第六章 模具排气系统
塑胶模具排气系统设计Venting System Design

排氣系統設計Venting System Design徐昌煜Charles Hsu2003. 8. 25.排氣系統的合理化蔡毓斌•注射的過程中,模穴(型腔)的空氣必須順利排出,塑料才能順利充填。
•排氣不良時,產品(制件)表面會有困氣造成的氣泡、甚至是焦痕。
•澆注系統的設計不當時,排氣易生問題。
•產品(制件)造型設計不當時,排氣問題難解。
排氣設計檢查點蔡毓斌•檢查模穴(型腔)充填末端是否能夠順利排氣(可以CAE模擬預測最後充填位置)•可利用澆口位置或/和尺寸的變更,調整最後充填位置。
排氣位置•在充填末端要加排氣(充填末端可用CAE模擬預測)•排氣位置可藉產品(制件)設計和澆口/流道設計而改變滑雪靴扣件設計焦痕組立圖3D 充填模式Y-Z 剖面造型對排氣的影響原始設計修正設計材料:透明PC3D 充填模式利用澆口尺寸控制排氣位置3D Model分析軟體:Moldflow MPI 4.0LCD TV喇叭飾板的設計排氣Vent為何排氣仍然還是一個問題?Why venting is still a problem ?因為降低射速,讓積風(氣穴)有較多的時間逃氣,是一件太容易的事。
但是…Because it is too easy to slow down the injection speed and give the trapped air more time to escape. But ...排氣Vent射速一降,熔膠溫度很快降低,射壓必須提高,殘餘應力隨之提高,翹曲的可能性增加。
如果想藉提高料溫,以降低射壓,料溫必須升得很高,這樣又會引起塑料劣解(降解)。
When injection speed is lower, melt temperature goes down very fast, injection pressure has to be increased, residual stress is increased and the possibility getting warppage becomes higher. If one would like to increase barrel temperature to reduce the required injection pressure, the barrel temperature has to be increased to a quite high level and polymer degradation would be induced.排氣Vent高料溫和高射壓都說明充填系統有了流動的問題Both high barrel temperature and high injection pressure are indications of flow problem in the filling system.排氣Vent我們常發現: 射速提高時,塑料表現得更為出色。
浇注系统与排气系统设计
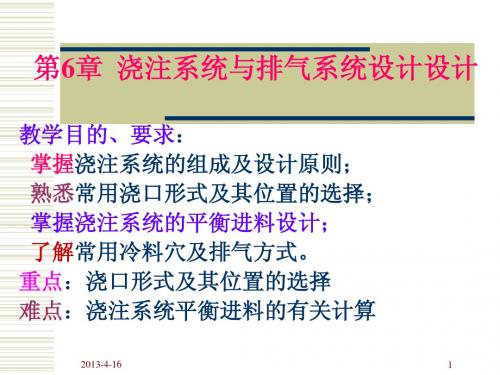
二、浇口种类及其应用
1.直接浇口(中心浇口) 直接浇口(中心浇口) 直接浇口 压力损失小, ①优缺点 压力损失小,充模容易 固化慢,成型时间长, 固化慢,成型时间长,易使制品变形 浇口去除较难, 浇口去除较难,残痕大
2011-3-18
27
②应用
适合于成型大而深的制品(开冷料井, 适合于成型大而深的制品(开冷料井,以补缩及 添冷料) 添冷料) ③尺寸:依塑料品种和制品大小查表(仿主流道) 尺寸:依塑料品种和制品大小查表(仿主流道) 见下表) (见下表)
2011-3-18
33
5 .点浇口(针状浇口) 点浇口( 点浇口 针状浇口)
①优缺点 ·降低塑料的表观粘度,提高料温,便于充模 降低塑料的表观粘度 降低塑料的表观粘度,提高料温, ·浇口位置灵活,浇口附近变形小 浇口位置灵活 浇口位置灵活,浇口附近变形小 ·截面尺寸小,开模时可自动拉断,浇口残痕小, 截面尺寸小 自动拉断, 残痕小, 截面尺寸小,开模时可自动拉断 浇口残痕小 易实现生产自动化 缺点: 缺点: 需要大注射压力 浇口冻结固化 大注射压力, 冻结固化快 需要大注射压力,浇口冻结固化快,不利于补缩 模具费用高——三板式双分型面或二板式热流道 三板式双分型面或 模具费用高 三板式双分型面
2011-3-18 34
②适用
阻力小、 利于补料) (图c阻力小、含玻纤塑料;图d利于补料) 阻力小 含玻纤塑料; 利于补料
适合于注射成型流动性好的热塑性塑料, 适合于注射成型流动性好的热塑性塑料,广泛应 用于单腔、多腔或多浇口的注射模中。 用于单腔、多腔或多浇口的注射模中。 ③尺寸设计 d=0.206 n4 t 2 A t—制品壁厚; 制品壁厚; 制品壁厚 A—制品外表面积 制品外表面积 常取 :
注塑模排气系统设计

4.排气槽了模具制造和清模的方便,排气槽应尽 量设在凹模的一面;
6.排气槽排气方向不应朝向操作面,防止注 射时漏料烫伤人;
7.排气槽(孔)不应有死角,防止积存冷料;
排气槽的宽度可取1.5~6mm,深度以塑料熔 体不溢出排气槽为宜,其数值与熔体粘度有关,一 般可在0.02~0.05mm范围内选择。根据一般经验, 常用塑料的排气槽厚度的取值如表3-1所示:
4.塑料中某些配合剂挥发或化学反应所生成 的气体(在热固件塑料成形时,常常存在由于化学反 应生成的气体)。
在排气不良的模具中,上述这些气体经受很大 的压缩作用而产生反压力,这种反压力阻止熔融塑 料的正常快速充模,而且,气体压缩所产生的热也 能使塑料烧焦。在充模速度大、温度高、物料粘度 低、注射压力大和塑件过厚的情况下,气体在一定 的压缩程度下能渗入塑料内部,造成熔接不牢、表 面轮廓不清、充填不满、气孔和组织疏松等缺陷。
注塑模排气系统设计
排气结构的作用
注射模的排气是模具设计中不可忽视的一个问 题,特别是快速注射成形工艺的发展对注射模排气 的要求就愈严格。
注射模内积集的气体有以下四个来源:
1.进料系统和型腔中存有的空气;
2.塑料含有的水分在注射温度下蒸发而成的 水蒸气;
3.由于注射温度过高,塑料分解所产生的气 体;
设计要点
排气槽(或孔)位置和大小的选定,主要依靠经 验。通常将排气槽(或孔)先开设在比较明显的部位, 经过试模后再修改或增加,但基本的设计要点可归 纳如下:
1.排气要保证迅速、完全,排气速度要与充 模速度相适应;
2.排气槽(孔)尽量设在塑件较厚的成形部位;
3.排气槽应尽量设在分型面上,但排气槽溢 料产生的毛边应不妨碍塑件脱模;
模具排气镶件的排气原理

模具排气镶件的排气原理模具排气镶件是一种用于模具中的排气装置,它的设计原理是通过合理的结构和材料选择,使得模具在工作过程中能够有效地排出气体,确保模具的正常运行和产品的质量。
排气是模具注塑过程中非常重要的一个环节,它直接影响到产品的质量和生产效率。
在注塑过程中,由于塑料熔化后会产生气体,如果没有良好的排气装置,这些气体就会被困在模具中,造成气泡、缺陷等问题,甚至会导致模具损坏。
因此,模具排气镶件的作用就是通过设计合理的结构,将这些气体顺利排出,保证模具和产品的质量。
模具排气镶件的排气原理主要包括以下几点:1. 气体的产生:在注塑过程中,由于塑料在加热和熔化的过程中会释放气体,这些气体主要来自于塑料的分解、挥发和反应等过程。
同时,还可能会产生一些溶解在塑料中的气体,如水分、空气等。
2. 气体的运动:在注塑过程中,由于塑料的流动和压缩,气体会被挤压和推动,沿着塑料流动的方向逐渐向模具的出口移动。
同时,由于注塑速度和压力的变化,气体也会产生剧烈的运动和振荡。
3. 排气通道的设计:模具排气镶件通常包括排气孔、排气槽和排气道等部分。
排气孔是指通过模具的壁面或部件上开设的小孔,用于气体的排出。
排气槽是指模具中的一个凹槽,用于收集和导向气体。
排气道是指将排气孔和排气槽连接起来的通道,它可以是直线的,也可以是弯曲的,甚至可以是螺旋状的。
4. 排气效果的评估:模具排气镶件的设计需要考虑气体的排出速度和排气压力等因素。
一方面,如果排气速度过快,会导致塑料流动受阻和产生缺陷;另一方面,如果排气速度过慢,会导致气体无法及时排出,造成气泡和缺陷。
因此,需要通过实验和模拟计算等方法,评估排气效果,确定最佳的排气设计。
模具排气镶件的排气原理是通过合理的结构和通道设计,将注塑过程中产生的气体顺利排出,确保模具和产品的质量。
在实际应用中,我们需要根据具体的注塑工艺和产品要求,选择合适的材料和设计参数,确保排气效果达到最佳状态。
只有这样,才能保证模具的寿命和产品的质量,提高生产效率和经济效益。
模具排气系统设计

12
13
(2) 设排气槽
❖ 因为合模间隙很小,在强大的合模力作用下, 模板产生一定的变形,合模间隙更小。所以, 对于型腔容积较大的模具,仅仅利用合模间隙 排气,排气速率一般达不到要求。这时需要专 门开设排气槽。
❖ 当充模料流末端不在分 型面上,又没有配合间 隙可用时,一般难以开 设排气槽。
❖ 此时可在与料流末端接 触的成型零件上镶嵌可 透气的烧结金属块,并 用排气孔与外界或真空 系统连通,构成排气系 统。
19
小
结
排气系统设计主要考虑: ❖ 位置:一般设在料流的末端。 ❖ 尺寸:排气而不漏料。 ❖ 实施方式:
❖ 为有效排除模腔内的气体,排气系统的入口位置 (即排气系统在型腔内的开口)必须设在充模料 流的汇集处(料流末端)。
❖ 排气系统的出口位置可根据模具结构灵活安排, 但应注意采用排气槽等大截面排气系统时出口不 要正对操作者,以避免因工艺波动导致高温高压 熔体喷出时,可能造成的工伤事故。
8
2.排气系统尺寸
(1)利用分型面间隙排气。 (2)设排气槽。 (3)利用成型零件配合间隙排气。 (4)专设排气系统。
20
度w,根据缝隙深度h及在充模时间内排出模
腔内气体所需的排气通道截面积A确定
(w≥A/h)。
9
❖ 排气通道截面积A产下式计算 : A=0.05V/n
式中:A——排气通道截面积,mm2; V——型腔及浇注系统总容积,cm3; n——排气槽的数量
[说明:溢边值即物料能流入的最小缝隙,成型用 物料的溢边值取决于由物料特性和工艺条件决定 的物料流动性,流动性越好,溢边值越小。常用 塑料、常规成型条件下的溢边值如下表所示。]
注塑模具的排气设置原理

注塑模具的排气设置原理注塑模具的排气设置原理是为了在注塑过程中有效地排除模腔内的气体,从而减少或避免产品出现气泡、气孔等缺陷。
合理的排气设置可以有效地改善产品质量,提高注塑成型的成功率。
下面将详细介绍注塑模具的排气设置原理。
首先,需要了解一些基本概念和原理。
在注塑过程中,塑料材料被加热熔化后通过注塑机的喷嘴进入模腔,填充整个模腔后形成产品。
在填充过程中,气体可能会受到压缩或被挤入产品中,从而导致产品中出现气泡、气孔等缺陷。
模具的排气设置原理主要包括以下几个方面:1. 模具排气孔的设置:模具通常会在样品、模腔以及顶出部分周围设置排气孔。
排气孔的设计和设置位置应该根据具体的注塑产品来确定,根据产品的形状、尺寸以及复杂程度等因素进行合理布置。
排气孔可以是细长的气体通道,它们可以连接到模腔的高气压区域,将气体引导到模腔外部,以实现排气效果。
2. 模具开模面的排气设计:模具的开模面也可以设计为排气通道。
在模具设计时,可以在开模面上设置槽状通道,用来引导和收集气体。
这样可以使气体通过模腔壁面尽快排出,并避免气体在产品内部凝结形成气泡。
3. 模具材料和表面处理:合适的模具材料和表面处理也可以改善模具的排气效果。
例如,选用表面光滑的材料可以减少气体附着在模具壁面上的可能性,减少气泡形成的机会。
4. 模具的设计和加工精度:模具的设计和加工精度对于排气效果也起到重要作用。
模腔和排气通道的加工精度应尽可能高,确保通道的表面光滑,无毛刺、凹凸等缺陷,以提高气体排除的效果。
总之,注塑模具的排气设置原理是通过合理的设计和布置排气通道,在注塑过程中迅速排出模腔内的气体,以减少产品中的气泡、气孔等缺陷。
合理的排气设置可以改善产品质量,提高注塑成型的成功率。
因此,在注塑模具设计和加工过程中,要充分考虑排气的原理,从而确保产品质量的同时提高生产效率。
模具排气系统的设计

早 面 型上 L 茫习 言分薯 茫马I一 』 面的 _ , ] , l _ L 口 j — 早
型面上 开设 专 门的排气槽 或导气 沟 。而它 的位 置通
图 1 分 型 面 捧 气 槽 枧 撼 I A { 翻I ) 2 0 冷 02年 第4 襄
这 种反 压力增加 了熔 融料 体充 模流 动的 阻力 ,阻止 致 塑料棱 边不清 。 ( )制 品上呈现 明 显 可见 的 流动 痕 和 熔 合 缝 , 2 制 件力学性 能 下降 。
大型 制件 的排气 ,因排气 量大 ,排气 位 置总是 熔 融塑料 正常快 速充模 ,使模具 型腔 不 能充满 ,导 在料 流 的末 端 而料 流 的末 端在 分型 面 时 ,可在分
( )提高 生产 效率 。 5 4 模具 排气 系统 的设计 要 点 .
()排 气 系 统 的设 计 ,要 保 证 迅 速 、完 全 排 1 气 排气 速度 与充模 速 度相适 应 。 ( )排气 系统 中孔 、槽 的设计 ,使 溢料 产生 的 2 毛边 应不妨 碍制 件 的脱 模 。 ( )排 气 系 统 中槽 的 设 计 ,应 便 于 制 造 、清 3
具 型腔 的表面 。
水 ,使 水 道 内 的 冷 却 水压 低 于 大 气 压 产 生 文 丘 里 现 象 ,将 气 体 排入冷 却水 道 。
一 茜
0 ◎
圆 匹
图 2 利用 分 型 面 排气 图例
( ) 在 熔 合 缝 位 7
{ (
置 开 设 冷 料 井 ,在 贮 留冷 料 前 也 滞 留 了 少
( )气 体压 缩后 ,会 渗 入到 塑料 内层 ,使塑 料 排 气 槽 称 为 水 平 3 产生 银 纹 、气 孔 、组 织 疏 松 、剥 层 等 表 面 质 量 缺 排 气 槽 , 它 有 两
电动机壳压铸成型模具设计中的模具排气系统优化

电动机壳压铸成型模具设计中的模具排气系统优化在电动机壳压铸成型模具设计中,模具排气系统的优化是至关重要的。
一个良好设计的模具排气系统能够有效地排除模具中的气体和气泡,保证铸件成品质量。
本文将重点探讨电动机壳压铸成型模具设计中的模具排气系统优化。
一、模具排气系统的作用模具排气系统是用来排除模具中气体和气泡的系统。
在电动机壳压铸成型过程中,熔化的金属液体会释放出大量的气体,如果这些气体不能及时排出模具,就会在铸件中形成气孔和气泡,严重影响铸件的质量。
因此,一个有效的模具排气系统对于确保铸件成品质量至关重要。
二、模具排气系统的设计原则1. 合理布局:模具排气系统的位置应当考虑到熔化金属液体流动的方向,尽可能置于熔池的高点,保证气体能够顺利排出模具。
2. 设计通道:模具排气通道应当尽可能短、宽,保证通畅。
同时,排气通道的截面积也要适当,不宜过小,以免造成排气不畅。
3. 避免死角:排气系统设计要避免死角,尽量减少气体困留的可能,确保气体能够顺利排出模具。
4. 多点排气:在模具设计中,应当考虑设置多个排气口,以增加排气效率,避免因为某个排气口被堵塞而导致排气不畅的问题。
三、模具排气系统的优化方案1. 采用液压顶出装置:在模具设计中,可以考虑在合适的位置装配液压顶出装置,通过液压力将气体推出模具,提高排气效率。
2. 添加排气针:在模具设计中,可以考虑在模具的关键位置设计排气针,利用针状结构的小孔将气体排出模具,从而加快排气速度。
3. 优化排气道设计:对于排气道的设计,可以通过优化通道的宽度、长度以及截面积等参数来提高排气效率,确保气体顺利排出。
四、总结在电动机壳压铸成型模具设计中,模具排气系统的优化是确保铸件质量的重要一环。
通过合理设计模具排气系统,能够有效避免气孔和气泡的生成,提高铸件的完整性和质量。
因此,在模具设计中,应当重视模具排气系统的设计,不断优化完善,以确保模具的稳定工作和生产出优质的铸件产品。
- 1、下载文档前请自行甄别文档内容的完整性,平台不提供额外的编辑、内容补充、找答案等附加服务。
- 2、"仅部分预览"的文档,不可在线预览部分如存在完整性等问题,可反馈申请退款(可完整预览的文档不适用该条件!)。
- 3、如文档侵犯您的权益,请联系客服反馈,我们会尽快为您处理(人工客服工作时间:9:00-18:30)。
★ 分型面排气
浇 口
气体
排气槽
浇口
图6-3
分型面上直通式排气槽的结构形式
★ 模具流道的排气道。
排气道
排气道
图6-4
流道的排气结构
(2)抽真空排气
这种方式要求模具的分型面吻合要好,通过气孔将模腔内 气体抽净。但需配备抽真空装置,增加模具成本,一般情况 下不用。
(3)利用间隙排气
1)镶拼零件的配合面间隙,如型腔、型芯镶块。 2)侧向抽芯零件间隙。 3)顶出零件配合间隙(推杆、块)。 4)分型面间隙(粗糙度一般)。 利用间隙排气时,使用时间长了,间隙可能堵塞,应 定期清理,保持通畅。
精密模具设计
Precision Mould Design
大 连 理 工 大 学 机 械 工 程 学 院 模 具 研 究 所
Institute of Die & Mould of School of Mechanical Engineering Dalian University of Technology
第六章
思考题
想一想
1 模具中的气体有哪些? 2 模具为什么需要排气?排气不畅会产生 什么后果?常用的排气方式有哪几种? 排气间隙大小如何确定? 3 掌握常用塑料材料的溢边值。
Thank you !
(1)开设排气槽排气
排气槽通常开设在型腔一侧,围绕型腔开设或在熔体 最后充满部位。
排气道环绕 型腔一周, 在四个角处 排出模外。 A 型腔
浇口
C
B
图6-2
镶块分型面上的环形排气道
★ 排气通道的尺寸
排气道 A 深:0.01~0.02mm(小于塑料溢边值) 宽:3~5mm 长:一般3~5mm 排气槽 B 深:一般0.5~0.8mm 宽:3~5mm或更大 长:据需要而定 排气道 C 深:可取1mm 宽:可大于5mm 长:连通至模板边界
★ 多孔金属排气的应用
多孔金属块
1—型腔;2 —多孔金属块;3 —型芯; 4—动模板;D—排气孔
图6-12
利用多孔金属排气
(5)混合排气
通常是开设排气通道和间隙排气混用。
6.3 塑料的溢边值与排气间隙
排气通道应保证气体顺利逸出,塑料熔体不能流出。 塑料材料的溢边值可分为如下三种: ◆ 低粘度材料不产生溢料的间隙为:0.01~0.03mm ◆ 中等粘度材料不产生溢料的间隙为:0.03~0.05mm ◆ 高粘度材料不产生溢料的间隙为:0.05~0.08mm 常用材料的模具排气间隙如下: 材料 排气间隙 PE 0.015mm PA 0.01mm PP 0.015mm PS 0.015mm PC 0.01~0.025mm POM 0.01~0.025mm PET 0.01~0.03mm ABS 0.025mm
第 六 章 模具排气系统设计
6.1 模具排气设计的意义 6.2 排气系统的方式 6.3 塑料溢边值与排气间隙
§ 6.1 模具排气设计的意义
1 模具内的气体来源
型腔和浇注系统中存在空气; 塑料原料中含有水分,在注射温度下蒸发 产生的气体; 塑料分解产生的气体; 塑料中某些添加剂挥发或化学反应生成的 气体; 脱模剂挥发产生的气体。
§6.2
排气系统设计
1 排气槽设计要点
排气槽应尽量设在分型面的凹模一边,以便于 模具制造与清理。 尽量设在料流末端和塑件壁厚较大部位。 排气方向不应朝向操作人员,并应加工成曲线 或折弯形状,以防气体喷射时烫伤工人。 排气槽宽度常取1.5~6㎜,槽深0.02~0.05㎜, 以塑料不进入排气槽为宜。
2 排气系统的方式
2 模具排气不良产生缺陷
阻碍塑料熔体正常快速充模 气体压缩所产生的热量可能使塑料烧焦 在充模速度大、温度高、物料粘度低、注射压力 大和塑件壁厚过大的情况下,气体会浸入塑件内 部,造成气孔、组织疏松等缺陷。
烧焦
充填不足
暗纹
色差
流紋
熔不良
排气不良
短射 图6-1
脫模不良
气泡
收缩
表面凹陷
模具排气不良可能产生的缺陷
★ 利用间隙排气的结构
图6-5 利用顶杆配合间隙排气
图6-6
利用分型面排气
图6-7
兼作排气的推杆结构
镶块间隙排气
型芯间隙排气
用侧型芯运动间隙排气 图6-8
用型芯与模板配合 间隙排气 利用间隙排气
(4) 用多孔金属排气
近年来新发展的一种内部具有均匀的相互联通的孔隙结构 的金属材料—多孔金属,对模具型腔的排气具有很好的效 果。当型腔某部位排气困难时,可选用多孔金属材料制作型 腔镶块,排气效果十分明显。 模具使用时应注意维护与清理,保持气孔通畅。 多孔烧结金属,孔隙体积 分布率在20%至30%之间。这 些孔隙相互连通,平均直径 为7微米或20微米,均匀分散 在材料中。其结构模型如图 7-10所示。 预硬化处理(35-40HRc), 更加耐磨。 图6-10 材料结构模型