设备。
2. 在膜上施加电场,使离子在膜上发生迁移和分离。
了解化学技术中的膜分离技术

了解化学技术中的膜分离技术膜分离技术是一种在化学技术领域广泛应用的技术,它通过膜的选择性透过性质,将混合物进行分离和纯化。
随着现代科学技术的不断发展,膜分离技术在化学领域发挥着越来越重要的作用。
膜分离技术的原理是利用膜的孔径、孔隙率和化学性质等差异,对溶液中的组分进行分离。
常见的膜包括纳滤膜、超滤膜、透析膜等。
这些膜可以在溶液中形成过滤层,通过调整膜的性质和孔隙率,实现对不同尺寸和性质的分子或离子的分离。
膜分离技术在很多领域都有广泛的应用。
首先,在水处理领域,膜分离技术可以有效去除水中的悬浮物、沉淀物、微生物和重金属离子等污染物,从而实现废水的净化和水资源的回收利用。
其次,在制药和生物工程领域,膜分离技术可以用于分离和提纯药物、蛋白质、酶等生物活性物质,提高产品的纯度和质量,并降低生产成本。
此外,在化工和化学制品生产中,膜分离技术可以实现对溶液中组分的浓缩、回收和分离,提高生产效率和产品的品质。
膜分离技术的发展离不开材料科学的进步。
近年来,随着纳米材料和纳米技术的发展,纳米膜分离技术成为研究的热点之一。
纳米膜具有特殊的孔径和表面性质,可以实现对尺寸更小的分子和离子的高效分离。
这种技术被广泛应用于海水淡化、废水处理、气体分离等领域,为解决水资源短缺和环境保护提供了新的思路和方法。
膜分离技术虽然具有许多优点,但也存在着一些挑战和问题。
首先,膜分离技术需要选用合适的膜材料,并对膜的性能进行调控,以实现对特定组分的高效分离。
其次,由于膜的使用过程中容易发生堵塞和污染,需要采取相应的清洗和维护措施。
此外,膜分离技术在大规模应用时,需要考虑生产成本和能源消耗等问题。
为了克服这些问题,科学家们正在不断研究和开发新的膜材料和膜分离技术。
例如,发展高通量、高选择性和耐污染的膜材料,提高膜的抗堵塞性能,减少膜分离过程中的能耗等。
此外,结合其他技术如电吸附、电渗透、化学吸收等,进一步提高膜分离技术的效率和可靠性。
总之,膜分离技术是一种非常重要的化学技术,它在水处理、制药、生物工程和化工等领域都有广泛应用。
膜分离技术的原理
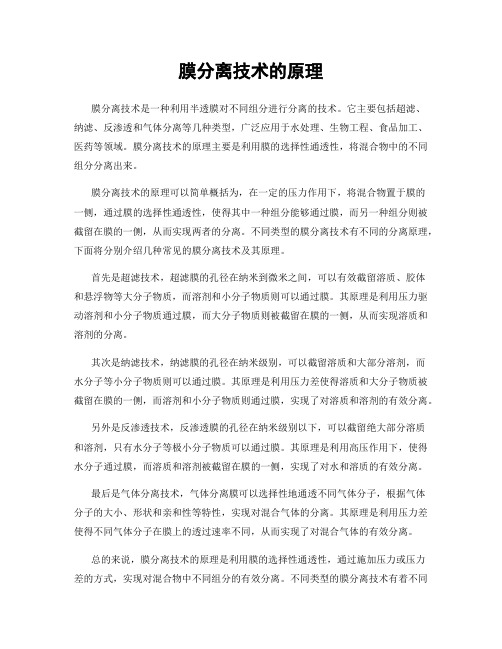
膜分离技术的原理膜分离技术是一种利用半透膜对不同组分进行分离的技术。
它主要包括超滤、纳滤、反渗透和气体分离等几种类型,广泛应用于水处理、生物工程、食品加工、医药等领域。
膜分离技术的原理主要是利用膜的选择性通透性,将混合物中的不同组分分离出来。
膜分离技术的原理可以简单概括为,在一定的压力作用下,将混合物置于膜的一侧,通过膜的选择性通透性,使得其中一种组分能够通过膜,而另一种组分则被截留在膜的一侧,从而实现两者的分离。
不同类型的膜分离技术有不同的分离原理,下面将分别介绍几种常见的膜分离技术及其原理。
首先是超滤技术,超滤膜的孔径在纳米到微米之间,可以有效截留溶质、胶体和悬浮物等大分子物质,而溶剂和小分子物质则可以通过膜。
其原理是利用压力驱动溶剂和小分子物质通过膜,而大分子物质则被截留在膜的一侧,从而实现溶质和溶剂的分离。
其次是纳滤技术,纳滤膜的孔径在纳米级别,可以截留溶质和大部分溶剂,而水分子等小分子物质则可以通过膜。
其原理是利用压力差使得溶质和大分子物质被截留在膜的一侧,而溶剂和小分子物质则通过膜,实现了对溶质和溶剂的有效分离。
另外是反渗透技术,反渗透膜的孔径在纳米级别以下,可以截留绝大部分溶质和溶剂,只有水分子等极小分子物质可以通过膜。
其原理是利用高压作用下,使得水分子通过膜,而溶质和溶剂被截留在膜的一侧,实现了对水和溶质的有效分离。
最后是气体分离技术,气体分离膜可以选择性地通透不同气体分子,根据气体分子的大小、形状和亲和性等特性,实现对混合气体的分离。
其原理是利用压力差使得不同气体分子在膜上的透过速率不同,从而实现了对混合气体的有效分离。
总的来说,膜分离技术的原理是利用膜的选择性通透性,通过施加压力或压力差的方式,实现对混合物中不同组分的有效分离。
不同类型的膜分离技术有着不同的应用和分离原理,但都以膜的选择性通透性为基础,为各行各业的生产和生活提供了重要的分离技术支持。
膜分离技术

混合气体通过多孔膜的传递过程应以分子流为主, 其分离过程应尽 可能满足下述条件: 多孔膜的微孔孔径必须小于混合气体中各组分的平均自由程。 由于在大气压力下的λ的值在1000-2000Å,为了使分子流占优势, 取得良好的分离效果, 一般要求多孔膜的孔径在( 50 ~ 300) Å;
混合气体的温度应足够高, 压力尽可能低。
膜改性
(1)表面活性剂改性
表面活性剂是由至少两种以上极性或亲媒性显著不同 的官能团,如亲水基和疏水基所构成,具有不对称结构。 在其与溶液相接的界面上,由于官能团的作用形成选 择性定向吸附,界面的状态和性质即随之发生显著变化。 非离子型表面活性剂会在与它相接的截面上形成致密的亲 水层,改善界面的亲水性。离子型表面活性剂含有电荷可 以通过静电排斥相同电荷的物质在界面上的吸附。
气体从膜的低压侧表面上脱附出去
m= D· · · d A S ΔP/ = ( P / d) · · A ΔP =J · · P A Δ 式中: P -----D· 渗透系数(10-8---10-14) S J------D· 渗透速率 S/d
(2)表征膜性能的基本参数
渗透速率(J) J=D· S/d
膜改性
(5)辐照接枝改性
辐照接枝改性对于聚合物材料的物化特性和制备亲水性的 膜是一种行之有效的方法,是膜表面改性的重要途径之一。 它主要是利用高能Y射线或电子束对聚合物进行高能辐射, 使其产生活性种,然后活性种引发单体进行接枝聚合反应, 把某些性能的基团或聚合物支链接到膜材料的高分子链上, 使膜具有某些需要的性能。 聚合物改性既可改变膜的物理、机械性能,又可改变膜的 化学或物理性能。
膜改性
技术优点
膜分离技术原理

膜分离技术原理膜分离技术是一种利用特殊膜对物质进行分离的技术,它在化工、环保、食品、制药等领域有着广泛的应用。
膜分离技术的原理主要包括渗透、分离和传质三个基本过程。
首先,渗透是膜分离技术的基本过程之一。
膜分离过程中,溶剂或溶质通过膜的渗透作用从高浓度区域向低浓度区域扩散,使得两侧的浓度趋于平衡。
这一过程是膜分离技术能够实现分离的基础。
其次,分离是膜分离技术的核心过程。
膜分离技术利用膜对不同大小、不同性质的分子或离子进行筛选和分离。
通过选择合适的膜材料和膜孔大小,可以实现对特定物质的选择性分离,从而达到提纯或浓缩的目的。
最后,传质是膜分离技术的关键过程之一。
膜分离技术通过膜的传质作用,实现溶质在膜中的传递和分离。
传质过程受到多种因素的影响,包括膜的孔隙结构、溶质的分子大小和形状、溶液的浓度和温度等因素。
膜分离技术的原理基础上,主要包括了渗透、分离和传质三个基本过程。
渗透是溶剂或溶质通过膜的渗透作用从高浓度区域向低浓度区域扩散,使得两侧的浓度趋于平衡。
分离是利用膜对不同大小、不同性质的分子或离子进行筛选和分离。
传质是通过膜的传质作用,实现溶质在膜中的传递和分离。
这三个过程相互作用,共同完成了膜分离技术的分离和提纯过程。
在实际应用中,膜分离技术具有许多优点,如操作简单、能耗低、分离效率高、产品质量好等。
因此,膜分离技术在化工、环保、食品、制药等领域有着广泛的应用前景。
总的来说,膜分离技术是一种利用特殊膜对物质进行分离的技术,其原理主要包括渗透、分离和传质三个基本过程。
膜分离技术具有许多优点,有着广泛的应用前景。
希望本文的介绍能够帮助大家更好地理解膜分离技术的原理和应用。
膜分离实验报告模板及数据处理方法
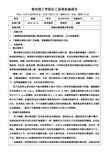
贵州理工学院化工原理实验报告学院:化学工程学院专业:化学工程与工艺(煤磷方向)班级:煤磷132班为Sourirajan 在Gibbs 吸附方程基础上提出的优先吸附-毛细孔流动机理,而后又按此机理发展为定量的表面力-孔流动模型(详见教材)。
3.膜性能的表征一般而言,膜组件的性能可用截留率(R )、透过液通量(J )和溶质浓缩倍数(N )来表示。
(12—1)式中, R -截流率;-原料液的浓度,kmol/m 3; -透过液的浓度,kmol/m 3。
对于不同溶质成分,在膜的正常工作压力和工作温度下,截留率不尽相同,因此这也是工业上选择膜组件的基本参数之一。
(12—2)式中, J -透过液通量,L/(m 2⋅h)-透过液的体积,L ; S -膜面积,m 2; t -分离时间,h 。
其中,tV Q p =,即透过液的体积流量,在把透过液作为产品侧的某些膜分离过程中(如污水净化、海水淡化等),该值用来表征膜组件的工作能力。
一般膜组件出厂,均有纯水通量这个参数,即用日常自来水(显然钙离子、镁离子等成为溶质成分)通过膜组件而得出的透过液通量。
PRc c N =(12—3) 式中, N —溶质浓缩倍数;-浓缩液的浓度,kmol/m 3; -透过液的浓度,kmol/m 3。
该值比较了浓缩液和透过液的分离程度,在某些以获取浓缩液为产品的膜分离过程中(如大分子提纯、生物酶浓缩等),是重要的表征参数。
三、实验装置本实验装置均为科研用膜,透过液通量和最大工作压力均低于工业现场实际使用情况,实验中不可将膜组件在超压状态下工作。
主要工艺参数如表1-1膜组件膜材料膜面积/m2最大工作压力/Mpa 纳滤(NF)芳香聚纤胺0.4 0.7反渗透(RO) 芳香聚纤胺0.4 0.7表1-1膜分离装置主要工艺参数反渗透可分离分子量为100级别的离子,学生实验常取0.5%浓度的硫酸钠水溶液为料液,浓度分析采用电导率仪,即分别取各样品测取电导率值,然后比较相对数值即可(也可根据实验前做得的浓度-电导率值标准曲线获取浓度值)。
- 1、下载文档前请自行甄别文档内容的完整性,平台不提供额外的编辑、内容补充、找答案等附加服务。
- 2、"仅部分预览"的文档,不可在线预览部分如存在完整性等问题,可反馈申请退款(可完整预览的文档不适用该条件!)。
- 3、如文档侵犯您的权益,请联系客服反馈,我们会尽快为您处理(人工客服工作时间:9:00-18:30)。
砜
耐辐射,机械强度较高。
含 聚偏氟乙烯膜(PVDF)、聚四氟 氟 乙烯膜(PTFE)、聚全氟磺酸 材 料
化学稳定性好,耐高温。如PTFE膜, -40~260oC,可耐强酸,强碱和各 种有机溶剂。具疏水性,可用于过滤 蒸气及腐蚀性液体。
P2 P3
膜过程的一些术语
1
2 3
浓差极化:在膜分离过程中, 一部分溶质被截留,在膜表 面及靠近膜表面区域的浓度 越来越高,造成从膜表面到 本体溶液之间产生浓度梯度,
这一现象称为“浓差极化”。
Cf Cm Cp
浓差 膜层 渗透侧
极化层
极化层
膜过程的一些术语
传递阻力:
1)膜阻Rm:与膜本身的结构有关,包含膜层到支撑层的 传递阻力;
膜过程的一些术语
通量衰减系数m:由于过程的浓差极化、膜的压密、膜污 染等的影响,使得通量随时间的变化
膜过程的一些术语
推动力: 1)对多孔膜而言,在对流流动的情况下,传质推动力是 膜两侧的压力差。
P1
P=(P1+P2)/2-P3
膜压降:P1-P2,是由于流体流动引起的。 2)对致密膜而言,推动力为膜两侧的化学势之差。
在其它工业废水处理中的应用
❖造纸工业的黑水和白水处理、纺织废水中PVA 回收等。
上海宝钢集团公司冷轧线
设备处理能力为:6万m3/年,油截留率大于99.9%,水回用率大于90%,回收油120吨 /年
钢铁冷轧乳化液废水处理回用技术
项目 设备折旧费用 (元)
能耗费用 (元) 人工费用 (元)
维修 (元) 清洗剂费用(元)
1827年Dutrochet引入名词渗透(Osmosis); 1861年Schmidt提出超滤概念; 1864年Traube成功研制了人类历史上第一张人造膜(亚铁氰化铜膜) 1918年Zsigmondy提出了商品微滤膜的制备方法,并将其应用于微
生物、微粒等方面的分离和富集; 1950年W.Juda成功研制了第一张具有实用价值的离子交换膜; 1960年Loeb 和Sourirajan研制出第一张不对称的醋酸纤维素反渗
取出,能提高反应速率或提高产品质量。
从20世纪初到20世纪90年代,膜技术基本已经从实验室 步入工业化,并在水处理、食品工业、环境保护、化工与 石油化工、电子、冶金、国防……等领域得到成功的应用。 目前全球膜产业的规模超过百亿美元,正以年30%的速 度递增着。
膜的应用
海水淡化 工业废水处理 城市废水资源化
常用膜分离技术的基本特征
项目 膜类型 操作压力 分离机理 适用范围
技术特点
不足之处
微滤 对称微孔膜 0.01 MPa~颗粒大小、含微粒或菌体溶 操作简便,通水量大,工 有机污染物的分
(MF) 0.02~10μm 0.2 MPa
形状
液的分离 作压力低,制水率高。 离效果较差。
超滤 不对称微孔膜 0.1 MPa ~颗粒大小、有机物或微生物 (UF) 0.001~0.1μm 0.5 MPa 形状 溶液的分离
透膜,导致了膜分离技术进入了实用和装置的研制阶段; 1967年以后在美国、丹麦、日本等国出现了多家膜及其组件的生产
厂家,逐渐开始了膜分离技术的规模应用。
膜的发展历史
我国1958年开始研究离子交换膜和电渗析,1966年 开始研究RO、UF、MF、液膜、气体分离等膜分离过 程应用与开发研究。80年代后期又陆续开展了渗透汽 化、膜萃取、膜蒸馏和膜反应等新膜过程的研究,并 着手进行膜技术的推广应用工作。
国家
德国 德国 荷兰 美国 美国 美国 美国 德国 德国/荷兰
年代
1920 1930 1950 1955 1960 1960 1979 1981 1982
应用
实验室用(细菌过滤器) 实验室用 人工肾 脱盐 海水脱盐 大分子物质浓缩 氢回收 水溶液浓缩 有机溶液脱水
膜的分类
膜材料
材料
特点
纤 二醋酸纤维素 (CDA)、三醋酸 成孔性、亲水性好、价廉易得,使用
“谁掌握了膜技术,谁就 掌握了21世纪的未来”
膜的简介
特征:具有选择性分离的功能薄膜
材料,以及以其为核心的装置、过 程、工艺的集成与应用。
特点:
浓缩液
无相变、低能耗
渗
高效率、污染小
透 液
工艺简单、操作方便
便于与其它技术集成
进料液
膜的发展历史
1748年Abble Nelkt 发现水能自然地扩散到装有酒精的猪膀胱内, 首次揭示了膜分离现象;
膜元件
膜元件
膜组件
一、板框式
1 - 轴芯 2 - O型环 3 - 垫圈 4 - 固定材 5-网 6 - 护罩 7 - 外层材 8-膜 9 - 内层材 10 - 固定 材
二、圆管式
圆管式膜组件的机构主要将 膜和支撑体均制成管状。
三、螺旋式膜组件 螺旋卷式膜组件是将做好的平板膜密封成膜袋,在两膜
国内主要的膜研究和推广单位: 1)气体分离:大连化学物理研究所(天邦膜公司) 2)液体分离:杭州水处理技术中心(西斗门公司)
天津纺织工学院(膜天公司) 3)无机膜:南京工业大学(久吾高科)
中国科技大学
膜的发展历史
膜过程
微滤 超滤 血液渗析 电渗析 反渗透 超滤 气体分离 膜蒸馏 全蒸发
/荷兰 19301950195 519601960197 9198
与微滤技术相似。
与微滤技术相似。
纳滤 带皮层不对称复 0.5 MPa ~优先吸附、硬水或有机物溶 可对原水进行部分脱盐和 常需预处理,工作 (NF) 合膜1~50 nm 2.5 MPa 表面电位 液的脱盐 软化,生产优质饮用水。 压力较高。
反渗透 (RO)
带皮层不对称复 合膜<1 nm
1.0 MPa 10 MPa
油回收费(元) 水回收费(元) 总费用 (元)
国产陶瓷膜(元/m3) 3.39 1.55 0.69 0.27 0.22
-2.25 -0.9
2.97
进口有机膜(元/m3) 18 9 1.4 1.0 4.0
-2.25 0(水质不稳定)
31.15
说明 1:年处理10万吨冷轧乳化液废水设备,采用国产陶瓷膜300 万元人民币(武钢),进口有机膜设备200万美元(宝钢,1988 年),成本仅是其1/10。
选择性:将混合物总的组分分离开来的能力。 1)液体分离的选择性常用截留率表示:
R=1-Cp/Cf 2)气体分离或有机溶剂混合物的分离常用分离因子表示选
择性:A/B=(yA/yB)/(xA/xB),其中y表示渗透侧各组分的浓 度,x表示原料侧的浓度。当A/B等于1,表示无法实现分 离目的,大于1表示A组分通过膜的速度大于B组分。
2)浓差极化阻力Rc:由于被截留组分在膜面浓度的增大 而引起的;
3)推动力的损失:进料侧和渗透侧的压力损失; 4)膜污染阻力:由于物料中的成分对膜产生吸附、堵塞、
以及沉积等现象而引起的。
Rm 膜管本身阻力 Ri 膜孔内污染阻力 Rg 凝胶层阻力 Rc 浓差极化阻力
膜污染
Cg
C
u
Cb
Rm Ri
维 纤维素 (CTA)、硝化纤维素(CN),温度范围较广,可耐稀酸,不适用于
素 混合纤维素(CN-CA)、乙基纤维 酮类,酯类、强酸和碱类等液体的过
素(EC)等。
滤。
聚 尼龙-6(NY-6)、尼龙-66(NY-66)、 具亲水性能,较耐碱而不耐酸,在酮、 酰 芳香聚酰胺(PI)、芳香聚酰胺酰 酚、醚及高相对分子质量醇类中,不 胺 肼(PPP)、聚苯砜对苯二甲酰 易被浸蚀,孔径型号也较多。
~优先吸附、海水或苦咸水的 溶解扩散 淡化
几乎可去除水中一切杂 质,包括悬浮物、胶体、 有机物、盐、微生物等。
工作压力高;制水 率低;能耗大。
原理
RO membrane UF membrane
NF membrane MF membrane
原理 动漫
膜过程的一些术语
通量:在一定操作条件下,单位时间通过单位面积膜的体 积流量。单位L/m2.h
舰艇淡水供应;战地医院污水净化;低放射性水处理;野战供水
膜技术用于生物质资源开发
传统过程:发酵速 率低、能耗大
纤维素
发酵
蒸馏
蒸馏
脱水
7 wt%乙醇
42 wt%乙醇
93 wt%乙醇
99.8 wt%乙醇
980 kcal/l
350 kcal/l
1380 kcal/l
膜生物反应 器:实现连 续生产,降
透 醇
(1) 分散得很细的固体,特别是与液体密度相近,胶状的可 压缩的固体微粒; (2) 低分子量的不挥发的有机物、药物与溶解的盐类; (3) 对温度、酸碱度等物理化学条件特别敏感的生物物质。
涉及气体分离、水溶液分离、生化产品的分离与纯化等操作 的食品和饮料加工过程、工业污水处理、大规模空气分离、 湿法冶金、气体和液体燃料的生产及石油化工制品的生产等。
膜分离技术及其应用
膜分离发展过程和趋势
反 超 微透 渗 滤 滤析 透
膜 反 活闸 应 化膜 器 传 递
电 渗 控析 制 气释 体放 渗分 透离 双极汽化 液膜 膜
低增长 高增长 可用?
膜的简介
定义: 具有选择性分离的功能 薄膜材料。
水 小分子 大分子 料液
膜
渗透液
“21世纪的多数工业中, 膜技术扮演着战略的角色”
各种膜组件的优缺点比较
组件
优点
缺点
板框 式
螺旋 卷式
管 式
保留体积小,操作费用低的压 力降,液流稳定,比较成熟
设备投资低,操作费用也低, 单位体积中所含过滤面积大, 换新膜容易
易清洗,单根管子容易调换, 对液流易控制,无机组件可在 高温下用有机溶剂进行操作并 可用化学试剂来消毒