精密切削加工资料
精密切削加工总结汇报

精密切削加工总结汇报精密切削加工是一项极其重要的制造工艺,它在许多行业中扮演着关键的角色。
在本次总结汇报中,我将对精密切削加工的定义、应用领域、工艺流程、优势和挑战等方面进行详细讨论。
精密切削加工是一种通过切削材料来获得极高精度和表面质量的制造工艺。
该技术广泛应用于航空航天、汽车、医疗器械、光学仪器等高要求的行业。
在这些领域中,零部件的精度和表面质量是至关重要的,而精密切削加工能够通过各种切削工具和机床来实现这些要求。
精密切削加工的工艺主要包括车削、铣削、磨削、电火花加工和线切割等。
这些工艺可以实现对工件的内外形状、尺寸和表面质量的高精度加工。
例如,车削可以用于加工旋转对称的工件,而磨削可以用于加工高硬度材料和形状复杂的工件。
通过灵活运用这些工艺,可以满足不同行业对零部件高精度加工的需求。
精密切削加工与其他制造工艺相比具有许多优势。
首先,它可以实现高精度加工,精度可以达到亚微米甚至纳米级。
其次,精密切削加工可以获得优异的表面质量,满足行业对光学和光电零件高光洁度的要求。
此外,该工艺还可以适用于各种材料,包括金属、复合材料和陶瓷等,具有非常广泛的应用领域。
然而,精密切削加工也面临一些挑战。
首先,该工艺对设备和工具的要求非常高,需要高精度的切削工具和稳定的机床。
此外,加工过程中还存在工件变形的问题,特别是对于大尺寸和细长的工件来说更加明显。
同时,精密切削加工的工艺参数选择和优化也是一个复杂的任务,需要对材料、切削力、温度等因素进行综合考量。
为了解决这些挑战,我们可以借助先进的切削技术和工艺改进来提高效率和质量。
例如,通过引入高速切削和超精密切削技术,可以提高加工速度和表面质量。
另外,通过优化刀具和刀具材料的选择,可以降低切削力和热变形。
总之,精密切削加工是一项不可或缺的制造工艺,具有广泛的应用领域和重要的经济意义。
在未来,随着科技的进步和工艺的改进,精密切削加工将会进一步提高加工效率和质量,为各行业的发展做出更大的贡献。
超精密切削加工技术探析
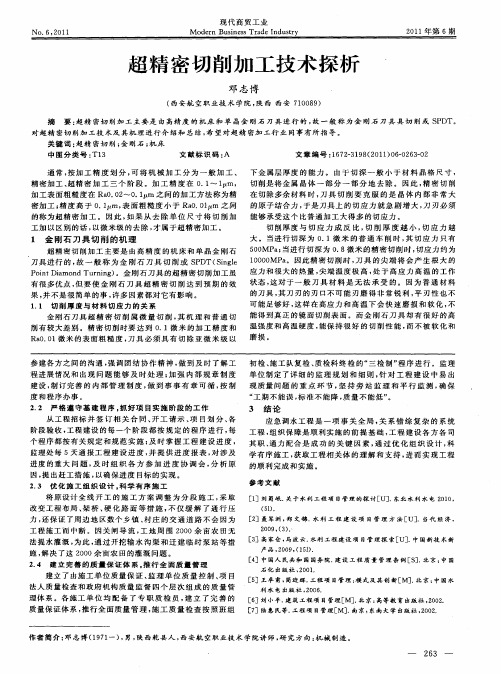
用 的 区 域 ) 是 加 工 单 位 , 工 单 位 的 大 小 和 材 料 缺 陷 分 布 切 削 刃钝 圆 圆 弧 上 某 一 质 点 A 的受 力 情 况 见 图 。该 点 有 切 就 加 的尺 寸 大 小 不 同 时 , 加 工 材 料 的 破 坏 方 式 就 不 同 。 被 向分 力 F 和 法 向 分 力 F , 力 为 F , 。切 向 分 力 使 质 点 z y合 yZ 向前 移 动 , 成 切 屑 ; 向 分 力 使 质 点 压 向 被 加 工 表 面 , 形 法 形 2 超精 : 精 密 切 削加 工 主 要 是 由 高精 度 的 机 床 和 单 晶 金 刚 石 刀 具 进 行 的 , 一 般 称 为金 刚 石 刀 具 具 切 削 或 S D 超 故 P T。
对 超 精 密 切 削加 工 技 术 及 其 机 理 进 行 介 绍 和 总 结 , 望 对 超 精 密加 工 行 业 同事 有 所 指 导 。 希
21 年第 6 01 期
1 2 材 料 缺 陷 及 其 对 超 精 密 切 削 的 影 响 .
2 2 金 刚 石 刀 具 超 精 密 车 削 的切 屑 形 成 . 金 刚 石 刀 具 超 精 密 车 削 是 一 种 原 子 、 子 级 加 工 单 位 分 金刚石 刀具超精密车削所 能切 除金 属层 的厚度 标志其 的去 除 ( 离 ) 工 方 法 , 从 工 件 上 去 除 材 料 , 要 相 当 大 加 工 水 平 。 当 前 , 小 切 削 深 度 可 达 0 1微 米 以 下 , 主 要 分 加 要 需 最 . 其 的能 量 , 种 能 量 可 用 临 界 加 工 能 量 密 度  ̄ J c ) 单 位 影 响 因素 是 刀 具 的锋 利 程 度 , 般 以 刀 具 的 切 削 刃 钝 圆 半 这 (/ m3 和 一
精密加工技术-概述

光整加工原理
光整加工的目的
光整加工的目的是提高工件表面质量,降低表面粗糙度,去除表 面划痕、微观裂纹等缺陷。
光整加工方法
光整加工方法包括研磨、抛光、刷光、超精加工等。根据工件的材 料和表面质量要求选择合适的方法。
光整加工材料与工具
光整加工中使用的材料和工具包括研磨剂、抛光轮、刷光轮等,其 质量和选择直接影响光整加工的效果。
精密加工技术在集成电路制造中发挥着重要作用,可以用于制造芯片和封装测试等环节,提高集成电 路的性能和可靠性。
电子元器件制造
精密加工技术可以用于制造各种电子元器件,如电容、电感、电阻等,提高元器件的精度和稳定性。
医疗器械领域的应用
人工关节制造
精密加工技术可以用于制造人工关节,如髋关节、膝关节等,提高关节的匹配度和使用 寿命。
加工过程的智能控制
1 2
实时监测与反馈控制
通过传感器和检测设备实时监测加工过程,对加 工参数进行实时调整,提高加工精度和稳定性。
机器学习与人工智能
利用机器学习和人工智能技术对加工数据进行处 理和分析,实现加工过程的智能优化和控制。
3
虚拟仿真与预测
通过虚拟仿真技术预测加工过程和结果,对加工 参数进行优化,减少试制和试验成本。
精密加工技术-概述
contents
目录
• 精密加工技术简介 • 精密加工技术的基本原理 • 精密加工的关键技术 • 精密加工技术的未来发展 • 精密加工技术的应用前景
01
精密加工技术简介
定义与特点
定义
精密加工技术是指在加工过程中 ,通过高精度和高效率的方法, 将原材料转化为具有特定形状、 尺寸和表面质量的产品的技术。
03
精密加工的关键技术
精密加工技术
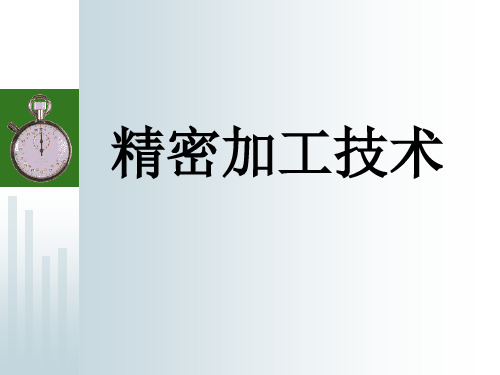
b.混粉加工方法
在放电加工液内混入粉末添加剂 ,以高速获得光泽面的加工方法称 之为混粉加工。该方法主要应用于 复杂模具型腔,尤其是不便于进行 抛光作业的复杂曲面的精密加工。 可降低零件表面粗糙度值,省去手 工抛光工序,提高零件的使用性能 (如寿命、耐磨性、耐腐蚀性、脱 模性等)。混粉加工技术的发展, 使精密型腔模具镜面加工成为现实 。
真空热处理炉已广泛采用了计算机 控制,目前已发展到真空化学热处理 和真空气淬热处理,包括高压真空 气淬、高流率真空气淬和高压高流 率真空气淬技术等。另外,激光热 处理技术在国外已广泛用于航空、 航天、电子、仪表等领域,如各种 复杂表面件、微型构件、需局部强 化处理构件、微型电子器件、大规 模集成电路的生产和修补、精密光 学元件、精密测量元件等。
4.数控电火花加工新工艺的应用
a.标准化夹具
数控电火花加工为保证极高的重 复定位精度且不降低加工效率,采用 快速装夹的标准化夹具。标准化夹具 ,是一种快速精密定位的工艺方法, 它的使用大大减少了数控电火花加工 过程中的装夹定位时间,有效地提升 了企业的竞争力。目前有瑞士的 EROWA和瑞典的3R装置可实现快速精 密定位。
5、抛光 是利用机械、化学、电 化学的方法对工件表面进行的一种微 细加工,主要用来降低工件表面粗糙 度,常用的方法有:手工或机械抛光 、超声波抛光、化学抛光、电化学抛 光及电化学机械复合加工等。手工或 机械抛光加工后工件表面粗糙度 Ra≤0.05µm,可用于平面、柱面、曲 面及模具型腔的抛光加工。超声波抛 光加工精度 0.01~0.02µm,表面粗糙 度Ra0.1µm。化学抛光加工的表面粗糙 度一般为Ra≤0.2µm。电化学抛光可提 高到Ra0.1~0.08µm。
模糊控制技术是由计算机监测来 判定电火花加工间隙的状态,在保持 稳定电弧的范围内自动选择使加工效 率达到最高的加工条件;自动监控加
常用精密加工和超精密加工方法
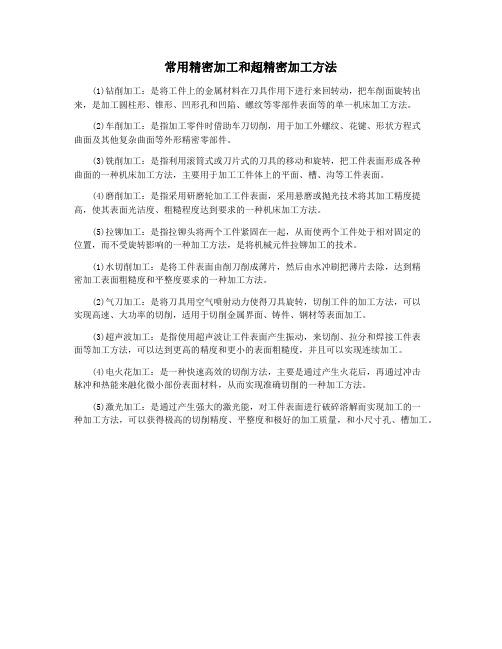
常用精密加工和超精密加工方法(1)钻削加工:是将工件上的金属材料在刀具作用下进行来回转动,把车削面旋转出来,是加工圆柱形、锥形、凹形孔和凹陷、螺纹等零部件表面等的单一机床加工方法。
(2)车削加工:是指加工零件时借助车刀切削,用于加工外螺纹、花键、形状方程式曲面及其他复杂曲面等外形精密零部件。
(3)铣削加工:是指利用滚筒式或刀片式的刀具的移动和旋转,把工件表面形成各种曲面的一种机床加工方法,主要用于加工工件体上的平面、槽、沟等工件表面。
(4)磨削加工:是指采用研磨轮加工工件表面,采用悬磨或抛光技术将其加工精度提高,使其表面光洁度、粗糙程度达到要求的一种机床加工方法。
(5)拉铆加工:是指拉铆头将两个工件紧固在一起,从而使两个工件处于相对固定的位置,而不受旋转影响的一种加工方法,是将机械元件拉铆加工的技术。
(1)水切削加工:是将工件表面由削刀削成薄片,然后由水冲刷把薄片去除,达到精密加工表面粗糙度和平整度要求的一种加工方法。
(2)气刀加工:是将刀具用空气喷射动力使得刀具旋转,切削工件的加工方法,可以实现高速、大功率的切削,适用于切削金属界面、铸件、钢材等表面加工。
(3)超声波加工:是指使用超声波让工件表面产生振动,来切削、拉分和焊接工件表面等加工方法,可以达到更高的精度和更小的表面粗糙度,并且可以实现连续加工。
(4)电火花加工:是一种快速高效的切削方法,主要是通过产生火花后,再通过冲击脉冲和热能来融化微小部份表面材料,从而实现准确切削的一种加工方法。
(5)激光加工:是通过产生强大的激光能,对工件表面进行破碎溶解而实现加工的一种加工方法,可以获得极高的切削精度、平整度和极好的加工质量,和小尺寸孔、槽加工。
超精密切削加工技术

(1)积屑瘤的生成规律及影响
• 超精密切削过程中积屑瘤对切削力的影响远远大 于在普通切削中的影响。 • 铝铜材料在低速切削时,切削力较大,随切削速 度的增加,切削力急剧下降,至200~300m/min 后,切削力基本保持不变。 • 其原因在于低速时生成的积屑瘤高,使切削层厚 度大幅度增加,故切削力也大,随速度增加积屑 瘤高度急剧减小,因而切削力也急剧下降。 • 这个规律与普通切削正好相反。
刀具的几何参数影响加工表面粗糙 度
• 若为圆弧刃切削,刀尖半径为r,进给量为f 则表面粗糙度 Rmax=f 2/8r • 若为直刃切削,主偏角Kγ,副偏角Kγ’ 则表面粗糙度 Rmax=f·tgkγ·tgk’ γ/ (tgKγ+tgK’ γ) • 因此刀具的主、辅偏角、刀尖半径和进给 量都会对超精密加工表面的粗糙度产生直 接的影响。
切削用量的选择
切削深度的选择
• 超精密切削时允许的最小切深取决于金刚 石刀具的刃口半径ρ,约是(1/2~1/3)ρ。 • 若刃口半径达到ρ=0.05~0.01μm,最小切 削深度可以在0.01μm以下,获得超光滑表 面。
进给量和修光刃的选择
• 超精密切削都采用很小的进给量,刀具制 成带修光刃的刀尖结构。 • 但对有修光刃的刀具且f≤0.02mm/r时,进 给量再减小对表面粗糙度的影响甚微。 • 修光刃可以减小加工表面粗糙度,修光刃 的长度取0.05~0.10mm。 • 长度过长,对提高加工表面质量效果不大。
加工环境与边缘技术是不可忽视的 间接因素
②振动 • 电机转子与定子间的磁力不均、联接器因 准直误差和回转振摆等都会产生振动问题。 • 为此需要改善各机械零部件和工艺系统的 动态特性,采用力偶传递动力,如精密摸 床上的双销鸡心夹头。
超精密切削加工技术介绍

超精密切削加工技术介绍
超精密加工技术是适应现代高科技的需要而发展起来的先进制造技术, 是高科技尖端产品开发中不可或缺的关键技术, 是一个国家制造业水平重要标志, 是先进制造技术基础和关键, 也是装备现代化不可缺少的关键技术之一, 在军用和民用工业中有着十分广阔的应用前景。
金刚石超精密切削技术, 是超精密加工技术发展最早的、应用最为广泛的技术之一。
超精密切削加工技术
1、超精密切削的历史
60年代初,由于宇航用的陀螺,计算机用的磁鼓、磁盘,光学扫描用的多面棱镜,大功率激光核聚变装置用的大直径非圆曲面镜,以及各种复杂形状的红外光用的立体镜等等,各种反射镜和多面棱镜精度要求极高,使用磨削、研磨、抛光等方法进行加工,不但加工成本很高,而且很难满足精度和表面粗糙度的要求。
为此,研究、开发了使用高精度、高刚度的机床和金刚石刀具进行切削加工的方法加工。
2、超精密切削加工的应用
(1)平面镜的切削
平面度
金刚石刀具
1、金刚石刀具特点
金刚石刀具拥有很高的高温强度和硬度,而且材质细密,经过精细研磨,切削刃可磨得极为锋利,表面粗糙度值很小,因此可进行镜面切削。
金刚石刀具超精密切削主要用于加工铜、铝等有色金属,如高密度硬磁盘的铝合金基片、激光器的反射镜、复印机的硒鼓、光学平面镜,凹凸镜、抛物面镜等。
超精切削刀具材料有天然金刚石,人造单晶金刚石。
金刚石刀具磨损的常见形式为机械磨损和破损。
机械磨损——机械摩擦、非常微小;破损。
精密和超精密加工复习整理资料

精密和超精密加⼯复习整理资料1.精密和超精密加⼯⽬前包含的三个领域:超精密切削、精密和超精密磨削研磨和精密特种加⼯2.超精密加⼯中超稳定的加⼯环境条件主要指(恒温)、(恒湿)、(防振)和(超净)四个⽅⾯的条件。
3.电⽕花型腔加⼯的⼯艺⽅法有:(单电极平动法)、(多电极更换法)、(分解电极法)、简单电极数控创成法等。
4.超精密加⼯机床的总体布局形式主要有以下⼏种:(T形布局)、(⼗字形布局)、(R-θ布局)、(⽴式结构布局)等。
5.实现超精密加⼯的技术⽀撑条件主要包括:(超精密加⼯机理与⼯艺⽅法)、(超精密加⼯机床设备)、(超精密加⼯⼯具)、(精密测量和误差补偿)、⾼质量的⼯件材料、超稳定的加⼯环境条件等。
6.激光加⼯设备主要包括电源、(激光器)、(光学系统)、(机械系统)、控制系统、冷却系统等部分。
7.精密和超精密加⼯机床主轴轴承的常⽤形式有(液体静压轴承)和(空⽓静压轴承)。
8.⾦刚⽯晶体的激光定向原理是利⽤⾦刚⽯在不同结晶⽅向上(因晶体结构不同⽽对激光反射形成不同的衍射图像)进⾏的。
9.电⽕花加⼯蚀除⾦属材料的微观物理过程可分为(介质电离击穿)、(介质热分解、电极材料熔化、⽓化)、(蚀除物抛出)和(间隙介质消电离)四个阶段。
10.超精密加⼯机床的关键部件主要有:(精密主轴部件)、(导轨部件)和(进给驱动系统)等。
11.三束加⼯是指电⼦束、离⼦束和激光束。
12.所谓空⽓洁净度是指空⽓中含尘埃量多少的程度。
13.⼯业⽣产中常见的噪声主要有空⽓动⼒噪声、机械噪声和电磁噪声。
14.纳⽶级加⼯精度包含:纳⽶级尺⼨精度、纳⽶级⼏何形状精度、纳⽶级表⾯质量。
15.超精密切削时积屑瘤的⽣成规律:1)在低速切削时,h0值⽐较稳定;在中速时值不稳定。
2)在进给量f很⼩时,h0较⼤3)在背吃⼑量a p<25um时,h0变化不⼤;在a p>25um时,h0将随a p的值增⼤⽽增⼤。
16.超精密切削时积屑瘤对切削过程的影响:积屑瘤⾼时切削⼒⼤,积屑瘤⼩时切削⼒⼩。
- 1、下载文档前请自行甄别文档内容的完整性,平台不提供额外的编辑、内容补充、找答案等附加服务。
- 2、"仅部分预览"的文档,不可在线预览部分如存在完整性等问题,可反馈申请退款(可完整预览的文档不适用该条件!)。
- 3、如文档侵犯您的权益,请联系客服反馈,我们会尽快为您处理(人工客服工作时间:9:00-18:30)。
一、切削速度、进给量、修光刃和背吃刀量的影响
2、进给量的影响
在进给量f<5μm/r
时,均达到
Rmax<0.05μm的加工 表面粗糙度。
2019/1/9
பைடு நூலகம்
一、切削速度、进给量、修光刃和背吃刀量的影响
3、修光刃的影响
修光刃长度常取0.05~ 0.20mm。 修光刃的长度过长,对 加工表面粗糙度影响不 大。 修光刃有直线和圆弧两 种,加工时要精确对 刀,使修光刃和进给方 向一致。圆弧刃半径一般 取2~5mm。
2019/1/9
二、积屑瘤对切削力和加工表面粗糙度的影响
2、对加工表面粗糙度的影响
积屑瘤高度大,表面粗糙度大,积屑瘤小表面粗糙度小。并 且可以看出,切削液减小积屑瘤,减小加工表面粗糙度。
2019/1/9
一、切削速度、进给量、修光刃和背吃刀量的影响
1、切削速度的影响
由图2-12知,在有切削液的条件下,切削速度对加工表面粗 糙度的影响很小。 图2-13说明,不同切削速度下均得到表面粗糙度极小的加工 表面 —镜面。 2019/1/9
刃口半径为0.6μm、0.3μm
刃口锋锐度对加工表面有一 定的影响,相同条件下(背 吃刀量、进给量),更锋锐 的刀具切出的表面粗糙度更 小;速度的影响不是很大。
2019/1/9
二、刀刃锋锐度对切削变形和切削力的影响
锋锐车刀切削变形系数明显低于 较钝的车刀。 刀刃锋锐度不同,切削力明显不 同。刃口半径增大,切削力增大, 即切削变形大。背吃刀量很小时, 切削力显著增大。因为背吃刀量很 小时,刃口半径造成的附加切削变 形已占总切削变形的很大比例,刃 口的微小变化将使切削变形产生很 大的变化。所以在背吃刀量很小的 精切时,应采用刃口半径很小的锋 锐金刚石车刀。
2019/1/9
一、切削参数对积屑瘤生成的影响 1、切削速度的影响
不管在多大的切削速度下都有积屑瘤生 成,切削速度不同,积屑瘤的高度也不 同。当切削速度较低时,积屑瘤高度较 高,当切削速度达到一定值时,积屑瘤 趋于稳定,高度变化不大。
2019/1/9
2、进给量f和背吃刀量 p 的影响
由图2-8可以看出在进给量很小时,积屑瘤的高度很大, 在f=5μm/r时,h0值最小,f值再增大时,h0值稍有增 加。 由图2-9所示,在背吃刀量<25μm时,积屑瘤的高度变 化不大,但在背吃刀量> 25μm后, h0值将随着背吃 刀量的增加而增加。
2019/1/9
一、切削速度、进给量、修光刃和背吃刀量的影响
4、背吃刀量的影响
在刀具刃口半径足够小时,超精密切削范围内,背吃 刀量变化对加工表面粗糙度影响很小。 背吃刀量减少,表面残留应力也减少,但超过某临界 值时,背吃刀量减少反而使加工表面残留应力增加。
2019/1/9
一、刃口锋锐度对加工表面粗糙度的影响
2019/1/9
总结:天然单晶金刚石刀具只能用在机床主轴转 动非常平稳的高精度车床上,否则由于振动金刚 石刀具将会很快产生刀刃微观崩刃。
2019/1/9
图2-3:图a是刀刃磨损的正 常情况,图b是剧烈磨损情 况,可以看到磨损后成层状, 即刀具磨损为层状微小剥落。 图2-4:图中所示沿切削速 度方向出现磨损沟槽,由于 金刚石和铁、镍的化学和物 理亲和性而产生的腐蚀沟槽。 图2-5:金刚石切削时,若 有微小振动,就会产生刀刃 微小崩刃。
2019/1/9
二、积屑瘤对切削力和加工表面粗糙度的影响
1、对切削力的影响
积屑瘤高时切削力也大,积屑瘤小时切削力也小。 与普通切削规律正好相反。
2019/1/9
切削模型分析
1)积屑瘤前端R大约
实际切削厚度
2~3μm,实际切削 力由刃口半径R起 作用,切削力明显 增加 。 2)积屑瘤与切削层和 已加工表面间的摩 擦力增大,切削力 增大。 3)实际切削厚度超过 名义值,切削厚度 增加 hD-hDu,切削 力增加。
第2章 精密切削加工
2.1概述 2.2精密切削加工的工艺规律和机理 2.3精密切削加工的机床及应用 2.4功率超声车削
2019/1/9
2.1概述
精密切削是使用精密的单晶天然金刚石刀具加工有色金属 和非金属,可以直接加工出超光滑的加工表面(粗糙度 Ra0.02~0.005µm,加工精度<0.01µm)。 用于加工:陀螺仪、激光反射镜、天文望远镜的反射镜、 红外反射镜和红外透镜、雷达的波导管内腔、计算机磁盘、 激光打印机的多面棱镜、录像机的磁头、复印机的硒鼓、 菲尼尔透镜等。 精密切削也是金属切削的一种,当然也服从金属切削的普 遍规律。 金刚石刀具的精密加工技术主要应用于单件大型超精密零 件的切削加工和大量生产中的中小型超精密零件加工。
2019/1/9
2.2精密切削加工机理
切削速度向来是影响刀具耐用度最主要的因素,但 是切削速度的高低对金刚石刀具的磨损大小影响甚 微,刀具的耐用度极高。原因是:金刚石的硬度极 高,耐磨性好,热传导系数高,和有色金属间的摩 擦系数低,因此切削温度低,在加工有色金属时刀 具耐磨度甚高,可用很高的切削速度1000~ 2000m/min,而刀具的磨损甚小。 超精密切削实际速度的选择根据所使用的超精密机 床的动特性和切削系统的动特性选取,即选择振动 最小的转速。
2019/1/9
精密加工的关键技术
1.精密加工机床:主轴回转精度、工作台直线运动精度以 及刀具微量进给精度 2.金刚石刀具:金刚石晶面选择、刀具刃口锋利性(刀具 刃口圆弧半径) 3.精密切削机理:微量切削过程的特殊性 4.稳定的加工环境:恒温、防振和空气净化 5.误差补偿:根据规律设定补偿,反馈控制系统 6.精密测量技术
2019/1/9
精密加工的加工范畴
按加工精度划分,可将机械加工分为一般加工、精密加工、超 精密加工三个阶段。
精密加工:加工精度在0.1~1µm,加工表面粗糙度在Ra0.02~ 0.1µm之间的加工方法称为精密加工;
超精密加工:加工精度高于0.1µm,加工表面粗糙度小于 Ra0.01µm之间的加工方法称为超精密加工(微细加工、超微细 加工、光整加工、精整加工等 )。
2019/1/9
三、刀刃锋锐度对切削表面层的冷硬和组织位错的影响