合成氨老系统废热锅炉
合成氨生产危险有害因素识别

1 火灾、爆炸危险1.1 合成氨生产采用的主要原料为煤,属可燃固体,这些物质在常温下不易引起燃烧,但如遇高温可能引起燃烧,在煤堆场,大量的煤堆积在一起,热量如无法及时散出,煤可能产生自燃,而引发火灾。
1.2 合成氨生产系统中存在大量的塔、槽、罐等静设备,由于其大部分承受高温高压,且压力和温度是经常变化的,同时参与工艺过程的介质绝大多数是易燃易爆、有腐蚀性和有毒的,因此如有操作失误、违章动火,或因密封装置失效、设备管道腐蚀,或因受设备、管道、阀门制造缺陷的影响等,将会引起泄漏,形成爆炸性混合物,造成爆炸事故。
1.3 合成氨生产系统中存在大量的换热器,有的换热工作条件要求在高温高压条件下进行,有的工作流体具有易燃易爆、有毒、腐蚀性的特点。
如果换热器的设计不合理、制造缺陷、材料选择不当、腐蚀严重、违章作业、操作失误和维护管理不善,可能发生换热器发生燃烧爆炸、严重泄漏和管束失控等事故。
1.4 造气炉是合成氨生产系统的生成合成氨原料气的关键设备,由于半水煤气的主要成分有氢气、一氧化碳和少量的硫化氢、甲烷等,这些气体不仅极易燃烧、爆炸,有的还具有腐蚀性、毒性,而且造气炉在高温条件下运行,其操作条件恶劣、造气周期短,如果稍有不慎或违反操作规程等都有可能导致造气炉发生炉爆炸事故。
经分析,发生造气炉爆炸的主要原因如下:(1)过氧操作致使造气炉爆炸。
在半水煤气生产过程中,为防止后工序变换工段触煤活性降低或被烧坏和引起造气系统发生爆炸,氧含量要求控制在0.5%以下。
如果半水煤气中氧含量增加,达到爆炸极限时,遇明火和其他激发能源,就会引起爆炸事故。
(2)空气、煤气倒流形成爆炸性混合物。
主要表现在:a、检修时,未采取盲板与系统切断措施,又未关闭下行阀,到气柜的煤气总管和气柜水封积水造成憋压,致使煤气冲破洗气塔水封,或盲板强度不够而被冲破,倒流到炉内引起爆炸。
b水封放水后或洗气箱上水阀损坏,致使水圭寸破坏,空气流入炉内,或洗气箱水封漏气,煤气倒流入炉内。
合成废热锅炉泄漏原因及采取措施

合成废热锅炉泄漏原因及采取措施作者:郭挺来源:《硅谷》2008年第02期[摘要]分析合成废热锅炉泄漏的原因及对系统的危害,提出如何更好的控制进合成回路压力,从而优化操作,最大限度的提高氨产量。
[关键词]合成废热锅炉合成气压差锅炉给水氨产量中图分类号:TF7文献标识码:A文章编号:1671-7597 (2008) 0120046-01我公司合成氨装置合成废锅E42是意大利IND.MECC.B公司设计制造的。
2006年12月16日,发现E67出口氢含量偏高。
经拆开封头分析确认是合成废锅管束泄漏。
一、合成废热锅炉简介(一)结构设计合成废热锅炉E42是DEU卧式蒸汽发生器,管程介质为锅炉给水,壳程介质为合成气,内部换热管为U形管。
设备参数:名称壳程管程设计压力(Mp)15.86 13.8设计温度(℃)495/477 359操作压力(Mp)14.69 13.1操作温度(℃)456/380 326.9/331工作介质合成气锅炉给水水压实验(Mp)28.120.7传热面积(m2)158.3保温(冷)厚度(mm)硅渣棉190+硅酸铝30+矿渣棉160设备总重量(kg)27000(二)工艺流程除氧水经锅炉给水泵P-14A/B升压,一部分锅炉水经H-1对流段加热后,进入汽包V-7,另一部分锅炉给水经高变出口换热器E-11加热后与锅炉循环水泵P-1A/B/C出口水相混合。
再经废热锅炉E-8、E-42、E-43、E-53加热,部分汽化后进入汽包V-7汽化,产生高压饱和蒸汽在H-1对流段吸收热量并达到过热(520℃)后被送至CT-2,自CT-2抽出的中压蒸汽直接输入SM总管,供各有关用户使用,V-7分离出的锅炉水再经P-1A/B/C进行强制循环。
二、泄漏原因(一)运行时间较长废热锅炉从安装使用到现在已有10年之久,设备内部结垢,传热不均匀,局部受热或长时间受腐蚀,导致管壁厚薄不均等。
(二)操作环境波动大开停车过程中合成废热锅炉管程与壳程压差相差较大,且在开停车中升降压速率较快,长此以往使得设备泄漏。
新型合成氨废热锅炉的技术特点

( 鲁化好 阳光生态肥 业有 限公 司 ,山东 滕州 2 7 7 5 2 7 )
[ 摘
要 ]介绍意大利 O L MI 公 司设 计制造的新型合成氨废热锅炉的材料选择 、换热管分布 、内孔焊等
技术特点 ,结合 国内情况 ,提 出借鉴方 向。
[ 关键词]合成氨废热锅炉 ;1 2 C r Mo 9 - 1 0;1 0 C r Mo 9 - 1 0 ;U形管 ;直连 ;内孔焊 ;n形 密封 [ 中图分 类号】T Q 1 1 3 . 2 5 1 . 5 [ 文献标志码 ]B [ 文章 编号 ]1 0 0 4— 9 9 3 2 ( 2 0 1 5 ) 0 4— 0 0 3 4— 0 3
兖 矿鲁南化工有限公 司 2 4 0 k t / a合成 氨项 目,工 艺包设 计 由 国外 某工 程公 司提 供 ,并配 套 提 供合 成废 热 回收器 。该废 热 回收器 在设 计制 造
中采用 了多 项 先进 技 术 ,具 有 独 特 的技 术优 势 ,
技 术参 数见 表 1 ,整体结 构 图见 图 1 。
第 4期 2 0 1 5年 7月
中 氮
肥
No . 4
M— S i z e d Ni t r o g e n o u s Fe r t i l i z e r P r o g r e s s
J u 1 .2 01 5
新 型 合 成 氨 废 热 锅 炉 的 技 术 特 点
表 1 废 热 锅 炉 主 要 技 术 参 数
壳 程
项 目
管 程 进口 出口
进口
出 口
运行稳定可靠,值得国内公司参考借鉴。现将其 主 要技术 特 点作一 介绍 。
1 设 备概 述
合成氨造气系统废热锅炉两次爆炸的分析
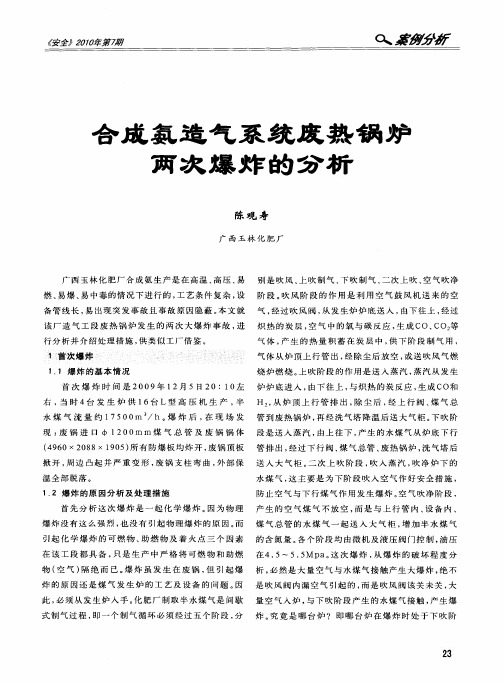
合 成 氨 造 气 系 统 废 热 锅 炉 两 次爆 炸 的分析
陈 观 寿
广 西 玉 林 化 肥 厂
广 西玉 林化 肥 厂 合成 氨生 产是 在 高温 、 压 、 高 易 别 是 吹 风 、 吹 制 气 、 吹 制 气 、 次 上 吹 、 气 吹 净 上 下 二 空 燃 、 爆 、 中毒 的情 况下 进 行的 , 艺 条件 复杂 , 易 易 工 设 阶 段 。 风 阶 段 的 作 用 是 利 用 空 气 鼓 风 机 送 来 的 空 吹 备 管 线 长 , 出 现 突 发 事 故 且 事 故 原 因 隐 蔽 。 文 就 气 , 过 吹 风 阀 , 发 生 炉 炉 底 送 入 , 下 往 上 , 过 易 本 经 从 由 经 该 厂造 气 工段 废 热 锅 炉 发 生 的两 次 大 爆 炸 事 故 , 进 炽 热 的 炭 层 , 气 中 的 氧 与 碳 反 应 , 成 CO、 O。 空 生 C 等 行分 析并 介绍 处理措 施 , 类似 工厂 借鉴 。 供 气体 , 生 的 热 量 积 蓄在 炭 层 中 , 下 阶 段制 气 用 , 产 供 气 体 从 炉 顶 上 行 管 出 , 除 尘 后 放 空 , 送 吹 风 气 燃 经 或 烧 炉 燃 烧 。 吹 阶 段 的 作 用 是 送 入 蒸 汽 , 汽 从 发 生 上 蒸
吹 风 阀 未 关 , 么 空 气 与 下 吹 时 产 生 的 水 煤 气 混 合 工 段 想 利 用 这 次 短 时 间 停 机 会 , 理 3# 炉 检 修 阀 , 那 处 就 会 发 生爆 炸 , 旦爆 炸 , 热 锅 炉 必 将遭 到 破 坏 。 此 阀 与 废 锅连 通 ( 间没 有 检 修 水 封 ) 检 修 时 , 一 废 中 。 把
氨合成系统检修中发现的问题及处理
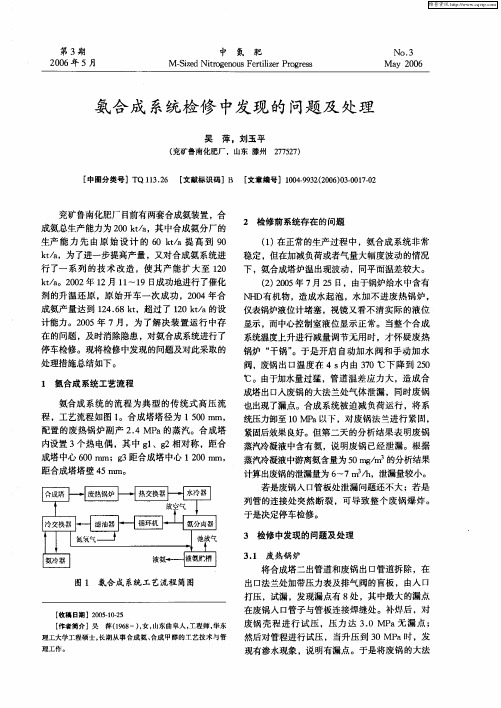
全 } I垫 H 垫 堡 卜. _ 窒塑 _ 一 奎 _ 1
}
放空气 l
厂 望 鲨 r 堡堡 H . 至 — 厂T
氮氧
3 检修中发现的问题及处理
液 叫
竺 竺
3 1 废 热锅 炉 .
图 1 氨合 成 系统工 艺流程 简 图
将合成塔二出管道和废锅出 口管道拆除 ,在 出口法兰处加带压力表及排气阀的盲板 ,由入 口
吴 萍 ,刘玉平
( 充矿鲁南化肥厂 ,山东 滕州 272) 7 5 7
[ 中图分类号]T 1.6 [ Q 132 文献标识码]B [ 文章编号]10—9220 )301— 04 3 (060— 70 9 0 2
兖矿鲁南化肥厂 目前有两套合成氨装置 ,合
成氨总生产能力为 2 0k/ ,其中合成氨分厂 的 0 ta 生产 能 力先 由原 始设 计 的 6 ta 高 到 9 0 k/ 提 0 k/,为了进一步提高产量 ,又对合成氨系统进 ta
然后对管程进行试压 ,当升压到 3 a 0MP 时,发
理工大学工程硕士 , 长期从事合成 氨、 合成 甲醇的工艺技术 与管
现有渗水现象 ,说明有漏点。于是将废锅的大法
维普资讯
・1Biblioteka 8・中 氮 肥 第 3期
兰拆卸 ,取出废锅内件 ,对管子一 管板焊缝打磨 后 ,用磁粉探伤 ,发现 2 处小裂纹 ,补焊后 ,继
2 检修 前 系统存在 的问题
() 1 在正常的生产过程中,氨合成系统非常
稳定 , 但在加减负荷或者气量大幅度波动的情况
行了一系列 的技术 改造 ,使其 产能扩 大至 10 2 k/。20 年 1 月 1~1 成功地进行了催化 ta 0 2 2 1 9日
合成氨工艺及设备说明书

第一章说明书1.1 概述1.1.1循环机位置本工段设置在氨分离系统后,合成塔之前,从而充分利用循环机压缩功,提高进合成塔温度,减少冷量消耗,降低氨冷器负荷,同时提高进塔压力,提高合成率,而进循环机的氨冷量较低,避免了塔后循环机流程容易带液氨而导致循环机泄漏。
1.1.2反应热回收的方式及利用这涉及到废热锅炉的热量利用及合成塔塔外换热器如何科学设置的问题,废热锅炉的配置实际上是如何提高反应热的回收率和获得高品位热的问题,本设计选择塔后换热器及后置锅炉的工艺路线,设置塔后换热器使废热锅炉出口气体与合成塔二进气体换热,充分提高合成塔二进温度,相应提高了合成塔二出温度,进废热锅炉的气体温360℃,副产1.3MPa的中压蒸汽,充分提高回收热量品位。
1.1.3采用“二进二出”合成流程全部冷气经合成塔环隙后进入热交换器,可使合成塔体个点温度分布均匀,出口气体保持较低温度,确保合成塔长期安全稳定运行,与循环机来的冷气直接进入热交换器相比,使热交换器出口温度增大。
进入水冷的气体温度降低意味着合成余热回收率高和水冷负荷低。
1.1.4水冷器、氨冷器的设置水冷后分离液氨再进行冷交,氨冷有利于降低后续氨冷的负荷,边冷却边分离液氨,即提高了液氨的分离效果,又避免了气液两相流的存在,通过设置两氨冷器的冷凝充分解决了低压下,水冷后很少有氨冷凝下来的矛盾,达到了进一步冷却,保证合成塔入口氨冷量的要求。
1.1.5补充气及放空点位置设置补充气设置在冷交的二次入口,以便减少系统阻力,并通过氨冷进一步洗脱微量二氧化碳和一氧化碳及氨基甲酸等杂质,有利于保护触媒防止管道和设备堵塞。
放空点设置在冷交换器和氨分离器之间,氨分后有效气体浓度较低,惰性气体含量较高,有利于降低新鲜气单耗。
1.1.6新型设备的使用离心式循环压缩机用于合成工段,能避免油污渗入循环气,提高合成气质量,从而可不设油分离器降低能耗,对于本工段选用冷激式内件,要求合成气质量较高,无油压缩机更为合适,离心式循环压缩机还具有运行时间长的特点,经XX化肥厂资料表明,无油压缩机与注油压缩机相比较平均使用寿命可延长十倍。
合成废热锅炉换热管泄漏原因分析及处理总结

合成废热锅炉换热管泄漏原因分析及处理总结摘要:本文针对合成氨系统中换热设备合成废热锅炉换热管泄漏多次处理进行了分析,通过分析换热管泄漏的原因以及处理过程中遇到的问题,制定了相应的改进措施,最终设备运行正常,同时也希望本文能在同行业的问题处理中起到一定的借鉴作用。
关键词:换热管;泄漏;处理;预防引言合成废热锅炉是合成氨系统中重要的换热设备,工作原理是利用氨合成塔系统出口高温气体与水进行换热产生蒸汽进行余热利用。
但由于合成废热锅炉在合成氨系统的特殊性,承受高温高压,设备出现问题较多,如设备换热管泄漏,壳程焊缝裂纹,高压管箱管板焊缝裂纹等,本文针对合成废热锅炉换热管在检修过程中重复出现泄漏进行了处理和检验分析。
1设备及问题简介集团公司合成氨事业部柔性改造合成车间合成工段合成废热锅炉由上海某公司制造,换热面积:400M²,壳程容积:24.5M³,直径φ2800/φ1400×48/24,总高7426,换热管φ24×5×3900,管间距32mm,呈三角形排列,共计520根,U型排列,材质0Cr18Ni9;管板材质10MoWVNb,设计压力管程31.4MPa,壳程3.9MPa。
按合成氨系统中修计划,对换热类设备合成水冷,合成废热锅炉换热管进行试漏处理,在对合成废热锅炉壳程试压至2.4MPa时发现换热管出现泄漏。
随机按要求对换热管进行堵漏处理。
2设备问题处理中修首日按计划对系统进行了泄压置换,待合格后,对合成废热锅炉进行了相关连接管道拆除及系统隔离。
随即对壳程进行了加水,启废热锅炉离心泵开始进行第一次试压,压力2.4MPa,经过对换热管检查,共计发现进出口换热管管泄漏8根,按技术方案要求设备厂家人员对泄漏的换热管进行堵焊处理。
换热管堵焊使用材质304机加工成的专用堵头,几何尺寸φ15mm×φ10mm×42mm,为了减少热影响,使用钨极氩弧焊(GTAW)进行补焊,焊丝材质ER309,规格:φ2.0mm。
合成氨装置废热锅炉FV-02033/34挡板改造

5 8
何 淑英
合 成氨装 置废热锅炉 F V一00 3 3 2 3/ 4 炉 F 0 0 3 V一 2 3 / 4 3 挡 板 改 造
何 淑 英
( 海洋 石油 富岛股份有限公司 , 海南 东方 5 20 ) 76 0
长期运行 , 给公司造成巨大损失。为了彻底解决 F V 003 3 23/ 4挡板 问题 , 20 在 0 5年 的大修 期 间 , F 对 V 003 3 板 进 行 了改 造 。经 过 两 年 的运 行 检 23/4挡 验 , 明对 F 003 3 证 V一 23/ 4挡板 改 造非 常成 功 。
的 目的 。
2 故障原 因及 改造方案
F V一0 0 3 3 2 3 / 4挡 板 的功 能 设 置 :V 一 2 3 F 0 0 3挡
板 开 ,V一00 4挡 板 关 时 , 热 锅 炉 在 F F方 式 F 23 废 D 运 行 。F 0 03挡 板关 ,V一004挡 板 开 时 , V一 23 F 23 废 热锅 炉 在 T G方 式运 行 。满 足 F F和 T G两 种 方 E D E
图 1 合 成 氨 装 置 废 热锅 炉
含 氧量 1% 。为充 分利 用这 些 热 能 , 6 把燃 气 透平 的
排放气引入废热锅炉 , 作为废热锅炉的燃烧空气 , 改 变 了 以往 合成 氨装 置 中将燃 气 透平 的乏气 引入 一段 炉 的惯例 , 高一 段 炉的操 作 弹性 和独立性 , 充分 提 又 利用 了燃气透平的乏气所携带的热能, 达到降低能
气透平排放 的乏气作 为废 热锅炉燃烧空气 的运行
工况。
F F方 式 的工 艺作 用 : 设 置 F F方式 满 足 工 D ① D
- 1、下载文档前请自行甄别文档内容的完整性,平台不提供额外的编辑、内容补充、找答案等附加服务。
- 2、"仅部分预览"的文档,不可在线预览部分如存在完整性等问题,可反馈申请退款(可完整预览的文档不适用该条件!)。
- 3、如文档侵犯您的权益,请联系客服反馈,我们会尽快为您处理(人工客服工作时间:9:00-18:30)。
合成氨老系统废热锅炉
化学清洗方案
编制:鸿化技术中心化学清洗站2007 年 7 月 18 日
一、前言
公司合成氨厂废热锅炉(H101)自年月投运,至今未进行过化学清洗,现运行中反应出热效率降低。
合成氨厂提出对其进行化学清洗以除去换热管内表面沉积物,提高热效率及废热锅炉运行质量,为此编写该锅炉化学清洗方案如下,供清洗施工时采用。
二、废热锅炉基本概况和主要参数
该废热锅炉为卧式布置,设有上汽包,锅筒内经1200mm,壁厚22mm,材质为20g钢材,汽包内经1200mm,壁厚20mm,材质为16MnR钢材。
废热锅炉与汽包由Ø89×6的上升、下降管联接。
废热锅炉主要参数:
三、清洗范围
本次化学清洗的范围确定主要清洗该废锅壳程部分,上部汽包、上升管、下降管、换热管(外壁)。
其有关参数见下表。
四、清洗工艺及清洗流程
1、清洗工艺及药剂选择:
该废热锅炉现正在运行过程中,无法取得垢样(需在停车后取样进行分析及
溶垢实验)。
从锅炉结构和锅炉的材质等初步决定采用浸泡加循环酸洗的方法进行化学清洗,以除去附着的结垢(现初步判断以钙、镁垢为主)和腐蚀产物(氧化铁垢),提高废热锅炉的换热效率和保障运行安全。
在化学清洗工作中,酸洗缓蚀剂的选择是十分重要的,它不仅直接影响清洗质量,而且还会影响到设备的安全,因此,我们在本清洗中选用的缓蚀剂,是经过在实验室模拟确定的工艺条件下试验,筛选并多次应用在各类化学清洗中的复配型缓蚀剂,具有优良的缓蚀效果。
清洗工艺为:
试漏水冲洗酸洗水冲洗漂洗水冲洗钝化清洗药剂选择为:
酸洗液:水+盐酸+酸洗缓蚀剂(HJQ-101)
漂洗液:水+漂洗剂
钝化液:水+钝化剂(磷酸三钠、多聚磷酸盐、氢氧化钠) 2、清洗流程及简述:
清洗系统简述如下:
外部进液点选择下锅筒底部排污管处连接。
清洗实施时,配置好的清洗液从循环清洗槽经循环泵加压由进液点进入锅炉下锅筒进行清洗,再沿水冷壁和对流管上升与管壁上的垢和腐蚀产物反应后进入上锅筒,进入上锅筒后与锅筒内壁上的垢层和腐蚀产物反应,再由排出口引出进入临时清洗系统回液管回到循环清洗槽完成循环。
五、锅炉化学清洗前的准备
1.用户单位派出技术人员配合清洗队伍开展清洗工作。
配合清洗现场的管理与安
全,协调好参加清洗的本单位人员的调度。
2.电源、热源、水源由用户单位保证安全可靠,水源需保证供应量大于25m3/h。
电源功率需提供不小于10kw 。
用户单位需提供清洗现场临时分析室和临时休息场所。
3.用户单位提前拆除或隔离清洗时有可能接触清洗液的铜芯阀,奥氏体不锈钢部件及其它不适合清洗的部件、管道、仪表、安全阀等防止被清洗液损坏,拆除上锅筒内影响人员进入检查、清扫的部件。
4.打开锅筒顶部放空阀作排空用,检查是否畅通,是否开到最大。
5.安装的化学清洗临时系统管道及设备内应干净不得有砂石、杂物等。
所用阀门、法兰、仪表等部件应耐蚀。
6.化学清洗所用仪器需提前校正。
7.所用清洗药品需复验并保证质量。
8.化学清洗临时系统安装完备后应现场校对无误。
9.监测试片在清洗前分别放入上、下锅筒和清洗槽。
10.锅炉清洗前应按有关规定对锅炉本体各部分进行检查并作好记录。
六、清洗操作简述
1.按清洗系统图连接好临时清洗系统,装好监测试件,腐蚀监测试片提前称重后分别装入上下锅筒和清洗循环槽。
2.水冲洗及清洗系统试漏
由外供给水管向清洗槽注水,开启清洗泵将清水送入锅炉本体,同时检查临时清洗系统各部件和联接点有无泄漏,循环清洗泵是否运转正常,阀门开关是否灵活及有无泄漏,发现问题应及时处理,保证临时清洗系统各部分能正常运行。
当水位达到规定要求时停止补水,加大清洗泵流量,按清洗回路强制循环。
调节补水及排放,达到水冲洗指标时,排尽炉内水。
3.酸洗
关闭进入锅炉本体清洗阀门,向清洗槽中加入缓蚀剂,溶解、混合均匀后加入盐酸混均,分析盐酸酸度在控制范围内后开阀门将清洗药液注入锅炉本体,重复上述操作当液位达到要求后进行循环。
循环均匀后按现场分析监测数据向清洗槽中补加盐酸控制酸度按清洗回路进行循环酸洗。
当分析结果显示酸液浓度趋于稳定:相隔30分钟,两次分析结果酸液浓度的绝对差值小于0.2×10-2,并且铁、钙离子浓度基本趋于平衡,可视为酸洗终点。
继续清洗0.5~1小时,结束酸洗,酸洗废液排放入污水处理池。
4.水冲洗
开启排污阀,同时向清洗槽中注入清水,由循环清洗泵将清水注入锅炉本体,沿清洗回路将酸液顶出排放,使PH值快速升到4~4.5,总铁含量降到50mg/L以下。
5.漂洗
将计量的漂洗剂加入清洗槽中溶解,混均,再由循环清洗泵将漂洗液送入锅炉本体,循环2小时左右。
重复步骤“4”,使进出口水的PH值相同,转入钝化。
6.钝化
向清洗槽中加入计量的钝化药品使其溶解,混均,再由循环清洗泵打入锅炉本体,适当升温至要求,控制循环维持24小时。
7.排弃钝化液至污水处理池,恢复系统,清洗结束。
七、清洗控制条件及指标
八、锅炉清洗质量要求
达到或优于国家质量技术监督局《锅炉化学清洗规则》(九九版)有关规定和要求。
1.用腐蚀指示片监测的金属腐蚀速度的平均值应小于6g/m2.h,并且腐蚀总量不大于60g/m2。
2.锅炉清洗金属表面不出现二次浮锈,无点蚀,形成良好的钝化膜,无金属粗晶析出的过洗现象。
3.除垢率>70×10-2以上。
4.锅炉所有水冷壁管和对流管应畅流无阻。
九、系统清洗后的检验及善后工作
化学清洗结束后,排净液体拆除清洗临时系统。
打开锅筒,取出腐蚀监测试片,恢复其它装置并由锅炉检验单位人员到现场检验清洗效果。
清洗废液按《锅炉化学清洗规则》有关规定中和后排放。
清洗、并收拾好可重复利用物资。
鸿化技术中心化学清洗站
2007年3月8日。