车间现场5S管理检查表
车间5S检查表
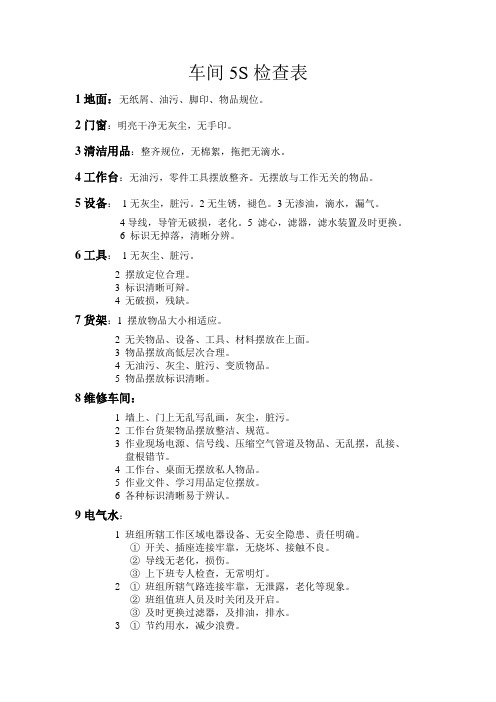
车间5S检查表1地面:无纸屑、油污、脚印、物品规位。
2门窗:明亮干净无灰尘,无手印。
3清洁用品:整齐规位,无棉絮,拖把无滴水。
4工作台:无油污,零件工具摆放整齐。
无摆放与工作无关的物品。
5设备:1无灰尘,脏污。
2无生锈,褪色。
3无渗油,滴水,漏气。
4导线,导管无破损,老化。
5 滤心,滤器,滤水装置及时更换。
6 标识无掉落,清晰分辨。
6工具:1无灰尘、脏污。
2 摆放定位合理。
3 标识清晰可辩。
4 无破损,残缺。
7货架:1 摆放物品大小相适应。
2 无关物品、设备、工具、材料摆放在上面。
3 物品摆放高低层次合理。
4 无油污、灰尘、脏污、变质物品。
5 物品摆放标识清晰。
8维修车间:1 墙上、门上无乱写乱画,灰尘,脏污。
2 工作台货架物品摆放整洁、规范。
3 作业现场电源、信号线、压缩空气管道及物品、无乱摆,乱接、盘根错节。
4 工作台、桌面无摆放私人物品。
5 作业文件、学习用品定位摆放。
6 各种标识清晰易于辨认。
9电气水:1 班组所辖工作区域电器设备、无安全隐患、责任明确。
①开关、插座连接牢靠,无烧坏、接触不良。
②导线无老化,损伤。
③上下班专人检查,无常明灯。
2①班组所辖气路连接牢靠,无泄露,老化等现象。
②班组值班人员及时关闭及开启。
③及时更换过滤器,及排油,排水。
3①节约用水,减少浪费。
②经常检查管道及水龙头,无渗漏,断裂等现象。
10穿戴:1 衣物无异味,经常换洗,整洁干净。
2头发干净,梳理舒畅。
3身体保持干净,无异味。
4女士不可涂脂抹粉,不可穿高跟鞋。
5男士上班不可穿短裤及拖鞋。
11交流用语规范:1 提倡文明用语,不可有粗俗和脏话,甚至骂人的言语出现。
2 同事之间交流应客气礼貌。
3 同事之间交流和讨论问题应该轻言细语,不可大声喧哗,而影响其他同事工作。
4 不可在工作场所唱歌,打闹,相互谩骂。
5 不可在工作场所打架。
12坐立姿势:1 坐立的姿势应该端正,协调并养成习惯。
2 不可在上班时间翘儿郎腿,或把脚放在办公台上。
生产车间5S检查表

素养
合计 说明
员工是否完全明白5S的含义
5
下班或员工较长时间离开工作岗位是否及时关闭电灯、设备电源开关门窗等
5
是否严格执行安全操作规程,工艺操作规程,出现异常及时上报
5
工作期间是否有闲谈、喧哗、串岗、打瞌睡、玩手机等,是否严格遵守工作纪律 遵守作息时间,无迟到、早退等不良上下班现象,按时就餐无浪费现象出现
5 5
小计
25
100
1.80分以上为合格,不足之处组长组织组员讨论并改善。2.不合格班组下次检查时作重点检查对象,累计三次不合格分将作相应处罚。
检查人:
日期:
5
各种生产用工序卡片、点检纪录等是否齐全并悬挂于醒目位置
5
各工序半成品、不合格品是否有效标识区分,前后工序间是否流畅
5
是否正确使用工具及设备,对已损坏的工具及设备是否及时清理出现场
5
小计
25
工作区域是否整洁,是否有尘垢,是否清洁无污渍,粉尘,不常用的是否遮盖, 防护
5
小计
10
员工按规定进入车间是否更换胶鞋,穿好工作服,佩带工作卡
5
相关工序人员是否戴防静电手套、鞋套,离开岗位时是否将这些辅助用品放置好以 备后用。
5
是否及时正确填写流程卡,开教验单,及设备点检、老化等记录,不得弄虚作假 5
整个班组日生产规划是否合理、顺畅,现场整洁、亮丽
5
小计
20
得分
较严重不符合项及责任人
班组: 项目 整理
整顿
清扫
清洁
检查内容及要求
配分
工作区域是否有与工作无关的东西
5
物料工具等摆放是否整齐有序,是否放置在指定位置
5
车间仓库厂区5S检查表

检查时间: 检查人:
项目
查检达标内容
不合格描述
整 理
1、现场是否有废料、无用杂物和设备工具等。
2、设备、工件材料上是否停放有生活用品等。
3、工作台、工具箱内是否有无用的物品资料。
4、现场有无失效或与生产无关的文件资料。
整 顿
1、是否分作业区、合格待转区、不合格品区并按区摆放。
2、现场原材料是否分类、摆放整齐。
其他
说明:1、行政部负责对问题进行汇总,并把发觉问题下发到相应部门进行整改。
2、整改期限内未整改,需说明缘由。
3、检查发觉有违规行为的,检查人员有权责令订正。
4、检查整改结果作为考核的依据。
4、张贴的资料、标语是否掉色、脱落。
清 洁
1、现场是否乱扔工件、纸屑、杂物。
2、工作台、工具箱是否保持洁净、用完的物品是否归位。
素 养
1、是否着装整齐、不戴工作证的现象。
(无统一配发的不考核工作证、厂服)
2、是否有旷工、脱岗窜岗睡岗、谈天或干与工作无关之事。
3、是否有铺张电、气现象。
4、墙上、工件上有否乱涂乱画乱张贴。
安 全
1、责任区内是否有生火吸烟及扔烟头。
2、是否有违反操作规程操作设备、或其他担忧全行为。
3、物料、工件叠放是否超过标准、倾斜、直接放地上。
4、物料、工件是否进行质量平安防护。
5、是否在物料、工件上躺坐、脚踩或放置尖硬物品。
6、是否按规定使用劳保用品。
7、消防道、走道有否堵塞现象,消防器材是否齐全有效。
3、记录是否正确、齐全、完好。
4、工量器具是否保管好且标记是否清楚精确 。
5、标识是否醒目、正确、齐全。
6、当天不需用的工具和文件资料是否归位保存。
生产车间5S检查表
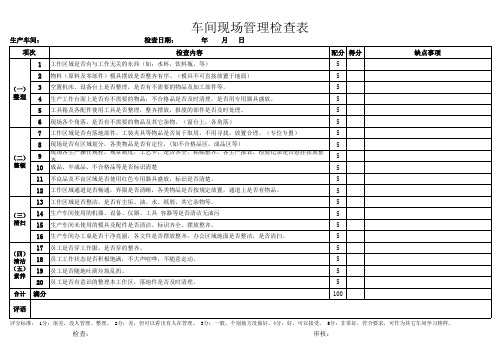
5
(四)
清洁 18 员工工作状态是否积极饱满,不大声喧哗,不随意走动。
5
(五) 19 员工是否随地吐痰垃圾乱扔。
5
素养
20 员工是否有意识的整理本工作区,落地件是否及时清理。
5
合计 满分
100
缺点事项
评语
评分标准: 1分:很差,没人管理、整理。 2分:差,但可以看出有人在管理。 3分:一般,个别地方没做好。4分:好,可以接受。 5分:非常好,符合要求,可作为其它车间学习榜样。
车间现场管理检查表
生产车间:
检查日期:
年 月日
项次
检查内容
配分 得分
1 工作区域是否有与工作无关的东西(如:水杯,饮料瓶,等)
5
2 物料(原料及零部件)模具摆放是否整齐有序。(模具不可直接放置于地面)
5
(一) 3 空置机床、设备台上是否整理,是否有不需要的物品及加工部件等。
5
整理 4 生产工作台面上是否有不需要的物品,不合格品是否及时清理,是否用专用器具盛放。
5
5 工具箱及各配件使用工具是否整理,整齐摆放,报废的部件是否及时处理。
5
6 现场各个角落,是否有不需要的物品及其它杂物。(窗台上,各角落)
5
7 工作区域是否有落地部件。工装夹具等物品是否易于取用,不用寻找,放置合理。(专位专置)
5
8 现场是否有区域划分,各类物品是否有定位,(如不合格品区,成品区等)
检查:
审核:
5Hale Waihona Puke 13 工作区域是否整洁,是否有尘垢、油、水、纸屑、其它杂物等。
5
(三) 14 生产车间使用的机器、设备、仪器、工具 容器等是否清洁无油污
5
车间现场5S管理检查表

检查表
存在问题
以下,除书面改善报告外,还将全厂通报批评。
分 很差:1分 ,限期整改。限期没有整改的罚款200元
生产车间现场5S管理检查表
检查项目 检查内容
工作区域是否有与工作无关的东西 物料、工具、器具等摆放是否整齐有序
分数 得分 5 5 5 5 20 5 5 5 5 5 25 5 5 5 5
整理
区分要用和不要用的,不要用的清除掉 工作工作区域是否有落地部件。落地部件是否有固定位置盛放 工作区域通道是否畅通,界线是否清晰 要用的东西依规定定位,定量地摆放整齐,明确地标示 成品、半成品、、不合格品等是否标识清楚 标识场所物品
目的:清除赃污保持现场内干干净净明明亮亮 20
5 5 清洁 5 目的:通过制度化来维持成果,并显示异常之所在15 员工是否完全明白5S的含义 5 制定共同遵守的有关规则规定 5 人人依规定行事,养成好习惯 5 素养 推动各种精神提升活动,早会 5 20 目的:改变人质养成工作规范认真的习惯
合计
100
整顿
目的:整齐,有标识,不用浪费时间找东西
工作区域是否整洁,是否有尘垢,建立清扫责人区 生产线使用的机器、仪器等是否清洁无油污
清扫
生产线使用的容器是否清洁、标识、摆放整齐 设备点检卡、工艺流水卡、标识牌是否按规定填写 将前3S实施的做法制度化,规范化,并贯切执行及维持成果 整个车间规划是否合理、顺畅、整洁 车间领导是否经常带头巡查,带头重视
注:80分以上为合格,不足之处自行改善;60-80分须向检查小组作书面改善报告;60分以下,除书面改善报告外,还
1. 评分标准: 非常好:5分 好:4分 一般:3分 差:2分 很差:1分 2. 如果被评为2分,贴黄牌警告,需进行整改;如果被评为1分,贴红牌警告,限期整改。限期没有整改 。
车间5S现场管理考核检查表

清洁
16
随时注意保持整理、整顿、清扫
5
17
设施完好可用,非正常状态有明显标识,
无灯不亮
3
18
消防器材、通道口、配电箱前畅通
3
19
物料箱堆码规范,无歪倒跌落
3
素养
20
坚持利用周会、月会等进行5S培训
5
21
注重安全,无违纪违章,遵守规定流程
3
22
着装得体,注意礼仪,不睡觉,不打闹,不串岗,不影响他人
5
5
7
图纸工艺文件、随货单、记录规范到位
3
8
工具柜、资料柜内分类明确,便于查找
3
9
清洁用具、消防辅助用品定置,整齐
3
10
现场无可见私人物品,水杯统一定位
3
清扫
11
设备设施、器具清洁无积垢积尘见本色
6
12
地面、墙面干净,无积油积水
5
13
门、窗户及玻璃清洁明亮,窗台无杂物
5
14
下班进行工位清洁整理
3
15
每周一次大扫除
车间5S现场管理考核检查表
考核单位:考核人:考核时间:年月日
项目
项次
检查内容
分值
扣分
扣分事项简述
整理
1
生产现场无不用或长期无用的物品
6
2
切屑、废料当班清理
5
3
工位、工具桌无废料、废资料、废纸
3
整顿
4
通道畅通,物料分区定位,无压线出线
6
5
物料、工具、转运板车放置整齐合理,生产物料不裸放地面
6
6
标识统一、美观、规范、明确,不合格品隔离存放并有明确标识
车间5s管理制度及检查表

车间现场的5S管理的管理制度一、管理目的为了加强车间现场管理,保证生产安全、提高生产效率和质量,制定本制度。
通过5S管理的实施,改善车间环境,提高设备利用率,减少浪费,降低生产成本,提高员工的工作积极性和主动性。
二、管理内容1. 整理(Seiri)(1)锯床、钻床和冲床等设备的布置应合理,按照工艺流程进行布置,确保设备之间有足够的操作空间和通道。
(2)清理车间各个角落,清除不必要的工具、废料、杂物等,防止产生安全隐患或影响生产。
2. 整顿(Seiton)(1)对车间内的设备、工具、零部件进行分类整理,制定并贴标识,确保一目了然,方便取放。
(2)设备维护保养保持整洁,确保设备状态良好。
3. 清扫(Seiso)(1)要求每位员工都有责任保持自己的工位、设备和周围环境的整洁,保持车间地面、墙面、设备的清洁干净。
(2)加强设备定期清洗保养,预防设备故障。
4. 清洁(Seiketsu)(1)营造良好的工作环境,建立每日、每周、每月的定期清洁制度,对车间进行定期清洁,保持整体卫生。
(2)设备更换润滑油、刀具等保养工作要规范执行,确保设备处于最佳状态。
5. 教育、培训、自律、习惯(Shitsuke)(1)培训员工参与5S管理的重要性,鼓励员工主动参与车间管理,增强员工的责任感。
(2)建立5S管理的考核制度,对车间5S管理进行定期检查和评估,激励员工积极参与5S管理。
三、执行机构车间主任负责制定具体的5S管理计划和组织实施。
班组长、操作工等负责具体的5S管理工作,每天下班前进行巡视、整理、清扫等。
四、督查检查生产部门负责对车间5S管理定期进行检查和评价,制定整改措施和奖惩办法,确保5S管理制度的执行。
五、奖惩措施对5S管理工作突出的个人和班组给予奖励;对违反5S管理规定的行为,给予相应的批评教育和处罚。
以上是关于机械加工企业车间现场的5S管理管理制度,希望通过5S 管理的实施,能够提高车间的整体管理水平,保障生产安全,提高生产效率和产品质量。
车间每日5s检查表

清扫
工具、设备无污秽 剩料、废料及时清理 手套、口罩无随处摆放现象 工作区域保持整洁无杂物 设备有维修保养
清洁
现场各种记录表格及时填写 文件清洁,无涂改、损坏现象 看板保持干净,内容时常更新 员工具有良好的5s观念 无违纪、违规,违反操作规程现象
素养
具有良好的工作习惯 工作服穿戴整齐,正确佩戴员工卡 正确穿戴劳防用品
车间每日5s检查表
5S项目
车间内无杂物
管理标准
人行道、安全垃圾及时处理 工作不常用的器物及时整理 工作区域内无茶杯、衣物等私人物品 车间内物品按规定摆放整齐 工具摆放合理,便于寻找、取放
整顿
工具、物品、文件有定位 标示清晰明确 车间文件有分类并整齐的摆放在规定位置 工作区域卫生时常打扫 车间地面、墙壁、门等卫生保持干净
- 1、下载文档前请自行甄别文档内容的完整性,平台不提供额外的编辑、内容补充、找答案等附加服务。
- 2、"仅部分预览"的文档,不可在线预览部分如存在完整性等问题,可反馈申请退款(可完整预览的文档不适用该条件!)。
- 3、如文档侵犯您的权益,请联系客服反馈,我们会尽快为您处理(人工客服工作时间:9:00-18:30)。
注:80分以上为合格,不足之处自行改善;60-80分须向检查小组作书面改善报告;60分以下,除书面改善报告外,还
1. 评分标准: 非常好:5分 好:4分 一般:3分 差:2分 很差:1分 2. 如果被评为2分,贴黄牌警告,需进行整改;如果被评为1分,贴红牌警告,限期整改。限期没有整改 。
检查表由5S管理小组进行评定
生产车间现场5S管理检查表
检查项目 检查内容
工作区域是否有与工作无关的东西 物料、工具、器具等摆放是否整齐有序
分数 得分 5 5 5 5 20 5 5 5 5 5 25 5 5 5 5
整理
区分要用和不要用的,不要用的清除掉 工作岗位是否有不良品没有及时更换
目的:把空间腾出来活用
工作区域是否有落地部件。落地部件是否有固定位置盛放 工作区域通道是否畅通,界线是否清晰 要用的东西依规定定位,定量地摆放整齐,明确地标示 成品、半成品、、不合格品等是否标识清楚 标识场所物品
检查表
存在问题
以下,除书面改善报告外,还将全厂通报批评。
分 很差:1分 ,限期整改。限期没有整改的罚款200元
整顿
目的:整齐,有标识,不用浪费时间找东西
工作区域等是否清洁无油污
清扫
生产线使用的容器是否清洁、标识、摆放整齐 设备点检卡、工艺流水卡、标识牌是否按规定填写 将前3S实施的做法制度化,规范化,并贯切执行及维持成果 整个车间规划是否合理、顺畅、整洁 车间领导是否经常带头巡查,带头重视
目的:清除赃污保持现场内干干净净明明亮亮 20
5 5 清洁 5 目的:通过制度化来维持成果,并显示异常之所在15 员工是否完全明白5S的含义 5 制定共同遵守的有关规则规定 5 人人依规定行事,养成好习惯 5 素养 推动各种精神提升活动,早会 5 20 目的:改变人质养成工作规范认真的习惯
合计
100