数控加工中刀具补偿的应用
数控加工中刀具补偿的应用

数控加工中刀具补偿的应用朱卫峰[中国长江动力公司(集团)]摘要:刀具补偿是数控机床的主要功能之一,他分为:刀具长度补偿、刀具半径补偿、刀具偏置补偿种。
它们基本上能解决加工过程中根据刀具几何形状尺寸产生零件轮廓轨迹等问题,从而保证加工出符合图纸尺寸要求的零件。
关键词:刀具半径补偿,刀具长度补偿,刀具几何补偿,磨损补偿引言:刀具补偿的理论及其实现,在各类数控系统中都已经是比较成熟的技术。
在使用数控机床加工零件的过程中,刀具的运动轨迹不等同于工件的轮廓。
为了保证工件轮廓形状,加工时数控系统必须根据工件轮廓和刀具的几何形状尺寸计算出刀具中心运动轨迹。
在建立、执行刀补后,数控系统自动计算、自动调整刀位点到刀具的运动轨迹从而加工出符合图纸尺寸要求的形状。
当刀具磨损或更换后,加工程序不变,只须更改程序中刀具补偿的数值。
刀具补偿使用简单方便,能极大提高编程的工作效率。
下面就刀具补偿在一般数控加工中的应用进行探讨:一.刀具半径补偿1.刀具半径补偿的概念A.在轮廓加工过程中,由于刀具总有一定的半径,刀具中心的运动轨迹与所需加工零件的实际轮廓并不重合。
在进行轮廓加工时,刀具中心偏离零件的实际轮廓表面(图纸中所要加工对象的轮廓)一个刀具半径值。
这种偏移,称为刀具半径补偿。
B.采用刀具半径补偿的作用和意义数控机床一般都具备刀具半径补偿的功能。
在加工中,使用数控系统的刀具半径补偿功能,就能避开数控编程过程中的繁琐计算,而只需计算出工件加工轮廓轨迹的起始点坐标值即可。
同时,利用刀具半径补偿功能,还可以实现同一程序的粗、精加工以及同一程序的阴阳模具加工等功能。
C.刀具半径补偿指令的使用方式根据ISO 标准规定,当刀具中心轨迹在编程轨迹前进方向的左边时,称为左刀补,用G41表示;刀具中心轨迹在编程轨迹前进方向的右边时,称为右刀补,用G42表示;注销刀具半径补偿时用G40表示。
2 刀具半径补偿过程A.刀具半径补偿建立:当输入的程序段包含有G41/G42命令时,系统认为此时已进入刀补建立状态。
数控加工中刀具补偿的运用
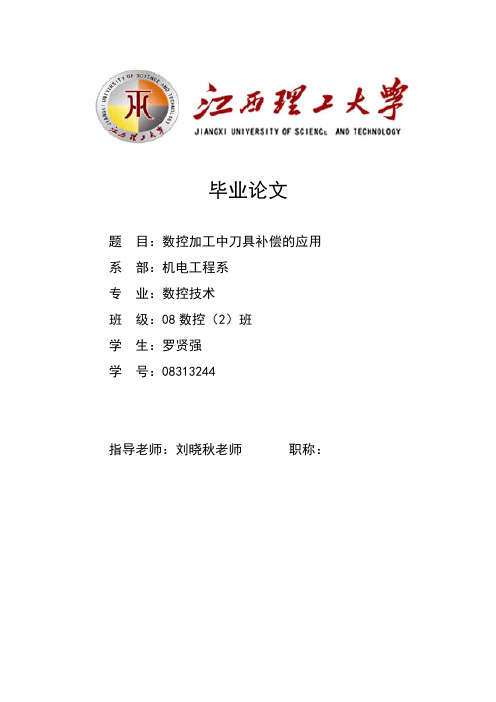
毕业论文题目:数控加工中刀具补偿的应用系部:机电工程系专业:数控技术班级:08数控(2)班学生:罗贤强学号:08313244指导老师:刘晓秋老师职称:江西理工大学南昌校区毕业设计(论文)任务书机电工程系系部数控专业2008级(2011届)数控(2)班学生罗贤强题目:数控加工中刀具补偿的应用专题题目(若无专题则不填):原始依据(包括设计(论文)的工作基础、研究条件、应用环境、工作目的等):工作基础:在20世纪60年代的数控加工中还没有出现补偿的概念,所以编程人员不得不围绕刀具的理论路线和实际路线的相对关系来进行编程,这样不仅很容易产生错误,而且生产效率低下。
当刀具补偿概念出现并应用到数控系统中后,编程人员就可以直接按照轮廓尺寸进行程序编制。
在建立、执行刀补后,由数控系统自动计算,自动调整刀位点到刀具的运动轨迹。
当刀具磨损或更换后,加工程序不变,只须更改程序中刀具补偿的数值。
因此刀具补偿的应用不仅提高了生产效率,还大大降低了技术人员的劳动强度。
研究条件:利用网络资源,参考相关文献,并在老师的提示和指导下熟悉并掌握刀具补偿的基本应用和相关注意事项。
应用环境:刀具补偿广泛用于数控车床、数控铣床、加工中心等淑红设备中。
提高了数控加工的精度。
工作目的:深入了解刀具补偿的概念以及分类,着重掌握数控车床车削加工中的刀具半径补偿的问题和车床的对刀问题。
并通过本论文提高自己在刀具补偿方面的理论水平。
主要内容和要求:(包括设计(研究)内容、主要指标与技术参数,并根据课题性质对学生提出具体要求):研究内容:1数控车床加工的对象:数控车床是目前使用比较广泛的数控机床,主要用干轴类和盘类回转体工件的加工,能自动完全内外圆面、柱面、锥面、圆弧、螺纹等工序的切削加工,并能进行切槽、钻、扩、铰孔等加工,适合复杂形状工件的加工。
与常规车床相比,数控车床还适合加工如下工件。
( 1 ) 轮廓形状特别复杂或难于控制尺寸的回转体零件,( 2 ) 精度要求高的零件。
数控车床加工中的刀具补偿应用

段 外圆作 为基准 ,0 、0 等 刀具依 次触碰 已加工 表面 , T 2T 3 分 输 入并 显示 。 4所 示 为 F N 图 A UC控制 系统 的刀具 补偿值 别记录移动偏差至相应刀具 的长度补 偿号对 应的 x值处 。 图 1 示 为 刀具 长 所 度 补 偿生 效 后 ,实 际刀 具 移 动示 意 图 。如果 不 使 用 刀具 补偿 ,调用 程
设定 完 T 1 具 的 z轴坐 标 系。 由于 在加 工 过程 中还 需 2 0刀 . 刀补 参数 设置 3
加 工前 , 数控 系统 刀具补偿 界面 内分别设置 x zR 在 、、 、 等刀具分别设定 z向长度补偿。方法为依次将 T 2T 3 T 0 、0 参数 所需 的数值 , 复位 清空数控缓存 区内的加工程序 , 重 等刀具触碰 T 1 0 刀具加工完成的 z向基准面 ,并将机床 新调人所需加工程序以使新设置的刀具补偿参数各值生效。 所 显示 的 z向 坐标 ,带 符号 分别 设 定 到对 应 刀具 的长 度 参数 设 置 时 , 首先 进 入 [ F S TwE R] 置量 显示 0 FE , A 偏
设 定界 面 。
OF ET W EAR FS / NO. W0 l WO 2 WO 3 W0 4 W0 5 W0 6 X 10 0 .0 0.0 0 0 0.0 0 0 00 0 .0 00 0 .0 0.0 0 0 Z 10 0 0 00 0 .0 00 0 .0 00 0 .0 00 0 .0 00 0 0 0 R 040 . 0 OOo . 0 N T l O
序 段 : 6 G 0 N 0 0 X2 0
000 . 0
0o O .0 0.0 0 0 00 0 .0
0
0 0 0
z 5T 2 0 刀 具 将 从 0 1 00 ,
简述刀具补偿在数控加工中的作用
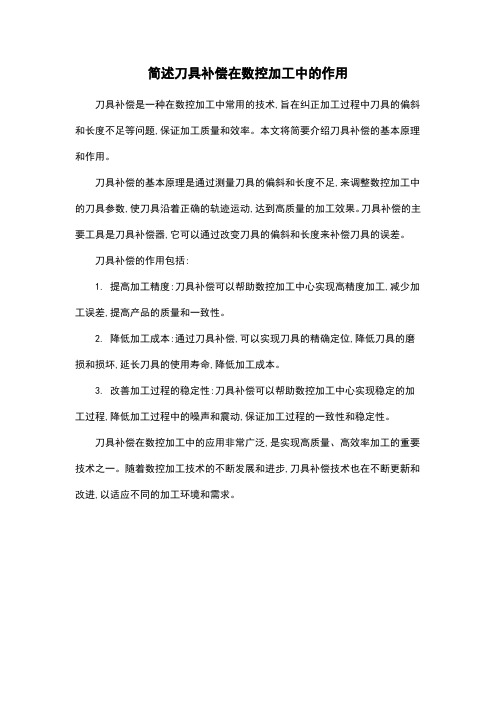
简述刀具补偿在数控加工中的作用
刀具补偿是一种在数控加工中常用的技术,旨在纠正加工过程中刀具的偏斜和长度不足等问题,保证加工质量和效率。
本文将简要介绍刀具补偿的基本原理和作用。
刀具补偿的基本原理是通过测量刀具的偏斜和长度不足,来调整数控加工中的刀具参数,使刀具沿着正确的轨迹运动,达到高质量的加工效果。
刀具补偿的主要工具是刀具补偿器,它可以通过改变刀具的偏斜和长度来补偿刀具的误差。
刀具补偿的作用包括:
1. 提高加工精度:刀具补偿可以帮助数控加工中心实现高精度加工,减少加工误差,提高产品的质量和一致性。
2. 降低加工成本:通过刀具补偿,可以实现刀具的精确定位,降低刀具的磨损和损坏,延长刀具的使用寿命,降低加工成本。
3. 改善加工过程的稳定性:刀具补偿可以帮助数控加工中心实现稳定的加工过程,降低加工过程中的噪声和震动,保证加工过程的一致性和稳定性。
刀具补偿在数控加工中的应用非常广泛,是实现高质量、高效率加工的重要技术之一。
随着数控加工技术的不断发展和进步,刀具补偿技术也在不断更新和改进,以适应不同的加工环境和需求。
数控车床加工刀具补偿功能怎么用?

数控车床加⼯⼑具补偿功能怎么⽤?⼀、数控车床⽤⼑具的交换功能1. ⼑具的交换指令格式⼀:T0101;该指令为FANUC系统转⼑指令,前⾯的T01表⽰换1号⼑,后⾯的01表⽰使⽤1号⼑具补偿。
⼑具号与⼑补号可以相同,也可以不同。
指令格式⼆:T04D01;该指令为SIEMENS系统转⼑指令,T04表⽰换4号⼑,D01表⽰使⽤4号⼑的1号⼑沿作为⼑具补偿存储器。
2. 换⼑点所谓换⼑点是指⼑架⾃动转位时的位置。
⼤部分数控车床,其换⼑点的位置是任意的,换⼑点应选在⼑具交换过程中与⼯件或夹具不发⽣⼲涉的位置。
还有⼀些机床的换⼑点位置是⼀个固定点,通常情况下,这些点选在靠近机床参考点的位置,或者取机床的第⼆参考点来作为换⼑点。
⼆、⼑具补偿功能1. ⼑具补偿功能的定义在数控编程过程中,为使编程⼯作更加⽅便,通常将数控⼑具的⼑尖假想成⼀个点,该点称为⼑位点或⼑尖点。
数控机床根据⼑具实际尺⼨,⾃动改变机床坐标轴或⼑具⼑位点位置,使实际加⼯轮廓和编程轨迹完全⼀致的功能,称为⼑具补偿(系统画⾯上为“⼑具补正”)功能。
数控车床的⼑具补偿分为:⼑具偏移(也称为⼑具长度补偿)⼑尖圆弧半径补偿2. ⼑位点的概念所谓⼑位点是指编制程序和加⼯时,⽤于表⽰⼑具特征的点,也是对⼑和加⼯的基准点。
数控车⼑的⼑位点如图所⽰。
尖形车⼑的⼑位点通常是指⼑具的⼑尖;圆弧形车⼑的⼑位点是指圆弧刃的圆⼼;成形⼑具的⼑位点也通常是指⼑尖。
三、⼑具偏移补偿1. ⼑具偏移的含义⼑具偏移是⽤来补偿假定⼑具长度与基准⼑具长度之长度差的功能。
车床数控系统规定X轴与Z 轴可同时实现⼑具偏移。
⼑具⼏何偏移:由于⼑具的⼏何形状不同和⼑具安装位置不同⽽产⽣的⼑具偏移。
⼑具磨损偏移:由⼑具⼑尖的磨损产⽣的⼑具偏移。
⼑具偏移补偿功能⽰例:FANUC系统的⼑具⼏何偏移参数设置如图所⽰,如要进⾏⼑具磨损偏移设置则只需按下软键[磨耗]即可进⼊相应的设置画⾯。
图中的代码“T”指⼑沿类型,不是指⼑具号,也不是指⼑补号。
数控机床操作中的自动刀具长度补偿方法
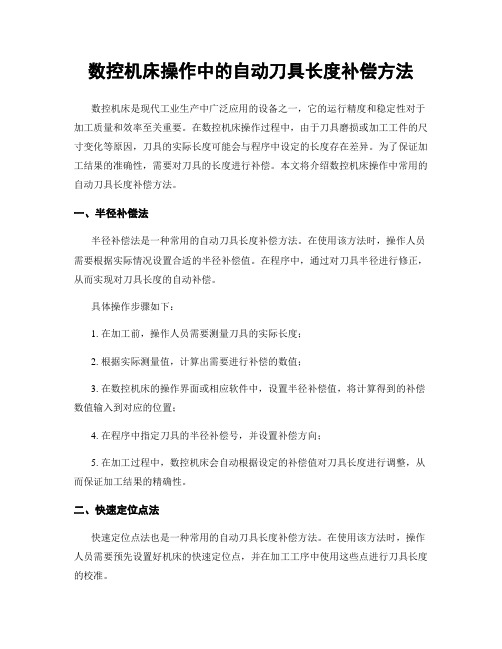
数控机床操作中的自动刀具长度补偿方法数控机床是现代工业生产中广泛应用的设备之一,它的运行精度和稳定性对于加工质量和效率至关重要。
在数控机床操作过程中,由于刀具磨损或加工工件的尺寸变化等原因,刀具的实际长度可能会与程序中设定的长度存在差异。
为了保证加工结果的准确性,需要对刀具的长度进行补偿。
本文将介绍数控机床操作中常用的自动刀具长度补偿方法。
一、半径补偿法半径补偿法是一种常用的自动刀具长度补偿方法。
在使用该方法时,操作人员需要根据实际情况设置合适的半径补偿值。
在程序中,通过对刀具半径进行修正,从而实现对刀具长度的自动补偿。
具体操作步骤如下:1. 在加工前,操作人员需要测量刀具的实际长度;2. 根据实际测量值,计算出需要进行补偿的数值;3. 在数控机床的操作界面或相应软件中,设置半径补偿值,将计算得到的补偿数值输入到对应的位置;4. 在程序中指定刀具的半径补偿号,并设置补偿方向;5. 在加工过程中,数控机床会自动根据设定的补偿值对刀具长度进行调整,从而保证加工结果的精确性。
二、快速定位点法快速定位点法也是一种常用的自动刀具长度补偿方法。
在使用该方法时,操作人员需要预先设置好机床的快速定位点,并在加工工序中使用这些点进行刀具长度的校准。
1. 在加工前,选择合适的位置作为快速定位点,并将其存储在数控机床中;2. 在程序中,使用快速定位点进行刀具长度的校准。
通过在程序中指定固定的刀具参考点,数控机床能够自动计算刀具与参考点之间的距离,并对刀具长度进行自动补偿;3. 在加工过程中,数控机床会根据预先设定的快速定位点,自动进行刀具长度的补偿,从而保证加工结果的准确性。
三、自动测量法自动测量法是一种基于传感器的自动刀具长度补偿方法。
该方法通过在数控机床中安装传感器,并将传感器与机床控制系统相连,实现对刀具长度的实时检测和自动补偿。
具体操作步骤如下:1. 在数控机床中安装相应的传感器,确保传感器可以准确测量刀具的长度;2. 将传感器与机床控制系统连接,并进行相应的设定和校准;3. 在加工过程中,传感器会实时监测刀具的长度,并将检测结果传输给机床控制系统;4. 机床控制系统根据传感器提供的数据,自动对刀具长度进行补偿,保证加工结果的准确性。
刀具补偿功能在数控加工中的应用
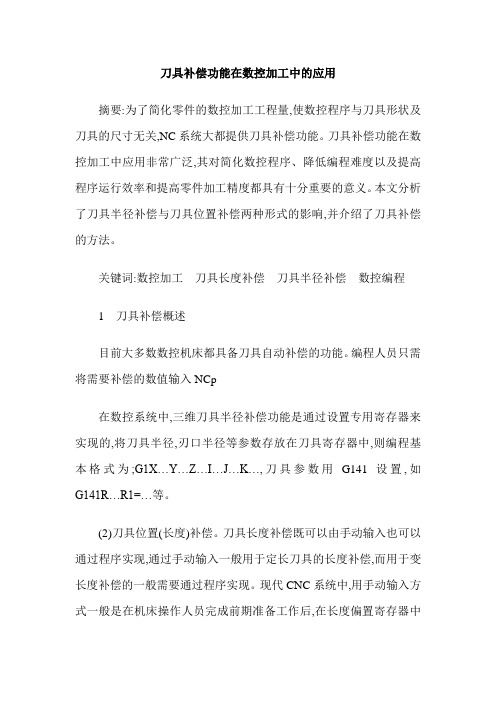
刀具补偿功能在数控加工中的应用摘要:为了简化零件的数控加工工程量,使数控程序与刀具形状及刀具的尺寸无关,NC系统大都提供刀具补偿功能。
刀具补偿功能在数控加工中应用非常广泛,其对简化数控程序、降低编程难度以及提高程序运行效率和提高零件加工精度都具有十分重要的意义。
本文分析了刀具半径补偿与刀具位置补偿两种形式的影响,并介绍了刀具补偿的方法。
关键词:数控加工刀具长度补偿刀具半径补偿数控编程1 刀具补偿概述目前大多数数控机床都具备刀具自动补偿的功能。
编程人员只需将需要补偿的数值输入NCp在数控系统中,三维刀具半径补偿功能是通过设置专用寄存器来实现的,将刀具半径,刃口半径等参数存放在刀具寄存器中,则编程基本格式为;G1X…Y…Z…I…J…K…,刀具参数用G141设置,如G141R…R1=…等。
(2)刀具位置(长度)补偿。
刀具长度补偿既可以由手动输入也可以通过程序实现,通过手动输入一般用于定长刀具的长度补偿,而用于变长度补偿的一般需要通过程序实现。
现代CNC系统中,用手动输入方式一般是在机床操作人员完成前期准备工作后,在长度偏置寄存器中写入刀具长度参数值实现的,程序命令方式主要是通过G43和G44代码实现。
在实际数控加工过程中,合理应用刀具补偿是提高加工质量的关键环节,下面针对不同的数控系统分析刀具补偿功能在数控加工中的应用。
2 数控车削中刀具补偿的应用数控车削中,刀具需要连续工作,由于换刀或安装,以及刀具磨和刀尖圆弧半径等产生的误差必须需要进行刀补工作。
通常以一把刀具为基准,以其刀尖位置建立坐标系,这样其他刀具在此坐标系下由于刀尖位置的偏差应对偏移量进行补偿。
在部分机床中,刀具的长度补偿可以通过T代码实现。
T代码的命名规则为前两位是刀具号,后两位为刀具的补偿号。
比如G02X50Z90T0305为选用3号刀具5号刀具补偿。
目前大多数的CNC系统都具有对刀显微系统,使用补偿指令之后,无需计算刀尖位置,只需要按照轮廓编程即可。
刀具补偿功能概述

刀具补偿功能概述刀具补偿是数控加工中一项关键的技术,它可以有效地提高加工精度和效率。
本文将对刀具补偿功能进行概述,介绍其原理、应用和优势。
一、刀具补偿的原理刀具补偿是通过在数控系统中对工具轨迹进行校正来实现的。
由于刀具的尺寸、形状和磨损等因素,工件的加工结果可能会与预期有所偏差。
刀具补偿基于工具几何和轨迹偏差的关系,通过调整数控程序中的刀具路径,使实际切削轨迹与期望轨迹保持一致,从而实现精准加工。
二、刀具补偿的应用领域刀具补偿广泛应用于各种数控加工领域,如铣削、车削、钻削等。
在这些加工过程中,刀具补偿能够提高零件的尺寸精度、表面质量和加工效率。
1. 铣削中的刀具补偿:在铣削过程中,刀具补偿可以根据刀具直径和偏移量来自动调整切削轨迹,确保切削结果符合要求。
同时,通过刀具补偿,还可以实现铣削过程中不同刀具的自动更换,提高生产效率。
2. 车削中的刀具补偿:车削过程中,刀具补偿可以针对工件的尺寸偏差进行调整,使加工后的工件尺寸与期望尺寸保持一致。
刀具补偿可以通过修正刀具位置或调整进给速度来实现,大大提高了车削加工的精度和稳定性。
3. 钻削中的刀具补偿:在钻削过程中,刀具补偿可以根据刀具尺寸和磨损情况来调整刀具的位置和轨迹。
通过刀具补偿,可以有效控制钻孔的直径误差和圆度误差,提高钻削加工的质量。
三、刀具补偿的优势刀具补偿具有许多优势,使其在数控加工中得到广泛应用。
1. 提高加工精度:刀具补偿可以消除工具尺寸和磨损等因素对加工精度的影响,实现更加精确的加工结果。
2. 提高加工效率:通过刀具补偿,可以使切削轨迹与工件的实际形状相匹配,减少加工过程中的空刀时间,提高生产效率。
3. 增强加工稳定性:刀具补偿可以对工具的位置和轨迹进行校正,减少切削力的变化,有助于提高加工过程的稳定性。
四、结论刀具补偿功能在数控加工中起到至关重要的作用,它通过调整刀具路径,确保加工结果与期望一致,提高加工精度和效率。
刀具补偿在铣削、车削、钻削等加工过程中广泛应用,并具有诸多优势,如提高加工精度、效率和稳定性。
- 1、下载文档前请自行甄别文档内容的完整性,平台不提供额外的编辑、内容补充、找答案等附加服务。
- 2、"仅部分预览"的文档,不可在线预览部分如存在完整性等问题,可反馈申请退款(可完整预览的文档不适用该条件!)。
- 3、如文档侵犯您的权益,请联系客服反馈,我们会尽快为您处理(人工客服工作时间:9:00-18:30)。
数控加工中刀具补偿的应用朱卫峰 [中国长江动力公司(集团)]摘要:刀具补偿是数控机床的主要功能之一,他分为:刀具长度补偿、刀具半径补偿、刀具偏置补偿种。
它们基本上能解决加工过程中根据刀具几何形状尺寸产生零件轮廓轨迹等问题,从而保证加工出符合图纸尺寸要求的零件。
关键词: 刀具半径补偿,刀具长度补偿,刀具几何补偿,磨损补偿引言:刀具补偿的理论及其实现,在各类数控系统中都已经是比较成熟的技术。
在使用数控机床加工零件的过程中,刀具的运动轨迹不等同于工件的轮廓。
为了保证工件轮廓形状,加工时数控系统必须根据工件轮廓和刀具的几何形状尺寸计算出刀具中心运动轨迹。
在建立、执行刀补后,数控系统自动计算、自动调整刀位点到刀具的运动轨迹从而加工出符合图纸尺寸要求的形状。
当刀具磨损或更换后,加工程序不变,只须更改程序中刀具补偿的数值。
刀具补偿使用简单方便,能极大提高编程的工作效率。
下面就刀具补偿在一般数控加工中的应用进行探讨:一.刀具半径补偿1.刀具半径补偿的概念A.在轮廓加工过程中,由于刀具总有一定的半径,刀具中心的运动轨迹与所需加工零件的实际轮廓并不重合。
在进行轮廓加工时,刀具中心偏离零件的实际轮廓表面(图纸中所要加工对象的轮廓)一个刀具半径值。
这种偏移,称为刀具半径补偿。
B.采用刀具半径补偿的作用和意义数控机床一般都具备刀具半径补偿的功能。
在加工中,使用数控系统的刀具半径补偿功能,就能避开数控编程过程中的繁琐计算,而只需计算出工件加工轮廓轨迹的起始点坐标值即可。
同时,利用刀具半径补偿功能,还可以实现同一程序的粗、精加工以及同一程序的阴阳模具加工等功能。
C.刀具半径补偿指令的使用方式根据ISO 标准规定,当刀具中心轨迹在编程轨迹前进方向的左边时,称为左刀补,用G41表示;刀具中心轨迹在编程轨迹前进方向的右边时,称为右刀补,用G42表示;注销刀具半径补偿时用G40表示。
2 刀具半径补偿过程A.刀具半径补偿建立:当输入的程序段包含有G41/G42命令时,系统认为此时已进入刀补建立状态。
当以下条件成立时,加工中心以移动坐标轴的形式开始补偿动作。
a.有G41或G42被指定;b.在补偿平面有轴的移动;c.指定了一个补偿号或已经指定一个补偿号但不能是D00;d.补偿平面被指定或已经被指定;e.G00或G01模式有效。
B.补偿模式:在刀具补偿进行期间,刀具中心轨迹始终偏离编程轨迹一个刀具半径值的距离。
此时半径补偿在G00、G01、G02、G03情况下均有效。
C.取消补偿:使用G40指令取消程序段偏置值,使刀具撤离工件,回到起始位置,从而使刀具中心与编程轨迹重合。
当以下两种情况之一发生时加工中心补偿模式被取消。
①给出G40同时要有补偿平面坐标轴移动。
②刀具补偿号为D00。
3 刀具半径补偿在数控加工中的应用有了刀具半径自动补偿功能,除可免去刀心轨迹的人工计算外,还可利用同一加工程序去完成粗、精加工及阴阳模具加工等。
A.不同平面图1 G18指令的使用的半径补偿刀具半径补偿用G17、G18、G19命令在被选择的工作平面进行补偿。
即当G18命令执行后,刀具半径补偿仅影响X、Z移动,而对Y轴没有作用。
铣削如图1所示圆柱面,使用刀具是半径为10mm的球形立铣刀。
编程控制点有两个,即刀尖、球心,这里使用球心。
O0001N1 G90G54G18G00X60.0Y0S1000M03;N2 Z0;N3 G91G01 G41X-20.0D01 F100;N4 G02X-80.0I40.0;N5 G40G0lX20.0;┇┇N22 G90G00Z100.0;N23 X0 Y0M05;N24 M30;B.实现同一程序的粗、精加工:刀具半径补偿除方便编程外,还可改变补偿大小的方法以用实现同一程序的粗精加工。
粗加工刀具补偿量=刀具半径+精加工余量,精加工刀具补偿量=刀具半径+修正量C.实现同一程序的阴阳模具加工,例如:在加工同一公称尺寸的、外两种型面时,可分别 调用G41、G42指令,利用同一程序(G41G42互换)完成、外两种型面的加工。
如图2。
例:考虑刀具半径补偿,编制图a 所示零件的加工程序。
要求建立如图所示的工件坐标系,按箭头所指示的路径进行加工。
设加工开始时刀具距离工件上表面50mm ,切削深度为2mm 。
YXO30201010203040-10-10A B C D E 对刀点K ①②③④⑤⑥⑦图a 刀补指令的应用解:一个完整的零件程序如表8-6。
表8-6 刀具半径补偿指令的应用程 序 说 明图2 、外两种型面的加工%8031 程序名N10 G92 X-10 Y-10 Z50 确定对刀点N20 G90 G17 在XY平面,绝对坐标编程N30 G42 G00 X4 Y10 D01 右刀补,进刀到(4,10)的位置N40 Z2 M03 S900 Z轴进到离表面2mm的位置,主轴正转N50 G01 Z-2 F800 进给切削深度N60 X30 插补直线A→BN70 G03 X40 Y20 I0 J10 插补圆弧B→CN80 G02 X30 Y30 I0 J10 插补圆弧C→DN90 G01 X10 Y20 插补直线D→EN100 Y5 插补直线E→(10,5)N110 G00 Z50 M05 返回Z方向的安全高度,主轴停转N120 G40 X-10 Y-10 返回到对刀点N130 M02 程序结束4 使用刀具半径补偿时常见的问题A.在建立、取消刀补时所使用的G41、G42、G40指令的程序段中,必须同时使用G00或G01指令,不能使用G02或G03指令;B.当刀具半径补偿取负值时,G41和G42的功能互换;C.刀具半径补偿有B功能和C功能两种补偿形式。
由于B功能刀具半径补偿只能根据本段程序进行刀补计算,在两个程序段之间的刀具中心轨迹就会出现间断点或交叉点. 因此工件尖角处工艺性较差;C功能刀具半径补偿能自动处理,两程序段之间采用直线或圆弧过渡, 其刀具中心轨迹的转接,可完全按照工件轮廓进行编程,因此现代CNC数控机床几乎都采用C功能刀具半径补偿。
当采用C功能刀具半径补偿时,要求在建立刀具半径补偿程序段的后续两个程序段中,必须含有指定补偿平面的位移指令(G00、G01,G02、G03等),否则无法建立正确的刀具半径补偿。
二.刀具长度补偿1.刀具长度在数控加工中是一个很重要的概念。
我们在对一个零件编程的时候,首先要指定零件的编程中心,然后才能建立工件编程坐标系。
长度补偿只是和主运动轴(一般为Z轴)坐标有关,它不同于X、Y平面的编程零点是由主轴锥孔定位而不改变,而对于Z坐标的零点就不一样了。
每一把刀的长度都是不同的,如图3所示我们要加工两个Φ20mm的孔(用1号刀)和一个Φ10mm(用2号刀)的孔,分别用一把长度50mm直径20mm的1号刀(基准刀)和长度100mm直径10mm的2号刀加工。
在该工件的加工过程中需要用两把不同的刀具,而此时机床已经设定了工件零点,当换刀加工另一个孔时,如果2号刀也从设定零点开始加工,2号刀因为比1号刀长,所以会导致刀具和工件相撞。
此时如果设定刀具补偿,把1号刀和2号刀的长度进行补偿,此时机床零点设定之后,即使是1号刀和2号刀长度不同,因补偿的存在,在调用2号刀工作时,零点Z坐标已经自动向Z+(或Z-)补偿了2号刀的长度,保证了加工零点的正确。
具体的加工程序如下:(以主轴轴端作为起刀点,设置H01= 50mm,H02= 100mm,图4)N10 G92 X0 Y0 Z0;N20 G90 G00 X60.0 Y70.0 Z150.0;N30 T01 M06;N40 G43 Z-32.0 H01;N50 G01 Z-53.0 F120;N60 G04 P2000;N70 G01 Z-32.0;N80 X150.0 Y50.0;N90 G01 Z-55.0 F120;N100 G04 P2000N110 G49 G00 Z-32.0;N120 M00;N130 G92 X0 Y0 Z0;N140 G90 G00 X90.0 Y30.0 Z150.0;N150 T02 M06;N160 G43 Z-32.0 H02;N170 G01 Z-70.0 F120;N180 G04 P2000;N190 G49 G01 Z-32.0;N200 G00 X0 Y0 Z0;N210 M30;在上述程序中,我们不难发现,在编程中坐标值是完全按工件的轮廓尺寸编写的,而编程的零点并不是刀位点,那么为何在加工过程中没有发生撞刀呢?这是因为我们使用了刀具长度补偿指令G43,执行该指令后会使刀具的位置发生变化,那么我们应该如何使用这个指令呢?2、刀具长度补偿指令的使用技巧刀具长度补偿指令主要针对刀具轴向(Z方向)的补偿。
它能使刀具在Z方向上的实际偏移量在程序给定值基础上增加或减少一个偏置量,由G43和G44两个指令实现。
G43为刀具长度正补偿,G44为刀具长度负补偿。
A、正负补偿及偏置量的确定在长度补偿指令中出现了两个指令,那么在编程过程中应该如何使用这两个指令呢?对于正、负补偿指令,主要是根据Z轴的方向确定,如果刀具的刀位点在编程原点Z坐标的负方向上,则使用正补偿指令(G43),反之,则用负补偿指令(G44)。
H为补偿功能代号,它后面的两位数字表示的是刀具补偿寄存器的地址字,寄存器中存放刀具长度的补偿值,那么补偿值应如何确定呢?一般有两种情况:一是以主轴轴端中心作为起刀点,则以刀具离轴端伸出的长度作为H中的偏置量;如果以标准刀的刀位点作为起刀点,则是以与标准刀的长度差值作为其偏置量。
该值可以为正,也可以为负。
如果刀具刀位点朝Z轴正方向运动是靠近编程零点位置,则用G43指令,H××中赋与正值,如果H××中赋与负值,就变成了G43指令的反方向补偿,即相当于指令G44。
为了不混淆G43、G44的用法,我们通常都采用G43指令,而通过H××中补偿量的正负设定来达到G44的使用效果。
B、长度补偿指令中刀具的位置变化由于刀具的位置直接影响工件的加工,因此刀具的位置的变化就显得至关重要,那么在执行长度补偿指令后刀具的位置究竟会发生怎样的变化呢?在教材的编排中主要是通过公式的坐标值计算来理解刀具位置的变化。
这一方法,在理解的过程中总是会出现一些偏差,而且用坐标的计算也相对来说比较的繁琐。
如将坐标的变化转化为工件坐标系的变化就直观多了.也就是将工件坐标系和刀具一起沿Z 轴方向移动一个刀具长度补偿值。
以G43指令为例,H ××中的补偿值为正则Z 轴正方向移动,反之则负方向移动。
我们还是以图5中孔的加工来进行说明。
当我们用1号刀加工孔①时,教材中的方法是执行G43后,起刀点Z 实际值=Z 指令值+50= - 53+50= - 3mm ,可以看到刀具在Z 方向的每一个坐标都要计算之后才能知道刀具刀尖点的正确位置。