RG03-12.18 ZG10Cr13铸造不锈钢冶炼浇注操作工艺规程
铸件操作规程讲解(3篇)
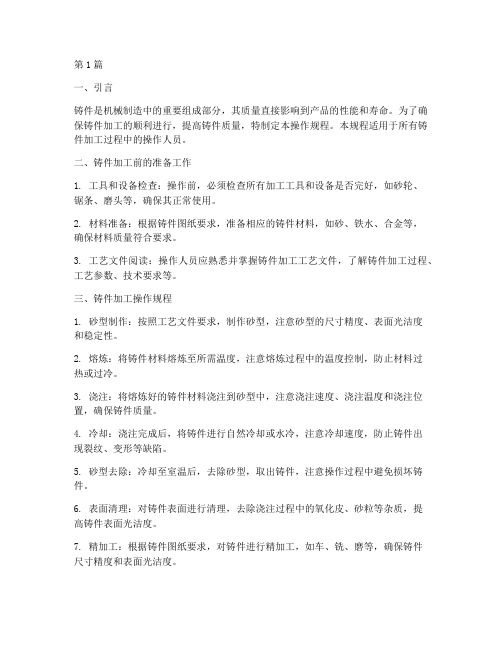
第1篇一、引言铸件是机械制造中的重要组成部分,其质量直接影响到产品的性能和寿命。
为了确保铸件加工的顺利进行,提高铸件质量,特制定本操作规程。
本规程适用于所有铸件加工过程中的操作人员。
二、铸件加工前的准备工作1. 工具和设备检查:操作前,必须检查所有加工工具和设备是否完好,如砂轮、锯条、磨头等,确保其正常使用。
2. 材料准备:根据铸件图纸要求,准备相应的铸件材料,如砂、铁水、合金等,确保材料质量符合要求。
3. 工艺文件阅读:操作人员应熟悉并掌握铸件加工工艺文件,了解铸件加工过程、工艺参数、技术要求等。
三、铸件加工操作规程1. 砂型制作:按照工艺文件要求,制作砂型,注意砂型的尺寸精度、表面光洁度和稳定性。
2. 熔炼:将铸件材料熔炼至所需温度,注意熔炼过程中的温度控制,防止材料过热或过冷。
3. 浇注:将熔炼好的铸件材料浇注到砂型中,注意浇注速度、浇注温度和浇注位置,确保铸件质量。
4. 冷却:浇注完成后,将铸件进行自然冷却或水冷,注意冷却速度,防止铸件出现裂纹、变形等缺陷。
5. 砂型去除:冷却至室温后,去除砂型,取出铸件,注意操作过程中避免损坏铸件。
6. 表面清理:对铸件表面进行清理,去除浇注过程中的氧化皮、砂粒等杂质,提高铸件表面光洁度。
7. 精加工:根据铸件图纸要求,对铸件进行精加工,如车、铣、磨等,确保铸件尺寸精度和表面光洁度。
8. 检验:对加工完成的铸件进行检验,包括尺寸、形状、表面质量等,确保铸件符合要求。
四、注意事项1. 操作人员应严格遵守操作规程,确保加工过程安全、高效。
2. 严禁在加工过程中吸烟、饮酒,保持加工环境整洁。
3. 操作设备时应注意设备维护,定期检查设备性能,确保设备正常运转。
4. 操作过程中,如发现异常情况,应立即停止操作,报告上级,待问题解决后方可继续操作。
5. 严格把控材料质量,确保铸件加工过程中材料符合要求。
五、总结铸件加工操作规程是确保铸件质量的关键,操作人员应严格遵守规程,不断提高自身技能水平,为我国机械制造业的发展贡献力量。
精铸不锈钢 ZG1Cr13材料技术要求
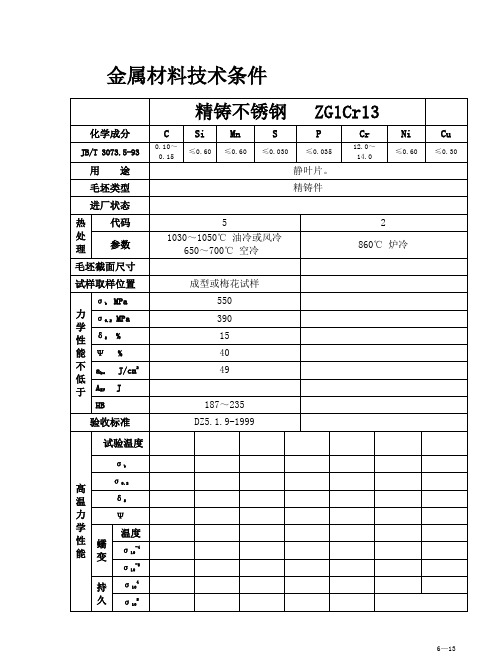
精铸不锈钢ZG1Cr13
化学成分
C
Si
Mn
S
P
Cr
Ni
Cu
JB/T3073.5-93
0.10~0.15
≤0.60
≤0.60
≤0.030
≤0.035
12.0~14.0
≤0.60
≤0.30
用途
静叶片。
毛坯类型
精铸件
进厂状态
热
处理
代码
5
2
参数
1030~1050℃油冷或风冷
650~700℃空冷
国外相近牌号
物
理
性
能
临界温度
℃
AC1
AC3
Ar1
Ar3
线膨胀系数
α×106
20~100℃
20~200℃
20~300℃
20~400℃
20~500℃
20~600℃
导热系数
λ
100℃
200℃
300℃400℃50 Nhomakorabea℃600℃
比 热
C
20~100℃
20~200℃
20~400℃
20~500℃
弹性模量
20℃
100℃
200℃
300℃
400℃
500℃
EGPa
密度
kg/m3
工艺性能
冶 炼
熔点:1500~1530℃;
铸造线收缩率:1.7%~2.0%。
铸 造
铸造性能较差,易造成氧化铬夹杂,导热性差,热应力大,易产生裂纹。
焊 接
焊接性尚可;用E410-16焊条,焊前需300℃预热,焊后去应力。
冷加工
说 明
不锈钢饰品铸造的工艺流程
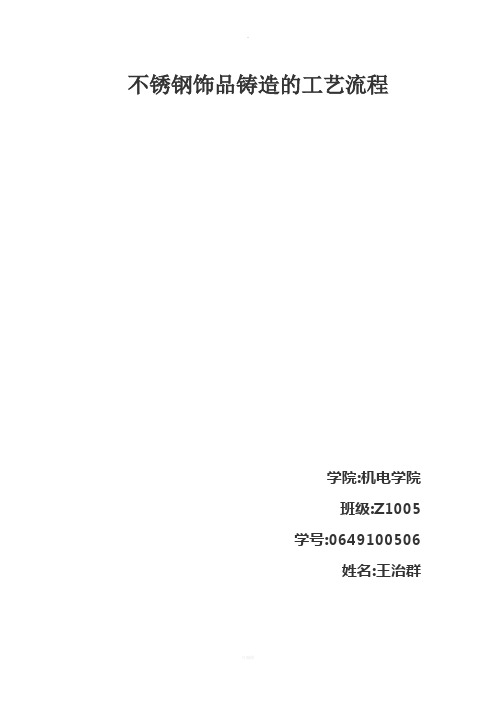
不锈钢饰品铸造的工艺流程学院:机电学院班级:Z1005学号:0649100506姓名:王治群1、制版失蜡浇铸需要蜡版,而蜡版的批量制作则需要用银版压制的橡胶模。
它是不锈钢饰品制作工艺中要求最高的工序,要求所制银板的表面,镂空部位和背面光洁无痕,要求银板的各部分结构合理,镶嵌钻石的位置尺寸准确无误,有些还要求对镶嵌部位进行预加工。
准备好银版后才可以进入失蜡浇铸工艺流程。
目前使用的制版工艺主要有:手工雕蜡版,电脑雕蜡版和手起银版。
三种工艺各有优点,相互补充。
手工雕蜡版即用石蜡雕出设计图纸上的造型,再利用失蜡浇铸的方法倒出银版;电脑雕蜡版不同于手工雕蜡的是它是通过电脑3D软件与喷蜡机相结合,做出蜡模造型,再使用失蜡浇铸的方法倒出银版;而手制银版,就是制版师傅直接手工制作设计图上的模型。
由于手工雕蜡版制版速度快,雕蜡过程修改容易,工具损耗相对小而被广泛使用。
2、失蜡铸造失蜡铸造俗称倒模,是目前不锈钢饰品生产的重要手段。
(1)压制胶模压制胶模的注意事项及过程:1)压模框和生胶片要清洁,不要用手直接接触生胶片的表面。
2)保证原版和橡胶之间不会粘连,应优先使用银版,铜板应先镀银。
3)确定适当的硫化温度和时间,两者基本上符合一个函数关系,与胶模的厚度,长宽及原版的复杂程度有关。
通常将压模温度定为150度左右,如果胶模厚度在3层(约10mm),一般硫化时间为20-25分钟,如果是4层(约13mm),则硫化时间可为30-35分钟。
依次类推。
同时硫化温度与原版的复杂程度也有关系,如原版复杂,细小,应降低硫化温度,延长硫化时间。
4)压模时要保证原版和生胶片之间没有缝隙。
采用塞、缠、补的方式将首版上的空隙位、凹位和镶石位等填满,用碎小的胶粒填满,用尖锐物质(如镊子)压紧。
5)先行预热。
硫化时间到了以后迅速取出胶模,压好的胶模要求整体不变形、光滑、水线不歪斜,最好使其自然冷却到不烫手时,就可以趁热用锋利的手术刀进行开胶模的操作。
炼钢连铸浇钢工艺

炼钢连铸浇钢工艺预览说明:预览图片所展示的格式为文档的源格式展示,下载源文件没有水印,内容可编辑和复制浇钢操作基本工艺规程1钢包包衬的浇注成型工艺操作1.1 钢包包衬的修砌与浇注成型1.1.1 包底永久层的砌筑:将包壳内的钢、渣及其它杂物清除干净后,用打结料打结包底,并以法兰为准找平(50mm厚),然后砌一层二等高铝标准砖。
1.1.2 砌包底砖用泥料:采用1#泥料。
1.1.3 包壁永久层的砌筑:沿包壁砌一圈A9粘土砖。
1.1.4 砌包壁砖用泥料:镁砂+(9-11%)卤水,和成粘稠状。
1.1.5 打包底前将座砖摆正。
1.1.6 工作层的浇注成型:采用铝-镁浇注料浇注成型,先浇注包底,而后浇注包壁。
1) 包底用料3.5吨(厚350mm),分两次打结。
2) 号在包壁永久层上贴硅酸铝纤维毡(8mm厚);浇注胎具安放在与钢包同心位置;当头批料浇至300mm高时,启动振动器,至浇到帽口后继续振动5分钟。
3)调和工作层浇注打结料时,一定要按配料的比例投料,使用搅拌机混料,每2.6吨混合料为一批,搅拌时间≥5分钟,包衬铝镁料配比如下表:※水玻璃模数>2.41.1.7 脱胎与养护1) 浇注好的钢包内衬,在自然干燥12小时后,包衬材料有一定强度方可脱出胎具。
脱胎时,要将模具吊正,切忌斜拉猛吊。
脱模后要对损坏的地方进行修补。
2) 脱胎后的钢包静置24小时后方可进行烘烤。
烘烤要求如下:前期低温烘烤(<400℃)8小时,中期中温烘烤(400-800℃)8小时,后期高温烘烤(>800℃)24小时。
2. 浇钢前准备2.1 钢包准备2.1.1 钢包使用前应认真检查包衬侵蚀情况和滑动机构有无损坏,侵蚀严重或有损坏时要停止使用或修复后再投入使用。
2.1.2 使用粘钢钢包应事先通知炼钢工,由炼钢工决定是否使用。
2.1.3 包内渣子清净,渣盖捅掉,保持包内清洁。
2.1.4 按要求加引流剂,摆包时严禁滑动机构、连杆与钢包车碰撞。
铸钢熔炼与浇注操作工艺规程.doc

无锡市灵通铸造有限公司作业指导书Z/LTZZ/RLJZ-2015A/0铸钢熔炼和浇注操作工艺规程年月日批准年月日实施编制校核审核版本号 /标记处数更改文件号签名年月日批准修改状态1、目的本工艺规程通过对中频电炉筑炉、烘炉以及铸钢熔炼和浇注工艺等相关技术要求的描述,以达到确保中频电炉正常熔炼和指导铸钢件生产的目的。
2、范围本作业指导书规定了中频电炉筑炉、烘炉工艺规程。
本作业指导书规定了中频电炉筑炉材料规格及混制备料工艺规程。
本作业指导书规定了铸钢熔炼和浇注操作的基本要求。
3、职责本工艺规程由技术质量部归口管理。
材料员按本作业指导书的规定提供各种原材料。
筑炉工按本作业指导书的规定进行筑炉、烘炉操作。
熔炼、浇注工按本作业指导书的规定进行熔炼、浇注操作。
4、程序4.1 原材料要求4.1.1所有炉料如低碳碳素废钢、浇口或废铸件等回炉料、各种合金等,都必须明确其化学成分,无标识或化学成分不明的炉料严禁使用。
4.1.2炉料必须无油、干燥、干净,潮湿、泥土、严重锈蚀、表面油污的炉料不准入炉;严禁任何有色金属混入;严禁爆炸物品混入雷管、密闭空气罐和有水的钢管等。
4.1.3辅料:a、脱氧用1)锰铁Mn2)硅铁 Si-753) 铝 2#Al4)硅钙5)硒土b、增碳用石墨电极100%c、覆盖剂:珍珠岩覆盖剂,干燥、洁净。
4.2 常用铸钢材料化学成分应符合表 1 的规定。
表 1、常用铸钢材料化学成分牌号 C Si Mn P S Cr Mo Ni V Cu ZG230-450.2 ~ 0.3 0.2 ~ 0.5 0.5 ~ 0.9 ≤0.04 ≤ 0.04 / / / / ≤0.3GS20Mn5 0.17 ~≤0.6 1.0 ~ 1.5 ≤ 0.02 ≤0.02 / / / / ≤ 0.3 0.23SCW480 0.18 ~0.4 ~ 0.6 0.9 ~ 1.2 ≤ 0.04 ≤0.04 / / / / ≤ 0.3 0.2045Mn2 0.40 ~0.2 ~ 0.4 1.6 ~ 1.8≤≤/ / / / / 0.50 0.035 0.035304 ≤ 0.08 ≤1.50.8 ~ 2.0 ≤ 0.04 ≤0.03 18.0 ~/8.0 ~/ / 20.0 11.0316L ≤ 0.030 ≤1.0 ≤ 2.0 ≤ 0.03≤16.0 ~ 2.0 ~10.0~14/ / 0.045 18.0 3.0 .021.0 ~2.5 ~4.50 ~2205 ≤ 0.030 ≤1.0 ≤ 2.0 ≤ 0.03 ≤0.02 3.5 / /23.0 6.504.3 中频电炉筑炉、烘炉工艺4.3.1 主要原材料:中性炉料修补辅助材料:水玻璃M2.6-3.4 d1.3左右硼酸工业硼酸应经过筛选后再用。
RG03-12.11电弧炉炼钢基本操作工艺规程

1.目的与适用范围本规程为我厂电弧炉炼钢的基本技术操作守则,是炼钢生产操作和技术检查的基本依据。
适用于电弧炉炼钢。
各钢种的具体操作工艺,详见《电弧炉炼钢分钢种技术操作规程》。
2.确保电弧炉正常冶炼的规定2.1 换新炉体后第一炉只准冶炼普通碳素钢。
新炉体第一炉必须做到:a.新炉体和新钢包不得在同一炉使用;新出钢槽,新钢包不得用于重点钢。
b.配碳量要适当提高,熔化期不得吹氧助熔,保证氧化期脱碳≥0.50%。
2.2 炉体损坏严重,经过大补炉,垫炉底后,前三炉不得冶炼重点钢。
只能冶炼不作重要用途的碳素钢。
2.3 上炉冶炼高合金钢,下一炉必须冶炼含有相应合金元素的低合金钢。
配料和熔炼都要考虑合金元素的影响。
电弧炉熔炼铸铁后,下一炉应彻底熔清炉底残铁,防止还原期或成品钢突然涨碳。
2.4 原材料(尤其是铁合金)使用前必须确知其化学成分,否则不得使用。
2.5 送电前应仔细检查水冷系统和机电设备,发现故障应及时处理。
保证水冷系统水流畅通,不漏水。
2.6 送电前调整好电极长度,必须留一螺丝孔长度在外,并上好电极螺丝接头。
熔化期发现炉料不导电或电极卡头打弧时,必须及时停电处理。
2.7 冶炼各期必须专人集中精力,看好电表。
严禁带负荷停电、送电。
必须在停电后由专人操作,切除或带上电抗。
电表员必须严格规定送电。
班长要控制好熔炼各期的温度,避免还原期后升温。
2.8 测量钢液温度要有代表性。
以热电偶测温。
测温前必须充分搅拌钢铁和炉渣。
3.配料本节主要指钢铁料的准备。
配料的其他注意事项,详见《电炉炼钢用原材料及配料规程》。
3.1 必须按所炼钢种、冶炼方法及生产计划,确定具体的配料方案。
所有合金废钢,特别是车间内部的浇冒口、注余、包底、废铸件等要分类管理,按计划合理使用,不得用作普通废钢。
3.2 采用氧化法冶炼时,炉料的配碳量应能保证氧化期脱碳量的要求。
钢铁料中不足的碳量,可配入生铁或废电极块补足。
3.3 废钢中不得混入有色金属,如:铜、铅、锡、锌、铝等,特别是巴氏轴承合金,一经发现,必须立即检出送交废品库集中处理。
RG03-12.14 ZG06Cr13Ni4Mo铸造不锈钢冶炼浇注操作工艺规程

1 适用范围、钢号特性及用途1.1 本规程适用于JB/DQ1554-89中小型水轮机铸钢件技术条件与GB6967-86工程结构用中、高强度不锈钢铸件中规定的ZG06Cr13Ni4Mo。
1.2 化学成分(wt.%)(2) 残余元素:Cu≤0.50%,V≤0.03%,W≤0.10%,残余元素总量≤0.80%。
1.3 机械性能(≥)1.4 ZG06Cr13Ni4Mo用于水轮机的叶片及转轮室等铸钢件,具有良好的抗汽蚀、耐泥沙磨损和抗水下疲劳性能,并有较高的强度和韧性,还有较好的铸造性能和焊接性能。
2 冶炼浇注特点2.1 本钢号要求C≤0.07%,尽量控制C≤0.06%,冶炼温度较高,因此,要求用无碳炉衬,能耐高温侵蚀。
所用原材料必须清洁干燥。
对于任何可能引起增碳的操作环节都要严格控制。
必须保证吹氧终点碳≤0.03%。
冶炼应安排在干燥、晴朗天气下进行。
2.2 在不锈钢中加入稀土元素可以有效地改善钢的耐蚀性、铸造流动性和机械性能。
为此,出钢时在钢包中以金属铈或混合稀土的形式加入0.15~0.20%Re。
为了使稀元素脱氧产物易于上浮,出钢温度相应提高20~30℃。
2.3 在空气中浇钢,二次氧化会严重恶化铸件的内在质量。
采用氩气保护浇注是防止二次氧化的有效措施。
即在钢包水口与浇口之间安装吹氩保护罩,浇注前向浇注系统及型腔内通氩气驱除空气,降低保护罩内氧的分压,并在氩气保护下浇注。
3冶炼前的准备3.1 对炉体的要求3.1.1 采用无碳炉衬,在炉龄前期(新打结的炉衬5炉以后),炉体坚实,形状良好的炉况下冶炼。
3.1.2 前一炉冶炼低碳钢,炉内不得残留废钢,尽量出尽炉渣,用镁砂(卤水粘结)仔细补好渣线,千万不得混入沥青。
3.2 原材料3.2.1 石灰:采用新焙烧的优质石灰。
还原期用的石灰一定要经过人工选择,选出烧透的块状石灰,装在料斗内,覆盖薄铁板烘烤,其中不得混入黑色或黄色块状物及碎屑。
3.2.2 Fe-Cr:采用含C≤0.06%的微碳铬铁,准确过磅后逐块用干燥的压缩空气吹干净,装在料斗内用柴油喷枪烘烤。
钢、铁水浇注岗位操作规程范文(二篇)

钢、铁水浇注岗位操作规程范文一、岗位背景钢、铁水浇注是金属冶炼工艺中至关重要的一环,也是保证成品质量的关键步骤。
岗位操作人员需要具备丰富的经验和严谨的操作技巧,以确保钢、铁水顺利浇注。
本操作规程旨在规范钢、铁水浇注岗位的操作流程,提高工作效率和安全性。
二、操作准备1. 检查设备:操作人员需仔细检查浇注设备(包括浇注罐、浇注车、浇注管道等)的完整性和正常运行情况,确保没有任何损坏或故障。
如有异常情况,应立即报告相关部门进行维修。
2. 检查材料:操作人员需核对钢、铁水的类型和规格,确保与订单一致。
同时需要检查钢、铁水的温度,确保符合浇注要求。
3. 安全防护:操作人员需佩戴符合要求的防护用品,包括防酸碱手套、防护眼镜、耐高温工作服等。
同时,需要确保工作区域的安全,如检查防护栏杆、紧急停机按钮等设备的正常工作,并保证工作区域内无其他杂物。
三、操作流程1. 对设备进行预热:操作人员需按照设备预热程序,对浇注罐和浇注管道进行预热。
预热温度需根据钢、铁水的熔点和浇注要求进行调整,确保钢、铁水可以顺利流动。
2. 准备浇注工具:操作人员需准备好浇注车、浇注罐以及其他必要的工具,如浇注铲、温度计等。
确保这些工具在操作过程中不会对钢、铁水产生污染。
3. 开始浇注:操作人员需按照指定的时间和顺序开启闸阀,浇注钢、铁水到浇注罐中。
在浇注过程中,需要注意控制浇注速度和浇注压力,确保钢、铁水均匀流动,并避免产生气泡和不良现象。
4. 监测浇注过程:操作人员需密切关注浇注过程中的各项指标,如温度、压力、流量等。
如发现异常情况(如温度过高、压力异常等),应立即停止浇注并报告相关部门。
5. 完成浇注:当钢、铁水浇注完毕后,操作人员需按照浇注工具清洗和维护的流程,对浇注罐、浇注车等设备进行清洗和维护,以确保下次使用时的正常运行。
四、安全措施1. 操作人员需经过相关岗位培训,并且持有相关操作证书。
未经培训和证书验证的人员禁止进行钢、铁水浇注操作。
- 1、下载文档前请自行甄别文档内容的完整性,平台不提供额外的编辑、内容补充、找答案等附加服务。
- 2、"仅部分预览"的文档,不可在线预览部分如存在完整性等问题,可反馈申请退款(可完整预览的文档不适用该条件!)。
- 3、如文档侵犯您的权益,请联系客服反馈,我们会尽快为您处理(人工客服工作时间:9:00-18:30)。
1 适用范围、钢号特性
1.1 本规程适用于GB6967-86工程结构用中、高强度不锈钢铸件规定的ZG10Cr13。
1.2 化学成分(wt.%)如下表:
1.3 力学性能
2 冶炼浇注特点
2.1 本钢号属半马氏体半铁素体钢,易产生轴心裂纹,对氢气敏感性强,力学性能(主要指强度)不易合格。
成品碳应尽量控制在0.10~0.15范围内。
2.2 在不锈钢中加入稀土元素及钙能有效地改善钢的耐腐蚀性、铸造流动性及力学性能(特别是冲击韧性)。
为此,出钢时在出钢槽内随钢流加入1kg/t的Ca-Si粒,出完钢在钢包中插入混合稀土丝0.10%,出钢前温度为1620~1640℃。
2.3 在大气中浇钢,钢液二次氧化会严重恶化铸件的内在质量。
氩气保护浇注是防止二次氧化的有效措施。
在钢包底部水口与铸型浇口之间安装吹氩保护罩,浇注前向浇注系统和型腔内通入氩气,驱除空气降低系统内氧的分压,并在氩气保护下浇注。
3 冶炼前的准备工作
参见ZG05Cr13Ni4Mo铸造不锈钢冶炼浇注工艺操作规程(RG.03-12.14)中的3.1、3.2、3.3节。
4 新料氧化法冶炼浇注操作要点
4.1 配料:钢铁料应选用清洁少锈的低磷硫碳素废钢,不得配入含铬、钼、镍的合金废钢。
配料成分应保证熔清后C≥0.40%,Cr≤0.50%,炉料中不足之碳用废电极块补足。
4.2 装料及熔化
4.2.1 装料前炉底垫石灰100~150kg。
4.2.2 熔化后期可吹氧助熔,熔清前可加≤1.5%碎矿石及适量石灰,放初期渣,以利早期去磷。
4.2.3 炉料全熔,温度达到1560℃,搅拌取样分析C、P、S及Cr的含量。
4.3 氧化
4.3.1 采用综合氧化,加矿氧化时做到高温沸腾,自动流渣,严禁发喷。
取样分析C、P,当P≤0.010%时,迅速扒去全部炉渣,加入石灰、萤石造新渣,做到流动性良好,以利吹氧去碳。
4.3.2 测温≥1600℃,单管吹氧,待炉内有强烈碳火焰喷出后,提升电极,停电连续吹氧。
汇流排氧压保持在2.0~2.5 MPa。
吹氧过程中,每隔5~6分钟取样分析C,估计碳降至0.06~0.08%,停止吹氧。
搅拌后取样分析C、Mn、P、Cr测温。
4.3.3 停吹氧前3~5分钟,必须将电极、卡头、横臂及绝缘圈上的灰尘吹净。
4.4 还原
4.4.1 停吹氧取样后,立即开出炉体,加入烤红的微碳铬铁,应尽量加在熔池中心,开进炉体,将暴露在渣面上的铬铁推入熔池,吹氧化铬铁,氧压5~8MPa。
随后加Fe-Si粉调整炉渣的流动性,用量3~4kg/t。
4.4.2 铬铁熔清:送电,预脱氧。
继续用Fe-Si粉与Ca-Si粉脱氧,用量3~5kg/t。
Al粉4~5kg/t。
待炉渣颜色变为黑褐色,流动性良好,扒去大部分或全部渣。
4.4.3 扒渣后在钢液面上加Ca-Si块2kg/t,然后加渣料,石灰16~20kg/t,稀渣化好后插铝1.0 kg/t。
还原过程中适当加石灰造渣。
4.4.4 用石棉绳封闭电极孔。
视温度情况决定是否关电。
分两批加Ca-Si粉脱氧,总用量5~7kg/t,Al粉2~3kg/t,间隔5分钟看渣,渣白则提升电极停电,连续搅6个耙子,取一个试样,专人连取2个试样全分析。
用Al粉与Ca-Si粉个1~2kg/t保持白渣。
10分钟后搅拌取还原第3样。
取还原1、3样时。
取渣样分析(FeC),要求≤0.50%。
4.4.5 钢液在白渣下30分钟,根据还原样分析结果,调整成分。
测温要求在1620~1640℃,插铝0.5kg/t。
适当加萤石稀渣,充分搅拌。
4.5 出钢浇注
4.5.1 提升电极,停止出钢。
渣钢混出,大流集中。
出钢槽中顺钢流加Ca-Si粒1kg/t,包内插混合稀土丝1kg/t,包内取成品样,并测温。
4.5.2 使用3次以后的新钢包,烘烤要控制好风油流量,避免柴油渗入包底,水口周围不得冒黑烟。
4.5.3 钢包调至浇注现场,松开塞杆保险前,安装吹氩保护罩,连接氩气管,对准浇口,落下保护罩,通入氩气,然后开浇,开启塞杆不得用力过猛,防止喷钢。
4.5.4 不锈钢含铬量高,易氧化产生氧化物夹杂。
应尽量快速平稳浇注。
上冒口后减慢注速。
平冒口达到1/3高度加覆盖剂,达到浇注高度后,补加覆盖剂。
5 返回吹氧法冶炼浇注操作要点
5.1 配料与装料
5.1.1 炉料由Cr13型返回钢(包括浇冒口、废铸件及汽轮机废叶片等)及优质低磷硫碳素废钢组成。
不得配入06Cr13Ni4Mo 及其它含镍、钼、钨、钒等元素的合金废钢。
5.1.2 配料成分规定如下:
C:0.25~0.35% 不足之碳用废电极补足。
P:≤0.020,S:≤0.035%
Cr:废钢中的铬按7~8%配入。
Si:按铬的1/10配入,不足的Si可在吹氧去碳前用细碎的
Fe-Si补足。
5.1.3 料前炉底垫石灰100~150 kg。
5.2 熔化
5.2.1 熔化期原则上不得吹氧助熔。
炉坡上的废钢尽量用铁耙拉下。
如必须吹氧,时间不得超过10分钟,以减少铬的烧损。
5.2.2 炉料彻底熔清,测温≥1600℃,取样分析C、P、S、Cr。
如渣层过厚可加部分Fe-Si粉对炉渣初步脱氧后,扒去部分炉渣,调整渣流动性,以便吹氧去碳。
5.3 吹氧脱碳
吹氧前加入0.5%Si的Fe-Si(平时用剩的细碎硅铁亦可),吹氧脱碳后期可适当加些Fe-Si粉保持炉渣流动性。
吹氧操作按氧化法操作要点中的4.3.2、4.3.3执行。
5.4 还原、出钢、浇注
同氧化法冶炼浇注操作要点。