脉动饮料瓶盖子模具设计
瓶盖注塑模具设计.ppt

瓶盖注塑模具设计1. 引言注塑模具是一种用于制造塑料制品的工具,常用于生产各种类型的瓶盖。
瓶盖注塑模具设计的目标是实现高效、精确和可靠的生产过程,以满足市场的需求。
本文档将介绍瓶盖注塑模具设计的关键要素,包括模具的结构、选材、制造工艺和检验方法等。
2. 模具设计要素在进行瓶盖注塑模具设计之前,需要考虑以下几个要素:2.1 瓶盖形状和尺寸瓶盖的形状和尺寸将直接影响到模具的设计。
设计师需要根据瓶盖的要求确定模具的尺寸和形状,包括瓶盖的直径、高度、壁厚等。
2.2 模具结构模具的结构决定了瓶盖的成型过程和质量。
常见的模具结构包括单腔模具、多腔模具和家模具等。
不同的模具结构会影响到注塑工艺和成本。
2.3 材料选用模具的选材是瓶盖注塑模具设计的重要环节。
常用的模具材料包括优质钢材和合金钢等。
合理选择材料能够提高模具的硬度、耐磨性和使用寿命。
2.4 模具制造工艺模具制造工艺决定了模具的精度和寿命。
常见的模具制造工艺包括加工中心加工、电火花加工和线切割等。
合理选择工艺可以提高模具的制造效率和质量。
2.5 模具调试和调整模具调试和调整是确保瓶盖注塑模具正常运行的关键环节。
设计师需要根据生产工艺和成型效果进行模具调试和调整,以提高模具的稳定性和生产效率。
3. 模具制造过程瓶盖注塑模具的制造过程主要包括以下几个步骤:3.1 模具设计在模具设计阶段,设计师需要根据瓶盖的要求和生产工艺,绘制出模具的结构设计图,确定模具的尺寸、形状和材料。
3.2 模具加工模具加工是将设计好的模具结构图转化为实际模具的过程。
常见的模具加工方法包括数控机床加工、车床加工和磨床加工等。
通过精密加工,可以保证模具的精度和质量。
3.3 模具装调模具装调是将制造好的模具安装到注塑机上,并进行调试和校准的过程。
在这个过程中,操作人员需要调整模具的位置、温度和注塑参数,以确保模具的正常运行和瓶盖的质量。
3.4 模具测试模具测试是对制造好的模具进行性能测试的过程。
瓶盖塑料模具设计
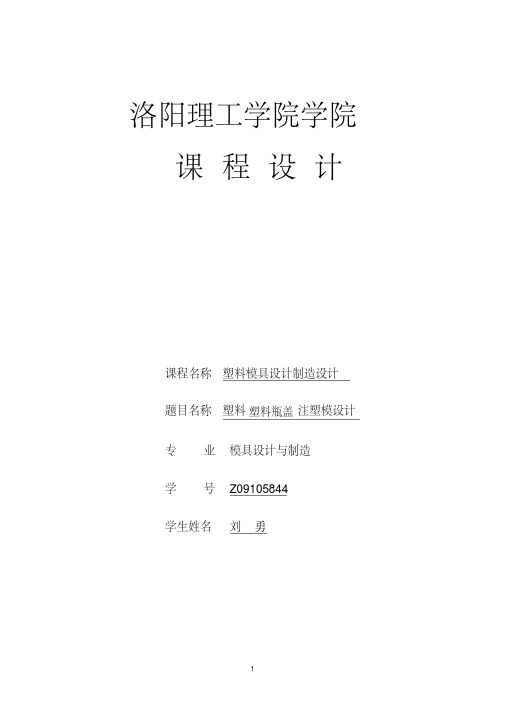
根据塑件的形状特点, 确定模具型腔的定模部分, 模具型芯在动模部分。 塑件 成型开模后, 塑件与型芯一起留在动模一侧。 该塑件有螺纹孔, 螺纹部分是由螺 纹型芯成型的, 由于成型该塑件的塑料 ABS可以采用强制脱模, 但是该制件是有 内螺纹的圆形制件, 故有需要较大的脱模力, 故采用推件版推出机构。 为了避免 推件孔的内表面与型芯的螺纹摩擦, 造成型芯的迅速刮伤, 将推件版的内孔与型 芯成型面做成单边斜度为 5~10 度的锥面,并且可以准确定位推件版,避免了该 处的飞边溢斜。
(1) 主流道的设计
6
主流道是连接注射机喷油嘴与分流道的一段通道, 轴线上,端面为圆形, 由注塑机的参数可知 : 喷嘴的直径为 d0=4mm 喷嘴的前端球半径 R0=15mm 根据主流道与喷嘴的关系得到: 主流道进口端球面半径 R=R0+(1~2)取 R=16mm
主流道进口端孔直径 d=d0+0.5=4+0.5=4.5mm.
3
10
120
105
0~220
325
15 螺杆式
125
模板的最大厚度 /mm
300
模板的最小厚度 /mm
200
最大模板尺寸 /mm 370*320
拉杆空间 /mm
345 345
合模方式
液压机械
电机功率 /KW
15
定位圈深度 /mm
10
喷嘴孔直径 /mm
4
最大成型面积 / cm 2
320
注塑速率 / (g.s 1 )
3
( 2) 塑件表面质量分析
该塑件表面没有很高的要求,在一般情况下,要求塑件光洁,表面粗糙度为
Rs,
对外表面可以取 0.8 μm;对内表面的 Rs 可以取 3.2 μ m。
饮料瓶瓶盖注射模具设计
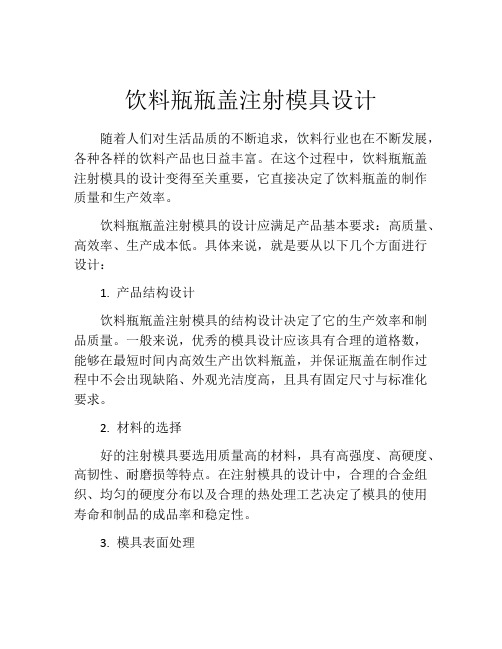
饮料瓶瓶盖注射模具设计随着人们对生活品质的不断追求,饮料行业也在不断发展,各种各样的饮料产品也日益丰富。
在这个过程中,饮料瓶瓶盖注射模具的设计变得至关重要,它直接决定了饮料瓶盖的制作质量和生产效率。
饮料瓶瓶盖注射模具的设计应满足产品基本要求:高质量、高效率、生产成本低。
具体来说,就是要从以下几个方面进行设计:1. 产品结构设计饮料瓶瓶盖注射模具的结构设计决定了它的生产效率和制品质量。
一般来说,优秀的模具设计应该具有合理的道格数,能够在最短时间内高效生产出饮料瓶盖,并保证瓶盖在制作过程中不会出现缺陷、外观光洁度高,且具有固定尺寸与标准化要求。
2. 材料的选择好的注射模具要选用质量高的材料,具有高强度、高硬度、高韧性、耐磨损等特点。
在注射模具的设计中,合理的合金组织、均匀的硬度分布以及合理的热处理工艺决定了模具的使用寿命和制品的成品率和稳定性。
3. 模具表面处理对模具表面进行光面处理能够提高注射模具的质量,表面处理的方法有电解镀铬、电子氧化等。
通过优化模具表面,能够减轻瓶盖模具的摩擦力,避免产品破损、变形等质量问题。
4. 注塑工艺设计饮料瓶瓶盖的生产过程中,温度、压力、流速等因素的控制是非常重要的。
优秀的注塑工艺设计应该包含精细的注塑参数设置、优化的熔体流动状态,并且要有良好的产品验收、测试程序与机器的调整性能。
总之,饮料瓶瓶盖注射模具设计对于饮料生产企业的产品质量和效率起着至关重要的作用。
优秀的注射模具应该满足生产企业的实际需求,采用高质量的材料、优化的结构设计等方式进行设计,同时还应该结合注塑工艺的合理配置,使生产过程达到高效、低成本并且质量优异的效果。
只有注射模具设计的高效性和高质量性得到保证,才能使饮料行业的生产得以更好地发展。
毕业设计开题报告---饮料瓶盖的注塑模具分析与设计
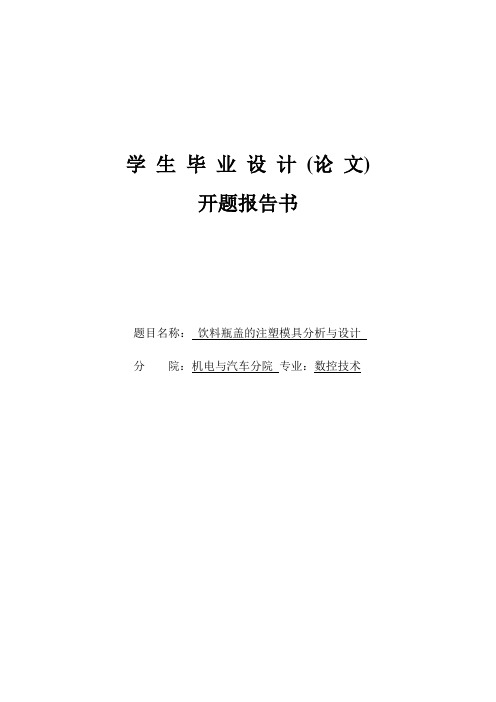
2008.12.10—12.30查阅资料,市场调研,确定课题方向
2009.01.08—01.14开题报告
2009.01.18—01.25文献综述,查阅文献
2009.02.22—04.13论文初稿
2009.04.13—04.28 修改论文
2009.04.25—05.29定稿
参考文献资料:
指导教师(签名):
年月日
分院毕业设计(论文)工作小组意见:
组长(签名):
年月日
学生毕业设计(论文)
开题报告书
题目名称:饮料瓶盖的注塑模具分析与设计
分院:机电与汽车分院专业:数控技术
主要研究(设计)内容:
对于饮料瓶盖的意义及其使用效果作了分析,研制出一种结构简单,干净卫生,价格便宜,制造容易,使用方注塑模的工艺设计方案分析及确定工艺加工过程中的步骤和方法,生产主要是为了提高生产效率,一定要保证其精度要求,模具要进行热处理,加高模具的硬度,提高模具使用寿命。并与常用的瓶盖进行了比较,证明了新型的优越性和科学性。
1、甄瑞麟.模具制造技术.北京:机械工业出版社,2005.4
2、马名峻.蒋亨顺.郭洁民.电火花加工技术在模具制造中的应用.北京:化学工业出版社,2004.6
3、崔北华.数控加工工艺.济南:山东科学技术出版社,2005.9
4、冯辛安.机械制造装备设计.北京:机械工业出版社,1999.12
指导教师意见:
方法及其预期目标:
一、对瓶盖设计的知识点进行广泛了解与分析
二、对现国内外饮料瓶盖制造中所存在的不足进行探讨
三、根据先前学的知识和对传统材料的不足研制出新型密度计
(1)设计指导思想
(2)对瓶盖使用进行测试
(3)瓶盖的内部材料分配
饮料瓶的模具设计
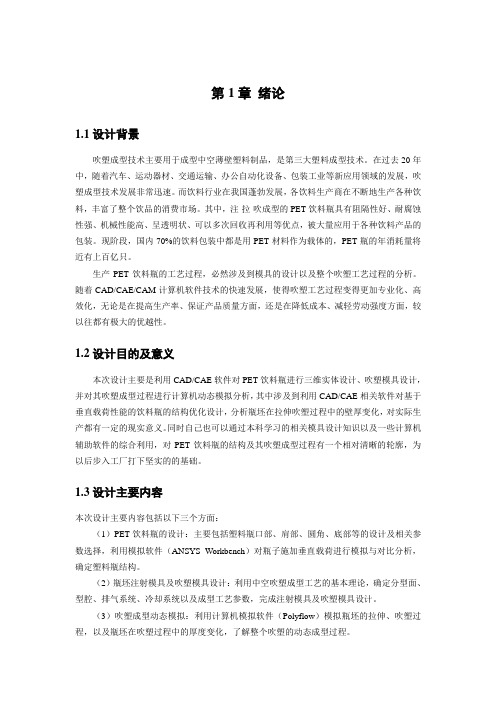
第1章绪论1.1设计背景吹塑成型技术主要用于成型中空薄壁塑料制品,是第三大塑料成型技术。
在过去20年中,随着汽车、运动器材、交通运输、办公自动化设备、包装工业等新应用领域的发展,吹塑成型技术发展非常迅速。
而饮料行业在我国蓬勃发展,各饮料生产商在不断地生产各种饮料,丰富了整个饮品的消费市场。
其中,注-拉-吹成型的PET饮料瓶具有阻隔性好、耐腐蚀性强、机械性能高、呈透明状、可以多次回收再利用等优点,被大量应用于各种饮料产品的包装。
现阶段,国内70%的饮料包装中都是用PET材料作为载体的,PET瓶的年消耗量将近有上百亿只。
生产PET饮料瓶的工艺过程,必然涉及到模具的设计以及整个吹塑工艺过程的分析。
随着CAD/CAE/CAM计算机软件技术的快速发展,使得吹塑工艺过程变得更加专业化、高效化,无论是在提高生产率、保证产品质量方面,还是在降低成本、减轻劳动强度方面,较以往都有极大的优越性。
1.2设计目的及意义本次设计主要是利用CAD/CAE软件对PET饮料瓶进行三维实体设计、吹塑模具设计,并对其吹塑成型过程进行计算机动态模拟分析,其中涉及到利用CAD/CAE相关软件对基于垂直载荷性能的饮料瓶的结构优化设计,分析瓶坯在拉伸吹塑过程中的壁厚变化,对实际生产都有一定的现实意义。
同时自己也可以通过本科学习的相关模具设计知识以及一些计算机辅助软件的综合利用,对PET饮料瓶的结构及其吹塑成型过程有一个相对清晰的轮廓,为以后步入工厂打下坚实的的基础。
1.3设计主要内容本次设计主要内容包括以下三个方面:(1)PET饮料瓶的设计:主要包括塑料瓶口部、肩部、圆角、底部等的设计及相关参数选择,利用模拟软件(ANSYS Workbench)对瓶子施加垂直载荷进行模拟与对比分析,确定塑料瓶结构。
(2)瓶坯注射模具及吹塑模具设计:利用中空吹塑成型工艺的基本理论,确定分型面、型腔、排气系统、冷却系统以及成型工艺参数,完成注射模具及吹塑模具设计。
瓶盖注塑模具设计(有全套图纸)

本科毕业设计(论文)通过答辩
目录 摘要 1 塑料的成型基础·····························································································································1
关键词:CAD;ProE 等软件;浇注系统;冷却系统
本科毕业设计(论文)通过答辩
The injecting model design of coverof the bottle bit of shampoo
ABSTRACT Mold CAD, ProE, software technology is 80-90 years before the emergence of a new design technology, These software technologies greatly enhance the wider use of the product and mold design quality products and the best performance. The software's main task is to help designers of the injection process, interpretation of the data and
(完整版)塑料瓶盖注塑模具设计
塑料瓶盖注塑模具设计绪论1.本课题的意义、目的及应达到的要求本设计主要意义是在我们学习完模具设计与制造的所有专业课之后,总结条理以前我们所学的知识,使之成为一个系统的理论体系,以便于我们在以后的工作中使用。
同时也让我们对模具的设计与制造有了初步的了解,掌握了查阅资料和使用工具书以及手册的能力。
【1】本设计的目的是在学生毕业前夕,将通过毕业实习和毕业设计的实践性环节,对医学知识进行全面的总结和应用,提高综合能力的培训以及扩大模具领域的新知识。
具体的要求是:1.系统总结,巩固过去所学的基础课和专业课知识。
2.运用所学的知识解决模具技术领域内的实际工程问题,以此进行综合知识的训练。
3.通过某项具体工程设计和实验研究,达到多种综合能力的培养,掌握设计和科研的基本过程和基本方法。
4.提高和运用与工程技术有关的人文科学,价值工程和技术经济的综合知识。
2 本课题的国内外现状2.1我国塑料模具工业的发展现状我国塑料模工业从起步到现在,历经半个多世纪,有了很大发展,模具水平有了较大提高。
在大型模具方面已能生产48英寸大屏幕彩电塑壳注射模具、6.5Kg大容量洗衣机全套塑料模具以及汽车保险杠和整体仪表板等塑料模具,精密塑料模具方面,已能生产照相机塑料件模具、多型腔小模数齿轮模具及塑封模具。
注塑模型腔制造精度可达0.02mm~0.05mm,表面粗糙度Ra0.2μm,模具质量、寿命明显提高了,非淬火钢模寿命可达10~30万次,淬火钢模达50~1000万次,交货期较以前缩短,但和国外相比仍有较大差距,(1)成型工艺方面:多材质塑料成型模、高效多色注射模、镶件互换结构和抽芯脱模机构的创新方面也取得较大进展。
气体辅助注射成型技术的使用更趋成熟,电视机外壳以及一些厚壁零件的模具上运用气辅技术,一些厂家还使用了C-MOLD气辅软件,取得较好的效果。
但总体上热流道的采用率达不到10%,与国外的50%~80%相比,差距较大。
(2)在制造技术方面:CAD/CAM/CAE技术的应用水平上了一个新台阶,以生产家用电器的企业为代表,陆续引进了相当数量的CAD/CAM系统,美国EDS的UG Ⅱ、美国Parametric Technology公司的Pro/Engineer、美国CV公司的CADS5、以及一些塑模分析软件等等。
饮料瓶瓶盖注射模设计
饮料瓶瓶盖注射模设计
引言
随着饮料市场的不断扩大,饮料瓶的需求量也在逐年增加。
饮料瓶瓶盖作为饮
料包装的重要组成部分,其设计和生产工艺对产品质量和生产效率都有着重要的影响。
本文将针对饮料瓶瓶盖注射模的设计进行详细探讨,包括设计要点、模具结构、材料选择等内容,希望能为相关行业提供一定的参考和借鉴。
设计要点
1. 瓶盖外形设计
•瓶盖外形应符合人体工程学,易于打开和关闭。
•应考虑到环保要求,避免过度包装。
2. 密封性能
•瓶盖与瓶口密合,确保饮料不泄漏。
•考虑塑料收缩率,避免尺寸变形影响密封性。
3. 注射成型
•注射模设计应考虑到注射成型的工艺要求,避免产品变形、气泡等质量问题。
•合理设计模具结构,提高生产效率,降低成本。
模具结构设计
1. 核心和腔面设计
•核心和腔面应采用优质材料,保证注射成型产品表面光滑。
2. 冷却系统设计
•合理设计冷却系统,控制模具温度,避免产品收缩不均匀。
3. 排气系统设计
•考虑产品内部气体的排出,避免气泡影响产品质量。
材料选择
1. 塑料材料选择
•一般选用聚丙烯(PP)、聚乙烯(PE)等食品级塑料材料。
2. 模具材料选择
•选择硬度高、耐磨性好的金属材料,如优质钢材。
结语
饮料瓶瓶盖注射模的设计是一个综合工程,细节决定成败。
通过合理的设计要点、模具结构设计和材料选择,可以确保产品质量和生产效率。
希望本文所述内容对相关行业人士有所帮助,促进饮料瓶瓶盖注射模领域的进一步发展。
脉动饮料瓶盖子模具设计
排气槽的作用是将型腔和型芯中周围空间内的气体及熔料所产生的气体排到模具之外。该注射模属于小型模具,在推杆的间隙和分型面上都有排气效果,又分型面积比较大,无需另外开排气槽[11]。
3.3.5型腔压力估算
据式P=KPo取压力损耗系数K=0.4,该射机压力Po=122MPa,则型腔压力P=KPo=49Mpa。
3.3.3浇口设计
选择浇口形式应该遵循以下原则[10]:
(1) 尽可能采用平衡式设置;
(2) 型腔排列进料均衡;
(3) 型腔布置和浇口开设部位力求对称,防止模具承受偏载而产生溢料现象;
(4) 确保耗料量小;
(5) 不影响塑件外观。
根据以上原则,决定选用侧浇口形式,这种浇口的优点为:去浇口方便,残留痕迹小;熔体流速高;翘曲比直接浇口小;宜成型薄壁、复杂形状制品。其缺点有:注射压力损失大;保压补缩作用比直接浇口小。总的来说,侧浇口适用于各种形状及一模多腔制品,是最常用的一种形式。
查找实用塑料注射模设计与制造27页表2-2及注塑模具设计与制造实用技术39页,聚乙烯的成型工艺参数可作如下选择:成型温度为140℃~200℃;该射压力为60MPa~100MPa。必须说明的是,上述工艺参数在试模时可作适当调整。
3 注射模的结构设计
3.1 分型面选择
合理选择分型面,有利于制品的质量提高,工艺操作和模具的制造。因此,在模具设计过程中是一个不容忽视的问题,选择分型面一般根据以下的原则[6]:
2.1.2塑件的结构和尺寸精度表面质量分析
(1)结构分析
从零件图上分析,该零件总体形状为圆筒形,顶端有沿径向截面长为1.5mm,高度为0.2mm的凸台,圆周有120条与轴平行的花纹线,内部有螺距为3mm是普通细牙螺纹。
饮料瓶瓶盖注射模设计
冯炳尧 , 韩泰荣 , 文森 . 具设计与 制造 简明手册【 】 蒋 模 M .上 海: 上海科学技术 出版社 .9 8 19 . 李德 群.塑料 成型工 艺及模 具设 计[ 】 M .北京 : 机械工业 出
版社 。9 4 19 .
尺寸的一致性 。 从而保证产 品的精度要求 。
为了提高侧抽芯时的精度要求 。 防止转盘在转动 过程 中因磨损影响产 品质量 ,设 计 中采用淬 火轴套 1, 1 以过盈配合固定在动模板 3 6的外侧 . 而转盘采用
1 塑 件 结构 分 析
图1 所示塑件 为某饮料瓶瓶盖 , 材料为 P ( E 聚乙
为半圆形 的螺纹及高为 4 m、 m 截面直径为 4 m ' m的防 l
伪圈与瓶子 内径严 密配合 ,而高为 l m,截面直径 m
烯)重量为 2 g , . 。瓶盖主体外侧均布 1 0 9 2 个增大摩擦 力的防滑筋 , 瓶盖顶部有商标名称 Z M的字样 。瓶盖 S
CWM 材料淬硬至 6 H C后研磨成与轴套 H / r n 0R 8 8的 f
配合 , 转盘上的腰 圆形的孔用线切割加工 。 由于动模板 3 是 以圆环形截面 固定在型芯固定 6
4 模具的特点
该套模具 为了达到产品的精 度要求 和设计要求 . 具有如下特点 : 每个侧滑块设计成不对称的形 式 。 这样一方面适 当加宽 了侧滑块的宽度 , 以便让 出限位螺钉在高度 方
・
唐志 玉 , 德群 , 佩弦.塑料模具 设计 师指 南[ .北 京 : 李 徐 M】
国防 工 业 出版 社 。9 9 19.
4 0・
《 具 制造) 0 6年 第 6期 模 20
Байду номын сангаас普资讯
- 1、下载文档前请自行甄别文档内容的完整性,平台不提供额外的编辑、内容补充、找答案等附加服务。
- 2、"仅部分预览"的文档,不可在线预览部分如存在完整性等问题,可反馈申请退款(可完整预览的文档不适用该条件!)。
- 3、如文档侵犯您的权益,请联系客服反馈,我们会尽快为您处理(人工客服工作时间:9:00-18:30)。
额定注射量
60
合模方式
液压-机械
螺杆直径
38mm
最大开模开程
180mm
注射压力
122mpa
最大注射面积
130cm2
顶出中心孔径
50
锁模力
500kN
注射方式
螺杆式
定位圈
55mm
模具最大厚度
200mm
喷嘴球半径
12mm
模具最小厚度
70mm
喷嘴孔直径
4mm
2.3 塑件注射工艺参数的确立
3.7 本模具工作原理
本模具的工作原理:注射成型后,动模首先移动,动模板把塑料制品从定模板内带出,然后注射机推出机构推动推板,并带动斜推杆推动螺纹型芯向中间合拢,塑料制品上的螺纹部分脱离螺纹型芯,完成一次推出,然后斜推杆把塑料制品推出,完成第二次推出。推出系统的复位,靠定模板上的反推杆。
4模具设计的有关计算
本模具成型零件工作尺寸计算时均采用平均法计算。查实用塑料注射模设计与制造P27表2-2得高压聚乙烯的收缩率为S=0.015~0.036,故平均收缩率为:
Scp=(0.015+0.036)/2=0.026
模具制造公差取Sz=△/3 。
(1) 分型面的位置要不影响制品的精度和外观;
(2) 尽量简单,避免采用复杂形状,使模具制造增加困难;
(3) 要尽量有利于塑料制品的脱模和抽芯;
(4) 有利于浇注系统的合理设计;
(5) 尽可能与料流末端重合,以利于系统的排气。
根据分型面选择原则和塑件成型要求来选择分型面。如图所示水平分型方式既可降低模具复杂程度,减少模具加工难度又便于成型后脱模。故选用如图所示的分型方式较为合理,如图3.1分型面的选择。
——HDPE所要求的脱模斜度,由经验数据取1
3.6 成型零件结构设计
3.6.1凹模的结构设计。
本例中模具采用一模四件的结构形式,考虑加工的难易程度和材料的价值利用等因素,凹模拟采用整体式结构,其结构形式如图3.5所示。
图3.5 凹模
3.6.2凸模结构设计
采用瓣合型镶块结构。通过内侧抽芯两块瓣合型镶块向中间合拢,从而达到脱模的目的。
(4) 推杆直径应满足相应的强度、刚度条件脱模力(推出力)计算。
将制品从包紧型芯上脱出所需要克服的阻力称为脱模力,是设计,计算顶出机构的依据:
根据式:
式中:F ——脱模力(KN)
——塑料对钢的摩擦系数 取0.1~0.3
A——塑料制品包容型芯面积(mm )
P—塑料件对型芯单位面积上的包紧力。一般情况下,模外冷却的塑件的P约为24 Mpa~39Mpa;模内冷却的塑件的P约为8 Mpa~12 Mpa。本塑件采用模内冷却,取P=10 Mpa
3.3.6锁模力校核
已知注射机最大锁模力F为500KN
式中:F——锁模力,kN
p——型腔压力,MPa
A——塑件及流道系统在分型面上的投影面积,mm²
已知型腔压力为49MPa;浇注系统的投影面积为1倍的塑件投影面积;塑件及流道系统在分型面上的投影面积为:
式中:S——流道系统在分型面上的投影面积,mm²
3.3.4排气槽的设计
排气槽的作用是将型腔和型芯中周围空间内的气体及熔料所产生的气体排到模具之外。该注射模属于小型模具,在推杆的间隙和分型面上都有排气效果,又分型面积比较大,无需另外开排气槽[11]。
3.3.5型腔压力估算
据式P=KPo取压力损耗系数K=0.4,该射机压力Po=122MPa,则型腔压力P=KPo=49Mpa。
图2.1 塑件图
塑件的材料采用HDPE,属热型性塑料。从使用性能看,该塑料耐酸碱及有机溶剂,成本低,成型加工方便,适于用作瓶盖材料,从成型性能看,该材料成型收缩率比一般塑料大,且刚性低,因而制品尺寸精度低[4]。成型时模具温度态均可一致,以减少温度差引起的不均匀收缩。保压也要充分,以便于补偿收缩溶体流动性好,流动比L/T=240,对压力变化敏感,故宜用较高压力注射,该射压力为60 MPa~70MPa。
查找实用塑料注射模设计与制造27页表2-2及注塑模具设计与制造实用技术39页,聚乙烯的成型工艺参数可作如下选择:成型温度为140℃~200℃;该射压力为60MPa~100MPa。必须说明的是,上述工艺参数在试模时可作适当调整。3 注射 Nhomakorabea的结构设计
3.1 分型面选择
合理选择分型面,有利于制品的质量提高,工艺操作和模具的制造。因此,在模具设计过程中是一个不容忽视的问题,选择分型面一般根据以下的原则[6]:
(3) 培养自己的动手能力、创新能力、计算机运用能力。
1.4 研究意义
(1) 对于模具的设计可以从选材到设计到成型有一个完整的了解和初步的掌握。以进一步的熟练掌握AutoCAD的运用。
(2) 锻炼自己的独立思考能力和创造能力,为更好更快的适应工作作准备。
2 瓶盖塑件详细分析
2.1 塑件工艺性分析
2.1.1塑件的原材料分析
3.4.4型芯座板尺寸
取型芯总座板半径为R=24mm,厚度为12mm。
3.5 脱模机构的设计
由于该塑件的脱模阻力不大,而推杆又加工简单、更换方便、脱模效果好,因此采用圆形推杆脱模机构。推杆的设置位置采取以下原则[12]:
(1) 推杆设在脱模阻力大的地方;
(2) 推杆位置均匀分布;
(3) 推杆设在塑料制品强度刚度较大的地方;
从塑件的壁厚来看,壁厚最大处为1.2mm,最小处为1.0mm,壁厚差为0.2mm,较均匀,有利于零件成型。
(3) 表面质量分析
该零件的表面除要求没有缺陷、毛刺外,没有特别的表面质量要求,故易于实现,综上分析可以看出,注射对在工艺参数控制得较好的情况下,零件的成型要求可以得到保证。
2.2 计算塑件的体积和质量
塑料注射模的设计与制造过程中所涉及了大量的内容,如:塑件的结构工艺性分析、塑件的成形工艺特性、塑料注射机的匹配、塑料注射成型工艺及控制、塑料注射模的设计及模具材料、塑料注射模的制造装备和制造工艺等。
1 本课题的研究内容、要求、目的及意义
1.1 本课题的研究内容
做螺纹瓶盖的模具设计,使该的瓶盖注射模结构简单,型腔、型芯、脱模机构设计合理,根据说明书画模具图。
1.2 本课题的研究要求
(1) 此塑件外表面不允许有印迹,并且要光滑。
(2) 要使注射模结构简单,并可脱模。
(3) 流道设计合理,可保证产品质量并且又节约生产原材料。
(4) 了解HDPE的性能、特性和设计时的要求。
1.3 本课题的研究目的
(1) 检验理论知识掌握情况,将理论与实践结合。
(2) 步掌握进行模具设计的方法、过程、为将来走向工作岗位进行科技开发工作和撰写科研论文打下基础。
根据注塑件的要求及模具的结构等方面来选择浇注系统。
3.3.1主流道设计
据注塑模具设计与制造实用技术39页查的XS-Z-60型注射机喷嘴的有关尺寸为喷嘴前端孔径do=4mm;喷嘴前端球面半径[7]:Ro=12mm
根据模具主流道与喷嘴R=Ro+(1~2)mm及d= do +(0.5~1)mm,取立流道球面半径R=13mm,小端直径d=4.5mm。
为了便于将凝料从主流道中拔出,将立流道设计成圆锥形其斜度为 2°~4°,查90页表[8]3-22的主流道大端直径D=6mm,内壁粗糙度为Ra=0.63μm。为使熔料顺利进入分流道,可在主流道出料端设计半径r=5mm的圆弧过渡。如图3.3所示。
图3.3 主流道衬套
3.3.2分流道设计
分流道的形状及尺寸,应该根据塑件的体积、壁厚、形状的复杂程度,注射速率、分流道长度因素来确定。本塑件的形状简单,熔料填充型腔较容易,为方便加工起见,选用截面形状为半圆形分流道[9],取R=2.8mm。
关键词:注射模 螺纹型芯 边缘浇口
脉动饮料瓶盖模具设计
引言
在现代制造业的发展过程中,模具的地位及其重要性日益受到人们的重视。在塑料材料和制造品设计及加工工艺确定后,塑料模具的质量与生产具有决定性的作用,模具成本对制品的成本也有很大的影响。塑料注射模是利用塑料具有良好的成型和加工性能[1]。
在欧美日等工业发达国家,模具工业年产值早已超过机床行业的年产值,在成型技术也在不断的更新与完善。CAD/CAE技术在塑料注射模中是应用最为广泛的。我国的模具工业是从20世纪80年代初开始的,其发展速度也是非常快的,同时模具技术也在不断的提高。我国在注射模方面也有很大的发展,以能制造48寸大屏幕彩电塑壳模具、大容量洗衣机全套塑料模具以及汽车保险杠和整体仪表板等塑料模具,并开始使用先进的热流道和气体辅助注射成形技术。尽管我国的模具在不断的发展,但也发达工业国家相比还有很大的差距,其道路还是很长的[2]。
n——模腔数
则: A=4×π(30/2)2+35×5×4
=3526mm2
即:p×A/1000=49×3526/1000
=172.77kN<500kN
所以锁模力符合要求。
3.3.7定位圈设计
定位圈设计配合注塑机的参数进行设计,如图3.4。
图3.4 定位圈
3.4 抽芯机构设计
塑件侧壁有M28×3细牙螺纹,它与脱模方向不一致,阻碍成型后塑件从模具脱出。因此成型塑件型芯必须做成活动的,即须设置抽芯机构。本模具采用瓣合型芯成型和脱出内螺纹。
2.1.2塑件的结构和尺寸精度表面质量分析
(1)结构分析
从零件图上分析,该零件总体形状为圆筒形,顶端有沿径向截面长为1.5mm,高度为0.2mm的凸台,圆周有120条与轴平行的花纹线,内部有螺距为3mm是普通细牙螺纹。
(2) 尺寸精度分析
该零件的尺寸精度均为8级(SJ/1372-78),由以上分析可见,该零件的尺寸精度较低,对应的模具相关零件的加工可以保证。
根据塑件的成型要求及型腔的排列方式,选用侧浇口较为理想。设计时考虑选择从塑件下端进料,料由下端向上流,而且模具型芯采用活动镶块式,有利于排气。故采用截面为矩形的侧浇口。浇口截面高度h=1/3~2/3×(制品最小壁厚),1>1/3~2/3 取h=0.5,浇口截面宽度b=(3~10)×h=1.5~5,b要小于分流道半径R,取b=2,浇口长度l一般可取0.7 mm~2.0mm,此处取l=0.8 mm,则初选尺寸为h×b×l=0.5mm×2mm×0.8mm,试模时修正。