质量管理常用的18个公式
质量管理18个公式

质量管理18个公式质量管理是指通过规划、控制和改进来确保产品或服务满足客户要求的过程。
在质量管理中,有许多重要的公式和指标,用于评估和改进质量。
以下是18个常用的质量管理公式:1. 流程能力指数(Process Capability Index,Cp):Cp = (USL-LSL) / (6*σ),其中USL是上限规范,LSL是下限规范,σ是标准差。
2. 流程能力指数指标(Process Capability Index Ratio,Cpk):Cpk = min[(USL-µ)/(3σ),(µ-LSL)/(3σ)],其中µ是平均值,σ是标准差。
3. 标准差(Standard Deviation,σ):σ = √(Σ(xi-µ)²/(n-1)),其中xi是数据点,µ是平均值,n是样本数量。
4. 总变差分析(Total Variance Analysis,TV):TV = σ² =Σ(xi-µ)²/n,其中σ是标准差,xi是数据点,µ是平均值,n是样本数量。
5. 缺陷比率(Defect Rate,DR):DR = (缺陷数/总产出) * 100%。
6. 缺陷密度(Defect Density,DD):DD = 缺陷数/代码或文件大小。
7. 产品可靠性(Product Reliability,PR):PR = (1-DR) * 100%。
8. 回归分析(Regression Analysis):可以用来分析因变量和自变量之间的关系。
9. 可行性研究(Feasibility Study):用于评估项目的可行性,包括技术、经济、法律等方面。
10. 成本效益分析(Cost-Benefit Analysis):比较实施项改进或投资的成本和收益。
11. 控制图(Control Chart):用于监控过程的稳定性和质量。
质量管理常用的18个公式学习资料

质量管理常用的18个公式1.废品率定义:该百分比由废品材料费用除以总生产成本或由废品总数量除以产品总生产数量得到。
目的:用作结果度量,来确定过程是否按照规范化进行零件生产和装配。
公式:废品率%=(废品的材料金额/总生产成本)×100%或(废品总数量/产品总生产数量)×100%。
术语:废品材料金额:是废品所使用的材料的价值。
总生产成本:是劳动力,材料和工厂负担(水、电等)的总和。
应用/信息:废品计算是直接从本单位的财务系统中得到其数值。
若公司的财务系统不能从劳动力和负担费用中分离出废品材料价值,应尽快与相关部门协调解决。
2.返工率定义:花费在返工活动中时间的比例,由返工工时除以生产劳动工时或返工(返修)品的总数量除以总的生产数量得到。
目的:用作结果度量,来强调那些在第一次质量中需要改进的操作工位。
公式:返工率%=(返工工时/总生产劳动工时)×100%或(返工(返修)品的总数量/总的生产数量)×100%。
术语:返工工时:是指再次加工,分拣,修复那些将成为废品的工件所花费的时间。
这些时间可以是用在在制品,成品和外购部件或材料上。
返工时间包括诸如修复,重新包装,再分拣,附加的检查活动和遏制等。
返工时间包括内部的或外部的活动。
应包括直接时间加上加班时间中的直接时间部分。
生产劳动工时:直接/生产劳动工人工作时间总和(包括直接时间加上加班时间中的直接时间部分)。
应用/信息:直接劳动工人的偶尔检查不应认为是返工。
任何再进入生产过程的产品应被认为返工。
生产线的总劳动内容的一部分应认为是返工。
该部分将根据返工的产品情况确定。
譬如,在最终检查时,涂漆生产线有10%的产品不合格,而该涂漆生产线共有20名操作员,返工的产品(10%)需要再次涂漆,涂漆生产线总工作时间的10%被认为是用来返工。
10%×20人×8小时=16 返工小时。
3.产品入库检验合格率定义:产品入库检验合格数量除以入库检验总数量所得。
质量管理常用的 18 个公式
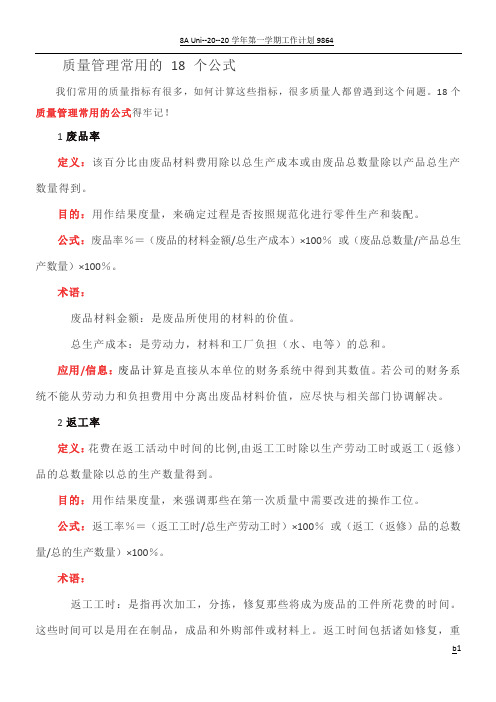
质量管理常用的18 个公式我们常用的质量指标有很多,如何计算这些指标,很多质量人都曾遇到这个问题。
18个质量管理常用的公式得牢记!1废品率定义:该百分比由废品材料费用除以总生产成本或由废品总数量除以产品总生产数量得到。
目的:用作结果度量,来确定过程是否按照规范化进行零件生产和装配。
公式:废品率%=(废品的材料金额/总生产成本)×100%或(废品总数量/产品总生产数量)×100%。
术语:废品材料金额:是废品所使用的材料的价值。
总生产成本:是劳动力,材料和工厂负担(水、电等)的总和。
应用/信息:废品计算是直接从本单位的财务系统中得到其数值。
若公司的财务系统不能从劳动力和负担费用中分离出废品材料价值,应尽快与相关部门协调解决。
2返工率定义:花费在返工活动中时间的比例,由返工工时除以生产劳动工时或返工(返修)品的总数量除以总的生产数量得到。
目的:用作结果度量,来强调那些在第一次质量中需要改进的操作工位。
公式:返工率%=(返工工时/总生产劳动工时)×100%或(返工(返修)品的总数量/总的生产数量)×100%。
术语:返工工时:是指再次加工,分拣,修复那些将成为废品的工件所花费的时间。
这些时间可以是用在在制品,成品和外购部件或材料上。
返工时间包括诸如修复,重新包装,再分拣,附加的检查活动和遏制等。
返工时间包括内部的或外部的活动。
应包括直接时间加上加班时间中的直接时间部分。
生产劳动工时:直接/生产劳动工人工作时间总和(包括直接时间加上加班时间中的直接时间部分)。
应用/信息:直接劳动工人的偶尔检查不应认为是返工。
任何再进入生产过程的产品应被认为返工。
生产线的总劳动内容的一部分应认为是返工。
该部分将根据返工的产品情况确定。
譬如,在最终检查时,涂漆生产线有10%的产品不合格,而该涂漆生产线共有20名操作员,返工的产品(10%)需要再次涂漆,涂漆生产线总工作时间的10%被认为是用来返工。
18个质量管理常用的公式得牢记
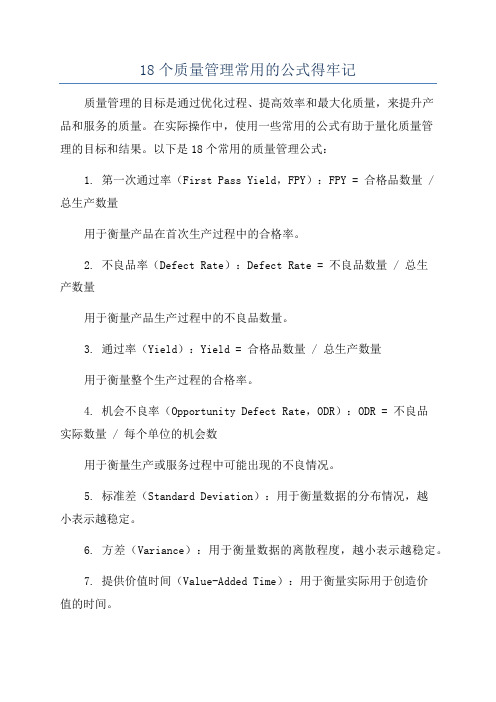
18个质量管理常用的公式得牢记质量管理的目标是通过优化过程、提高效率和最大化质量,来提升产品和服务的质量。
在实际操作中,使用一些常用的公式有助于量化质量管理的目标和结果。
以下是18个常用的质量管理公式:1. 第一次通过率(First Pass Yield,FPY):FPY = 合格品数量 / 总生产数量用于衡量产品在首次生产过程中的合格率。
2. 不良品率(Defect Rate):Defect Rate = 不良品数量 / 总生产数量用于衡量产品生产过程中的不良品数量。
3. 通过率(Yield):Yield = 合格品数量 / 总生产数量用于衡量整个生产过程的合格率。
4. 机会不良率(Opportunity Defect Rate,ODR):ODR = 不良品实际数量 / 每个单位的机会数用于衡量生产或服务过程中可能出现的不良情况。
5. 标准差(Standard Deviation):用于衡量数据的分布情况,越小表示越稳定。
6. 方差(Variance):用于衡量数据的离散程度,越小表示越稳定。
7. 提供价值时间(Value-Added Time):用于衡量实际用于创造价值的时间。
8. 总提供时间(Total Lead Time):用于衡量从开始到完成产品所需的总时间。
9. 效率(Efficiency):Efficiency = 实际产出 / 标准产出用于衡量生产或服务过程的效率。
10. 效益(Effectiveness):Effectiveness = 实际产出 / 理论产出用于衡量生产或服务过程的效益。
11. 系统失效率(System Failure Rate):用于衡量整个系统的失效率。
12. 故障率(Failure Rate):用于衡量设备或系统的故障率。
13. 维修率(Repair Rate):用于衡量进行维修的频率。
14. MTTF(Mean Time to Failure):用于衡量设备或系统的平均使用时间。
18个质量管理常用的公式得牢记

18个质量管理常用的公式得牢记质量管理个我们常用的质量指标有很多,如何计算这些指标,很多质量人都曾遇到这个问题。
18 得牢记!常用的公式废品率、1该百分比由废品材料费用除以总生产成本或由废品总数量除以产品总生产数量得到。
定义:目的:用作结果度量,来确定过程是否按照规范化进行零件生产和装配。
产品总生产数量)×/%或(废品总数量/公式:废品率%=(废品的材料金额总生产成本)×100 100%。
术语:?废品材料金额:是废品所使用的材料的价值。
?总生产成本:是劳动力,材料和工厂负担(水、电等)的总和。
.?应用/信息:废品计算是直接从本单位的财务系统中得到其数值。
若公司的财务系统不能从劳动力和负担费用中分离出废品材料价值,应尽快与相关部门协调解决。
返工率、2定义:花费在返工活动中时间的比例,由返工工时除以生产劳动工时或返工(返修)品的总数量除以总的生产数量得到。
目的:用作结果度量,来强调那些在第一次质量中需要改进的操作工位。
公式:返工率%=(返工工时/总生产劳动工时)×100%或(返工(返修)品的总数量/总的生产数量)×100%。
术语:?返工工时:是指再次加工,分拣,修复那些将成为废品的工件所花费的时间。
这些时间可以是用在在制品,成品和外购部件或材料上。
返工时间包括诸如修复,重新包装,再分拣,附加的检查活动和遏制等。
返工时间包括内部的或外部的活动。
应包括直接时间加上加班时间中的直接时间部分。
?生产劳动工时:直接/生产劳动工人工作时间总和(包括直接时间加上加班时间中的直接时间部分)。
应用/信息:直接劳动工人的偶尔检查不应认为是返工。
任何再进入生产过程的产品应被认为返工。
生产线的总劳动内容的一部分应认为是返工。
该部分将根据返工的产品情况确定。
譬如,在最终检查时,涂漆生产线有10%的产品不合格,而该涂漆生产线共有20名操作员,返工的产品(10%)需要再次涂漆,涂漆生产线总工作时间的10%被认为是用来返工。
质量管理经常用到的18个公式
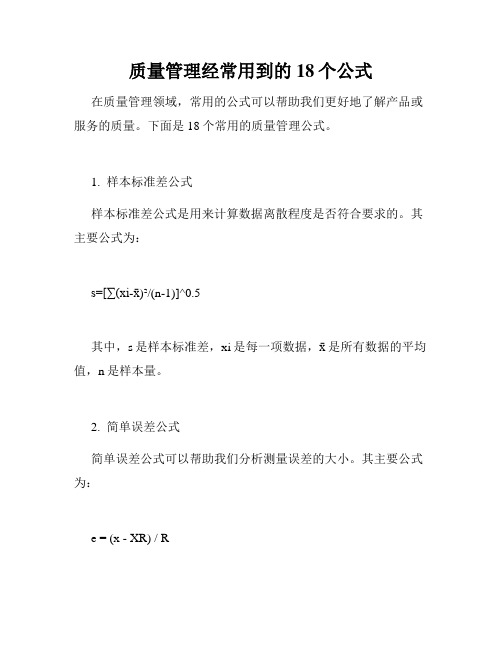
质量管理经常用到的18个公式在质量管理领域,常用的公式可以帮助我们更好地了解产品或服务的质量。
下面是18个常用的质量管理公式。
1. 样本标准差公式样本标准差公式是用来计算数据离散程度是否符合要求的。
其主要公式为:s=[∑(xi-x)²/(n-1)]^0.5其中,s是样本标准差,xi是每一项数据,x是所有数据的平均值,n是样本量。
2. 简单误差公式简单误差公式可以帮助我们分析测量误差的大小。
其主要公式为:e = (x - XR) / R其中,e是误差百分数,x是单次测量值,XR是所有测量的平均值,R是标准值。
3. 可重复度公式可重复度公式可以帮助我们评估同一测量的可重复程度。
其主要公式为:R = X2 - X1其中,R是可重复度,X1是第一次测量值,X2是第二次测量值。
4. 变异系数公式变异系数公式可以帮助我们评估数据的稳定程度。
其主要公式为:CV = s / x ×100%其中,CV是变异系数,s是标准差,x是平均值。
5. 一致度检验公式一致度检验公式可以帮助我们判断同一批次的产品或服务是否符合要求。
其主要公式为:Cp = (USL - LSL) / 6σ其中,Cp是一致度指数,USL是最大限制线,LSL是最小限制线,σ是标准差。
6. 相对误差公式相对误差公式可以帮助我们评估测量值与真实值之间的差异。
其主要公式为:εr = |(Xi - Xt) / Xt| ×100%其中,εr是相对误差,Xi是测量值,Xt是真实值。
7. 置信区间公式置信区间公式可以帮助我们评估样本均值与总体均值之间的差异。
其主要公式为:CI = X ± t * SE其中,CI是置信区间,X是样本均值,t是t分布表中的统计值,SE是标准误。
8. 相对容差公式相对容差公式可以帮助我们评估产品或服务的制造工艺。
其主要公式为:TR = (USL - LSL) / X其中,TR是相对容差,USL是最大限制线,LSL是最小限制线,X是平均值。
质量管理常用的18个公式
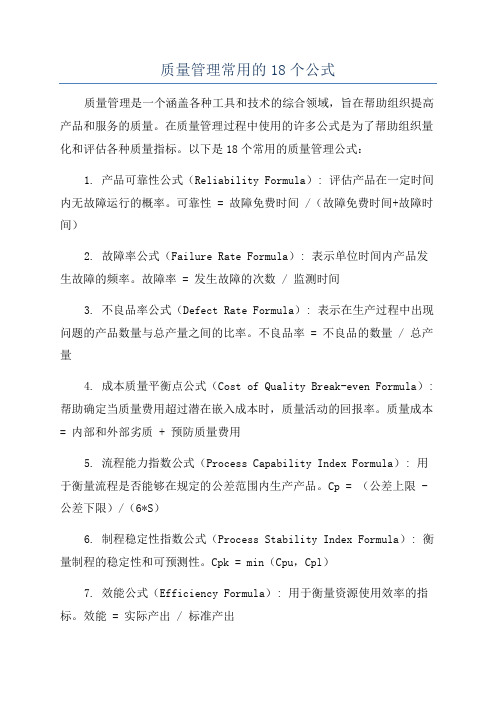
质量管理常用的18个公式质量管理是一个涵盖各种工具和技术的综合领域,旨在帮助组织提高产品和服务的质量。
在质量管理过程中使用的许多公式是为了帮助组织量化和评估各种质量指标。
以下是18个常用的质量管理公式:1. 产品可靠性公式(Reliability Formula): 评估产品在一定时间内无故障运行的概率。
可靠性 = 故障免费时间 /(故障免费时间+故障时间)2. 故障率公式(Failure Rate Formula): 表示单位时间内产品发生故障的频率。
故障率 = 发生故障的次数 / 监测时间3. 不良品率公式(Defect Rate Formula): 表示在生产过程中出现问题的产品数量与总产量之间的比率。
不良品率 = 不良品的数量 / 总产量4. 成本质量平衡点公式(Cost of Quality Break-even Formula): 帮助确定当质量费用超过潜在嵌入成本时,质量活动的回报率。
质量成本= 内部和外部劣质 + 预防质量费用5. 流程能力指数公式(Process Capability Index Formula): 用于衡量流程是否能够在规定的公差范围内生产产品。
Cp = (公差上限 - 公差下限)/(6*S)6. 制程稳定性指数公式(Process Stability Index Formula): 衡量制程的稳定性和可预测性。
Cpk = min(Cpu,Cpl)7. 效能公式(Efficiency Formula): 用于衡量资源使用效率的指标。
效能 = 实际产出 / 标准产出8. 效益公式(Effectiveness Formula): 衡量达到预期结果的能力。
效益 = 实际产出 / 预期产出9. 成本效益比公式(Cost-effectiveness Ratio Formula): 表示单位成本所能达到的预期成果量。
成本效益比 = 花费 / 预期成果10. 缺陷定位率公式(Defect Localization Rate Formula): 用于评估在测试过程中发现的缺陷的准确性。
质量管理用到的公式
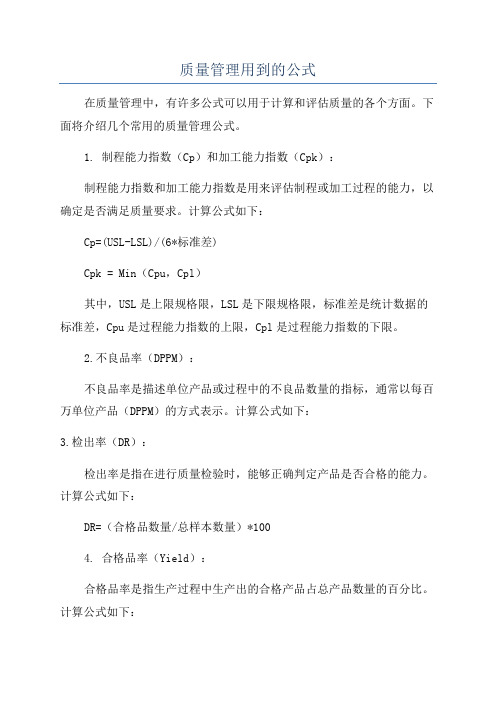
质量管理用到的公式在质量管理中,有许多公式可以用于计算和评估质量的各个方面。
下面将介绍几个常用的质量管理公式。
1. 制程能力指数(Cp)和加工能力指数(Cpk):制程能力指数和加工能力指数是用来评估制程或加工过程的能力,以确定是否满足质量要求。
计算公式如下:Cp=(USL-LSL)/(6*标准差)Cpk = Min(Cpu,Cpl)其中,USL是上限规格限,LSL是下限规格限,标准差是统计数据的标准差,Cpu是过程能力指数的上限,Cpl是过程能力指数的下限。
2.不良品率(DPPM):不良品率是描述单位产品或过程中的不良品数量的指标,通常以每百万单位产品(DPPM)的方式表示。
计算公式如下:3.检出率(DR):检出率是指在进行质量检验时,能够正确判定产品是否合格的能力。
计算公式如下:DR=(合格品数量/总样本数量)*1004. 合格品率(Yield):合格品率是指生产过程中生产出的合格产品占总产品数量的百分比。
计算公式如下:Yield = (合格产品数量 / 总产品数量) * 1005. 效能(Efficiency):效能是指生产过程中实际生产的产品数量与理论最大产能之间的比率。
计算公式如下:Efficiency = (实际生产数量 / 理论最大产能) * 1006. 效益(Effectiveness):效益是指实际生产的产品数量与计划生产的产品数量之间的比率。
计算公式如下:Effectiveness = (实际生产数量 / 计划生产数量) * 1007. 效率(Productivity):效率是指单位时间内实现的产量与所需资源之间的比率。
计算公式如下:Productivity = (产量 / 资源消耗) * 1008.成本绩效指数(CPI)和进度绩效指数(SPI):成本绩效指数和进度绩效指数是用于评估项目的成本和进度表现的指标。
计算公式如下:CPI=挣值(EV)/实际成本(AC)SPI=挣值(EV)/计划值(PV)其中,挣值(EV)是实际完成工作的预算成本,实际成本(AC)是实际花费的成本,计划值(PV)是计划的预算成本。
- 1、下载文档前请自行甄别文档内容的完整性,平台不提供额外的编辑、内容补充、找答案等附加服务。
- 2、"仅部分预览"的文档,不可在线预览部分如存在完整性等问题,可反馈申请退款(可完整预览的文档不适用该条件!)。
- 3、如文档侵犯您的权益,请联系客服反馈,我们会尽快为您处理(人工客服工作时间:9:00-18:30)。
质量管理常用的18个公式
1废品率
定义:该百分比由废品材料费用除以总生产成本或由废品总数量除以产品总生产数量得到。
目的:用作结果度量,来确定过程是否按照规范化进行零件生产和装配。
公式:废品率%=(废品的材料金额/总生产成本)×100%或(废品总数量/产品总生产数量)×100%。
术语:废品材料金额:是废品所使用的材料的价值。
总生产成本:是劳动力,材料和工厂负担(水、电等)的总和。
应用/信息:废品计算是直接从本单位的财务系统中得到其数值。
若公司的财务系统不能从劳动力和负担费用中分离出废品材料价值,应尽快与相关部门协调解决。
2返工率
定义:花费在返工活动中时间的比例,由返工工时除以生产劳动工时或返工(返修)品的总数量除以总的生产数量得到。
目的:用作结果度量,来强调那些在第一次质量中需要改进的操作工位。
公式:返工率%=(返工工时/总生产劳动工时)×100%或(返工(返修)品的总数量/总的生产数量)×100%。
术语:返工工时:是指再次加工,分拣,修复那些将成为废品的工件所花费的时间。
这些时间可以是用在在制品,成品和外购部件或材料上。
返工时间包括诸如修复,重新包装,再分拣,附加的检查活动和遏制等。
返工时间包括内部的或外部的活动。
应包括直接时间加上加班时间中的直接时间部分。
生产劳动工时:直接/生产劳动工人工作时间总和(包括直接时间加上加班时间中的直接时间部分)。
应用/信息:直接劳动工人的偶尔检查不应认为是返工。
任何再进入生产过程的产品应被认为返工。
生产线的总劳动内容的一部分应认为是返工。
该部分将根据返工的产品情况确定。
譬如,在最终检查时,涂漆生产线有10%的产品不合格,而该涂漆生产线共有20名操作员,返工的产品(10%)需要再次涂漆,涂漆生产线总工作时间的10%被认为是用来返工。
10%×20人×8小时=16 返工小时。
3产品入库检验合格率
定义:产品入库检验合格数量除以入库检验总数量所得。
目的:用作过程度量,用来衡量整个生产过程的质量水平。
公式:产品入库检验合格率%=(产品入库检验合格数量/入库检验总数量)×100%。
4百万分之不合格品数
(顾客退货率或产品不良率)
定义:每百万件产品中客户退货/拒收的数量或不合格产品数量占全部发运数量或全部生产总数的比值。
目的:用作结果度量,来全面显示产品不满意造成的影响,使得集中精力解决问题。
公式:顾客退货率= 退回件数/发货件数产品总数量*1,000,000 或产品不良率=不合格总数/产品总数量*1,000,000。
5质量事故
定义:每年由于产品不合格引起的生产停顿次数。
导致公司停止发货,停止生产或者要求将已制造的产品进行修正。
目的:用作整体结果度量,反应由公司质量事故次数引起的产品不满意,以利于集中精力解决问题。
公式:质量事故= 每年公司定义的质量事故造成的工厂生产停顿次数。
6零件加工不良率
(巡检合格率或工序合格率)
定义:巡检合格率或工序合格率即零件生产过程一次合格数量除以零件生产总数量所得或加权平均所得;零件加工不良率为零件不合格总数出除以零件生产投入数量所得。
目的:用作过程度量,用来确定生产工序过程的质量水平。
公式:(巡检合格率或工序合格率)%=(工序一次合格数量/零件生产总数量)×100% 零件加工不良率=(零件不合格数量/零件生产投入数量)×1,000,000。
7顾客验货一次通过率
定义:指交付的产品,一次通过顾客验货合格接收的数量除以交付产品的总数量。
目的:用作结果度量,衡量出库成品的质量水平。
公式:顾客验货一次通过率%=(一次通过顾客验货合格接收的数量/交付产品的总数量)×100%。
8进料检验合格率
(来料一次检验合格率)
定义:一定时间内,进料检验合格数量除以进料检验数量所得。
目的:用作结果度量,用来监控供方供货质量水平。
公式:进料检验合格率%=(进料检验合格数量/进料检验总数量)×100%。
4质量成本
定义:简单定义为一定时期内的故障(损失)成本。
目的:用作结果度量,用来反映公司质量管理体系运行有效性的综合成果体现。
公式:质量成本=内部故障(损失)成本+外部故障(损失)成本;内部故障(损失)成本=报废损失费+返工或返修损失费;外部故障(损失)成本=顾客退货损失费+产品责任费+投诉费;质量成本占销售额比率=(质量成本÷销售额)×100%。
术语:内部故障(损失)成本:产品在交付前不能满足质量要求所造成的损失;外部故障(损失)成本:产品在交付后不能满足质量要求所造成的损失;报废损失费:因产成品、半成品、在制品达不到质量要求且无法修复或在经济上不值得修复造成报废所损失的费用;
返工或返修损失费:为修复不合格品使之达到质量要求或预期使用要求所支付的费用;顾客退货损失费:顾客退货的废品损失费用;
产品责任费:因产品质量故障而造成的有关赔偿损失费用;投诉费:对顾客投诉有质量问题的产品的修理或更换等所支出的费用。
10批量不合格率
定义:是指在一定期间内,在所有的检验批中,若因检验判定不合格而整个检验批需要返工(或返修或报废)的批数占总的检验批的批数的比例。
目的:用作结果度量,用来监控过程整体质量水平。
公式:批量不合格率= 不合格批数/总的检验批数*100%。
检验批:是提交进行检验的一批产品,也是作为检验对象而汇集起来的一批产品。
通常检验批应由同型号、同等级和同种类(尺寸、特性、成分等),且生产条件和生产时间基本相同的单位产品组成。
生产批:是指由生产计划决定的投入生产的一定数量的一批产品。
11质量损失率
公式:
其中:Ci:内部损失成本,它由1 )报废损失率、2)返修率、3)仃工费、
4)降级损失率、5)产品质量事故处理费等组成
Ce :外部损失成本,它由1)索赔费、2)退货损失费、3)折价损失费
4)保修费等组成
Po :工业总产值(均为现行价)
12错检率
公式:
错检率
其中:n : 抽样数量、d : 检出不合格数、b : 在合格品中检出不合格品数13漏检率
公式:
漏检率
14降低质量损失率
公式:
降低质量损失率
质量损失金额
去年同期质量实施金额
15成品项目检测合格率公式:
成品项目检测合格率检验成品合格项目数量同期检测成品项目总数
16不合格材料(公司内)退货率公式:
不合格材料公司内退货率车间退货总数同期检验总数
17不合格材料(公司外)退货率公式:
不合格材料公司外退货率进厂检验不合格总数同期检验总数
(进厂检验是退货)18成品产品退货率
公式:
成品产品退货率
退货数量
同期成品合格数量。