分解炉温度上下倒挂的原因及解决措施
N-MFC型分解炉流化床压床原因及解决措施

12 预 热 器 塌 料 .
预 热 器塌 料 由于操 作 等 方 面 的原 因造 成 预 热 器塌 料 , 问大 量物 料 冲 入分 解 炉 , 坏 了流 化层 , 瞬 破
导致 后 续物 料 在床 层 上不 能 被带 走 , 形成 压床 。
12。 误 操 作 造 成 预 热 器 塌 料 。1
由 5 %降 低 到 4 % , 时 喂 料 量 虽 然 仍 是 2 0/ , 3 8 此 4t h 但 因 为 系 统 风 量 变 小 ,造 成 系 统 塌 料 ,分 解 炉 压 床 , 原 因为 中控 员 操 作 不 熟 练 , 能 及 时 发 现 系 其 未 统变 化 。
12 2 预 热 器 出 口负 压 波 动 造 成 预 热 器 塌 料 __
由于燃 料 在 N— C 内燃 烧 不 完 全 , 料 的沸 MF 物
四 JI水 泥 一 25— l
维普资讯
腾 状 况 又 不 好 , 口温 度 低 , 分 燃 料 到 C 出 部 内继
续 燃烧 ,造 成 N— C 出 口与 C 出 口温 度 倒 挂 的 MF
一
窑 系 统 正 常 喂 料 量 一般 为 2 0/ 右 , 一 旦 4t h左
5 0P 0 0 a降 至 一 00 a 预 热器 各 级 下 料 管 温 度 急 2 0P ,
喂 料 量 波 动 到 20/ 右 时 , 解 炉 负 荷 加 大 , 7t h左 分 承 载 能 力 差 , 解 炉 层 压 就会 急 剧 上 升 , 果采 取 措 分 如 施 不 果 断就 会造 成分 解 炉 流 化床 压 床 的事 故 。 () 化 库 底 罗 茨风 机 皮 带 打 滑 , 成 下 料 不 1均 造
维普资讯
N o. 2OO8 3.
分解窑操作中常见的几个问题和产生问题的原因

分解窑操作中常见的几个问题和产生问题的原因,燃烧机(燃烧器)一、窑尾和预分解系统温度偏高1)核查是否生料kh、n值偏高,熔融相(ai203和fe203)含量偏低生料中是否si02比较高和生料细度偏粗。
如若干项情况属实,则由于生料易烧性差,熟料难烧结,上述温度偏高属正常现象。
但应注意极限温度和窑尾o:含量的控制。
2)窑内通风不好,窑尾空气过剩系数控制偏低,系统漏风产生二次燃烧。
3)排灰阀配重太轻或因为怕堵塞,窑尾岗位工把排灰阀阀杆吊起来,致使旋风筒收尘效率降低,物料循环量增加,预分解系统温度升高。
4)供料不足或来料不均匀。
5)旋风筒堵塞使系统温度升高。
6)燃烧器外流风太大、火焰太长,致使窑尾温度偏高。
7)烧成带温度太低,煤粉后燃。
8)窑尾负压太高,窑内抽力太大,高温带后移。
二、窑尾和预分解系统温度偏低1)对于一定的喂料量来说,用煤量偏少。
2)排灰阀工作不灵活,局部堆料或塌料。
由于物料分散不好,热交换差,致使预热器c,出口温度升高,但窑尾温度下降。
3)预热器系统漏风,增加了废气量和烧成热耗,废气温度下降。
三、烧成带温度太低1)风、煤、料配合不好。
对于一定喂料量,热耗控制偏低或火焰太长,高温带不集中。
2)在一定的燃烧条件下,窑速太快。
3)预热器系统的塌料以及温度低、分解率低的生料窜人窑前。
4)窑尾来料多或垮窑皮时,用煤量没有及时增加。
5)在窑内通风不良的情况下,又增加窑头用煤量,结果窑尾温度升高,烧成带温度反而下降。
6)冷却机一室篦板上的熟料料层太薄,二次风温度太低。
四、烧成带温度太高1)来料少而用煤量没有及时减少。
2)燃烧器内流风太大,致使火焰太短,高温带太集中。
3)二次风温度太高,黑火头短,火点位置前移。
五、二次风温度太高1)火焰太散,粗粒煤粉掺人熟料,人冷却机后继续燃烧。
2)熟料结粒太细致使料层阻力增加,二次风量减少,风温升高大量细粒熟料随二次风一起返回窑内。
3)熟料结粒良好,但冷却机一室料层太厚。
气化炉环形空间温度异常状况分析及总结
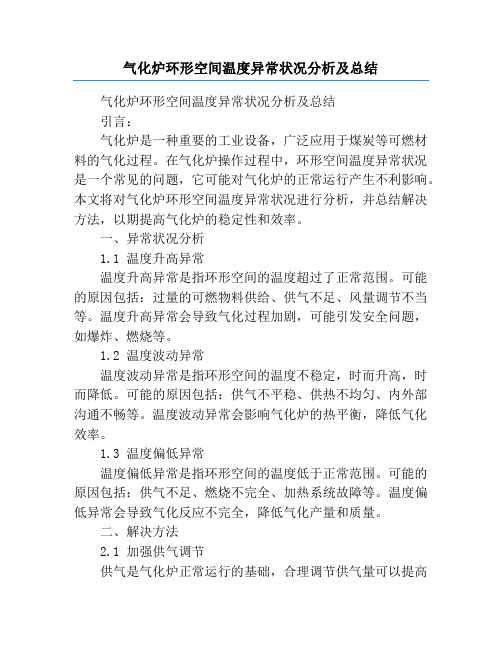
气化炉环形空间温度异常状况分析及总结气化炉环形空间温度异常状况分析及总结引言:气化炉是一种重要的工业设备,广泛应用于煤炭等可燃材料的气化过程。
在气化炉操作过程中,环形空间温度异常状况是一个常见的问题,它可能对气化炉的正常运行产生不利影响。
本文将对气化炉环形空间温度异常状况进行分析,并总结解决方法,以期提高气化炉的稳定性和效率。
一、异常状况分析1.1 温度升高异常温度升高异常是指环形空间的温度超过了正常范围。
可能的原因包括:过量的可燃物料供给、供气不足、风量调节不当等。
温度升高异常会导致气化过程加剧,可能引发安全问题,如爆炸、燃烧等。
1.2 温度波动异常温度波动异常是指环形空间的温度不稳定,时而升高,时而降低。
可能的原因包括:供气不平稳、供热不均匀、内外部沟通不畅等。
温度波动异常会影响气化炉的热平衡,降低气化效率。
1.3 温度偏低异常温度偏低异常是指环形空间的温度低于正常范围。
可能的原因包括:供气不足、燃烧不完全、加热系统故障等。
温度偏低异常会导致气化反应不完全,降低气化产量和质量。
二、解决方法2.1 加强供气调节供气是气化炉正常运行的基础,合理调节供气量可以提高气化炉的稳定性。
通过监测环形空间的温度变化,及时调整供气量,避免温度升高、波动和偏低异常状况的发生。
2.2 优化风量控制风量的调节对于燃烧的均匀性和热平衡至关重要。
通过合理设置风量控制设备,控制环形空间的气流分布,减少温度波动异常的发生。
2.3 定期检查和维护加热系统加热系统是保持环形空间温度稳定的关键设备。
定期检查和维护加热装置,确保其正常工作和高效传热,有效避免温度偏低异常状况的出现。
2.4 强化安全措施针对温度异常可能带来的安全隐患,加强安全措施是至关重要的。
建立完善的安全预警机制,配备温度报警装置和消防设备,及时发现和应对温度异常状况,防范事故发生。
三、总结气化炉环形空间温度异常状况是一个常见但又重要的问题,对气化炉的安全性和效率产生直接影响。
窑预分解系统的问题分析及改进措施

窑预分解系统的问题分析及改进措施摘要:我厂1号RSP窑经过6年多的运转,系统耐火材料呈现出不同程度的磨损、烧坏现象。
SB室下部掉砖,进而壳体烧损;SC室用风不良,导致边壁物料保护层不均衡,局部衬砖磨损严重;斜烟道及鹅颈管侧墙衬砖垮落,由于鹅颈管结构缺陷,经常结皮和堆料;MC室断面物料分布不均,物料稀相区炉壁烧损,直至筒体严重变形;因窑尾缩口处风速低,喷腾能力减弱而塌料;高温级旋风筒分离效率低,导致物料大量返回,内循环增加等。
本文依据热工标定结果,对该预分解系统出现的问题进行分析,并提出改进措施。
1 RSP窑系统工况分析热工标定主要参数对比见表1、表2,窑尾高温区工艺流程见图1。
表1 预热预分解系统温度变化℃表2 RSP炉的分解进程变化注:1997年数据为南京化工大学硅酸地方国营工程研究所的热工标定结果,SC 室出口指斜烟道出进口等同于鹅颈管出口。
图1 窑尾高温区工艺流程1.1 三次风温度及其对SC室工况的影响由表1可见,三次风温度和入炉生料温度分别只有600℃和671℃。
入炉生料温度低主要是由于C4锥体及下料管增开人孔门较多,外漏风量和散热损失增加引起的,通过加强管理,隔热堵漏后完全可以解决;三次风温度目前基本稳定在560~580℃,提高的余地很小。
其原因是:我厂采用单筒冷却机,经过多年的运转,内部装置所遭受的磨损和腐蚀不断加剧,而且增加了砌筑耐火砖的长度,熟料停留时间短(约为30min),出机熟料温度高(~290℃),使热效率本身就不高的单筒冷却机热回收率进一步降低(1997年热工标定结果为56.6%)。
三次风温度是影响分解率和燃尽率的重要因素。
较低的三次风温度导致炉内煤粉着火速度减慢,形成滞后燃烧,特别是SC室内煤粉是在纯助燃空气中燃烧,助燃空气的温度在很大程度上决定了煤粉燃尽率,三次风温度低,即使分解炉多加煤,SC室内温度也不会高,反而会加剧煤粉滞后燃烧。
从表1和表2可以看出,SC室生料出口温度和分解率分别是948℃和43.4%,结合入炉生料表观分解率已达22.6%的实际情况,说明SC室内的分解反应极低,煤粉燃烧状况不理想。
焦炉温度产生波动的原因,提出了进一步稳定炉温的措施

焦炉温度产生波动的原因,提出了进一步稳定炉温的措施2010-04-25 17:57焦炉加热管理包括温度的管理和压力制度的管理。
其任务是按规定的结焦时间、装煤量、装煤水分及加热煤气性状等实际条件,及时测量调整焦炉加热系统各控制点的温度、压力,实现全炉各炭化室在规定时间内各部位均匀成焦, 使焦炉均衡生产并达到稳产、优质、低耗、长寿、高产。
其中焦炉温度的管理贯穿于炼焦生产的始终,它对于降低热耗、提高焦炭质量、延长焦炉寿命有着决定性的意义。
因此加强对炉温的分析,有助于更好地改善操作。
一、炉温产生波动的原因1、换向期间炉温的变化焦炉加热的特点是双联火道、废气循环、焦炉煤气下喷、高炉煤气侧入,每30分钟要改变一次单、双火道的加热方式以保证加热均匀。
焦炉直行温度一般在换向10分钟后测。
由于焦炉的燃烧室较多,在测直行温度时,有的测的早,有的测的晚。
测得早的火道温度下降得少一些,测得晚的火道温度下降得多些,所以测得的温度不能代表火道的真实温度,所测温度换算成换向后20秒的温度,以确定该火道测温点的最高温度。
冷却温度作为一个校正值,其本身受各种复杂因素的影响,如冬夏季节温度变化较大、改变加热煤气种类或结焦时间等情况。
因此应加强测量以减少直行温度换算时的误差。
2、结焦期间炉料状态的变化对炉温的影响直行温度测量中以换算到下降后20秒的温度来消除换向期间温度波动引起的误差,尚不够全面,还应该分析结焦期间炉料状态的变化对炉温的影响。
装入煤在炭化室分层结焦,煤料各层经过干燥、热解、熔融、粘结、固化、收缩等阶段而成焦炭。
在整个结焦时间内,进入燃烧室的热量是保持一定的。
刚装煤时,炭化室墙将大量热传给煤料,使其表面温度急剧下降。
一般从装煤开始后的1~2小时,由1050 C~1100 C降至700 C左右。
因炉墙两侧温差急剧加大,炉墙大量放热,同时提高了火焰和墙面间的温差,使火焰传给炉墙的热量也急剧增加。
以后随着炭化室墙面温度的升高,热量逐渐平稳。
预分解窑烧成温度窑尾温度高低的原因及处理
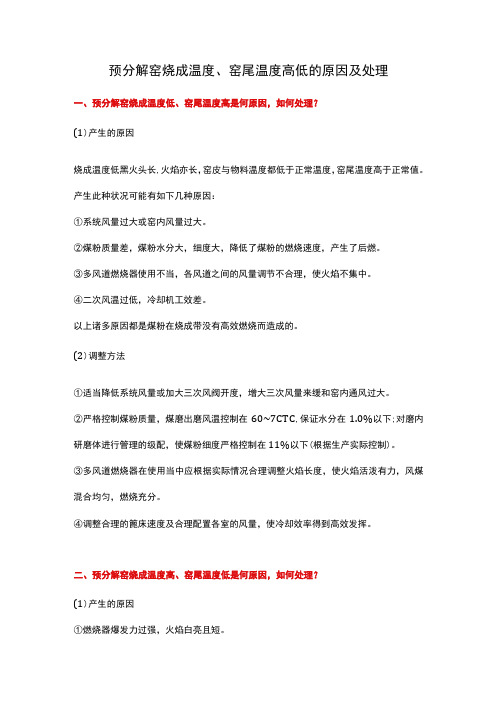
预分解窑烧成温度、窑尾温度高低的原因及处理一、预分解窑烧成温度低、窑尾温度高是何原因,如何处理?(1)产生的原因烧成温度低黑火头长,火焰亦长,窑皮与物料温度都低于正常温度,窑尾温度高于正常值。
产生此种状况可能有如下几种原因:①系统风量过大或窑内风量过大。
②煤粉质量差,煤粉水分大,细度大,降低了煤粉的燃烧速度,产生了后燃。
③多风道燃烧器使用不当,各风道之间的风量调节不合理,使火焰不集中。
④二次风温过低,冷却机工效差。
以上诸多原因都是煤粉在烧成带没有高效燃烧而造成的。
(2)调整方法①适当降低系统风量或加大三次风阀开度,增大三次风量来缓和窑内通风过大。
②严格控制煤粉质量,煤磨出磨风温控制在60~7CTC,保证水分在1.0%以下;对磨内研磨体进行管理的级配,使煤粉细度严格控制在11%以下(根据生产实际控制)。
③多风道燃烧器在使用当中应根据实际情况合理调整火焰长度,使火焰活泼有力,风煤混合均匀,燃烧充分。
④调整合理的篦床速度及合理配置各室的风量,使冷却效率得到高效发挥。
二、预分解窑烧成温度高、窑尾温度低是何原因,如何处理?(1)产生的原因①燃烧器爆发力过强,火焰白亮且短。
②煤粉质量好,灰分小,细度小,水分小。
③系统风量过小或三次风与窑内风量匹配不合理,造成窑内通风过小。
④窑内有结圈或长厚窑皮影响窑内通风,使火焰短,窑尾温下降。
(2)调整方法①合理调节多风道燃烧器各风道间的风量,如火焰温度过高、白亮且短,可适当调节内风与外风的比例,减小内风增大外风,确保火焰形状合理。
②不要过分地追求高质量的煤粉,只要煤粉的控制指标在合理的范围内就可以(细度≤11%,水分≤1.0%,根据生产实际控制),煤粉质量可根据实际情况具体调整。
③可增大系统风量,减小三次风阀开度,增大窑内的通风。
调整合理的系统风量且平衡好三次风与窑内的通风,合理的风量配备是稳定烧成的最基本条件之一。
④窑内有结圈或长厚窑皮且伴有主机电流升高、窑尾有溢料等现象,最直观地反映为窑内通风差,出现此状况应及时处理结圈和长厚窑皮。
分解炉的控制方法

分解炉控制对于窑外分解窑来说,分解炉是其核心部分,它不仅承担了系统中燃料燃烧,气固换热,碳酸盐分解的任务,而且对整个烧成系统的热力分布,热工制度的稳定起着至关重要的作用,虽然现在应用的分解炉型式众多,结构各异,但其特点和具有的功能基本上都是一样的,都属于高温气固多相流反应器,且具有悬浮床的特征。
对于中控窑操作者来说:分解炉温度(包括分解炉本体温度和出口温度)是最重要的检测控制参数之一,因为它不但表征了生料在分解炉内的预分解情况,也就是生料在分解炉中分解率的高低(分解率的高低直接影响着回转窑运转的稳定性和熟料产、质量以及能耗的高低);同时也表征了燃料在分解炉中的燃烧情况。
因此,作为中控窑操作员来说,要想操作好预分解窑,首先必须保证分解炉的热工制度稳定,要想使分解炉的热工制度稳定,就必须搞清楚以下几个问题:(1)燃料在分解炉中的燃烧传热特性及其影响因素;(2)生料在分解炉中的吸热分解速度及其影响因素;(3)气流在分解炉中运动对燃料燃烧放热和生料分解吸热的影响;(4)分解炉温度高低对回转窑煅烧的影响;(5)分解炉温度调节控制的原则与方法;(6)分解炉温度异常情况的原因与处理等。
下面就这几个问题谈一下个人的看法与认识。
不足之处,尚请指正。
一、燃料在分解炉中的燃烧、传热特性及其影响因素1.燃料在分解炉中的燃烧特性在分解炉中,燃料的燃烧传热特性与回转窑内燃料的燃烧传热特性有着本质上的区别。
回转窑内燃料的燃烧是扩散控制的过程,其火焰必须与回转窑内的煅烧制度相适应,即要求有一定的火焰形状、长度和温度。
通常我们所说的火焰形状为“毛笔头状”、“棒槌状”以及不正常时形成的“球形”火焰,“舔料形”火焰等就是这一特征的体现。
而当煤粉颗粒喷入分解炉后,在旋流和喷腾作用的影响下,使得煤粉颗粒浮游于热气流中,经过预热,分解——煤中的挥发分吸收热量放出氮、氢、氧等,燃烧发出光和热,形成一个一个的小火星,无数的煤粉颗粒便形成无数个迅速燃烧的小火星,这些小火星实质上也就是一个个的小火焰,它们在气流的悬浮作用下充满整个分解炉,从而在整个分解炉内都形成燃烧区。
炉底温度两点或多点下降较大表现及处理办法
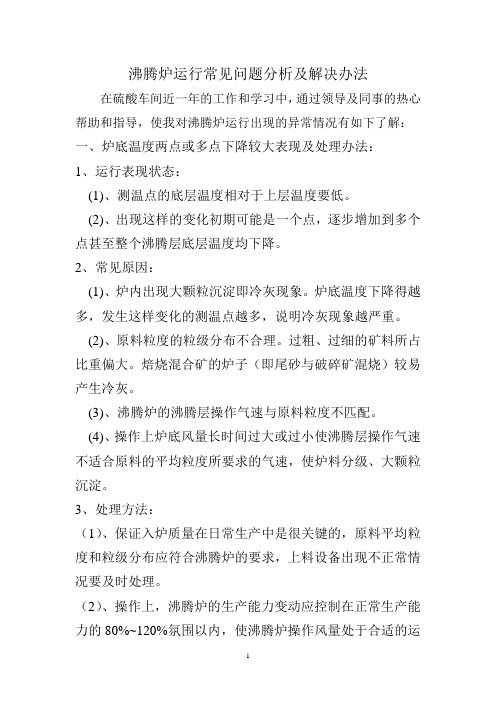
沸腾炉运行常见问题分析及解决办法在硫酸车间近一年的工作和学习中,通过领导及同事的热心帮助和指导,使我对沸腾炉运行出现的异常情况有如下了解:一、炉底温度两点或多点下降较大表现及处理办法:1、运行表现状态:(1)、测温点的底层温度相对于上层温度要低。
(2)、出现这样的变化初期可能是一个点,逐步增加到多个点甚至整个沸腾层底层温度均下降。
2、常见原因:(1)、炉内出现大颗粒沉淀即冷灰现象。
炉底温度下降得越多,发生这样变化的测温点越多,说明冷灰现象越严重。
(2)、原料粒度的粒级分布不合理。
过粗、过细的矿料所占比重偏大。
焙烧混合矿的炉子(即尾砂与破碎矿混烧)较易产生冷灰。
(3)、沸腾炉的沸腾层操作气速与原料粒度不匹配。
(4)、操作上炉底风量长时间过大或过小使沸腾层操作气速不适合原料的平均粒度所要求的气速,使炉料分级、大颗粒沉淀。
3、处理方法:(1)、保证入炉质量在日常生产中是很关键的,原料平均粒度和粒级分布应符合沸腾炉的要求,上料设备出现不正常情况要及时处理。
(2)、操作上,沸腾炉的生产能力变动应控制在正常生产能力的80%~120%氛围以内,使沸腾炉操作风量处于合适的运行范围,从而保证炉料正常的气速。
(3)、出现炉底温度下降的现象后,一种处理方法是先减小排渣量,提高炉底压力,然后加大炉底风量,将沉淀的大颗粒从炉内吹出。
另一种办法是减小风量、提高炉料中的细灰比例,增大排渣量将大粒子带出,从而将冷灰逐步消除。
(4)、沸腾炉操作上要注意控制风量与原料粒度相匹配,操作风速不能太小也不能太大。
(5)、改用细矿,炉底压力维持高一些,把炉温适当地提高些,连续运行2 ~3天一般可将冷灰消除。
(6)、除上述的一些基本方法外,生产中如发现炉温不平衡,可先适当增加炉底风量,使炉内沸腾状况得到改善,如炉温没有得到恢复再进行其它处理。
二、炉底下料口温度或多点温度突然上升后又缓慢下降1、表现状态:(1)、炉内其它炉底测温点温度或中层温度上升后又缓慢下降。
- 1、下载文档前请自行甄别文档内容的完整性,平台不提供额外的编辑、内容补充、找答案等附加服务。
- 2、"仅部分预览"的文档,不可在线预览部分如存在完整性等问题,可反馈申请退款(可完整预览的文档不适用该条件!)。
- 3、如文档侵犯您的权益,请联系客服反馈,我们会尽快为您处理(人工客服工作时间:9:00-18:30)。
分解炉温度上下倒挂的原因及解决措施
问
分解炉温度上下倒挂的原因及解决措施
——用户“阿瓦达”的提问
答
1 主要原因分析
煤粉粗,分解炉用风不足,三次风量小,煤粉在分解炉底部不能充分燃烧,煤粉会随风上移在分解炉上部燃烧,使分解炉上部温度升高,出现上下温度倒挂现象。
2 如何发现与检测
可在中控室温度显示屏上看出,只要分解炉热电耦不发生故障,显示温度准确,便可准确地进行判断,一般在窑上操作都要随时关注此处温度变化。
3 故障的处理与预防
控制煤粉细度不过粗,在5%以下;三次风的温度要提高,控制在850℃以上;三次风阀的开度不能过小,保持有足够的三次风量,三次风阀开度控制在40%左右,停窑检查三次风进口处结皮积料,并进行清理,检查三次风阀板与四周墙壁的粘结情况,每三个月检查一次,每半年彻底清理一次。
4 故障的影响
分解炉内底部与上部温度出现倒挂现象常有发生,出口温度明显高于低部温度,会造成分解率低,煤在分解炉内燃烧不
充分,且燃烧位置上移,分解炉内高温点也上移,生料在炉内高温区的路径相应缩短,生料的分解受到影响,使五级预热器温度升高,易引起五级锥体产生结皮堵塞现象。