[资料]粉末的烧结工艺
金属粉末直接烧结法

⾦属粉末直接烧结法⼀、引⾔⾦属粉末直接烧结法是⼀种制造⾦属零件的重要⽅法,具有近净成形、节能环保等优点。
此技术是将⾦属粉末经过成形、烧结和后处理等⼯序,最终得到具有所需形状、结构和性能的⾦属零件。
本⽂将详细介绍⾦属粉末直接烧结法的原理、⼯艺流程、应⽤领域以及发展前景。
⼆、⾦属粉末直接烧结法的基本原理⾦属粉末直接烧结法的基本原理是将⾦属粉末加热⾄其熔点以下的温度,使其在固态下通过原⼦或分⼦的扩散和流动,实现粉末颗粒之间的结合,形成具有所需形状和性能的⾦属零件。
在烧结过程中,⾦属粉末的表⾯会形成液相,有助于颗粒之间的润湿和结合。
随着温度的升⾼,原⼦或分⼦的扩散和流动速度加快,使得颗粒之间的结合更加紧密,最终得到⾼致密度的⾦属零件。
三、⾦属粉末直接烧结法的⼯艺流程1.制备⾦属粉末:根据所需零件的材质和性能要求,选择合适的⾦属粉末。
⾦属粉末的粒度、纯度、松装密度等参数对最终零件的性能有重要影响。
2.成形:将⾦属粉末装⼊模具中,施加压⼒或磁场等外⼒,使粉末在模具内成形为所需形状的坯体。
成形的⽅法有多种,如压制成形、注射成形等。
3.烧结:将成形后的坯体加热⾄烧结温度,使粉末颗粒之间发⽣结合,形成具有所需强度和致密度的⾦属零件。
烧结温度和时间的选择是关键因素,直接影响零件的性能。
4.后处理:烧结后的零件可能需要进⾏热处理、机加⼯、表⾯处理等后处理⼯序,以提⾼其性能和满⾜使⽤要求。
四、⾦属粉末直接烧结法的应⽤领域⾦属粉末直接烧结法具有⼴泛的应⽤领域,包括汽⻋制造、航空航天、电⼦、医疗器械等。
在汽⻋制造领域,利⽤⾦属粉末直接烧结法可以制造⾼性能的发动机零件、⻮轮、刹⻋盘等。
在航空航天领域,该⽅法可⽤于制造轻质⾼强的航空结构件、发动机零件等。
在电⼦领域,可以制造⾼性能的电⼦元件和电路板。
在医疗器械领域,可以制造⾼精度、⾼耐磨性的⽛科种植体、⻣科⼿术⽤具等。
五、⾦属粉末直接烧结法的发展前景随着科技的不断进步和⼯业⽣产的快速发展,⾦属粉末直接烧结法在技术进步和应⽤拓展⽅⾯具有⼴阔的发展前景。
烧结的工艺技术
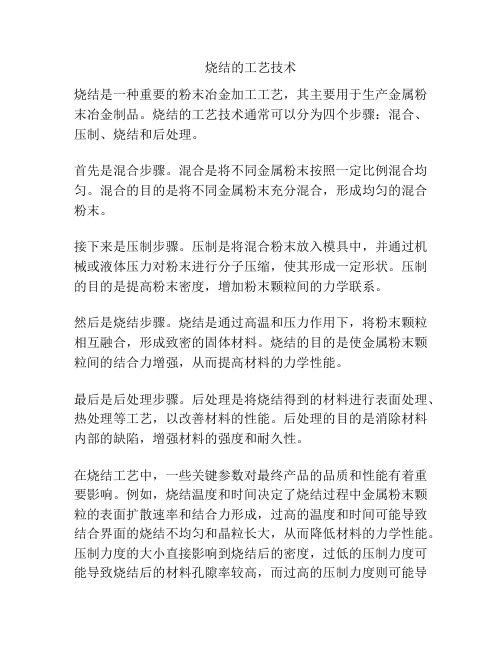
烧结的工艺技术烧结是一种重要的粉末冶金加工工艺,其主要用于生产金属粉末冶金制品。
烧结的工艺技术通常可以分为四个步骤:混合、压制、烧结和后处理。
首先是混合步骤。
混合是将不同金属粉末按照一定比例混合均匀。
混合的目的是将不同金属粉末充分混合,形成均匀的混合粉末。
接下来是压制步骤。
压制是将混合粉末放入模具中,并通过机械或液体压力对粉末进行分子压缩,使其形成一定形状。
压制的目的是提高粉末密度,增加粉末颗粒间的力学联系。
然后是烧结步骤。
烧结是通过高温和压力作用下,将粉末颗粒相互融合,形成致密的固体材料。
烧结的目的是使金属粉末颗粒间的结合力增强,从而提高材料的力学性能。
最后是后处理步骤。
后处理是将烧结得到的材料进行表面处理、热处理等工艺,以改善材料的性能。
后处理的目的是消除材料内部的缺陷,增强材料的强度和耐久性。
在烧结工艺中,一些关键参数对最终产品的品质和性能有着重要影响。
例如,烧结温度和时间决定了烧结过程中金属粉末颗粒的表面扩散速率和结合力形成,过高的温度和时间可能导致结合界面的烧结不均匀和晶粒长大,从而降低材料的力学性能。
压制力度的大小直接影响到烧结后的密度,过低的压制力度可能导致烧结后的材料孔隙率较高,而过高的压制力度则可能导致烧结成型困难。
此外,烧结工艺中的气氛和保护措施,以及烧结过程中的冷却速率等因素也会对烧结工艺和产品质量产生影响。
总的来说,烧结作为一种重要的粉末冶金加工工艺,具有许多优点,如可以制备高强度、高硬度和高耐磨性的制品,且原材料利用率高、产品尺寸精度高等。
但是,烧结工艺也存在一些挑战,如烧结时控制工艺参数较为复杂,产品质量易受原料和工艺影响,烧结成本相对较高等。
因此,烧结工艺技术的研究和改进仍然具有重要意义,可进一步提高产品质量和开发新材料。
烧结工艺流程简述
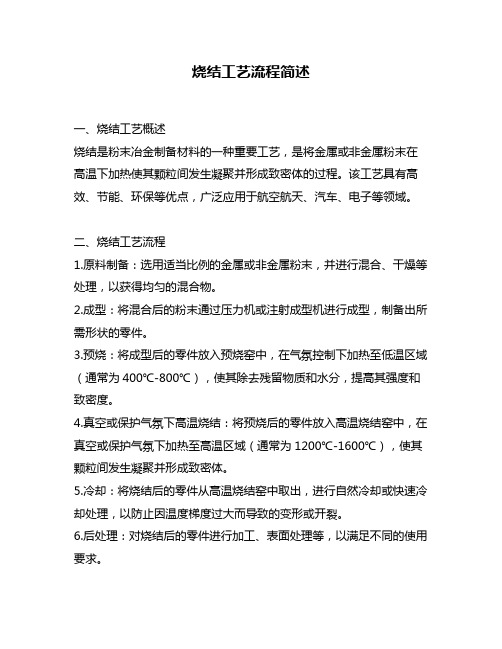
烧结工艺流程简述一、烧结工艺概述烧结是粉末冶金制备材料的一种重要工艺,是将金属或非金属粉末在高温下加热使其颗粒间发生凝聚并形成致密体的过程。
该工艺具有高效、节能、环保等优点,广泛应用于航空航天、汽车、电子等领域。
二、烧结工艺流程1.原料制备:选用适当比例的金属或非金属粉末,并进行混合、干燥等处理,以获得均匀的混合物。
2.成型:将混合后的粉末通过压力机或注射成型机进行成型,制备出所需形状的零件。
3.预烧:将成型后的零件放入预烧窑中,在气氛控制下加热至低温区域(通常为400℃-800℃),使其除去残留物质和水分,提高其强度和致密度。
4.真空或保护气氛下高温烧结:将预烧后的零件放入高温烧结窑中,在真空或保护气氛下加热至高温区域(通常为1200℃-1600℃),使其颗粒间发生凝聚并形成致密体。
5.冷却:将烧结后的零件从高温烧结窑中取出,进行自然冷却或快速冷却处理,以防止因温度梯度过大而导致的变形或开裂。
6.后处理:对烧结后的零件进行加工、表面处理等,以满足不同的使用要求。
三、烧结工艺参数1.预烧温度:预烧温度过低会导致残留物质和水分未完全除去,影响零件强度和致密度;预烧温度过高则会使零件表面氧化、变质等不良反应发生。
2.高温烧结温度:高温烧结温度是影响零件致密度和力学性能的重要参数。
一般情况下,高温烧结温度越高,零件的致密度越大、力学性能越好。
但超过一定范围后,会出现晶粒长大、相变等问题。
3.保护气氛:保护气氛可以有效防止零件表面氧化、变质等问题,提高烧结质量。
常用的保护气氛有氢气、氮气、氩气等。
4.烧结时间:烧结时间是影响零件致密度和力学性能的重要参数。
一般情况下,烧结时间越长,零件的致密度越大、力学性能越好。
但过长的烧结时间会导致晶粒长大、相变等问题。
四、烧结工艺优点1.高效:粉末冶金制备材料的成型和加工过程简单,可实现快速生产。
2.节能:相比于传统工艺,烧结工艺耗能较低。
3.环保:粉末冶金制备材料过程中无废水废气排放,符合环保要求。
粉末冶金烧结工艺
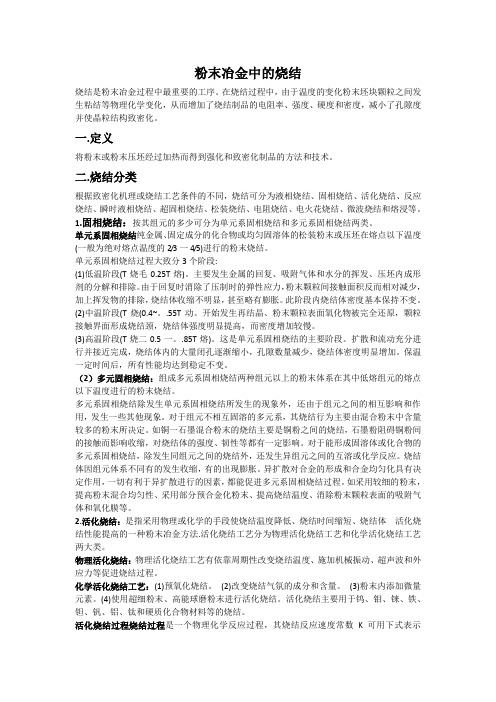
粉末冶金中的烧结烧结是粉末冶金过程中最重要的工序。
在烧结过程中,由于温度的变化粉末坯块颗粒之间发生粘结等物理化学变化,从而增加了烧结制品的电阻率、强度、硬度和密度,减小了孔隙度并使晶粒结构致密化。
一.定义将粉末或粉末压坯经过加热而得到强化和致密化制品的方法和技术。
二.烧结分类根据致密化机理或烧结工艺条件的不同,烧结可分为液相烧结、固相烧结、活化烧结、反应烧结、瞬时液相烧结、超固相烧结、松装烧结、电阻烧结、电火花烧结、微波烧结和熔浸等。
1.固相烧结:按其组元的多少可分为单元系固相烧结和多元系固相烧结两类。
单元系固相烧结纯金属、固定成分的化合物或均匀固溶体的松装粉末或压坯在熔点以下温度(一般为绝对熔点温度的2/3一4/5)进行的粉末烧结。
单元系固相烧结过程大致分3个阶段:(1)低温阶段(T烧毛0.25T熔)。
主要发生金属的回复、吸附气体和水分的挥发、压坯内成形剂的分解和排除。
由于回复时消除了压制时的弹性应力,粉末颗粒间接触面积反而相对减少,加上挥发物的排除,烧结体收缩不明显,甚至略有膨胀。
此阶段内烧结体密度基本保持不变。
(2)中温阶段(T烧(0.4~。
.55T动。
开始发生再结晶、粉末颗粒表面氧化物被完全还原,颗粒接触界面形成烧结颈,烧结体强度明显提高,而密度增加较慢。
(3)高温阶段(T烧二0.5一。
.85T熔)。
这是单元系固相烧结的主要阶段。
扩散和流动充分进行并接近完成,烧结体内的大量闭孔逐渐缩小,孔隙数量减少,烧结体密度明显增加。
保温一定时间后,所有性能均达到稳定不变。
(2)多元固相烧结:组成多元系固相烧结两种组元以上的粉末体系在其中低熔组元的熔点以下温度进行的粉末烧结。
多元系固相烧结除发生单元系固相烧结所发生的现象外,还由于组元之间的相互影响和作用,发生一些其他现象。
对于组元不相互固溶的多元系,其烧结行为主要由混合粉末中含量较多的粉末所决定。
如铜一石墨混合粉末的烧结主要是铜粉之间的烧结,石墨粉阻碍铜粉间的接触而影响收缩,对烧结体的强度、韧性等都有一定影响。
金属粉末材料间接烧结工艺过程

金属粉末材料间接烧结工艺过程金属粉末材料是一种广泛应用于各种领域的材料,特别是在航空航天、汽车、医疗器械等高端制造领域拥有广泛的应用。
而金属粉末材料的制造则需要通过一系列的加工工艺来获得。
这其中,间接烧结工艺是一种重要的金属粉末材料加工方式。
间接烧结工艺是指将金属粉末材料加入到形状设计好的烧结模具中,在高温高压下进行热压、扩散、再结晶等进程。
基本流程为:向模具中加入粉末、置于恒压下、通过预热、烧结、再结晶等步骤进行制备金属材料。
该工艺在保证金属颗粒之间能够良好结合的前提之下,又能给金属材料带来更好的力学性能。
从工艺流程上来说,间接烧结工艺主要具有以下步骤:粉末制备、制备成型、初热处理、中温烧结、高温处理、再结晶等步骤。
其中,粉末制备是关键,这需要使用多种技术进行制备,例如:机械合金化、气相沉积、真空热压等多种方法。
而在加入烧结模具中后,就需要通过调整温度和压力进行烧结过程。
间接烧结过程中,金属粉末之间的结合主要包括扩散和液相烧结两个方面。
在烧结过程中,热流对粉末材料的影响也非常明显,需要切合实际进行调整。
使用间接烧结工艺加工所得到的金属粉末材料具有很高的密度和良好的力学性能。
同时,这种工艺更适用于大块金属的制备,而且能够得到更高的质量和性能。
与其他材料制备方法相比,间接烧结工艺还具有精度高、成本低、易于控制等优势,因此广泛应用于各种行业。
特别是在高端制造领域,间接烧结工艺被广泛使用,例如航空航天、汽车、医疗器械的制造中的金属材料制备等领域。
综上所述,间接烧结工艺具有重要的意义。
通过这种工艺制备出的金属材料具有优良的力学性能和高密度。
同时,这种方法适用于大块金属的制备,成本低,容易控制,精度高。
这些优势使得间接烧结工艺得到广泛应用,成为高端制造领域的重要工艺之一。
粉末烧结技术
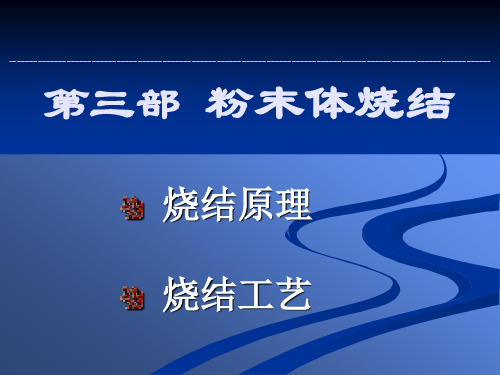
加压烧结—加压和加热同时并用,以达到消除孔
隙的目的,从而大幅度提高粉末制品的性能。常用
的加压烧结工艺有热压、热等静压及烧结-热等静压。
热压—将粉末装在压模内,在加压的同时把粉末加热到熔
点以下,使之加速烧结成比较均匀致密的制品。
热等静压—把粉末压坯或把装入特制容器内的粉末置于热
等静压机高压容器内,使其烧结成致密的材料或零件的过 程。
电火花等离子烧结—也叫等离子活化烧结或电火
花等离子烧结,是利用粉末间火花放电多产生的等
离子活化颗粒,同时在外力作用下进行的一种特殊
烧结方法。
真空热压烧结炉图
微波生物陶瓷烧结炉图
微波烧结炉图
热等静压烧结炉图
放电等离子烧结炉图
烧结-热等静压—把压坯放入烧结-热等静压设备的高压容
器内,先进行脱蜡、烧结,再充入高压气体进行热等静压。
反应烧结—先将原材料(如制备Si3N4时使用Si粉)
粉末以适当方式成形后,在一定气氛中(如氮气)
加热发生原位反应合成所需的材料并同时发生烧结。
微波烧结—材料内部整体地吸收微波能并被加热,
使得在微波场中试样内部的热梯度和热流方向与常规 烧结的试样相反。
表面张力造成的一种机械力,它垂直作用于烧结颈曲面上, 使烧结颈向外扩大,最终形成孔隙网。 过剩空位浓度梯度将引起烧结颈表面下微小区域内的空位 向粉末颗粒内扩散,从而造成原子在相反方向上的迁移, 使颈部得以长大。
烧结时物质迁移
烧结过程的传质机理很复杂,目前大体上有四种说法
粘塑性流动过程 扩散过程,包括体积、 表面和界面的扩散
依靠外在条件变 化活化烧结过程
提高粉末 本身活性
二、烧结工艺
烧结工艺
无压烧结
烧结工艺说明

烧结工艺烧结是粉末或粉末压坯加热到低于其中基本成分的熔点的温度,然后以一定的方法和速度冷却到室温的过程。
烧结的结果是粉末颗粒之间发生粘结,烧结体的强度增加,把粉末颗粒的聚集体变成为晶粒的聚结体,从而获得所需的物理、机械性能的制品或材料。
1.低温预烧阶段在此阶段主要发生金属的回复及吸附气体和水分的挥发,压坯内成形剂的分解和排除等。
2.中温升温烧结阶段此阶段开始出现再结晶,在颗粒内,变形的晶粒得以恢复,改组为新晶粒,同时表面的氧化物被还原,颗粒界面形成烧结颈。
3.高温保温完成烧结阶段此阶段中的扩散和流动充分的进行和接近完成,形成大量闭孔,并继续缩小,使孔隙尺寸和孔隙总数有所减少,烧结体密度明显增加。
烧结生产工艺流程[1]1.烧结的概念将各种粉状含铁原料,配入适量的燃料和熔剂,加入适量的水,经混合和造球后在烧结设备上使物料发生一系列物理化学变化,将矿粉颗粒黏结成块的过程。
2. 烧结生产的工艺流程目前生产上广泛采用带式抽风烧结机生产烧结矿。
烧结生产的工艺流程如图2—4所示。
主要包括烧结料的准备,配料与混合,烧结和产品处理等工序。
抽风烧结工艺流程烧结原料的准备①含铁原料含铁量较高、粒度<5mm的矿粉,铁精矿,高炉炉尘,轧钢皮,钢渣等。
一般要求含铁原料品位高,成分稳定,杂质少。
②熔剂要求熔剂中有效CaO含量高,杂质少,成分稳定,含水3%左右,粒度小于3mm的占90%以上。
在烧结料中加入一定量的白云石,使烧结矿含有适当的MgO,对烧结过程有良好的作用,可以提高烧结矿的质量。
③燃料主要为焦粉和无烟煤。
对燃料的要求是固定碳含量高,灰分低,挥发分低,含硫低,成分稳定,含水小于10%,粒度小于3mm的占95%以上。
对入厂烧结原料的一般要求见表2—2。
入厂烧结原料一般要求配料与混合①配料配料目的:获得化学成分和物理性质稳定的烧结矿,满足高炉冶炼的要求。
常用的配料方法:容积配料法和质量配料法。
容积配料法是基于物料堆积密度不变,原料的质量与体积成比例这一条件进行的。
烧结工艺介绍

烧结工艺介绍烧结工艺是一种常见的冶金工艺,用于将粉末状物质加热至接触点熔融,形成固态结合体的过程。
本文将介绍烧结工艺的原理、应用范围以及工艺流程。
一、原理烧结是通过热量作用使粉末颗粒表面融合,而形成较强的固态接触的过程。
烧结过程中,粉末颗粒相互接触,颗粒表面由于温度升高而软化或熔化,粒子间形成了弥散相和连续相,使颗粒间形成了较强的结合力。
通过控制加热温度、时间以及加压力度等工艺参数,使颗粒状物质在相互接触的同时,形成致密且高强度的结构体。
二、应用范围烧结工艺在冶金、陶瓷、粉末冶金、高分子材料等领域有着广泛的应用。
1. 冶金领域烧结工艺在冶金领域广泛应用于粉末冶金制品的制备,如金属粉末冶金零件、冶金陶瓷、高合金材料等。
2. 陶瓷领域烧结是陶瓷领域中常用的制备工艺之一,通过烧结工艺可以制备出具有高强度和良好耐磨性的陶瓷制品,如瓷砖、陶瓷碗碟等。
3. 粉末冶金领域粉末冶金是一种以粉末为原料,通过烧结工艺制备制品的工艺。
烧结工艺可以将金属粉末制备成各种零件,如齿轮、凸轮等。
4. 高分子材料领域烧结工艺在高分子材料领域中用于制备具有特殊性能的塑料制品,如高强度塑料零件、高耐磨塑料制品等。
三、工艺流程烧结工艺的基本流程包括原料制备、粉末颗粒的装填、加热烧结和冷却等步骤。
1. 原料制备:首先需要根据所需制品的要求,选择合适的原料并对其进行加工和处理。
这一步骤可以包括粉末的混合、筛分以及添加特定添加剂等。
2. 粉末颗粒的装填:将经过处理的粉末颗粒通过特定的装填方式填入烧结模具中。
装填要求均匀且适量,以确保烧结过程中的热量传导均匀。
3. 加热烧结:将装有粉末颗粒的模具放入烧结炉中,加热至一定温度并保持一定时间。
温度和时间的选择根据所需制品的要求来确定。
4. 冷却:烧结结束后,需要进行冷却处理。
冷却可以通过自然冷却或者采用特殊的冷却方法来进行。
四、工艺优势烧结工艺相对于其他加工方式具有以下优势:1. 提高材料的致密度和强度。