大容量输液制剂的生产工艺
4[1][1].2大容量注射剂(输液)制备与分析 ——之学生工作页
![4[1][1].2大容量注射剂(输液)制备与分析 ——之学生工作页](https://img.taocdn.com/s3/m/0325805777232f60ddcca157.png)
姓名:项 目 任 务 书一、项目描述二、材料清单序号 各种材料清单数量 备注 1 2 3 4 5 6 7 8 9 10课题 葡萄糖注射液制备与分析 班级:制药103提出问题 输液是医生把救治病人的药物直接注射到病人血液里的一种治疗方法,同时也是医生救治病人最常用的一种治疗方法。
所以输液在制备方法上和产品质量上有重要的意义。
请问:人为何要输液?你能举例说出在什么情况下病人必须要挂水?什么是输液?葡萄糖注射液是如何制备和质量评价? 任务分析 1、葡萄糖注射液的制备方案设计2、葡萄糖注射液质量分析方案设计3、项目实施 相关知识及资料三、项目实施过程(一)任务分析:通过本模块的学习,学生明确1、掌握输液剂的生产工艺过程及操作要点;2、掌握输液瓶及容器具的处理方法与要求;3、能按生产指令单,领取原材料,完成制备操作并作好其它准备工作4、掌握GMP对大容量注射剂制备过程管理要点及安全环保知识5、熟悉无菌操作室的洁净处理、空气灭菌和无菌操作的要求及操作方法。
6、掌握葡萄糖注射液生产中的中间质量控制的质量检测项目及方法。
7、掌握旋光仪、酸度计等仪器的操作方法。
(二)任务实施要求1. 查找资料,了解葡萄糖注射液的药理作用,葡萄糖的化学及物理性质,并在课业报告中加以描述。
2. 设计药剂处方和质量分析,其内容包括:确定葡萄糖注射液制备工艺、pH 计和旋光度的原理及其使用方法。
药剂处方中各成分的作用为课后报告内容。
3. 思考并设计分析、配制方法,并预先考虑应该注意的事项。
4. 在药物制剂技术实验室完成药剂的分析。
在课业报告中详细描述分析过程。
5. 每个小组选一个学生代表将本组的工作情况向其他小组同学介绍。
6、本小组同学集体给本组工作评分,并给其他小组评分。
(三)具体项目任务实施任务一:详述葡萄糖注射液的药理作用,葡萄糖的化学及物理性质【药理作用】葡萄糖是人体主要的热量来源之一,每1克葡萄糖可产生4大卡(16.7kJ)热能,故被用来补充热量。
大容量注射剂生产工艺流程图
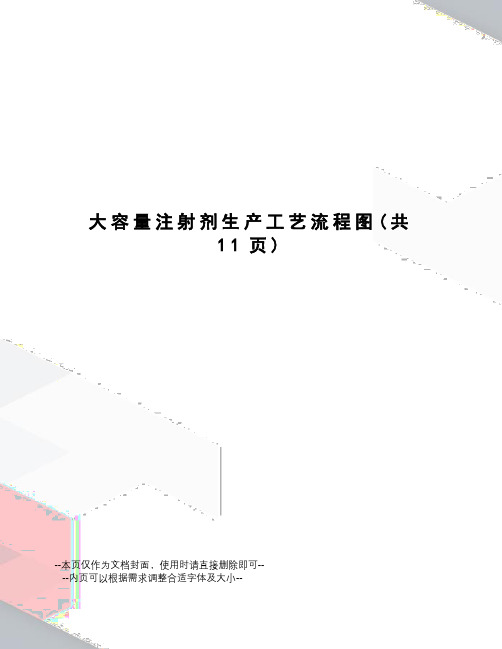
大容量注射剂生产工艺流程图(共11页)--本页仅作为文档封面,使用时请直接删除即可----内页可以根据需求调整合适字体及大小--目录1.大容量注射剂生产区概况2.需要验证的关键工序及工艺验证3.工艺流程的实施4.操作过程及工艺条件5.技术安全、工艺卫生及劳动保护6.物料平衡及技经指标7.设备一览表8.岗位定员9.附件(含设备操作、清洁规程)10.变更记录1.大容量注射剂生产区概况本生产区面积904㎡,其中1万级净化区域167㎡,10万级净化区域174㎡。
大容量注射剂车间采用10万级和1万级(局部百级)空气净化洁净级别,10万级区域设置缓冲、更衣、洗涤、洁具、称量、配碳、浓配、洗瓶等,1万级区域设置缓冲、更衣更鞋、稀配、化验、灌装、加塞、轧盖、洗涤、存放、洁具等功能间,所有隔断采用无粉尘产生的静电喷涂彩钢板,结合处采用圆角处理,不易产生积灰;人员经过三次更衣和二次更鞋后进入洁净区操作,物料进入洁净区均采用传递窗或气闸进行传递,人流、物流的进入相对分开,保证了洁净区空气洁净度要求;生产设备均采用优质不锈钢材料制造,采用洗瓶、灌装、压塞、轧盖联动线生产,其中洗瓶出口、灌装、加塞采用百级层流保护,灭菌器采用水浴式灭菌器。
1.1 大容量注射剂生产工艺流程图(见后页)1.2 大容量注射剂生产区工艺布局布置图(见后页)1.3 大容量注射剂生产区工艺设备布置图(见后页)1.4 大容量注射剂生产区送回风口平面布置图(见后页)以上项目按验证文件规定,均已在规定周期内进行相关的验证,验证方案及报告见相应文件。
大容量注射剂生产工艺流程图3.工艺流程的实施3.1 批生产指令的签发3.1.1 批生产指令由车间技术负责人根据生产计划表起草,并依据产品工艺规程于生产前一个工作日制定。
3.1.2 批生产指令应经QA质监员审核并签字,由车间主任签字批准后生效。
3.2 生产批记录的发放3.2.1 除配制工序和包装工序外,工序相应的生产批记录于生产当日由车间工艺质监员发放给各工序负责人,并于工序结束当日填写完整返回车间工艺质监员处汇总。
大输液质量控制

大输液生产工艺流程及控制要点
大输液生产工艺流程及控制要点
车间介绍 大输液生产工艺流程
总结
2
科技为本 · 创造健康生活
车间介绍
科技为本 · 创造健康生活
➢车间为软袋大容量注射剂(最终灭菌)车间,车间于2011年筹建,2012年通过 GMP认证,2017年通过GMP再认证。现主要生产品种有钠钾镁钙葡萄糖注射液 (500ml、250ml),钠钾葡萄糖注射液500ml等。
0022
脱包:物料接收、传递 配制:独立复核
03 灌装:装量控制、质量检查
大输液工艺控制点总结
包装:打印标签复核、区域 隔离、清场彻底、物料平衡
大输液生产工艺流程介绍
科技为本 · 创造健康生活
01
生产前 准备
清场, 内包材; CIP、SIP
0022
试试灌灌装
焊接质量 装量
打印
03
正正式式生生 产产
每半小 时检查 相关质量 控制项目
灌装
大输液生产工艺流程介绍
科技为本 · 创造健康生活
灌装:生产前准备
➢ 确认房间状态为清场合格证状态,是否在有效期内。
0022 液均一性。 03 ➢药➢ 液通 岗装过位量人重是员量否每法符半测合小定要时(求药进。液行重相量关质=体量积监×测密项度目+检空查袋正正产。重式式量生生)所灌
➢ 车间生产的产品自浓配开始至稀配结束、稀配结束至灌装 结束、灌装结束至灭菌开始等工序时限工艺中均有规定。
第一百九十七条 液体制剂的配制、过滤、灌封、灭菌等工序应当 规定时间内完成。
大输液生产工艺流程介绍
科技为本 · 创造健康生活
卸袋 1、灭菌结束后,小车经物流输送系统至自动卸袋机,进行拆盘卸袋; 2、灭菌合格品经隧道式干燥机传送至灯检间; 3、下料过程中如发现不合格产品,及时放入不合格品收集柜内。
输液的生产工艺流程

输液的生产工艺流程
输液是一种将药物溶液通过静脉途径输送到患者体内的治疗方式,广泛应用于临床医学中。
输液的生产工艺流程主要包括药物配制、净化处理、灌装封口和包装等环节。
首先,药物配制是输液生产的第一步。
首先,根据处方要求计量所需的药物原料。
然后,将药物原料加入容器中,加入适量的溶剂使其溶解。
配制过程中,需严格按照配方要求进行计量和操作,确保药物的准确性和稳定性。
接下来是净化处理。
输液需要经过严格的净化处理,以确保其符合药物管理标准。
净化处理主要包括过滤和杀菌两个环节。
过滤过程中,使用一系列的过滤器去除悬浮物和颗粒杂质,确保制剂的清澈和无菌。
杀菌过程中,采用高温高压或化学消毒法杀灭微生物,确保制剂的无菌性。
随后是灌装封口。
净化完成后,将药物溶液灌装到洁净的容器中。
灌装过程中,需注意避免空气进入容器,以防止药物氧化或污染。
同时,要确保灌装的准确性和稳定性,确保药物每瓶分装均匀。
最后是包装。
完成灌装封口后,将药物装入耐压容器。
容器需要符合相关的药品包装规范,保证药物的质量和稳定性。
同时,要对容器进行密封,确保药物的无菌性和安全性。
在整个输液生产过程中,要严格按照药品管理法规进行操作,保证药物的质量和安全。
此外,还要定期检查和验证生产流程,
确保输液生产的持续性和稳定性。
总之,输液生产工艺流程包括药物配制、净化处理、灌装封口和包装等环节。
通过严格的操作和检验,确保输液的药物质量和安全性。
这些工艺流程的实施和管理将可以保证输液的质量和疗效。
大容量注射液生产工艺规程

制药有限公司大容量注射液生产工艺规程颁发单位:GMP办公室工艺规程批准程序目录1. 剂型、规格 (3)2. 生产工艺流程 (3)3. 操作过程及工艺条件 (4)4.质量控制要点 (6)5.设备一览表、主要设备生产能力 (7)6.工艺过程中的SOP (7)7.中间产品的控制 (8)8.验证工作要点 (8)9.工艺卫生和环境卫生 (10)10.劳动组织及岗位定员 (10)一、制剂类型:最终灭菌大容量注射液,100ml规格,西林瓶包装。
二、流程图:大容量注射剂工艺流程图三、操作过程及工艺条件1 生产前的检查与确认1.1 是否还留有前批生产的产品或物料,是否已清洁并取得“清场合格证”。
1.2 检查确认生产现场的机器设备和器具是否已清洁并准备完毕挂上“合格”标示。
1.3 所使用原辅料是否准备齐全。
是否有质量检验报告单,合格品才能使用。
1.4 检查工艺用水是否新鲜制备,贮存不得超过24小时。
1.5 检查确认与生产品种相适应的批生产指令、配套文件及有关记录是否已准备齐全。
1.6 检查确认生产场所的温度是否在规定范围内(18-26℃,相对湿度在30%-65%)。
2 洗瓶、塞、铝盖2.1理瓶:根据“批生产指令”准备所需的清洁盘、领取必须的西林瓶。
在理瓶室将西林瓶的合格品摆满瓶盘。
2.2清洗:把西林瓶放在不锈钢传送链条上,开动洗瓶机,定时检查安瓿的清洁度:目检1000ml注射用水无可见异物,抽50支,毛、块≤2%。
洗瓶岗位按清场SOP进行清场,并填写生产记录。
2.3 理塞、铝盖:根据《生产指令》准备所需的丁基胶塞和铝盖,分别、依次放入多功能胶塞漂洗机。
2.4清洗:将丁基胶塞放入多功能漂洗机后,加入纯化水,开动机器进行清洗,清洗后捞出、沥干。
排除纯化水后再加入注射用水清洗,捞出、沥干。
将铝盖放入多功能漂洗机后,加入纯化水,开动机器清洗,清洗后捞出、沥干。
排除纯化水后再加入注射用水清洗,捞出、沥干。
清洗过后,按岗位清场操作规程进行清场,填写清场合格证,并填写生产记录。
大容量输液制剂的生产工艺
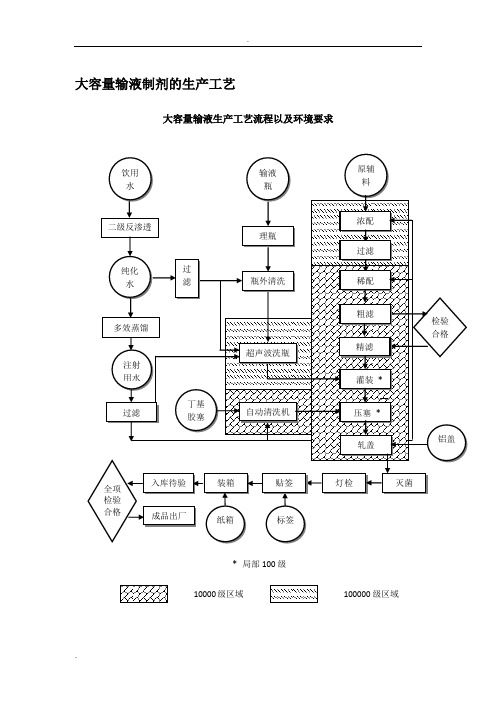
大容量输液制剂的生产工艺大容量输液生产工艺流程以及环境要求大容量输液认证检查要点大输液又名可灭菌大容量注射剂,是指将配制好的药液灌入大于50 ml的输液瓶或袋内,加塞、加盖、密封后用蒸汽热压灭菌而制备的灭菌注射剂。
1、机构与人员a)主管生产和质量管理的企业负责人、生产管理和质量管理部门负责人均应具有医药或相关专业大专以上学历,并具有药品生产和质量管理经验,并履行其职责。
b)企业负责人和各级管理人员应定期接受药品管理法律法规培训。
c)质量检验、生产、维修保养、清洁人员应定期进行卫生和微生物学基础知识、洁净作业等方面的培训和考核,并具有实际操作技能。
2、厂房设施的管理要点及检查重点a)洁净区:我国《药品生产质量管理规范》对最终灭菌的无菌药品生产厂房洁净度级别的要求是:浓配或采用密闭系统的稀配应在100000级洁净区内进行;稀配、滤过、灌封、直接接触药品的包装材料的最终处理等操作应在10000级洁净区内进行;物料、中间品应经过物流缓冲间或传递柜进、出洁净区。
称量配料间如产尘应与洁净走廊呈相对负压,必要时设捕尘设施。
中国药典规定:微生物限度检查、无菌检查应在100级或10000级背景下的局部100级区内进行,并与生产区分开。
微生物限度检查与无菌检查用的实验室和空气净化系统最好彼此分开,以尽可能减少对无菌检查的干扰。
b)空气净化系统应能确保洁净区的洁净度级别、温湿度、压差等符合生产工艺要求并经过验证。
初效、中效过滤器应明确清洗/更换周期,高效过滤器应定期检测其完整性,如有泄漏或阻塞应及时更换。
空气净化系统应每天24小时运行,停用后再次运行应进行清洁、消毒并经过再验证,符合要求的方可开始生产。
c)与产品直接接触的压缩空气、氮气、二氧化碳等辅助设施这些气体因与产品直接接触,不得对产品带来污染。
应对系统进行验证。
PQ测试项目包括洁净度级别、含水量、含油量等。
d)注射用水(WFI)系统以纯化水为原水,经多效蒸馏制得。
大输液生产工艺
大输液生产工艺大输液是指用于输液治疗的药物溶液,主要用于静脉注射。
大输液的生产工艺是指将药物原料经过一系列的加工和处理,制成符合药品质量标准的药物溶液的过程。
大输液的生产工艺一般包括以下步骤。
首先,进行原材料准备。
根据配方要求,准备药物原料、辅料和溶剂等。
药物原料主要是指需要进行溶解或混合的药物成分,辅料主要是为了调节药物制剂的各种性质,如稳定性、pH值等。
溶剂主要是用于溶解药物和辅料的介质,常见的有注射用水。
其次,进行溶解和混合。
将药物原料和辅料按照一定比例加入溶剂中,通过搅拌和加热等方式将其溶解和混合均匀。
这一步骤的目的是将药物和辅料充分溶解在溶剂中,使其形成均匀的药物溶液。
然后,进行过滤和灭菌。
将溶解和混合好的药物溶液进行过滤,去除其中的杂质和微生物。
过滤一般采用微孔滤器或膜滤器等器械,通过筛网或膜孔来阻挡杂质和微生物。
过滤后的药物溶液还需要进行灭菌处理,常见的方法有热灭菌和无菌过滤等。
接着,进行包装和质量检验。
将经过过滤和灭菌处理的药物溶液按照一定规格装入适宜的容器中,如注射瓶、袋装等。
装瓶前需要进行质量检验,包括外观检查、标志和标签的贴附和打印等。
质量检验的目的是确保药物溶液的质量符合规定标准。
最后,进行包装成品的包装和储存。
将装瓶好的药物溶液进行密封和包装,以确保其在储存和运输过程中不受外界环境的影响。
包装常采用塑料袋、纸箱等包材,包装成品应符合药品包装和储存的要求,如密封性、防水性等。
以上就是大输液的生产工艺的主要步骤。
通过上述工艺步骤,可制得符合药品质量标准的药物溶液,以满足临床治疗的需要。
在整个生产工艺中,需严格按照药品生产的标准操作,确保药物的质量和安全性。
年产5200万瓶大输液(葡萄糖注射液)车间GMP工艺设计
课程设计说明书题目: 年产5300万瓶大输液(葡萄糖注射液)车间 GMP 工艺设计2 0 0 7 13 2 8 6张世平 江章应2011 年 1 月 6 日院 系: 专业班级: 学 号: 学生姓名: 指导教师:制药工程系 制药工程07-1班安徽理工大学课程设计(论文)任务书2010年12月20日目录第一章前言1.1 简介大输液为大容量注射剂,是我国医药行业五大类重要制剂之一,在临床上应用广泛。
随着我国医疗技术的进步和人民生活水平的提高,近十多年来,输液剂的研究取得了令人瞩目的成绩。
目前,我国经批准上市的新品种达100 余种;输液产量从1990 年的6.34 亿瓶增加到2003 年的35 亿瓶,输液剂的种类也发生了很大的变化,进一步满足了临床治疗的需要。
输液又名打点滴或者挂水。
是由静脉滴注输入体内的大剂量(一次给药在100ml 以上)注射液。
通常包装在玻璃或塑料的输液瓶或袋中,不含防腐剂或抑菌剂。
使用时通过输液器调整滴速,持续而稳定地进入静脉,以补充体液、电解质或提供营养物质。
由于其用量大而且是直接进入血液的,故质量要求高,生产工艺等亦与小针注射剂有一定差异。
1.2 输液的分类及临床用途1.电解质输液用以补充体内水分、电解质,纠正体内酸碱平衡等。
如氯化钠注射液、复方氯化钠注射液、乳酸钠注射液等。
2.营养输液用于不能口服吸收营养的患者。
营养输液有糖类输液、氨基酸输液、脂肪乳输液等。
糖类输液中最常用的为葡萄糖注射液。
氨基酸输液与脂肪乳输液将在后面专门论述。
3.胶体输液用于调节体内渗透压。
胶体输液有多糖类、明胶类、高分子聚合物类等,如右旋糖酐、淀粉衍生物、明胶、聚乙烯吡咯烷酮(PVP) 等。
1.3 输液的质量要求1、在无菌、澄明度及无热源这三项,应更加特别注意,它们也是输液生产中经常出现的主要问题。
2、含量,色泽,pH 也应符合要求。
pH 应在保障疗效和制品稳定的基础上,力求接近人体的pH,过高或过低都会引起酸碱中毒。
可灭菌大容量注射剂(大输液质量控制点
可灭菌大容量注射剂(大输液)可灭菌大容量注射剂又名大输液、输液剂。
是指将配制好的药液灌入大于50ml的输液瓶或袋内,加塞、加盖、密封后用蒸汽热压灭菌而制备的灭菌注射剂。
常用的输液瓶的玻璃瓶和塑料瓶两种。
重点介绍玻璃瓶装的大容量注射剂的实施要求。
制剂管理要点1. 配制:本工序包括称量、浓配、稀配及半成品检验、过滤等过程。
(1) 称量1)配料前核对原辅料品名、规格、批号、生产厂及数量,并应具有原辅料检验报告单。
调换原辅料生产厂及特殊品种需有小样试制合格报告。
2)原辅料投料量的计算、称量及投料必须复核,操作人、复核人均应在原始记录上签名。
3)剩余的原辅料应封口贮存,在容器外标明品名、批号、日期、剩余量及使用人签名。
4)天平、磅秤每次使用前应校正,并定期由法定部门专人校验、做好记录。
(2) 配制及过滤1) 每个配制罐须标明配制液的全名、规格和批号。
2)板柜过滤机应每次过滤完毕,立即清洗,按清洁操作规程处理。
药液终端用孔径为0.45~0.65μm的滤膜过滤。
3)接触药液的一切容器具,使用前后都必须用注射用水清洗。
更换品种或停用一天以上时必须以清洁剂处理,再以注射用水洗涤至清洁。
4)使用微孔滤膜时先用注射用水漂洗至无异物脱落,并在使用前后作起泡点试验。
5)药液经含量、pH值半成品检验合格后方可精滤。
调整含量须重新测定。
精滤药液经澄明度检查合格后才能灌装。
6)使用的注射用水在80℃以上保温下其贮存时间不宜超过12h。
7)直接与药液接触的惰性气体,用前需经净化处理,其所含微粒量要符合规定的洁净度要求。
2. 洗瓶(1) 瓶子在准备室除去外包装后送至粗洗室。
(2) 选用适当的去污剂,用饮用水精洗,用纯水洗涤内外壁,再用澄明的纯水精洗,最后用孔径为0.45μm滤膜滤过的注射用水洗净。
(3) 定时检查洗瓶质量。
3. 灌装灌装机上盛装药液的容器、管道和管件使用前应以注射用水洗净,更换产品需用清洁剂处理。
软管应选用不落微粒者,特殊产品专用。
年产2000万瓶大输液(葡萄糖注射液)车间GMP工艺设综述
制药设备与工程设计题目:年产2000万支大容量注射剂(100、250、500ml)玻璃生产车间设计学院:药学院中医药学院专业:制药工程(化工制药)年级:09 级组别:第十二组组长:廖勇组员:侯迪、李邦、赵源、彭正刚、杨炜龙、王俊翔、郭舜、赵辉指导教师:刘红刘雪梅成绩:2012年5月28日年产2000万支大容量注射剂(100、250、500ml)玻璃生产车间设计分工明细廖勇:第一章前言第二章工艺设计与说明第三章物料衡算附图设计的总体布置、排版与致谢侯迪:第四章热量衡算彭正刚:第五章设备选型赵源:第六章车间布置设计李邦、杨炜龙:第七章质量控制标准王俊翔:第八章劳动保护与安全生产郭舜、赵辉:第九章“三废”处理及其综合利用年产2000万瓶玻璃大输液车间设计摘要:本设计内容主要包括玻璃瓶大输液的概述与设计依据,工艺流程选择与流程设计,全流程物料衡算,设备设计计算与选型,车间布置设计,劳动保护,工程经济和安全生产。
对玻璃瓶输液的各种生产工艺及生产设备进行了比较,介绍玻璃瓶输液生产车间平面布局方式,并提出了玻璃输液生产车间设计应注意的关键问题。
关键词:玻璃瓶大输液;生产工艺;生产设备;设计Design of a Glass Bottle Infusion Workshop withAnnual Production of 20,000 thousandAbstract: The design include an overview of glass bottle infusion and design basis, process selection and process design, the whole process material balance, equipment design calculations and selection, plant layout design, labor protection, engineering, economy and safety.Glass bottles for infusion of various processes and production equipment were compared, introducing glass bottle manufacturing plant layout infusion methods, and proposed the key issues about designing workshop glass infusion should pay attention to key issues.Key word:Glass bottle infusion; production process; production equipment; Design第一章前言1.1 简介大输液为大容量注射剂,是我国医药行业五大类重要制剂之一,在临床上应用广泛。
- 1、下载文档前请自行甄别文档内容的完整性,平台不提供额外的编辑、内容补充、找答案等附加服务。
- 2、"仅部分预览"的文档,不可在线预览部分如存在完整性等问题,可反馈申请退款(可完整预览的文档不适用该条件!)。
- 3、如文档侵犯您的权益,请联系客服反馈,我们会尽快为您处理(人工客服工作时间:9:00-18:30)。
大容量输液制剂的生产工艺大容量输液生产工艺流程以及环境要求大容量输液认证检查要点大输液又名可灭菌大容量注射剂,是指将配制好的药液灌入大于50 ml的输液瓶或袋,加塞、加盖、密封后用蒸汽热压灭菌而制备的灭菌注射剂。
1、机构与人员a)主管生产和质量管理的企业负责人、生产管理和质量管理部门负责人均应具有医药或相关专业大专以上学历,并具有药品生产和质量管理经验,并履行其职责。
b)企业负责人和各级管理人员应定期接受药品管理法律法规培训。
c)质量检验、生产、维修保养、清洁人员应定期进行卫生和微生物学基础知识、洁净作业等方面的培训和考核,并具有实际操作技能。
2、厂房设施的管理要点及检查重点a)洁净区:我国《药品生产质量管理规》对最终灭菌的无菌药品生产厂房洁净度级别的要:浓配或采用密闭系统的稀配应在100000级洁净区进行;稀配、滤过、灌封、直接接触药品的包装材料的最终处理等操作应在10000级洁净区进行;物料、中间品应经过物流缓冲间或传递柜进、出洁净区。
称量配料间如产尘应与洁净走廊呈相对负压,必要时设捕尘设施。
中国药典规定:微生物限度检查、无菌检查应在100级或10000级背景下的局部100级区进行,并与生产区分开。
微生物限度检查与无菌检查用的实验室和空气净化系统最好彼此分开,以尽可能减少对无菌检查的干扰。
b)空气净化系统应能确保洁净区的洁净度级别、温湿度、压差等符合生产工艺要求并经过验证。
初效、中效过滤器应明确清洗/更换周期,高效过滤器应定期检测其完整性,如有泄漏或阻塞应及时更换。
空气净化系统应每天24小时运行,停用后再次运行应进行清洁、消毒并经过再验证,符合要求的方可开始生产。
c)与产品直接接触的压缩空气、氮气、二氧化碳等辅助设施这些气体因与产品直接接触,不得对产品带来污染。
应对系统进行验证。
PQ测试项目包括洁净度级别、含水量、含油量等。
d)注射用水(WFI)系统以纯化水为原水,经多效蒸馏制得。
制水系统应能提供足够量的符合质量要求的注射用水。
注射用水制备和分配系统材质应无毒、耐腐蚀,设计和安装应避免死角和盲管;储罐应密闭,并安装有经完整性检查合格的无菌级别的疏水性过滤器,设有保温装置;管道通过卡箍连接,有一定的倾斜度,最低位出水,阀门用隔膜阀而不是球阀;注射用水的储存应采用80o C以上保温或65o C以上保温循环,应有温度控制和指示装置;设有必要的取样口包括注射用水储罐的入水口、总出水口和总回水口,并便于取样;储罐、增压泵、管道可以排空便于清洁、消毒或灭菌。
e)纯蒸汽系统纯蒸汽通常用于与产品接触物品的灭菌及产品的最终灭菌,质量应符合要求,纯蒸汽系统应经过验证并定期监测。
3、设备a)配制系统称量用秤的精度应符合物料的称量要求,并定期校验,贴有合格标志。
配制罐体积应与生产批量相匹配,材质应符合要求,禁用铁类容器或露铁搪瓷桶,配有搅拌、降温等装置,可定容。
配制罐宜自带称量系统或液位电极、或液位标尺,如采用玻璃液位管应能拆卸,以便清洗。
因配制需要在低于30℃、 CO2饱和的注射用水溶解原辅料,应有有效的控温装置,CO2输送管道终端应连有0.45 μm或精度更高的疏水性过滤器。
配有粗滤所需要的0.45μm 过滤器。
配有终端过滤所需要的2个0.22μm过滤器及过滤器完整性测试设备。
过滤器的安装应符合工艺要求,一个0.22μm的过滤器应可能接近灌封机(欧盟无菌药品附录要求),与产品直接接触的过滤器材质应不得吸附药液组分和释放异物(应有验证数据支持)。
反复使用的过滤芯应灭菌干燥后保存,并规定有灭菌有效期和使用次数。
配制系统宜采用密闭系统,并配有自动清洗、消毒或灭菌装置。
管道通过卡箍连接,使用结束应能排空。
b)大输液生产联动线理瓶机:将拆包取出的输液瓶按顺序排列起来,并逐个送至洗瓶机。
洗瓶机:应安装在100000级洁净区。
洗瓶能力应能满足工艺需要,洗净后瓶子的清洁度符合要求。
灌封系统:应安装在10000级洁净区,能有效控制装量,灌装过程中药液无溅壁现象,在药液灌装完成后,要立即封口,以免药液被污染或空气氧化,瓶子封口完好。
灌装头、灌装管道等灌装器具应按规定的程序清洁、消毒或灭菌。
控制与显示关键参数的仪表如:温度,传送速度应经过定期校验,并贴有合格校验标签。
c)灭菌设备用高压灭菌釜对产品进行湿热灭菌的方法包括冷空气重力置换法、预真空法、脉冲真空法、蒸汽-空气和蒸汽-水-空气灭菌法、过热水浸没灭菌法。
企业应根据产品特性选择合适的灭菌设备,能满足产品的最终灭菌和生产用器具的灭菌要求。
灭菌设备应具灭菌温度、时间自动监测、记录装置,其能力应与生产批量相适应。
仪表经过校验,并贴有校验合格标志。
直接与产品接触的器具和产品的灭菌应用纯蒸汽。
检漏用色水宜经过灭菌处理。
d)文件每台主要设备都应建立设备使用标准操作程序(SOP)、清洁、消毒或灭菌标准操作程序、维护保养标准操作程序、使用记录和设备档案。
4、物料的管理要点及检查重点a)物料的采购应由具有产品专业知识的人员负责,从企业质量审计合格的供应商处采购。
b)原辅料的检验、贮存及分发物料应保存于企业规定的适宜的环境中并有明确的标识,质控部门应按批取样、检验、签发。
取样应具有代表性,样品应按企业控标准进行检验。
原辅料应经质量部门签发后在有效期使用。
不合格的原辅料不得用于生产。
c)包装材料大容量输液灌装的瓶子或袋子经检验合格后方可投入使用。
药品标签和说明书应与药品监督管理部门批准的容、式样、文字相一致,经企业质量管理部门校对无误后印制、发放、使用。
标签发放、使用、销毁应有记录。
d)不合格品不合格物料、产品应专区存放,应有易于识别的明显标志,并按有关规定及时处理,并有记录。
对不合格产品应查明原因并采取必要的纠正措施。
e)退回产品、收回产品应按相关程序处理并作适当记录。
5、验证的管理要点及检查重点a)HVAC系统及洁净室的验证新车间应进行前验证,包括IQ、OQ和PQ,车间运行一定时间或停止运行后再次使用前应进行再验证。
验证测试项目应重点检查洁净度级别(尘埃粒子、微生物)、高效过滤器完整性(DOP)、压差、温、湿度(应能满足生产工艺要求)、局部100级区的气流流型、洁净室的清洁及消毒措施等。
b)压缩空气、氮气、二氧化碳等辅助系统的验证新系统应进行前验证,包括IQ、OQ和PQ,系统运行一定时间后应进行再验证。
气体储存及分配系统材质应无毒,并设终端过滤器。
验证测试项目应包括洁净度级别(尘埃粒子、微生物)、含水量、含油量等。
c)注射用水系统的验证新的注射用水系统应进行前验证,包括IQ、OQ和PQ。
注射用水储罐和分配系统选用材质应无毒、耐腐蚀,管道的设计和安装应避免了死角、盲管,储罐应安装有疏水性过滤器,储罐和管道应能排空,注射用水及分配系统的保温效果应能达到设计要求(80o C以上保温或65o C以上保温循环)。
注射用水质量应不低于中国药典(2005年版)注射用水质量标准,验证测试时间应不少于3周,并应监测季节变化对水质的影响。
企业应根据验证结果规定注射用水系统的清洗、灭菌周期。
企业应制定注射用水系统监测计划,包括对微生物、毒素、理化指标,并按计划对水质进行监测并有完整记录,鼓励企业做趋势分析、年度回顾。
d)大容量输液联动机组的验证新系统应进行前验证,包括IQ、OQ和PQ,系统运行一定时间后应进行再验证。
洗瓶机清洗安瓿后的洁净程度(清洗后往安瓿中加入注射用水,振摇后检查澄明度和不溶性颗粒)。
灌装机装量准确性、灌装后对瓶子或袋子密封的效果等。
e)湿热灭菌工艺的验证中国药典(2005年版)要求,对热稳定的产品,可采用过度杀灭法,其无菌保证水平(SAL)应≤10-12,热稳定较差产品的标准灭菌时间F0一般不低于8分钟,此情况下,应在生产全过程中,对产品中污染的微生物严加监控,并采取各种措施降低微生物污染水平,确保被灭菌产品达到无菌保证要求。
在注射液生产中,产品的最终灭菌和与产品直接接触的器具如过滤器的灭菌等采用湿热灭菌。
该产品最终灭菌的工艺参数为121°C 20分钟。
进行灭菌验证时,被灭菌物品的数量和装载方式、灭菌温度和时间或F0必须在验证方案中明确规定,至少进行3次空载热分布试验,每种装载方式都至少进行3次负载热穿透试验,并选用合适的生物指示剂。
空载热分布试验和负载热穿透试验至少用12个热电偶,应有热电偶分布示意图,热电偶在每次使用前后均应进行校正。
121°C蒸汽灭菌通常选用中嗜热脂肪芽孢杆菌作为生物指示剂。
验证过程中应考虑灭菌参数的上限和下限,保证灭菌效果和产品质量。
f)工艺验证工艺验证应在洁净室系统、压缩空气及氮气系统、工艺用水系统、热力灭菌系统、检测方法等验证合格且人员经相关培训考核合格后进行。
应连续3批产品验证合格。
验证的批量应与工艺规程规定的相同,关键工艺控制参数如配制工序中的pH值、温度、搅拌时间、瓶输送带速度、灌装工序中的装量、最终灭菌的温度及时间等是应在工艺规程规定的围之。
采集的用于检验的样品应足够,能反映整批产品的质量。
如检查安瓿是否清洗干净时,应在清洗安瓿的前、中、后期取样对安瓿的洁净度进行检查;检查装量时,应在灌装的前、中、后期采集了足够的样品并分别进行检验;成品应按灭菌柜次取样并分别作无菌试验等。
工艺验证应包括最差条件,如从配制到灌装或灭菌的时间间隔要求、灌装期间进入灌装间人员的数量、设备出现故障时进行必要的检修等。
灌装期间应对灌装间进行微生物监测,监测结果应作为产品放行审核的一部分。
变更控制和偏差管理应符合规定,对出现的偏差应进行了调查和记录等。
g)清洁验证不同产品共用生产设备,或产品不稳定生成了降解产物,或清洁过程引入了外来物质如清洁剂等,应进行清洁验证。
清洁验证是对某一具体的清洁程序进行验证。
重点检查清洁程序的可操作性、清洁过程中是否引入了外来物质、允许残留量计算的依据、化学残留量检测方法的灵敏度、是否考虑了所有共用设备、管道中的残留等。
清洁验证判断标准应包括目测、漂洗液取样检验和棉签擦拭取样检验。
棉签擦拭取样检验应做回收率试验作为取样、检测方法的依据。
清洁验证通常与工艺验证同时进行,并应包括最差条件如产品批量、生产完成后到清洁的时间间隔、清洁液用量等。
h)检验方法验证采用药典未收载的检验方法时,应进行检验方法验证。
检验方法验证容应包括准确度、精密度、专属性、检测限、定量限、线性、围、耐用性等。
微生物限度检查和无菌试验方法的验证过程和容应符合《中国药典》的指导原则。
i)验证文件验证文件应包括验证主计划、验证方案、SOP、验证报告。
验证计划应明确验证项目、验证顺序、组织机构职责等,验证方案应包括验证目的、围、职责、方法、接受标准、相关文件、变更控制及再验证等,SOP应具体,具有可操作性,验证报告应汇总验证全过程、结果、结论及建议等。