线材生产工艺专题培训课件
电缆生产工艺培训课件
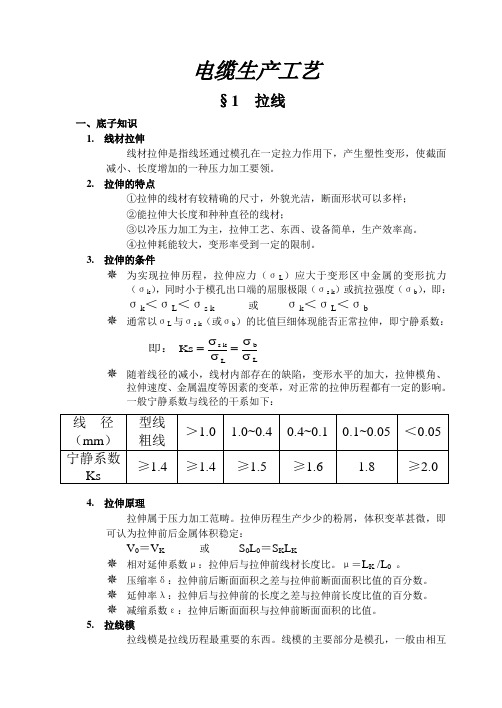
电缆生产工艺§1 拉线一、 底子知识 1. 线材拉伸线材拉伸是指线坯通过模孔在一定拉力作用下,产生塑性变形,使截面减小、长度增加的一种压力加工要领。
2. 拉伸的特点①拉伸的线材有较精确的尺寸,外貌光洁,断面形状可以多样; ②能拉伸大长度和种种直径的线材;③以冷压力加工为主,拉伸工艺、东西、设备简单,生产效率高。
④拉伸耗能较大,变形率受到一定的限制。
3. 拉伸的条件为实现拉伸历程,拉伸应力(σL )应大于变形区中金属的变形抗力 (σk ),同时小于模孔出口端的屈服极限(σs k )或抗拉强度(σb ),即:σk <σL <σs k 或 σk <σL <σb通常以σL 与σs k (或σb )的比值巨细体现能否正常拉伸,即宁静系数:随着线径的减小,线材内部存在的缺陷,变形水平的加大,拉伸模角、拉伸速度、金属温度等因素的变革,对正常的拉伸历程都有一定的影响。
一般宁静系数与线径的干系如下:4. 拉伸原理拉伸属于压力加工范畴。
拉伸历程生产少少的粉屑,体积变革甚微,即可认为拉伸前后金属体积稳定:V 0=V K 或 S 0L 0=S K L K相对延伸系数μ:拉伸后与拉伸前线材长度比。
μ=L K /L 0 。
压缩率δ:拉伸前后断面面积之差与拉伸前断面面积比值的百分数。
延伸率λ:拉伸后与拉伸前的长度之差与拉伸前长度比值的百分数。
减缩系数ε:拉伸后断面面积与拉伸前断面面积的比值。
5. 拉线模拉线模是拉线历程最重要的东西。
线模的主要部分是模孔,一般由相互LbL k s Ks σσ=σσ=即:圆滑连接的润滑区、事情区、定径区、出口区四个区域组成。
润滑区:润滑剂在这里停留并被带入事情区。
事情区:金属在这个区域内实现变形(变细、变长),实际与金属打仗的部分叫做变形段。
定径区:使拉线尺寸准确,形状切合要求,模孔直径即定径区直径。
出口区:不刮伤从定径区出来的线材,同时防备停机线材回弹引起断线。
6.拉伸历程线材的一次拉伸:从放线到收线只经过一道线模拉伸。
线材生产工艺及特点 ppt课件
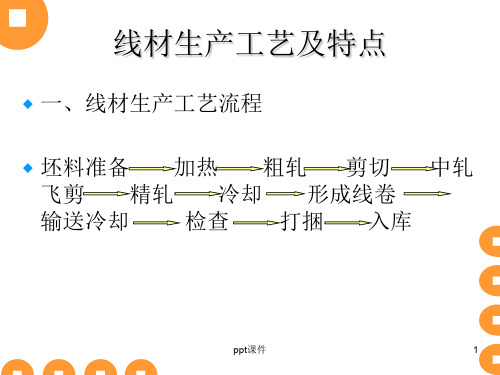
ppt课件
9
线材轧机布置方式
线材生产从坯料到成品断面尺寸变化较大, 轧制道次多,轧机布置一般分为粗轧、中轧 和精轧。
(1)粗轧机组的布置形式
1)横列式布置:横列式布置的粗轧机,一般 为二辊轧机或二辊交替式轧机。机架数目和 轧机大小根据所用坯料的大小来决定,辊径 一般为φ400~500mm,主传动电机一般用异步 交流电机传动。
这是最老式的布置,一般由5~7架轧机组成。 其传动形式与横列式布置的中轧机组相同, 可以是一台电机传动,也可以是两台电机从 两侧传动,相邻机架的轧制速度靠轧辊直径 的匹配来调节。
2)半连续式布置:精轧机组采用半连续布置
主要是复二重布置。
ppt课件
15
3)连续式布置:精轧机组连续式布置一般都 采用集体传动。这是因为精轧机组的轧制速
线材生产工艺及特点
一、线材生产工艺流程
坯料准备 加热 粗轧 剪切 中轧 飞剪 精轧 冷却 形成线卷 输送冷却 检查 打捆 入库
ppt课件
1
二、线材生产特点
线材特点为断面小、长度大、要求尺寸精度 和表面质量高。
线材发展:大盘重、小线径、使线材生产有 如下特点
1、坯料特点
1)断面小、尺寸长:有利于保证终轧温度, 适应线材发展需要。目前,最大断面 150mm2,最长22米。
ppt课件
7
高速线材轧机盘重大,采用散卷冷却。由精
轧机轧出的线材,经水冷管进行强制冷却, 在接近相变温度时由吐丝机将线材一圈一圈 地平铺在运行的辊道上,进行冷却。在输送
过程中可控制冷却速度,然后收集。散卷冷 却,冷却均匀而且冷却速度可控制,产品质
量好。通过 控制冷却,可以得到各种性能要 求的线材。而且线材的通条性能均匀。
高速线材生产工艺技术教材课件
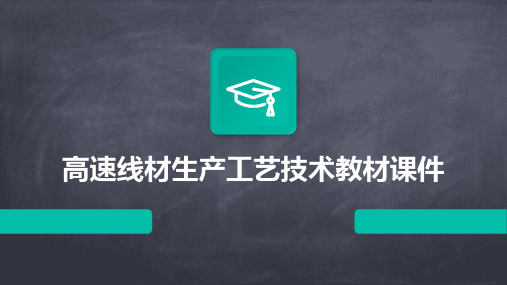
详细描述
04
高速线材生产质量控制
Chapter
03
生产环境控制
保持生产环境的清洁、卫生,防止灰尘、杂物等对产品质量的影响。
01
工艺参数控制
严格控制各项工艺参数,如温度、压力、时间等,确保生产过程的稳定性和产品质量的一致性。
02
设备维护与保养
定期对生产设备进行维护和保养,确保设备正常运行,延长设备使用寿命。
详细描述
连铸连轧设备将连续铸造和轧制工艺相结合,实现了从熔炼到成品的连续生产。这种设备具有高生产效率、低能耗、高成品质量等优点,是现代高速线材生产的重要发展方向。
总结词
热处理设备用于对高速线材进行加热、冷却等处理,以改善其机械性能和表面质量。
热处理设备通常包括加热炉、冷却装置、热处理介质等。通过合理的热处理工艺,可以改变高速线材的内部组织结构,提高其强度、韧性、耐腐蚀性等性能,以满足不同领域的需求。
循环经济
节能减排技术
感谢观看
THANKS
热处理技术是高速线材生产中的重要环节,通过合理的热处理工艺,可以调整线材的显微组织和机械性能,提高线材的综合性能。
总结词
热处理技术包括淬火、回火、退火等工艺,通过控制加热、保温和冷却等参数,实现对线材显微组织和机械性能的精确调控。合理的热处理工艺可以提高线材的强度、韧性、耐腐蚀性等性能,满足不同领域的需求。
高速线材生产发展趋势与展望
Chapter
采用先进的连铸工艺,提高钢水收得率和连铸坯质量,降低能耗和生产成本。
高效连铸技术
轧制新工艺
合金化技术
研究开发新的轧制工艺,如高速轧制、低温轧制等,提高线材产品的尺寸精度和表面质量。
通过添加合金元素,改善线材产品的机械性能和耐腐蚀性能,满足不同领域的需求。
高速线材生产工艺培训44页B
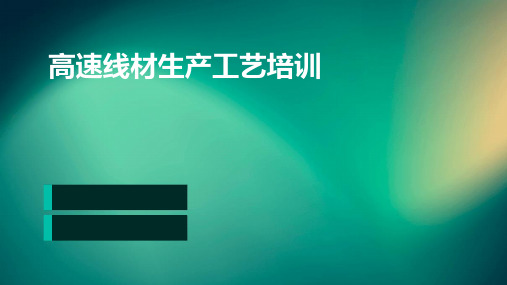
03 加热炉设备与操作技术要 点
加热炉类型及结构特点介绍
推钢式加热炉
炉长较长,炉子分为预热段、加 热段和均热段,加热段和均热段
炉顶设有平焰烧嘴。
步进式加热炉
靠炉底或水冷金属梁的上升、前 进、下降、后退等动作将料坯一 步一步地移送前进的连续加热炉。
环型加热炉
炉底为环形,料坯由装料口装入 后,在炉内作回转运动直至出料
原料准备阶段需要对原料进行检验、配料和 预处理等操作,确保原料质量符合要求。
加热阶段采用高温炉对原料进行加热, 使其达到轧制温度。
轧制阶段通过高速轧机对原料进行连续轧 制,形成所需尺寸和形状的线材产品。
冷却阶段采用水冷或空冷等方式对线材 产品进行冷却,以控制其组织和性能。
精整阶段对线材产品进行矫直、切断、 打包等操作,以便储存和运输。
预处理工艺参数
如加热温度、加热速度、保温时间等, 对产品的组织和性能有重要影响。
案例分析:优化原料选择与预处理方案
案例一
通过优化原料成分和预处理工艺 参数,提高产品的力学性能和耐
腐蚀性能。
案例二
针对特定产品要求,选择合适的原 料形态和尺寸,优化预处理方案, 提高产品成材率和生产效率。
案例三
通过对比分析不同原料供应商的产 品质量,选择质量稳定可靠的原料 供应商,确保生产顺利进行。
轧制过程中关键参数控制
1 2 3
轧制温度
控制加热炉温度和轧制速度,确保线材在轧制过 程中保持适宜的温度范围,以获得良好的塑性和 变形能力。
轧制力
合理调整轧辊直径、轧辊材质和轧制速度等参数, 以控制轧制力在适宜范围内,避免线材产生过大 的拉应力和表面缺陷。
张力控制
通过调整张力控制装置,使线材在轧制过程中保 持恒定的张力,确保线材的尺寸精度和表面质量。
线材培训资料(PPT 43页)

外被 铝箔 绝缘 导体 地线
2.铝箔 3.地线
16
VGA 线材结构
一、3+7:(*AWG*1C+S)*3Coax+*AWG*1P+*AWG*5C+ADB
1.外被 5.1P 6.单芯 7.3Coax
地线
5
1C 1 1P
3 3C
4
2C
2
中被 编织 铝箔 外被
绝缘 导体
2.编织 3.铝箔 4.地线 9.缠绕 8.中被
4P
3P
2.编织
4.麦拉
外被 铝箔 麦拉 绝缘 导体 编织
25
网线线材结构
四、CAT.6 UTP: *AWG*4P+F(”-”&”+”)
1.外被 2. 4P 3.一字架
1P
2P
4P
3P
外被 一字架
绝缘 导体
26
网线线材结构
五、CAT.6 FTP(STP): *AWG*4P+F(”-”&”+”)MDA
用热镀或电镀方式将金属锡镀于铜导体表面﹐以防止铜腐蚀/变色﹐及使导 体更易焊接。分为单根(或实心)镀锡铜线和绞合。绞合的目的是保持导体柔 软。 主要用于电子线上﹐一方面便于焊锡﹐另一方面由于导体较硬,不易弯曲﹐ 便于插到印刷电路板上面。
主要用于电子线上﹐性能同裸绞镀铜线﹐锡层附着性优于裸绞镀铜线。
3
成型时可不使用填充,但芯线必须经过过粉工艺处理。
电源线的芯线
电源线的芯线可以有二芯和三芯等。
电源线的材质1、导体使用裸铜; 2、绝来自和护套采用PVC。10
线材的结构
数据传输线
数据传输线的结构比较复杂,出现了地线、编织、铝箔 和麦拉(PET)等。这些结构部分都是起到屏蔽的作用。
线材工艺介绍.pptx

⑤ 在预精轧两个机组间设置一架碎断剪(2#飞剪),正常情况用 于轧件的头尾剪切,故障时将轧件导入碎断装置,同时配合 的还有两个机组前的卡断剪闭合。
机组 Ⅰ预精轧 Ⅱ预精轧
辊环材质 球磨铸铁 硬质合金
最大辊径 285mm 208mm
最大转速 740rpm 880rpm
马钢第三钢轧总厂线材分厂
技术工艺类课件
一、线材生产线总体概括
➢ 马钢第三钢轧总厂线材分厂是目前国内重要的 线材生产基地,于2002-2003年与SMS公司合作, 对主体设备进行全面改造,形成了70万吨/年的 高品质线材生产能力。
➢ 在轧制工艺上能够实现世界先进的工艺技术— —热机轧制,多途径的大圆盘活套控制技术, 为控轧控冷工艺的良好实施提供了基础;加长 的斯太尔摩空冷辊道可实现延迟、强迫等冷却 方式。
2010.03.08
8
马钢第三钢轧总厂线材分厂
技术工艺类课件
2.4、精轧机组工艺流程及技术参数
PR2
LOOP6A PR3及3#飞剪
FB机组
6#WB 7~8#WB
PR1 LOOP6B 9#WB
5#WB
I. 精轧机组(FB):德国西马克公司引进,45°无扭精轧机组, 高速设备,共8个道次。主要承担Φ6.5~11.0mm规格的各 种线材生产。优点包括:效率高、轧件尺寸精度高、调整 操作方便。
最大线速度 70m/s
最高转速 820rpm
2010.03.08
10
马钢第三钢轧总厂线材分厂
技术工艺类课件
2.5、减定径机组工艺流程及技术参数
Ⅰ. 工艺流程
来料(半成品) (LOOP7储套消张) 10#~13#WB冷却 测径仪测量尺寸
《棒线材生产特点及工艺》课件
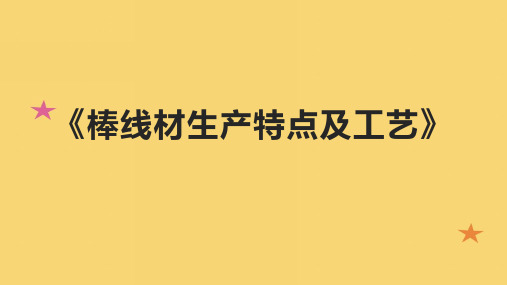
2023/12/18
12
2023/12/18
13
2023/12/18
14
生产特点及工艺
冷却和精整
线材:
精轧
水冷
吐丝机
检查
包装
散卷控制冷却
集卷
2023/12/18
15
上料台架 钢坯辊道 称重台 加热炉加热 钢坯出炉 高压水除鳞 夹送钢坯 粗轧机轧制 6HV 1#飞剪切头 中轧机组轧制6HV
2#飞剪切头 预精轧机组轧制 6HV 水箱冷却 3#飞剪切头 精轧机组轧制10 水箱冷却 减定径机组轧制 水箱冷却 线材测径 夹送吐丝
外车间热处理
收集Leabharlann 精整棒材入库2023/12/18
10
生产特点及工艺
2.2线材生产工艺
坯料:
✓ 连铸坯为主,初轧坯 ✓ 方坯:120-150mm,坯料长Max:22M ✓ 检查与清理严格
加热和轧制
冷坯加热 (连铸坯热装加热)
粗轧
中轧
(线材预精
轧)
精轧
2023/12/18
11
生产特点及工艺
✓ 线材轧制的加热温度较低 ; ✓ 步进式加热炉; ✓ 坯料两端加热温度高于中间温度; ✓ 轧制速度快,小辊径,高转速; ✓ 线材的合适轧制方式是连轧; ✓ 机架多,分工细; ✓ 轧机平立(VH布置)交替布置,线材轧机的机架数为21-28架; ✓ 线材的孔型:箱-椭圆-圆
棒 、 线 材 的 断 面 形 状 简 单 , 用 量 巨 大 , 适 于 进 行 大 规模的专业化生产。(国内占总产量40%,世界最高)
线 材 的 断 面 尺 寸 是 热 轧 材 中 最 小 的 , 所 用 的 轧 机 是 最小型的。轧件的总延伸非常大,需要的轧制道次 很多。
线材生产工艺培训教材PPT课件
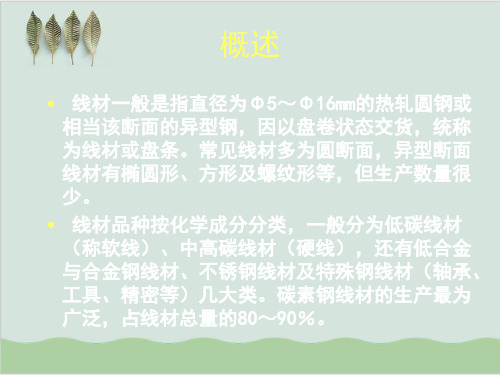
线材轧线上总的来说布置有两种剪机,一种是用于切头尾和事故碎断的剪机,即我们常说的飞剪,由电机驱动,剪切过程中剪刃随轧件同步前进,如轧线上的1#、2#、3#(组合工作,由3#飞剪和碎断剪组成)飞剪;另一种是用于事故时阻止后续轧件继续进入相应机组的的剪机—卡断剪,压缩空气驱动,如布置在1#轧机前、预精轧机组和精轧机组前的卡断剪(该两组剪机已取消使用)
高速线材轧机特点
一般将轧制速度大于40m/s(区分高线和普线的一个基本特点)的线材轧机称为高速线材轧机。 高速线材轧机的生产工艺特点: 连续、高速、无扭和控冷。其中高速轧制 是最主要的工艺特点(此外,单线、微张 力、组合结构、碳化钨辊环和自动化)。 高速线材产品特点: 盘重大、精度高、性能优良。
1#水咀
1、3#水咀
1、3、5#水咀
反吹水咀、反吹气咀
3#水冷箱开启
1#水咀
1、3#水咀
1、3、5#水咀
反吹水咀、反吹气咀
吐丝机夹送辊投入状态
夹尾
夹送辊超前率
%
2.0-2.5
吐丝机夹送辊尾部滞后率
%
1.0-1.5
吐丝机超前率
%
2.5-3.0
风机开启
台
1
2
2
夏季高温时分别可适当增开1台
高速无扭精轧
高速无扭精轧工艺是现代线材生产的核心技术之一,它是针对以往各种线材轧机存在诸多问题,综合解决产品多品种规格、高断面尺寸精度、大盘卷和高生产率的有效手段。唯精轧高速度才能有高生产率。才能解决大盘重线材轧制过程的温降问题。精轧的高速度要求轧制过程中轧件无扭转,否则事故频发,轧制根本无法进行。因此,高速无扭精轧是高速线材轧机的一个基本特点。
生产工艺-轧制
- 1、下载文档前请自行甄别文档内容的完整性,平台不提供额外的编辑、内容补充、找答案等附加服务。
- 2、"仅部分预览"的文档,不可在线预览部分如存在完整性等问题,可反馈申请退款(可完整预览的文档不适用该条件!)。
- 3、如文档侵犯您的权益,请联系客服反馈,我们会尽快为您处理(人工客服工作时间:9:00-18:30)。
各区域主要设备及工艺特点简介
加热炉:加热炉为端进侧出推钢式重油加热 炉,设计加热能力180吨/小时,采用两段式 加热制度,即根据炉内的供热分配分为加热 段和均热段,加热段的主要作用就是快速加 热钢坯,使其达到需要温度,因为升温速度 快,所以钢坯通体温度不均匀,这时均热段 的作用就得以发挥,通过均热段使钢坯表面、 心部及头尾温度达到一致。缺点:钢坯易出 现“黑印”(与炉底纵水管接触位置),炉 内钢坯不能完全出净。
高速线材轧机的发展过程
轧制速度是高速线材轧机发展水平的标志, 按照轧制速度可将现代轧机分为如下几代:
第一代,1966~1969年,轧制速度43~50m/s; 第二代,1970~1975年,轧制速度50~60 m/s; 第三代,1976~1978年,轧制速度61~75m/s; 第四代,1979~1980年,轧制速度75~80m/s; 第五代,1981~1985年,轧制速度80~100m/s; 第六代,1986年以后,轧制速度100~120m/s。 现在又出现了模块化轧机,进一步缩小了轧机体积,降
粗中轧调整控制方式为手动控制速度和压下实现微 张力轧制,粗中轧机组作用是以较大的压下量实现 大的变形和延伸,为预精轧机组输送合适尺寸的轧 件。缺点是5#机架后椭圆轧件进入圆孔机架需要扭 转90°,对导卫的安装、调整要求高。
各区域主要设备及工艺特点简介
预精轧:预精轧机组为单机传动,双线布置, 每线4台285平立交替悬臂式轧机,工作辊采 用WC硬质合金辊环,在机组的前后设置水平 活套,机组机架间设有立活套。控制方式为 手动加活套自动调节实现无张力轧制。预精 轧机组的作用是轧件延伸,提高轧件表面质 量和尺寸精度,为精轧机组输送合适的轧件
低轧机重心和传动轴高度,减小了轧机运转过程中的震 动等不利因素,使轧制速度达到更高水平。
线材生产线简介
恒钢线材厂05年3月投产,设计年产量100万吨,设计速度90 米/秒,采用150mm*150mm方形断面连铸坯,可生产 Φ5.5~Φ16规格光面盘圆钢筋和Φ6、Φ8、Φ10 螺纹钢筋, 目前我们主要生产Φ6.5、Φ8、Φ10的HPB235普通建筑用钢 筋,受轧机因素所限最高速度只能达到70m/s。
线材生产按其流程特点基本上划分为3大工序(可细分为6个 工序),即原料加热、轧制控冷、精整成品库。轧制工序的 区域包括从加热炉出口直至吐丝机区域。轧制区中最主要的 设备是轧线上的主轧机(包括传动装置),以及一些辅助设 备(飞剪、活套等),全轧线共42台轧机,双线布置,采用 仿摩根5代45°顶交精轧机,水冷加风冷的斯太尔摩冷却工 艺。
工艺流程
钢坯垛 上料台架 入炉辊道 称重 推钢入炉 加热 出炉辊道 1#卡断剪 粗轧(1)
预水冷 预精轧 1#活套 2#飞剪 导钢装置 中轧 1#飞剪 粗轧(2) 分钢辊道
3#飞剪 5#活套 碎断剪
ห้องสมุดไป่ตู้精轧
入库
卸卷
水冷 夹送、吐丝 风冷运输 集卷 运卷上钩 P/F线
挂牌
称重
打包 检验 头尾修剪 质量检查
活套作用:贮存多余轧件用以应对轧机转速突然升 高和降低引起的秒流量变化,实现无张力轧制,确 保轧件尺寸精度。
各区域主要设备及工艺特点简介
精轧机:精轧机组为集体传动,A、B双线布置,分 别由一台5500KW交流电机拖动,每线10架轧机(5架 230轧机和5架170轧机)交替与水平面成45°和 135°设置,即相临机架互相垂直,与平立交替布置 相当,轧件不需扭转,采用WC辊环。
控制方式为:精确的传动比、配辊及辊缝设定实现 微张力轧制。作用以小的压下使轧件逐渐减径延伸, 得到表面质量和尺寸精度良好的成品。
生产过程中不是所有机架都会用到,根据规格不同, 投入使用的机架数不同。
辅传动设备—夹送辊、吐丝机
夹送辊位于吐丝机之前,水冷段之后,其作用是夹 持水冷后的线材顺利进入吐丝机布圈,对于小规格 (高速度)线材尾部脱离精轧机后控制其降速,对 于大规格(低速度)则控制其升速。
各区域主要设备及工艺特点简介
粗中轧:粗中轧共14台闭口式轧机,单机传动, 1#~6#为550轧机、7#~12#为450轧机、13# 14#为350 轧机。
其中1#~4#为平立交替单机单线,不与后面机架连轧, 4#轧机后设分钢辊道(3段),通过分钢辊道中的拨 料杆将轧件拨入A线或B线,喂入后续轧机进行轧制。 5#~14#全为水平轧机且为单机双线。
线材生产工艺
概述
线材一般是指直径为Φ5~Φ16mm的热轧圆钢或 相当该断面的异型钢,因以盘卷状态交货,统称 为线材或盘条。常见线材多为圆断面,异型断面 线材有椭圆形、方形及螺纹形等,但生产数量很 少。
线材品种按化学成分分类,一般分为低碳线材 (称软线)、中高碳线材(硬线),还有低合金 与合金钢线材、不锈钢线材及特殊钢线材(轴承、 工具、精密等)几大类。碳素钢线材的生产最为 广泛,占线材总量的80~90%。
高速无扭精轧
高速无扭精轧工艺是现代线材生产的核心技 术之一,它是针对以往各种线材轧机存在诸 多问题,综合解决产品多品种规格、高断面 尺寸精度、大盘卷和高生产率的有效手段。 唯精轧高速度才能有高生产率。才能解决大 盘重线材轧制过程的温降问题。精轧的高速 度要求轧制过程中轧件无扭转,否则事故频 发,轧制根本无法进行。因此,高速无扭精 轧是高速线材轧机的一个基本特点。
活套
活套布置:线材轧线每线设有5个活套,分别为位于 预精轧机组和精轧机组前的1#和5#水平活套(我们 习惯称为侧活套)、位于预精轧机组各机架间的2# 3# 4#立式活套。之所以将活套都布置在该区域,是 因为预精轧机组轧制速度相对较高,单机传动,因 各种原因引起的秒流量较小的变化既有可能发生堆 钢事故。
高速线材轧机特点
一般将轧制速度大于40m/s(区分高线和普 线的一个基本特点)的线材轧机称为高速线 材轧机。
高速线材轧机的生产工艺特点: 连续、高速、无扭和控冷。其中高速轧制
是最主要的工艺特点(此外,单线、微张 力、 组合结构、碳化钨辊环和自动化)。 高速线材产品特点:
盘重大、精度高、性能优良。