第二章 精密切削加工分析
精密切削加工总结汇报

精密切削加工总结汇报精密切削加工是一项极其重要的制造工艺,它在许多行业中扮演着关键的角色。
在本次总结汇报中,我将对精密切削加工的定义、应用领域、工艺流程、优势和挑战等方面进行详细讨论。
精密切削加工是一种通过切削材料来获得极高精度和表面质量的制造工艺。
该技术广泛应用于航空航天、汽车、医疗器械、光学仪器等高要求的行业。
在这些领域中,零部件的精度和表面质量是至关重要的,而精密切削加工能够通过各种切削工具和机床来实现这些要求。
精密切削加工的工艺主要包括车削、铣削、磨削、电火花加工和线切割等。
这些工艺可以实现对工件的内外形状、尺寸和表面质量的高精度加工。
例如,车削可以用于加工旋转对称的工件,而磨削可以用于加工高硬度材料和形状复杂的工件。
通过灵活运用这些工艺,可以满足不同行业对零部件高精度加工的需求。
精密切削加工与其他制造工艺相比具有许多优势。
首先,它可以实现高精度加工,精度可以达到亚微米甚至纳米级。
其次,精密切削加工可以获得优异的表面质量,满足行业对光学和光电零件高光洁度的要求。
此外,该工艺还可以适用于各种材料,包括金属、复合材料和陶瓷等,具有非常广泛的应用领域。
然而,精密切削加工也面临一些挑战。
首先,该工艺对设备和工具的要求非常高,需要高精度的切削工具和稳定的机床。
此外,加工过程中还存在工件变形的问题,特别是对于大尺寸和细长的工件来说更加明显。
同时,精密切削加工的工艺参数选择和优化也是一个复杂的任务,需要对材料、切削力、温度等因素进行综合考量。
为了解决这些挑战,我们可以借助先进的切削技术和工艺改进来提高效率和质量。
例如,通过引入高速切削和超精密切削技术,可以提高加工速度和表面质量。
另外,通过优化刀具和刀具材料的选择,可以降低切削力和热变形。
总之,精密切削加工是一项不可或缺的制造工艺,具有广泛的应用领域和重要的经济意义。
在未来,随着科技的进步和工艺的改进,精密切削加工将会进一步提高加工效率和质量,为各行业的发展做出更大的贡献。
2精密磨削加工

精密磨削机理
②磨粒的等高性
微刃是由砂轮的精 细修整形成的,分布在 砂轮表层的同一深度上 的微刃数量多,等高性 好(即细而多的切削刃具 有平坦的表面) 。 由于加工表面的残 留高度极小,因而形成 了小的表面粗糙度值。
磨粒的等高性
1 粘结剂 2 磨料 3 砂轮表面
精密磨削机理
③微刃的滑擦、挤压、抛光作用
多用球磨机,而涂敷多用类似印刷机的涂敷机,可获得质量
良好的砂带。
静电植砂法:利用静电作用将砂粒吸附在已涂胶的基底上。
能使砂粒尖端朝上,因此切削性能强,等高性好、加工质量好。
2. 2
精密磨削加工机理
精密磨削是指加工精度为l--0.1μm、表面粗糙度值R a 达到0.2--0.025μm的磨削加工方法,又称低粗糙值磨削。 它是用微小的多刃刀具削除细微切屑的一种加工方法。一般 是通过氧化铝和碳化硅砂轮来实现的。 一般用于机床主轴、轴承、液压滑阀、滚动导轨、量规 等的精密加工。
补充概念
粒度指磨料颗料的大小。粒度分磨粒与微粉两组。磨粒用 筛选法分类,它的粒度号以筛网上一英寸长度内的孔眼数来表 示。例如 60#粒度的的磨粒,说明能通过每英寸长有 60 个孔 眼的筛网,而不能通过每英寸 70 个孔眼的筛网。 微粉用显微测量法分类,它的粒度号以磨料的实际尺寸来 表示( W )。如W20表示微粉的实际尺寸为20μm。 粒度号 适用范围 粗磨、荒磨、切断钢 坯、打磨毛刺 粗磨、半精磨、精磨 粒度号 适用范围 精磨、超精磨、螺纹 磨、珩磨 精磨、精细磨、超精 磨、镜面磨
涂覆磨具
涂覆磨具是将磨料用粘结 剂均匀的涂覆在纸、布或其它 复合材料基底上的磨具,又称 为涂敷磨具。 常用的涂敷磨具是有砂纸、 砂带、砂布、砂盘和砂布套等。
精密加工技术第二讲
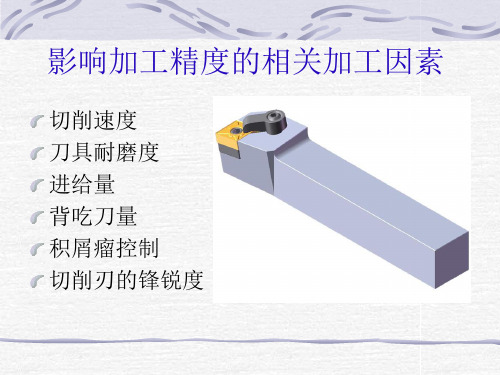
2.3 切削时积屑瘤的生成规律
2、进给量f的影响
进给量很小时, 积屑瘤的高度很 大;
f=5μm/r 时, h0值最小; f值再增大时, h0值稍有增加。
2.3 切削时积屑瘤的生成规律
3、背吃刀量ap的影 响
在背吃刀量<25μm 时,积屑瘤的高度 变化不大,
但在背吃刀量> 25μm后, h0值将 随着背吃刀量的增 加而增加。
第2章 金刚石刀具的切削机理
刀具寿命评判标准
加工表面粗糙度是否超过规定值; 刀具寿命以切削长度计;
寿命达:数百千米
第2章 金刚石刀具的切削机理
影响刀具耐磨度的因素
切削速度直接影响刀具耐磨度很小; 振动引
Ktd0a vba f capd awe z
降低振动技术
高速精密电 主轴中的陶
瓷轴承
高速精密空 气轴承的电
主轴
2.3 切削时积屑瘤的生成规律
一、积屑瘤的生成现象
切削过程中,会出现一 小块金属牢固地粘附住 所用刀具的前刀面上, 这一小块金属就是积屑 瘤。
积屑瘤是在很大的压力、 强烈摩擦和剧烈的金属 变形的条件下产生的
2.3 切削时积屑瘤的生成规律
刀具晶面的选用
应考虑因素: 刀具耐磨性好; 刀刃微观强度高,不易产生微观崩刃; 刀具和被加工材料间摩擦系数低,使切削变 形小,加工表面质量高; 制造研磨容易。
(111)晶面不适合作前后面。推荐采用(100)晶面作金 刚石刀具的前后刀面,原因:
•1)(100)晶面的耐磨性高于(110)晶面;
•2 )(100)晶面的微观破损强度高于(110)晶面,(100) 晶面受载荷时的破损机率比(110)晶面低很多;
金刚石晶体的解理现象
2 精密切削2
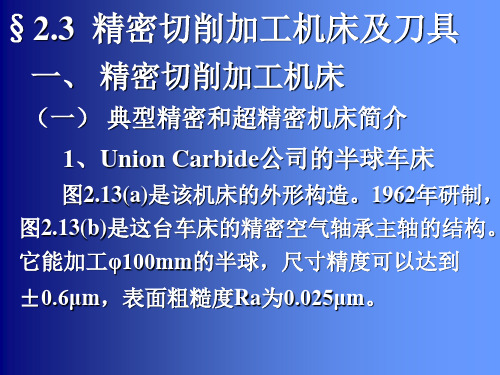
1)不易磨损
2)不易生锈腐蚀
3)热膨胀系数要小
4)材料的稳定性要好
2、主轴的驱动方式
1)电动机通过带传动驱动
2)采用内装式同轴电动机驱动机床主轴
3)电动机通过柔性联轴器驱动机床主轴
(五) 床身和精密导轨部件
1、床身和导轨的材料
目前精密机床主要采用下列材料作为床身和导轨
材料:
1)优质耐磨铸铁,其优点是工艺性好 ;
1)V-平面
2)双V形导轨能为直线运动提供良好的导向
性。 3)压力油润滑导轨 4)导轨偶合面的接触形式
3、导轨类型
导轨类型分三类:滚动导轨 、液体静压导轨、 气浮导轨和空气静压导轨。
4、进给驱动系统
精密进给驱动系统必须由滚珠丝杠副驱动 (见图2.27) 、液体静压和空气静压丝杠副驱
动(见图2.28 )、摩擦驱动(见图2.29 )、微
2)刃口能磨得极其锋锐,刃口半径ρ值极
小.能实现超薄切削厚度。
3)刀刃无缺陷,切削时刃形将复印在加工
表面上,能得到超光滑的镜面。
4)和工件材料的抗粘结性好、化学亲和性 小、摩擦系数低,能得到极好的加工表面完整 性。 由于单晶金刚石现在是无法代替的超精密 切削用刀具材料,故分析研究金刚石的性能是 研究超精密切削的重要基础。
2)花岗岩 。其尺寸稳定性,振动衰减能力,
硬度、耐磨性和抗腐蚀性等方面的性能都优越 ; 3)人造花岗岩。不仅可铸造成形,吸湿性低, 而且加强了振动的衰减能力。
2、导轨的要求和结构形式
常用的机床的导轨结构形式有燕尾形的,有平 面的,有V-平面的,有双V形的。现在液体静压
导轨和空气静压导轨多数采用平面导轨结构。
近期目标2.5nm 近期目标0.001K
第二章 金刚石刀具精密切削加工

复习晶体结构
晶格模型
面心结构
晶体结构指晶体内部原子规则排列的方式.晶体结构不同, 其性能往往相差很大。为了便于分析研究各种晶体中原子 或分子的排列情况,通常把原子抽象为几何点,并用许多 假想的直线连接起来,这样得到的三维空间几何格架称为 晶格。
晶胞
Z
晶胞
c
b Y
a
X
晶格常数 a , b, c
人造单晶金刚石刀具 金刚石刀具 PCD刀具
多晶金刚石刀具
CVD金刚石薄膜涂层刀具
CVD金刚石刀具 金刚石厚度膜焊接刀具
金刚石刀具的性能特点
极高的硬度和耐磨性:硬度达HV10000,是自然界最硬的物质, 具有极高的耐磨性,天然金刚石耐磨性为硬质合金80-120倍,人 造金刚石耐磨性为硬质合金60-80倍。 各向异性能:单晶金刚石晶体不同晶面及晶向的硬度、耐磨性能 、微观强度、研磨加工的难易程度以及与工件材料之间的摩擦系 数等相差很大,因此,设计和制造单晶金刚石刀具时,必须进行 晶体定向。
二、典型机床简介
Pneumo 公司的MSG-325超精密车床
采用T形布局,机床空气主轴的径向圆跳动和轴向 跳动均小于等于0.05μm。床身溜板用花岗岩制造,导 轨为气浮导轨;机床用滚珠丝杠和分辨率为0.01μm的 双坐标精密数控系统驱动,用HP5501A双频激光干涉仪 精密检测位移。
DTM-3大型超精密车床
分为:液体静压和空气静压
供油压力恒定的液体静压轴承
主轴始终悬浮 在高压油膜上
液体静压轴承与气压轴承
1、液体静压轴承主轴
优点
回转稳定性好 刚度高 无振动
缺点
回转运动有温升 回油时有空气进入油源 注:空气静压轴承原理与静
机械制造技术课件第二章金属切削基本原理
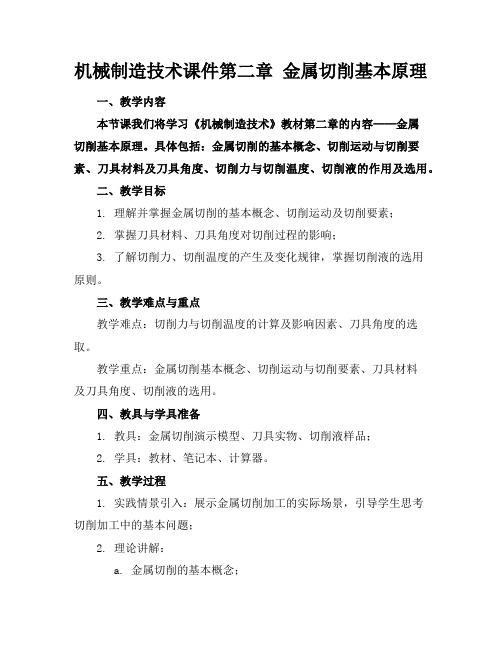
机械制造技术课件第二章金属切削基本原理一、教学内容本节课我们将学习《机械制造技术》教材第二章的内容——金属切削基本原理。
具体包括:金属切削的基本概念、切削运动与切削要素、刀具材料及刀具角度、切削力与切削温度、切削液的作用及选用。
二、教学目标1. 理解并掌握金属切削的基本概念、切削运动及切削要素;2. 掌握刀具材料、刀具角度对切削过程的影响;3. 了解切削力、切削温度的产生及变化规律,掌握切削液的选用原则。
三、教学难点与重点教学难点:切削力与切削温度的计算及影响因素、刀具角度的选取。
教学重点:金属切削基本概念、切削运动与切削要素、刀具材料及刀具角度、切削液的选用。
四、教具与学具准备1. 教具:金属切削演示模型、刀具实物、切削液样品;2. 学具:教材、笔记本、计算器。
五、教学过程1. 实践情景引入:展示金属切削加工的实际场景,引导学生思考切削加工中的基本问题;2. 理论讲解:a. 金属切削的基本概念;b. 切削运动与切削要素;c. 刀具材料及刀具角度;d. 切削力与切削温度;e. 切削液的作用及选用;3. 例题讲解:通过具体例题,讲解切削力与切削温度的计算方法,以及刀具角度的选取原则;4. 随堂练习:布置相关练习题,巩固所学知识;六、板书设计1. 金属切削基本概念;2. 切削运动与切削要素;3. 刀具材料及刀具角度;4. 切削力与切削温度;5. 切削液的选用。
七、作业设计1. 作业题目:a. 解释金属切削的基本概念;b. 列出切削运动及切削要素;c. 分析刀具材料、刀具角度对切削过程的影响;d. 计算给定条件下的切削力与切削温度;e. 论述切削液的选用原则。
2. 答案:a. 略;b. 略;c. 略;d. 略;e. 略。
八、课后反思及拓展延伸1. 反思:本节课学生对金属切削基本原理的理解程度,以及切削力与切削温度的计算掌握情况;2. 拓展延伸:引导学生了解金属切削技术的发展趋势,如高速切削、绿色切削等。
精密机械加工中的切削力分析与刀具选择
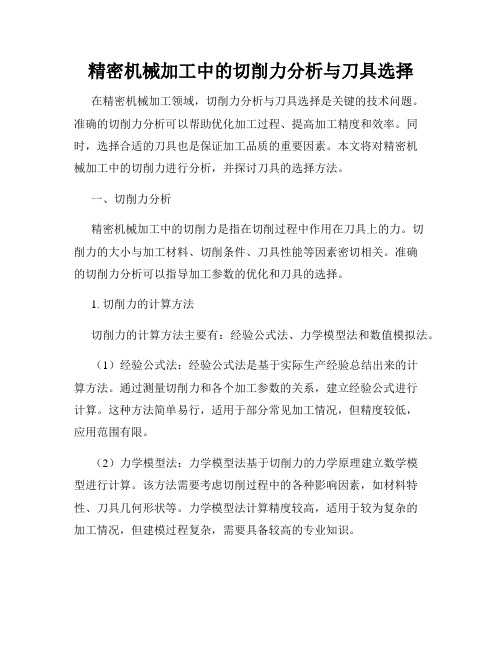
精密机械加工中的切削力分析与刀具选择在精密机械加工领域,切削力分析与刀具选择是关键的技术问题。
准确的切削力分析可以帮助优化加工过程、提高加工精度和效率。
同时,选择合适的刀具也是保证加工品质的重要因素。
本文将对精密机械加工中的切削力进行分析,并探讨刀具的选择方法。
一、切削力分析精密机械加工中的切削力是指在切削过程中作用在刀具上的力。
切削力的大小与加工材料、切削条件、刀具性能等因素密切相关。
准确的切削力分析可以指导加工参数的优化和刀具的选择。
1. 切削力的计算方法切削力的计算方法主要有:经验公式法、力学模型法和数值模拟法。
(1)经验公式法:经验公式法是基于实际生产经验总结出来的计算方法。
通过测量切削力和各个加工参数的关系,建立经验公式进行计算。
这种方法简单易行,适用于部分常见加工情况,但精度较低,应用范围有限。
(2)力学模型法:力学模型法基于切削力的力学原理建立数学模型进行计算。
该方法需要考虑切削过程中的各种影响因素,如材料特性、刀具几何形状等。
力学模型法计算精度较高,适用于较为复杂的加工情况,但建模过程复杂,需要具备较高的专业知识。
(3)数值模拟法:数值模拟法利用计算机进行切削力分析,通过建立几何模型和物理模型,采用数值方法求解切削力的分布和大小。
这种方法可以考虑各种复杂加工情况和刀具形状,计算精度较高,但需要较高的计算资源和软件工具支持。
2. 切削力的影响因素切削力的大小受到多种因素的影响,主要包括:(1)材料硬度:材料硬度越高,切削力越大。
(2)切削速度:切削速度增加,切削力一般也会增加。
(3)进给速度:进给速度增加,切削力也会相应增加。
(4)切削深度:切削深度增加,切削力也会增加。
(5)切削角度:合理选择切削角度可以减小切削力。
3. 切削力的测量方法切削力的测量方法主要有:直接测力法、敏感元件法和间接法。
(1)直接测力法:直接测力法通过采用力传感器或测力仪器,直接测量切削过程中的切削力。
这种方法能够提供准确的切削力数据,适用于实际加工过程中的力学参数测量。
机械制造技术PPT课件第二章 金属切削基本原理

机械制造技术基础
◆切削功率
—切削过程中所消耗的功率
切削功率
Pc
Fcvc 60
103
机床电机所需功率
PE
Pc
传动效率 0.75 ~ 0.85
—校验和选取机床电机的依据
机械制造技术基础
2.2.4 影响切削力的因素 ①工件材料 —强度、硬度、塑性大→切削力大
机械制造技术基础
2.3.2 切削温度 —切屑与前刀面接触区域的平均温度
C
ax p
f
v k y z c
最典型值:
x 0.1 y 0.2 z 0.4
机械制造技术基础
工件材料:低碳易切钢;
刀具:o=30,o=7;
二维切削中 的温度分布
切削用量:ap=0.6mm, vc =0.38m/s;
机械制造技术基础
2.3.1 切削热的来源与传导
◆来源: —弹性、塑性变形功,摩擦功
Q=Fc vC
◆传导: →切屑、刀具、工件、介质
车:50~86%→切屑,10~40%→车刀 3~9%→工件,1% →空气
钻:28%→切屑,14.5%→刀具 52.5%→工件,5%→介质
磨:4%→磨屑,12%→砂轮,84%→工件
◆工件材料 ◆刀具前角
—前角大,刃锋利,挤压小,剪切角大→切屑变形小
机械制造技术基础
2.1.3 影响切削变形的因素
◆工件材料 ◆刀具前角 ◆切削用量
①切削速度 —影响积屑瘤和切削温度
呈波形变化
②进给量 —进给量越大→切屑变形小
机械制造技术基础
2.2
切削力
- 1、下载文档前请自行甄别文档内容的完整性,平台不提供额外的编辑、内容补充、找答案等附加服务。
- 2、"仅部分预览"的文档,不可在线预览部分如存在完整性等问题,可反馈申请退款(可完整预览的文档不适用该条件!)。
- 3、如文档侵犯您的权益,请联系客服反馈,我们会尽快为您处理(人工客服工作时间:9:00-18:30)。
2.1概述 2.2精密切削加工的工艺规律和机理 2.3精密切削加工的机床及应用 2.4功率超声车削
2019/4/20
2.1概述
精密切削是使用精密的单晶天然金刚石刀具加工有色金属 和非金属,可以直接加工出超光滑的加工表面(粗糙度 Ra0.02~0.005µm,加工精度<0.01µm)。 用于加工:陀螺仪、激光反射镜、天文望远镜的反射镜、 红外反射镜和红外透镜、雷达的波导管内腔、计算机磁盘、 激光打印机的多面棱镜、录像机的磁头、复印机的硒鼓、 菲尼尔透镜等。 精密切削也是金属切削的一种,当然也服从金属切削的普 遍规律。 金刚石刀具的精密加工技术主要应用于单件大型超精密零 件的切削加工和大量生产中的中小型超精密零件加工。
一、切削速度、进给量、修光刃和背吃刀量的影响
2、进给量的影响
在进给量f<5μm/r
时,均达到
Rmax<0.05μm的加工 表面粗糙度。
2019/4/20
一、切削速度、进给量、修光刃和背吃刀量的影响
3、修光刃的影响
修光刃长度常取0.05~ 0.20mm。 修光刃的长度过长,对 加工表面粗糙度影响不 大。 修光刃有直线和圆弧两 种,加工时要精确对 刀,使修光刃和进给方 向一致。圆弧刃半径一般 取2~5mm。
由图2-8可以看出在进给量很小时,积屑瘤的高度很大, 在f=5μm/r时,h0值最小,f值再增大时,h0值稍有增 加。 由图2-9所示,在背吃刀量<25μm时,积屑瘤的高度变 化不大,但在背吃刀量> 25μm后, h0值将随着背吃 刀量的增加而增加。
2019/4/20
二、积屑瘤对切削力和加工表面粗糙度的影响
2019/4/20
精密加工的关键技术
1.精密加工机床:主轴回转精度、工作台直线运动精度以 及刀具微量进给精度 2.金刚石刀具:金刚石晶面选择、刀具刃口锋利性(刀具 刃口圆弧半径) 3.精密切削机理:微量切削过程的特殊性 4.稳定的加工环境:恒温、防振和空气净化 5.误差补偿:根据规律设定补偿,反馈控制系统 6.精密测量技术
刃口半径为0.6μm、0.3μm
刃口锋锐度对加工表面有一 定的影响,相同条件下(背 吃刀量、进给量),更锋锐 的刀具切出的表面粗糙度更 小;速度的影响不是很大。
2019/4/20
二、刀刃锋锐度对切削变形和切削力的影响
锋锐车刀切削变形系数明显低于 较钝的车刀。 刀刃锋锐度不同,切削力明显不 同。刃口半径增大,切削力增大, 即切削变形大。背吃刀量很小时, 切削力显著增大。因为背吃刀量很 小时,刃口半径造成的附加切削变 形已占总切削变形的很大比例,刃 口的微小变化将使切削变形产生很 大的变化。所以在背吃刀量很小的 精切时,应采用刃口半径很小的锋 锐金刚石车刀。
2019/4/20
一、切削速度、进给量、修光刃和背吃刀量的影响
4、背吃刀量的影响
在刀具刃口半径足够小时,超精密切削范围内,背吃 刀量变化对加工表面粗糙度影响很小。 背吃刀量减少,表面残留应力也减少,但超过某临界 值时,背吃刀量减少反而使加工表面残留应力增加。
2019/4/20
一、刃口锋锐度对加工表面粗糙度的影响
2019/4/20
精密加工的加工范畴
按加工精度划分,可将机械加工分为一般加工、精密加工、超 精密加工三个阶段。
精密加工:加工精度在0.1~1µm,加工表面粗糙度在Ra0.02~ 0.1µm之间的加工方法称为精密加工;
超精密加工:加工精度高于0.1µm,加工表面粗糙度小于 Ra0.01µm之间的加工方法称为超精密加工(微细加工、超微细 加工、光整加工、精整加工等 )。
2019/4/20
三、刀刃锋锐度对切削表面层的冷硬和组织位错的影响
2019/4/20
总结:天然单晶金刚石刀具只能用在机床主轴转 动非常平稳的高精度车床上,否则由于振动金刚 石刀具将会很快产生刀刃微观崩刃。
2019/4/20
图2-3:图a是刀刃磨损的正 常情况,图b是剧烈磨损情 况,可以看到磨损后成层状, 即刀具磨损为层状微小剥落。 图2-4:图中所示沿切削速 度方向出现磨损沟槽,由于 金刚石和铁、镍的化学和物 理亲和性而产生的腐蚀沟槽。 图2-5:金刚石切削时,若 有微小振动,就会产生刀刃 微小崩刃。
2019/4/20
一、切削参数对积屑瘤生成的影响 1、切削速度的影响
不管在多大的切削速度下都有积屑瘤生 成,切削速度不同,积屑瘤的高度也不 同。当切削速度较低时,积屑瘤高度较 高,当切削速度达到一定值时,积屑瘤 趋于稳定,高度变化不大。
2019/4/20
2、进给量f和背吃刀量 p 的影响
1、对切削力的影响
积屑瘤高时切削力也大,积屑瘤小时切削力也小。 与普通切削规律正好相反。
2019/4/20
切削模型分析
1)积屑瘤前端Rቤተ መጻሕፍቲ ባይዱ约
实际切削厚度
2~3μm,实际切削 力由刃口半径R起 作用,切削力明显 增加 。 2)积屑瘤与切削层和 已加工表面间的摩 擦力增大,切削力 增大。 3)实际切削厚度超过 名义值,切削厚度 增加 hD-hDu,切削 力增加。
2019/4/20
二、积屑瘤对切削力和加工表面粗糙度的影响
2、对加工表面粗糙度的影响
积屑瘤高度大,表面粗糙度大,积屑瘤小表面粗糙度小。并 且可以看出,切削液减小积屑瘤,减小加工表面粗糙度。
2019/4/20
一、切削速度、进给量、修光刃和背吃刀量的影响
1、切削速度的影响
由图2-12知,在有切削液的条件下,切削速度对加工表面粗 糙度的影响很小。 图2-13说明,不同切削速度下均得到表面粗糙度极小的加工 表面 —镜面。 2019/4/20
2019/4/20
2.2精密切削加工机理
切削速度向来是影响刀具耐用度最主要的因素,但 是切削速度的高低对金刚石刀具的磨损大小影响甚 微,刀具的耐用度极高。原因是:金刚石的硬度极 高,耐磨性好,热传导系数高,和有色金属间的摩 擦系数低,因此切削温度低,在加工有色金属时刀 具耐磨度甚高,可用很高的切削速度1000~ 2000m/min,而刀具的磨损甚小。 超精密切削实际速度的选择根据所使用的超精密机 床的动特性和切削系统的动特性选取,即选择振动 最小的转速。